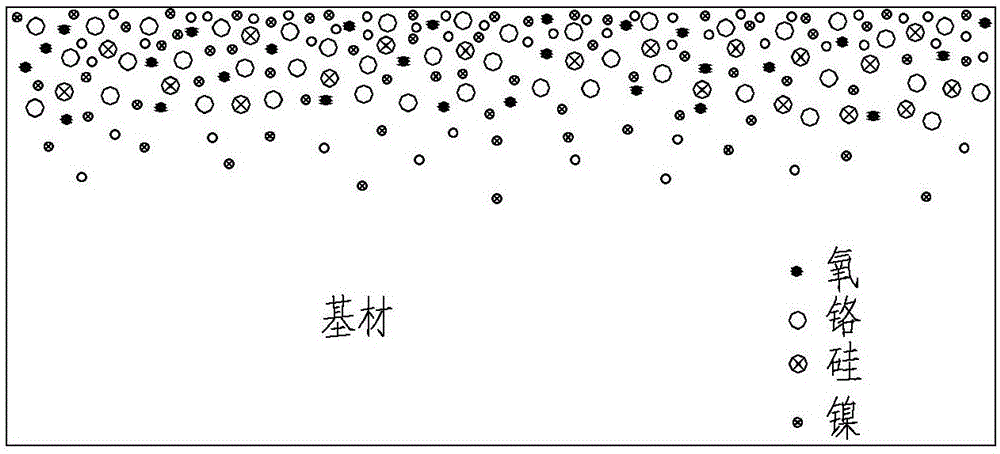
本發明涉及煉油、石化、化工、石油制品加工設備領域,尤其涉及一種應用在煉油、石化、石油加工、化工等高腐蝕環境中的基于不銹鋼表面的抗結焦納米材料及其制備方法。
背景技術:
:石油化工管道、換熱器、塔內件填料、鍋爐、爐管等在高溫下的結焦、結垢和堵塞問題一直影響企業的正常生產經營。目前關于爐管的抗結焦研究比較多,而在其它領域的抗結焦研究比較少,如煉油換熱器、塔內件填料受到高溫影響的結焦、結垢對換熱、分離效率影響非常大,時間越長結焦、結垢越嚴重,積累到一定量后將造成嚴重事故而不得不停車檢修、更換結焦的塔內件填料或者清洗結焦、結垢的換熱器;管道長時間結垢影響泵的效率和增加泵的負荷,特別是結焦塊過多后脫落而堵塞下游裝備。因此,研究針對于煉油、化工抗結焦的基于不銹鋼表面的納米材料具有獨特的意義。目前抗結焦的方法很多,最主要的做法是研究設備的表面材料,針對不同應用環境制作膜層新材料,其主要的有:1、針對高溫爐管等表面滲鋁的情況,加入二氧化硅、陶瓷等等抗結焦層;2、在重質油等物料組分中加入抗結焦抑制劑;3、對容易結焦的部分進行表面噴涂抗結焦涂料;4、將抑制劑和涂層進行結合抗結焦。抗結焦涂料是比較常用的一種抗結焦方法,如中國專利申請CN105111854A、CN103421531A、CN102585571A等,均通過各類涂料涂層來增加抗結焦效果。在重質油等原料中加入抗結焦抑制劑也是目前應用很多的一種抗結焦方法,特別是在裂解爐的爐管中使用;如中國專利申請CN102251225A、CN103421531A等通過在原料流體中加入抑制劑抗結焦。對爐管、換熱器、鍋爐等易結焦部位的表面進行處理來增加抗結焦效果是一種使用效果較好的常用抗結焦方法,如中國專利申請CN103861662A通過在金屬表層增加鋁來達到抗結焦效果,中國專利申請CN105200338A通過在金屬表層增加Mn和Si來增加抗結焦效果,中國專利申請CN101379362A通過加入各類稀有金屬元素來增加抗結焦效果。現有的抗結焦涂料效果雖好,但涂料與基材的結著力往往不夠,在高溫、流體流速高的環境中涂料易于脫落,從而顯著影響抗結焦效果,該方法目前主要用于靜置液體的裝置。涂層在復雜設備的內件幾乎無法涂層而限制了其的應用。而抗結焦抑制劑會對下游工藝或者最終成品帶來影響,其一般都是與其他抗結焦方式組合使用。因此,抑制劑和涂層的組合使用也是一種常用的抗結焦方法,多重抗結焦途徑的組合使用能最大程度的抑制結焦,如中國專利申請CN102251225A。因此,對不銹鋼件表面進行處理是目前研究最為廣泛的一種抗結焦技術,而各種不同的工藝帶來的抗結焦效果也不一樣,成本有高有低,目前通常是采用不停的更換、清洗等方式來抗結焦,對工藝造成了很大影響。技術實現要素:本發明的目的是提供一種基于不銹鋼表面的抗結焦納米材料,其由氧化鉻、氧化硅等金屬氧化物組成,能夠作用于各類不銹鋼基材,相比于常規不銹鋼基材的結焦量降低30%以上;該基于不銹鋼表面的抗結焦納米材料通過電化學處理后的表面更加光滑;該基于不銹鋼表面的抗結焦納米材料與基材鑲嵌結合,無明顯結合面;此外,所述抗結焦納米材料表面與基材熱膨脹系數相當,其長時間在高溫介質的反復變化不會與所述不銹鋼基材脫落;所述抗結焦納米材料的預處理、后處理等過程在常溫、常壓下進行,易于工業化及大型化不銹鋼設備的應用。