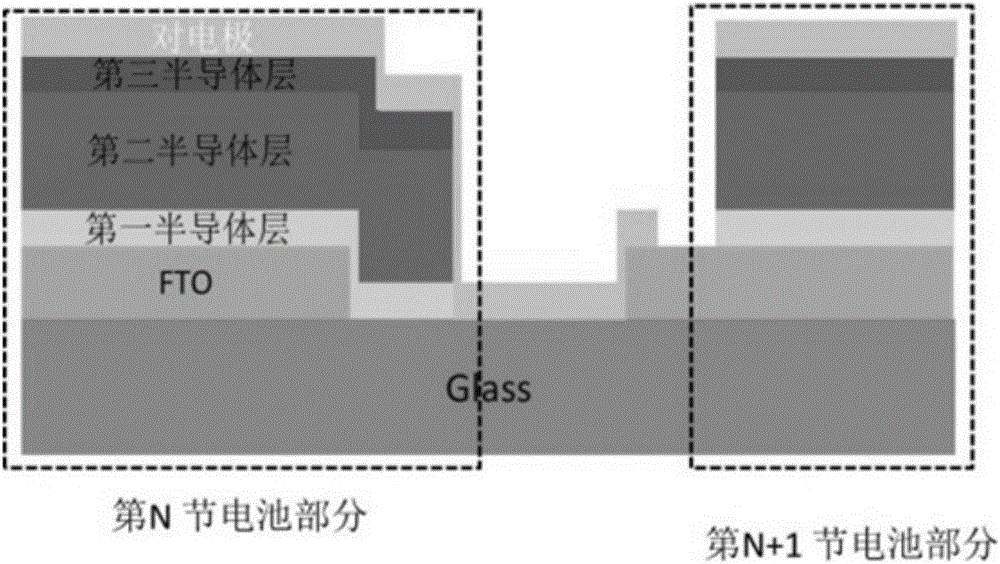
本發明屬于太陽能電池
技術領域:
,具體涉及一種單節鈣鈦礦太陽能電池及其鈣鈦礦太陽能電池模塊。
背景技術:
:太陽能光伏發電是解決目前日益嚴重的能源與環境問題的一種有效手段。經過數十年的發展,電池的種類從傳統的單晶硅電池發展到各類新型太陽能電池,包括無機半導體薄膜電池、有機半導體薄膜電池、染料敏化電池以及鈣鈦礦薄膜電池等。在染料敏化太陽能電池基礎上發展起來的鈣鈦礦太陽能電池,在短短幾年內實現了光電轉換效率的飆升,被Science評為“2013年十大科學突破”之一。鈣鈦礦太陽電池光電轉換效率在短短幾年的研究效率如此迅速的提升,這在太陽能電池研究領域是沒有先例的,已經引起了國內外學術界和工業界廣泛關注和興趣。這種新型太陽能電池包括透明導電基底(透明基底上沉積導電層),在該導電基底上形成的光生電單元(例如,由電子傳輸層、鈣鈦礦光電轉換層和空穴傳輸層形成的光生電單元),以及對電極層。鈣鈦礦太陽能電池可以分為正式和反式兩種,正式太陽能電池基本結構是FTO/電子傳輸層(如二氧化鈦)/鈣鈦礦/空穴傳輸層(如Spiro-MeTAD)/金屬電極(如Au);反型鈣鈦礦電池基本結構是ITO或FTO/空穴傳輸層(如PEDOT:PSS)/鈣鈦礦/電子傳輸層(如PCBM)/金屬電極(如Ag)。相比于其他太陽能電池,作為光電轉換層的有機-無機雜化鈣鈦礦具有大的光吸收系數、高的載流子遷移率和價帶低等特征,是一種非常良好的光吸收材料。2006年,日本Miyasaka課題組首次報道將CH3NH3PbX3型鈣鈦礦用于太陽能電池,光電轉換效率僅為3%。2011年,韓國Park等報道出此類電池效率提升為6.5%。2013年,英國Snaith等將鈣鈦礦太陽能電池提高到9%,這時鈣鈦礦電池的研究引起了太陽能研究領域的高度關注。2014年,韓國Seok課題組通過改善鈣鈦礦形貌與調節鈣鈦礦組成成分,大幅度提高了效率,獲得了超過20%的認證效。2015年,韓禮元等通過優化界面層,大幅度提高了界面層的導電性,進而可以制備大面積的電池,并采用了無機界面層同時提高了器件的穩定性。這是首次認證的大于1cm2的鈣鈦礦太陽能電池器件,獲得了15%的光電轉換效率。鈣鈦礦太陽能電池在電池效率、器件結構和制備方法上有了迅速進步和發展。但是現在報道的鈣鈦礦電池的有效面積相對比較小(0.2cm2以下)、并且器件穩定性差,因此這類太陽能電池產業化任重而道遠。目前,作為一種仍較為新穎的太陽能電池,研究人員對于器件穩定性方面的研究主要集中在改進材料層的性能方面,但是,這種對材料性能的改進往往伴隨著工藝復雜化,以及成本大幅增加的問題。因此,在鈣鈦礦太陽能電池領域,仍缺乏簡便易行且成本較低的可提高器件穩定性方面的工藝設計。技術實現要素:為解決上述問題,本發明的目的在于提供一種單節鈣鈦礦太陽能電池。該電池采用了特殊的結構設計,使得器件穩定性得到改善。本發明的另一目的是提供一種包括上述單節鈣鈦礦太陽能電池的鈣鈦礦太陽能電池模塊。本發明的又一目的是提供一種用于斷開鈣鈦礦太陽能電池中設于基底上的連續導電層的隔斷溝道。為達到上述目的,本發明提供了一種單節鈣鈦礦太陽能電池,該單節鈣鈦礦太陽能電池導電層的至少一個斷開端具有第一斜坡結構,所述第一斜坡結構具有與基底成110-170°的第一坡面。