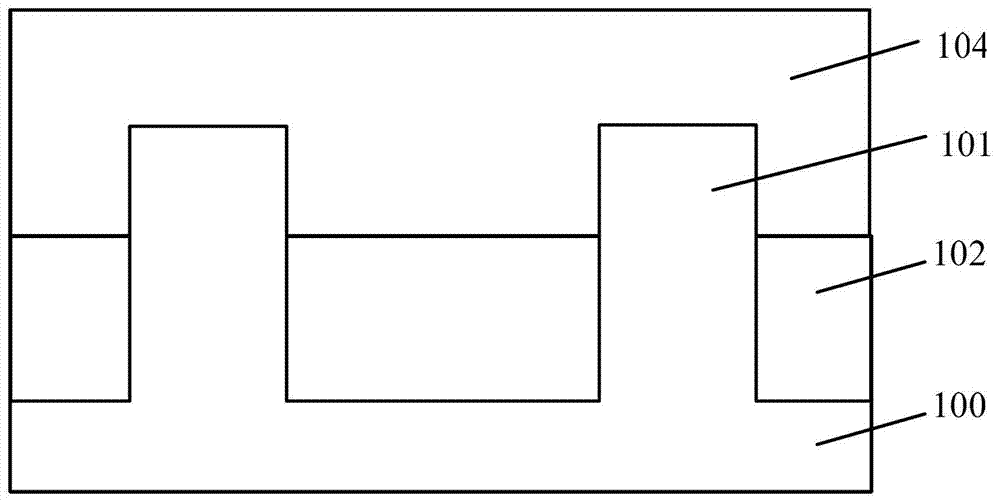
本發明涉及半導體制造領域,特別涉及一種鰭式場效應管的形成方法。
背景技術:MOS晶體管通過在柵極施加電壓,調節通過溝道區域的電流來產生開關信號。但當半導體技術進入30納米以下節點時,傳統的平面式MOS晶體管對溝道電流的控制能力變弱,造成嚴重的漏電流。鰭式場效應晶體管(FinFET)是一種新興的多柵器件,它一般包括凸出于半導體襯底表面的半導體鰭部,覆蓋部分所述鰭部的頂部和側壁的柵極結構,位于所述柵極結構兩側的鰭部內的源區和漏區。為了降低鰭式場效應晶體管柵極的寄生電容,提高器件速度,高K柵介電層與金屬柵極的柵極疊層結構被引入到鰭式場效應晶體管中。現有金屬柵極與高K柵介電層的柵極疊層結構通常采用“后柵(gatelast)”工藝制作。圖1~圖2示出了現有技術的一種鰭式場效應晶體管的形成過程的剖面結構示意圖。首先,請參考圖1,提供半導體襯底100,所述半導體襯底100上具有若干凸起的鰭部101;然后,在相鄰鰭部101之間的半導體襯底100上形成隔離結構102,所述隔離結構102的頂部表面低于所述鰭部101的頂部表面;接著,形成覆蓋所述鰭部101和隔離結構102上的犧牲層103。在后柵(Gate-last)工藝中,所述的犧牲層103后續用于形成偽柵。由于所述隔離結構102的頂表面低于所述鰭部101的頂表面,相鄰鰭部101之間具有凹槽,在形成犧牲層103時,會使得隔離結構102上方的犧牲層的表面低于鰭部101上方的犧牲層的表面,造成犧牲層103表面凹凸不平,柵犧牲層103的厚度均勻性較差,不利于光刻中對焦深的控制,影響后續制造工藝。而為了解決該問題,現有通常會對形成的犧牲層103進行平坦化工藝,參考圖2,采用化學機械研磨(CMP)工藝拋光所述犧牲層103(如圖1所示),形成偽柵材料層104,形成的偽柵材料層104的表面比較平整,厚度的均勻性較好。后續通過刻蝕偽柵材料層104,形成橫跨鰭部101的側壁和頂部表面的偽柵。但是,現有化學機械研磨所述犧牲層103的過程中,難以控制拋光后的形成偽柵材料層104的厚度,使得偽柵材料層104的厚度具有不確定性,通過刻蝕偽柵材料層104形成的偽柵的厚度也具有不確定性,造成后續偽柵的去除深度和金屬柵的填充深度具有不確定性。其他有關鰭式場效應晶體管的形成方法,還可以參考公開號為US2011/0147812A1的美國專利申請。
技術實現要素:本發明解決的問題是精確控制鰭式場效應晶體管的偽柵的高度。為解決上述問題,本發明技術方案提供了一種鰭式場效應晶體管的形成方法,包括:提供半導體襯底,所述半導體襯底上具有若干分立的鰭部,相鄰鰭部之間具有隔離結構,所述隔離結構的表面低于鰭部的頂部表面;形成覆蓋所述鰭部以及隔離結構的犧牲層;對所述犧牲層進行離子注入,在所述犧牲層中形成離子摻雜層;采用化學機械研磨工藝平坦化所述犧牲層,以離子摻雜層作為停止層;刻蝕剩余的犧牲層,形成橫跨所述鰭部頂部和側壁表面的偽柵。可選的,所述犧牲層的材料為多晶硅或無定形硅。