用于實現上述目的的技術方案如下:本發明提供一種基于不銹鋼表面的抗結焦納米材料,按重量百分比計,所述納米結晶材料包含:碳0-3%,氧23-38%,鉻38-53%,鐵10-35%,鉬0-2%,鎳0-4%,硅3.5-5%,鈣0-1%,余量為雜質元素;優選地,所述納米結晶材料包含:碳0.71%,氧34.62%,鉻42.81%,鐵13.11%,鎳3.1%,硅4.73%,鈣0.92%,余量為雜質元素。本發明還提供一種所述抗結焦納米材料的制備方法,所述方法包括以下步驟:(1)使用氫氧化鈉溶液和含堿蝕添加劑的溶液對不銹鋼表面進行化學除油和堿蝕處理,后水洗;(2)將步驟(1)處理后的不銹鋼表面經氧化溶液進行氧化處理,后水洗;(3)將步驟(2)處理后的不銹鋼表面作為陰極浸泡在電解液中進行電解,后水洗;(4)將步驟(3)處理后的不銹鋼表面于溫度50-60℃、濕度60-70%下放置,后再于溫度35-40℃、濕度40-50%下放置,進行硬化處理。優選地,所述步驟(1)中,所述氫氧化鈉溶液和含堿蝕添加劑的溶液的溫度為80-85℃;優選地,所述氫氧化鈉溶液的濃度為6.5-8%;優選地,所述含堿蝕添加劑的溶液的濃度為0.3-0.5%;優選地,所述堿蝕添加劑為HDW-1050堿蝕添加劑;優選地,所述化學除油和堿蝕處理進行10-15分鐘;優選地,所述水洗是使用80-85℃的水,優選地,所述水洗時間為3-5分鐘。優選地,所述步驟(2)中,所述氧化溶液包含CrO3200-300g/L;優選地,所述氧化溶液的溫度為75-90℃;優選地,所述氧化溶液的pH為0.4-1.5;優選地,通過向所述氧化溶液中加入H2SO4溶液來調整氧化溶液的pH為0.4-1.5;優選地,所述H2SO4溶液的濃度為98%;優選地,所述氧化處理進行15-35分鐘;優選地,所述步驟(2)氧化后水洗,水洗是于25-40℃下循環水洗3-5分鐘;優選地,水的pH為>3;優選地,所述步驟(3)中,所述電解液包含CrO3100-150g/L、Na2SiO380-100g/L、納米氮化硅15-20g/L、納米碳化硅3-5g/L;優選地,所述電解液的溫度為40-52℃;優選地,所述電解液的pH為0.5-1.5;優選地,通過向所述電解液中加入H2SO4溶液來調整電解液的pH為0.5-1.5;優選地,所述H2SO4溶液的濃度為98%;優選地,進行所述電解的電流為直流電;優選地,所述電流的強度為42-4A/m2;優選地,所述電流強度初始為40-42A/m2,后電流強度按照i=3+30/t逐步減小至4A/m2,其中,所述i為電流強度,所述t為時間;優選地,所述電解時間為25-55分鐘;優選地,所述電解包括以初始為40-42A/m2的電流強度電解10-25分鐘,后在電解的同時經過14-18分鐘將所述電流強度按照i=3+30/t逐步減小至4A/m2;優選地,所述水洗是在25-40℃下循環水洗3-5分鐘;優選地,水的pH為>3。優選地,所述步驟(4)中,兩次放置進行硬化處理的時間分別是3-3.5小時和48-72小時。本發明所述的制備方法所制備的基于不銹鋼表面的抗結焦納米結晶材料。包括通過本發明所述制備方法所制備的抗結焦納米結晶材料的不銹鋼基材。為了使本發明的目的、技術特征及有益效果更加詳細,以下結合不銹鋼304、316L、317L及0Cr13,對本發明所述抗結焦納米材料進一步進行說明。