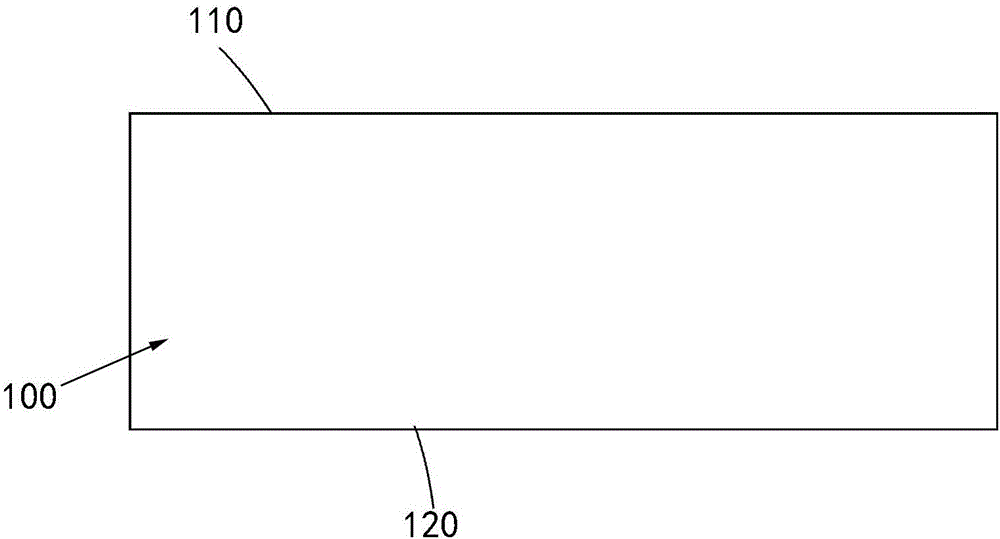
本發明涉及太陽能電池
技術領域:
,具體為一種N型單晶硅雙面電池的制作方法。
背景技術:
:常規的化石燃料日益消耗殆盡,在現有的可再生能源中,太陽能無疑是最有發展前景的替代能源。在所有的太陽能電池中,晶體硅太陽能電池在光伏領域占據著絕對的主導地位。其中,N型硅片由于其材料本身少子壽命高,幾乎無光致衰減(LID),而成為近年來太陽能電池領域研發的熱點。隨著科技水平的不斷發展,原來困擾N型晶體硅太陽能電池的技術難題逐漸被攻克,極大的促進了N型晶體硅太陽能電池在結構和工藝方面的發展。美國SunPower公司生產的背面接觸太陽能電池(IBC)和日本Sanyo公司生產的HIT太陽能電池就是基于N型晶體硅襯底制作的商業化太陽能電池。這兩款電池是目前商業化生產轉化效率最高的太陽能電池,也是商業化生產轉換效率突破20%的僅有的兩款太陽能電池。上述兩種電池除了加工復雜外,對電池硅材料和表面鈍化質量要求也非常高,而且IBC電池要求背面上金屬觸點的高對準精度。雙面透光的N型電池,不僅能夠吸收從電池正面入射的太陽光,而且還能夠吸收來自電池背面的散射光、反射光等,從而產生額外的電能。因此,雙面電池能更加充分的利用太陽光,其發電量要遠高于傳統的P型單面電池,提高了電池的發電效益,而且該種電池還適合建筑一體化、垂直安裝等應用。然而傳統的雙面電池的制備方法包括了多步擴散工藝,往往還需要用到離子注入、選擇性發射極、背面局域擴散等復雜技術,整個工藝流程復雜,制備成本高,使得雙面電池大規模的生產及應用遇到了瓶頸。目前,N型雙面太陽能電池的制備方法主要包括如下步驟:1.表面制絨;2.正面擴散制結;3.熱氧化,形成擴散阻擋膜;4.背面擴散制結;5.周邊刻蝕;6.去除擴散后雜質玻璃層;7.去除正面阻擋膜;8.鍍膜(一般是雙面沉積氮化硅);9.絲網印刷并燒結形成金屬化接觸電極。在上述制備工藝中,N型雙面電池需要對硅襯底進行雙面摻雜,目前太陽能電池生產中主要利用液態磷源、硼源作為摻雜源,在N型硅襯底的兩面分別形成n+層、p+層,其中摻P或摻B的先后順序因具體工藝路線而有所不同。以先摻B為例,現有工藝主要采用氣體攜帶三溴化硼分子的方式進行擴散,為了保證硼源有足夠的空間散布到硅片上,相鄰硅片之間需要保持一定的距離,導致產能受到限制。同時,在非擴硼面也會不可避免的沾染到硼源而形成PN結,后期需要額外的清洗步驟去除,影響了生產加工的效率。上述擴散方式中,擴散的均勻性難以控制;并且擴散溫度較高(1000℃左右),擴散溫度過高會使得晶體硅襯底性能變壞。在完成單面摻雜形成p+層后,為了避免正反面擴散的互相繞擴影響,需要增加一層擴散阻擋膜層(阻擋膜通常采用熱氧化形成SiO2氧化層,或PECVD形成SiNX膜)。熱氧化生長的SiO2薄膜作為摻P面的擴散阻擋層的方法涉及高溫過程,熱氧化的溫度高達1000℃以上,同時氧化時間不少于30min以形成厚度約100nm的SiO2薄膜。此高溫過程易導致p+層的擴散曲線發生改變,如表面摻雜濃度的降低,結深的增加,導致電池的串聯電阻增加,電接觸性能下降;同時高溫過程易導致硅襯底的摻雜濃度增加,電池的體復合隨之加劇,最終表現為開路電壓和整體效率的下降。并且生長擴散阻擋膜的過程中同樣會有繞擴的問題,使得阻擋擴散的效果并不好;另外,對于P型表面(擴硼面)的鈍化及減反射效果,主要通過制作氮化硅或氧化硅實現的。