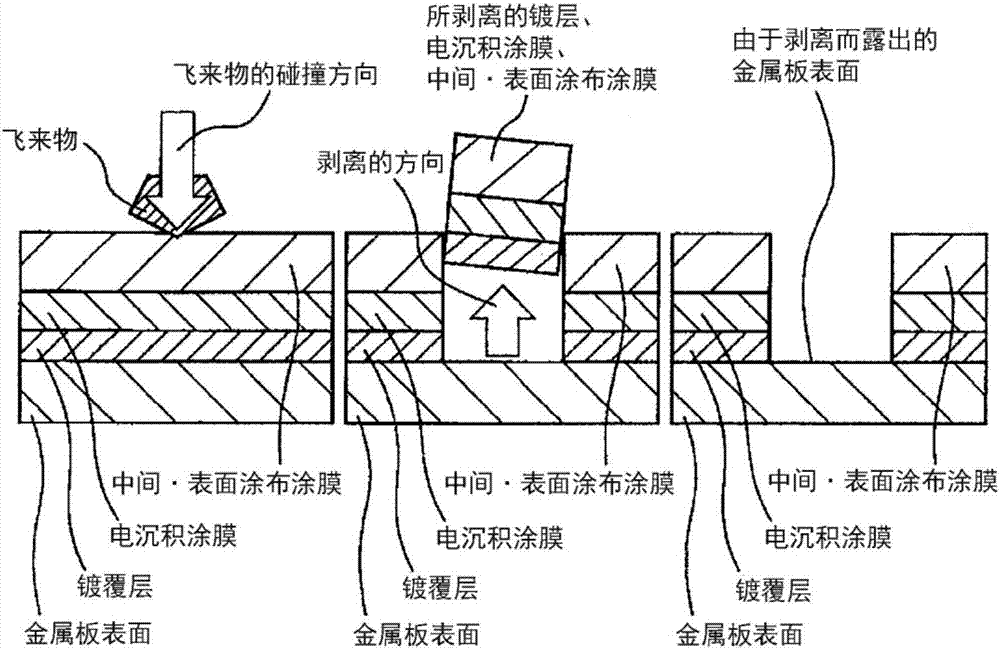
本發明涉及具有耐崩裂(chipping)性、低溫行駛環境中的防銹性優異的汽車用涂裝金屬板。
背景技術:
:以下對本發明的
背景技術:
進行說明。汽車車體用構件大部分是將鋼板等金屬板作為原材料,經過[1]將金屬板切斷為規定尺寸的毛坯工序、[2]用油洗滌金屬板的油洗工序、[3]將毛坯壓制成型的工序、[4]通過點焊、粘接等將成型材料裝配到所希望形狀的構件的接合工序、[5]對于構件表面的壓力機油進行脫脂以及洗滌的工序、[6]化學轉化處理工序、[7]電沉積涂裝工序等很多工序制造。用作外板的車體用構件通常進而經過[8]中間涂布工序、[9]表面涂布工序等涂裝工序。因此,汽車業界中,通過制造工序、特別是化學轉化處理工序、涂裝工序的省略、簡化來實現成本削減的需求高。為了響應這些需求,省略汽車制造時的化學轉化處理工序,省略、簡化電沉積涂裝工序,省略、削減輔助資材,迄今研究汽車車體用構件使用涂裝金屬板(預涂金屬板)。汽車車體用構件所要求的重要性能之一為耐崩裂性。崩裂指的是汽車行駛時飛濺的石頭等與車體碰撞、此時涂膜和鍍覆覆膜被破壞、剝離的現象。該現象在寒冷地區成為重要的問題,被稱為低溫崩裂現象。寒冷地區中,涂膜暴露于低溫,想要縮短的內部應力發揮作用。若對于涂膜施加石頭飛濺等沖擊則不僅涂膜損傷,而且處于其下的鍍覆覆膜也損傷,進而有可能產生龜裂直至鍍覆覆膜與鋼板的界面為止。認為這是由于,涂膜的內部應力作用于鍍覆覆膜。這種鍍覆覆膜的剝離部直接導致耐蝕性的降低,為汽車車體涂膜系的大問題。作為汽車車體用構件的崩裂對策,以往進行的是,在電沉積涂膜與中間涂布涂膜之間插入崩裂底漆。崩裂底漆的目的在于,通過作為緩沖層發揮功能,緩和石頭碰撞時對涂膜的沖擊。因此,作為崩裂底漆的性質,要求涂膜的彈性高、涂膜的伸長率大、涂膜強度高。作為涂膜的伸長率大的崩裂底漆,專利文獻1(日本特開2003-251272公報)中記載了玻璃化轉變溫度(tg)調整于0~-75℃的水性崩裂底漆。另一方面,如上所述,汽車業界中,通過制造工序、特別是涂裝工序的省略、簡化來實現成本削減的需求高,謀求可以省略崩裂底漆涂布這樣的附屬工序的汽車車體涂膜系。例如專利文獻2(日本特開2003-245605公報)、專利文獻3(日本特開2005-15516號公報)中記載了使得中間涂布涂膜中含有用于吸收崩裂的沖擊的橡膠顆粒、賦予耐崩裂性、沒有涂布崩裂底漆的層疊涂膜的形成方法。專利文獻4(日本特開2003-253211號公報)中公開了包含涂膜形成性樹脂、固化劑、著色顏料、滑石和硅烷偶聯劑的具有耐崩裂性的水性中間涂布涂料組合物。專利文獻2~4的目的都在于,在汽車用鋼板涂布電沉積涂料等底涂布涂料之后,對于所層疊的中間涂布層賦予耐崩裂性,省略崩裂底漆。與此相對,在汽車車體用構件使用涂裝金屬板、對于該涂裝金屬板的涂膜自身賦予耐崩裂性、省略崩裂底漆的汽車車體涂膜系尚未存在。現有技術文獻專利文獻專利文獻1:日本特開2003-251272號公報專利文獻2:日本特開2003-245605號公報專利文獻3:日本特開2005-15516號公報專利文獻4:日本特開2003-253211號公報技術實現要素:發明要解決的問題本發明是鑒于上述問題而提出的,涉及具有耐崩裂性、并且低溫行駛環境中的防銹性優異的汽車用涂裝金屬板。用于解決問題的方案本發明人等發現,將以往的崩裂底漆中使用的伸長率高、玻璃化轉變溫度tg為0℃以下的有機樹脂用于涂裝金屬板的涂膜,賦予耐崩裂性,可以省略崩裂底漆。但是,由玻璃化轉變溫度tg為0℃以下的有機樹脂形成的涂膜存在下述問題:常溫下具有粘合性,若層疊來保存則上下的涂裝金屬板接合。本發明人等進一步進行研究結果,通過使得涂膜中含有具有特定硬度的顆粒,解決該問題,可以得到本發明的具有耐崩裂性的汽車用涂裝金屬板。本發明具體而言如下所述。[1]一種汽車用涂裝金屬板,其含有金屬板、和處于前述金屬板的至少一表面上的涂膜(α),前述涂膜(α)含有有機樹脂(a)、導電性顏料(b)和防銹顏料(c),涂膜(α)表面的-20℃時的最小馬氏硬度在測定100點時20點以上為hm10~200(mg/mm2),涂膜(α)表面的40℃時的最小馬氏硬度在測定100點時5點以上為hm200~200000(mg/mm2)。[2]根據[1]所述的汽車用涂裝金屬板,其中,前述有機樹脂(a)的玻璃化轉變溫度tg為-80℃~-20℃。[3]根據[1]所述的汽車用涂裝金屬板,其中,前述有機樹脂(a)選自由聚酯樹脂、聚氨酯樹脂、丙烯酸系樹脂或它們的改性體組成的組中。[4]根據[1]所述的汽車用涂裝金屬板,其中,前述導電性顏料(b)為選自硼化物、碳化物、氮化物、硅化物中的至少一種的25℃的電阻率為0.1×10-6~185×10-6ωcm的非氧化物陶瓷顆粒。[5]根據[1]所述的汽車用涂裝金屬板,其中,前述涂膜(α)含有0.5vol%~65vol%的量的導電性顏料(b)。[6]根據[1]所述的汽車用涂裝金屬板,其中,前述防銹顏料(c)含有選自下述化合物和或下述顆粒中的一種或兩種以上,所述化合物能夠釋放硅酸根離子、磷酸根離子、釩酸根離子、鎢酸根離子或鉬酸根離子,所述顆粒含有選自由si、ti、al和zr組成的組中的金屬元素。[7]根據[1]所述的汽車用涂裝金屬板,其中,前述涂膜(α)含有1vol%~40vol%的量的防銹顏料(c)。[8]根據[1]所述的汽車用涂裝金屬板,其中,涂膜中含有40℃時的馬氏硬度為200mg/mm2~200000mg/mm2的粒狀的顆粒(d)。[9]一種汽車部件,其是將[1]所述的汽車用涂裝金屬板加工、成型而形成的。[10]一種汽車部件,其是對[9]所述的汽車部件進一步涂布電沉積涂膜層、中間涂布涂膜層、表面涂布涂膜層中的任意一層以上而形成的。發明的效果本發明的汽車用涂裝金屬板由于涂膜其自身具有耐崩裂性,因此在將該涂裝金屬板加工、成型為汽車部件后的涂裝工序中,無需設置崩裂底漆的涂布工序。另外,該涂膜的耐崩裂性特別是在-15℃以下的低溫環境中有效,可以提供耐蝕性優異的汽車用涂裝金屬板。附圖說明圖1表示具有崩裂底漆的以往的汽車涂膜結構的截面的示意圖。圖2表示汽車車體用構件與飛來物碰撞、金屬板的表面露出時的涂膜截面的示意圖。圖3表示使用了本發明的汽車用涂裝金屬板的汽車車體用構件與飛來物碰撞而金屬板露出,然后被水潤濕而由涂膜(α)溶出的防銹成分在所露出的金屬板表面反應,由此形成保護性的覆膜時的涂膜截面的示意圖。圖4表示使用了涂膜(α)的物性不適合于本發明的范圍的汽車用涂裝金屬板的汽車車體用構件與飛來物碰撞,涂膜(α)的內部應力大,因此包括鍍覆層在內的上層覆膜大幅剝離,金屬板表面的露出大,因此即使此后被水潤濕,金屬板表面也不會被通過源自涂膜(α)的防銹成分形成的保護性的覆膜充分覆蓋時的涂膜截面的示意圖。圖5表示存在基底處理時的本發明的汽車用涂裝金屬板的截面的示意圖。圖6表示沒有基底處理時的本發明的汽車用涂裝金屬板的截面的示意圖。圖7表示示出本發明的汽車用涂裝金屬板的截面中的顆粒(p)的分布狀態的示意圖。具體實施方式以下對于本發明進行詳細說明。<金屬板>本發明的汽車用涂裝金屬板為用特定的導電性涂膜覆蓋表面的至少一部分而成的例如帶鍍覆覆膜的金屬板。該金屬板根據用途,可以金屬板的兩面被導電性涂膜覆蓋或僅單面被覆蓋,另外,可以表面的一部分被覆蓋或全部表面被覆蓋。金屬板的被導電性涂膜覆蓋的部位的電阻焊性、耐蝕性優異。作為可以用于本發明的涂裝金屬板的帶鍍覆覆膜的金屬板的構成金屬,例如可以含有鋁、鈦、鋅、銅、鎳、以及鋼等。對于這些金屬成分沒有特別限定,例如使用鋼的情況下,可以為普通鋼或含有鉻等添加元素的鋼。但是,本發明的金屬板由于壓制成型,任意一種金屬板的情況下,為了具備所希望的成型加工追隨性,都優選適當控制添加元素的種類和添加量、以及金相組織。另外,作為金屬板,使用鋼板的情況下,對于其表面鍍覆覆膜的種類沒有特別限定。作為能夠適用的鍍覆覆膜,可列舉出例如含有鋅、鋁、鈷、錫、鎳中的任意一種金屬元素的鍍層,以及含有這些金屬元素、進而其它的金屬元素、非金屬元素的合金鍍層等。特別是作為鋅系鍍覆覆膜,可列舉出例如包含鋅的鍍層,鋅、和鋁、鈷、錫、鎳、鐵、鉻、鈦、鎂、錳中的至少一種金屬元素的合金鍍層,或者進而含有其它的金屬元素、非金屬元素的各種鋅系合金鍍層(例如鋅、和鋁、鎂、硅的4元合金鍍層),但是對于鋅以外的合金成分沒有特別限定。進而這些鍍覆覆膜,作為少量的異種金屬元素或雜質,可以含有鈷、鉬、鎢、鎳、鈦、鉻、鋁、錳、鐵、鎂、鉛、鉍、銻、錫、銅、鎘、砷等,也可以含有分散有二氧化硅、氧化鋁、二氧化鈦等無機物的物質。作為鋁系鍍覆覆膜,可列舉出包含鋁的鍍層,或者鋁和硅、鋅、鎂中的至少一種的合金鍍層(例如鋁和硅的合金鍍層,鋁和鋅的合金鍍層,鋁、硅、鎂的3元合金鍍層)等。進而,也能夠適用前述鍍層和其它種類的鍍層例如鐵鍍層、鐵和磷的合金鍍層、鎳鍍層、鈷鍍層等組合而成的多層鍍層。對于鍍覆覆膜的形成方法沒有特別限定。例如可以使用電鍍、化學鍍覆、熱浸鍍、蒸鍍鍍覆、分散鍍覆等。鍍覆處理方法可以為連續式、間歇式中的任意一種。另外,使用鋼板的情況下,作為鍍覆后的處理,有可能存在作為熱浸鍍后的外觀均勻處理的零鋅花(zerospangle)處理,作為鍍覆覆膜的改性處理的退火處理,用于表面狀態、材質調整的調質軋制等,但是本發明中不特別限定于它們,可以適用任意一種。<涂膜(α)>覆蓋本發明的金屬板的涂膜(α)含有有機樹脂(a)、導電性顏料(b)和防銹顏料(c),涂膜(α)表面的-20℃時的最小馬氏硬度在測定100點時20點以上為hm10~200(mg/mm2),涂膜(α)表面的40℃時的最小馬氏硬度在測定100點時5點以上為hm200~200000(mg/mm2)。最小馬氏硬度hm通常為表示硬度的指標,在本發明中,規定涂膜(α)的表面的硬度。最小馬氏硬度hm可以通過使用fischerinstrumentsk.k制、nano-indenterhm500,對于厚度10μm以上的涂膜,將擠入深度設定于5μm以下來測定。