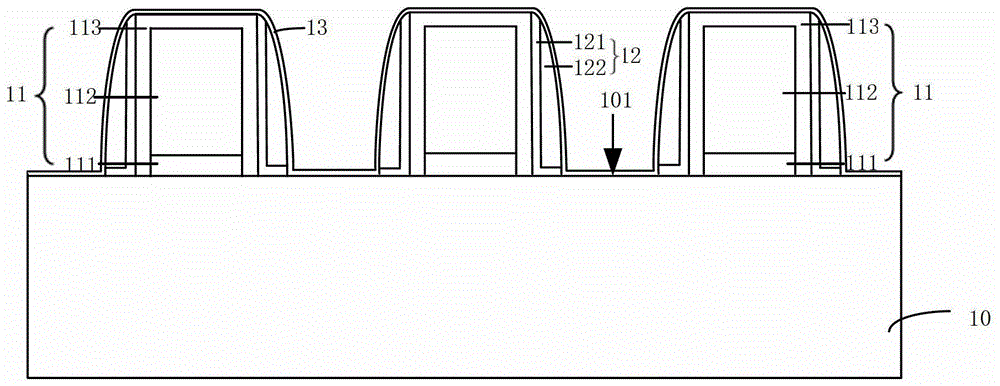
本發明屬于半導體制造領域,特別是涉及一種PMOS晶體管及其制作方法。
背景技術:隨著集成電路集成度的提高,半導體器件的尺寸逐步按比例縮小,在半導體器件尺寸按比例縮小的過程中,漏極電壓并不隨之減小,這就導致源極與漏極之間的溝道區電場增大,在強電場作用下,電子在兩次碰撞之間會加速到比熱運動速度高許多倍的速度,由于電子的動能很大該電子被稱為熱電子,從而引起熱電子效應(hotelectroneffect)。熱電子效應會導致熱電子向柵介質層注入,形成柵電極電流和襯底電流,以致影響半導體器件和電路的可靠性。為了克服熱電子效應,有多種對MOS晶體管結構的改進方法,例如雙注入結構、埋溝結構、分立柵結構、埋漏結構等等,其中研究較多且實用價值較大的一種是輕摻雜漏(LightlyDopedDrain,簡稱LDD)結構。輕摻雜漏結構可以降低電場,并可以顯著改善熱電子效應。除了改進熱電子效應以提高MOS晶體管的性能外,由于應力可以改變硅材質的能隙和載流子遷移率,因此通過應力來提高MOS晶體管的性能成為越來越常用的手段。具體地,通過適當控制應力,可以提高載流子(NMOS晶體管中的電子,PMOS晶體管中的空穴)遷移率,進而提高驅動電流,以此極大地提高MOS晶體管的性能。以PMOS晶體管為例,可以采用嵌入式硅鍺技術(EmbeddedSiGeTechnology)以在晶體管的溝道區域產生壓應力,進而提高載流子遷移率。所謂嵌入式硅鍺技術是指在半導體襯底的需要形成源極及漏極的區域中埋置硅鍺材質,利用硅與硅鍺(SiGe)之間的晶格失配對溝道區域產生壓應力。更多關于嵌入式硅鍺技術的文獻請參照公開號為US7446350B2的美國專利。然而,本發明人在實際使用上述嵌入式技術的PMOS晶體管過程中,發現仍存在載流子的遷移速率過慢的問題。
技術實現要素:本發明要解決的技術問題是改善PMOS晶體管的載流子遷移速率過慢的問題。為解決上述問題,本發明提供一種PMOS晶體管的制作方法,包括:提供硅襯底,在所述硅襯底上形成柵極結構及側墻,所述柵極結構至少包括形成在硅襯底上的柵介質層及所述柵介質層上的柵電極層;在所述柵極結構及側墻上形成保護層,光刻膠殘留物去除溶液對所述保護層的去除速率低于對硅鍺材質的去除速率;在硅襯底中預形成源極及漏極的區域形成sigma形凹槽;在所述sigma形凹槽內填充硅鍺材質,所述硅鍺材質的上表面高于所述硅襯底表面;去除所述側墻,采用光刻膠覆蓋所述硅襯底的其它區域,以在所述側墻暴露的硅襯底區域形成輕摻雜區;采用光刻膠殘留物去除溶液清洗所述硅襯底以形成PMOS晶體管,所述清洗過程中,高于所述硅襯底表面的硅鍺材質被所述保護層保護。可選地,光刻膠殘留物去除溶液包括氨水,雙氧水及水。可選地,所述側墻至少包括氮化硅層或氧化硅層,所述保護層的材質為摻碳氮化硅或摻氧氮化硅。可選地,所述摻碳氮化硅中,碳的原子個數含量為0.5%-5%。可選地,所述保護層的厚度為可選地,所述保護層的形成方法包括:爐管工藝、物理氣相沉積法、化學氣相沉積法或原子層沉積法。可選地,所述側墻至少包括氮化硅層,所述氮化硅層的去除溶液為熱磷酸,熱磷酸對所述保護層的去除速率低于對氮化硅層的去除速率。