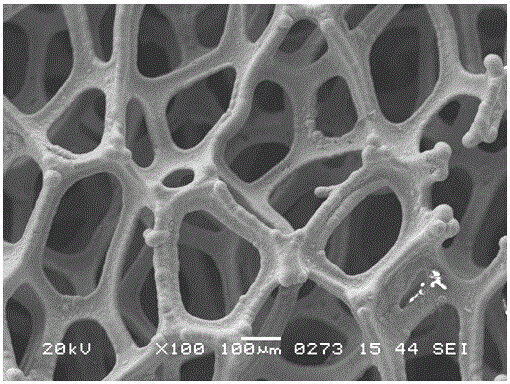
本發明屬于電化學
技術領域:
,尤其涉及到一種制備多孔鋁過程中具有均勻鍍層且無裂紋產生的方法。
背景技術:
:近年來,全球鋰離子電池產業規模保持高速增長,2015年,全球鋰離子電池總體產量達到100.75Gwh,動力電池占比28.26%,隨著動力電池的高速發展,人們對鋰離子電池容量提出了更高的需求。根據相關研究報道,通過增大集流體的表面積可以增大活性物質的量并且使得活性物質更加有效的利用,而多孔鋁具有大的比表面積及大的孔隙率,作為集流體應用到鋰離子電池中可以有效增大鋰離子電池的容量,從而有助于增加電動汽車行駛里程,對電動汽車行業具有很大的推動作用。常規方法制備多孔鋁的流程為:以具有均勻孔徑的海綿為基體,經過導電化處理,用電沉積方法制備多孔鋁。在制備過程中若關鍵技術處理不好,其獲得的多孔鋁鍍層厚度不均勻,并且海綿骨架尖端處存在裂紋,影響使用性能。多孔鋁鍍層沉積不均勻及產生裂紋是電沉積法制備多孔鋁存在的主要問題。技術實現要素:為解決上述問題,本發明提供了一種制備多孔鋁過程中具有均勻鍍層且無裂紋產生的方法,該方法通過改進聚氨酯海綿的預處理、導電化處理以及電沉積來獲得具有均勻鍍層且無裂紋的多孔鋁,通過控制海綿骨架的尖端圓角半徑≥2.0μm以及使用環形鋁板為陽極,保證獲得具有均勻鍍層且無裂紋存在的多孔鋁,該多孔鋁可作為鋰離子電池尤其是電動汽車或者大功率儲能設備用鋰離子電池的正極集流體、催化劑的載體以及過濾材料等使用。為實現上述發明目的,本發明采用如下技術方案:一種制備多孔鋁過程中具有均勻鍍層且無裂紋產生的方法,該方法經歷聚氨酯海綿的預處理、導電化處理和電沉積三個過程,其中聚氨酯海綿的孔徑要求控制在0.35~1.0mm,厚度為0.5~2.0mm,導電化處理過程中使用到導電膠,電沉積過程中使用到電溶液,電溶液由無水AlCl3和1-乙基-3-甲基氯化咪唑EMIC配置而成,其特征是:預處理:預處理液采用強氧化性的酸性溶液,所述酸性溶液是1.0~2.0g/L的KMnO4與0.3~1.0ml/L的H2SO4的混合液;用酒精清洗聚氨酯海綿5min以除去其表面雜質,在20~40℃條件下將聚氨酯海綿浸泡在所述酸性溶液中并超聲波振動3~10min,之后取出并得到海綿骨架,將海綿骨架放入40~60℃的干燥箱中干燥0.5~1.5h,經預處理后的海綿骨架要求其尖端圓角半徑≥2.0μm;導電化處理:將海綿骨架浸入到導電膠中,通過超聲波對海綿骨架振動10~20分鐘,之后取出海綿骨架并擠出導電膠,然后加熱海綿骨架至80~90℃并固化30~60min;電沉積:將導電化處理的海綿骨架與直流電源的負極連接形成陰極,將環形鋁板與直流電源的正極連接形成陽極,此時環形鋁板的面積與海綿骨架的面積比要大于2:1,即環形鋁板的面積:海綿骨架的面積﹥2:1,之后將所述陰極置于所述陽極的環形中并一同放入盛有電溶液的容器中,接通直流電源,直流電源的電壓小于4V而電流密度控制在30~40mA/cm2,在20~30℃條件下通過電磁攪拌器攪拌80~120min,電磁攪拌器的攪拌速度要小于400r/min,攪拌過程中向容器內通入氬氣或是氮氣,電沉積后即可制備出鍍層厚度差異<30%的多孔鋁。