但是,其中氮化硅的方式由于氮化硅帶正電荷,屬負電中心,因此對P型表面的鈍化效果很差;氧化硅采用的是熱氧化的方法制備,該方法需要至少800℃以上的高溫過程,能耗高且容易破壞已形成的PN結形貌,工藝較難把控。技術實現要素:為解決上述現有技術中的至少一種缺陷,本發明提供了一種N型單晶硅雙面電池的制作方法,所采用的N型硅片襯底包括第一表面和與所述第一表面相對設置的第二表面,所述方法包括:對所述硅片襯底進行表面制絨處理;對所述硅片襯底的第一表面進行硼擴散處理,制得硼摻雜層;在所述硼摻雜層形成至少一層掩膜;對所述硅片襯底的第二表面進行磷擴散處理,制得磷摻雜層;去除所述至少一層掩膜;以及分別在通過硼擴散處理的第一表面以及通過磷擴散處理的第二表面制作電極,制得所述N型單晶硅雙面電池。根據本發明的一實施方式,所述表面制絨處理包括:以氫氧化鈉或氫氧化鉀溶液對所述硅片襯底的第一表面、第二表面進行處理,在所述第一表面、第二表面制得陷光結構;以及用鹽酸和氫氟酸對所述第一表面、第二表面進行清洗。根據本發明的一實施方式,所述硼擴散處理包括:通過旋涂的方式在硅片襯底的第一表面涂抹液態硼源,并對所述硅片襯底進行烘干處理;以及將經過烘干處理的硅片襯底于擴散爐管中進行硼擴散。根據本發明的一實施方式,所述至少一層掩膜包括位于所述硼摻雜層上的二氧化硅掩膜層以及位于所述二氧化硅掩膜層上的氮化硅掩膜層。根據本發明的一實施方式,所述磷擴散處理包括:在所述第二表面沉積二氧化硅層;以及在沉積了二氧化硅層的第二表面進行磷擴散處理。根據本發明的一實施方式,待所述硼擴散處理、磷擴散處理完成后,通過等離子刻蝕或激光刻蝕去除周邊的邊結。根據本發明的一實施方式,在所述硼摻雜層的表面通過等離子化學氣相沉積法形成氧化鋁鈍化層。根據本發明的一實施方式,在所述氧化鋁鈍化層上形成至少一層氮化硅減反射層。根據本發明的一實施方式,在所述磷摻雜層的表面通過等離子化學氣相沉積法形成二氧化硅鈍化層;以及在所述二氧化硅鈍化層上形成至少一層氮化硅減反射層。本發明一實施方式的N型單晶硅雙面電池的制作方法,工藝簡單,有效地提高了電池的效率。附圖說明通過結合附圖考慮以下對本發明的優選實施例的詳細說明,本發明的各種目標、特征和優點將變得更加顯而易見。附圖僅為本發明的示范性圖解,并非一定是按比例繪制。在附圖中,同樣的附圖標記始終表示相同或類似的部件。其中:圖1為本發明一實施方式的硅片襯底的結構示意圖;圖2是本發明一實施方式的經過清洗制絨后的硅片的結構示意圖;圖3是本發明一實施方式的經過清洗制絨后在第一、第二表面制備二氧化硅膜的硅片的結構示意圖;圖4是本發明一實施方式的第一表面的二氧化硅膜上均勻涂上硼源后的硅片的結構示意圖;圖5是本發明一實施方式的第一表面上形成P+層的硅片的結構示意圖;圖6是本發明一實施方式的去除P+層上硼硅玻璃后的硅片的結構示意圖;圖7是本發明一實施方式的在P+層上制備二氧化硅掩膜后的硅片的結構示意圖;圖8是本發明一實施方式的在二氧化硅掩膜上制備氮化硅掩膜后的硅片的結構示意圖;圖9是本發明一實施方式的去除第二表面二氧化硅膜后的硅片的結構示意圖;圖10是本發明一實施方式的在第二表面制備二氧化硅膜阻擋層后的硅片的結構示意圖;圖11是本發明一實施方式在第二表面制備N+層后的硅片的結構示意圖;圖12是本發明一實施方式的去除第一表面氮化硅掩膜后的硅片的結構示意圖;圖13是本發明一實施方式的去除第一表面二氧化硅掩膜及第二表面N+層磷硅玻璃后的硅片的結構示意圖;圖14是本