針對現有技術中對器件效率和穩定性方面的改進大多不適用工業化生產的問題,本發明提出了從結構設計層面改善器件效率和穩定性的方案,該方案采用了一種將導電層的斷開端設置為斜坡結構的設計。這種設計基本不會增加現有工藝的成本,卻可以獲得較好的影響因子和穩定性。申請人基于對現有技術中鈣鈦礦太陽能電池結構的深入研究,經過大量研究發現,電池器件穩定性差除了鈣鈦礦本身容易分解的問題外,還存在材料層的斷開端容易產生過薄或局部斷開等缺陷,因此,要提高器件的穩定性,需要設計更合理的結構,以減少上述缺陷的發生。現以現有技術中一種電池模塊的結構為例(參考圖2和圖4)說明上述缺陷形成的原因。圖2的導電層中用于隔離單節電池的溝道側墻呈直角,這將導致后續覆蓋的材料層容易在垂直側墻的上半部分形成一段薄層段(嚴重時會產生孔洞甚至斷開);尤其是對于蒸鍍和濺射工藝制備的材料層而言,這種現象則非常明顯。在蒸鍍和濺射工藝中,材料層是逐步疊加形成的,而蒸鍍和濺射出的材料在直角型的側墻上進行附著是較困難的,這就使得材料層在垂直側墻的上半部分(垂直拐角附近)沉積的較少,會不可避免的形成一段薄層段。由于薄層段的存在,該層材料在此處容易斷開,而材料層的過薄或斷開會影響該層材料的功能(尤其是對于還需要擔負隔斷作用的材料層,大大增加了上下兩層的接觸幾率,容易形成電荷復合),嚴重降低了器件的影響因子和穩定性。基于對上述原因的深刻認識,本發明提出了將導電層的段開端設置為斜坡結構的設計(參考圖1和圖3),使得蒸鍍和濺射出的材料可以在傾斜的側墻上順利附著,而在導電層上最先形成的材料層也會順延這種斜坡趨勢進行生長,后續沉積的材料層也可能延續這種斜坡趨勢,可見,僅是通過導電層的斜坡結構就可以大大減少產生薄層段的問題,因而使得鈣鈦礦太陽能電池的器件影響因子、穩定性、光電轉效率等性能得到顯著的改善。而且,現有技術中的各種形式的鈣鈦礦太陽能電池中導電層的斷開段基本都能采用本發明提供的斜坡結構設計,因此,該方案具有很廣泛的應用范圍。本發明提供的方案中,導電層的斜坡結構可以通過常規的干刻或者濕刻方法獲得,因此,基本不增加工藝成本。在本發明提供的一種優選實施方式中,采用激光蝕刻法制備斜坡結構。本發明提供的方案中,將斜坡結構的第一坡面設置為與基底呈110-170°的角度可以獲得對電池器件穩定性方面較好的改善;在此基礎上,角度可以優選為120-160°,進一步優選為130-155°,更選為140-150°。在上述單節鈣鈦礦太陽能電池中,優選地,所述第一坡面為平面狀坡面或階梯狀坡面。進一步優選地,所述階梯狀坡面由若干臺階單元組成,所述臺階單元的拐角角度大于90°。當第一坡面具有階梯形狀時,通過對臺階高度的合理設計(例如,使臺階單元的高度小于材料易沉積處的最低高度),可避免過薄層的形成,這種結構不僅適用于蒸鍍、濺射制備材料層的工藝,而且還適用于噴涂、旋涂等工藝,液態的材料層能夠在臺階型坡面上形成滯留,從而制備連續的具有第一坡面結構的材料層。在上述單節鈣鈦礦太陽能電池中,優選地,該單節鈣鈦礦太陽能電池包括基底、導電層、對電極,以及設于所述導電層和對電極之間用于實現電子傳輸、光吸收和空穴傳輸功能的光生電單元;所述光生電單元由一層或多層功能材料組成。