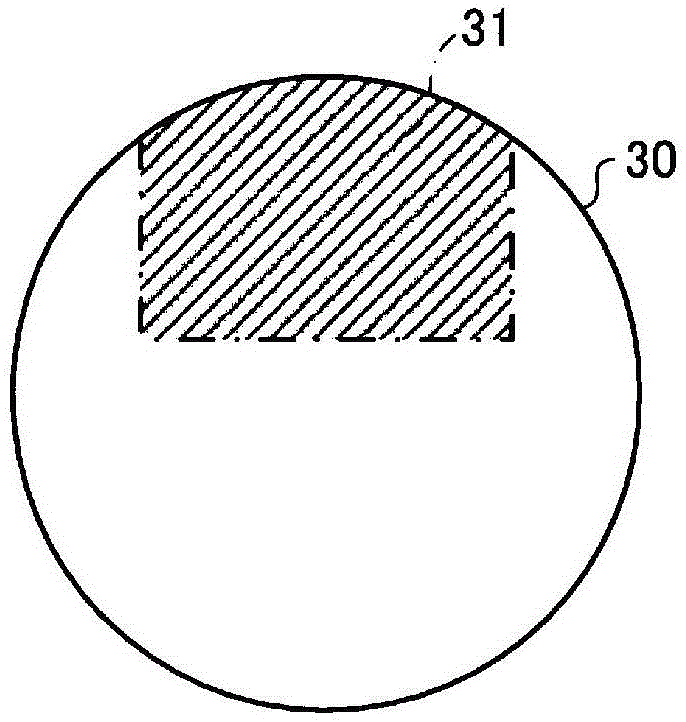
本發明涉及半導體器件的制造方法。
背景技術:即使當施加反向電壓時,反向阻斷IGBT(RB-IGBT:反向阻斷絕緣柵雙極晶體管)也必需確保與正向阻斷性能相等的反向阻斷性能以保證擊穿電壓。為了確保反向阻斷性能,在反向阻斷IGBT中通過擴散層(在下文中稱為分離層)來形成pn結,該擴散層在與主表面垂直的方向上穿過半導體芯片并且使半導體芯片的側面與漂移層分離。反向阻斷半導體器件的反向擊穿電壓由pn結維持。接著,將描述反向阻斷IGBT的制造(制備)方法(在下文中稱為第一制造方法)。圖8至12是示出根據現有技術制成的反向阻斷IGBT的截面圖,并且示出擴散來自雜質源(液體擴散源)的施加到半導體晶片上的摻雜劑以形成分離層的方法(施加和擴散方法)。首先,如圖8所示,通過熱氧化方法使用摻雜劑掩模在n型半導體晶片1的正面形成厚度為例如約2.5μm的氧化膜2。接著,如圖9所示,通過光刻選擇性地去除氧化膜2以形成開口3,從而形成分離層。接著,如圖10所示,將硼(B)源4施加到氧化膜2上,以使硼源4設置在開口3中。接著,將半導體晶片1插入擴散爐,并且在高溫(例如,1300°C)下長時間(例如,100小時)地執行熱擴散工藝。通過熱擴散工藝將硼源4的硼從氧化膜2的開口3擴散到半導體晶片1中以形成p型擴散層,該p型擴散層是半導體晶片1的正面的表面層中的厚度為例如約數百微米的分離層5。接著,如圖11所示,去除硼源4和氧化膜2,并且在半導體晶片1的正面形成反向阻斷IGBT的正面元件結構(未示出)。接著,半導體晶片1的背面接地,直至露出分離層5以使半導體晶片1減薄。接著,如圖12所示,在半導體晶片1的接地背面形成包括p+集電極區6和集電電極的背面元件結構。接著,沿著在分離層5的中心形成的切割線將半導體晶片1切割成切割芯片。以此方式,完成在該芯片的側面具有分離層5的反向阻斷IGBT。接著,將描述反向阻斷IGBT的另一種制造方法(在下文中稱為第二制造方法)。圖13至16是示出根據現有技術制成的反向阻斷IGBT的另一示例的截面圖,并且示出將雜質離子注入半導體晶片且使其擴散以形成分離層的方法。首先,如圖13所示,通過熱氧化方法使用摻雜劑掩模在n型半導體晶片11的正面形成厚度為例如約1μm的氧化膜12。接著,如圖14所示,通過光刻選擇性地去除氧化膜12以形成開口13,從而形成分離層。接著,如圖15所示,使用氧化膜12作為掩模將硼離子14注入半導體晶片11。所注入的離子14的劑量可以是例如約1×105cm-2。接著,如圖16所示,將半導體晶片11插入擴散爐,并且在高溫(例如,1300°C)下長時間(例如,100小時)地執行熱擴散工藝。通過熱擴散工藝擴散注入半導體晶片11的硼以形成p型擴散層,該p型擴散層是半導體晶片11的正面的表面層中的厚度為例如約數百微米的分離層15。接著,去除用于離子注入的氧化膜12,并且在半導體晶片11的正面形成反向阻斷IGBT的正面元件結構(未示出)。接著,與以上所述的第一制造方法類似,半導體晶片11的背面接地,直至露出分離層15(參見圖11)。接著,如圖12所示,與第一制造方法類似,在半導體晶片11(在圖12中由附圖標記1表示)的接地背面形成p+集電極區6和集電電極,并且沿著切割線(未示出)切割半導體晶片11。以此方式,完成在該芯片的側面具有分離層15(在圖12中由附圖標記5表示)的反向阻斷IGBT。