可選的,所述犧牲層的厚度大于等于600納米。可選的,所述犧牲層的材料為多晶硅時,所述離子注入的雜質離子為鍺離子、硅離子和碳離子中的一種,形成的離子摻雜層為非晶層,化學機械研磨所述犧牲層時,當檢測到研磨的速率發生變化時,停止研磨的進行。可選的,化學機械研磨所述犧牲層時,當檢測到研磨速率從一定的速率逐漸增大,達到最大值后再逐漸減小時,停止研磨的進行。可選的,所述犧牲層的材料為多晶硅或無定形硅時,所述離子注入的雜質離子為氧離子、氮離子、砷離子、硼離子和銻離子中的一種,化學機械研磨所述犧牲層時,當檢測到研磨液中雜質離子的濃度變化時,停止研磨的進行。可選的,化學機械研磨所述犧牲層時,當檢測到研磨液中的雜質離子的濃度先逐漸增大,達到最大值后再逐漸減小時,停止研磨的進行。可選的,所述離子注入的能量為1~20Kev,劑量大于等于1E15/cm2可選的,在所述犧牲層表面形成填充材料層,以填充犧牲層表面形成的凹陷,對所述犧牲層和填充材料層進行離子注入,在犧牲層中形成離子摻雜層。可選的,所述犧牲層的厚度為30~200納米。可選的,所述離子注入的雜質離子為鍺離子、硅離子、碳離子、氧離子、氮離子、砷離子、硼離子或銻離子,所述離子注入的能量為1~20Kev,劑量大于等于1E15/cm2。可選的,所述填充材料層為無定形碳。可選的,所述填充材料層的厚度為200~400納米。可選的,所述填充材料層的形成工藝為可流動性化學氣相沉積。可選的,所述化學機械研磨工藝采用的研磨液的主體成分為膠體氧化硅,稀釋劑為氫氧化鈉,膠體氧化硅的質量百分含量為10%~20%,研磨液的PH值為10~13。可選的,還包括:形成覆蓋所述鰭部和偽柵的介質層;平坦化所述介質層,暴露出偽柵的頂部表面;去除所述偽柵,形成凹槽;在凹槽中填充滿金屬,形成金屬柵極。可選的,在凹槽中填充金屬之前,在凹槽的側壁和底部表面形成高K柵介質層,在高K柵介質層上形成功能層。可選的,在所述金屬柵極兩側的鰭部內形成鰭式場效應管的源/漏區。可選的,所述源/漏區為嵌入式源漏區。與現有技術相比,本發明技術方案具有以下優點:在形成覆蓋所述鰭部以及隔離結構的犧牲層后,對所述犧牲層進行離子注入,在所述犧牲層中形成離子摻雜層,當采用化學機械研磨工藝平坦化所述犧牲層時,以離子摻雜層作為停止層,然后刻蝕剩余的犧牲層,形成橫跨所述鰭部頂部和側壁表面的偽柵。由于離子摻雜層是通過注入工藝形成的,注入工藝可以較為精確的控制在犧牲層中形成的離子摻雜層的位置,當以犧牲層中的離子摻雜層作為研磨的停止層時,在研磨犧牲層的過程中,即使研磨速率會發生變化,剩余的犧牲層的厚度也能較精確的控制,使得刻蝕剩余的犧牲層形成的偽柵的高度也比較精確。進一步,所述犧牲層的材料為多晶硅,進行離子注入時注入的雜質離子為鍺離子、硅離子或碳離子,使得注入離子位置對應的多晶硅非晶化,形成的離子摻雜層為非晶層,多晶硅被非晶化后形成的非晶層的熔點、密度和硬度都會明顯低于多晶硅,由于非晶層與多晶硅層不同的物理特性,在進行化學機械研磨時,多晶硅的研磨速率會小于非晶層的研磨速率,由于形成的非晶層是位于犧牲層中,當從犧牲層表面向下研磨時,研磨到非晶層時的研磨速率會發生明顯變化,因此通過檢測研磨過程中研磨的速率變化,即可判斷是否研磨到非晶層,從而停止研磨的進行,以便較為精確的控制剩余的犧牲層的厚度。