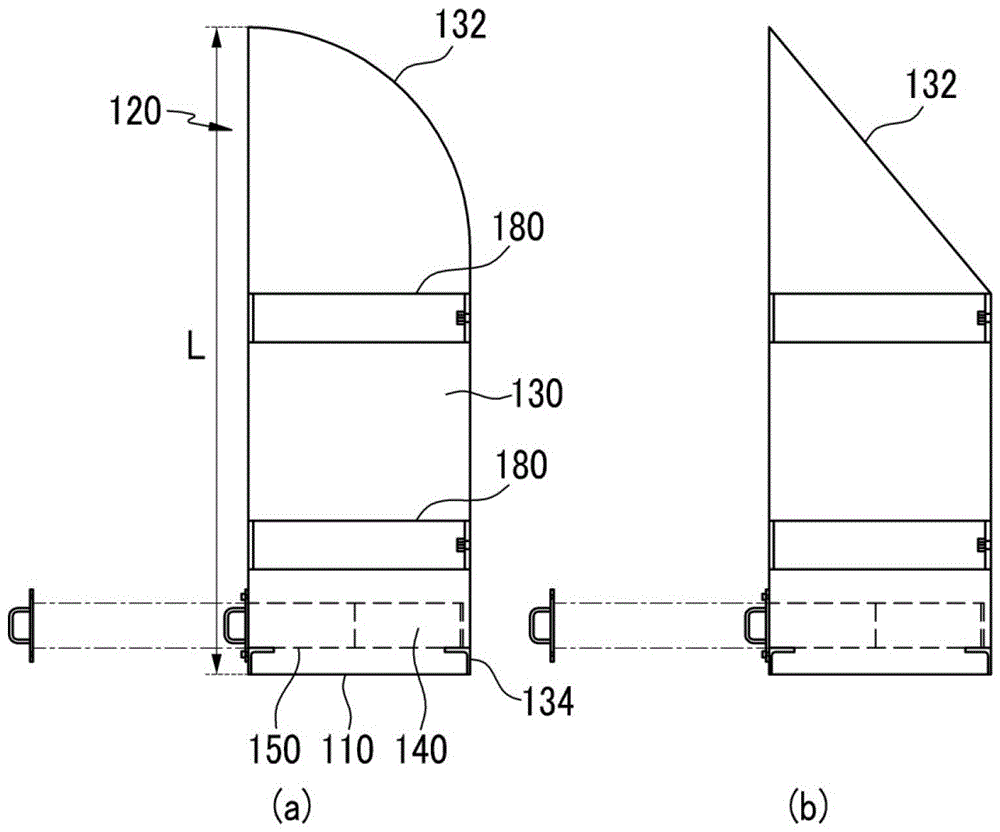
本發明涉及一種用于控制核反應堆中的氫氣(氫,hydrogen)的被動式自催化復合器(非能動自催化復合器,passiveautocatalyticrecombiner)以及利用其控制核反應堆中的氫氣的方法,更特別地,涉及一種用于將產生的氫氣再結合成水以便防止由于在核電站的核反應堆中產生的氫氣的富集而引起的爆炸的被動式自催化復合器以及使用該被動式自催化復合器來控制核反應堆中的氫氣的方法。
背景技術:隨著至今已被用作主要能源的諸如煤和石油的化石燃料逐漸被耗盡,核能發電作為一種替代方式已得到關注,并且核能設施的數量在世界范圍內以及在韓國傾向于增加反映了這些情況。然而,由于已公知核能發電的危險性,例如1979年三里島核電站事故、1986年切爾諾貝利核電站事故和最近的福島核電站事故,所以與核能發電相關的安全性已作為迫切需要解決的問題出現。前述核電站事故的最根本的起因是由于在核反應堆中燃料棒的熔化過程期間產生的氫氣富集所引起的爆炸。即,在伴隨堆芯熔毀(coremeltdown)的主要事故期間,大量的氫氣通過鋯錫合金(鋯合金,zircaloy)的氧化反應、核燃料包殼材料(nuclearfuelcladdingmaterial)而產生,并且當產生的氫氣達到預定的濃度時可能會存在自燃和爆炸的危險。因此,為了不使核電站中產生的氫氣濃縮(富集),已經安裝了諸如氫氣點火器和熱復合器的設備,從而按照以下化學式1通過使氫氣與空氣中的氧氣結合而將氫氣轉化成水,而沒有爆炸的危險。[化學式1]2H2+O2→2H2O然而,由于前述典型的設備或設施總是需要電力以控制氫氣,并且作為結果,與在福島核電站事故的情況中一樣,在不可能供應電力的狀態下,可能具有喪失它們的功能的嚴重局限性。因此,需要一種在事故期間在無需單獨的能量來源的情況下處理產生的氫氣的方法。最近,一種能夠解決這樣的局限性的被動式自催化復合器(PAR)受到了關注。該被動式自催化復合器可以在沒有單獨的動力源(例如熱或電)的情況下使氫氣和存在于空氣中的氧氣在催化劑上再結合成水,并且可以通過利用由于此時產生的熱引起的系統中的自然對流現象而自動防止氫氣的富集。因此,其可能是用于防止由于氫氣富集導致的爆炸而引起的核電站事故的最佳技術。與前述被動式自催化復合器的性能相關的核心技術可以總結為用于使系統中的氣流平穩的設計技術和用于基本上產生氫氣的再結合的催化劑相關技術,并且在下面描述了相關技術。韓國專利申請公開號2000-35983和2002-1814披露了能夠使氫氣再結合的板型(plate-type)被動式自催化復合器的設計。該前述專利使用金屬板用于促進氣體流動的自然對流,并且披露了用鉑或鈀直接涂覆金屬板以使氫氣再結合成為可能的技術。然而,由于使用多個鉑涂覆的金屬板,所以成本可能較高,并且直接參與氫氣再結合反應的催化活性位點的暴露程度可能較低。并且,當待處理的氫氣濃度較高時,由于該板的邊緣部分確實作為點火器,因此可能會促進氫氣爆炸。韓國專利申請公開號2010-36625披露了一種用于氫氣再結合的金屬泡沫型催化劑材料。