各層材料的制備工藝可采用現有技術中的常規方法(噴涂、旋涂、磁控濺射或者真空蒸鍍等),具體材料的選用和膜厚等參數的參考現有技術中的方案即可。在上述單節鈣鈦礦太陽能電池中,優選地,所述光生電單元由三層功能材料組成,具體結構為:鈣鈦礦光吸收層為中間層,電子傳輸層和空穴傳輸層分置于鈣鈦礦光吸收層的兩側。在上述單節鈣鈦礦太陽能電池中,優選地,所述基底、導電層、對電極或功能材料之間設置有輔助層,所述輔助層用于改善相應層材料的強度、平整度、粘接性或透光率。在上述單節鈣鈦礦太陽能電池中,優選地,所述導電層選自氧化銦錫層、摻雜鋁的氧化鋅層或摻雜氟的氧化錫層。在上述單節鈣鈦礦太陽能電池中,優選地,所述基底的材質包括玻璃、金屬、陶瓷或耐高溫有機聚合物。在上述單節鈣鈦礦太陽能電池中,優選地,所述電子傳輸層選自無機電子傳輸材料或有機電子傳輸材料中的一種或幾種的組合;其中,所述無機電子傳輸材料包括TiO2、ZnO或SnO2;所述有機電子傳輸材料包括PCBM。在上述單節鈣鈦礦太陽能電池中,優選地,所述空穴傳輸層選自無機空穴傳輸材料或有機空穴傳輸材料中的一種或幾種的組合;其中,所述無機空穴傳輸材料包括NiO、Cu2O或MoO3;所述有機空穴傳輸材料包括Spiro-OMeTAD、PEDOT:PSS或PTAA。在上述單節鈣鈦礦太陽能電池中,優選地,所述鈣鈦礦光吸收層中包含一種或幾種鈣鈦礦材料ABX3,A為NH=CHNH3、CH3NH3或Cs;B為Pb或Sn;X為I、Cl或Br。在上述單節鈣鈦礦太陽能電池中,優選地,所述對電極為金屬電極或非金屬電極,所述金屬電極包括Al、Ag、Au、Mo和Cr中的一種或多種的組合;所述非金屬電極包括碳電極。在上述單節鈣鈦礦太陽能電池中,優選地,在所述第一坡面上方形成的功能材料層中的一層或多層,具有順勢形成的第一斜坡段(由于是在斜角坡面上覆蓋功能材料層,因此,功能材料層該段的底面也為斜面狀,但是對于頂面是否也具有斜面狀不進行限定;優選的情況是頂面和底面都具有斜面狀);進一步優選地,所述電子傳輸層、鈣鈦礦光吸收層和空穴傳輸層具有順勢形成的第一斜坡段;更優選地,在所述功能材料層的斜坡段上方形成的對電極層,具有順勢形成的第一斜坡段。在上述單節鈣鈦礦太陽能電池中,根據本發明提供的導電層斷開端的設計結構的理念,還可以將功能材料層的斷開端設置為斜坡結構,這將有利于制備性能良好的對電極層,從而進一步提供器件的穩定性。優選地,所述功能材料層的斷開端具有第二斜坡結構;所述第二斜坡結構具有與基底成成110-170°的第二坡面;優選為120-160;進一步優選為130-155°;更優選為140-150°。本發明還提供了一種鈣鈦礦太陽能電池模塊(太陽能池組件),其包括兩個以上上述單節鈣鈦礦太陽能電池;各單節鈣鈦礦太陽能電池分置于一塊整體基底材料上。由于在一塊整體基底上可以制備包含若干單節鈣鈦礦太陽能電池的鈣鈦礦太陽能電池模塊,將本發明提供的導電層斷開端的斜坡結構應用于單節電池之間的隔離溝道設計,可以獲得器件穩定性較高的鈣鈦礦太陽能電池模塊。相應地,鈣鈦礦太陽能電池模塊中的功能材料層或對電極層的斷開段也可以設計為斜坡結構,以進一步提高器件穩定性和影響因子。