發明一實施方式的在第一表面制備氧化鋁鈍化層后的硅片的結構示意圖;圖15是本發明一實施方式的在第一表面的氧化鋁鈍化層上制備三層氮化硅減反射膜后的硅片的結構示意圖;圖16是本發明一實施方式的在第二表面的N+層上制備二氧化硅鈍化層后的硅片的結構示意圖;圖17是本發明一實施方式的在第二表面二氧化硅鈍化層上制備兩層氮化硅減反射膜后的硅片的結構示意圖;圖18是本發明一實施方式制得的N型單晶硅雙面電池的結構示意圖;圖19是本發明另一實施方式制得的N型單晶硅雙面電池的結構示意圖。具體實施方式體現本發明特征與優點的典型實施方式將在以下的說明中詳細敘述。應理解的是本發明能夠在不同的實施方式上具有各種的變化,其皆不脫離本發明的范圍,且其中的說明及圖示在本質上是當作說明之用,而非用以限制本發明。本發明一實施方式提供了一種N型單晶硅雙面電池的制作方法,所采用的N型硅片襯底包括第一表面和與所述第一表面相對設置的第二表面,所述方法包括:對所述硅片襯底進行表面制絨處理;對所述硅片襯底的第一表面進行硼擴散處理;在通過硼擴散處理后的第一表面上形成至少一層掩膜;對所述硅片襯底的第二表面進行磷擴散處理;去除所述至少一層掩膜;以及分別在通過硼擴散處理的第一表面以及通過磷擴散處理的第二表面制作電極,制得所述N型單晶硅雙面電池。本發明一實施方式的雙面太陽能電池,所使用的是N型硅片,N型硅片具有較長的少數載流子壽命,并且太陽能電池背面使用磷重摻雜,電池無翹曲,能加工更薄的硅襯底;電池背面印刷電極后,在磷背場作用下,可將入射到太陽能電池背面光產生的載流子收集,實現了雙面光電轉化效應。與現有P型單面電池相比,本發明一實施方式的雙面電池具有更好的弱光響應和溫度特性,在早晨和傍晚能發出更多的電量。如圖1至19所示,本發明一實施方式的N型單晶硅雙面電池的制作方法,以N型硅片為襯底,硅片襯底100包括第一表面110和與第一表面110相對設置的第二表面120。具體地,雙面電池的制作方法包括如下步驟:S1:對硅片襯底100進行表面制絨處理于本發明的一實施方式中,可先將原始硅片襯底100在氫氧化鈉及雙氧水的混合液中進行超聲清洗,再利用氫氧化鈉和制絨添加劑的混合液對硅片襯底100的第一表面110、第二表面120進行處理,制備出具有大小均勻的金字塔形狀的陷光結構,以提高所制作的雙面電池的陷光性,增加太陽光的利用率。隨后分別用鹽酸和氫氟酸混合液、去離子水對硅片襯底100進行漂洗,得到如圖2所示的具有陷光結構的硅片襯底100。其中,氫氧化鈉及雙氧水的混合液中,純度≥98%(EL級)氫氧化鈉的濃度可以為2~10wt%,雙氧水的質量濃度可以為25%~30%;氫氧化鈉和制絨添加劑的混合液中,氫氧化鈉的濃度可以為2~10wt%,制絨添加劑可以為常州時創TS45、德清麗晶S403等單晶硅制絨輔助品;鹽酸和氫氟酸混合液中,鹽酸的質量濃度可以為36~38%,氫氟酸的質量濃度可以為48~50%。S2:對硅片襯底100的第一表面110進行硼擴散處理于本發明的一實施方式中,硼擴散處理包括:通過旋涂的方式在硅片襯底100的第一表面110涂抹液態硼源,并對硅片襯底100進行烘干處理;然后將經過烘干處理的硅片襯底100于擴散爐管中進行硼擴散。通過旋涂的方式在硅片襯底的第一表面涂抹液態硼源,不僅提高了硼擴散的均勻性,使得擴散時爐管的產能得到提高;同時,還能夠有效控制硼源的涂布范圍,使得在非擴散區域不會沾染到硼源,省去了后期的額外清洗步驟。