由于該專利使用首先用金屬氧化物、氧化鋁(Al2O3)涂覆金屬泡沫(metalfoam),然后在其上涂覆鉑的方法,以便降低在氫氣再結合反應過程中作為活性物質的貴金屬的含量,并且使用金屬泡沫作為催化劑結構,已經報道了與在前述專利中公開的那些方法相比,該方法呈現出更高的催化劑性能。然而,關于以上專利,可能無法避免壓力損失的增加,同時由于結構的特征可能會使催化活性位點增加,并且由于催化劑結構易于被外來物質(雜質,foreignmatter)例如系統環境中存在的灰塵污染或沉積,所以活性位點可能會減少。因此,對開發一種用于自然對流和氫氣再結合性能的被動式自催化復合器存在需要,所述被動式自催化復合能夠完全解決由于外來物質引起的污染問題以及催化劑結構的壓力損失。
技術實現要素:技術問題本發明提供了一種在沒有單獨的能量來源的情況下通過安裝在核反應堆中以有效地控制封閉空間內的氫氣而能夠防止氫氣富集和爆炸的新型被動式自催化復合器和利用該被動式自催化復合器來控制氫氣的方法。本發明還提供了一種能夠同時解決指出作為傳統設備的結構局限性,諸如差的氣體流動、催化劑結構和系統的壓力損失、氫氣再結合的反應速率、以及由于灰塵和其他外來物質導致的污染的局限性的先進型被動式自催化復合器,以及利用該被動式自催化復合器控制氫氣的方法。技術方案根據本發明的一個方面,提供了一種用于控制核反應堆中的氫氣的被動式自催化復合器,該被動式自催化復合器包括容納在殼體(case)中的催化劑結構,該殼體包括氣體進口(進氣口,gasinlet)和氣體出口(出氣口,gasoutlet),該催化劑結構與從氣體進口沿向上方向流動的氣體接觸,其中氣體出口位于殼體的上端側部(upperendsideportion),該殼體的上端形成為彎曲表面或傾斜表面,并且該催化劑結構由蜂窩狀陶瓷(honeycomb-shapedceramic)形成。并且,該催化劑結構可以安裝在能夠滑進和滑出殼體的滑動箱(slidingbox)中。并且,該滑動箱可以由兩個以上的格柵(grid)形成,并且催化劑結構設置在每個格柵中。并且,該催化劑結構可以包括在催化劑結構周圍的墊圈(緩沖環,襯墊環,cushionring),并且將該墊圈容納(包括)并接合(連接,join)在催化劑結構與加勁板(加筋板,加固板,stiffenedplate)之間。并且,在格柵與加勁板之間可以形成固定構件以固定催化劑結構。并且,該蜂窩狀陶瓷(蜂窩陶瓷,honeycombceramic)可以具有從約5cpsi至約100cpsi(單元/平方英寸)范圍的單元密度(celldensity)。并且,該催化劑結構可以通過用催化劑材料涂覆蜂窩狀陶瓷的表面來形成。并且,該催化劑材料可以包含鉑或鈀。并且,在該氣體進口和該氣體出口處可以安裝用于阻止外來物質引入的網格(網篩,mesh)。并且,該殼體可以包括在該氣體進口與氣體出口之間的一個或多個內側部增強板(內側部加強板,innersideportionreinforcingpanel)。并且,該被動式自催化復合器在氣流方向的長度可以在約0.5m至約2.0m的范圍內。根據本發明的另一個方面,控制核反應堆中的氫氣的方法包括:將該被動式自催化復合器安裝在反應堆中;以及通過自然對流使包括在核反應堆中產生的氫氣的混合氣體從被動式自催化復合器的氣體進口通到(流到)氣體出口。并且,使混合氣體通過被動式自催化復合器可以在室溫環境中進行。并且,使混合氣體通過被動式自催化復合器可以在具有約95%以上的相對濕度的環境中進行。