可選地,熱磷酸的溫度為100℃-180℃。可選地,所述側墻至少包括氧化硅層,所述氧化硅層的去除溶液為氫氟酸,氫氟酸對所述保護層的去除速率低于對氧化硅層的去除速率。可選地,在所述sigma形凹槽內填充硅鍺材質步驟包括:在所述硅鍺材質表面形成帽層,所述帽層的材質為硅。可選地,在所述sigma形凹槽內填充硅鍺材質步驟包括:先形成第一硅鍺材質層,后形成第二硅鍺材質層,所述第二硅鍺材質層的鍺含量高于所述第一硅鍺材質層的鍺含量。可選地,在所述sigma形凹槽內填充硅鍺材質的方法為分子束外延法或化學汽相外延法。可選地,所述硅襯底的其它區域具有半導體器件。可選地,所述柵極結構還包括覆蓋所述柵介質層及所述柵電極層的覆蓋層。此外,本發明還提供了上述制作方法形成的PMOS晶體管。與現有技術相比,本發明具有以下優點:1)為了提高對溝道施加的壓應力,本發明在源/漏區的sigma形凹槽內填入硅鍺材質時,使得硅鍺材質的表面高于硅襯底表面以增加硅鍺材質的填充量;此外,在半導體工藝中,一片晶圓除了制作PMOS晶體管,在其它區域還需形成其它半導體器件,例如NMOS晶體管,因而,在對晶圓進行離子注入形成PMOS晶體管的輕摻雜區時,對其它區域需采用光刻膠覆蓋加以保護,淺結制作完成后,該光刻膠殘留物需進行去除,為防止上述清洗過程對硅鍺材質腐蝕,本發明在硅鍺材質的側面覆蓋保護層,從而提高了載流子的遷移速率。2)可選方案中,光刻膠殘留物去除溶液包括氨水,雙氧水及水,上述混合溶液對硅鍺的腐蝕速率較快,采用去除速率慢于硅鍺的材質作為保護層即可起到提高源/漏區硅鍺材質的填充量,此外,還可以避免硅鍺材質由于腐蝕導致的表面缺陷,降低了漏電流。3)可選方案中,在2)可選方案基礎上,保護層的材質可以為摻碳氮化硅或摻氧氮化硅,為保護層的材質提供了選擇。其中,對于摻碳氮化硅,碳的含量(原子個數)優選為0.5%-5%,摻碳氮化硅易于生長且對于氨水,雙氧水,相對硅鍺的刻蝕選擇比較佳。4)可選方案中,所述側墻的材質至少包括氮化硅層或氧化硅層,對于氮化硅,去除溶液為熱磷酸,此外,優選熱磷酸對所述保護層的去除速率低于對氮化硅層的去除速率,以避免去除側墻過程中腐蝕或過多腐蝕保護層;對于氧化硅,去除溶液為氫氟酸,類似地,優選氫氟酸對所述保護層的去除速率低于對氧化硅層的去除速率,以避免去除側墻過程中腐蝕或過多腐蝕保護層。5)可選方案中,在所述sigma形凹槽內填充硅鍺材質步驟包括:先形成第一硅鍺材質層,后形成第二硅鍺材質層,所述第二硅鍺材質層的鍺含量高于所述第一硅鍺材質層的鍺含量;利用第一硅鍺材質層作為緩沖層,第二硅鍺材料層主要對溝道施加壓應力。6)可選方案中,在所述sigma形凹槽內填充硅鍺材質步驟包括:在所述硅鍺材質表面形成帽層,所述帽層的材質為硅;上述帽層用于形成金屬硅化物,以降低源/漏區的接觸電阻。附圖說明圖1至圖10是本發明實施例的PMOS晶體管在不同制作階段的剖視圖。具體實施方式如前所述,為了提高對溝道施加的壓應力,本發明在源/漏區的sigma形凹槽內填入硅鍺材質時,使得硅鍺材質的表面高于硅襯底表面以增加硅鍺材質的填充量。