進一步,當所述犧牲層的材料為多晶硅或無定形硅時,所述離子注入的雜質離子為氧離子、氮離子、砷離子、硼離子或銻離子一種,并且所述摻雜離子與研磨液的成分和犧牲層的材料成分不相同,形成的離子摻雜區中含有其中某一種摻雜離子(比如:硼離子),離子摻雜層是位于犧牲層中,從犧牲層表面向下研磨,當研磨到離子摻雜層時,研磨液中某種雜質離子(比如:硼離子)的濃度會從無到有,并逐漸增大,因此當檢測到研磨液中雜質離子的濃度變化時,停止研磨的進行。進一步,所述化學機械研磨工藝采用的研磨液的主體成分為膠體氧化硅,稀釋劑為氫氧化鈉,膠體氧化硅的質量百分含量為10%~20%,研磨液的PH值為10~13,減小對研磨過程中研磨速率的影響或者研磨液中雜質離子濃度的影響,有利于通過研磨速率的變化或雜質離子濃度的變化來判定研磨終點,提高研磨的效率和研磨終點判斷的準確性。附圖說明圖1~圖2是現有技術鰭式場效應晶體管的形成過程的剖面結構示意圖;圖3~圖6為本發明第一實施例鰭式場效應晶體管的形成過程的剖面結構示意圖;圖7~圖10為本發明第二實施例鰭式場效應晶體管的形成過程的剖面結構示意圖。具體實施方式發明人在采用現有技術在制作鰭式場效應晶體管過程中發現,當采用化學機械研磨工藝平坦化犧牲層,由于犧牲層表面凹凸不平,會使得研磨過程中,化學機械研磨的研磨速率不一樣,并且研磨過程中不存在研磨停止層,當通過控制研磨時間終止研磨進行時,使得剩余的犧牲層(或偽柵材料層)的厚度具有不確定性,剩余的犧牲層的厚度與目標值的偏差較大,當刻蝕剩余的犧牲層形成偽柵時,使得偽柵的高度的精度大幅減低,最終使得在去除偽柵形成凹槽,并在凹槽中形成的金屬柵極的高度的精度也大幅降低,不利于器件穩定性的提高和工藝的管控。基于上述研究,發明人提出一種鰭式場效應晶體管的形成方法,在形成覆蓋所述鰭部以及隔離結構的犧牲層后,對所述犧牲層進行離子注入,在所述犧牲層中形成離子摻雜層,當采用化學機械研磨工藝平坦化所述犧牲層時,以離子摻雜層作為停止層,然后刻蝕剩余的犧牲層,形成橫跨所述鰭部頂部和側壁表面的偽柵。由于離子摻雜層是通過注入工藝形成的,注入工藝可以較為精確的控制在犧牲層中形成的離子摻雜層的位置,當以犧牲層中的離子摻雜層作為研磨的停止層時,若研磨犧牲層的過程中,即使研磨速率會發生變化,剩余的犧牲層的厚度也能較精確的控制,使得刻蝕剩余的犧牲層形成的偽柵的高度也比較精確。為使本發明的上述目的、特征和優點能夠更加明顯易懂,下面結合附圖對本發明的具體實施方式做詳細的說明。在詳述本發明實施例時,為便于說明,示意圖會不依一般比例作局部放大,而且所述示意圖只是示例,其在此不應限制本發明的保護范圍。此外,在實際制作中應包含長度、寬度及深度的三維空間尺寸。第一實施例圖3~圖6為本發明第一實施例鰭式場效應晶體管的形成過程的剖面結構示意圖。