在本發明提供的一種優選實施方式中,該鈣鈦礦太陽能電池模塊中的功能材料層或對電極層的斷開段具有第一斜坡結構,所述第一斜坡結構具有與基底成110-170°的第一坡面;優選為120-160;進一步優選為130-155°;更優選為140-150°。在上述鈣鈦礦太陽能電池模塊中,優選地,相鄰的單節鈣鈦礦太陽能電池之間為串聯連接;進一步優選地,所述串聯連接的具體方式為:前一個單節鈣鈦礦太陽能電池的對電極層與后一個單節鈣鈦礦太陽能電池的導電層聯通。更優選地,與對電極層相連通的導電層的段開端具有第一斜坡結構;這樣可以提高前后兩個單節鈣鈦礦太陽能電池連通的穩定性,從而進一步提高鈣鈦礦太陽能電池模塊的器件穩定性。在本發明提供的一種優選實施方式中,鈣鈦礦太陽能電池模塊包括:透明導電玻璃、第一半導體層、第二半導體層、第三半導體層和對電極層;透明導電玻璃(FTO、ITO、AZO等)通過干刻或者濕刻導電層,得到每個單節鈣鈦礦太陽能電池導電基底,其中每個單節鈣鈦礦太陽能電池由蝕刻的溝道隔開;透明導電玻璃和透明的第一半導體層組成鈣鈦礦太陽能電池的光電極;第一半導體層(電子傳輸層或空穴傳輸層)覆蓋上述導電基底,并具有高的透明度;第二半導體層(鈣鈦礦光吸收層)覆蓋上述第一半導體層;第三半導體層(當第一半導體層為電子傳輸層時,第三半導體層為空穴傳輸層;當第一半導體層為空穴傳輸層時,第三半導體層為電子傳輸層)覆蓋上述第二半導體層;透明導電玻璃基底上的蝕刻溝道的兩面側墻為斜角設置,分別與底面成110-170°的夾角。該鈣鈦礦太陽能電池模塊的具體制備工藝包括以下步驟:(1)通過干刻或者濕刻等方法,蝕刻導電玻璃的基底導電層,進行底部單節電池絕緣隔離,蝕刻寬度大于100nm,厚度為50-500nm,蝕刻的基底導電層側表面與基底夾角為110-170°(形成利于沉積的斜坡);(2)通過噴涂、旋涂、磁控濺射或者真空蒸鍍等方法制備第一半導體層,厚度為10nm-200nm;(3)通過噴涂、旋涂或者真空蒸鍍等方法制備第二半導體層,厚度為50nm-1000nm;(4)通過噴涂、旋涂或者真空蒸鍍等方法制備第三半導體層,厚度為10nm-500nm;(5)通過干刻或者濕刻等方法,蝕刻第一半導體層、第二半導體層和第三半導體層;(6)通過噴涂、旋涂或者真空蒸鍍等方法制備對電極層,厚度為10nm-1000nm;(7)通過干刻或者濕刻等方法,蝕刻電極層,蝕刻寬度為1um-500um。本發明另提供了一種用于斷開鈣鈦礦太陽能電池中設于基底上的連續導電層的隔斷溝道,所述隔斷溝道包括基底材質的底面和導電層材質的兩面側墻,其中,至少一面側墻與底面呈110-170°;優選為120-160°;進一步優選為130-155°;更優選為140-150°。在上述用于斷開鈣鈦礦太陽能電池中設于基底上的連續導電層的隔斷溝道中,優選地,所述底面的寬度至少大于100nm(最大寬度可根據電池的實際要求進行常規設置),側墻的垂直高度50-500nm。在上述用于斷開鈣鈦礦太陽能電池中設于基底上的連續導電層的隔斷溝道中,優選地,所述側墻具有平面狀坡面或階梯狀坡面;進一步優選地,所述階梯狀坡面由若干臺階單元組成,所述臺階單元的拐角角度大于90°。附圖說明圖1為實施例1中鈣鈦礦太陽能電池模塊中具有斜坡結構的隔斷溝道示意圖;圖2為對比例1中鈣鈦礦太陽能電池模塊中具有直角結構的隔斷溝道示意圖;圖3為實施例1中鈣鈦礦太陽能電池模塊的制備流程示意圖;圖4為對比例1中鈣鈦礦太陽能電池模塊的制備流程示意圖。