另外,由于各個硅片之間無需保留類似氣體攜帶硼源擴散時的較大距離,因此擴散時相鄰硅片之間的距離可以適當減小,大大增加了單爐擴散硅片的數量,提高了生產線擴散工序的產能。具體地,如圖3所示,先以體積比為6:2:1的濃HNO3(質量濃度65~68%)、雙氧水(質量濃度25~30%)、鹽酸(質量濃度36~38%)混合液,于2~15min內處理硅片襯底100,在第一表面110、第二表面120分別制備出厚度為2~10nm的二氧化硅膜111、121。其中,二氧化硅膜111可以提高P+擴散層方阻的均勻性,二氧化硅膜121可以形成阻擋層,減小硼對硅片第二表面120繞擴的影響;接著,如圖4所示,通過旋涂的方式在二氧化硅膜111的表面中心區域滴定硼源,滴定量為0.2~1.5cc,然后利用旋轉的方式使硅片上的硼源均勻分布,硅片旋轉轉速可以為500~2500轉/分,再對旋涂硼源的硅片進行烘干處理,烘干溫度可以為100~250℃,時間為1~10min;本發明對所使用的硼源沒有限定,可以為現有的硼源。將經過烘干處理的硅片在擴散爐管中進行硼擴散,在爐管中進行硼擴散時,擴散溫度可以為850~950℃,氧氣與氮氣的體積比可以為1:5~1:20,擴散時間可以為45min~2h,得到擴散方阻為40~100ohm/sq。從而,在硅片襯底100的第一表面110形成P+層——硼摻雜層112,具體如圖5所示。S3:在硼摻雜層112上沉積掩膜如圖5、6所示,可通過濕法刻蝕設備利用HF溶液將經過步驟S2處理后的硅片襯底100表面的硼硅玻璃(BSG)去除,硼硅玻璃是在進行硼擴散過程中形成的副產物;接下來,如圖7所示,可通過濃HNO3(質量濃度65~68%)、雙氧水(質量濃度25~30%)、鹽酸(質量濃度36~38%)的混合液在硼擴散層112的表面制備厚度例如為2~10nm的二氧化硅掩膜113。其中,濃HNO3、雙氧水、鹽酸的體積比可以為6:2:1,混合液對硼擴散層112的作用時間可以為2~10min。二氧化硅掩膜113不僅可以作為阻擋層,降低第二表面120磷擴散的繞擴影響,還可以減小沉積氮化硅膜過程中對PN結的不利影響。厚度為20~30nm的氮化硅膜已經能夠阻擋方阻為50~70ohm/sq范圍的雜質擴散。利用這一特性將其應用于N型雙面電池第二次擴散的阻擋層,能夠有效避免熱氧化高溫過程對電池接觸性能及開路電壓的影響。如圖8所示,可利用PECVD在二氧化硅掩膜113上沉積一層厚度例如為20~50nm的氮化硅掩膜114;沉積溫度可以為300~470℃,反應壓強可以為185~220Pa,功率可以為2000~4000W。本發明一實施方式采用二氧化硅掩膜113+氮化硅掩膜114形成的疊層掩膜以對擴散硼的表面進行保護,防止后續制作步驟影響到擴散硼的表面。利用高致密的二氧化硅+氮化硅作為擴散阻擋層實現N型電池的雙面擴散,避免了傳統工藝中采用熱氧化二氧化硅薄膜作為擴散阻擋層時所經歷的高溫過程,保證一次擴散曲線及硅襯底的雜質濃度不變,實現了N型雙面電池良好的電接觸性能,并有效降低電池的體復合速率。S4:磷擴散處理如圖9所示,可通過濕法刻蝕設備利用HF和HNO3的混合液對硅片襯底100的第二表面120進行清洗,以去除第二表面120的二氧化硅膜121;接下來,如圖10所示,可通過濃HNO3、H2O2、鹽酸的混合液在第二表面120制備厚度例如為2~10nm的二氧化硅膜122。