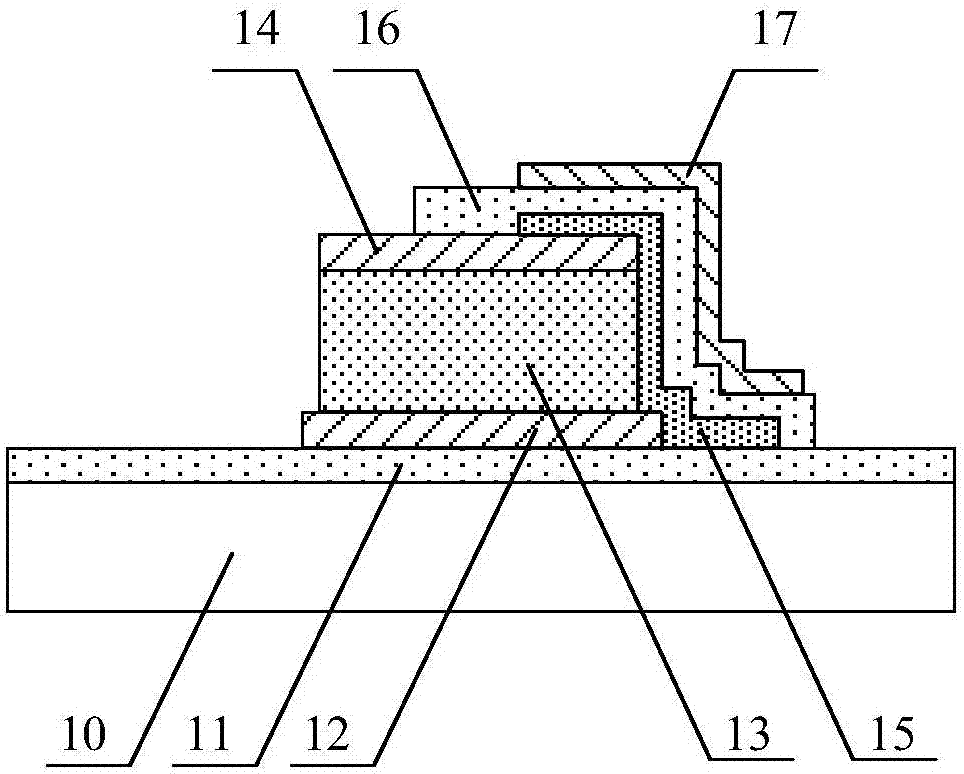
本發明涉及顯示
技術領域:
,具體涉及一種垂直型薄膜晶體管及其制備方法。
背景技術:
:平板顯示裝置,如薄膜晶體管液晶顯示器(thinfilmtransistorliquidcrystaldisplay,tft-lcd)和有源矩陣有機發光二極管(activematrixorganiclightemittingdiode,amoled),因其具有體積小、功耗低、無輻射以及制作成本相對較低等特點,越來越多地被應用于高性能顯示領域當中。其中,tft-lcd的主體結構包括對盒的陣列基板和彩膜基板,陣列基板包括矩陣排列的多個像素單元,像素單元由多條柵線和多條數據線垂直交叉限定,在柵線與數據線的交叉位置處設置tft。amoled的結構主要由tft和oled構成。近年來,高分辨率顯示面板逐漸成為行業發展趨勢。顯示面板的分辨率(pixelsperinch,ppi)與陣列基板的像素開口率有關,而陣列基板的像素開口率與每個像素單元的薄膜晶體管尺寸有關,薄膜晶體管所占區域越大,像素開口率就越低,顯示面板的分辨率越低,為此,現有技術提出了一種垂直型薄膜晶體管,通過減小薄膜晶體管尺寸,提高像素開口率,提高分辨率。圖1為現有垂直型薄膜晶體管的結構示意圖。如圖1所示,垂直型薄膜晶體管包括:設置在基底10上的緩沖層11,設置在緩沖層11上的源電極12,設置在源電極12上的間隔層13,設置在間隔層13上的漏電極14,設置在漏電極14和源電極12上的有源層15,覆蓋有源層15的柵絕緣層16,設置在柵絕緣層16上的柵電極17。現有垂直薄膜晶體管的制備流程為:通過第一次構圖工藝形成緩沖層11和源電極12,通過第二次構圖工藝形成間隔層13,通過第三次構圖工藝形成漏電極14,通過第四次構圖工藝形成有源層15,通過第五次構圖工藝形成柵絕緣層16,通過第六次構圖工藝形成柵電極17。根據現有垂直型薄膜晶體管的結構和制備流程可以看出,由于該結構形式的薄膜晶體管具有7個膜層,需要6次構圖工藝,不僅工序復雜導致生產效率低、生產成本高,并且誤差疊加影響對位精度,良品率低。技術實現要素:本發明實施例所要解決的技術問題是,提供一種垂直型薄膜晶體管及其制備方法,以克服現有制備方法工序復雜、對位精度低等缺陷。為了解決上述技術問題,本發明實施例提供了一種垂直型薄膜晶體管的制備方法,包括:在基底上依次形成第一電極、隔離層、有源層和柵絕緣層;在柵絕緣層上同時形成第二電極和柵電極,第二電極通過柵絕緣層過孔與有源層連接。可選地,所述隔離層的厚度為0.5μm~2.0μm;所述隔離層在基底上的正投影寬度小于第一電極在基底上的正投影寬度,隔離層鄰近有源層一側露出所述第一電極的表面,所述有源層與第一電極露出的表面連接。可選地,所述在基底上依次形成第一電極、隔離層、有源層和柵絕緣層,包括:在基底上形成第一電極;在第一電極上形成隔離層,所述隔離層鄰近有源層一側露出所述第一電極的表面;形成有源層,所述有源層的一部分設置在所述隔離層上,另一部分設置在所述基底上,且與第一電極露出的表面連接;形成覆蓋所述第一電極、間隔層和有源層且具有柵絕緣層過孔的柵絕緣層。可選地,所述在基底上依次形成第一電極、隔離層、有源層和柵絕緣層,包括:在基底上形成第一電極和隔離層,所述隔離層鄰近有源層一側露出所述第一電極的表面;形成有源層,所述有源層的一部分設置在所述隔離層上,另一部分設置在所述基底上,且與第一電極露出的表面連接;形成覆蓋所述第一電極、間隔層和有源層且具有柵絕緣層過孔的柵絕緣層。