此外,在半導體工藝中,一片晶圓除了制作PMOS晶體管,在其它區域還需形成其它半導體器件,例如NMOS晶體管,因而,在對晶圓進行離子注入形成PMOS晶體管的輕摻雜區時,對其它區域需采用光刻膠覆蓋加以保護,淺結制作完成后,該光刻膠殘留物需進行去除。為防止上述清洗過程對硅鍺材質腐蝕,本發明在硅鍺材質的側面覆蓋保護層。經驗證,采用本發明的技術方案的PMOS晶體管,載流子的遷移速率及漏電流問題已得到很大程度改善。為使本發明的上述目的、特征和優點能夠更加明顯易懂,下面結合附圖對本發明的具體實施方式做詳細的說明。由于本發明重在解釋原理,因此,未按比例制圖。圖1至圖10是本發明的一個實施例中PMOS晶體管在不同制作階段的剖視圖,下面將結合圖1至圖10對制作方法進行詳細說明。首先執行步驟S1:提供硅襯底,在所述硅襯底上形成柵極結構及側墻,所述柵極結構至少包括形成在硅襯底上的柵介質層及所述柵介質層上的柵電極層。如圖1所示,襯底10為單晶硅襯底,其具有表面101。可在襯底10中形成淺溝槽隔離結構(ShallowTrenchIsolation,簡稱STI)(未圖示),以將襯底10中的有源區域隔離起來。柵極結構11包括形成在硅襯底10上的柵介質層111及形成在柵介質層111上的柵電極層112。柵介質層111的材質可為氧化硅,在一個實施例中,柵介質層111的厚度為其可利用熱氧化法形成。柵電極層112的材質可為多晶硅,在一個實施例中,柵電極層112的厚度為其可利用傳統的高溫爐管(Furnace)工藝形成。在具體實施過程中,由于PMOS晶體管采用硅鍺嵌入技術以對溝道施加壓應力,改善空穴載流子的遷移速率,該嵌入的硅鍺一般采用外延生長工藝形成,為防止該硅鍺在源極與漏極生長同時還在材質為多晶硅的柵電極層112上形成,在柵電極層112上形成覆蓋層113,該覆蓋層113可以選擇現有電絕緣材質,例如氧化硅,氮化硅,氮氧化硅或其中幾種的組合,本實施例中,以氮化硅為例。在一個實施例中,柵極結構11的制作方法包括:在硅襯底10上由下至上依次沉積一層柵介質層(未圖示)及一層柵電極層(未圖示),在所述柵電極層上形成圖形化光刻膠,去除未被圖形化光刻膠覆蓋的所述柵電極層及柵介質層,之后在保留的柵電極層112及柵介質層111上覆蓋一層電絕緣層,形成柵極結構11。仍參照圖1所示,側墻12的材質可以為現有介電材質,例如氮化硅、氮氧化硅、氧化硅等。以氮化硅為例,側墻12的形成可以通過在柵極結構11及硅襯底10上淀積一均等厚度的氮化硅,接著采用回蝕(Etchback),即無掩膜板刻蝕,形成底部大,頂部小的側墻結構(spacer)。本實施例中,所述側墻12包括依次覆蓋在柵極結構11上的氧化硅層121及氮化硅層122。接著執行步驟S2:在所述柵極結構及側墻上形成保護層,光刻膠殘留物去除溶液對所述保護層的去除速率低于對硅鍺材質的去除速率。在半導體工藝中,一片晶圓除了制作PMOS晶體管,在其它區域還需形成其它半導體器件,例如NMOS晶體管,因而,在對晶圓進行離子注入形成PMOS晶體管的輕摻雜區時,對其它區域需采用光刻膠覆蓋加以保護,淺結制作完成后,該光刻膠殘留物需進行去除。