對于厚度不足10μm的涂膜而言,可以通過將擠入深度設為涂膜厚度的1/5來測定,但是這種情況下,測定的偏差增大,因此適當增加測定次數,將其平均值作為測定值。本發明中,對于涂裝金屬板的涂膜(α)表面的任意點,隨機測定100點的-20℃時的最小馬氏硬度hm時,其中20點以上的hm為10~200(mg/mm2),并且隨機測定100點的40℃時的最小馬氏硬度hm時,其中5點以上的hm為200~200000(mg/mm2)的情況下,作為本發明的汽車用涂裝金屬板。進而,優選的是,隨機測定100點的-20℃時的最小馬氏硬度hm時,其中40點以上的hm為10~200(mg/mm2),并且隨機測定100點的40℃時的最小馬氏硬度hm時,其中10點以上的hm為200~200000(mg/mm2)的情況,更優選的是,隨機測定100點的-20℃時的最小馬氏硬度hm時,其中60點以上的hm為10~200(mg/mm2),并且隨機測定100點的40℃時的最小馬氏硬度hm時,其中20點以上的hm為200~200000(mg/mm2)的情況。在此,“隨機”指的是選擇作為測定點的100點時、排除測定結果不平衡的恣意性。例如可以設定任意的2點、在其之間以等間隔或任意的間隔選擇100點,測定20℃時的最小馬氏硬度hm和40℃時的最小馬氏硬度hm。此時,所鄰接的測定點之間的間隔優選為互相不受到測定點的硬度的影響的位置。另外認為雖然設為100點,但是測定點越增加則測定值越平均化,精度進一步提高。發明人發現,實施了面向汽車的電沉積涂裝、中間涂布涂裝、表面涂布涂裝的具有本發明的涂膜(α)的金屬板在低溫環境中受到飛來的石頭飛濺時,涂膜(α)即使在低溫環境下也充分柔軟的情況,與在低溫下并非充分柔軟的情況相比,可抑制由于石頭飛濺的沖擊而甚至達到鍍覆層剝離的顯著受損。另外發現,涂膜(α)的低溫環境下的最小馬氏硬度處于10~200(mg/mm2)的低的范圍內的情況下,可抑制顯著的受損。涂膜(α)在低溫下并非充分柔軟的情況下,由于石頭飛濺的沖擊而表面涂布涂膜、中間涂布涂膜、電沉積涂膜被破壞,進而涂膜(α)被破壞。此時發現,由于破壞而釋放的這些涂膜的收縮應力作為剝離鍍覆層的應力傳導,作為其結果,鍍覆層大幅剝離。另一方面發現,涂膜(α)在低溫下具有充分的柔軟性的情況下,即使由于石頭飛濺的沖擊而處于涂膜(α)之上的涂膜被破壞,其收縮應力也會通過涂膜(α)變形而被吸收,不會傳導到鍍覆層,其結果鍍覆層的剝離得到抑制。如此發現,即使處于上方的涂膜受到損傷、鍍覆層的剝離也得到抑制的情況下,通過涂膜(α)所含有的防銹顏料的作用而在受損部露出的鍍覆層和基底金屬板表面的腐蝕得到抑制,因此崩裂耐蝕性高。根據發明人等的研究,由涂膜(α)的表面測定的最小馬氏硬度hm在-20℃時相對于隨機的測定部位100點、20點以上為10~200的情況下,涂膜(α)為柔軟、為充分發揮前述效果的程度。若hm超過200則涂膜(α)變得不柔軟,抑制涂膜的收縮應力對鍍覆層的傳遞的效果不充分。需要說明的是,對于-20℃時的hm的下限沒有特別規定,但是以通常的工業上成本得不到實現不足10這樣的涂膜(α)的樹脂,因此該值為實質上的下限。對于具有-20時的hm為200以下的部位的、低溫時柔軟的涂膜(α),在20~40℃左右的所謂常溫時的保管、搬運等狀況下,若將帶涂膜的金屬板之間重疊來保持則涂膜(α)之間相互粘合或熔接,對于工業上的處理容易造成障礙。根據發明人等的研究,由涂膜(α)的表面測定的最小馬氏硬度hm在40℃時相對于隨機的測定部位100點、5點以上為200~200000的情況下,前述的涂膜(α)之間的相互粘合或熔接得到充分抑制。在20~40℃左右的所謂常溫時的保管、搬運等狀況下,將帶涂膜的金屬板之間重疊來保持時,通過在涂膜(α)的表面存在如此40℃時的hm高的部位,先前所述的-20℃時的hm低至10~200的部位之間的接觸得到抑制,推測其結果,涂膜(α)之間的粘合或熔接得到防止。最小馬氏硬度hm在40℃時為200~200000的部位相對于隨機的測定部位100點不足5點的情況下,前述的效果降低。涂膜(α)的-20℃時的最小馬氏硬度hm通常可以通過適當選擇涂膜用組合物的有機樹脂(a)、固化劑來控制。具體而言,可以使用樹脂分子結構含有交聯點之間的分子量大、容易變形的柔軟的結構,通過調節固化劑的種類、添加量來將樹脂的分子鏈之間的交聯密度保持得低,通過涂膜燒結溫度的降低、燒結時間的縮短來緩和利用固化劑進行的交聯反應等手法。以下,本發明中,將用于得到涂膜(α)的涂裝用組合物記載為涂裝用組合物(β)。作為涂裝用組合物(β),可列舉出水系涂裝用組合物、有機溶劑系涂裝用組合物。本發明中,“水系涂裝用組合物”指的是使用水為全部溶劑的50質量%以上的“水系溶劑”構成的組合物。另外,“有機溶劑系涂裝用組合物”指的是使用有機溶劑為全部溶劑的50質量%以上的“有機溶劑系溶劑”構成的組合物。作為上述的“水系溶劑”的水以外的構成成分,可列舉出例如與水充分混合的硫酸、硝酸、鹽酸、磷酸、硼酸、氫氟酸等無機酸,前述無機酸的金屬鹽、銨鹽等無機鹽類中溶解于水的物質,溶解于水的硅酸鹽、硫代硫酸鹽、硫氰酸鹽等無機化合物,和與水混合的有機化合物。另外,根據需要,也可以向上述的“水系溶劑”中加入有機溶劑。但是,從勞動衛生上的觀點考慮,本發明的“水系涂裝用組合物”中,優選調整有機溶劑的種類、添加量以形成不符合由勞動安全衛生法施行令(有機溶劑中毒預防規則第一章第一條)定義的有機溶劑等(第一種有機溶劑、第二種有機溶劑、第三種有機溶劑、或含有超過5質量%的前述有機溶劑的情況)的涂裝用組合物。作為對金屬板的制膜方法,例如水系、溶劑系涂裝用組合物的情況下,優選為通過輥涂、有槽輥涂布、簾流涂布、卷簾涂布、浸漬(dip)、氣刀軋液等公知的涂裝方法在金屬板上涂布涂裝用組合物(β),然后,將濕式涂膜的水分、溶劑進行干燥的方法。作為這些干燥涂膜的固化方法,優選通過將涂膜中的有機樹脂加熱燒結來進行聚合、固化,但是若涂膜中的樹脂能夠利用紫外線進行聚合則可以使用利用紫外線照射進行聚合或固化,若涂膜中的樹脂能夠利用電子束進行聚合則可以使用利用電子束照射進行聚合或固化。為了進一步改善前述涂膜(α)對金屬板的密合性、耐蝕性等,可以在該涂膜與金屬板表面之間設置基底處理覆膜。設置基底處理覆膜的情況下,對于其層數、組成沒有限定,但是需要基底處理覆膜對金屬板和上層涂膜(α)的密合性優異從而不會損害將金屬板成型加工時的涂膜(α)的加工追隨性、耐蝕性。若考慮到對環境的適合性則基底處理覆膜優選為無鉻酸鹽的結構。另外,為了確保覆膜厚度方向的充分的導電性,優選基底處理覆膜厚度為0.5μm以下。設置基底處理覆膜的情況下,若為工業上可以適用的制膜方法則對于基底處理覆膜的制膜方法沒有限定。基底處理覆膜的制膜方法可例示出基底處理用組合物的涂裝、蒸鍍、薄膜粘貼等方法,但是從制膜成本(生產率)、通用性等觀點考慮,優選為利用水系或溶劑系的基底處理用組合物的涂裝、干燥進行的方法。使用水系或溶劑系的基底處理用組合物的情況下,可以從包括基底處理覆膜在內的多層涂膜的最下層直至最表面層為止每1層反復涂布和干燥(依次涂裝法),由此形成多層涂膜。另外,作為簡便且有效地將涂膜形成于金屬板表面的方法,可以通過以下述順序包括將從與金屬板表面接觸的最下層直至最表層為止的各層的涂膜在濕式狀態下依次或同時多層覆蓋的工序(涂裝用組合物的濕式對濕式(wetonwet)涂裝或多層同時涂裝工序),將濕式狀態的各層覆膜的水分、溶劑同時干燥的干燥工序,將前述多層涂膜固化的制膜工序的層疊方法制膜。在此,濕式對濕式涂裝法指的是在金屬板上涂布涂液后,在該涂液干燥之前的含溶劑狀態(濕式狀態)中,在其上涂布其它涂液,將所得到的層疊涂液的溶劑同時干燥、固化,從而制膜的方法。另外,多層同時涂裝法指的是通過多層滑動式簾涂機、狹縫金屬型涂料機等,將多層的涂液以層疊狀態同時涂布于金屬板上后,將層疊涂液的溶劑同時干燥、固化,從而制膜的方法。覆蓋本發明的金屬板的涂膜(α)的平均厚度優選處于0.5~30μm厚度的范圍內、更優選處于1~15μm厚度的范圍內。不足0.5μm的厚度時,涂膜過薄、不能保持充分量的防銹顏料、有可能得不到耐蝕性。若涂膜厚度超過30μm則不僅所使用的涂裝用組合物(β)的量增加而制造成本變高,而且壓制成型時涂膜有可能內聚破壞或者剝離。另外,由于厚膜而膜厚方向的電絕緣性升高,難以進行電阻焊。進而,使用水系涂裝用組合物的情況下,產生噴涌等涂膜缺陷的可能性升高,不容易穩定地得到作為工業產品所需要的外觀。前述涂膜(α)的厚度可以通過涂膜的截面觀察等測定。需要說明的是,即使將附著于金屬板的單位面積的涂膜的質量除以涂膜的比重、或涂裝用組合物(β)的干燥后的比重來算出,也應該形成與通過截面觀察測定的情況相同的測定值,因此也可以簡便地利用以比重算出的方法。涂膜的附著質量可以從涂裝前后的質量差、涂裝后的涂膜的剝離前后的質量差、或者對于涂膜進行熒光x射線分析測定預先知道涂膜中的含量的元素的存在量等現有的手法適當選擇。涂膜的比重或涂裝用組合物(β)的干燥后的比重可以從測定所分離的涂膜的容積和質量、將適量的涂裝用組合物(β)取于容器并且測定干燥后的容積和質量、或者由涂膜構成成分的配混量和各成分的已知的比重計算等現有的手法適當選擇。<有機樹脂(a)>本發明的有機樹脂(a)為涂膜(α)的粘結劑成分,通過適當選擇其,可以得到本發明的汽車用涂裝金屬板的涂膜所需要的-20℃時的最小馬氏硬度hm和tg。有機樹脂(a)可以為水系、有機溶劑系樹脂中的任意一種,特別是為后述的樹脂(a1)。有機樹脂(a)可以進一步追加含有樹脂(a1)的反應衍生物(a2)。對于本發明的有機樹脂(a)以下進行詳細說明,優選具有-80℃~-20℃的玻璃化轉變溫度tg。本發明中,為了形成涂膜(α)而使用的涂裝用組合物(β)可以使用水系、有機溶劑系中的任意一種,以不揮發成分的50~100質量%含有后述的樹脂(a1)。