本發明中,在不銹鋼表面所形成的抗結焦納米材料層與不銹鋼基材為嵌入式結合,該不銹鋼基材在表面由淺入深地形成蜂窩狀基材結構,在該蜂窩狀結構的空隙中填充嵌入了本發明所述的抗結焦納米材料,不銹鋼基材與納米材料無結合面,不銹鋼基材與納米材料的熱膨脹不會出現明顯的斷層,當接觸介質的溫度反復明顯波動變化的時候,這種嵌入式的結合方式使納米材料與不銹鋼基材不會出現膜層脫落的情況,納米材料的附著力遠超抗結焦涂料。具體而言,如圖1,空白區域為例如不銹鋼304基材,本發明所述的抗結焦納米材料與不銹鋼304基材的結合方式是表面密集、內層逐步稀疏,納米材料的氧化鉻、氧化硅表層與基材的嵌入結合如圖2。通過X射線光電子能譜分析該不銹鋼304基材與本發明所述納米材料結合的物質組成層,發現從最外的表層到內依次為氧化硅層、兩性氫氧化物層、氧化鉻層、基材層,層與層之間沒有明顯的間斷面,具體的組成與深度的趨勢見圖3,其中:氧化硅層:厚度1-150nm,此層的主要特點是為氧化硅、氧化鉻抗結焦結垢材質共存,其中三價鉻及六價鉻共存,其中的三價鉻為表面晶體骨架,六價鉻為填充,兩者共同維持了層面元素的穩定,增加了抗腐蝕能力;兩性氫氧化物層:厚度150-500nm,此層主要為氧化鉻、氫氧化鉻層;氧化物層:厚度500-900nm,此層主要為氧化鉻、鉻單質層,同時鐵單質層在此層的含量迅速提升至與所述304基材的含量相當;基材層:厚度≥900nm,此層為不銹鋼304基材的正常組成;結合圖1可以看出,基材層與表面的三層物質之前沒有明顯的界限,結合能力強。本發明所述抗結焦納米材料與不銹鋼基材結合力的測試:將基于不銹鋼表面的抗結焦納米材料實驗片加熱至設定的高溫后放于冷水急冷,反復進行上述實驗測試,觀測上述結合層的附著力。按GB/T5270-2005/ISO2819:1980標準對不銹鋼材質的納米表面結晶層進行熱震測試,試驗溫度以此提高,100℃、300℃、500℃、800℃、1000℃,表面未發現裂紋、膜層脫落情況,在高溫800℃、1000℃表面顏色改變,通過X射線光電子能譜測試,表面納米材料層組成不變,在1000℃高溫下拉伸變形30%,納米材料層與基材具有同樣的伸縮率。本發明中,基于常用不銹鋼(304、316L、317L及0Cr13不銹鋼)不同基材表面的抗結焦納米材料層通過X射線光電子能譜元素分析多次分析,元素組成如下表1:表1:本發明所述基于不銹鋼表面的抗結焦納米材料元素組成其中,本發明所述基于不銹鋼304基材的樣品測試結果如表2:表2:本發明所述基于304基材表面的抗結焦納米材料元素組成本發明所形成的納米材料相比于不銹鋼表面,其表面更加光滑、摩擦系數減小,摩擦系數減少33%,有利于流體的流動,垢污不容易附著在該納米材料表面;其中,以304基材樣品為例,按GB/T12444-2006,對本發明所述的納米材料表面進行了磨損試驗,結果如表3:表3:本發明所述的納米材料表面的磨損試驗測試位置摩擦應變ε摩擦力f=3.44ε(g)摩擦系數μ304基材表面7.525.80.129本發明所述納米材料表面5.017.20.086本發明所形成的納米材料相比原來的基材,水性及油性物質不容易在其表面成膜,納米材料表面對水、有機物的潤濕角都增大,說明本發明所述納米材料對油性物質、水性物質都不容易潤濕,具有一定的抗性;其中,以304基材樣品為例,按GB/T24368-2009,對本發明所述的納米材料表面進行了潤濕角試驗,結果如表4:表4:本發明所述的納米材料表面的潤濕角測試本發明中,根據不同的不銹鋼基材,工藝路線為熱堿化學除油堿蝕-水洗-氧化-水洗-電解-致密化-硬化;具體如下:(1)使用氫氧化鈉溶液及含堿蝕添加劑的溶液進行化學除油及堿蝕,上述溶液溫度控