可選地,所述在基底上形成第一電極和隔離層,所述隔離層鄰近有源層一側露出所述第一電極的表面,包括:在基底上沉積第一金屬薄膜和涂覆有機薄膜;采用半色調掩膜版或灰色調掩膜版對有機薄膜進行階梯曝光并顯影,在第一電極位置形成未曝光區域,在數據線位置形成部分曝光區域,在其余位置形成完全曝光區域;刻蝕掉完全曝光區域的第一金屬薄膜,形成第一電極和數據線;灰化處理,去除部分曝光區域的有機薄膜,形成露出第一電極部分表面的隔離層。可選地,所述在基底上依次形成第一電極、隔離層、有源層和柵絕緣層中,還包括形成緩沖層的步驟。可選地,所述在柵絕緣層上同時形成第二電極和柵電極,第二電極通過柵絕緣層過孔與有源層連接,包括:在柵絕緣層上沉積金屬薄膜;通過一次構圖工藝形成同層設置的第二電極和柵電極,所述第二電極在基底上的正投影寬度小于所述第一電極在基底上的正投影寬度;所述柵電極在基底上的正投影寬度小于所述有源層在基底上的正投影寬度;所述柵電極在基底上的正投影與所述第二電極在基底上的正投影部分重合;所述第二電極通過柵絕緣層過孔與有源層連接。可選地,所述柵電極在基底上的正投影與所述第二電極在基底上的正投影重合區域寬度為0。為了解決上述技術問題,本發明實施例還提供了一種垂直型薄膜晶體管,包括:第一電極,設置在基底上;間隔層,設置在第一電極上;有源層,一部分設置在所述隔離層上,另一部分設置在基底上,與所述第一電極連接;柵絕緣層,覆蓋所述第一電極、間隔層和有源層;第二電極,設置在所述柵絕緣層上,且通過柵絕緣層過孔與所述有源層連接;柵電極,設置在所述柵絕緣層上,且與所述第二電極同層。可選地,所述隔離層的厚度為0.5μm~2.0μm;所述隔離層在基底上的正投影寬度小于第一電極在基底上的正投影寬度,隔離層鄰近有源層一側露出所述第一電極的表面,所述有源層與第一電極露出的表面連接。可選地,所述第二電極在基底上的正投影寬度小于所述第一電極在基底上的正投影寬度;所述柵電極在基底上的正投影寬度小于所述有源層在基底上的正投影寬度;所述柵電極在基底上的正投影與所述第二電極在基底上的正投影部分重合。可選地,所述柵電極在基底上的正投影與所述第二電極在基底上的正投影重合區域寬度為0。可選地,還包括緩沖層,所述緩沖層設置在基底上,所述第一電極設置在所述緩沖層上。本發明實施例還提供了一種陣列基板,所述陣列基板包括前述的垂直型薄膜晶體管。本發明實施例還提供了一種顯示面板,所述顯示裝置包括前述的陣列基板。本發明實施例所提供的垂直型薄膜晶體管及其制備方法,由于柵電極和第二電極通過一次構圖工藝形成,減少了工藝流程,提高了生產效率,降低了成本。同時,由于柵電極和第二電極同層設置,對位精度高,提升了良品率。進一步地,垂直型薄膜晶體管有效減小了薄膜晶體管的尺寸,提高了開口率,實現了高分辨率顯示。當然,實施本發明的任一產品或方法并不一定需要同時達到以上所述的所有優點。本發明的其它特征和優點將在隨后的說明書實施例中闡述,并且,部分地從說明書實施例中變得顯而易見,或者通過實施本發明而了解。本發明實施例的目的和其他優點可通過在說明書、權利要求書以及附圖中所特別指出的結構來實現和獲得。附圖說明附圖用來提供對本發明技術方案的進一步理解,并且構成說明書的一部分,與本申請的實施例一起用于解釋本發明的技術方案,并不構成對本發明技術方案的限制。附圖中各部件的形狀和大小不反映真實比例,目的只是示意說明本
