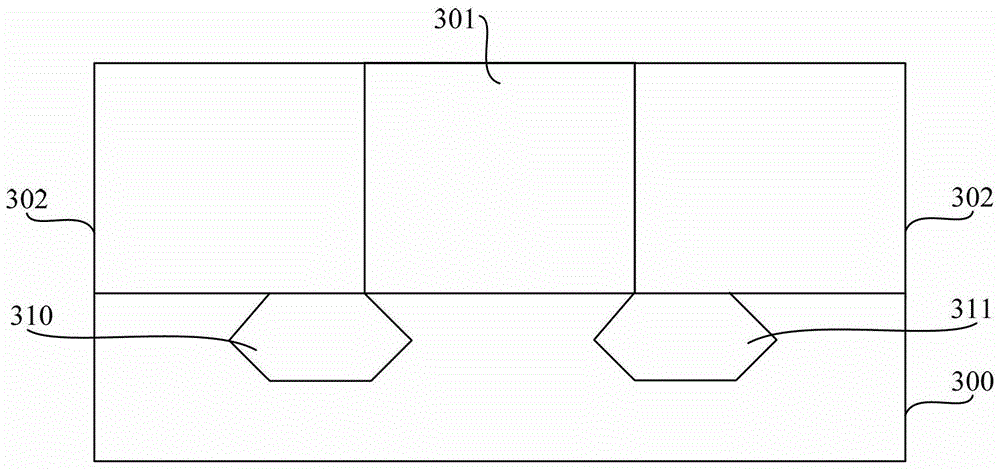
本發明涉及半導體技術領域,尤其涉及一種晶體管的形成方法。
背景技術:隨著半導體技術的不斷發展,MOS晶體管的特征尺寸不斷縮小,MOS晶體管的柵介質層的厚度也按等比例縮小的原則變得越來越薄。當所述柵介質層的厚度薄到一定的程度后,其可靠性問題,尤其是與時間相關的擊穿、熱載流子效應、柵電極中的雜質向襯底的擴散等問題,將嚴重影響器件的穩定性和可靠性。現在,SiO2層作為柵介質層已經達到其物理厚度極限,利用高K柵介質層替代SiO2柵介質層,可以在保持等效氧化層厚度(EOT,EquivalentOxideThickness)不變的情況下大大增加柵介質層的物理厚度,從而減小了柵極漏電流。但是由于高K柵介質層大多是金屬離子氧化物,且沒有固定的原子配位,其與硅襯底之間鍵合的穩定程度較SiO2與硅襯底之間鍵合的穩定程度相比要差得多,造成高K柵介質層與硅襯底之間具有大量的界面缺陷。在現有技術中,一種典型的金屬柵結構包括:界面層(interfaciallayer,IL)、位于界面層上的高K柵介質層、位于高K柵介質層上的金屬柵極。在這種情況下,等效氧化層厚度(EOT)等于等效界面層厚度加等效高K柵介質層厚度。由于界面層的厚度已經達到物理極限,現有技術通過降低高K柵介質層的厚度來降低等效氧化層厚度。降低高K柵介質層的厚度可以提高溝道區中載流子的遷移率,抑制短溝道效應。但隨著半導體工藝技術節點不斷降低,尤其是從32nm技術節點進入22nm,甚至更低,現有技術為獲得較低的等效氧化層厚度而減小高K柵介質層的物理厚度的空間也越來越小,溝道區中載流子的遷移率逐漸降低,柵極漏電流增加。由此,制造的晶體管的性能也降低了。更多關于等效氧化層厚度的知識,請參照2010年9月29日公開的公開號為CN101290880B的中國專利文獻。
技術實現要素:本發明解決的問題是,現有技術為獲得較低的等效氧化層厚度而減小高K柵介質層的物理厚度的空間也越來越小。由此,制造的晶體管的性能也降低了。為解決上述問題,本發明提供一種新的晶體管的形成方法,包括:提供具有偽柵極的半導體襯底,在半導體襯底上形成有層間介質層;去除所述偽柵極,形成第一溝槽;在所述第一溝槽底部形成氧化硅層,作為界面層;形成氧化硅層后,在所述第一溝槽中形成位于所述氧化硅層上的高K柵介質層、位于所述高K柵介質層上的氮化鈦層,填充部分深度的第一溝槽;對所述氮化鈦層進行吸氧物質摻雜;對所述氮化鈦層進行吸氧物質摻雜后,形成多晶硅層,填充第一溝槽;去除所述多晶硅層,形成第二溝槽;在所述第二溝槽中形成導電物質,作為柵極。可選地,對所述氮化鈦層進行吸氧物質摻雜的方法為物理氣相沉積法,其中,在沉積反應腔內的溫度范圍為0℃~500℃。可選地,所述氮化鈦層中的吸氧物質的質量濃度范圍為0.01%~10%。可選地,所述吸氧物質包括銅、鐵、鈷、鋅、錫或錳中的一種或多種。可選地,所述形成多晶硅層的方法為化學氣相沉積法,其中,在沉積反應腔內溫度范圍為400℃~600℃。可選地,所述去除多晶硅層的方法,包括:在所述層間介質層上形成圖形化的掩模層,定義第一溝槽中多晶硅層的位置;以所述圖形化的掩模層為掩模,刻蝕去除第一溝槽中的多晶硅層;去除圖形化的掩模層。