制在80-85℃,處理時間為10-15min,后使用80-85℃熱水循環清洗3-5min;氫氧化鈉溶液及含堿蝕添加劑的溶液的用量以能浸泡整個不銹鋼表面工件為準;(2)氧化溶液的成分包括CrO3200-300g/L,在75-90℃下,通過向所述氧化溶液中加入H2SO4溶液來調整氧化溶液的pH為0.4-1.5;所述H2SO4溶液的濃度為98%;所述氧化時間為15-35分鐘;(3)電解溶液成分包括CrO3100-150g/L、Na2SiO380-100g/L;納米氮化硅15-20g/L、納米碳化硅3-5g/L;通過向所述溶液中加入H2SO4溶液來調整溶液的pH為0.5-1.5,溫度控制40-52℃,以不銹鋼件作為陰極,所述電解液中的電流為直流電,其中,電流強度初始為40-42A/m2,電解10-25分鐘;然后電流強度按照i=3+30/t逐步減小,其中,所述i為電流強度,所述t為時間,電解14-18分鐘,最終電流控制在4-6A/m2;在25-40℃下循環水洗3-5分鐘;所述水洗是在pH>3下進行水洗;(4)將電解清洗完成的膜層放于溫度50-60℃、濕度60-70%下進行硬化3-.5小時,后將膜層在溫度35-40℃、濕度40~50%下硬化48-72小時,處理完成。本發明所述基于不銹鋼表面形成的抗結焦納米材料層為氧化鉻、氧化硅層。該納米材料與不銹鋼基材無明顯結合面,納米材料是鑲嵌結合在不銹鋼基材表面的,其主要原理是通過對不銹鋼基材進行氧化,從而在不銹鋼基材表面形成的蜂窩狀表層結構,所述納米材料填充在蜂窩狀結構中;所述氧化過程采用氧化溶液使不銹鋼表面形成蜂窩狀的微小孔隙結構,后通過特定的電解過程和硬化過程,使所述納米材料與不銹鋼基材鑲嵌結合。電解過程中的電流強度控制相當重要,時間短、電流大容易使不銹鋼表面蜂窩孔中填充的鉻、硅元素不充分,從而導致中間層帶孔、致密度不夠,抗腐蝕效果變差;因此,電流強度的大小、電解的時間和溫度、電解后期電流強度逐步變小的曲線決定了膜層的致密度。膜層硬化的控制溫度、濕度非常重要,溫度過高,膜層老化出現裂紋,溫度低,膜層松軟,特別是填充的金屬及金屬氧化物晶體在沖刷及摩擦過程膜層很容易與基材脫落。膜層的硬化經過試驗取得一個比較平衡的溫度及時間,容易實現工業化。本發明所述的基于不銹鋼表面的抗結焦納米材料及其制備方法,在不銹鋼表面形成納米材料層,該納米層結構為氧化鉻、氧化硅、氫氧化鉻的組合;該納米材料層與不銹鋼基材表面為嵌入式結合的方式,無結合面;該納米材料層與不銹鋼基材的熱膨脹系數沒有明顯的斷層;經本發明所述制備方法處理后的不銹鋼基材形成了蜂窩狀空隙結構。本發明中,所述氧化工藝pH控制為0.4-1.5之間,氧化時間15-35分鐘。所述電解工藝pH值控制在0.5-1.5,溫度控制40-52℃,該工藝以不銹鋼件作為陰極,所述電流強度初始為40-42A/m2,后電流強度按照i=3+30/t逐步減小,其中,所述i為電流強度,所述t為時間;所述電解時間為25-55分鐘;其中,所述電流強度以初始電流強度40-42A/m2進行的電解時間為10-25分鐘;后所述電流強度按照i=3+30/t逐步減小的方式進行的電解時間為14-18分鐘。所述硬化工藝在溫度50-60℃、濕度60-70%下進行硬化3-3.5小時,后在溫度35-40℃、濕度40-50%下硬化48~72小時。