光刻膠殘留物去除溶液包括氨水,雙氧水及水,上述混合溶液對硅鍺材質(將在步驟S4中形成)的腐蝕速率較快,本步驟中形成的保護層覆蓋在硅鍺材質上,可以起到減輕上述清洗過程中的去除溶液對硅鍺材質的腐蝕。參照圖2所示,可以理解的是,對于光刻膠殘留物去除溶液,本實施例中為氨水,雙氧水及水的混合溶液,去除速率慢于硅鍺材質的材質都可為作為保護層13的材質,例如摻碳氮化硅或摻氧氮化硅。其中,對于摻碳氮化硅,碳的含量(原子個數)優選為0.5%-5%,摻碳氮化硅易于生長且對于氨水、雙氧水,相對硅鍺的刻蝕選擇比較佳。保護層13根據其材質可以選擇現有的沉積工藝,對于摻碳氮化硅或摻氧氮化硅,可以采用例如爐管工藝、物理氣相沉積法、化學氣相沉積法或原子層沉積法等形成。然后執行步驟S3:在硅襯底中預形成源極及漏極的區域形成sigma形凹槽。在一個實施例中,所述sigma形凹槽15的形成方法包括:如圖3所示,以柵極結構11、側墻12及保護層13為掩膜,在硅襯底10中預形成源極及漏極的區域形成碗狀溝槽14,在一個實施例中,碗狀溝槽14的深度為如圖4所示,將圖3中的碗狀溝槽14暴露在TMAH(TetramethylAmmoniumHydroxied,四甲基氫氧化氨)水溶液中,TMAH水溶液腐蝕硅襯底10,在硅襯底10中預形成源極及漏極的區域形成sigma形凹槽15,在一個實施例中,sigma形凹槽15的深度為在一個實施例中,碗狀溝槽14的形成方法包括:利用各向異性的干法刻蝕在硅襯底10中預形成源極及漏極的區域形成溝槽,所述各向異性的干法刻蝕工藝參數包括:刻蝕氣體包括CF4和HBr,溫度為40℃~60℃,功率為200W~400W,偏壓為50V~200V,時間為10s~20s;然后,利用各向同性的干法刻蝕繼續蝕刻所述溝槽形成碗狀溝槽14,所述各向同性的干法刻蝕工藝參數包括:刻蝕氣體包括Cl2和NF3,溫度為40℃~60℃,功率為100W~500W,偏壓為0V~10V,時間為5s~50s。sigma形凹槽15的形成工藝參數包括:時間為60s~180s,溫度為20℃~60℃,TMAH水溶液的體積百分比濃度為2%~20%。TMAH具有較高的腐蝕速率、無毒無污染、便于操作,且TMAH的晶向選擇性好,其在晶向<100>及<110>方向上的腐蝕速度較快,而在其它晶向方向,如晶向<111>上的腐蝕速率很緩慢,因此,可利用TMAH水溶液在襯底不同晶向上具有不同刻蝕速率的特性,繼續蝕刻碗狀溝槽14以形成sigma形凹槽15。圖5是圖4中sigma形凹槽15的放大圖,如圖5所示,sigma形凹槽15具有第一側壁151、與第一側壁151相連的第二側壁152、第一側壁151與第二側壁152形成的凹槽尖端156、第三側壁153、與第三側壁153相連的第四側壁154、第三側壁153與第四側壁154形成的凹槽尖端156、及底壁155,底壁155與第二側壁152及第四側壁154相連。根據TMAH的腐蝕特性,第一側壁151與硅襯底表面101之間的夾角A1為銳角,且為54.7°,硅襯底表面101與第二側壁152之間的夾角A2為銳角,硅襯底表面101與第三側壁153之間的夾角A3為銳角,且為54.7°,第四側壁154與硅襯底表面101之間的夾角A4為銳角。