樹脂(a1)穩定地存在于涂裝用組合物(β)中。若將這種涂裝用組合物(β)涂布于金屬板、進行加熱則大部分情況下,樹脂(a1)不會反應而直接干燥。前述涂裝用組合物(β)中含有硅烷偶聯劑、固化劑、交聯劑等的情況下,樹脂(a1)的至少一部分與它們反應而形成樹脂(a1)的衍生物(a2)。因此,這種情況下,成為作為涂膜(α)的粘結劑成分的有機樹脂(a)包含未反應的樹脂(a1)以及樹脂(a1)的反應衍生物(a2)。作為前述樹脂(a1)的種類,沒有特別限定,若具有必要的最小馬氏硬度hm和玻璃化轉變溫度tg則可列舉出例如聚氨酯樹脂、聚酯樹脂、環氧樹脂、(甲基)丙烯酸系樹脂、聚烯烴樹脂、或它們的改性體等。也可以將它們中的一種或兩種以上混合來作為前述樹脂(a1)使用,也可以將通過至少一種有機樹脂改性而得到的有機樹脂一種或兩種以上混合來作為前述樹脂(a1)使用。作為前述樹脂(a1),優選使用聚氨酯樹脂、聚氨酯樹脂改性體、聚氨酯樹脂復合物、它們和其它樹脂的混合物等。聚氨酯樹脂中的氨基甲酸酯基(-nhcoo-)與其它的大部分有機基團相比具有高的分子內聚能(8.74kcal/摩爾),因此若在樹脂(a1)中含有聚氨酯樹脂則具有下述效果:涂膜的密合性升高,壓制成型時,不易產生涂膜的剝離、粘著,并且通過比較高的內聚能,腐蝕因子遮蔽性(涂膜的致密性)提高而耐蝕性提高。氨基甲酸酯基以外的有機基團例如亞甲基(-ch2-)、醚基(-o-)、仲氨基(亞氨基、-nh-)、酯基(-coo-)、苯環的分子內聚能分別為0.68kcal/摩爾、1.00kcal/摩爾、1.50kcal/摩爾、2.90kcal/摩爾、3.90kcal/摩爾,氨基甲酸酯基(-nhcoo-)的分子內聚能與它們相比相當高。因此,大部分情況下,含有聚氨酯樹脂的涂膜與包含其它的大部分樹脂、例如聚酯樹脂、(甲基)丙烯酸系樹脂、聚烯烴樹脂等的涂膜相比密合性高、耐蝕性高。前述樹脂(a1)若如已經所述那樣具有必要的玻璃化轉變溫度tg則對于其種類沒有特別限制。優選為在樹脂(a1)的結構中含有選自羧基(-cooh)、羧酸鹽基(-coo-m+、m+為一價陽離子)、磺酸基(-so3h)、磺酸鹽基(-so3-m+、m+為一價陽離子)、伯氨基(-nh2)、仲氨基(-nhr1、r1為烴基)、叔氨基(-nr1r2、r1和r2為烴基)、季銨鹽基(-n+r1r2r3x-,r1、r2、r3為烴基,x-為一價陰離子)、锍鹽基(-s+r1r2x-,r1、r2為烴基,x-為一價陰離子)、磷鎓鹽基(-p+r1r2r3x-,r1、r2、r3為烴基,x-為一價陰離子)中的至少一種官能團的樹脂。它們的詳細內容、具體例如后文所述。需要說明的是,本發明中,用于得到涂膜(α)的涂裝用組合物(β)中使用的樹脂中可以含有完全溶解于水、有機溶劑的水溶性、溶劑溶解型的樹脂,和以乳狀液、懸浮液等形態均勻微分散于水、溶劑中的樹脂(水分散性樹脂、溶劑分散性樹脂)。另外,在此“(甲基)丙烯酸系樹脂”指的是丙烯酸系樹脂和甲基丙烯酸系樹脂。前述樹脂(a1)中,作為聚氨酯樹脂,可列舉出例如使得多元醇化合物和多異氰酸酯化合物反應、然后進而利用增鏈劑進行增鏈而得到的聚氨酯樹脂等。作為前述多元醇化合物,若為每一分子含有兩個以上羥基的化合物則沒有特別限定,可列舉出例如乙二醇、丙二醇、二甘醇、1,6-己二醇、新戊二醇、三甘醇、甘油、三羥甲基乙烷、三羥甲基丙烷、聚碳酸酯多元醇、聚酯多元醇、雙酚羥基丙基醚等聚醚多元醇、聚酯酰胺多元醇、丙烯酸系多元醇、聚氨酯多元醇、或它們的混合物。作為前述多異氰酸酯化合物,若為每一分子含有兩個以上異氰酸酯基的化合物則沒有特別限定,可列舉出例如六亞甲基二異氰酸酯(hdi)等脂肪族異氰酸酯、異佛爾酮二異氰酸酯(ipdi)等脂環族二異氰酸酯、甲苯二異氰酸酯(tdi)等芳香族二異氰酸酯、二苯基甲烷二異氰酸酯(mdi)等芳香脂肪族二異氰酸酯、或它們的混合物。作為前述增鏈劑,若為分子內含有一個以上活潑氫的化合物則沒有特別限定,可以適用水或胺化合物。作為胺化合物,可列舉出乙二胺、丙二胺、六亞甲基二胺、二亞乙基三胺、二亞丙基三胺、三亞乙基四胺、四亞乙基五胺等脂肪族多胺,亞芐基二胺、苯二甲胺、二氨基二苯基甲烷等芳香族多胺,二氨基環己基甲烷、哌嗪、2,5-二甲基哌嗪、異佛爾酮二胺等脂環式多胺,肼、琥珀酸二酰肼、己二酸二酰肼、鄰苯二甲酸二酰肼等肼類,羥基乙基二亞乙基三胺、2-[(2-氨基乙基)氨基]乙醇、3-氨基丙二醇等烷醇胺等。想要得到水系聚氨酯樹脂的情況下,可列舉出例如在樹脂制造時,將前述多元醇化合物的至少一部分替代為含有羧基的多元醇化合物,與多異氰酸酯化合物反應而向樹脂鏈導入羧基后,用堿中和羧基,形成水系樹脂而成的聚氨酯樹脂。或者可列舉出在樹脂制造時,將前述多元醇化合物的至少一部分替代為分子內具有仲氨基或叔氨基的多元醇化合物,與多異氰酸酯化合物反應而向樹脂鏈導入仲氨基或叔氨基后,用酸中和,形成水系樹脂而成的聚氨酯樹脂。樹脂鏈具有叔氨基的情況下,也可以通過向叔氨基導入烷基而季化,形成具有季銨鹽基的水系陽離子樹脂。這些化合物可以單獨使用或以兩種以上的混合物形式使用。如此,可以用作前述樹脂(a1)的聚氨酯樹脂優選使用分子結構中含有很多芳香環的聚氨酯樹脂。這種聚氨酯樹脂與分子結構中不具有芳香環、或者芳香環少的聚氨酯樹脂相比,玻璃化轉變溫度高,分子鏈剛直且對涂膜變形的抵抗強,涂膜的伸長變形率低,因此,與不具有芳香環或者芳香環少的聚氨酯樹脂相比,本發明中所必要的涂膜(α)的硬度和脆性高。因此,對于樹脂制造中使用的多元醇化合物、多異氰酸酯化合物、增鏈劑沒有特別限制,但是優選使用含有很多芳香環的芳香脂肪族、芳香脂環族等化合物。前述樹脂(a1)中,作為聚酯樹脂,若具有必要的hm和玻璃化轉變溫度tg則沒有特別限定。可列舉出例如乙二醇、1,3-丙二醇、1,2-丙二醇、丙二醇、二甘醇、1,6-己二醇、新戊二醇、三甘醇、雙酚羥基丙基醚、2-甲基-1,3-丙二醇、2,2-二甲基-1,3-丙二醇、2-丁基-2-乙基1,3-丙二醇、1,4-丁二醇、2-甲基-1,4-丁二醇、2-甲基-3-甲基-1,4-丁二醇、1,5-戊二醇、3-甲基-1,5-戊二醇、1,6-己二醇、1,4-環己烷二甲醇、1,3-環己烷二甲醇、1,2-環己烷二甲醇、氫化雙酚-a、二聚物二醇、三羥甲基乙烷、三羥甲基丙烷、甘油、季戊四醇等多元醇,與鄰苯二甲酸、鄰苯二甲酸酐、四氫鄰苯二甲酸、四氫鄰苯二甲酸酐、六氫鄰苯二甲酸、六氫鄰苯二甲酸酐、甲基四鄰苯二甲酸、甲基四氫鄰苯二甲酸酐、間苯二甲酸、對苯二甲酸、琥珀酸酐、己二酸、癸二酸、馬來酸、馬來酸酐、衣康酸、富馬酸、降冰片烯二羧酸酐、偏苯三酸、偏苯三酸酐、均苯四甲酸、均苯四甲酸酐、壬二酸、琥珀酸、琥珀酸酐、乳酸、十二烯基琥珀酸、十二烯基琥珀酸酐、環己烷-1,4-二羧酸、納迪克酸酐等多元羧酸進行脫水縮聚而得到的聚酯樹脂。進而,可列舉出將它們用氨、胺化合物等中和,形成水系樹脂而成的聚酯樹脂等。前述樹脂(a1)中,作為環氧樹脂,若具有必要的hm和玻璃化轉變溫度tg則沒有特別限定。例如使得雙酚a型環氧樹脂、雙酚f型環氧樹脂、間苯二酚型環氧樹脂、氫化雙酚a型環氧樹脂、氫化雙酚f型環氧樹脂、間苯二酚型環氧樹脂、酚醛清漆型環氧樹脂等環氧樹脂與二乙醇胺、n-甲基乙醇胺等胺化合物反應來得到。進而,可列舉出將它們用有機酸或無機酸中和、形成水系樹脂而成的環氧樹脂,在前述環氧樹脂的存在下將高酸值丙烯酸系樹脂自由基聚合后,用氨、胺化合物等中和形成水系化而成的環氧樹脂等。前述樹脂(a1)中,作為(甲基)丙烯酸系樹脂,若具有必要的hm和玻璃化轉變溫度tg則沒有特別限定。可列舉出例如通過使用聚合引發劑,使得(甲基)丙烯酸乙酯、(甲基)丙烯酸2-乙基己酯、(甲基)丙烯酸正丁酯等(甲基)丙烯酸烷基酯,(甲基)丙烯酸2-羥基乙酯等(甲基)丙烯酸羥基烷基酯,(甲基)丙烯酸烷氧基硅烷酯等(甲基)丙烯酸酯與(甲基)丙烯酸一起在水中進行自由基聚合而得到的(甲基)丙烯酸系樹脂。對于前述聚合引發劑沒有特別限定,例如可以使用過硫酸鉀、過硫酸銨等過硫酸鹽,偶氮雙氰基戊酸、偶氮雙異丁腈等偶氮化合物等。在此,“(甲基)丙烯酸酯”指的是丙烯酸酯和甲基丙烯酸酯,“(甲基)丙烯酸”指的是丙烯酸和甲基丙烯酸。前述樹脂(a1)中,作為聚烯烴樹脂,若具有必要的玻璃化轉變溫度tg則沒有特別限定。可列舉出例如乙烯和甲基丙烯酸、丙烯酸、馬來酸、富馬酸、衣康酸、巴豆酸等不飽和羧酸類在高溫高壓下進行自由基聚合而成的聚烯烴樹脂。另外,可列舉出將它們進而用氨、胺化合物、koh、naoh、lioh等堿性金屬化合物或含有前述金屬化合物的氨、胺化合物等中和,形成水系樹脂而成的聚烯烴樹脂等。前述樹脂(a1)可以使用一種或混合兩種以上來使用。另外,作為前述涂裝用組合物(β)的主要成分,可以匯總通過在至少一種樹脂(a1)的存在下、將至少其一部分的樹脂(a1)改性而得到的復合樹脂中的一種或兩種以上來用作樹脂(a1)。<有機樹脂(a)的玻璃化轉變溫度tg>前述有機樹脂(a)的玻璃化轉變溫度tg優選為-80℃~-20℃。玻璃化轉變溫度tg可以通過將形成涂膜的有機樹脂在達到溫度200℃下加熱固化、形成膜厚15μm的薄膜,作為差示掃描量熱計(dsc)的峰溫度或利用動態粘彈性測定機裝置得到的轉變溫度測定。tg優選為-80℃以上且-20℃以下。tg高于-20℃的樹脂由于柔軟性低,緩和隨著因石頭飛濺的碰撞所導致的涂膜的受損而釋放的涂膜的收縮應力傳導到鍍覆層的能力小。對于tg的下限沒有特別規定,但是具有低于-80℃的tg的有機樹脂在工業上難以廉價地獲得。進而,tg優選為-60℃以上且-30℃以下。<導電性顏料(b)>作為導電性顏料(b),優選使用選自金屬、合金、導電性碳、磷化鐵、碳化物、半導體氧化物之中的一種以上。可列舉出例如鋅、鎳、鐵、鋁、鈷、錳、銅、錫、鉻等金屬或它們的合金粉末,導電性碳、石墨粉末等導電性碳粉末,磷化鐵粉末、碳化鈦、碳化硅等碳化物粉末,導電性半導體粉末、陶瓷顆粒等。