發明內容。圖1為現有垂直型薄膜晶體管的結構示意圖;圖2為本發明實施例垂直型薄膜晶體管的結構示意圖;圖3為本發明實施例垂直型薄膜晶體管制備方法的流程圖;圖4為本發明第一實施例形成緩沖層和第一電極圖案后的示意圖;圖5為本發明第一實施例形成隔離層圖案后的示意圖;圖6為本發明第一實施例形成有源層圖案后的示意圖;圖7為本發明第一實施例形成柵絕緣層圖案后的示意圖;圖8為本發明第一實施例同時形成第二電極和柵電極后的示意圖;圖9為本發明第一實施例柵電極與第二電極位置關系的示意圖;圖10為本發明第二實施例形成緩沖層、第一金屬薄膜和有機薄膜后的示意圖;圖11為本發明第二實施例曝光顯影后的示意圖;圖12為本發明第二實施例形成第一電極和數據線后的示意圖;圖13為本發明第二實施例灰化處理后的示意圖。附圖標記說明:10—基底;11—緩沖層;12—源電極;13—間隔層;14—漏電極;15—有源層;16—柵絕緣層;17—柵電極;18—第一電極;19—第二電極;20—第一金屬薄膜;30—有機薄膜;40—數據線。具體實施方式下面結合附圖和實施例對本發明的具體實施方式作進一步詳細描述。以下實施例用于說明本發明,但不用來限制本發明的范圍。需要說明的是,在不沖突的情況下,本申請中的實施例及實施例中的特征可以相互任意組合。目前,現有垂直型薄膜晶體管具有7個膜層,需要6次構圖工藝,不僅制備工序復雜導致生產效率低、生產成本高,并且誤差疊加影響對位精度,良品率低。為了克服現有垂直型薄膜晶體管制備方法工序復雜、對位精度低等缺陷,本發明實施例提供了一種垂直型薄膜晶體管及其制備方法。圖2為本發明實施例垂直型薄膜晶體管的結構示意圖。如圖2所示,垂直型薄膜晶體管包括第一電極18、間隔層13、有源層15、柵絕緣層16、第二電極19和柵電極17,其中:第一電極18,設置在基底10上;間隔層13,設置在第一電極18上;有源層15,一部分設置在隔離層13上,另一部分設置在基底10上,與第一電極18連接;柵絕緣層16,覆蓋第一電極18、間隔層13和有源層15;第二電極19,設置在柵絕緣層16上,且通過柵絕緣層過孔與有源層15連接;柵電極17,設置在柵絕緣層16上,且與第二電極19同層。本發明實施例中,柵電極和第二電極同層且通過一次構圖工藝形成,第一電極、有源層和第二電極依次疊設,形成溝道區域垂直于基底平面的垂直型薄膜晶體管。其中,數據線與第一電極同層,柵線與柵電極同層。在具體實施時,可以將第一電極作為源電極,第二電極作為漏電極;或者將第一電極作為漏電極,第二電極作為源電極,在此不做限定。隔離層的厚度為0.5μm~2.0μm,隔離層在基底上的正投影與第一電極在基底上的正投影重合,隔離層的正投影寬度小于第一電極的正投影寬度,使隔離層鄰近有源層一側露出第一電極的部分表面。有源層的一部分位于隔離層上,另一部分位于基底上,中間部分與第一電極露出的部分表面相接觸,有源層厚度為2000~8000埃,有源層材料既可以是多晶硅,形成低溫多晶硅(lowtemperaturepoly-silicon,ltps)薄膜晶體管,也可以是金屬氧化物,形成氧化物(oxide)薄膜晶體管。柵絕緣層覆蓋第一電極、隔離層和有源層,也可以覆蓋整個基底,柵絕緣層過孔設置在位于隔離層上的有源層位置。第二電極在基底上的正投影與第一電極在基底上的正投影重合,第二電極的正投影寬度小于第一電極的正投影寬度,柵電極在基底上的正投影與有源層在基底上的正投影重合,柵電極的正投影寬度小于有源層的正投影寬度。柵電極在基底上的正投影與第二電極在基底上的正投影部分重合,優選地,重合區域寬度等于0。此外,垂直型薄膜晶體管還可以包括緩沖層,緩沖層設置在基底上,第一電極設置在緩沖層上。圖3為本發明實施例垂直型薄膜晶體管制備方法的流程圖。如圖3所示,垂直型薄膜晶體管制備方法包括:s1、在基底上依次形成第一電極、隔離層、有源層和柵絕緣層;s2、在柵絕緣層上同時形成第二電極和柵電極,第二電極通過柵絕緣層過孔與有源層連接。