有益效果根據被動式自催化復合器和使用其控制氫氣的方法,選擇蜂窩狀陶瓷作為催化劑結構以改善氫氣再結合的反應速率并且能夠防止催化劑結構和核反應堆系統的壓力損失。并且,由于該設備的上端形成為彎曲表面或傾斜表面且氣體出口位于該設備的上端側部,所以可以平穩地維持通過設備的氣流,并且同時,可以防止由于從該設備的上部滴下的液滴引起妨礙氣體流動并且可以保護催化劑。將網格安裝在該設備的氣體進口和出口處,因此可以防止由于外來物質的引入而導致的污染。催化劑結構構成一個模塊(module)以便被安裝在滑動箱中,因此根據對該催化劑結構的安裝和分離(例如檢查、修理和更換),可以獲得設備管理的減輕。此外,在該催化劑結構中包括強度增強裝置(strengthreinforcingmeans),因此可以防止陶瓷材料的強度隨著蜂窩形狀的采用的降低。附圖說明通過參照附圖對其示例性實施方式進行詳細描述,本發明的上述以及其他特征和優點會變得更加顯而易見,在附圖中:圖1和圖2是分別示出了根據本發明實施方式的被動式自催化復合器的透視圖和側面剖視圖;圖3是示出了根據本發明的實施方式的蜂窩狀催化劑結構的照片;圖4是示出了圖1的被動式自催化復合器中的滑動箱的結構的俯視圖;圖5是說明了根據本發明中格柵的數量的滑動箱的俯視圖;圖6是示出了本發明中包括強度增強裝置的催化劑結構的俯視圖和剖視圖;圖7是示出了本發明中固定構件的俯視圖;圖8是示出了在實驗實施例2中通過使用氫氣分析儀在穹頂(圓頂室,dome)內氫氣濃度測量結果的圖;以及圖9是示出了在實驗實施例2中在氫氣氧化過程中溫度變化的曲線圖。具體實施方式以下將參照附圖更詳細地描述本發明的優選實施方式。將省略與公知的功能或構造相關的詳細描述以便使本發明的主題沒有不必要地模糊。為了清楚地示出,每副圖都可以被部分簡化或放大,并且相似的參考數字始終指代相似的要素(元件)。并且,當描述某物“包括”某些要素時,應當理解為其可以僅包括那些要素,或者在沒有具體限定時其可以包括其他要素以及那些要素。首先,將更詳細地描述根據本發明的用于在核反應堆中控制氫氣的被動式自催化復合器。圖1和圖2是分別示出了根據本發明實施方式的被動式自催化復合器的透視圖和側面剖視圖,并且圖3是示出了根據本發明的實施方式的蜂窩狀催化劑結構的照片。參照圖1至圖3,根據本發明的實施方式的被動式自催化復合器100包括容納在殼體130中的催化劑結構140,該殼體130包括氣體進口110和氣體出口120,并且所述催化劑結構140與從氣體進口110沿向上方向流動的氣體接觸。本發明的被動式自催化復合器100是安裝在核反應堆中的設備,以從該氣體進口110引入包括在核反應堆中產生的氫氣的混合氣體并且使其通過催化劑結構140排出至氣體出口120。該設備為垂直型的,其中底座(基座,pedestal)(未示出)安裝在殼體130的下部,并且可以安裝在核反應堆中或者可以通過在殼體130的側部131包括緊固裝置(fasteningmeans)(未示出)而安裝和緊固在核反應堆的側壁。本發明的氣體出口120位于殼體130的上端側部并且殼體130的上端可以形成為彎曲表面132。