它們之中,本發明的涂裝金屬板中,特別優選為非氧化物陶瓷顆粒。使用非氧化物陶瓷顆粒的情況下,即使用于得到涂膜(α)的涂裝用組合物(β)為水系組合物的情況下,這些非氧化物陶瓷顆粒在組合物中也不會劣化,恒久地保持高的導電能力。因此,與由于水分而劣化的導電性顆粒、例如賤金屬顆粒、硅鐵合金顆粒等相比,可以在非常長的期間保持優異的電阻焊性。構成本發明的涂膜(α)中含有的非氧化物陶瓷顆粒的非氧化物陶瓷為25℃的電阻率(體積電阻率、比電阻)處于0.1×10-6~185×10-6ωcm的范圍內的硼化物陶瓷、碳化物陶瓷、氮化物陶瓷、或硅化物陶瓷。在此所稱的非氧化物陶瓷指的是包含不含氧的元素、化合物的陶瓷。另外,在此所稱的硼化物陶瓷、碳化物陶瓷、氮化物陶瓷、硅化物陶瓷分別指的是將硼b、碳c、氮n、硅si作為主要的非金屬構成元素的非氧化物陶瓷。它們之中,沒有25℃的電阻率不足0.1×10-6ωcm的物質。另外,非氧化物陶瓷的25℃的電阻率(體積電阻率、比電阻)超過185×10-6cm的情況下,為了對于樹脂涂膜賦予充分的導電性,需要向涂膜大量添加,將本發明的涂裝金屬板壓制成型時,產生顯著的涂膜剝離、粘著,耐蝕性降低,因此不合適。本發明的涂膜(α)中含有的非氧化物陶瓷顆粒由于具有高的導電性,因此用于對樹脂涂膜賦予充分的導電性的添加量可以更少量,其結果,對涂裝金屬板的耐蝕性、成型性的不良影響進一步減小。需要說明的是,僅供參考可知,純金屬的電阻率處于1.6×10-6ωcm(ag單質)~185×10-6ωcm(mn單質)的范圍內,本發明中用作導電性顆粒的非氧化物陶瓷(電阻率0.1×10-6~185×10-6ωcm)具有與純金屬同等程度的優異的導電性。作為本發明中可以使用的非氧化物陶瓷,可例示出以下。即,作為硼化物陶瓷,可例示出周期表的iv族(ti、zr、hf)、v族(v、nb、ta)、vi族(cr、mo、w)各過渡金屬、mn、fe、co、ni、稀土元素、或be、mg以外的堿土金屬(ca、sr、ba)的硼化物。但是,be的硼化物中25℃時的電阻率超過185×10-6ωcm的物質(例如be2b、beb6等)由于導電性能不充分,因此不適于在本發明中適用。另外,mg的硼化物(mg3b2、mgb2等)由于對于水、酸不穩定,因此不適于在本發明中適用。作為碳化物陶瓷,可例示出iv族、v族、vi族的各過渡金屬、mn、fe、co、ni的碳化物。但是,在濕潤氣氛下有可能水解的稀土元素、堿土金屬的碳化物(例如yc2、lac2、cec2、prc2、be2c、mg2c3、src2等)不適于在本發明中適用。作為氮化物陶瓷,可例示出iv族、v族、vi族的各過渡金屬、或mn、fe、co、ni的氮化物。但是,在濕潤氣氛下有可能水解的稀土元素、堿土金屬的氮化物(例如lan、mg3n2、ca3n2等)不適于在本發明中適用。作為硅化物陶瓷,可例示出iv族、v族、vi族的各過渡金屬、或mn、fe、co、ni的硅化物。但是,在濕潤氣氛下有可能與水反應、產生氫的稀土元素、堿土金屬的硅化物(例如lasi、mg2si、srsi2、basi2等)不適于在本發明中適用。進而可例示出選自這些硼化物、碳化物、氮化物、硅化物中的兩種以上的混合物、或將這些陶瓷與金屬的粘合材料混合、燒結而成的金屬陶瓷等。涂膜(α)由水系涂裝用組合物制作的情況下,優選構成金屬陶瓷的一部分的金屬的標準電極電位為-0.3v以上且為耐水劣化性。這是由于,構成金屬陶瓷的一部分的金屬的標準電極電位不足-0.3v的情況下,若該金屬陶瓷顆粒長期存在于水系涂裝用組合物中則在顆粒的表面產生銹層、厚的氧化絕緣層,有可能失去顆粒的導電性。作為耐水劣化性的金屬陶瓷顆粒的例子,可列舉出wc-12co、wc-12ni、tic-20tin-15wc-10mo2c-5ni等。co、ni的標準電極電位分別為-0.28v、-0.25v,都高于-0.3v,任意一種金屬都為耐水劣化性。前述的非氧化物陶瓷中,cr系陶瓷(crb、crb2、cr3c2、cr2n、crsi等)由于擔心對環境負荷,另外,hf系陶瓷(hfb2、hfc、hfn等),與tb相比重稀土側的稀土元素系的陶瓷大部分價格昂貴,另外在市場上不流通,因此本發明中,優選使用由上述組除去了它們的非氧化物陶瓷、或者選自這些中的兩種以上的混合物。進而,從工業產品的有無、國內外市場中的穩定流通性、價格、電阻率等觀點考慮,更優選為以下的非氧化物陶瓷。即,優選使用bab6(電阻率77×10-6ωcm)、ceb6(電阻率30×10-6ωcm)、co2b(電阻率33×10-6ωcm)、cob(電阻率76×10-6ωcm)、feb(電阻率80×10-6ωcm)、gdb4(電阻率31×10-6ωcm)、gdb6(電阻率45×10-6ωcm)、lab4(電阻率12×10-6ωcm)、lab6(電阻率15×10-6ωcm)、mo2b(電阻率40×10-6ωcm)、mob(電阻率35×10-6ωcm)、mob2(電阻率45×10-6ωcm)、mo2b5(電阻率26×10-6ωcm)、nb3b2(電阻率45×10-6ωcm)、nbb(電阻率6.5×10-6ωcm)、nb3b4(電阻率34×10-6ωcm)、nbb2(電阻率10×10-6ωcm)、ndb4(電阻率39×10-6ωcm)、ndb6(電阻率20×10-6ωcm)、prb4(電阻率40×10-6ωcm)、prb6(電阻率20×10-6ωcm)、srb6(電阻率77×10-6ωcm)、tab(電阻率100×10-6ωcm)、tab2(電阻率100×10-6ωcm)、tib(電阻率40×10-6ωcm)、tib2(電阻率28×10-6ωcm)、vb(電阻率35×10-6ωcm)、vb2(電阻率150×10-6ωcm)、w2b5(電阻率80×10-6ωcm)、yb4(電阻率29×10-6ωcm)、yb6(電阻率40×10-6ωcm)、yb12(電阻率95×10-6ωcm)、zrb2(電阻率60×10-6ωcm)、moc(電阻率97×10-6ωcm)、mo2c(電阻率100×10-6ωcm)、nb2c(電阻率144×10-6ωcm)、nbc(電阻率74×10-6ωcm)、ta2c(電阻率49×10-6ωcm)、tac(電阻率30×10-6ωcm)、tic(電阻率180×10-6ωcm)、v2c(電阻率140×10-6ωcm)、vc(電阻率150×10-6ωcm)、wc(電阻率80×10-6ωcm)、w2c(電阻率80×10-6ωcm)、zrc(電阻率70×10-6ωcm)、mo2n(電阻率20×10-6ωcm)、nb2n(電阻率142×10-6ωcm)、nbn(電阻率54×10-6ωcm)、scn(電阻率25×10-6ωcm)、ta2n(電阻率135×10-6ωcm)、tin(電阻率22×10-6ωcm)、zrn(電阻率14×10-6ωcm)、cosi2(電阻率18×10-6ωcm)、mo3si(電阻率22×10-6ωcm)、mo5si3(電阻率46×10-6ωcm)、mosi2(電阻率22×10-6ωcm)、nbsi2(電阻率6.3×10-6ωcm)、ni2si(電阻率20×10-6ωcm)、ta2si(電阻率124×10-6ωcm)、tasi2(電阻率8.5×10-6ωcm)、tisi(電阻率63×10-6ωcm)、tisi2(電阻率123×10-6ωcm)、v5si3(電阻率115×10-6ωcm)、vsi2(電阻率9.5×10-6ωcm)、w3si(電阻率93×10-6ωcm)、wsi2(電阻率33×10-6ωcm)、zrsi(電阻率49×10-6ωcm)、zrsi2(電阻率76×10-6ωcm)、或選自它們中的兩種以上的混合物。它們之中,特別優選為25℃的電阻率處于0.1×10-6~100×10-6ωcm的范圍內的非氧化物陶瓷。因為它們與25℃的電阻率處于超過100×10-6ωcm直至185×10-6ωcm為止的范圍內的非氧化物陶瓷相比,具有高的導電性,因此用于對樹脂涂膜賦予充分的導電性的顆粒添加量可以為更少的量,僅形成貫通涂膜的腐蝕電流的導通路,耐蝕性幾乎沒有降低。另外是因為,由于顆粒添加少量,因此在壓制成型時不會誘發涂膜剝離、粘著,成型性幾乎不會降低。前述的非氧化物陶瓷的附注于括弧內的電阻率分別為作為工業用原材料銷售、使用的非氧化物陶瓷的代表值(文獻值)。這些電阻率由于根據進入到非氧化物陶瓷的晶格的雜質元素的種類、量而增減,因此在本發明中使用時,例如可以通過使用了mitsubishichemicalanalytechco.,ltd.制的電阻率計lorestaep(mcp-t360型)和esp探頭(端子的平頭部的直徑2mm)的四端子四探針法、恒定電流施加方式,根據jisk7194,實際測定25℃的電阻率,確認處于0.1×10-6~185×10-6ωcm的范圍內后來使用。前述導電性顏料(b)的顆粒形狀優選為球狀顆粒、或偽球狀顆粒(例如橢圓球體狀、雞蛋狀、橄欖球狀等)、多面體顆粒(例如足球狀、骰子狀、各種寶石的磨光刻花形狀等)等接近于球的形狀。細長的形狀(例如棒狀、針狀、纖維狀等)、平面形狀(例如小片狀、平板狀、薄片狀等)的顆粒在涂裝過程中平行排列于涂膜面或者沉積于作為涂裝用基材的金屬板(在金屬面存在基底處理的情況下為基底處理層)與涂膜的界面附近而難以形成貫通涂膜的厚度方向的有效的通電路,因此不適于本發明的用途。對于前述導電性顏料(b)的平均粒徑沒有特別限定,但是本發明的涂裝用組合物(β)中,優選以體積平均直徑0.2~20μm的顆粒存在、更優選以體積平均直徑0.5~12μm的顆粒存在、特別優選以體積平均直徑1~8μm的顆粒存在。具有這些體積平均直徑的分散顆粒若在涂裝用組合物(β)的制造工序、保管·搬運時、對作為涂裝用基材的金屬板(在金屬面存在基底處理的情況下為基底處理層)的涂裝工序等中穩定地存在于涂裝用組合物(β)中則可以為單一顆粒或多個單一顆粒強力聚集而成的二次顆粒。