由于采用如上所述技術方案,本發明產生如下積極效果:1、本發明通過預處理和導電化處理過程使得聚氨酯海綿的尖端角處得到鈍化,從而利于導電材料在其尖端角的鍍覆,確保導電材料均勻涂覆在海綿骨架表面和尖端角處,通過預處理和導電化處理過程可以有效抑制裂紋的產生。2、采用環形鋁板為陽極對海綿骨架進行電沉積,從而獲得具有均勻鍍層及無裂紋存在的多孔鋁。附圖說明圖1是本發明的制備過程簡圖。圖2是本發明多孔鋁的三維網狀掃描電鏡圖。圖3是聚氨酯海綿未經預處理但經過電沉積后多孔鋁截面金相圖。圖4是聚氨酯海綿經本發明后的多孔鋁截面金相圖。圖1中:1-直流電源;2-環形鋁板;3-海綿;4-電磁攪拌器;5-電溶液;6-容器。具體實施方式本發明是一種制備多孔鋁過程中具有均勻鍍層且無裂紋產生的方法,該方法經歷聚氨酯海綿的預處理、導電化處理及電沉積三個過程,通過預處理和導電化處理過程使得聚氨酯海綿的尖端角處得到鈍化,從而利于導電材料在尖端角的鍍覆,確保導電材料均勻涂覆在海綿骨架表面和尖端角處,可以有效抑制裂紋的產生,其中聚氨酯海綿的孔徑要求控制在0.35~1.0mm,厚度為0.5~2mm。導電化處理過程中使用到導電膠,電沉積過程中使用到電溶液,電溶液由無水AlCl3和1-乙基-3-甲基氯化咪唑EMIC配置而成,該配置比例是電沉積的常用比例,導電膠化工市場可購。本發明的預處理方法是:預處理液采用強氧化性的酸性溶液,所述酸性溶液是1.0~2.0g/L的KMnO4與0.3~1.0ml/L的H2SO4的混合液。用酒精清洗聚氨酯海綿5min以除去其表面雜質,在20~40℃條件下將聚氨酯海綿浸泡在所述酸性溶液中并超聲波振動3~10min,超聲波振動可以保證海綿尖端圓角變得更大,之后取出并得到海綿骨架,將海綿骨架放入40~60℃的干燥箱中干燥0.5~1.5h,經預處理后的海綿骨架要求其尖端圓角半徑≥2.0μm,若海綿骨架的尖端圓角半徑小于或遠小于2.0μm,容易在尖端圓角處造成裂紋,也造成導電材料無法均勻鍍覆在尖端圓角處,導致尖端圓角處不導電,從而使得后續電沉積時無法鍍覆鋁鍍層。預處理制備出的海綿骨架其尖端圓角處變的鈍化,尖端圓角的半徑越大越利于導電材料的鍍覆,從而有效抑制裂紋的產生。本發明的導電化處理方法是:將海綿骨架浸入到導電膠中,通過超聲波對海綿骨架振動10~20分鐘,超聲波振動可以保證所述海綿骨架的表面覆蓋一層導電膠并使其完全導電化,之后取出海綿骨架并擠出導電膠,然后加熱海綿骨架至80~90℃并固化30~60min,在保溫時間段中海綿骨架得到固化并確保其全部實現導電化。本發明的電沉積方法是:結合圖1,將導電化處理的海綿骨架3與直流電源1的負極連接形成陰極,將環形鋁板2與直流電源1的正極連接形成陽極,此時環形鋁板2的面積與海綿骨架3的面積比要大于2:1,即環形鋁板的面積:海綿骨架的面積﹥2:1,之后將所述陰極置于所述陽極的環形中并一同放入盛有電溶液5的容器6中,將所述陰極置于所述陽極的環形中這一點非常重要,它對制備出的多孔鋁具備三維網狀結構并均勻鍍層且無裂紋產生具有重要意義,關于此意義通過圖2即可看出。