其中,步驟s1可以包括:s111、在基底上形成第一電極;s112、在第一電極上形成隔離層,隔離層鄰近有源層一側露出第一電極的部分表面;s113、在隔離層形成有源層,有源層的一部分設置在隔離層上,另一部分設置在基底上,且與第一電極露出的部分表面連接;s114、形成覆蓋第一電極、間隔層和有源層且具有柵絕緣層過孔的柵絕緣層。其中,步驟s1還可以包括:s121、在基底上形成第一電極和隔離層,隔離層鄰近有源層一側露出第一電極的部分表面;s122、在隔離層上形成有源層上,有源層的一部分設置在隔離層上,另一部分設置在基底上,且與第一電極露出的部分表面連接;s123、形成覆蓋第一電極、間隔層和有源層且具有柵絕緣層過孔的柵絕緣層。其中,步驟s121包括:在基底上沉積第一金屬薄膜和涂覆有機薄膜;采用半色調掩膜版或灰色調掩膜版對有機薄膜進行階梯曝光并顯影,在第一電極位置形成未曝光區域,在數據線位置形成部分曝光區域,在其余位置形成完全曝光區域;刻蝕掉完全曝光區域的第一金屬薄膜,形成第一電極和數據線;灰化處理,去除部分曝光區域的有機薄膜,形成露出第一電極部分表面的隔離層。其中,步驟s1中還包括形成緩沖層的步驟,緩沖層形成在基底上,第一電極形成在緩沖層上。其中,步驟s2包括:s21、在柵絕緣層上沉積一金屬薄膜;s22、通過一次構圖工藝形成同層設置的第二電極和柵電極,第二電極在基底上的正投影與第一電極在基底上的正投影重合,柵電極在基底上的正投影與有源層在基底上的正投影重合,第二電極通過柵絕緣層過孔與有源層連接。其中,柵電極在基底上的正投影與第二電極在基底上的正投影部分重合,重合區域寬度為d,d=0~3000埃。優選地,重合區域寬度d等于0。本發明實施例提供了一種垂直型薄膜晶體管及其制備方法,由于柵電極和第二電極通過一次構圖工藝形成,減少了工藝流程,提高了生產效率,降低了成本。同時,由于柵電極和第二電極同層設置,對位精度高,提升了良品率。進一步地,垂直型薄膜晶體管有效減小了薄膜晶體管的尺寸,提高了開口率,實現了高分辨率顯示。下面通過垂直型薄膜晶體管的制備過程進一步說明本發明實施例的技術方案。第一實施例圖4~8為本發明制備垂直型薄膜晶體管第一實施例的示意圖。其中,本實施例中所說的“構圖工藝”包括沉積膜層、涂覆光刻膠、掩模曝光、顯影、刻蝕、剝離光刻膠等處理,是現有成熟的制備工藝。沉積可采用濺射、蒸鍍、化學氣相沉積等已知工藝,涂覆可采用已知的涂覆工藝,刻蝕可采用已知的方法,在此不做具體的限定。第一次構圖工藝中,在基底上形成緩沖層和第一電極圖案。形成緩沖層和第一電極圖案包括:在基底10上依次沉積緩沖層和第一金屬薄膜;在第一金屬薄膜上涂覆一層光刻膠,采用單色調掩膜版對光刻膠進行曝光并顯影,在第一電極和數據線圖案位置形成未曝光區域,保留光刻膠,在其它位置形成完全曝光區域,無光刻膠,暴露出第一金屬薄膜;對完全曝光區域的第一金屬薄膜進行刻蝕并剝離剩余的光刻膠,形成緩沖層11、第一電極18和數據線(未示出)圖案,如圖4所示。其中,基底可以采用玻璃基底或石英基底,緩沖層用于阻擋基底中離子對薄膜晶體管的影響,可以采用氮化硅sinx、氧化硅siox或sinx/siox的復合薄膜,第一金屬薄膜可以采用鉑pt、釕ru、金au、銀ag、鉬mo、鉻cr、鋁al、鉭ta、鈦ti、鎢w等金屬中的一種或多種。第二次構圖工藝中,在形成有第一電極圖案和緩沖層的基底上,形成隔離層圖案。