首先,參考圖3,提供半導體襯底300,所述半導體襯底300上具有若干分立的鰭部301,相鄰鰭部301之間的半導體襯底301上具有隔離結構302,所述隔離結構302的表面低于鰭部301的頂部表面。所述半導體襯底300可以是硅或者絕緣體上硅(SOI),所述半導體襯底300也可以是鍺、鍺硅、砷化鎵或者絕緣體上鍺。本實施例中,所述鰭部301通過刻蝕半導體襯底300形成,在本發明的其他實施例中,所述鰭部301通過外延工藝形成。所述隔離結構302用于電學隔離相鄰的鰭部301,所述隔離結構302的材料為氧化硅、氮化硅或氮氧化硅。隔離結構302形成的具體過程為:首先形成覆蓋所述半導體襯底300和鰭部301的隔離材料層;然后采用化學機械研磨工藝平坦化所述隔離材料層,以鰭部301的頂部表面為停止層;接著刻蝕所述剩余的隔離材料層,形成隔離結構302,所述隔離結構302的表面低于鰭部301的頂部表面。在形成隔離結構302,相連鰭部301之間會具有一個凹槽,以便后續形成橫跨所述鰭部301的頂部表面和暴露的側壁的偽柵或柵極結構。接著,請參考圖4,形成覆蓋所述鰭部301以及隔離結構302的犧牲層303。所述犧牲層303后續用于形成鰭式場效應管的偽柵,所述犧牲層303的形成工藝為化學氣相沉積(CVD),由于隔離結構302表面低于鰭部301頂部表面,相鄰的鰭部301之間具有凹槽,因此在沉積形成犧牲層303時,鰭部301上方形成的犧牲層303表面會高于隔離結構302上方形成的犧牲層303的表面,使最終形成犧牲層303的表面會凹凸不平,犧牲層303表面的平整度較差。在本實施例中,所述犧牲層303的厚度大于等于600納米,通過形成較厚的犧牲層303,以減小隔離結構302表面和鰭部301頂部表面之間的高度差異對形成的犧牲層303表面平整度的影響,減小隔離結構302上方的犧牲層303的表面高度與鰭部301上方的犧牲層303表面的高度之間的差異,后續對犧牲層303進行離子注入,在犧牲層303中形成離子摻雜層時,使得離子摻雜層在犧牲層303中的分布的均勻性受到犧牲層303表面的平整度的影響最小,以使離子摻雜層能較準確的作為平坦化犧牲層303時的停止層。需要說明的是,本是實施例中,所述犧牲層303的厚度是指鰭部301頂部表面上方的犧牲層303的厚度。所述犧牲層303的材料為多晶硅或無定形硅,本實施例中,所述犧牲層303的材料為多晶硅。接著,請參考圖5,對所述犧牲層303進行離子注入,在所述犧牲層303中形成離子摻雜層304。本實施例中所述犧牲層303的材料為多晶硅,進行離子注入時注入的雜質離子為鍺離子、硅離子或碳離子,使得注入離子位置對應的多晶硅非晶化,形成的離子摻雜層304為非晶層,多晶硅被非晶化后形成的非晶層的熔點、密度和硬度都會明顯低于多晶硅,由于非晶層與多晶硅層不同的物理特性,在進行化學機械研磨時,多晶硅的研磨速率會小于非晶層的研磨速率,本實施例中,由于形成的非晶層(離子摻雜層304)是位于犧牲層303中,當從犧牲層303表面向下研磨時,研磨到非晶層時的研磨速率會發生明顯變化,因此通過檢測研磨過程中研磨的速率變化,即可判斷是否研磨到非晶層(離子摻雜層304),從而停止研磨的進行,以便較為精確的控制剩余的犧牲層303的厚度。