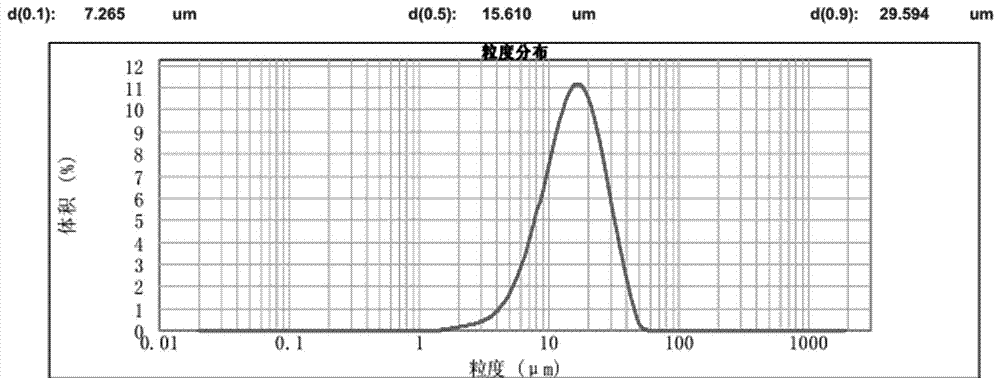
本發明涉及鋰離子二次電池正極材料,特別是具有高放電電壓平臺的鋰離子電池正極材料的制備方法。
背景技術:隨著智能數碼產品的不斷更新換代,不斷豐富的功能極大的改變了我們生活,然而,隨著新功能的不斷增加,對智能設備的動力供給帶來了極大的考驗。在我們使用智能設備的過程中,經常會出現電池掉電快、不耐用等問題。除了設備本身的功耗問題,與鋰離子電池的放電電壓平臺時間有著緊密的聯系,之所以三元正極材料無法使用在手機等智能設備上主要是因為其放電電壓平臺偏低,手機續航能力不足。鋰離子電池充放電電壓平臺反應機理如下:吉布斯相律,兩相反應時自由度為0,化學勢不變,有電壓平臺。具體:基礎物理化學的相律:F=C-P+n其中F:自由度;C:獨立組分數;P:相態數目;n:外界因素,多數取n=2,代表壓力和溫度;在對電極材料的研究中,溫度和壓力為常數,因此n=0.F=C-P在此,我們討論二元系(C=2),如果在一個粒子中含有一個相,即P=1,則F=1,化學勢是一個自由度,隨鋰濃度的變化而變化。如果粒子中包含兩個相,即P=2,則F=0。當兩相共存時,在一個二元系電極材料中存在平坦的電壓平臺。影響鋰離子電池充放電平臺的因素很多,正負極材料自身性能、電池各部件界面問題、電池內阻的控制等。實際生產中在給定材料的前提下多數是通過改善電池內阻的方式來提升平臺。從正極材料的角度考慮,通常是改善材料自身的離子電導性能,降低鋰離子在材料內部的遷移阻力。其次是改善材料比表面積,使材料和電解液充分接觸,擴展鋰離子進入正極材料的通道。降低界面極化。但是一味地將材料比表面提升會產生較多的不良影響:一方面材料的加工性能收到影響,另一方面材料碾壓性能不佳,造成體積能量密度無法提升。
技術實現要素:針對上述問題,本發明提供了一種高放電電壓平臺鋰離子電池正極材料的制備方法。本發明一改常規鋰離子電池正極材料正態分布的特點,采用左偏態分布,通過補充一定量的小顆粒材料,提升材料的比表面積實現材料與電解液的充分接觸,極大的改善了鋰離子電池充放電過程中鋰離子的擴散通道,降低正極材料和電解液界面的極化內阻,提高了鋰離子電池3.6V放電電壓平臺時間,同時較大粒度材料顆粒維持了材料高壓實性能,保證了鋰離子電池的體積能量密度。本發明為了實現材料制備的一致性,通過對粉碎后的材料進行二次修復焙燒,改善了材料表面殘留堿。包括以下步驟:1)初混按照鈷金屬摩爾比,將納米鈷化合物和四氧化三鈷以1:4~1:5的比例投入混料器混合3~8h得到混合鈷料;2)混料將步驟1)得到的混合鈷料進行鈷元素分析,得到混合物鈷元素含量,按照鋰鈷摩爾比,將碳酸鋰和步驟1)得到的混合鈷料以1:1.04~1.1的比例投于高速混料器,同時添加金屬摩爾比例為步驟1)得到的混合物金屬摩爾量的0.1%~0.3%的納米金屬氧化物,將物料按照設定程序混合均勻,得到混合物;3)焙燒將步驟2)中得到的混合物在空氣氣氛輥道爐中加熱到900~1050℃進行焙燒,焙燒8~12h,得到塊狀化合物;4)粉碎處理將步驟3)中得到的塊狀化合物放入氣流粉碎設備進行氣流粉碎,400目篩分處理控制物料最大粒徑后得到初成品;5)二次焙燒取納米鈷化合物,質量占步驟4)得到的初成品的2~4%,和步驟4)得到的初成品在高速混料器混合均勻,然后在空氣氣氛輥道爐中加熱到700~950℃進行二次焙燒,焙燒4~8h,得到新塊狀化合物,將新塊狀化合物解聚并篩分500目篩網,得到粒度分布為左偏態的鋰離子電池正極材料。進一步地,步驟1)和5)中所述的納米鈷化合物為納米無定形態氫氧化亞鈷。進一步地,步驟1)中所述的四氧化三鈷為電池級,粒度為10~18μm。進一步地,步驟2)中所述的納米金屬氧化物為納米二氧化鈦、納米氧化鎂中的一種或兩種的混合。進一步地,步驟2)和5)中所述的高速混料器混料程序設定為150R/min混料5min;600R/min混料10min;800R/min混料15min。