形成隔離層圖案包括:在形成有第一電極圖案和緩沖層的基底上涂覆有機薄膜,采用單色調掩膜版對有機薄膜進行曝光并顯影,在隔離層圖案位置形成未曝光區域,保留有機薄膜,在其它位置形成完全曝光區域,無有機薄膜,形成位于第一電極18上的隔離層13圖案,隔離層13在基底10上的正投影與第一電極18在基底10上的正投影重合,但隔離層13的正投影寬度小于第一電極18正投影寬度,使隔離層13的至少一側露出第一電極18的部分表面,如圖5所示。其中,隔離層13的厚度為0.5μm~2.0μm,該厚度決定了溝道的長度。實際實施時,由于薄膜晶體管制備中膜層厚度的控制精度優于圖案位置的控制精度,因此本實施例薄膜晶體管具有溝道長度控制精度高的優點。本實施例中,隔離層鄰近有源層一側露出第一電極的部分表面,第一電極露出的部分表面用于在后續工藝中使有源層與第一電極連接。實際實施時,第一電極露出的部分表面的寬度可以設置為0.5μm~1.5μm。第三次構圖工藝中,在形成有隔離層圖案的基底上,形成有源層圖案。形成有源層圖案包括:在形成有前述圖案的基底上沉積有源層薄膜,在有源層薄膜上涂覆一層光刻膠;采用單色調掩膜版對光刻膠進行曝光并顯影,在有源層圖案位置形成未曝光區域,保留光刻膠,在其它位置形成完全曝光區域,無光刻膠,暴露出有源層薄膜;對完全曝光區域的有源層薄膜進行刻蝕并剝離剩余的光刻膠,形成有源層15圖案,有源層15的一部分位于隔離層13上,另一部分位于緩沖層11上,中間部分與第一電極18露出的部分表面相接觸,如圖6所示。其中,有源層厚度為2000~8000埃,材料既可以是非晶硅、多晶硅或微晶硅材料,形成ltps薄膜晶體管,也可以是金屬氧化物材料,形成oxide薄膜晶體管,金屬氧化物材料可以是銦鎵鋅氧化物(indiumgalliumzincoxide,igzo)或銦錫鋅氧化物(indiumtinzincoxide,itzo)。第四次構圖工藝中,在形成有有源層圖案的基底上,形成柵絕緣層圖案。形成柵絕緣層圖案包括:在形成有前述圖案的基底上沉積柵絕緣薄膜;在柵絕緣薄膜上涂覆一層光刻膠,采用單色調掩膜版對光刻膠進行曝光并顯影,在過孔圖案位置形成完全曝光區域,無光刻膠,暴露出柵絕緣薄膜,在其它位置形成未曝光區域,保留光刻膠;對完全曝光區域的柵絕緣薄膜進行刻蝕并剝離剩余的光刻膠,形成具有過孔的柵絕緣層16圖案,柵絕緣層16覆蓋第一電極18、隔離層13和有源層15,并覆蓋整個基底,過孔露出有源層15,設置在位于隔離層13上的有源層15位置,如圖7所示。其中,柵絕緣層可以采用氮化硅sinx、氧化硅siox或sinx/siox的復合薄膜。第五次構圖工藝中,在形成有柵絕緣層圖案的基底上,同時形成第二電極和柵電極圖案。同時形成第二電極和柵電極包括:在形成有前述圖案的基底上沉積第二金屬薄膜;在第二金屬薄膜上涂覆一層光刻膠,采用單色調掩膜版對光刻膠進行曝光并顯影,在第二電極和柵電極圖案位置形成未曝光區域,保留光刻膠,在其它位置形成完全曝光區域,無光刻膠,暴露出第二金屬薄膜;對完全曝光區域的第二金屬薄膜進行刻蝕并剝離剩余的光刻膠,形成第二電極19和柵電極17圖案,柵電極17和第二電極19同層但隔離,第二電極19在基底上的正投影與第一電極18在基底上的正投影重合,且通過過孔與有源層15連接。柵電極17在基底上的正投影與有源層15在基底上的正投影重合,如圖8所示。其中,第二金屬薄膜可以采用鉑pt、釕ru、金au、銀ag、鉬mo、鉻cr、鋁al、鉭ta、鈦ti、鎢w等金屬中的一種或多種。本實施例中,第四次構圖工藝形成具有過孔的柵絕緣層圖案時,還包括采用底切(undercut)方式在柵電極與第二電極斷開的位置形成底槽的處理。底槽用于使同時形成的柵電極和第二電極在基底上的正投影部分重合,以避免在柵電極與第二電極之間有間隙而無法形成柵控制溝道。