其中,濃HNO3、H2O2、鹽酸的體積比可以為6:2:1,混合液對第二表面120的作用時間可以為2~10min;然后,如圖11所示,將硅片襯底100的第二表面120在擴散爐中進行磷擴散形成N+層——磷摻雜層123;磷擴散的擴散溫度可以為800~900℃,擴散時間可以為30min~2h,擴散方阻為20~60Ω。本發明一實施方式中,二氧化硅膜122可采用室溫、濕法氧化或快速臭氧氧化工藝制備,不但避免了高溫熱氧化對硅片造成的不利影響,而且可以作為電池第二次擴散的阻擋層,提高背面N+層擴散方阻的均勻性。S5:去除掩膜如圖12所示,可通過熱磷酸對氮化硅、二氧化硅薄膜進行選擇性刻蝕,將硅片襯底100浸泡于155~165℃的熱磷酸中5~15min,可去除第一表面110的氮化硅掩膜114;如圖13所示,將硅片浸泡于HF溶液中,以去除第一表面110的二氧化硅掩膜113及第二表面120的磷硅玻璃,磷硅玻璃是在進行磷擴散過程中形成的副產物;所采用的HF溶液的質量濃度可以為5%,浸泡時間可以為5~10min;在去除磷硅玻璃的同時,HF溶液將步驟S5中制作的二氧化硅掩膜113也一同去除,從而暴露出制作的P型層。S6:電極制作于本發明的一實施方式中,可通過絲網印刷制作電極。具體地,可在第一表面110的硼摻雜層的上部印刷銀鋁漿,形成如圖18所示的電池正極119,電池正極119所在的表面為電池的正面,在第二表面120的磷摻雜層的上部印刷銀漿,形成如圖18所示的電池負極127,電池負極127所在的表面為電池的背面;然后于600~950℃的溫度下,將上述硅片在燒結爐中進行燒結,讓電極和硅形成歐姆接觸,即得到如圖18所示的電池成品。于本發明的一實施方式中,可在磷擴散處理步驟之后,進行周邊PN結的去除步驟,具體可通過等離子刻蝕工藝或激光刻蝕工藝去除邊結。另外,待電池制成后,可通過激光刻蝕電池正面邊結(參見圖19),以減少電池漏電。于本發明的一實施方式中,如圖14所示,可在硼擴散層112的表面形成氧化鋁鈍化層115。氧化鋁鈍化層115的厚度可以為6~15nm,其可通過等離子化學氣相沉積法形成,沉積溫度可以為300~400℃,反應壓強可以為180~230Pa,功率可以為1000~4000W。于本發明的另一實施方式中,還可在氧化鋁鈍化層115上形成至少一層氮化硅減反射層。如圖15所示,氮化硅減反射層可以為三層,分別為:厚度為26~33nm、折射率為2.6~2.8的氮化硅減反射層116,厚度為20~29nm、折射率為2.1~2.5的氮化硅減反射層117,厚度為47~56nm、折射率為2.0~2.1的氮化硅減反射層118。氮化硅減反射層可通過等離子化學氣相沉積法形成,沉積溫度可以為300~400℃,反應壓強可以為180~220Pa,功率可以為2000~4000W。本發明一實施方式的氧化鋁鈍化層的制作方法屬于低溫工藝,不會破壞PN結。且針對電池正面P+層和背面N+層的不同特性,在電池正面采用鈍化效果更好的氧化鋁與氮化硅疊層鈍化的方式,氧化鋁起到鈍化作用,氮化硅起到保護及調整光學參數,降低電池正面反射率的作用。由于氧化鋁與硅接觸面具有較高固定負電荷密度,通過屏蔽正表面P型硅表面光生電子而表現出顯著的內電場效應而起到鈍化特性,使得硅片表面的鈍化效果較傳統鋁背場鈍化技術有較大的提升;另外,氧化鋁薄膜在低摻雜和高摻雜的P型硅表面具有很好的熱穩定性,這一點對于絲網印刷太陽電池來說尤為重要;氧化鋁薄膜對于可見光波段的光完全透明,且具有較低溫度(100~350℃)的生長窗口。于本發明的一實施方式中,如圖16所示,可在磷摻雜層123的表面形成二氧化硅鈍化層124。