需說明的是,本發明中硅襯底表面101與sigma形凹槽15側壁之間的夾角及sigma形凹槽15側壁與硅襯底表面101之間的夾角是指沿圖中所示方向的夾角。上述形成碗狀溝槽14的刻蝕過程,尤其是各項異性刻蝕過程中,保護層13進行了部分厚度消耗,一些實施例中,位于側墻12頂部的保護層13已被消耗完。之后執行步驟S4:在所述sigma形凹槽內填充硅鍺材質,所述硅鍺材質的上表面高于所述硅襯底表面。在sigma形凹槽15內填充硅鍺材質的方法有多種,例如分子束外延法或化學汽相外延法。本實施例采用化學汽相外延法生長。此外,考慮到對溝道施加充分的壓應力,在生長終點控制時,如圖6所示,使得硅鍺材質16的表面高于硅襯底10表面以增加硅鍺材質的填充量。在具體實施過程中,硅鍺材質16可以包括第一硅鍺材質層161,第二硅鍺材質層162與第三硅鍺材質層163。以下分別進行介紹。第一硅鍺材質層161的鍺的含量比較低,可以起到防止后續形成鍺含量比較高的硅鍺材質與襯底10中硅的界面引起較大的晶格失配,避免造成后者生長效果較差。可以理解的是,該第一硅鍺材質層161起到了緩沖作用,因而也稱緩沖層。基于此,若采用化學式Si1-xGex表示第一硅鍺材質層161的材質,則x的范圍為5~30%,換言之,緩沖層161的鍺的原子數所占百分比為5~30%。該第二硅鍺材質層162的目的是對凹槽15與襯底10的各邊界施加壓應力,可以理解的是,該第二硅鍺材質層162主要起到了的施加壓應力的作用,因而也稱填充層。基于此,若采用化學式Si1-yGey表示第二硅鍺材質層162的材質,則y的范圍為20~60%,換言之,填充層162的鍺的原子數所占百分比為20~60%;優選地,y的范圍為40~60%,即填充層162的鍺的原子數所占百分比為40~60%。上述步驟完成后,根據源區與漏區的需要,在sigma形凹槽15內填充的硅鍺材質內進行P型離子注入。當然,上述第一硅鍺材質層161與第二硅鍺材質層162也可以邊生長邊進行P型離子摻雜。為了減小該源區與漏區與后續形成在各自之上的金屬互連結構的導電插塞之間的接觸電阻,可以利用金屬硅化工藝在第三硅鍺材質層163形成金屬硅化物,以減小接觸電阻。基于上述目的,該第三硅鍺材料層163也稱帽層,若采用化學式Si1-zGez表示第三硅鍺材料層163的材質,則z的范圍為小于30%,換言之,帽層163的鍺的原子數所占百分比為其內的原子數所占百分比小于30%。本實施例中,上述帽層163為單質硅。之后執行步驟S5:去除所述側墻,采用光刻膠覆蓋所述硅襯底的其它區域,以在所述側墻暴露的硅襯底區域形成輕摻雜區。如圖10所示,本步驟去除所述側墻12(參照圖7所示)的作用是在其下的硅襯底10中形成輕摻雜區17。本實施例中,所述側墻12包括氧化硅層121及氮化硅層122。