例如,如圖1中所示,殼體130的上端接近于彎曲表面形狀,因此,從氣體進口110向上流動的混合氣體并不在該殼體130的上端沿直接向上方向(正向上方向,directlyupwarddirection)排出,并且可以在沿著形成彎曲表面132的殼體130上端的內表面流動后從形成彎曲表面132的殼體130上端的頂部133沿著向下方向通過以預定距離打開而形成的氣體出口120排出。即,可以從被動式自催化復合器100的上部滴下的液滴未被引入到氣體出口120中,而是使得沿著通過使殼體130的上端形成為彎曲形狀的彎曲形狀132流動。因此,在本發明中,該殼體130上端的形狀可以包括在本發明的技術構思中,只要該形狀可以使液滴滴到核反應堆中的該復合器100而不引入到氣體出口120但是沿著殼體130的上端流動,例如,該形狀可以是如圖2(b)中所示的傾斜表面132。然而,該殼體130上端的形狀例如可以是彎曲表面132以便通過使相對于殼體130的內表面的摩擦阻力最小化而使氣體排出。本發明的催化劑結構140是用于再結合的要素(元件,element),其使從氣體進口110引入的混合氣體中的氫氣與氧氣結合從而轉化成水,并考慮到氣流的壓力損失和氫氣(一種反應物)的接觸面積,由如圖3所示的蜂窩狀陶瓷形成。此時,可以使用擠出物(extrudate),其中催化劑結構由催化劑本身形成。然而,由于生產成本可能增加,因此可以使用通過用催化劑材料涂覆蜂窩狀陶瓷的表面而形成的催化劑結構140。可以使用貴金屬催化劑作為催化劑材料,并且例如,可以使用鉑或鈀。考慮到在氫氣再結合反應中的優勢,可以使用鉑。貴金屬催化劑的涂覆可以通過涂覆通過使用二氧化鈦載體(titaniasupport)而制備的漿料來進行。例如,稱取基于100重量份的二氧化鈦載體為1至10重量份的鉑前體并使其溶解在蒸餾水中。引入二氧化鈦載體以制備漿料,然后可以通過用該漿料涂覆擠出成具有預定規格的蜂窩狀陶瓷結構,并干燥和熱處理涂覆的蜂窩狀陶瓷結構來制備催化劑結構140。可以將本發明中的催化劑結構140安裝在模塊(組件)中。即,將催化劑結構140穩固地設置在安裝在氣體進口110附近并且能夠滑入和滑出殼體130的滑動箱150中,并且可以通過包括抽屜形式的滑動箱150來促進安裝和分離。圖4是示出了圖1的被動式自催化復合器中的滑動箱結構的俯視圖。參照圖4和圖2,滑動箱150可以形成為對應于殼體130的規格的格柵狀以使其能夠沿著容納在殼體130中的導軌134滑動,并且可以形成使催化劑結構140穩固地設置在格柵的內側方向的剩余部分151。此時,該滑動箱150可以全部由剛性不銹鋼(stiffstainlesssteel)形成以增強后面待描述的催化劑結構140的強度。并且,格柵的上部和下部可以形成為按順序打開,用于使從氣體進口110引入的混合氣體平穩流動。同時,圖4示出了滑動箱150由4個格柵G構成,因此,可以安裝催化劑結構140以便使其對應于4個格柵G中的每一個。即,當本發明的催化劑結構140與滑動箱150一起構成模塊,且同時該滑動箱150由多個格柵G構成時,對于每個格柵G,獨立管理(例如催化劑結構140的安裝、檢查、修理和更換)是可能的。因此,可以進一步改善設備管理的簡易性。因此,如圖5所示,考慮到所需的催化劑性能、平穩的自然對流以及核反應堆的內部空間尺寸,可以更多的數量包括構成滑動箱150的格柵G,例如8個(a)或16個(b)。