涂裝用組合物對基材的涂裝工序中,在涂膜的干燥、制膜時,前述(b)顆粒聚集、涂膜中的體積平均直徑增大也沒有影響。需要說明的是,在此所稱的體積平均直徑指的是由顆粒的體積分布數據求出的體積基準的平均直徑。其可以使用通常已知的任意的粒徑分布測定方法求出,但是優選使用通過庫爾特法(細孔電阻法)測定的球體積相當直徑分布的平均值。這是由于,庫爾特法與其它的粒徑分布測定方法(例如(a)由通過激光衍射散射法得到的體積分布算出、(b)將通過圖像解析法得到的圓面積相當直徑分布換算為體積分布、(c)由通過離心沉降法得到的質量分布算出等)相比,幾乎沒有根據測定機廠商、機型不同而測定值不同,可以正確地進行高精度的測定。庫爾特法中,在電解質水溶液中懸浮受試顆粒,在玻璃管的細孔流通恒定的電流,進行設定從而通過負壓而顆粒通過細孔。若顆粒通過細孔則由于排除了顆粒的電解質水溶液的體積(=顆粒的體積),而細孔的電阻增加。若施加恒定電流則顆粒通過時的電阻變化被電壓脈沖變化反映,因此通過對每1個該電壓脈沖高度進行測定處理,就可以直接測定各顆粒的體積。顆粒為不規則形狀的情況多,因此假定與顆粒相同體積的球體,換算為該球體的直徑(=球體積相當直徑)。熟知這種利用庫爾特法的球體積相當直徑的測定方法,例如詳細記載于文獻:beckmancoulter,inc.互聯網公式網站上的網頁[http://www.beckmancoulter.co.jp/product/product03/multisizer3.html(精密粒度分布測定裝置multisizer3)]。體積平均直徑不足0.2μm的非氧化物陶瓷顆粒與體積平均直徑大于此的非氧化物陶瓷顆粒相比通常昂貴,作為工業產品在市場上流通的情況少。另外,由于比表面積比較大,因此制造水系或有機溶劑系的涂裝用組合物時,即使使用濕潤分散劑也難以將顆粒表面整體潤濕、進行分散,產生不溶于水、有機溶劑的面塊、面團的情況多,因此本發明中不使用為宜。另外,體積平均直徑超過20μm的非氧化物陶瓷顆粒與體積平均直徑小于此的非氧化物陶瓷顆粒相比,在水系或有機溶劑系的涂裝用組合物中容易快速沉降(通過斯托克斯式子可知)。因此,即使設法選擇分散劑也難以確保分散穩定性,顆粒不會漂浮而短時間內沉降,有可能產生聚集·固化、難以再分散等不良問題,因此本發明中不使用為宜。能夠獲得的導電性顏料(b)由于通常大多將原料粉碎、根據需要進行分級而制造為規定的粒徑,因此具有粒徑不同的顆粒混合而成的粒徑分布。因此,即使體積平均直徑處于上述的粒徑范圍中、也會由于其粒徑分布而對焊接性造成影響。導電性顏料(b)中各自的體積粒徑為0.25~24μm的(b1)對于良好的焊接性尤其表現出效果。涂膜(α)中的導電性顏料(b)的25℃時的含量優選為0.5~65體積%,從電阻焊時的電導通性、成型性確保以及由于導電性顏料增加所導致的成本增加的觀點考慮,更優選為1~40體積%、進一步優選2~20體積%。從除了確保充分的耐蝕性和成型性之外、還確保充分的電阻焊性的觀點考慮,特別優選處于4~20體積%的范圍內。本發明的涂裝金屬板中,涂膜(α)表現出良好的導電性的理由認為在于,涂膜(α)中,作為導電性顆粒的導電性顏料(b)幾乎不會聚集,在涂膜面整體充分均勻地分散,對處于下方的金屬板的電導通路不會不均勻存在于涂膜內。若導電性顆粒在涂膜內產生聚集則難以在涂膜內形成在涂膜面整體均勻地散布的狀態的電導通路,在涂膜內容易產生完全沒有電導通路的對電阻焊造成障礙的區域。在那樣的情況下,為了確保導通路就必須添加更多的導電材料,從而升高不能保持良好的耐蝕性和成型性的可能性升高。本發明的涂裝金屬板中,產生這種問題的可能性非常低。若涂膜(α)中的導電性顏料(b)的含量超過65體積%則可以保持充分的導電性,但是在壓制成型時容易產生涂膜剝離、粘著,不能保持良好的成型性,涂膜剝離部位的耐蝕性有可能降低。另外,若超過65體積%則盡管焊接性的提高效果飽和,但是導電性顆粒的成本升高。需要說明的是,添加涂膜的0.5體積%以上且不足1體積%的導電性顆粒時,電阻焊時的電導通性有可能不充分,另外添加涂膜的40體積%以上且65體積%以下的導電性顆粒時,成型性和成本適合性有可能不充分,因此更優選為導電性顏料(b)的體積比為1體積%以上直至不足40體積%為止的添加。另外,即使添加涂膜的1體積%以上且不足2體積%的導電性顆粒、電阻焊時的電導通性也有可能稍微不充分,另外即使添加涂膜的20體積%以上且不足40體積%的導電性顆粒、成型性和成本適合性也有可能稍微不充分,因此進一步優選為2體積%以上直至不足20體積%為止的添加。但是,添加涂膜的2體積%以上且不足4體積%的導電性顆粒時,大幅改變電阻焊條件的情況下,有可能不能總是確保高且穩定的焊接性,因此特別優選為4體積%以上且不足20體積%的添加。涂膜(α)中的導電性顏料(b)的含量不足0.5體積%的情況下,分散于涂膜中的非氧化物陶瓷顆粒的量少,因此不能確保良好的導電性,根據涂膜(α)的厚度,有可能不能對涂膜賦予充分的電阻焊性。<防銹顏料(c)>作為本發明中使用的防銹顏料(c)的種類,沒有特別限定,但是優選含有選自硅酸鹽化合物、磷酸鹽化合物、釩酸鹽化合物和金屬氧化物微粒中的一種或兩種以上。硅酸鹽化合物、磷酸鹽化合物、釩酸鹽化合物在涂裝用組合物(β)、涂膜(α)中,根據該組合物、涂膜中的水分、與共存物質、基材面的接觸、ph等環境變化,可以分別釋放硅酸根離子、磷酸根離子、釩酸根離子、和這些陰離子的抗衡陽離子(例如堿土金屬離子、zn離子、al離子等)。認為,對于這些離子中已經在涂裝用組合物(β)中溶出的離子,在制膜時被引進到涂膜(α),根據涂膜內的水分的增減、與共存物質、基材面的接觸、ph變化等,與共存的其它的原子、原子團形成難溶性鹽、氧化物的覆膜,抑制腐蝕。另外認為,被引進到涂膜(α)的硅酸鹽化合物、磷酸鹽化合物、釩酸鹽化合物的情況也同樣地,根據涂膜形成后的環境變化,緩慢釋放上述的陰離子、陽離子,形成難溶性鹽、氧化物的覆膜,抑制腐蝕。上述的作用即使在涂膜受損、金屬板的鍍覆覆膜或鍍層之下的基底金屬露出的情況下,也會通過硅酸根離子、磷酸根離子、釩酸根離子、和這些陰離子的抗衡陽離子被釋放并且到達所露出的鍍覆覆膜或基底金屬的表面而得以發揮作用。在受損的程度被抑制得小、鍍覆覆膜或基底金屬的露出面積被限定得小的情況下,該作用進一步有效地發揮。作為本發明中可以使用的硅酸鹽化合物,可列舉出例如硅酸鎂、硅酸鈣等堿土金屬的硅酸鹽,硅酸鋰、硅酸鈉、硅酸鉀等堿金屬的硅酸鹽,硅酸鋁等。它們之中,作為硅酸鋰、硅酸鈉、硅酸鉀,可例示出氧化硅(sio2)與氧化鋰(li2o)的構成摩爾比率為0.5≤(sio2/li2o)≤8的硅酸鋰、氧化硅(sio2)與氧化鈉(na2o)的構成摩爾比率為0.5≤(sio2/na2o)≤4的硅酸鈉、氧化硅(sio2)與氧化鉀(k2o)的構成摩爾比率為0.5≤(sio2/k2o)≤4的硅酸鉀、和這些硅酸鹽的水合物。作為它們的具體例,可列舉出原硅酸鋰(li4sio4;2li2o·sio2)、原二硅酸六鋰(li6si2o7;3li2o·2sio2)、偏硅酸鋰(li2sio3;li2o·sio2)、二硅酸鋰(li2si2o5;li2o·2sio2)、七硅酸四鋰(2li2o·7sio2)、四硅酸鋰(li2si4o9;li2o·4sio2)、九硅酸四鋰(2li2o·9sio2)、十五硅酸四鋰(2li2o·15sio2)、以及原硅酸鈉(na4sio4;2na2o·sio2)、偏硅酸鈉(na2sio3;na2o·sio2)、二硅酸鈉(na2si2o5;na2o·2sio2)、四硅酸鈉(na2si4o9;na2o·4sio2)、原硅酸鉀(k4sio4;2k2o·sio2)、偏硅酸鉀(k2sio3;k2o·sio2)、二硅酸鉀(k2si2o5;k2o·2sio2)、四硅酸鉀(k2si4o9;k2o·4sio2)、和這些硅酸鹽的水合物。需要說明的是,這些硅酸鹽的水合物大部分根據ph、溫度等環境變化而在水合狀態下容易地凝膠化,存在一部分高分子化而形成聚硅酸鹽的情況。可以適用于本發明的硅酸鹽化合物中也包括這種聚硅酸鹽。作為本發明中可以使用的磷酸鹽化合物,可列舉出例如正磷酸、多磷酸(單獨的直至正磷酸的聚合度6為止的直鏈狀聚合物、或它們的兩種以上的混合物)、偏磷酸(單獨的直至正磷酸的聚合度3~6為止的環狀聚合物、或它們的兩種以上的混合物)、四偏磷酸、六偏磷酸等的金屬鹽、五氧化磷、三斜磷鈣石、磷酸鋰鐵礦、白磷鈣石、磷釔礦、磷鈉銨石、鳥糞石、藍鐵礦石等磷酸鹽礦物,多磷酸二氧化硅、三多磷酸鹽等市售的復合磷酸鹽顏料,植酸、膦酸(亞磷酸)、次膦酸(次磷酸)等的金屬鹽,或它們的兩種以上的混合物等。在此所稱的正磷酸鹽也包括其一氫鹽(hpo42-)的鹽、二氫鹽(h2po4-)。另外,多磷酸鹽包括氫鹽。作為形成磷酸鹽的陽離子種類,沒有特別限制,可列舉出例如co、cu、fe、mn、nb、ni、sn、ti、v、y、zr、al、ba、ca、mg、sr和zn等金屬離子,氧釩基、氧鈦基、氧鋯基等氧代陽離子,但是優選使用al、ca、mg、mn、ni。前述磷酸鹽化合物可以單獨使用或組合使用兩種以上。作為形成磷酸鹽的陽離子種類,不優選使用大量堿金屬。使用堿金屬的磷酸鹽的情況下,存在通過工業上的制造工序焙燒而得到的生成物過度溶解于水的傾向。但是,使用堿金屬的磷酸鹽的情況下,若可以在防銹顏料制造時、涂裝用組合物的制造時、對金屬板的制膜時、或涂裝金屬板的使用時等實施對水的溶解性的控制則可以稍微多地使用。這種控制,可列舉出例如使得防銹顏料與抑制對水的溶解性的其它添加劑共存或者與高度交聯的樹脂系、無機系的高分子共存來控制對水的溶出速度等方法。本發明中可以使用的釩酸鹽化合物為釩的原子價具有0、2、3、4或5中的任意一種價數、或兩種以上價數的復合化合物,可列舉出例如它們的氧化物、氫氧化物、各種金屬的含氧酸鹽、氧釩基化合物、鹵化物、硫酸鹽、金屬粉等。