近年來,已提出了使用蝕刻在半導體晶片中形成凹槽且在該凹槽的側壁上形成分離層、由此制造反向阻斷IGBT的方法。另外,已提出了以下方法。其中形成有構成半導體芯片的正面結構和背面結構的薄半導體晶片通過雙面膠帶附連到支承基板。通過各向異性濕法蝕刻在薄半導體晶片中形成用作劃線的溝槽,從而露出晶面。通過離子注入以及低溫退火或激光退火在溝槽的側面形成用于維持反向擊穿電壓的分離層,從而使其與作為背面擴散層的p集電極區接觸且延伸到正面側。接著,在不過度或不欠缺的情況下進行激光切割以清晰地切割分離層下方的集電電極。接著,從集電電極剝離雙面膠帶以獲取半導體芯片。以此方式,形成反向阻斷半導體器件(例如,參見以下專利文獻1)。此外,已提出了以下方法作為反向阻斷IGBT的另一種制造方法。其中形成有構成半導體芯片的正面結構的薄半導體晶片的正面通過雙面膠帶附連到支承基板。通過各向異性濕法蝕刻在薄半導體晶片的背面形成用作劃線的溝槽,從而露出晶面。通過離子注入以及低溫退火或激光退火在溝槽的露出晶面的側面形成用于維持反向擊穿電壓的分離層,該分離層與作為背面擴散層的p集電極區同時形成。接著,從集電電極剝離雙面膠帶以獲取半導體芯片。以此方式,形成反向阻斷半導體器件(例如,參見以下專利文獻2)。已提出了一種如下方法作為反向阻斷IGBT的另一種制造方法,該方法包括:在第一導電型晶片的第一主表面中形成第二導電型的第一半導體區的第一半導體區形成步驟;在晶片的第一主表面上形成正面元件結構的正面元件結構形成步驟;形成從晶片的第二主表面延伸至第一半導體區的凹部的凹部形成步驟;在晶片的第二主表面中形成第二導電型的第二半導體區以使其電連接到第一半導體區的第二半導體區形成步驟;以及去除第一半導體區的一部分且將晶片切割成芯片的切割步驟。在切割步驟中,去除第一半導體區以使第一半導體區的切割面相對于晶片的第一主表面傾斜(例如,參見以下專利文獻3)。圖17所示的反向阻斷IGBT通過在以下專利文獻1至專利文獻3中公開的技術制成。圖17是示出根據現有技術的反向阻斷IGBT的結構的截面圖。如圖17所示,通過蝕刻以凹槽形狀去除包含切割線的半導體晶片的區域,由此形成半導體芯片21的側面22,從而形成反向阻斷IGBT。形成例如擊穿電壓結構的p+區23設置在半導體芯片21的側面22的正面側表面層中。p+集電極區24在半導體芯片21的背面形成。p+分離層25設置在半導體芯片21的側面22上,并且使設置在半導體芯片21的正面的p+區23與設置在半導體芯片21的背面的p+集電極區24相連。與在分離層通過上述第一和第二制造方法形成時類似地,當p+分離層25通過在以下專利文獻1至專利文獻3中公開的技術來形成時,在許多情況下,在高溫下長時間地執行熱擴散工藝以形成p+分離層25。此外,已提出了一種如下方法作為用于形成分離層的方法,該方法包括:在雜質氣氛中對晶面取向(111)或(100)的晶片表面進行沉積的第一擴散步驟,該晶片從具有晶軸<111>或<100>的單晶硅錠切割一預定厚度且其兩面同時加有研磨劑以具有均勻的處理應變;以及第二擴散步驟,其中在包含0.5至10(vol)%的O2氣體以及Ar或He的混合氣體氣氛中在1250°C至1310°C的溫度下對經過第一擴散步驟的晶片進行處理達20至450小時、從而在晶片的中心形成不擴散雜質的一個層以及在晶片的兩面形成擴散有雜質的多個層(例如,參見以下專利文獻4)。已提出了一種如下的半導體硅晶片制造方法作為用于形成分離層的另一種方法,該半導體硅晶片制造方法包括:在經研磨硅半導體晶片的兩面淺沉積N雜質的第一擴散步驟;以及在高溫下長時間地對晶片進行熱處理以在晶片的表面中獲取必要的擴散深度和濃度的第二擴散步驟。