殼體130的規格可以根據滑動箱150的格柵G的數量而變化。在本發明中,為了改善氫氣再結合的反應速率并且防止催化劑結構和核反應堆系統的壓力損失,可以根據選擇蜂窩狀陶瓷材料作為催化劑結構140而需要與傳統結構相比用于防止機械強度降低的裝置(means)。因此,本發明可以包括關于催化劑結構140的強度增強裝置(strengthreinforcingmeans)。圖6是示出了本發明中包括強度增強裝置的催化劑結構的俯視圖(a)和剖視圖(b)。參照圖6,在催化劑結構140的周圍包括墊圈160,并且將墊圈160容納并接合在催化劑結構140與加勁板152之間,因此使其能夠通過剛性材料的加勁板152的一部分來吸收(緩沖)外部沖擊。因此,可以防止催化劑結構140的機械強度的降低,并且也可以防止由于外來物質例如可能會從催化劑結構140側面引入的灰塵引起的污染。可以使用剛性材料例如不銹鋼作為加勁板152。可以通過接合方法(連接方法,joiningmethod)例如將與墊圈160接觸的加勁板152的一部分焊接來進行催化劑結構140與加勁板152之間的接合(連接)。因此,可以使用金屬材料例如鋁或不銹鋼作為墊圈160以便使其容易地接合至不銹鋼的加勁板152的所述部分上,并且例如,根據接合表面積的增加可以使用金屬網格用于更平滑的接合(連接)。圖6示出了墊圈160分別形成在催化劑結構140的上部和下部。然而,墊圈160的數量和形成的位置沒有限制,只要墊圈160可以起作用以接合在催化劑結構140與加勁板152之間。當包括前述強度增強裝置的催化劑結構140穩固地定位在滑動箱150的格柵G中時,由于規格誤差可能會在加勁板152與格柵G之間形成間隙,因此,由于穩定地定位在格柵G中的催化劑結構140未完全固定,所以可能發生因外部振動或沖擊而導致的局限性。因此,在本發明中,在格柵G與加勁板152之間形成固定構件153,因此,預防外部振動或沖擊,特別是預防地震發生的有效抗震設計(effectiveaseismicdesign)可能是可行的。如圖7所示,該固定構件153可以包括具有通過保持預定角度而獲得的彈性力的剛性材料(stiffmaterial)例如不銹鋼的推動部(pushingportion)153a。因此,如圖4所示,該推動部153a推動穩固設置的催化劑結構140的加勁板152的一部分,因此催化劑結構140可以完全固定在格柵G中。此時,可以在穩固地定位催化劑結構140之前通過附著于格柵G的中間部分而安裝固定構件153,或者在穩固地定位催化劑結構140之后通過插入來安裝固定構件153。推動部153a還可以安裝在圖4的情況(殼體,case)的相對方向,即,格柵G的方向中。此外,在本發明中,固定構件153的形狀例如線圈狀或板狀沒有限制,只要固定構件153由剛性材料形成且具有彈力即可。每單位面積的構成蜂窩狀陶瓷的單元(蜂窩,cell)141的數量可以影響氫氣再結合的反應速率。即,隨著每單位面積的單元141的數量(單元/平方英寸:cspi)增加,可以維持更平穩的自然對流并且可以防止催化劑結構140和核反應堆系統的壓力損失,但是氫氣再結合的反應速率可能會降低。隨著每單位面積的單元141的數量降低,氫氣再結合的反應速率可能會增加,但是當超出每單位面積的單元141的預定數量時可能會防止自然對流并且可能會發生催化劑結構140和核反應堆系統的壓力損失。