進一步地,步驟3)和5)中所述的焙燒方式分為預熱升溫段和恒溫保溫段,兩段焙燒時間比為1:1.8~2.4.進一步地,步驟4)中所述的氣流粉碎設備為流化床氣流粉碎設備或扁平式氣流粉碎設備。進一步地,步驟5)中二次焙燒的后獲得的新塊狀化合物解聚時氣流粉碎進氣強度不得高于0.2MPa,避免對產品顆粒造成二次破壞。本發明方法中鋰鈷摩爾配比采用1:1.04~1:1.1,焙燒時可以保證正極材料一次晶粒生長。本發明方法中焙燒溫度為900℃~1050℃,采用快速升溫工藝,保證正極材料一次晶粒長大。本發明方法步驟4)中的一次粉碎處理采用的粉碎氣壓高于0.5MPa,保證正極材料一次顆粒充分解聚的同時,產生部分小粒度微粉,達到左偏態分布。本發明方法中二次焙燒處理是為降低第一次粉碎增高的表面殘留堿,保證用材料做成的電池安全性能合格。本發明具有以下有益效果:與現有技術相比,本發明制備的一次高放電電壓平臺鋰離子電池正極材料中心粒度為12-18um,粒度分布為左偏態分布,粉體振實密度大于2.7g/cm3,做成全電池加工性能良好,極片壓實密度可達到4.1g/cm3,3.0V~4.2V全電池性能檢測1C放電克容量發揮146mAh/g,1C放電3.6V平臺比率可達到85~90%。附圖說明圖1是實施例1所制得的鋰離子電池正極材料放大500倍后的掃描電鏡圖片;圖2是實施例1所制得的鋰離子電池正極材料使用馬爾文MS2000激光粒度儀器測試的粒度分布結果。具體實施方式實施例1將20kg納米無定形態氫氧化亞鈷和67.9kg中心粒度為16um的電池級四氧化三鈷在100L橄欖型混料罐內混合均勻,以鋰鈷1.05:1的比例添加41.57kg電池級碳酸鋰,同時添加0.085kg納米二氧化鈦和0.17kg納米氧化鎂,在高速混料器內混合均勻。置于空氣氣氛輥道爐內焙燒1040℃,恒溫保溫9h得到正極材料初成品。將初品對輥后經0.5MPa的氣流粉碎通過篩分400目篩網,并與質量比為2%的納米無定形態氫氧化亞鈷在高速混料器內混合均勻。將得到的物料在輥道爐內焙燒1000℃,將得到的塊狀化合物經過對輥0.2MPa的氣流粉碎,篩分400目篩網后得到鋰離子電池正極材料。經測試所制得的鋰離子電池正極材料中心粒度為15.6um,粒度分布呈左偏態分布,比表面積0.223m2/g,振實密度2.91g/cm3。將所制得的鋰離子電池正極材料按質量比與1.8%PVDF和1.5%碳納米管混合使用。先將PVDF溶解于NMP得到固含量8%的膠液,擱置3h后與固含量5%的碳納米管漿料混合并高速分散1.5h,隨后加入本產品捏合攪拌3.5h,再加入NMP至固含量63%左右并分散1h得到穩定漿料。采用相似的方法制得負極漿料。分別將正、負極漿料涂覆在鋁箔和銅箔,經烘干、輥壓、分條等工序制得極片。制成385465-1.5Ah方形全電池,測試電池容量,平臺比率。根據全電池測試結果,采用本實施例所得的高放電電壓平臺鋰離子電池正極材料的電池在4.2V截止電壓下,1C克容量發揮為146.2mAh/g,25℃環境溫度4.2V截止電壓下1C充放電3.6V平臺比例達到88.2%,加工過程中極片極限壓實密度4.41g/cm3。實施例2按照實施例1的過程制備類高放電電壓平臺鋰離子電池正極材料,一次焙燒溫度改為1000℃。其他條件不變。經測試所制得的鋰離子電池正極材料中心粒度為13.2um,粒度分布呈左偏態分布,比表面積0.251m2/g,振實密度2.64g/cm3。根據全電池測試結果,采用本實施例所得的高放電電壓平臺鋰離子電池正極材料的電池在4.2V截止電壓下,1C克容量發揮為144.1mAh/g,25℃環境溫度4.2V截止電壓下1C充放電3.6V平臺比例達到79.2%,加工過程中極片極限壓實密度4.22g/cm3。實施例3按照實施例1的過程制備類高放電電壓平臺鋰離子電池正極材料,將粉碎后的鋰離子電池正極材料和納米氧化亞鈷按照重量比改為1:0.04的比例混合分散均一,其他條件不變。經測試所制得的鋰離子電池正極材料中心粒度為16.2um,粒度分布呈左偏態分布,比表面積0.211m2/g,振實密度2.93g/cm3。