附圖說明圖1為304基材抗結焦納米表面元素分布示意圖;圖2為304基材抗結焦納米表層元素SEM晶體圖;圖3為通過X射線光電子能譜分析的本發明所述納米結晶材料的物質組成層趨勢圖;圖4為不銹鋼316L基材填料片放置減壓塔減三線3年5個月后結焦層的厚度;圖5為不銹鋼316L基材填料片經本發明的納米晶體材料處理后的放置減壓塔減三線3年5個月后結焦層的厚度;圖6為不銹鋼317L基材填料片放置減壓塔洗滌段3年5個月后結焦層的厚度;圖7不銹鋼317L基材填料片經本發明的納米晶體材料處理后的放置減壓塔減三線3年5個月后結焦層的厚度;圖8為電解電流控制電流強度i=40-2.33t(i電流強度,t致密持續時間min)電解15min;圖9為電解電流控制電流強度0~5min,電流40A/㎡,5~10min,電流20A/㎡,10~15min,電流5A/㎡電解15min;圖10為電解電流控制電流強度i=3+30/t(i電流強度,t致密持續時間min)電解15min。具體實施方式以下參照具體的實施例來說明本發明。本領域技術人員能夠理解,這些實施例僅用于說明本發明,其不以任何方式限制本發明的范圍。下述實施例中的實驗方法,如無特殊說明,均為常規方法。下述實施例中所用的原料、試劑材料等,如無特殊說明,均為市售購買產品。實施例1:柴油裂解結焦試驗在中國石化某研究單位采用本發明所述的不銹鋼基材317L的抗結焦納米材料裂解爐管(采用柴油(餾程:186-316.2℃))與未經處理的普通不銹鋼317L基材的裂解爐管做對比測試,如表5。表5:待測試的裂解和燒焦工藝如下:爐型實驗室小試裝置橫跨溫度560℃裂解溫度790℃停留時間0.33S水油比(重量)1出口壓力MPa(表)常壓進料量150g/h裂解時間2h燒焦溫度790℃經測試,未經處理的普通不銹鋼317L基材的裂解爐管表面結焦量為1.5464g,而本發明所述的不銹鋼317L基材的抗結焦納米材料的裂解爐管,第一根結焦量為1.0487g,相對減少32%,第二根結焦量為1.0049g,相對減少35%,抗結焦效果明顯。實施例2:減壓塔填料抗結焦試驗中國石油化工股份有限公司某分公司原油劣質化改造工程常減壓蒸餾裝置設計加工原油為高硫高酸原油。(1)在減壓塔第三段填料底部放置未經處理的普通不銹鋼316L基材填料片和本發明所述的不銹鋼316L基材的抗結焦納米表面層填料片,具體溫度如表6:表6:待測試的填料片溫度減三線溫度(℃)硫含量酸值殘炭含量213~331.20.77m%1.062.26%上述填料片經運行3年5個月后,經過金相制樣,觀察結焦層厚度如下:未經處理的普通不銹鋼316L基材的填料片結焦層(圖4)及本發明所述的不銹鋼316L基材的抗結焦納米填料片結焦層(圖5);通過對比可以看出,圖4所示的結焦層厚度為6.39微米,圖5(本發明所述的不銹鋼316L基材的抗結焦納米表面層)的結焦層厚度為2.55微米,結焦量相比減少60.1%。(2)在減壓塔第四段填料底部放置未經處理的普通不銹鋼317L基材填料片和本發明所述的不銹鋼317L基材的抗結焦納米表面層填料片,具體溫度如表7:表7:待測試的填料片溫度減四線溫度(℃)硫含量酸值殘炭含量329-3880.77m%1.0611.4%運行3年5個月后,經過金相制樣,觀察結焦層厚度如下:未經處理的普通不銹鋼317L基材填料片的結焦層(圖6)及本發明所述的不銹鋼317L基材的抗結焦納米填料片的結焦層(圖7);通過對比可以看出,圖6所示的結焦層厚度為12.22微米微米,圖7(本發明所述的不銹鋼317L基材的抗結焦納米表面層)的結焦層厚度為5.61微米,結焦量相比減少54.1%。