因此,為了解決本發明中的前述限制,可以通過包括在5cpsi至100cpsi,例如20cpsi至60cpsi的范圍內,并且例如在30cpsi至40cpsi范圍內的每單位面積的單元141的數量來制備催化劑結構140。在本發明中,在氣體進口110和氣體出口120處安裝的網格170用于防止由于核反應堆中的自然對流而將外來物質引入到被動式自催化復合器100中。金屬材料的網格170可以用于增強總體設備的強度以及防止外來物質的引入,并且考慮到在核反應堆中產生的外來物質的大小可以適當地選擇網格170的尺寸。同時,圖1示出了在殼體130的上端側部的氣體出口120處形成網格170,但是網格170可以以橫向方向(transversedirection)安裝在殼體130的中間部分。然而,當網格170以橫向方向安裝時,由于因外來物質的積累可能會阻礙平穩的氣體流動(氣流),因此網格170可以形成在如圖1所示的殼體130的上端側部的氣體出口120處。由于被動式自催化復合器100暴露于各種危險因素,例如地震或爆炸,因此確保機械強度可能是非常重要的因素。因此,在本發明中,可以包括用于確保被動式自催化復合器100的整體強度以及前述催化劑結構140的機械強度的裝置(means)。即,本發明的殼體130可以基本上由剛性不銹鋼形成并且可以在氣體進口110和氣體出口120之間形成一個或多個內側部增強板180。同時,對限制被動式自催化復合器100的尺寸以便在反應堆中平穩地形成且維持自然對流存在需要。被動式自催化復合器100的尺寸可以根據其中安裝了被動式自催化復合器100的核反應堆的尺寸而變化,但是當考慮到通常使用的核反應堆的尺寸時,基于氣流方向(垂直方向)上的長度L,本發明的被動式自催化復合器100的尺寸可以在0.5m至2.0m的范圍內,并且例如,可以在0.8m至1.2m的范圍內。根據本發明的被動式自催化復合器100安裝在核反應堆中,將包括在核反應堆中產生的氫氣的混合氣體引入到氣體進口110中,在催化劑結構140中使氫氣與氧氣結合以轉化成水,并且通過借助于由于此時產生的熱引起的自然對流使氫氣持續地通過設備100來控制核反應堆中的氫氣。通過使用根據本發明的被動式自催化復合器100控制核反應堆中的氫氣可以在目前通常操作的核反應堆的環境,即,室溫環境或者具有95%以上相對濕度的潮濕環境中進行。實施例1基于100重量份的二氧化鈦載體稱取3重量份的硝酸四氨合鉑(tetra-amineplatinumnitrate,四氨合硝酸鉑)(Pt(NH3)4(NO3)2)作為鉑前體并且在室溫下使其溶解在蒸餾水中。同時,可以使用羥基鉑((NH2-CH2CH2-OH)·2Pt(OH)6)或氯化鉑(PtCl4)作為鉑前體,并且在使用氯化鉑時通過提高蒸餾水的溫度在約60°C下溶解該氯化鉑。之后,將稱取的二氧化鈦(TiO2)載體引入到其中溶解有鉑前體的水溶液中以制備成漿料形式,并且使用制備好的漿料涂覆規格為20cpsi的蜂窩狀陶瓷結構以便用催化劑涂覆該蜂窩狀陶瓷結構。將該涂覆的蜂窩狀陶瓷結構在80°C至120°C的溫度范圍內干燥24小時以上從而完全去除微孔中包含的水分,然后通過進行熱處理來制備催化劑結構(參見圖3左側的結構)。