根據全電池測試結果,采用本實施例所得的高放電電壓平臺鋰離子電池正極材料的電池在4.2V截止電壓下,1C克容量發揮為146.7mAh/g,25℃環境溫度4.2V截止電壓下1C充放電3.6V平臺比例達到86.2%,加工過程中極片極限壓實密度4.45g/cm3。實施例4按照實施例1的過程制備類高放電電壓平臺鋰離子電池正極材料,將二次焙燒溫度改為900℃,其他條件不變。經測試所制得的鋰離子電池正極材料中心粒度為15.8um,粒度分布呈左偏態分布,比表面積0.235m2/g,振實密度2.88g/cm3。根據全電池測試結果,采用本實施例所得的高放電電壓平臺鋰離子電池正極材料的電池在4.2V截止電壓下,1C克容量發揮為145.7mAh/g,25℃環境溫度4.2V截止電壓下1C充放電3.6V平臺比例達到84.2%,加工過程中極片極限壓實密度4.35g/cm3。對比例1按照實施例1的過程制備類高放電電壓平臺鋰離子電池正極材料,將鋰和金屬化合物摩爾比例改為1:1.08.其他條件不變。經測試所制得的鋰離子電池正極材料中心粒度為18.8um,粒度分布呈左偏態分布,比表面積0.185m2/g,振實密度3.12g/cm3。根據全電池測試結果,采用本實施例所得的高放電電壓平臺鋰離子電池正極材料的電池在4.2V截止電壓下,1C克容量發揮為144.7mAh/g,25℃環境溫度4.2V截止電壓下1C充放電3.6V平臺比例達到82.6%,加工過程中極片極限壓實密度4.64g/cm3。對比例2按照實施例1的過程制備類高放電電壓平臺鋰離子電池正極材料,一次氣流粉碎氣流改為0.2MPa.其他條件不變。經測試所制得的鋰離子電池正極材料中心粒度為17.8um,粒度分布呈左偏態分布,比表面積0.193m2/g,振實密度2.85g/cm3。根據全電池測試結果,采用本實施例所得的高放電電壓平臺鋰離子電池正極材料的電池在4.2V截止電壓下,1C克容量發揮為145.1mAh/g,25℃環境溫度4.2V截止電壓下1C充放電3.6V平臺比例達到76.9%,加工過程中極片極限壓實密度4.29g/cm3。對比例3按照實施例1的過程制備類高放電電壓平臺鋰離子電池正極材料,一次氣流粉碎方式改為機械粉碎,粉碎出的結果為正態分布,其他條件不變。經測試所制得的鋰離子電池正極材料中心粒度為17.5,粒度分布呈正態分布,比表面積0.188m2/g,振實密度2.79g/cm3。根據全電池測試結果,采用本實施例所得的高放電電壓平臺鋰離子電池正極材料的電池在4.2V截止電壓下,1C克容量發揮為144.3mAh/g,25℃環境溫度4.2V截止電壓下1C充放電3.6V平臺比例達到63.1%,加工過程中極片極限壓實密度4.40g/cm3。表1:各鋰離子電池正極材料樣品的物理指標和電化學性能由表1分析可知,按本發明專利方法合成的高放電電壓平臺鋰離子電池正極材料鋰離子全電池容量發揮,3.6V放電平臺表現出良好的特性,比傳統鋰離子電池在4.2V截止電壓下1C倍率的3.6V放電平臺有明顯改善。本發明中混料鋰鈷配比采用富鋰配方一是為了保證有足量的鋰離子嵌入材料,二是為了在焙燒時促進顆粒生長。由對比例7可知,當材料一次顆粒粒度達到16um以上,氣流粉碎左偏態處理的材料擁有較高的碾壓性能,制成的鋰離子電池體積能量密度較高。初始粒度太小不利于材料碾壓性能的提升。由對比例3可知,未呈左偏態分布的材料雖然有較高的碾壓性能,但3.6V放電平臺比率較差,分析原因主要是因為正態分布的材料擁有較少的小粒度,整體比表面較小,電池內部電解液和材料的接觸不夠充分,界面極化嚴重,造成平臺偏低。圖1為實施例1所制得的鋰離子電池正極材料放大500倍后的掃描電鏡圖片,由圖1可知,本實施例所制得的鋰離子電池正極材料有明顯的小顆粒和大顆粒混摻效果。圖2為實施例1所制得的鋰離子電池正極材料使用馬爾文MS2000激光粒度儀器測試的粒度分布結果,由圖2可知,本實施例所制得的鋰離子電池正極材料呈左偏態分布。