二氧化硅鈍化層124的厚度可以為10~30nm,其可通過等離子化學氣相沉積法形成,沉積溫度可以為300~470℃,反應壓強可以為185~220Pa,功率可以為2000~4000W。于本發明的另一實施方式中,還可在二氧化硅鈍化層124上形成至少一層氮化硅減反射層。如圖17所示,氮化硅減反射層可以為兩層,分別為:厚度為21~26nm、折射率為2.79~2.92的氮化硅減反射層125及厚度為56~60nm、折射率為1.9~2.0的氮化硅減反射層126。氮化硅減反射層可通過等離子化學氣相沉積法形成,沉積溫度可以為300~470℃,反應壓強可以為185~220Pa,功率可以為2000~4000W。本發明的一實施方式中,在電池背面采用鈍化效果更好的二氧化硅與氮化硅疊層鈍化的方式。其中,二氧化硅起到鈍化作用,氮化硅起到保護及調整光學參數,降低電池背面反射率的作用。本發明一實施方式的N型單晶硅雙面電池,可以在現有常規P型硅太陽能電池生產線的基礎上改造完成,工藝簡單,并且采用該方法制備的N型雙面電池不存在硼繞擴導致的顏色不均勻問題,正反兩面色差較小,滿足太陽電池的外觀需求。以下,結合附圖及具體實施例對本發明的N型單晶硅雙面電池的制作方法做進一步說明。實施例1對硅片襯底100進行表面制絨處理先將原始硅片襯底100在氫氧化鈉及雙氧水的混合液中進行超聲清洗,再利用氫氧化鈉和制絨添加劑的混合液對硅片襯底100的第一表面110、第二表面120進行處理;隨后分別用鹽酸和氫氟酸混合液、去離子水對硅片襯底100進行漂洗,得到如圖2所示的具有陷光結構的硅片襯底100。對硅片襯底100的第一表面110進行硼擴散處理以體積比為6:2:1的濃HNO3、H2O2、鹽酸混合液,于15min內處理硅片襯底100,在第一表面110、第二表面120分別制備出厚度為2~10nm的二氧化硅膜111、121。接著,通過旋涂的方式在二氧化硅膜111的表面中心區域滴定硼源,滴定量為1.0cc,然后利用旋轉的方式使硅片上的硼源均勻分布,硅片旋轉轉速為2000轉/分,再對旋涂硼源的硅片進行烘干處理,烘干溫度為250℃,時間為10min;將經過烘干處理的硅片襯底100在擴散爐管中進行硼擴散,擴散溫度可以為900℃,氧氣與氮氣的體積比可以為1:20,擴散時間為2h,擴散方阻為100ohm/sq。從而,在硅片襯底100的第一表面110形成硼摻雜層112。在硼摻雜層112上沉積掩膜通過濕法刻蝕設備利用HF溶液將經過硼擴散的硅片襯底100表面的硼硅玻璃去除;接下來,通過體積比為6:2:1的濃HNO3、H2O2、鹽酸的混合液在硼擴散層112的表面制備厚度為10nm的二氧化硅掩膜113。混合液對硼擴散層112的作用時間為8min。然后,利用PECVD在二氧化硅掩膜113上沉積一層厚度為40nm的氮化硅掩膜114;沉積溫度為400℃,反應壓強為200Pa,功率為3000W。磷擴散處理通過濕法刻蝕設備利用HF和HNO3的混合液對硅片襯底100的第二表面120進行清洗,以去除第二表面120的二氧化硅膜121;接下來,通過體積比為6:2:1的濃HNO3、H2O2、鹽酸的混合液在第二表面120制備厚度為8nm的二氧化硅膜122,混合液對第二表面120的作用時間為5min;然后,將硅片襯底100的第二表面120在擴散爐中進行磷擴散形成磷摻雜層123;磷擴散的擴散溫度為800℃,擴散時間可以為1h,擴散方阻為30Ω。