可選地,形成高K柵介質層和氮化鈦層的方法,包括:沉積高K介質層、氮化鈦材料層,覆蓋所述層間介質層、填充第一溝槽;去除高出層間介質層的高K介質層、氮化鈦材料層,在所述氧化硅層上形成高K柵介質層和位于高K柵介質層上的氮化鈦層。可選地,去除高出層間介質層的高K介質層、氮化鈦材料層的方法,包括化學機械拋光或回刻工藝。可選地,所述高K介質層的材料包括氧化鉻或氧化鋯。可選地,在所述半導體襯底上形成層間介質層之前,在所述偽柵極兩側的半導體襯底中形成源極和漏極。可選地,所述形成源極和漏極的方法,包括:在所述偽柵極兩側的半導體襯底中形成sigma形凹槽;在所述sigma形凹槽中形成半導體材料;在所述半導體材料中進行離子注入形成源極和漏極。可選地,所述去除偽柵極還包括,去除所述偽柵極下部分深度的半導體襯底,形成第一溝槽的底部處于sigma形凹槽的尖角與半導體襯底表面之間。可選地,若晶體管為P型晶體管,所述半導體材料為鍺硅;若晶體管為N型晶體管,所述半導體材料為碳硅。可選地,形成所述氧化硅層的方法,包括熱氧化生長法或化學氣相沉積。可選地,去除所述偽柵極的方法,包括:在層間介質層上形成圖形化的光刻膠層,定義所述偽柵極的位置;以所述圖形化的光刻膠層為掩模,干法刻蝕去除所述偽柵極,形成第一溝槽;去除圖形化的光刻膠層;使用濕法腐蝕去除所述干法刻蝕中在第一溝槽側壁和底部產生的聚合物。與現有技術相比,本發明具有以下優點:本發明在半導體襯底上形成偽柵極和覆蓋襯底的層間介質層后,去掉偽柵極,形成第一溝槽;之后,在所述第一溝槽中形成占第一溝槽部分深度的氧化硅層、位于氧化硅層上的高K柵介質層和位于高K柵介質層上的氮化鈦層;接著,對氮化鈦層進行吸氧物質摻雜;緊接著,在第一溝槽的氮化鈦層上形成多晶硅層。在形成多晶硅層過程中,多晶硅層用于阻擋外界環境的氧與氮化鈦層中的吸氧物質發生氧化反應,并且,在形成多晶硅層的過程中,高K柵介質層中出現快速移動的氧空穴,氧化硅層中的氧原子進入高K柵介質層,并隨氧空穴在高K柵介質層中移動。在到達高K柵介質與氮化鈦層的界面處,大部分氧原子受到吸氧物質層的“吸引”而進入到氮化鈦層,氧原子與吸氧物質反應,通過化學鍵結合生成穩定物質。而與此同時,氧化硅層中的氧損失,其中的硅又會與襯底重新結合而成為襯底的一部分。氧化硅層中的氧損失,使得氧化硅層的厚度減小,進而使得等效氧化層厚度減。與現有技術的高K柵介質層技術相比,本發明的等效氧化層厚度降到0.5nm以下,最終穩定并提升了溝道區中載流子的遷移率,抑制漏電流的產生。附圖說明圖1是本發明具體實施例的晶體管形成方法的流程示意圖;圖2~圖8是本發明具體實施例的晶體管形成方法的剖面結構示意圖。具體實施方式為使本發明的上述目的、特征和優點能夠更加明顯易懂,下面結合附圖對本發明的具體實施方式做詳細的說明。在下面的描述中闡述了很多具體細節以便于充分理解本發明,但是本發明還可以采用其他不同于在此描述的其它方式來實施,因此本發明不受下面公開的具體實施例的限制。參照圖2,并結合參照圖1,執行步驟S11,提供具有偽柵極301的半導體襯底300,在半導體襯底300上形成有層間介質層302。