它們在加熱時或水的存在下分解、與共存的氧反應。例如釩的金屬粉或二價化合物最終變化為3、4、5價中的任意一種的化合物。0價的物質例如釩金屬粉可以因上述理由使用,但是存在氧化反應不充分等問題,因此實用上不優選。5價的釩化合物具有釩酸根離子,與磷酸根離子加熱反應,容易制作有助于防銹的雜聚物,因此優選含有5價的釩化合物作為一種成分。作為釩化合物的具體例,可列舉出氧化釩(ii)、氫氧化釩(ii)等釩(ii)化合物,氧化釩(iii)等釩(iii)化合物,氧化釩(iv)、鹵化氧釩基等釩(iv)化合物,氧化釩(v)、釩酸鹽(各種金屬的原釩酸鹽、偏釩酸鹽、焦釩酸鹽等)等釩(v)化合物、或它們的混合物。構成釩酸鹽的優選的金屬種類與磷酸鹽所示的金屬相同。使用堿金屬的釩酸鹽的情況下,存在通過工業上的制造工序焙燒而得到的生成物過度溶解于水的傾向,因此與磷酸鹽的情況同樣地不優選使用大量的堿金屬的釩酸鹽。但是若與使用堿金屬的磷酸鹽的情況同樣地控制對水的溶解性則也可以使用它們。釩的鹵化物、硫酸鹽的情況也同樣。本發明的涂裝金屬板中,前述硅酸鹽化合物、磷酸鹽化合物、釩酸鹽化合物的總量為涂膜(α)的1~40體積%、優選1~20體積%、更優選2~15體積%。不足1體積%時,硅酸鹽化合物、磷酸鹽化合物、釩酸鹽化合物的作用不充分,因此耐蝕性有可能降低。若超過20體積%則涂膜變脆,有可能由于涂膜內聚破壞而成型時的涂膜密合性、涂膜追隨性降低或者焊接性降低。防銹顏料(c)優選含有硅酸鹽化合物、磷酸鹽化合物、釩酸鹽化合物中的一種或兩種以上,但是磷酸鹽化合物(磷酸根離子源)和硅酸鹽化合物(硅酸根離子源)或釩酸鹽化合物(釩酸根離子源)中的至少一種共存,在提高防銹效果上更優選。所配混的磷酸根離子源與硅酸根離子源、釩酸根離子源的總量之比,更優選[p2o5的摩爾數]:[sio2和v2o5的總摩爾數]的比率為25:75~99:1。若硅酸根離子源和釩酸根離子源的總量與磷酸根離子源、硅酸根離子源、釩酸根離子源的總量的摩爾比超過75%則利用磷酸根離子實現的防銹效果有可能降低,硅酸根離子源和釩酸根離子源的總量的摩爾比少于1%的情況下,利用硅酸根離子(或釩酸根離子)實現的周邊化學種的氧化、固定效果有可能不充分。除了上述之外,作為本發明中使用的防銹顏料(c),還可以使用包含選自由si、ti、al、zr組成的組中的一種或兩種以上的金屬元素的金屬氧化物微粒。通過將這些金屬氧化物微粒單獨使用或者與硅酸鹽化合物、磷酸鹽化合物、釩酸鹽化合物一起配混,可以進一步提高耐蝕性。若硅酸鹽化合物、磷酸鹽化合物、釩酸鹽化合物和二氧化硅共存則耐蝕性進一步提高,因此優選。作為二氧化硅,可列舉出例如氣相二氧化硅、膠態二氧化硅、聚集二氧化硅等。另外,也可以使用鈣沉積二氧化硅。作為本發明中可以使用的前述金屬氧化物微粒,可列舉出例如體積平均直徑為0.2~10μm左右的二氧化硅微粒、氧化鋁微粒、二氧化鈦微粒、氧化鋯微粒等,進一步優選為體積平均直徑0.5~30nm左右的金屬氧化物納米微粒。它們可以單獨使用或組合使用兩種以上。它們之中,二氧化硅納米微粒可以在需要涂膜的耐蝕性提高和增韌這兩者的情況下添加。作為粒徑為0.5nm以上且不足30nm的金屬氧化物納米微粒,例如可以使用膠態二氧化硅、膠態二氧化鈦、膠態氧化鋯。它們由于制法與通過粉碎將上述金屬氧化物微粒化而成的微粒不同,因此在微細的一次顆粒粒徑(0.5nm~30nm)的狀態下容易分散于涂料中和涂裝后的涂裝金屬材料的涂膜中。這些金屬氧化物納米微粒與粒徑更大的相同組成的金屬氧化物微粒相比,防銹效果高。但是,這種金屬氧化物納米微粒在例如點焊等用電極施加負荷的同時通電、利用焦耳熱進行焊接的通電電阻焊中有可能阻礙焊接性。金屬氧化物納米微粒的量優選涂膜中的金屬氧化物納米微粒的總體積與非氧化陶瓷顆粒(b)的總體積之比(金屬氧化物納米微粒/b)為20以下。重視焊接性的情況下,更優選為10以下。作為(金屬氧化物納米微粒/b)的下限,優選為0.1以上。(金屬氧化物納米微粒/b)不足0.1時,為涂膜中的非氧化陶瓷顆粒(b)過多或金屬氧化物納米微粒過少的狀態。對于前者而言,涂膜中的非氧化陶瓷顆粒(b)的量過多,因此涂膜變脆,有可能產生成型時的涂膜破裂、涂膜脫落。涂膜破裂、涂膜脫落導致利用涂膜實現的耐蝕性的降低、涂裝金屬板的外觀不良。對于后者而言,涂膜中的金屬氧化物納米微粒的量不充分,因此有可能不能充分得到提高耐蝕性的效果。由于為了確保焊接性、抑制金屬氧化物納米微粒的量而降低的防銹性,可以通過添加粒徑100nm以上的防銹顏料(c)來補充。粒徑100nm以上的防銹顏料(c)在涂膜涂布于金屬板上的狀態、或由于焊接電極所致的負荷而涂膜變形的狀態下,不易進入到電極與(b)、(b)之間、或(b)與金屬板之間,因此與金屬氧化物納米微粒相比,對通電電阻焊的不良影響小。前述防銹顏料(c)的量優選為涂膜(α)的1~40體積%并且與導電性顏料(b)的量的總計不超過80體積%。重視涂裝金屬板的耐蝕性的情況下,更優選防銹顏料(c)的量為3~40體積%、進一步優選7.5~40體積%。進而進一步重視涂裝金屬板的耐蝕性的情況下,更優選防銹顏料(c)的量為13~40體積%。不足1體積%時,防銹顏料(c)的量不充分,因此有可能不能充分得到提高耐蝕性的效果。若超過40體積%則由于涂膜的脆化、對金屬板的涂膜密合性降低,因此產生由于成型時的涂膜破壞、涂膜剝離所導致的金屬板的露出,有可能產生涂裝金屬板的外觀劣化、利用涂膜實現的耐蝕性提高效果降低。導電性顏料(b)的量、防銹顏料(c)的量可以對涂膜截面進行電子顯微鏡觀察,識別各顆粒后,對每截面的個數進行計數,換算為涂膜單位體積的個數后算出。此時,根據需要可以使用edx分光裝置等識別各顆粒。也可以由涂裝前的涂料中含有的(b)、(c)的量和對金屬板的涂膜附著量算出涂膜中的各顆粒量。若判明涂裝前的涂料中的(b)、(c)的投料量則可以由投料量和對金屬板的涂料附著量算出涂膜中的各顆粒量。不清楚投料量的情況下,例如可以通過使用malvern公司制的顆粒圖像解析裝置morphologig3等裝置,利用圖像解析對于稀釋到適當濃度的涂料中的顆粒分別進行識別、計數來算出。該手法也可以用于將附著于金屬板的涂膜溶解、對顆粒的個數進行計數的情況。但是涂膜(α)中的導電性顏料(b)的量、防銹顏料(c)的量即使基于有機樹脂(a)、導電性顏料(b)、防銹顏料(c)的配混比、干燥后的各比重算出,也應該成為與通過截面觀察來測定的情況相同的測定值,因此也可以簡便地利用由配混比算出的方法。前述各種防銹顏料優選適量預先溶解或分散穩定化于涂裝用組合物(β)中而導入到涂膜(α)中的有機樹脂(a)。<顆粒(d)>除了上述導電性顏料(b)、防銹顏料(c)之外,作為本發明的涂膜中的顆粒,還可以含有40℃時的馬氏硬度為200mg/mm2~200000mg/mm2的粒狀的蠟、樹脂珠等顆粒(d)。40℃時的馬氏硬度為200mg/mm2~200000mg/mm2的粒狀的蠟、樹脂珠可以考慮到對涂料的添加的容易性等來任意選擇。例如可以使用聚烯烴蠟、聚乙烯蠟、聚丙烯蠟、聚丁烯蠟、改性聚烯烴蠟、丙烯酸系樹脂顆粒、有機硅樹脂顆粒、氟樹脂顆粒、聚丙烯腈樹脂等。顆粒(d)的40℃時的馬氏硬度不足200mg/mm2的情況下,本發明的涂裝金屬板的表面之間、或者與其它的原材料、器具·工具接觸的情況下,與樹脂(a)相比優先接觸,防止涂膜(α)對于它們粘合或熔融的效果小。40℃時的馬氏硬度超過200000mg/mm2的顆粒(d)難以在工業上容易地找到,實質上為hm的上限。進而,馬氏硬度的硬度范圍更優選處于300mg/m2以上且2000mg/m2以下的范圍內。選自上述的導電性顏料(b)、防銹顏料(c)和顆粒(d)中的、一次顆粒的直徑為1μm~10μm的顆粒作為顆粒(p)。顆粒(p)包含導電性顏料(b)、防銹顏料(c)中的至少一種,根據需要可以含有顆粒(d)。顆粒(p)的露出狀態、及其粒徑可以通過由涂裝金屬板的上方或者對截面進行顯微鏡觀察來確認。所露出的顆粒(p)的密度也可以通過由涂裝金屬板的上方觀察來確認。或者若顆粒(p)的原材料的粒徑、顆粒數已知則可以由涂料中的配混量算出。在涂膜(α)的表面露出的顆粒(p)的40℃時的最小馬氏硬度hm為200~200000(mg/mm2),構成涂膜(α)表面的至少一部分。根據發明人的研究,在涂膜(α)的表面露出的顆粒(p)與構成涂膜(α)的樹脂(a)相比不易變形,因此本發明的涂裝金屬板的表面之間、或者與其它的原材料、器具·工具接觸的情況下,顆粒(p)與涂膜(α)相比優先地接觸,可以防止涂膜(α)對于它們粘合或熔融。圖7以示意圖的形式表示顆粒(p)由涂膜(α)露出的狀態。為了在與其它原材料接觸時顆粒(p)與涂膜(α)相比優先地接觸,干燥后的涂膜的厚度(t)和顆粒(p)的粒徑(r)的關系優選滿足下式:t/r=0.6~2.5(式中,r為前述顆粒p的體積平均粒徑(μm))。若t/r不足0.6則顆粒(p)的各顆粒大部分由涂膜(α)突出,因此顆粒(p)容易脫落,顆粒(p)沒有充分發揮效果或者所脫落的顆粒(p)混入到工序而容易產生品質上的問題,因此不優選。另外,若超過2.5則顆粒(p)由涂膜(α)的露出不充分,防止粘合或熔融的效果低,因此不優選。顆粒(p)的一次顆粒的直徑為1μm~10μm、露出密度為100~2.0×106個/mm2的情況下,其效果顯著。優選露出密度為1.0×103個~2.0×105個/mm2的情況,進一步優選露出密度為5.0×103個~2.0×104個/mm2的情況。一次顆粒的直徑不足1μm的情況下,顆粒(p)埋沒于涂膜(α)之中,因此難以發揮顆粒(p)優先接觸等作用。一次顆粒的直徑超過10μm的情況下,顆粒(p)難以穩定地存在于用于形成涂膜(α)的涂料中,涂料保管、涂布的經濟性變差。顆粒(p)的露出密度不足100個/mm2的情況下,其密度過低,因此難以發揮顆粒(p)優先接觸等作用。