去除周邊PN結通過等離子刻蝕工藝去除電池周邊PN結。去除掩膜通過熱磷酸對氮化硅、二氧化硅薄膜進行選擇性刻蝕,將硅片襯底100浸泡于155~165℃的熱磷酸中10min,去除第一表面110的氮化硅掩膜114;將硅片浸泡于5%的HF溶液中,去除第一表面110的二氧化硅掩膜113及第二表面120的磷硅玻璃,浸泡時間為10min;在去除磷硅玻璃的同時,HF溶液將二氧化硅掩膜113也一同去除,從而暴露出制作的P型層。在硼擴散層112的表面形成氧化鋁鈍化層115通過等離子化學氣相沉積法在硼擴散層112的表面形成厚度為10nm的氧化鋁鈍化層115,沉積溫度為400℃,反應壓強為200Pa,功率為4000W。在氧化鋁鈍化層115的表面依次形成三層氮化硅減反射層在氧化鋁鈍化層115的表面采用等離子化學氣相沉積法依次沉積厚度為28nm的氮化硅減反射層116、厚度為22nm的氮化硅減反射層117以及厚度為47nm的氮化硅減反射層118。沉積溫度為350℃,反應壓強為180Pa,功率為2000W。在磷摻雜層123的表面形成二氧化硅鈍化層124在磷摻雜層123的表面采用等離子化學氣相沉積法沉積厚度為30nm的二氧化硅鈍化層124,沉積溫度為400℃,反應壓強為220Pa,功率為4000W。在二氧化硅鈍化層124的表面依次形成兩層氮化硅減反射層在二氧化硅鈍化層124的表面采用等離子化學氣相沉積法依次沉積厚度為25nm的氮化硅減反射層125及厚度為57nm的氮化硅減反射層126,沉積溫度為400℃,反應壓強為190Pa,功率為2000W。電極制作采用印刷的方法在硅片的第一表面110的的硼摻雜層112上印刷銀鋁漿,形成電池正極119,電池正極119所在的表面為電池的正面;在第二表面120的磷摻雜層123上印刷銀漿,形成電池負極127,電池負極127所在的表面為電池的背面;然后于950℃的溫度下,將上述硅片在燒結爐中進行燒結,讓電極和硅形成歐姆接觸,即得到如圖18所示的電池成品。將實施例1制得的N型雙面M2(244.32cm2)單晶硅太陽電池和傳統晶體硅加工技術生產的單晶M2(244.32cm2)電池(對比例)進行了平均電性能測試,兩者均采用意大利Baccini太陽電池I-V測試儀,在測試溫度為25±2℃、太陽模擬器光強為1000±50W/m2標準測試條件下進行測試,相關數據如下表所示:Pmpp/WUoc/VIsc/ARs/ΩRsh/ΩFF/%NCellIrev2/A實施例14.94260.64609.57300.00370380.2320.23%0.043對比例4.90590.64419.49890.00249180.1820.08%0.029其中,Pmpp為最大工作功率,Uoc為開路電壓,Isc為短路電流,Rs為串聯電阻,Rsh為并聯電阻,FF為填充因子,Ncell為電池光電轉換效率,Irev2為電池反向偏壓12V時的漏電流。實施例2本實施例的工藝步驟與實施例1相同,故省略相同內容的說明。兩者的主要區別在于本實施例省略了通過等離子刻蝕工藝去除電池周邊PN結的步驟,同時在電極制作完成后,利用激光刻蝕正面邊結,得到如圖19所示的電池成品。除非特別限定,本發明所用術語均為本領域技術人員通常理解的含義。本發明所描述的實施方式僅出于示例性目的,并非用以限制本發明的保護范圍,本領域技術人員可在本發明的范圍內作出各種其他替換、改變和改進,因而,本發明不限于上述實施方式,而僅由權利要求限定。當前第1頁1 2 3