具體地,第四次構圖工藝在對完全曝光區域的柵絕緣薄膜進行刻蝕過程中,采用底切或過刻蝕方式,在過孔鄰近柵電極一側的側壁上形成底槽結構。實際制備時,可以采用灰度曝光方式控制過孔兩側側壁形貌不一致,過孔鄰近柵電極一側的側壁上為底槽結構,而過孔的另一側的側壁為常規結構。在第五次構圖工藝中,同層的柵電極和第二電極在過孔的底槽結構處斷開,柵電極鄰近第二電極的端部位于過孔之外的柵絕緣層上,第二電極鄰近柵電極的端部位于過孔之內,并延伸到底槽結構的側壁,使柵電極在基底上的正投影與第二電極在基底上的正投影部分重合,重合區域寬度d=0~3000埃,如圖9所示。實際實施時,可以通過過孔和底槽結構的結構設計使重合區域寬度d等于0,即柵電極鄰近第二電極的端部在基底上的正投影位置與第二電極鄰近柵電極的端部在基底上的正投影位置相接觸。本實施例通過柵電極與第二電極位置的設計,避免了在柵電極與第二電極之間有間隙而無法形成柵控制溝道,提高了薄膜晶體管的電學性能。本實施例中,“寬度”是指陣列基板的數據線寬度方向的特征尺寸,或者說,是指垂直于數據線長度方向的特征尺寸。因此,柵電極(第二電極、有源層、隔離層或第一電極)在基底上正投影的寬度是指,在數據線長度的垂直方向(如圖4~8所示平面的水平方向),柵電極(第二電極、有源層、隔離層或第一電極)截面的特征尺寸。此外,本實施例中,“重合”是指,兩圖案在基底上的正投影范圍完全相同,即兩圖案在基底上正投影的寬度相同,或一圖案在基底上的正投影范圍位于另一圖案在基底上的正投影范圍之內,即一圖案在基底上的正投影的寬度小于另一圖案在基底上的正投影的寬度。“部分重合”是指,一圖案在基底上的正投影范圍與另一圖案在基底上的正投影范圍部分重疊。通過圖4~9所示的制備薄膜晶體管過程可以看出,本實施例通過5次普通掩膜的構圖工藝,形成了具有6個膜層的垂直型薄膜晶體管。與現有垂直型薄膜晶體管具有7個膜層、需要6次構圖工藝制備相比,減少了一個膜層和一次構圖工藝,工藝流程得到簡化,提高了生產效率,降低了成本。同時,由于柵電極和第二電極同層設置,對位精度高,提升了良品率。進一步地,垂直型薄膜晶體管有效減小了薄膜晶體管的尺寸,提高了開口率,實現了高分辨率顯示。現有薄膜晶體管制備中,溝道刻蝕過程中普遍存在溝道損傷的問題。而由于本實施例制備方法不存在溝道刻蝕工藝,因此本實施例不僅有效消除了現有技術存在的溝道損傷問題,而且所制備垂直型薄膜晶體管的溝道具有較高的溝道均勻性。由于溝道長度由隔離層厚度確定,因此溝道長度的控制精度高,提高了薄膜晶體管的性能。雖然薄膜晶體管整體上為垂直結構,但各膜層均設置有水平覆蓋結構,可以補償垂直方向覆蓋面積少的問題。例如,有源層的一部分水平鋪設在隔離層上,另一部分水平鋪設在緩沖層上,中間部分與第一電極的表面接觸。又如,柵電極的一部分水平鋪設在柵絕緣層上,另一部分水平鋪設在緩沖層上。目前,使用0.5μm的高精度曝光設備可以實現本實施例垂直型薄膜晶體管各膜層的制備。本實施例做制備的垂直型薄膜晶體管包括:設置在基底10上的緩沖層11;設置在緩沖層11上的第一電極18;設置在第一電極18上的間隔層13,隔離層13鄰近有源層一側露出第一電極18的部分表面;設置在間隔層13、第一電極18和緩沖層11上的有源層15,有源層15一部分設置在隔離層13上,另一部分設置在緩沖層11上,且與第一電極18露出的部分表面連接;覆蓋第一電極18、間隔層13和有源層15且具有過孔的柵絕緣層16,過孔露出有源層15;設置在柵絕緣層16上的柵電極17和第二電極19,第二電極19在基底上的正投影與第一電極18在基底上的正投影重合,第二電極19的正投影寬度小于第一電極18的正投影寬度,第二電極19通過過孔與有源層15連接;柵電極17在基底上的正投影與有源層15在基底上的正投影重合,柵電極17的正投影寬度小于有源層15的正投影寬度。