在本發明的其他實施例中,當所述犧牲層303的材料為多晶硅或無定形硅時,所述離子注入的雜質離子為氧離子、氮離子、砷離子、硼離子或銻離子一種,并且所述摻雜離子與研磨液的成分和犧牲層的材料成分要不相同,形成的離子摻雜區304中含有其中某一種摻雜離子(比如:硼離子),離子摻雜層304是位于犧牲層303中,從犧牲層303表面向下研磨,當研磨到離子摻雜層304時,研磨液中某種雜質離子(比如:硼離子)的濃度會從無到有,并逐漸增大,因此當檢測到研磨液中雜質離子的濃度變化時,停止研磨的進行。所述離子注入的能量為1~20Kev,劑量大于等于1E15/cm2,通過控制離子注入的能量,能較為準確的犧牲層303中形成的控制離子摻雜層304的深度,當離子摻雜層304的深度確定后,對犧牲層303進行平坦化時,剩余的犧牲層的厚度也就確定了,通過控制離子注入的劑量,使得離子摻雜層304中雜質離子的濃度大于等于10E18/cm3,以提高非晶化的程度或者研磨時剩余的研磨液中的待檢測雜質離子的濃度,當研磨到離子摻雜層304時,從而提高檢測研磨速率變化或者研磨液中雜質離子的濃度變化的靈敏度,提高檢測的研磨終點判斷的精度。在具體的實施例中,所述離子注入的能量和劑量根據不同的待注入雜質離子作出選擇,使不同的雜質離子注入后形成的離子摻雜層304均能達到作為研磨停止層的效果,并且利于離子摻雜層304的深度控制,當注入的雜質離子為鍺離子、硅離子或碳離子時,離子注入的能量為5~20Kev,劑量大于等于1E15/cm2,當注入的雜質離子為氧離子、氮離子、砷離子、硼離子或銻離子時,離子注入的能量為1~20Kev,劑量大于等于1E15/cm2。接著,參考圖6,采用化學機械研磨工藝平坦化所述犧牲層303,以離子摻雜層304作為停止層。本實施例中,所述離子摻雜層304為非晶層,采用化學機械研磨工藝平坦化所述犧牲層303時,當檢測到研磨速率從一定的速率逐漸增大,達到最大值后再逐漸減小時,停止研磨的進行,即相對于化學機械研磨時,以離子摻雜層304作為停止層。本實施例中進行化學機械研磨所采用的研磨設備能實時檢測研磨測速率,并將檢測結果實時反饋給研磨設備的主控制單元,主控制單元能根據研磨速率的變化發出停止研磨的信號,從而停止研磨的進行。在本發明的其他實施例中,所述離子摻雜層304為摻雜有雜質離子的多晶硅或無定形硅時,采用化學機械研磨工藝平坦化所述犧牲層303時,當檢測到研磨液中的某一雜質離子的濃度先逐漸增大,達到最大值后再逐漸減小時,停止研磨的進行,即相對于化學機械研磨時,以離子摻雜層304作為停止層。本實施例中進行化學機械研磨所采用的研磨設備具有光譜檢測單元,光譜檢測單元通過檢測研磨液中某一雜質離子的反射光譜的變化來確定研磨液中某一雜質離子濃度。