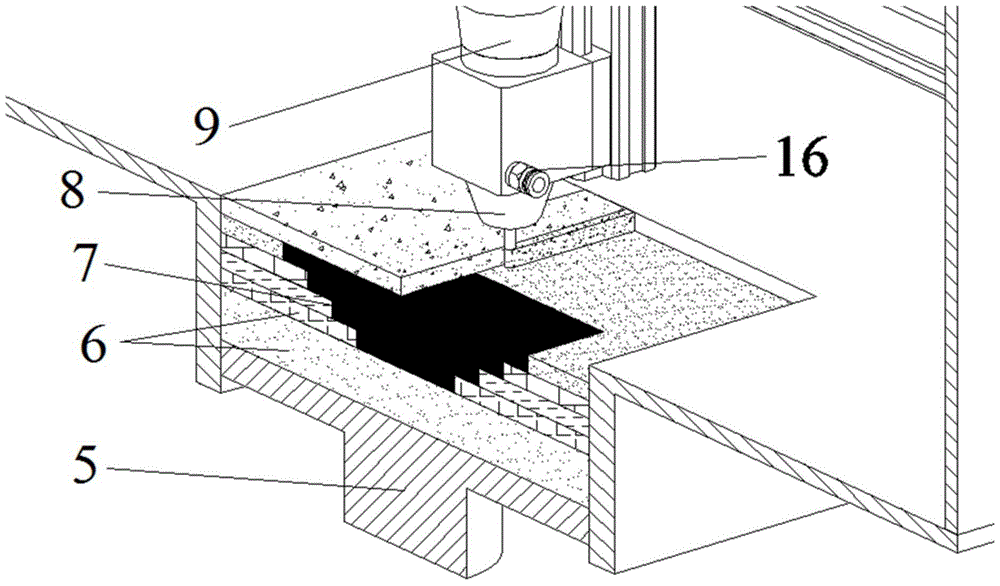
本發明涉及增材制造領域,尤其是涉及一種基于三維異質鋪粉的功能梯度零件增材制造方法。
背景技術:現代水電、宇航、電子、海洋、生物醫療等技術的迅猛發展,對零件的性能提出了更高的要求,例如零件的不同部位需要呈現不同的特性,如力學性能、耐高溫、腐蝕性能、抗氧化性能、外觀性能等。一般的單質零件很難滿足這些條件,傳統的復合材料零件雖然可以綜合利用單一材料的性能,但是零件內部往往存在著大量基體和增強材料不同相之間的界面,這些界面是應力分布發生突變或應力集中的區域,對于零件的整體性能產生負面影響,另外,傳統復合材料往往很難制成復雜的三維零件。1984年,日本國立宇航實驗室從層狀平滑連續變化的貝殼殼體斷面組織中得到啟發,提出了功能梯度材料(FunctionallyGradientMaterials,簡稱FGM)的設想。這種“組分、結構和性能連續變化”的材料,最早被用于宇航器材的熱防護。功能梯度材料制成的功能梯度零件,有著廣泛的應用前景。如生物組織工程中應用的支架,需要匹配被替代部位的力學性能,以骨替代為例,支架由內部向外需分別匹配密質骨、松質骨、皮質骨的力學性能。再如航天發動機中使用的壓氣機葉片盤,在盤緣和盤芯要求較高的室溫塑性、強度和低周疲勞性能,而盤緣則要有高的高溫斷裂韌性和蠕變抗力。以上零件不僅具有復雜的三維結構,零件內部還有著復雜的功能梯度,這為加工技術提出了新的要求。增材制造技術是采用將材料逐步累積成形三維零件的技術,與傳統的材料去除加工方法相比,具有節約材料,加工速度快,靈活性高,可加工的結構度復雜度高等優點。在眾多增材制造技術中,選擇性激光燒結(SelectiveLaserSintering,簡稱SLS) 與選擇性激光熔化技術(SelectiveLaserMelting,簡稱SLM)是目前被廣泛應用的增材制造方法。相比其他增材制造技術,選擇性激光燒結和選擇性激光熔化技術具有可加工的材料范圍廣、不需要額外設計支撐結構、材料利用率高等優點。這兩種技術的基本原理是:首先對零件的三維CAD模型進行切片,獲得每一層切片的截面信息。鋪粉裝置在成形缸內鋪一層粉末,采用激光在該層粉末上進行選擇性的掃描,使得掃描區的粉末粘結或熔化,得到零件的單層形狀;接著成形缸底部的活塞下降一個高度,鋪粉裝置在前一層粉末上再鋪設一層粉末,激光則按照下一層切片的截面信息對粉末進行選擇性掃描;依此逐層累加,最終獲得三維的零件。近年來也出現了采用電子束代替激光,作為能量輸入的選區電子束熔化技術(ElectronBeamMelting,簡稱EBM),但其基本原理相同。利用傳統的SLS(SLM,EBM)技術,可以加工出結構復雜的三維零件,但是難以實現零件內部復雜的功能梯度。目前常用的方法,是通過連續改變激光(電子束)的加工參數,來獲得空隙率、微觀組織等性能連續變化的功能梯度材料。對于通過改變材料組分的方法來實現功能梯度,也有部分人提出了一些改進方案,但都存在明顯的不足。