在具體實施例中,半導體襯底300的材料可以包括單晶、多晶或非晶結構的硅或硅鍺(SiGe),也可以包括混合的半導體結構,例如碳化硅(SiC)、銻化銦、碲化鉛、砷化銦、磷化銦、砷化鎵或銻化鎵、合金半導體或其組合;也可以是絕緣體上硅(SOI)或其他材料,在此不再一一列舉。在具體實施例中,所述偽柵極301的材料可以選擇多晶硅、無定形碳或氮化硅。形成所述偽柵極301的方法,包括:在半導體襯底300上形成刻蝕阻擋層(未示出),所述刻蝕阻擋層通常選擇氧化硅,在后續刻蝕偽柵極層過程中起到刻蝕阻擋作用;沉積形成覆蓋刻蝕阻擋層的偽柵極層;圖形化所述偽柵極層,形成偽柵極301。其中,圖形化所述偽柵極層的方法,可以為:在偽柵極層上形成硬掩模材料;圖形化所述硬掩模材料,在待形成的偽柵極位置形成硬掩模層;以硬掩模層為掩模,刻蝕偽柵極層,至刻蝕阻擋層停止,剩余硬掩模層下的偽柵極層為偽柵極301。硬掩模層可以選擇去除,也可以保留,在后續工藝中起到掩模作用。此為本領域技術人員所熟知的技術,在此不再贅述。在具體實施例中,在襯底300上形成層間介質層302的方法,包括:化學氣相沉積,形成覆蓋半導體襯底300、偽柵極301的介質層;化學機械拋光或回刻工藝或其他可選工藝,去除高出偽柵極301表面的介質層,形成層間介質層302。若在其他實施例中,在偽柵極301上還形成有硬掩模層,則去除高出硬掩模層表面的介質層,形成層間介質層。層間介質層的材料通常選擇氧化硅。在具體實施例中,在形成層間介質層302之前,還要在偽柵極301兩側的半導體襯底300中進行離子注入,形成源極310和漏極311。在本實施例中,形成源極和漏極的方法引入嵌入式鍺硅技術,包括:在半導體襯底300兩側的半導體襯底中形成sigma形凹槽;在sigma形凹槽中形成半導體材料;在所述半導體材料中進行離子注入形成源極310和漏極311。在具體實施例中,當晶體管為P型晶體管,半導體材料為鍺硅,鍺硅為溝道區提供壓應力;當晶體管為N型晶體管,半導體材料為碳硅,碳硅為溝道區提供張應力。嵌入式鍺硅技術的應用,可以明顯提高溝道區中載流子的遷移率,提升晶體管的性能。參照圖2和圖3,并結合參照圖1,執行步驟S12,去除偽柵極301,形成第一溝槽303。在具體實施例中,去除偽柵極301的方法,包括:在層間介質層302上形成圖形化的光刻膠層,定義偽柵極301的位置;以圖形化的光刻膠層為掩模,干法刻蝕去除偽柵極301,形成第一溝槽303,在該過程產生聚合物,該聚合物附著在第一溝槽303底部和側壁;接著,去除圖形化的光刻膠層;使用濕法腐蝕去除干法刻蝕中產生的聚合物。當本發明引入嵌入式鍺硅技術,可選的,執行步驟S12去除偽柵極301中,還可以繼續去除偽柵極301下的半導體襯底300,使得第一溝槽303的底部處于sigma形凹槽的尖角與半導體襯底300表面之間,大約地,第一溝槽303底部位于半導體襯底300表面下小于等于100nm處。由于靠近Sigma形凹槽的尖角處的半導體材料能夠提供較大的應力,將第一溝槽303的底部處于sigma形凹槽的尖角與半導體襯底300表面之間,相對地將溝道區與柵介質層的界面下移,溝道區下移,溝道區受到較大應力作用,溝道區中載流子的遷移率得到提高,進一步提升晶體管的性能。