所述化學機械研磨工藝采用的研磨液的主體成分為膠體氧化硅,稀釋劑為氫氧化鈉,膠體氧化硅的質量百分含量為10%~20%,研磨液的PH值為10~13,減小對研磨過程中研磨速率的影響或者研磨液中雜質離子濃度的影響,有利于通過研磨速率的變化或雜質離子濃度的變化來判定研磨終點,提高研磨的效率和研磨終點判斷的準確性。在進行研磨時,所述離子摻雜層304能被全部研磨或部分剩余。最后,在平坦化所述犧牲層303后,刻蝕剩余的犧牲層303,形成橫跨所述鰭部頂部和側壁表面的偽柵(圖中未示出);還包括:形成覆蓋所述鰭部301和偽柵的介質層(圖中未示出);平坦化所述介質層,暴露出偽柵的頂部表面;去除所述偽柵,形成凹槽(圖中未示出);在凹槽中填充滿金屬,形成金屬柵極(圖中未示出);在所述金屬柵極兩側的鰭部內形成鰭式場效應管的源/漏區。在凹槽中填充金屬之前,在凹槽的側壁和底部表面形成高K柵介質層,在高K柵介質層上形成功能層,調節鰭式場效應管的功函數。所述源/漏區為嵌入式源漏區,以提高鰭式場效應管的性能。第二實施例請參考圖7,提供半導體襯底300,所述半導體襯底300上具有若干分立的鰭部301,相鄰鰭部301之間的半導體襯底301上具有隔離結構302,所述隔離結構302的表面低于鰭部301的頂部表面;形成覆蓋所述鰭部301以及隔離結構302的犧牲層303。本實施例中,所述犧牲層303的厚度為30~200納米,由于形成的犧牲層303的厚度較薄,采用化學氣相沉積工藝形成犧牲層303時,隔離結構302表面和鰭部301頂部表面之間的高度差異對形成的犧牲層303表面平整度的影響較大,使得隔離結構302上方的犧牲層的表面高度與鰭部301上方的犧牲層表面的高度之間的差異較大,犧牲層303的表面的凹凸不平(凹陷)比較明顯,后續對犧牲層303進行離子注入,在犧牲層303中形成離子摻雜層時,使得離子摻雜層在犧牲層303中的分布的受到犧牲層303表面的平整度的影響較大,后續進行化學機械研磨時,不利于研磨停止時機的判斷。接著,請參考圖8,在所述犧牲層303表面形成填充材料層307,以填充犧牲層303表面形成的凹陷。所述填充材料層307為無定形碳,填充材料層303的形成工藝為可流動性化學氣相沉積(FCVD),當形成晶粒較小的無定形碳時,無定形碳具有較好的填充凹陷的能力,并使得形成的填充材料層307具有較平坦的表面。所述填充材料層307的厚度為200~400納米,后續進行離子注入時,填充材料層307對離子注入的影響較小,使犧牲層303中形成的離子摻雜層的分布較為均勻。然后,請參考圖9,對所述犧牲層303和填充材料層307進行離子注入,在犧牲層303中形成離子摻雜層404。所述離子注入的雜質離子為鍺離子、硅離子、碳離子、氧離子、氮離子、砷離子、硼離子和銻離子中的一種。由于存在填充材料層307,本實施例中,離子注入的能量要大于第一實施例中離子注入的能量,以在犧牲層303中形成離子摻雜層404,所述離子注入的能量為1~40Kev,劑量大于等于1E15/cm2。本實施例中,當所述犧牲層303的材料為多晶硅,進行離子注入時注入的雜質離子為鍺離子、硅離子或碳離子,使得注入離子位置對應的多晶硅非晶化,形成的離子摻雜層304為非晶層,后續研磨填充材料層307和犧牲層303時,當研磨速率發生變化時,即可停止研磨的進行。