實施例3:本發明所述抗結焦納米材料的硅元素含量測試本發明人發現,所述不銹鋼表面的抗結焦效果,其硅元素的含量有著決定性的影響,所述不銹鋼表面的硅元素含量越高,抗結焦的效果越好,通過對Na2SiO3和納米氮化硅的濃度控制來測試所述抗結焦納米材料的硅元素含量,下面以不銹鋼304基材為例,見表7和表8。表7:所述抗結焦納米材料的硅元素含量通過表7可以看出,本發明中當Na2SiO3濃度為80-100g/L時,所得到的抗結焦納米材料中的硅含量較高。表8:所述抗結焦納米材料的硅元素含量通過表8可以看出,納米氮化硅對抗結焦納米材料的硅元素含量有一定的影響,但是,添加過多的納米氮化硅,抗結焦納米材料的粗糙度會提升,在流體環境中抗結焦納米材料層的附著力會下降,反而對抗結焦不利,因此,本發明所述納米氮化硅的最佳范圍為15-20g/L。實施例4:電解工藝測試本發明經研究發現,電化過程中電流的變化對所述抗結焦納米材料表面的光滑度有很大的影響,為此通過電流強度的變化來確定表面摩擦系數的變化,其摩擦系數越小,其抗結焦的效果越好,其表面越不容易附著污垢。如圖8-10,X軸為時間(min),Y軸為電流強度(A/m2);方案1:圖8中,電流強度i=40-2.33t(i為電流強度,t為持續時間);方案2:圖9中,電流強度為40A/m2保持0-5min;電流強度為20A/m2保持5-10min;電流強度為5A/m2保持10-15min;方案3(本發明所述制備方法的電流控制方案):圖10中,電流強度為i=3+30/t(i為電流強度,t為持續時間);上述測試結果見表9:表9:基于不銹鋼304基材的抗結焦納米材料,摩擦系數對比:致密電流變化方案摩擦系數μ方案10.095方案20.103方案30.086結論:電解電流的變化方式不同導致不銹鋼納米表面的致密程度不同,由表可以看到,測試的摩擦系數μ越小,代表納米結晶表面的致密度越高,納米表面膜層越光滑,,從而導致抗垢層附著的效果越好。實施例5:本發明所述基于不銹鋼表面(304基材)的納米結晶材料的制備(1)使用濃度為7%的氫氧化鈉溶液及含有0.5%的HDW-1050堿蝕添加劑的溶液對所述不銹鋼表面(304基材)進行化學除油及堿蝕,整個溶液的總量以能全部浸沒不銹鋼工件表面為準,上述溶液溫度控制在80℃,處理時間為15min;后用80℃的水進行清洗3min;(2)所述氧化溶液的成分包括CrO3300g/L;在78℃下,使用濃度為98%的H2SO4溶液將pH控制為1.3,所述氧化時間為15分鐘,氧化完畢后常溫下水洗3分鐘。(3)所述電解溶液成分包括CrO3100g/L、Na2SiO3100g/L、納米氮化硅18g/L、納米碳化硅3g/L;使用濃度為98%的H2SO4溶液將pH值控制在1.3,溫度控制40℃,以不銹鋼件(304基材)作為陰極,根據不銹鋼件表面積計,以電流強度為40A/m2電解10分鐘,后采用i=3+30/t(i為電流強度A/m2,t為持續時間min)的逐步減小的電流強度進行電解15min;后常溫清水清洗不銹鋼件表面的電解液。(4)將不銹鋼件(304基材)放于溫度55℃、濕度60%的環境進行膜層硬化3小時;后將膜層放入溫度38℃、濕度45%下硬化72小時;即得基于不銹鋼表面(304基材)的抗結焦納米材料。本發明所述基于304不銹鋼的抗結焦納米材料測試結果:所述納米結晶材料包含:碳0.71%,氧34.62%,鉻42.81%,鐵13.11%,鎳3.1%,硅4.73%,鈣0.92%,余量為雜質元素。當前第1頁1 2 3