接通直流電源1,直流電源1的電壓小于4V而電流密度控制在30~40mA/cm2,在20~30℃條件下通過電磁攪拌器4攪拌80~120min,電磁攪拌器4的攪拌速度要小于400r/min,攪拌過程中向容器6內通入氬氣或是氮氣,電沉積后即可制備出鍍層厚度差異<30%的多孔鋁,該多孔鋁的三維網狀結構掃描電鏡圖見圖2所示。上述預處理和電沉積是本發明的關鍵步驟,也是區別
背景技術:
所在,通過預處理和電沉積而得到的多孔鋁截面具有本質不同,從圖3和圖4可以得到充分驗證。圖3是聚氨酯海綿未經預處理但經過電沉積后的多孔鋁截面金相圖,從圖3中的可以明顯看出,在A和B處存在貫穿裂紋和微裂紋。圖4是聚氨酯海綿經本發明后多孔鋁截面金相圖,從圖4中的可以明顯看出其尖端圓角處無裂紋存在。下面就具體的實施例進行說明,需要強調的是:下述實施例只用來說明本發明的個案但不用來限制本發明的技術范圍,未述部分以技術方案為準。預處理:用酒精清洗聚氨酯海綿5min以除去其表面雜質,采用1.2g/L的KMnO4和0.5ml/L的H2SO4混合溶液對聚氨酯海綿進行處理,溫度為20℃并超聲波振動,處理時間5min,之后放入50℃的干燥箱中干燥1h以充分的除去水分。將海綿骨架浸入導電膠中,反復擠壓至海綿骨架中全部浸入了導電膠,超聲波振動10min,通過超聲波對海綿骨架振動10~20分鐘,在85℃下固化60min。以環形鋁板為陽極,以長×寬×厚=10mm×10mm×1mm的海綿骨架為陰極,環形鋁板與海綿骨架的面積比達到5:1,直流電源的電壓設定為3.5V、電流控制在35mA并在20℃和200r/min的攪拌速度下通入氬氣作為保護氣體進行恒電流沉積。實施例和三個比較例的具體參數見下表,其中三個比較例是按常規處理所制。在上表中:√號為本發明的方法,×號為常規處理方法。試驗及評價結果見下表。海綿骨架尖端圓角半徑R鍍層均勻性評價有無裂紋評價實施例1≥2.0μmAA比較例1<2.0μmBC比較例2≥2.0μmCA比較例3<2.0μmCC評價標準:1)鍍層均勻性評價:不同位置鍍層厚度差在30%以內的評價為A且結果為優秀,厚度差在30~50%之間的評價為B且結果為一般,厚度差大于50%的定為C其結果為差。2)有無裂紋評價:海綿骨架截面中裂紋從鍍層內部延續到鍍層外部稱為貫穿裂紋如圖3中A所示,鍍層中裂紋沒有延續到鍍層內外稱為局部裂紋如圖3中B所示。裂紋比例統計方法為存在裂紋或局部裂紋的三角尖端數量占總體三角尖端數量的比例。將鍍層中不存在貫穿裂紋,骨架中只存在小于10%局部裂紋的評價為A且結果為優秀,存在小于10%貫穿裂紋或大于10%且小于50%的局部裂紋評價為B且結果為一般,存在大于10%貫穿裂紋或大于50%局部裂紋的評價為C且結果為差。通過上述兩表的比較和圖2可以看出:采用本發明的方法,制備的多孔鋁具有鍍層厚度均勻、結構體中無裂紋之現象。以上僅是本發明的具體應用范例,對本發明的保護范圍不構成任何限制。凡采用等同變換或者等效替換而形成的技術方案,均落在本發明權利保護范圍之內。當前第1頁1 2 3