具體實施方式為了對本發明的技術特征、目的和有益效果有更加清楚的理解,現對本發明的技術方案進行以下詳細說明,但不能理解為對本發明的可實施范圍的限定。實施例1本實施例提供了一種鈣鈦礦太陽能電池模塊,斷開鈣鈦礦太陽能電池模塊基底上連續導電層的隔斷溝道的側墻具有斜坡結構(隔斷溝道結構如圖1所示),該斜坡結構具有與基底成135°的坡面,具體制備步驟(制備流程如圖3所示)包括:(1)激光刻蝕鈣鈦礦太陽能電池模塊中隔離單節電池的溝道,具體為:將透明導電玻璃(在透明玻璃基底上已沉積有導電層)放置于夾具之中,調整導電玻璃與投射激光的角度為135°,通過控制軟件設定刻蝕位置和參數,然后按照設定參數對導電玻璃上的導電層進行刻蝕(刻蝕后的溝道為敞口形狀);刻蝕參數具體為功率為2000mW,速度20mm/s,頻率20000Hz,刻蝕寬度為100μm;(2)在上述透明導電基底上通過噴涂、或蒸鍍、或濺射、或絲網印刷的方法依次制備第一半導體層(電子傳輸層)、第二半導體層(鈣鈦礦吸光層)和第三半導體層(空穴傳輸層),具體為:底部電子傳輸層為TiO2層(厚度為20nm致密層和150nm多孔層),鈣鈦礦吸光層為CH3NH3PbI3(厚度為400nm),Spiro-OMeTAD空穴傳輸層,厚度為200nm;(3)激光蝕刻上述第三半導體層至第一半導體層:將透明導電玻璃放置于夾具之中,調整導電玻璃與投射激光的角度為90°,將激光光束聚焦,然后按照設定參數進行刻蝕;刻蝕參數具體為功率為200mW,速度50mm/s,頻率50000Hz,刻蝕寬度為200μm;(4)在上述第三半導體層上,通過蒸鍍方法制備對電極層,具體為:通過蒸鍍方法制備厚度100nmAg;(5)激光蝕刻上述對電極層:將透明導電玻璃放置于夾具之中,調整導電玻璃與投射激光的角度為90°,將激光光束聚焦在Ag對電極表面,然后按照設定參數進行刻蝕,完成一塊鈣鈦礦太陽能電池模塊的制備;刻蝕參數具體為功率為400mW,速度20mm/s,頻率100000Hz,刻蝕寬度為100μm。按照上述步驟分別制備三塊鈣鈦礦太陽能電池模塊,并分別標記為A1、A2和A3。實施例2本實施例提供了一種鈣鈦礦太陽能電池模塊,斷開鈣鈦礦太陽能電池模塊基底上連續導電層的隔斷溝道的側墻具有斜坡結構(呈120°),具體制備步驟包括:(1)激光刻蝕鈣鈦礦太陽能電池模塊中隔離單節電池的溝道,具體為:將透明導電玻璃放置于夾具之中,調整導電玻璃與投射激光的角度為120°,通過控制軟件設定刻蝕位置和參數,然后按照設定參數進行刻蝕;刻蝕參數具體為功率為3000mW,速度100mm/s,頻率30000Hz,刻蝕寬度為100μm;(2)在上述透明導電基底上通過噴涂、或蒸鍍、或濺射、或絲網印刷的方法依次制備第一半導體層(空穴傳輸層)、第二半導體層(鈣鈦礦吸光層)和第三半導體層(電子傳輸層),具體為:底部空穴傳輸層為NiO層(厚度為20nm),鈣鈦礦吸光層為CH3NH3PbI3(厚度為400nm),PCBM電子傳輸層(厚度為120nm);(3)激光蝕刻上述第三半導體層至第一半導體層:將透明導電玻璃放置于夾具之中,調整導電玻璃與投射激光的角度為