露出密度超過2.0×106個/mm2、達到大量的程度的情況下,涂膜(α)中的顆粒(p)的量過多,因此涂膜容易剝離,產生難以涂布等問題。<涂裝用組合物(β)的制造>對于用于形成本發明的涂膜(α)的涂裝用組合物(β)的制造方法沒有特別限定。可列舉出例如向水中或有機溶劑中添加各涂膜(α)形成成分,用散布機等分散機進行攪拌,進行溶解、分散或破碎分散的方法。水系涂裝用組合物的情況下,為了提高各涂膜(α)形成成分的溶解性或分散性,根據需要可以添加公知的親水性溶劑等。特別是水系涂裝用組合物(β)的情況下,可以向前述樹脂(a1)、前述導電性顏料(b)、防銹顏料(c)中,根據需要除了上述顆粒(d)之外,在不會損害涂料的水性、涂布性的范圍內添加各種水溶性或水分散性的添加劑。例如可以添加沒有形成顏料形態的水溶性或水分散性的各種防銹劑、消泡劑、防沉降劑、流平劑、濕潤分散劑等表面活性劑、以及增稠劑、粘度調整劑等。進而,為了樹脂、其它有機化合物等涂裝用組合物(β)的構成成分的穩定化等,可以在不符合由勞動安全衛生法施行令(有機溶劑中毒預防規則第一章第一條)定義的有機溶劑等(第一種有機溶劑、第二種有機溶劑、第三種有機溶劑、或含有超過5質量%的前述有機溶劑的情況)的范圍內添加少量的有機溶劑。本發明的涂膜(α)由水系涂裝用組合物(β)形成的情況下,由于為水系,因此與有機溶劑系涂裝用組合物相比,表面張力高,對作為基材的金屬板(存在基底處理的情況下為基底處理層)、導電性顏料(b)、防銹顏料(c)、顆粒(d)等的潤濕性變差,對于基材進行規定量的涂布的情況下,有可能得不到均勻的涂裝性、顆粒分散性。這種情況下,添加前述的濕潤分散劑、增稠劑為宜。作為濕潤分散劑,可以使用使得表面張力降低的表面活性劑,使用分子量為2000以上的高分子表面活性劑(高分子分散劑)為宜。低分子表面活性劑由于可以在含有濕氣的樹脂涂膜中比較容易地移動,因此容易將吸附于表面活性劑的極性基團的水、介由該水將溶解氧、溶解鹽等腐蝕因子引入到金屬面,另外自身容易滲出而溶出,因此大多使得涂膜的防銹性劣化。與此相對,高分子表面活性劑由于可以多點吸附于金屬、陶瓷顆粒、顏料的表面,若一旦吸附則不易分離,即使濃度低、對于潤濕性改善也是有效的。并且,由于分子膨松而不易在樹脂涂膜中移動、不易將腐蝕因子引入到金屬面。前述<有機樹脂(a)>的項中,在推薦對有機樹脂(a)添加的丙烯酸系樹脂的一部分具有這種高分子表面活性劑的功能,具有在水系涂裝用組合物中,抑制導電性顏料(b)、防銹顏料(c)、顆粒(d)等的沉降并且進行均勻地分散的效果。增稠劑可以作為對于基材表面的排斥部位僅利用濕潤分散劑時得不到充分的表面覆蓋性的情況、或者水系涂裝用組合物的粘度過低而不能確保必要的涂膜厚度的情況的對策而添加。分子量大多為數千~數萬,多點吸附于顏料等的表面,增稠劑自身互相結合而形成弱的網眼結構,從而可以提高涂裝用組合物的粘度。水系涂裝用組合物(β)含有高比重的導電性顏料(b)、防銹顏料(c)、顆粒(d)的情況下,根據需要可以向涂料添加可以賦予觸變的性質(揺溶性)的粘度調整劑。粘度調整劑與前述增稠劑的情況同樣地,在水系涂裝用組合物中多點吸附于顏料等的表面,形成網眼結構。這種粘度調整劑的分子量為數十萬~數百萬、非常高,因此在水系涂裝用組合物(β)中形成具有大的屈服值的牢固的網眼結構,因此,涂裝用組合物(β)在低剪切速度下不易變形、粘度高。若對于涂裝用組合物(β)施加提高屈服值的大的剪切應力則網眼結構損壞而粘度急劇降低。因此若添加粘度調整劑則在水系涂裝用組合物(β)保持大致靜止狀態的保管時、運送時,提高涂裝用組合物(β)的粘度而抑制重質顏料類的沉降,在涂裝工廠中在配管內流通時、對基材的涂裝時等施加高的剪切應力(高剪切速度)時,使涂裝用組合物(β)的粘度降低而容易流動。有機溶劑系的涂裝用組合物(β)的情況下,在使樹脂溶解于有機溶劑而成的涂裝用組合物的粘度比較高并且容易調整粘度。因此,可以將涂裝用組合物粘度容易且穩定地保持于對于顏料沉降抑制而言有利的100mpa·s以上。另外,用作導電性材料的非氧化物陶瓷為在表面也具有疏水性部位的物質,因此通常對于有機溶劑系的涂裝用組合物(β)的分散也容易,涂布時可以使涂裝用組合物(β)中的導電性顏料(b)不會沉降地進行涂裝,因此是合適的。若將形成涂膜的有機溶劑系的涂裝用組合物(β)的粘度為100~2000mpa·s的涂裝用組合物利用輥涂機或簾涂機涂布于金屬板上后進行干燥燒結,則導電性顏料(b)不易沉降而更優選。若涂裝用組合物(β)的粘度不足100mpa·s,則導電性顏料(b)容易沉降,超過2000mpa·s的情況下,有可能粘度過高而產生通常被稱為膏化(livering)等的涂裝時的外觀不良。更優選為250~1000mpa·s。有機溶劑系的涂裝用組合物(β)的粘度可以在與用輥涂機或簾涂機涂布時的涂裝用組合物的溫度相同的溫度下使用b型粘度計測定。粘度調整可以通過所使用的有機溶劑的種類、溶劑量調整。有機溶劑通常可以使用公知的溶劑,但是優選為沸點高的有機溶劑。本發明的金屬板的生產線中,由于燒結時間短,因此若使用沸點低的溶劑則有可能產生通常被稱為沸騰(boiling)的涂裝缺陷。對于溶劑的沸點而言,優選使用120℃以上的有機溶劑。作為這些沸點高的有機溶劑,可以使用公知的溶劑、例如環己烷、作為芳香族烴系有機溶劑的solvesso(exxonmobilcorporation的產品名)等。<涂膜(α)的形成>本發明的前述涂膜(α),如<涂膜(α)>的項所述,涂裝用組合物(β)為水系、有機溶劑系組合物的情況下,優選為使用輥涂、有槽輥涂布、簾流涂布、卷簾涂布、浸漬(dip)、氣刀軋液等公知的涂裝方法在金屬板上涂布涂裝用組合物(β),然后,將濕式涂膜的水分、溶劑成分干燥的制膜方法。它們之中,水系、有機溶劑系的紫外線固化型組合物、電子束固化型組合物的情況下,優選用前述涂布方法涂布于金屬板之后,將水分或溶劑成分干燥,照射紫外線、電子束進行聚合。對于涂裝用組合物(β)為水系或有機溶劑系的燒結固化型組合物的情況的燒結干燥方法進行具體說明。涂裝用組合物(β)為水系或有機溶劑系的燒結固化型組合物的情況下,對于燒結干燥方法沒有特別限制,可以預先將金屬板加熱、或在涂布后將金屬板加熱、或組合它們進行干燥。對于加熱方法沒有特別限制,可以單獨使用或組合使用熱風、感應加熱、近紅外線、直火等。對于燒結干燥溫度,涂裝用組合物(β)為水系的燒結固化型組合物的情況下,按金屬板表面達到溫度計優選為120℃~250℃。達到溫度低于120℃時,涂膜固化不充分,耐蝕性有可能降低,若超過250℃則燒結固化過度,耐蝕性、成型性有可能降低。燒結干燥時間優選為1~60秒、進一步優選為3~20秒。若不足1秒則燒結固化不充分,耐蝕性有可能降低,若超過60秒則生產率有可能降低。涂裝用組合物(β)為有機溶劑系的燒結固化型組合物的情況下,優選金屬板表面達到溫度為180℃~260℃。達到溫度低于180℃時,涂膜固化不充分,耐蝕性有可能降低,若超過260℃則燒結固化過度,耐蝕性、成型性有可能降低。燒結干燥時間優選為10~80秒、進一步優選40~60秒。若不足10秒則燒結固化不充分,耐蝕性有可能降低,若超過80秒則生產率有可能降低。對于涂裝用組合物(β)為水系或有機溶劑系的紫外線固化型組合物、電子束固化型組合物的情況的制膜方法進行具體說明。將這些組合物通過與前述的水系、有機溶劑系組合物的情況相同的方法涂布后,將濕式涂膜的水分、溶劑成分干燥,然后照射紫外線或電子束。涂膜由于主要將利用紫外線或電子束照射而生成的自由基作為起點進行固化制膜,因此,對于干燥溫度而言,與燒結固化型組合物的情況相比可以為低的干燥溫度。干燥工序中,優選在80~120℃左右的比較低的金屬表面達到溫度下使得水分、溶劑的大部分揮發后,進行紫外線或電子束照射。利用紫外線將涂膜中的紫外線固化型樹脂進行自由基聚合、進行固化的紫外線照射通常在大氣氣氛中、非活性氣體氣氛中、大氣和非活性氣體的混合氣氛中等進行。本發明的紫外線固化中,優選在氧濃度調整到10體積%以下的大氣和非活性氣體的混合氣氛、非活性氣體氣氛中進行紫外線照射。由于氧成為自由基聚合的阻聚劑,因此紫外線照射時的氣氛氧濃度低的情況下,由于對生成自由基的氧化所導致的失活、交聯反應阻礙少,本發明中使用的紫外線固化型組合物經過自由基聚合、交聯而充分高分子化。因此,對導電性顏料(b)、金屬板表面的密合性提高,作為結果,與大氣氣氛中的紫外線固化的情況相比,涂膜的耐蝕性提高。作為在此使用的非活性氣體,可例示出氮氣、二氧化碳、氬氣、和它們的混合氣體等。作為紫外光源,例如使用金屬蒸氣放電方式的高壓水銀燈、鹵化金屬燈等、稀有氣體放電方式的氙燈等、使用微波的無電極燈等,由此可以照射紫外線。對于本發明的涂裝金屬板而言,若可以將紫外線固化型的涂膜充分固化,得到所希望的電阻焊性、耐蝕性、成型性則可以使用任意的燈。另外,通常涂膜受光的紫外線的峰照度、累計光量支配涂膜的固化性,但是若可以將紫外線固化型的涂膜充分固化,得到所希望的耐蝕性、成型性則對于紫外線的照射條件沒有特別限定。涂裝用組合物(β)為電子束固化型組合物的情況下,電子束固化可以使用在印刷、涂裝、薄膜涂覆、包裝、滅菌等領域中使用的通常的電子束照射裝置。它們在高真空中對于由熱燈絲產生的熱電子施加高電壓進行加速,將所得到的電子流取出到非活性氣體氣氛中,對聚合性物質進行照射。對于本發明的涂裝金屬板而言,若可以將電子束固化型的涂膜充分固化,得到所希望的電阻焊性、耐蝕性、成型性則可以使用任意裝置。另外,通常涂膜所吸收的電子束的加速電壓支配電子束浸滲涂膜的深度,吸收劑量支配聚合速度(涂膜的固化性),但是若可以將電子束固化型的涂膜充分固化,得到所希望的耐蝕性、成型性則對于電子束的照射條件沒有特別限定。但是,利用電子束進行自由基聚合的情況下,即使存在微量的氧、也會產生由于對生成自由基的氧化所導致的失活、交聯反應阻礙,固化變得不充分,因此優選在氧濃度為500ppm以下的非活性氣體氣氛中進行電子束照射。