如中國專利公開號CN103480845A發明了一種3D打印方法及其送粉刷機構,送粉刷機構包括漏斗式缸體,漏斗式缸體的出粉口呈長條形,出粉口的兩側各對稱設置有一塊由電機驅動、且能上下運動的彈性刮板;漏斗式缸體的出粉口設置有一個由電機控制其開關的閥門;用三維軟件設計零件模型,對不同材質的零件進行標識;然后切片分層處理;在粉末缸和漏斗式缸體中各自預存一種所需的粉末;控制系統根據切片的輪廓信息,控制送粉刷機構給成形缸提供粉末,激光熔化燒結粉末,這樣完成一層加工,可實現復合材料零件的3D打印制造。但是該發明能夠鋪設的粉末種類受到漏斗缸中分隔腔數的限制,鑒于漏斗缸的體積不可能太大,因而可用粉末種類必然較少。且一個切片層內的粉末組分是固定的。即使在一個切片層內,通過開關不同出粉口閥門的方式進行單層內的異質鋪粉,不同粉末也只能呈平行的帶狀分布,且不同粉末組分間有明顯的交界面,無法實現零件內部任意位置材料組分的精確控制和連續變化。與此類似的還有中國專利公開號CN103978211A發明的鋪粉裝置。另外,中國專利公開號CN103480843A發明了一種基于三缸成形機的復合材料零件的3D打印方法,包括如下步驟:用三維軟件設計零件模型;在三維模型的基礎上,對不同材質的零件進行標識,同一材質的零件,使用同一種標識,不同材質的零件采用不同的標識;然后三維模型進行 切片分層處理;在3D打印機的粉末缸中分別預存所需的一種粉末材料,控制3D打印機的系統根據三維模型切片的輪廓信息,并控制兩個送粉缸給成形缸供粉,激光熔化燒結粉末,這樣完成一層加工;控制成形缸下降一個層厚,重復鋪粉的步驟,層與層堆積,一次直接完成復合材料的3D打印制造。但是該發明只能使用預存的兩種粉末,種類較少,且兩種預存粉末的配比不可變,同一切片層內只能使用同一種粉末,無法實現零件內部任意位置材料組分的精確控制和連續變化。另外,實用新型專利授權公告號CN201109649Y發明了一種用于選區激光熔化成形的金屬粉末鋪粉裝置。其通過漏嘴的形式,利用螺桿與漏嘴下端的間隙配合,實現落粉。但是該方法的粉末是預存在漏嘴的腔體,因此粉末原料配比不可變。當粉末原料種類較多時,需要預置很多的漏嘴,結構十分復雜,且無法實現粉末組分的連續變化。
技術實現要素:本發明的目的就是為了克服上述現有技術存在的缺陷而提供一種基于三維異質鋪粉的功能梯度零件增材制造方法,適用于快速制造結構及其內部功能的梯度都十分復雜的零件。本發明的目的可以通過以下技術方案來實現:一種基于三維異質鋪粉的功能梯度零件增材制造方法,其特征在于,包括以下步驟:(1)設計出零件的三維結構,根據零件三維結構和內部材料分布的要求,對零件進行分層切片,得到各層切片的厚度及截面形狀,接著對每一層切片進行點離散處理,并記錄切片內每一點的材料組分信息;(2)確定鋪粉工藝參數,以及燒結或熔化工藝參數;(3)在獨立于成形室之外的供粉系統中,向不同的并列式儲粉器內預存入不同的粉末原料;(4)所述供粉系統根據供粉時序表,控制粉末閥的開度,實時配制相應組分的粉末,通過粉末傳輸裝置送入成形室內的料倉中,所述料倉對送來的粉末進行緩沖收容并按序堆疊;(5)當料倉內的粉末緩存量達到設定值時,成形缸活塞下降與當前待加工切片層厚度相對應的高度,料倉及其下方的鋪粉嘴在導軌的帶動下,沿相應的鋪粉路徑對成形缸頂面進行逐點掃描,將料倉內堆疊的粉末按序鋪入成形缸內,當鋪粉嘴 