在第一擴散步驟中,晶片中的N雜質的擴散源是氯氧化磷中的磷,氯氧化磷蒸氣與包含0.5%或更多的O2氣體的Ar氣體一起連續地供應,溫度維持在1100°C至1300°C的范圍內,并且進行擴散達一預定時間,從而在第二擴散步驟之后獲取目標擴散深度和目標晶片表面濃度(例如,參見以下專利文獻5)。已提出了一種如下方法作為用于形成分離層而無需在高溫下長時間地執行熱擴散工藝的方法,該方法在半導體晶片的正面使用蝕刻來形成溝槽,在溝槽的底部和側壁上形成用作分離層的擴散層,并且將分離層保留在溝槽的側壁上作為分離層(在下文中稱為第三制造方法)。引用列表專利文獻專利文獻1:US7741192專利文獻2:JP2006-303410A專利文獻3:JP2011-181770A專利文獻4:JP2607853B1專利文獻5:JP2975912B1
技術實現要素:本發明要解決的問題然而,在第三制造方法中,為了形成分離層不在高溫下長時間地執行熱擴散工藝,但是形成溝槽以形成分離層花費了長時間。當通過典型的干法蝕刻裝置來形成深度約為200μm的溝槽時,每一半導體晶片形成溝槽所需的時間約為100分鐘。因此,交付周期增加,或者維持蝕刻裝置的次數增加。如在以上所述的專利文獻1至專利文獻5中公開的技術中,在高溫下長時間地執行熱擴散工藝以形成分離層時,在熱擴散工藝期間,由于形成半導體晶片的成分或者包括在氣氛中的成分,在半導體晶片中發生晶體缺陷。這導致半導體元件的成品率降低。鑒于上述問題已作出了本發明,并且本發明的目的在于,提供一種具有高成品率的半導體器件的制造方法。用于解決問題的手段為了解決以上問題且實現本發明的目的,根據本發明的一方面,提供了一種半導體器件的制造方法,該制造方法包括:在惰性氣體氣氛中在高于或等于1290°C且低于硅的熔點的溫度下對使用通過切克勞斯基法制成的單晶硅錠作為原材料且以作為浮動法制成的硅晶片、或者使用多晶硅錠作為原材料且以浮動法制成的硅晶片進行熱處理。在根據本發明的上述方面的半導體器件的制造方法中,惰性氣體氣氛可以是包含氬氣作為主要成分的氣體氣氛。在根據本發明的上述方面的半導體器件的制造方法中,可在高于或等于1300°C且低于或等于1350°C的溫度下進行熱處理。在根據本發明的上述方面的半導體器件的制造方法中,可使用使用多晶硅錠作為原材料且以作為浮動法制成的硅晶片,惰性氣體氣氛可以是氮氣氣氛,并且可在高于或等于1290°C且低于硅的熔點的溫度下進行熱處理。熱處理可在高于或等于1290°C且低于或等于1350°C的溫度下進行。根據本發明的上述方面,可在高溫下長時間地進行熱處理,從而在通過FZ法制成的硅晶片中不發生晶體缺陷。因此,可在硅晶片中沒有任何晶體缺陷的情況下,使用在高溫下長時間進行的熱處理來制造半導體器件。以此方式,可防止反向擊穿電壓缺陷或正向缺陷在反向阻斷IGBT中發生。為了解決上述問題且實現本發明的目的,根據本發明的另一方面,提供了一種半導體器件的制造方法,該制造方法包括:在氮氣氣氛中在高于或等于1290°C且低于硅的熔點的溫度下對使用通過切克勞斯基法制成的單晶硅錠作為原材料且以浮動法制成的硅晶片進行熱處理的熱處理步驟;以及研磨硅晶片的一個主表面直至去除掉包含由于熱處理步驟而在硅晶片中發生的晶體缺陷的區域的研磨步驟。根據本發明的上述方面,在氮氣氣氛中,在高溫下長時間地對通過FZ法制成的硅晶片進行熱處理。