柵電極17在基底上的正投影與第二電極19在基底上的正投影部分重合,優選地,重合區域寬度d等于0。第二實施例圖10~圖13為本發明制備薄膜晶體管第二實施例的示意圖。本實施例是基于第一實施例的一種擴展,其特點是通過一次構圖工藝形成第一電極和隔離層圖案。其中,圖10~圖13中,左側的示意圖為薄膜晶體管位置,右側的示意圖為數據線位置。第一次構圖工藝中,在基底上形成緩沖層、第一電極和隔離層圖案。形成緩沖層、第一電極和隔離層圖案包括:在基底10上依次沉積緩沖層11和第一金屬薄膜20,隨后在第一金屬薄膜20上涂覆有機薄膜30,如圖10所示。采用半色調掩膜版或灰色調掩膜版對有機薄膜進行階梯曝光并顯影,在第一電極位置形成未曝光區域a,具有第一厚度的有機薄膜;在數據線位置形成部分曝光區域b,具有第二厚度的有機薄膜;在其余位置形成完全曝光區域c,無有機薄膜,暴露出第一金屬薄膜20,第一厚度大于第二厚度,如圖11所示。刻蝕掉完全曝光區域c的第一金屬薄膜,形成第一電極18和數據線40,如圖12所示。進行有機薄膜灰化處理,使有機薄膜在整體上去除第二厚度,即去除部分曝光區域b的有機薄膜,形成位于第一電極18上且露出第一電極18部分表面的隔離層13圖案,同時暴露出數據線40的表面,如圖13所示。灰化處理中,在有機薄膜厚度整體減小過程中,第一電極18上的隔離層13的圖案也隨之減小,因而在灰化處理后,使隔離層13在基底上的正投影與第一電極18在基底上的正投影重合,但隔離層13在基底上的正投影寬度小于第一電極18在基底上的正投影寬度,第一電極18的部分表面得以暴露出來。第二次構圖工藝中,在形成有隔離層圖案的基底上,形成有源層圖案,如圖6所示。本實施例第二次構圖工藝與第一實施例的第三次構圖工藝相同,這里不再贅述。第三次構圖工藝中,在形成有有源層圖案的基底上,形成柵絕緣層圖案,如圖7所示。本實施例第三次構圖工藝與第一實施例的第四次構圖工藝相同,這里不再贅述。第四次構圖工藝中,在形成有柵絕緣層圖案的基底上,同時形成第二電極和柵電極圖案,如圖8所示。本實施例第四次構圖工藝與第一實施例的第五次構圖工藝相同,這里不再贅述。通過圖10~圖13所示的制備薄膜晶體管過程可以看出,本實施例通過4次構圖工藝,形成了具有6個膜層的垂直型薄膜晶體管。4次構圖工藝包括3次普通掩膜和1次半色調掩膜或灰色調掩膜。本實施例中,各膜層材料及厚度等參數與第一實施例相同,所形成的垂直型薄膜晶體管的結構與第一實施例相同。本實施例所制備的垂直型薄膜晶體管,不僅具有第一實施例的各種優點,還進一步減少了一次構圖工藝,最大限度地簡化了工藝流程,進一步提高了生產效率,進一步降低了成本。第三實施例在前述第一、第二實施例技術方案基礎上,本申請還提供了一種包括前述垂直型薄膜晶體管的陣列基板。陣列基板的制備過程包括:在基底上形成薄膜晶體管。在形成有薄膜晶體管的基底上沉積一鈍化層,在鈍化層上涂覆一層光刻膠,采用單色調掩膜版對光刻膠進行曝光并顯影,對鈍化層進行刻蝕并剝離剩余的光刻膠,形成鈍化層過孔圖案,鈍化層過孔位于第二電極位置。其中,鈍化層可以采用氮化硅sinx、氧化硅siox或sinx/siox的復合薄膜。在鈍化層上沉積一透明導電薄膜,在透明導電薄膜上涂覆一層光刻膠,采用單色調掩膜版對光刻膠進行曝光并顯影,對透明導電薄膜進行刻蝕并剝離剩余的光刻膠,形成像素電極圖案,像素電極通過鈍化層過孔與第二電極連接。其中,透明導電薄膜可以采用氧化銦錫ito,氧化銦鋅izo,或者氧化銦錫/銀/氧化銦錫ito/ag/ito復合膜。