完成當前鋪粉路徑的掃描時,當前待加工切片層的粉末材料鋪設完畢;(6)光源在振鏡系統的驅動下,依照與當前切片層相對應的燒結或熔化參數,沿相應的掃描路徑對成形缸頂面的粉末進行掃描,被掃描區域的粉末燒結或熔化凝固,至此完成一層切片的加工;(7)計算機讀取與下一層切片相對應的層厚、鋪粉工藝參數、燒結或熔化工藝參數信息,重復步驟(3)至(6),直到完成所有切片的加工后,通過逐層堆疊,獲得完整的三維零件。所述的供粉系統包括至少2個的儲粉器,與儲粉器數量相等的粉末閥、粉末混合器、送粉器和粉末輸送裝置,按照供粉時序表,供粉系統實時控制各個粉末閥的開度,以實現粉末配比的實時變化和控制,粉末混合器將粉末快速混合并送入送粉器,送粉器將混合后的粉末送入粉末輸送裝置。每個儲粉器存儲組分不同的粉末原料。所述的料倉接收來自粉末輸送裝置的粉末材料,進行緩沖后按序堆疊,再供給鋪粉嘴。所述的料倉上設有泄粉口,通過抽吸的方式將料倉內的多余粉末經泄粉口排去。所述的燒結或熔化加工在環境控制箱內進行。加工時對加工環境進行惰性氣體保護及對粉末進行預熱。所述的光源為激光或電子束。所述的鋪粉工藝參數包括鋪粉嘴的鋪粉路徑、鋪粉速度以及供粉系統的供粉時序表,所述的燒結或熔化工藝參數包括光源功率、掃描間距、掃描速度和掃描路徑。與現有技術相比,本發明具有以下優點:1)通過計算機的控制,使得粉末閥、送粉器、導軌、鋪粉嘴協同工作,依據對零件內各個切片層的供粉時序表,實時調節粉末的配比,可以實現單一切片層內的粉末組分精確控制以及可連續變化的特點;通過所有切片層的縱向累積,實現零件內部的三維異質鋪粉,從而實現零件內部復雜的功能梯度,大大提高了零件的功能梯度在三維空間中的復雜程度。2)由于粉末是通過外部的供粉系統進入環境控制箱保護的成形室內的,所以省去了供粉缸或者落料斗的空間。使得環境控制箱內的結構更加緊湊,降低加工成本。附圖說明圖1為用于實現本發明的系統布局示意圖;圖2為成形缸室的放大圖;圖3為功能梯度零件的內部組分變化示意圖。其中1.送粉器,2.混合器,3.粉末閥,4.并列式儲粉器,5.成形缸活塞,6.未燒結粉末,7.已燒結粉末,8.鋪粉嘴,9.料倉,10.導軌,11.粉末傳輸裝置,12.環境控制箱,13.振鏡系統,14.激光光源,15.保護鏡,16.泄粉口。具體實施方式下面結合附圖和具體實施例對本發明進行詳細說明。實施例粉末閥可以采用開度可控的電磁閥。混合器可以采用螺旋錐形混合機。送粉方式可以是依據粉體力學設計的連續流動輸送機,也可以是依據顆粒流體力學設計的氣流輸送機。若選擇連續流動輸送機,則粉末傳輸裝置為引導粉末的封閉式送料槽,若選擇氣流輸送機,則粉末傳輸裝置則為粉末輸送管。