因此,即使當晶體缺陷發生時,也有可能制造半導體器件以使不包括在硅晶片中發生的晶體缺陷。以此方式,可防止反向擊穿電壓缺陷或正向缺陷在反向阻斷IGBT中發生。根據本發明的上述方面的半導體器件的制造方法還可包括:使用熱處理將第二導電型擴散層從硅晶片的一個主表面擴散到另一主表面的擴散步驟,該第二導電型擴散層與作為反向阻斷絕緣柵雙極晶體管的第一導電型漂移層的硅晶片形成pn結。在該擴散步驟中,第二導電型擴散層可擴散以到達在擴散步驟之前或之后在硅晶片的另一主表面中形成的第二導電型集電極區。根據本發明的上述方面,可使用使用多晶硅錠作為原材料且以作為浮動法制成的硅晶片、或者使用通過切克勞斯基法制成的單晶硅錠作為原材料且以浮動法制成且具有與使用多晶硅錠作為原材料且以浮動法制成的硅晶片相同的質量特性的硅晶片來制造半導體器件。另外,根據本發明的上述方面,可使用使用通過切克勞斯基法制成的單晶硅錠作為原材料且以浮動法制成、且作為通過切克勞斯基法制造的單晶硅錠的特征的其直徑可容易地增加的硅晶片來制造半導體器件。本發明的有益效果根據本發明的半導體器件的制造方法,可改進成品率。附圖說明圖1是示出其中捕捉到半導體晶片的X射線形貌圖像的位置的平面圖。圖2是示意性地示出在氮氣氣氛中經受熱處理的半導體晶片的X射線形貌圖像的平面圖。圖3是示出根據第一實施例的半導體器件的反向擊穿電壓特性的特性圖。圖4是示出在半導體器件中發生晶體缺陷的狀況的截面圖。圖5是示出根據第四實施例的正在制造的半導體器件的截面圖。圖6是示出根據第四實施例的正在制造的半導體器件的截面圖。圖7是示出根據第四實施例的正在制造的半導體器件的截面圖。圖8是示出根據現有技術的正在制造的反向阻斷IGBT的截面圖。圖9是示出根據現有技術的正在制造的反向阻斷IGBT的截面圖。圖10是示出根據現有技術的正在制造的反向阻斷IGBT的截面圖。圖11是示出根據現有技術的正在制造的反向阻斷IGBT的截面圖。圖12是示出根據現有技術的正在制造的反向阻斷IGBT的截面圖。圖13是示出根據現有技術的正在制造的反向阻斷IGBT的另一示例的截面圖。圖14是示出根據現有技術的正在制造的反向阻斷IGBT的另一示例的截面圖。圖15是示出根據現有技術的正在制造的反向阻斷IGBT的另一示例的截面圖。圖16是示出根據現有技術的正在制造的反向阻斷IGBT的另一示例的截面圖。圖17是示出根據現有技術的反向阻斷IGBT的結構的截面圖。具體實施方式在下文中,將參考附圖詳細描述根據本發明的示例性實施例的半導體器件的制造方法。在說明書和附圖中,在附加有“n”或“p”的層和區域中,電子和空穴是多數載流子。另外,添加到n或p的符號“+”和“-”是指雜質濃度比沒有這些符號的層或者區域的濃度高和低。在以下實施例和附圖的描述中,相同的組件由相同的附圖標記表示,并且其描述將不再重復。(第一實施例)根據第一實施例的半導體器件使用從單晶硅錠(在下文中稱為FZ錠)切割(切掉)的半導體晶片(在下文中稱為從通過切克勞斯基(CZ)法制成的晶棒獲取的FZ晶片)制成,該單晶硅錠使用通過CZ法制成的單晶硅錠(在下文中稱為CZ錠)作為原材料且以浮動(FZ)法制成。例如,從通過CZ法制成的晶棒獲取的FZ晶片如下地制造。首先,使用粗略壓碎的多晶硅作為原材料制成的CZ錠的一端與籽晶接觸。接著,高頻電壓被施加到線圈以對CZ錠加熱且使其熔化成帶狀,并且熔化的帶狀部移動到籽晶以制成FZ錠。接著,切割FZ錠。以此方式,完成從通過CZ法制成的晶棒獲取的FZ晶片。在根據第一實施例的半導體器件...