本實施例所制備的陣列基板包括:設置在基底上的緩沖層;設置在緩沖層上的第一電極和數據線;設置在第一電極上的間隔層,隔離層鄰近有源層一側露出第一電極的部分表面;設置在間隔層、第一電極和緩沖層上的有源層,有源層一部分設置在隔離層上,另一部分設置在緩沖層上,且與第一電極露出的部分表面連接;覆蓋第一電極、間隔層和有源層且覆蓋整個基底的具有過孔的柵絕緣層,過孔露出有源層;設置在柵絕緣層上的柵線、柵電極和第二電極,第二電極在基底上的正投影與第一電極在基底上的正投影重合,第二電極的正投影寬度小于第一電極的正投影寬度,且通過過孔與有源層連接;柵電極在基底上的正投影與有源層在基底上的正投影重合,柵電極的正投影寬度小于有源層的正投影寬度。柵電極在基底上的正投影與第二電極在基底上的正投影部分重合,優選地,重合區域寬度等于0;覆蓋第二電極、柵線、柵電極的鈍化層,鈍化層在第二電極位置設置有鈍化層過孔;設置在鈍化層上的像素電極,像素電極通過鈍化層過孔與第二電極連接。其中,柵電極和第二電極同層且通過一次構圖工藝形成,第一電極、有源層和第二漏電極依次疊設,垂直型薄膜晶體管,溝道區域垂直于基底平面。柵線和柵電極同層,數據線與第一電極同層。在柵線(柵電極)加載柵掃描信號時,鄰近柵電極一側的有源層形成垂直于基底的電流通道,電流通道將與有源層連接的第一電極和第二電極導通,使薄膜晶體管處于開啟狀態,數據信號線上加載的灰階信號通過第一電極、有源層中形成的電流通道、第二電極施加到像素電極上。實際實施時,可以通過控制間隔層的厚度來調整溝道長度,以提升薄膜晶體管的導通電流量,從而提高薄膜晶體管性能。本實施例所提供的陣列基板,由于柵電極和第二電極通過一次構圖工藝形成,減少了工藝流程,提高了生產效率,降低了成本,由于柵電極和第二電極同層設置,對位精度高,提升了良品率。同時,垂直型薄膜晶體管有效減小了薄膜晶體管的尺寸,提高了開口率,實現了高分辨率顯示。第四實施例基于前述實施例的發明構思,本發明實施例還提供了一種顯示面板,該顯示面板包括采用前述實施例的垂直型薄膜晶體管,或包括采用前述實施例的陣列基板。顯示面板可以為:手機、平板電腦、電視機、顯示器、筆記本電腦、數碼相框、導航儀等任何具有顯示功能的產品或部件,可以是液晶(liquidcrystaldisplay,lcd)顯示面板,也可以是有機發光二極管(organiclight-emittingdiode,oled)顯示面板,還可以是其它有機電致發光器件等。在本發明實施例的描述中,需要理解的是,術語“中部”、“上”、“下”、“前”、“后”、“豎直”、“水平”、“頂”、“底”“內”、“外”等指示的方位或位置關系為基于附圖所示的方位或位置關系,僅是為了便于描述本發明和簡化描述,而不是指示或暗示所指的裝置或元件必須具有特定的方位、以特定的方位構造和操作,因此不能理解為對本發明的限制。在本發明實施例的描述中,需要說明的是,除非另有明確的規定和限定,術語“安裝”、“相連”、“連接”應做廣義理解,例如,可以是固定連接,也可以是可拆卸連接,或一體地連接;可以是機械連接,也可以是電連接;可以是直接相連,也可以通過中間媒介間接相連,可以是兩個元件內部的連通。對于本領域的普通技術人員而言,可以具體情況理解上述術語在本發明中的具體含義。雖然本發明所揭露的實施方式如上,但所述的內容僅為便于理解本發明而采用的實施方式,并非用以限定本發明。任何本發明所屬領域內的技術人員,在不脫離本發明所揭露的精神和范圍的前提下,可以在實施的形式及細節上進行任何的修改與變化,但本發明的專利保護范圍,仍須以所附的權利要求書所界定的范圍為準。當前第1頁12