料倉內安裝有多孔隔板(例如采用陶瓷多孔板材料),將粉末和氣體分離,氣體通過料倉頂端的排氣孔排除,粉末則沉降至料倉底部。鋪粉嘴可采用螺旋擠出式或者齒輪擠出式。激光光源可是二氧化碳激光器(適合于燒結聚合物),也可以是光纖激光(適合于燒結金屬)。如采用電子束作為燒結(熔化)能源,則振鏡系統改為電子束聚焦引導系統。如圖2所示,為一種簡明的功能梯度零件示意圖,其長為L,寬為W,高為H,材料由粉末1、粉末2、粉末3組成,其變化規律可用零件內各點的坐標位置表示為:組分1(%)=80+10y/L組分2(%)=(20-10y/L)×[0.5+0.125(x/W+z/H)]組分3(%)=(20-10y/L)×[0.5-0.125(x/W+z/H)]其中,x∈[0,W],y∈[0,L],z∈[0,H]首先,利用CAD三維設計軟件設計出零件的三維結構,并依據上述公式給三維零件中的每一點標志材料組分信息。然后對三維零件進行切片,在獲得每一層切片形狀的同時,得到切片內每一點的材料組分信息。通過算法,確定鋪粉嘴的鋪粉 路徑、鋪粉速度、供粉系統的供粉時序表等鋪粉工藝參數,計算激光的掃描間距、掃描路徑、激光功率等燒結(熔化)工藝參數。在1號儲粉缸內存入純粉末1,在2號儲粉缸內存入純粉末2,在3號儲粉缸內存入純粉末3。成形缸活塞下降一個層厚h,鋪粉嘴在導軌的帶動下向成形缸移動,準備進行鋪粉。同時,供粉系統根據與當前層相應的供粉時序表,向料倉供粉。當料倉內有足夠粉末緩存時,開始鋪粉。當供粉系統在為坐標(0,0,0)的點供粉時,與1號儲粉缸對應的1號粉末閥的開度為80%,與2號儲粉缸對應的2號粉末閥開度為10%,與3號儲粉缸對應的3號粉末閥開度為10%。在鋪粉嘴沿x軸從(0,0,0)點鋪粉至(L,0,0)點的過程中,1號粉末閥保持80%的開度,2號粉末閥的開度由10%線性增加至12.5%,3號粉粉末閥的開度由10%減少到7.5%。粉末在料倉內按序堆疊,再由鋪粉嘴送入成形缸進行鋪設。依照上述原理,鋪粉嘴完成當前待加工切片層的鋪粉工作,在導軌的帶動下,回到起始位置。激光在振鏡系統的驅動下,采用對應的燒結(熔化)工藝參數,沿相應的掃描路徑對成形缸內的粉末進行掃描,被掃描部分燒結(熔化凝固)。至此完成第一層切片的燒結(熔化)加工。計算機獲取與下一層切片相對應的層厚、鋪粉工藝參數、燒結(熔化)工藝參數等信息,仍依照上述過程進行下一切片層的鋪粉和選擇性燒結(熔化)成形。通過循環上述步驟,逐層累加,直至完成三維零件的成形過程。成形過程所在的成形室,如有需要,可以進行抽真空及惰性氣體保護的功能。成形缸內的粉末,如有需要,可以進行預熱。如需要基板,則成形缸活塞上可安裝基板。料倉及鋪粉嘴內的粉末,可以通過泄粉口被排出,以應對供粉出錯或者其他故障導致加工中斷時,重置料倉內的粉末緩存。本發明的實施方式并不受上述實施例的限制,其他任何未背離本發明的精神實質與原理下所作的改變、修飾、替代、組合、簡化,均應為等效的置換方式,都包含在本發明的保護范圍內。