參照圖4,并結合參照圖1,執行步驟S13,在第一溝槽303底部形成氧化硅層304,作為界面層(interfaciallayer,IL)。該界面層不僅能在襯底和界面層之間提供較佳品質的界面,還能在高K柵介質層和界面層之間提供較佳品質的界面,從而改善后續高K柵介質層與襯底之間的界面特性,進而提高晶體管的電學性能。在具體實施例中,在第一溝槽303底部形成氧化硅層304的方法包括熱氧化生長法或化學氣相沉積。熱氧化生長法為公知的技術,不再贅述。若使用化學氣相沉積,形成覆蓋層間介質層302、填充第一溝槽303的介質層,之后,去除高出層間介質層302的介質層,在第一溝槽303底部和側壁形成氧化硅層,作為界面層。參照圖5,并結合參照圖1,執行步驟S14,形成氧化硅層304后,在第一溝槽303中形成位于氧化硅層304上的高K柵介質層305、位于高K柵介質層305上的氮化鈦層306,填充部分深度的第一溝槽303。高K柵介質層305除了覆蓋氧化硅層304外,還覆蓋第一溝槽303的側壁。當然的,氮化鈦層306也形成在第一溝槽303側壁的高K柵介質層上。在本步驟,氧化硅層304、高K柵介質層305和氮化鈦層306組成的疊層結構,并未填充滿第一溝槽303。在具體實施例中,形成高K柵介質層305、氮化鈦層306的方法,包括:沉積高K介質層、氮化鈦材料層,覆蓋層間介質層302、填充第一溝槽303;去除高出層間介質層302的高K介質層、氮化鈦材料層,在氧化硅層304上形成高K柵介質層305和位于高K柵介質層305上的氮化鈦層306。其中,在第一溝槽303側壁上也形成有高K柵介質層和位于高K柵介質層上的氮化鈦層。在具體實施例中,去除方法可選擇化學機械拋光(CVD)或回刻工藝。在具體實施例中,高K柵介質層305的材料選擇氧化鉻或氧化鋯。一方面,氮化鈦層306可以阻擋氧化硅層304中的氧經高K柵介質層擴散至柵極,也阻止柵極中的元素向高K柵介質層擴散。另一方面,在本發明中,氮化鈦層306是“接收”氧化硅層304中氧的“容器”,這會在后續步驟中說明。繼續參照5,并結合參照圖1,執行步驟S15,對氮化鈦層306進行吸氧物質摻雜。在本實施例中,在同一條件下,吸氧物質與氧結合的能力大于硅與氧結合的能力,這樣,在后續步驟中,氧化硅層304中的氧就會被“吸引”至氮化鈦層306中而與吸氧物質結合。在具體實施例中,對氮化鈦層306進行吸氧物質摻雜的方法,可以選擇物理氣相沉積(PVD)法,例如濺射法、離子鍍等。首先,在層間介質層302上形成圖形化的掩模層,定義氮化鈦層306的位置;以圖形化的掩模層為掩模,對氮化鈦層306進行物理氣相沉積,形成吸氧物質摻雜,在該過程中,沉積反應腔內的溫度范圍為0℃~500℃,可以保證吸氧物質可以對氮化鈦層306形成摻雜。最終,在氮化鈦層306中的吸氧物質的質量濃度范圍為0.01%~10%。由于未進行摻雜的氮化鈦層306不具備“吸引”氧而與氧結合的能力,而吸氧物質可以在后續沉積多晶硅過程中的高溫條件下與氧結合。氮化鈦層306充當了吸氧物質與氧結合的媒介作用。在本實施例中,吸氧物質為金屬,包括銅、鐵、鈷、鋅、錫或錳中的一種或多種。