90°,將激光光束聚焦,然后按照設定參數進行刻蝕;刻蝕參數具體為功率為200mW,速度50mm/s,頻率50000Hz,刻蝕寬度為200μm;(4)在上述第三半導體層上,通過噴涂、或蒸鍍、或濺射、或絲網印刷的方法制備對電極層,具體為:通過蒸鍍方法制備厚度100nmAg;(5)激光蝕刻上述對電極層:將透明導電玻璃放置于夾具之中,調整導電玻璃與投射激光的角度為90°,將激光光束聚焦在Ag對電極表面,然后按照設定參數進行刻蝕;完成一塊鈣鈦礦太陽能電池模塊的制備;刻蝕參數具體為功率為400mW,速度20mm/s,頻率100000Hz,刻蝕寬度為100μm。按照上述步驟分別制備三塊鈣鈦礦太陽能電池模塊,并分別標記為B1、B2和B3。實施例3本實施例提供了一種鈣鈦礦太陽能電池模塊,斷開鈣鈦礦太陽能電池模塊基底上連續導電層的隔斷溝道的側墻具有斜坡結構(呈150°),具體制備步驟包括:(1)激光刻蝕鈣鈦礦太陽能電池模塊中隔離單節電池的溝道,具體為:將透明導電玻璃放置于夾具之中,調整導電玻璃與投射激光的角度為150°,通過控制軟件設定刻蝕位置和參數,然后按照設定參數進行刻蝕;刻蝕參數具體為功率為3000mW,速度100mm/s,頻率30000Hz,刻蝕寬度為100μm;(2)在上述透明導電基底上通過噴涂、或蒸鍍、或濺射、或絲網印刷的方法依次制備第一半導體層(空穴傳輸層)、第二半導體層(鈣鈦礦吸光層)和第三半導體層(電子傳輸層),具體為:底部空穴傳輸層為NiO層(厚度為20nm),鈣鈦礦吸光層為CH3NH3PbI3(厚度為400nm),PCBM電子傳輸層(厚度為120nm);(3)激光蝕刻上述第三半導體層至第一半導體層:將透明導電玻璃放置于夾具之中,調整導電玻璃與投射激光的角度為90°,將激光光束聚焦,然后按照設定參數進行刻蝕;刻蝕參數具體為功率為200mW,速度50mm/s,頻率50000Hz,刻蝕寬度為200μm;(4)在上述第三半導體層上,通過噴涂、或蒸鍍、或濺射、或絲網印刷的方法制備對電極層,具體為:通過蒸鍍方法制備厚度100nmAg;(5)激光蝕刻上述對電極層:將透明導電玻璃放置于夾具之中,調整導電玻璃與投射激光的角度為90°,將激光光束聚焦在Ag對電極表面,然后按照設定參數進行刻蝕;完成一塊鈣鈦礦太陽能電池模塊的制備;刻蝕參數具體為功率為400mW,速度20mm/s,頻率100000Hz,刻蝕寬度為100μm。按照上述步驟分別制備三塊鈣鈦礦太陽能電池模塊,并分別標記為C1、C2和C3。實施例4本實施例提供了一種鈣鈦礦太陽能電池模塊,斷開鈣鈦礦太陽能電池模塊基底上連續導電層的隔斷溝道的側墻具有斜坡結構(呈135°),具體制備步驟包括:(1)激光刻蝕鈣鈦礦太陽能電池模塊中隔離單節電池的溝道,具體為:將透明導電玻璃放置于夾具之中,調整導電玻璃與投射激光的角度為135°,通過控制軟件設定刻蝕位置和參數,然后按照設定參數進行刻蝕;刻蝕參數具體為功率為3000mW,速度100mm/s,頻率30000Hz,刻蝕寬度為100μm;(2)在上述透明導電基底上通過噴涂、或蒸鍍、或濺射、或絲網印刷的方法依次制備第一半導體層(空穴傳輸層)、第二半導體層(鈣鈦礦吸光層)和第三半導體層(電子傳輸層),具體為:底部空穴傳輸層為NiMgLiO層(