在本發明的其他實施例中,當所述犧牲層303的材料為多晶硅或無定形硅時,所述離子注入的雜質離子為氧離子、氮離子、砷離子、硼離子或銻離子一種,并且所述摻雜離子與研磨液的成分和犧牲層303和填充材料層307的材料成分均不相同,形成的離子摻雜區304中含有其中某一種摻雜離子(比如:硼離子),離子摻雜層304是位于犧牲層303中,從填充材料層307表面向下研磨,當研磨到離子摻雜層304時,研磨液中某種雜質離子(比如:硼離子)的濃度會從無到有,并逐漸增大,因此當檢測到研磨液中雜質離子的濃度變化時,即可停止研磨的進行。在具體的實施例中,所述離子注入的能量和劑量根據不同的待注入雜質離子作出選擇,使不同的雜質離子注入后形成的離子摻雜層304均能達到作為研磨停止層的效果,并且利于離子摻雜層304的深度控制,當注入的雜質離子為鍺離子、硅離子或碳離子時,離子注入的能量為5~40Kev,劑量大于等于1E15/cm2,當注入的雜質離子為氧離子、氮離子、砷離子、硼離子或銻離子時,離子注入的能量為1~40Kev,劑量大于等于1E15/cm2。參考圖10,采用化學機械研磨工藝平坦化所述填充材料層307(如圖9所示)和犧牲層303,以離子摻雜層304作為停止層。當離子摻雜層304為非晶層,由于本實施例的犧牲層303表面會具有填充材料層307,因此對填充材料層307和犧牲層303堆疊結構進行研磨時,研磨速度首先保持一定的速度,當研磨到填充材料層307和犧牲層303交接處時,研磨速率會逐漸減小,當研磨到離子摻雜層304區時,研磨速率會逐漸增大并且變化速率的變化幅度較大,當研磨速率達到最大值后再逐漸減小時,停止研磨的進行。當所述離子摻雜層304為摻雜有雜質離子的多晶硅或無定形硅時,其研磨過程請參考第一實施例。在平坦化所述犧牲層303后,刻蝕剩余的犧牲層303,形成橫跨所述鰭部頂部和側壁表面的偽柵(圖中未示出);還包括:形成覆蓋所述鰭部301和偽柵的介質層(圖中未示出);平坦化所述介質層,暴露出偽柵的頂部表面;去除所述偽柵,形成凹槽(圖中未示出);在凹槽中填充滿金屬,形成金屬柵極(圖中未示出);在所述金屬柵極兩側的鰭部內形成鰭式場效應管的源/漏區。綜上,本發明實施例鰭式場效應管的形成方法,離子摻雜層是通過注入工藝形成的,注入工藝可以較為精確的控制在犧牲層中形成的離子摻雜層的位置,當以犧牲層中的離子摻雜層作為研磨的停止層時,若研磨犧牲層的過程中,即使研磨速率會發生變化,剩余的犧牲層的厚度也能較精確的控制,使得刻蝕剩余的犧牲層形成的偽柵的高度也比較精確。本發明雖然已以較佳實施例公開如上,但其并不是用來限定本發明,任何本領域技術人員在不脫離本發明的精神和范圍內,都可以利用上述揭示的方法和技術內容對本發明技術方案做出可能的變動和修改,因此,凡是未脫離本發明技術方案的內容,依據本發明的技術實質對以上實施例所作的任何簡單修改、等同變化及修飾,均屬于本發明技術方案的保護范圍。