其去除過程如下:(1)首先,采用熱磷酸去除氮化硅層122,保護層13的材質選擇使得熱磷酸對其具有一定腐蝕性,如圖7所示,先去除保護層13后,再如圖8所示,直至氮化硅層122被去除完,上述過程例如耗費5分鐘至100分鐘;上述過程中,保護層13的材質選擇優選使得熱磷酸對其的去除速率低于對氮化硅層122的去除速率,以避免去除側墻12過程中腐蝕或過多腐蝕保護層13,經實際驗證,摻碳氮化硅或摻氧氮化硅符合上述要求,可以理解的是,符合上述要求的材質不限于摻碳氮化硅或摻氧氮化硅;此外,熱磷酸的溫度為100℃-180℃時,對保護層13與氮化硅層122的選擇比較佳;(2)接著,采用氫氟酸去除氧化硅層121,直至圖9所示氧化硅層121被去除完;上述過程中,保護層13的材質選擇也需優選使得氫氟酸對其的去除速率低于對氧化硅層121的去除速率,以避免去除側墻12過程中腐蝕或過多腐蝕保護層13,經實際驗證,摻碳氮化硅或摻氧氮化硅也符合上述要求,可以理解的是,符合上述要求的材質不限于摻碳氮化硅或摻氧氮化硅。其它實施例中,所述側墻12可以只包括一層氧化硅層121或氮化硅層122,也可以為交替設置的多層,對應地,保護層13的材質可以但不限于為摻碳氮化硅或摻氧氮化硅。如前所述,在半導體工藝中,一片晶圓除了制作PMOS晶體管,在其它區域還需形成其它半導體器件,因而,在對晶圓進行離子注入形成PMOS晶體管的輕摻雜區時,對其它區域需采用光刻膠(未圖示)覆蓋加以保護。本步驟工藝參考現有的光刻工藝。之后,如圖10所示,以圖形化光刻膠為掩膜對硅襯底10進行離子注入,在柵極結構11的兩側、側墻12暴露的硅襯底10區域形成輕摻雜區17(包括輕摻雜源結構與輕摻雜漏結構)。在一個實施例中,注入離子為B(硼),注入離子的劑量為E13/cm2~E15/cm2。可以看出,該柵極結構11中的覆蓋層113在定義輕摻雜區17過程中保護了柵電極層112及柵介質層111。上述先形成源/漏區,后定義輕摻雜區17的方案,可以避免先定義輕摻雜區后刻蝕其形成源/漏區所造成的輕摻雜區的缺陷,降低了漏電流。然后執行步驟S6:采用光刻膠殘留物去除溶液清洗所述硅襯底以形成PMOS晶體管,所述清洗過程中,高于所述硅襯底表面的硅鍺材質被所述保護層保護。如前所述,采用氨水,雙氧水及水的混合溶液去除光刻膠殘留物,由于此時硅鍺材質16高于所述硅襯底表面部分側壁覆蓋有保護層13,氨水,雙氧水及水的混合溶液對保護層13的去除速率慢于對硅鍺材質16的去除速率,因而,可以減緩硅鍺材質16從側面被腐蝕的程度,當然,在保護層13具有一定厚度情況下,例如可以避免硅鍺材質16從側面被腐蝕。可以理解的是,硅鍺材質16表面為單質硅帽層163時,由于氨水,雙氧水及水的混合溶液對硅的腐蝕速率非常小,因而可以避免上述光刻膠殘留物去除溶液從頂部腐蝕硅鍺材質16。經過上述步驟,如圖10所示,形成了一種PMOS晶體管。在采用氨水,雙氧水及水的混合溶液去除光刻膠殘留物時,由于硅鍺材質16高于所述硅襯底表面部分側壁覆蓋有保護層13,因而起到了避免硅鍺材質16側面的腐蝕,提高了硅鍺填充量,增加了對溝道的壓應力,提高了載流子遷移速率,另外,避免硅鍺材質16側面的腐蝕也減少了硅鍺材質16的缺陷,降低了漏電流。本發明雖然已以較佳實施例公開如上,但其并不是用來限定本發明,任何本領域技術人員在不脫離本發明的精神和范圍內,都可以利用上述揭示的方法和技術內容對本發明技術方案做出可能的變動和修改,因此,凡是未脫離本發明技術方案的內容,依據本發明的技術實質對以上實施例所作的任何簡單修改、等同變化及修飾,均屬于本發明技術方案的保護范圍。