厚度為20nm),鈣鈦礦吸光層為(NH2CH=NH2PbI3)0.15(CH3NH3PbI3)0.85(厚度為400nm);PCBM/TiO2電子傳輸層(厚度為120nm);(3)激光蝕刻上述第三半導體層至第一半導體層:將透明導電玻璃放置于夾具之中,調整導電玻璃與投射激光的角度為90°,將激光光束聚焦在,然后按照設定參數進行刻蝕;刻蝕參數具體為功率為200mW,速度50mm/s,頻率50000Hz,刻蝕寬度為200μm;(4)在上述第三半導體層上,通過噴涂、或蒸鍍、或濺射、或絲網印刷的方法制備對電極層,具體為:通過蒸鍍方法制備厚度100nmAg;(5)激光蝕刻上述對電極層:將透明導電玻璃放置于夾具之中,調整導電玻璃與投射激光的角度為90°,將激光光束聚焦在Ag對電極表面,然后按照設定參數進行刻蝕;完成一塊鈣鈦礦太陽能電池模塊的制備;刻蝕參數具體為功率為400mW,速度20mm/s,頻率100000Hz,刻蝕寬度為100μm。按照上述步驟分別制備三塊鈣鈦礦太陽能電池模塊,并分別標記為D1、D2和D3。對比例1本對比例1提供了一種現有技術中的鈣鈦礦太陽能電池模塊,斷開鈣鈦礦太陽能電池模塊基底上連續導電層的隔斷溝道的側墻為近似90°的直角結構(隔斷溝道結構如圖2所示),具體制備過程參照實施例3進行,除了將步驟(1)中的導電玻璃與投射激光的角度調整為90°外,其他參數設置均相同(制備過程如圖4所示)。按照上述步驟分別制備三塊用于對比的鈣鈦礦太陽能電池模塊,分別記為E1、E2和E3。測試例1本測試例提供了實施例1-4和對比例1中鈣鈦礦太陽能電池模塊的性能測試實驗,具體測試數據見表1-表5。表1實施例1中鈣鈦礦太陽能電池模塊性能(電池面積36cm-2)短路電流(mAcm-2)開路電壓(V)影響因子效率(%)A12.0110.150.7114.48A22.0210.160.7214.78A32.0110.140.7214.67表2實施例2中鈣鈦礦太陽能電池模塊性能(電池面積36cm-2)短路電流(mAcm-2)開路電壓(V)影響因子效率(%)B12.1110.070.6914.66B22.110.060.6914.58B32.0910.040.6814.27表3實施例3中鈣鈦礦太陽能電池模塊性能(電池面積36cm-2)短路電流(mAcm-2)開路電壓(V)影響因子效率(%)C12.0410.160.7315.13C22.0210.160.7314.98C32.0310.150.7214.83表4實施例4中鈣鈦礦太陽能電池模塊性能(電池面積36cm-2)短路電流(mAcm-2)開路電壓(V)影響因子效率(%)D12.1310.110.7215.50D22.1110.120.6914.73D32.110.110.6814.44表5對比例1中鈣鈦礦太陽能電池模塊性能(電池面積36cm-2)短路電流(mAcm-2)開路電壓(V)影響因子效率(%)E11.989.150.6511.78E21.819.450.6511.12E31.628.650.628.69通過表1-表5的測試數據可知,實施1-4中制備的溝道側墻為斜坡結構的鈣鈦礦太陽能電池模塊的性能全面優于對比例中的溝道側墻為直角結構的鈣鈦礦太陽能電池模塊。當前第1頁1 2 3