實施例2除了使用規格為35cpsi的蜂窩狀陶瓷結構以外,以與實施例1相同的方式制備催化劑結構(參見圖3右側的結構)。按照實施例1和2制備的催化劑結構的規格(間距(pitch)和截深(web))、開口比(openingrate)和表面積在下面的表1中示出。[表1]類別間距截深開口比表面積單位mmmm%cm2/cm3實施例15.681.00685.8實施例24.290.65727.9實驗實施例1為了評估根據實施例1和2制備的催化劑結構的性能,當氫氣與氧氣以在35,000至100,000范圍內的氣時空速(gashourlyspacevelocity)(GHSV)引入時,研究了氫氣再結合速率,并且其結果在表2中示出。此處,根據以下方程1來計算氫氣再結合速率。[方程1]氫氣再結合速率(%)=((引入的氫氣濃度﹣排出的氫氣濃度)/引入的氫氣濃度)×100[表2]GHSV(h-1)實施例1實施例2100,00081.2%95.6%70,00089.4%97.9%60,00092.1%98.3%50,00095.2%99.2%35,00097.4%100.0%參照表2,可以確定,對于作為實施例2的每種空速(spacevelocity)來說,當每單位面積蜂窩狀陶瓷結構的單元數量相對均大時氫氣再結合性能更好。可以理解,這是由于催化劑結構的開口比和暴露的表面積所引起的。實驗實施例2為了評估其中安裝有按照實施例1和2制備的催化劑結構的被動式自催化復合器的自然對流和氫氣控制性能的實質影響,將圖1中所示的被動式自催化復合器安裝在具有氫氣和氧氣兩者的真實穹頂(realdome)(飛機棚模擬系統(hangarsimulationsystem))中。通過在一定條件下持續維持反應的初始溫度來實施反應,其中穹頂充有包含1.5vol%的氫氣和21vol%的氧氣的混合氣體,相對濕度為100%,然后通過利用氫氣分析儀(FujielectronicsZAFEK403K)來測定穹頂中氫氣的濃度。其結果示出在圖8中,并且對于實施例2測量了在氫氣的氧化過程中溫度的變化,并且其結果示出在圖9中。如圖6所示,在安裝的被動式自催化復合器中的滑動箱的每個格柵中制備好的催化劑結構周圍安裝鋁網格,然后通過焊接至由不銹鋼形成的滑動箱的格柵而接合,并且將該設備的總高度制成為1m。首先,參照圖9,該設備的氣體出口的溫度增加,同時穹頂中氫氣的濃度在被動式自催化復合器運行時開始降低,并且由于氫氣的總濃度被控制,因此溫度在氫氣的濃度增加之前維持在一定溫度附近。結果,可以證實,通過形成由于根據由催化劑結構引起的氫氣再結合反應產生的熱引起的自然對流而獲得了氫氣的平穩控制。同時,參照圖8,可以證實,當安裝按照實施例2制備的催化劑結構時,與實施例1的情況相比,氫氣的控制更快。此時,關于實施例1和2的氫氣再結合的反應速率分別為0.22g/s和0.27g/s,因此,可以理解,可以提供具有非常良好的氫氣控制性能的被動式自催化復合器。雖然已經參照其優選的實施方式對本發明進行了具體示出和描述,但本領域技術人員會理解,在不背離如由所附權利要求所限定的本發明的精神和范圍的情況下,可以在其中進行形式和細節的各種變化。因此,本發明的范圍不是由本發明的詳細描述所限定的而是由所附的權利要求所限定,并且源于所附權利要求的含義、范圍和等同概念的所有改變和變形將被視為包括在本發明中。