參照圖5和圖6,并結合參照圖1,執行步驟S16,對氮化鈦層306進行吸氧物質摻雜后,形成多晶硅層307,填充第一溝槽303。在具體實施例中,形成多晶硅層307的方法,使用化學氣相沉積,其中,在沉積反應腔內提供的溫度范圍為400℃~600℃。使用化學氣相沉積,形成的多晶硅層307不僅填充第一溝槽303,也覆蓋層間介質層302。在沉積多晶硅層過程中,多晶硅層307用于阻擋外界環境中的氧與氮化鈦層306中的吸氧物質發生氧化反應。在400℃~600℃的較高溫度下,氧化硅層304中的氧與硅分離,擴散進入高K柵介質層305。在較高溫度下,高K柵介質層中出現快速移動的氧空穴,氧化硅層304中的氧原子進入高K柵介質層,并隨氧空穴在高K柵介質層中移動。在到達高K柵介質層305與氮化鈦層306的界面處,大部分氧原子受到吸氧物質層的“吸引”而進入到氮化鈦層306中,氧原子與吸氧物質反應,通過化學鍵結合生成穩定物質。而與此同時,氧化硅層304中的氧損失,其中的硅又會與襯底300重新結合而成為襯底300的一部分。氧化硅層304中的氧損失,使得氧化硅層304的厚度減小,進而使得等效氧化層厚度減。與現有技術的高K柵介質層技術相比,本發明的等效氧化層厚度降到0.5nm以下,最終穩定并提升了溝道區中載流子的遷移率,抑制漏電流的產生。在本實施例中,對沉積多晶硅層溫度范圍限制在400℃~600℃,一方面是沉積形成多晶硅層的要求。另一方面,在400℃~600℃下,氧化硅層304中的氧易分離,高K柵介質層305中的氧空穴可以形成穩定的移動,氧化硅層304中分離的氧在高K柵介質層305中也形成穩定移動擴散。而且,該溫度范圍提供了足夠的能量促使氧與吸氧物質發生反應,并抑制了氧與氧化硅層304中的硅的結合重生成氧化硅。若溫度高于600℃,也不會對氧空穴、氧的移動產生更積極的效果,反而會影響多晶硅層307的沉積形成。繼續參照圖6和圖7,并結合參照圖1,執行步驟S17,去除多晶硅層307,形成第二溝槽308。在具體實施例中,由于使用化學氣相沉積,多晶硅層303也覆蓋層間介質層302。所以,去除多晶硅層307的步驟:首先,去除高出層間介質層302的多晶硅層部分,可以使用化學機械拋光或回刻工藝;然后,在層間介質層302上形成圖形化的掩模層,可以選擇光刻膠,定義第一溝槽中多晶硅層的位置;以圖形化的掩模層為掩模,刻蝕去除第一溝槽中的多晶硅層;去除圖形化的掩模層。參照圖7和圖8,并結合參照圖1,執行步驟S18,在形成第二溝槽308后,在第二溝槽308中形成導電物質309,作為柵極。其中,導電物質309的材料可以為金屬,包括Al、Cu、Ag、Au、Pt、Ni、Ti、TiN、TaN、Ta、TaC、TaSiN、W、WN、WSi的一種或多種。除了金屬外,還可包括其他可行材料。本發明雖然已以較佳實施例公開如上,但其并不是用來限定本發明,任何本領域技術人員在不脫離本發明的精神和范圍內,都可以利用上述揭示的方法和技術內容對本發明技術方案做出可能的變動和修改,因此,凡是未脫離本發明技術方案的內容,依據本發明的技術實質對以上實施例所作的任何簡單修改、等同變化及修飾,均屬于本發明技術方案的保護范圍。