作為在此使用的非活性氣體,可例示出氮氣、二氧化碳、氬氣、和它們的混合氣體等。實施例實施例i以下通過使用了水系涂裝用組合物的實施例i對本發明進行具體說明。1.金屬板的準備準備以下的5種鋅系鍍覆鋼板,浸漬于水系堿脫脂劑(nihonparkerizingco.,ltd.制fc-301)的2.5質量%、40℃水溶液2分鐘,將表面脫脂后,進行水洗、干燥,形成涂裝用的金屬板。eg:電鍍鋅鋼板(板厚0.8mm、鍍覆附著量30g/m2)zl:電鍍zn-10%ni合金鋼板(板厚0.8mm、鍍覆附著量30g/m2)gi:熱浸鍍鋅鋼板(板厚0.8mm、鍍覆附著量40g/m2)sd:熱浸鍍zn-11%al-3%mg-0.2%si合金鋼板(板厚0.8mm、鍍覆附著量40g/m2)ga:合金化熱浸鍍鋅鋼板(板厚0.8mm、10%fe、鍍覆附著量45g/m2)2.基底處理覆膜的制膜如<涂膜(α)>的項所述,本發明中,未必需要在涂膜(α)與金屬板表面之間設置基底處理覆膜,但是有時為了進一步改善涂膜(α)對金屬板的密合性、耐蝕性等而使用。在此,在一部分的涂裝用金屬板設置基底處理覆膜來進行評價。作為用于制造基底處理覆膜的涂裝用組合物,準備包含聚酯樹脂、二氧化硅微粒、硅烷偶聯劑的水系涂裝用組合物。將上述組合物以覆膜厚度0.08μm的方式棒涂于前述的涂裝用金屬板,將其利用熱風爐在金屬表面達到溫度70℃下干燥、風干。3.水系涂裝用組合物的制造和制膜為了制造水系涂裝用組合物,首先準備樹脂(a)、導電性顏料(b)、防銹顏料(c)。(1)樹脂(a1)準備表1所示的樹脂a1~a8的市售的樹脂作為實施例用(發明例)、比較例用樹脂。[表1](2)導電性顏料(b)使用表2所示的市售的微粒(試劑)(實施例)。體積平均粒徑使用beckmancoulter,inc.制multisizer3(利用庫爾特原理的精密粒度分布測定裝置)測定。對于電阻率而言,由各微粒制成長度80mm、寬度50mm、厚度2~4mm的燒結板,通過使用mitsubishichemicalanalytechco.,ltd.制的電阻率計lorestaep(mcp-t360型)和esp探頭(端子的平頭部的直徑2mm)的四端子四探針法、恒定電流施加方式,根據jisk7194在25℃下測定。[表2]導電性顏料b種類實施例b1tib實施例b2zrb實施例b3mob實施例b4lab實施例b5vc實施例b6tic實施例b7tin實施例b8nisi實施例b9sus實施例b10zrb+vc(體積比率:1∶1)實施例b11zrb+tic(體積比率:1∶1)實施例b12vc+tin(體積比率:1∶1)tib:tib2微粒(株式會社高純度化研究所制tii11pb、體積平均直徑2.9μm、電阻率30×10-6ωcm)zrb:zrb2微粒(和光純藥工業株式會社制、體積平均直徑2.2μm、電阻率70×10-6ωcm)mob:mo2b微粒(三津和化學藥品株式會社制硼化二鉬、體積平均直徑5.2μm、電阻率30×10-6ωcm)lab:lab6微粒(添川理化學株式會社制六硼化鑭、體積平均直徑2.8μm、電阻率20×10-6ωcm)vc:vc微粒(和光純藥工業株式會社制、體積平均直徑2.3μm、電阻率140×10-6ωcm)tic:tic微粒(和光純藥工業株式會社制、體積平均直徑3.2μm、電阻率180×10-6ωcm)tin:tin微粒(和光純藥工業株式會社制、體積平均直徑1.6μm、電阻率20×10-6ωcm)nisi:ni2si微粒(將株式會社高純度化學研究所制nii11pb添加于水,進行攪拌、懸浮,將經過5分鐘后仍然漂浮的微小顆粒過濾來使用。體積平均直徑4.8μm、電阻率40×10-6ωcm)sus:sus304顆粒(體積平均直徑3.3μm、電阻率70×10-6ωcm)zrb+vc:前述zrb和前述vc的混合物(體積比1∶1)zrb+tic:前述zrb和前述tic的混合物(體積比1∶1)vc+tin:前述vc和前述tin的混合物(體積比1∶1)(3)防銹顏料(c)使用表3、表4所示的市售的試劑、工業產品,或將它們混合來使用(實施例)。[表3]防銹顏料c種類實施例c1焦磷酸鎂實施例c2硅酸鈣實施例c3磷酸氫鎂實施例c4焦磷酸鎂+硅酸鈣2∶1混合物實施例c5磷酸三鈣+五氧化釩2∶1混合物實施例c6c1和d1的1∶2混合物實施例c7c3和d2的1∶1混合物實施例c8c1和d3和d4的1∶1∶1混合物實施例c9c2和d4的1∶2混合物實施例c10c3和d1和d5的1∶1∶1混合物[表4](4)顆粒(d)使用表5所示的市售的工業產品(實施例)。[表5]接著使用前述的樹脂(a)、導電性顏料(b)、防銹顏料(c)、顆粒(d)和蒸留水,以各種配混比率制造水系涂裝用組合物。對于導電性顏料(b)、防銹顏料(c)、顆粒(d),以相對于水系涂裝用組合物的不揮發成分中含有的樹脂(a)、導電性顏料(b)、防銹顏料(c)、顆粒(d)的總量的所希望的體積比率配混。對于水系涂裝用組合物的不揮發成分的濃度,為了得到目的的涂膜附著量、良好的涂裝性,改變水的添加量來適當調整。在此,“不揮發成分”指的是作為溶劑配混于涂料、組合物的水、有機溶劑類揮發后殘留的成分。表6示出使用上述的涂膜構成成分制作的涂膜(α)的成分構成和涂膜中的含量(體積分數%)。[表6-1][表6-2]制造前述水系涂裝用組合物,將各成分均勻分散后,使用輥涂機涂布于前述的涂裝用金屬板、或設置有基底處理覆膜的金屬板,將其利用熱風爐在金屬表面達到溫度200℃下干燥,進行水冷、風干。表7示出制膜后的涂膜厚度(μm單位)。需要說明的是,前述涂膜厚度通過將涂裝后的涂膜的剝離前后的質量差除以涂膜比重來算出。涂膜比重由涂膜構成成分的配混量和各成分的已知比重計算。表6(表6-1、表6-2)示出涂裝金屬板表面的涂膜(α)表面的-20℃時的hm分布和40℃時的hm分布。各分布狀態如下所示。(1)-20℃時的hm分布狀態1:-20℃時的最小馬氏硬度hm為10~200mg/mm2的測定部位在隨機的測定點數100點中為0~19點狀態2:hm為10~200mg/mm2的測定部位為20~39點狀態3:hm為10~200mg/mm2的測定部位為40~59點狀態4:hm為10~200mg/mm2的測定部位為60點以上(2)40℃時的hm分布狀態1:40℃時的最小馬氏硬度hm為200~200000mg/mm2的測定部位在隨機的測定點數100點中為0~4點狀態2:hm為200~200000mg/mm2的測定部位為5~9點狀態3:hm為200~200000mg/mm2的測定部位為10~19點狀態4:hm為200~200000mg/mm2的測定部位為20點以上4.性能評價使用通過前述3.的方法制成的涂裝金屬板,對于焊接性、耐蝕性、耐崩裂性、崩裂后耐蝕性和耐堆積性進行評價。以下示出各試驗和評價的方法。(1)焊接性使用前端直徑5mm、r40的cf型cr-cu電極,在加壓力1.96kn、焊接電流8ka、通電時間12次循環/50hz的條件下進行點焊的連續打點性試驗,求出焊塊直徑即將切割3t(t為板厚)之前的打點數。使用以下的評分評價點焊性的優劣。4:打點數為1000點以上3:200點以上且不足1000點2:不足200點1:未生成焊塊、不能焊接1點(2)耐蝕性由通過前述3.的方法制成的涂裝金屬板切出150×70mm尺寸的長方形的試驗片,將端部進行樹脂密封作為平面部耐蝕性的試驗片。對于這些試驗片,實施將鹽水噴霧2小時、干燥4小時、濕潤2小時的總計8小時作為1次循環的循環腐蝕試驗。鹽水噴霧的條件基于jis-z2371。干燥條件為溫度60℃、濕度30%rh以下,濕潤條件為溫度50℃、濕度95%rh以上。調查紅銹產生狀況,使用以下的評分評價加工部耐蝕性的優劣。4:450次循環時不會產生紅銹3:300次循環時不會產生紅銹2:150次循環時不會產生紅銹1:150次循環時產生紅銹(3)耐崩裂性由通過前述3.的方法制成的涂裝金屬板切出150×70mm尺寸的長方形的試驗片,作為耐崩裂性的試驗片。試驗片實施電沉積涂裝(膜厚15μm)、中間涂布涂裝(膜厚30μm)·表面涂布涂裝(膜厚30μm)。對于上述完成涂布的鋼板,在氣溫-15℃的室內發射100個以空氣壓力加速到時速30~60km/h的速度的碎石(玄武巖、粒徑5~7.5mm),使得試驗板的平面相對于碎石的飛來方向傾斜15度發生碰撞。觀察碎石的碰撞的中心部20×20mm的范圍,使用以下的評分評價加工部耐蝕性的優劣。4:沒有露出鍍覆鋼板的鐵3:鍍覆鋼板的鐵按長徑和短徑的平均計以100μm以上的尺寸露出1個部位2:鍍覆鋼板的鐵按長徑和短徑的平均計以100μm以上的尺寸露出2~4個部位1:鍍覆鋼板的鐵按長徑和短徑的平均計以100μm以上的尺寸露出5個部位以上(4)崩裂后耐蝕性通過前述(4)的方法受損的涂裝金屬板作為崩裂后耐蝕性的試驗片。對于這些試驗片,實施將鹽水噴霧2小時、干燥4小時、濕潤2小時的總計8小時作為1次循環的循環腐蝕試驗。鹽水噴霧的條件基于jis-z2371。干燥條件為溫度60℃、濕度30%rh以下,濕潤條件為溫度50℃、濕度95%rh以上。調查紅銹產生狀況,使用以下的評分評價加工部耐蝕性的優劣。4:60次循環時沒有產生肉眼發現銹液的紅銹3:30~59次循環時產生肉眼發現銹液的紅銹2:13~29次循環時產生肉眼發現銹液的紅銹1:12次循環時產生肉眼發現銹液的紅銹(5)耐堆積性使得所制作的涂裝金屬板的表面和作為其相反面的背面在加壓下進行面接觸,評價耐堆積性。對于試驗方法,將切斷為50mm×50mm的試驗片以表面與背面之間進行面接觸的方式重疊,40℃下實施100kg/cm2×24小時的熱壓,熱壓后,涂膜的堆積(接合)程度通過下述基準評價。3:幾乎沒有涂膜之間的堆積,2:涂膜之間稍微堆積,但是簡單地用手就能夠輕便剝離的程度,1:涂膜之間堆積,用手不容易剝離的程度。表7(表7-1、表7-2)示出評價結果。[表7-1][表7-2]當前第1頁12