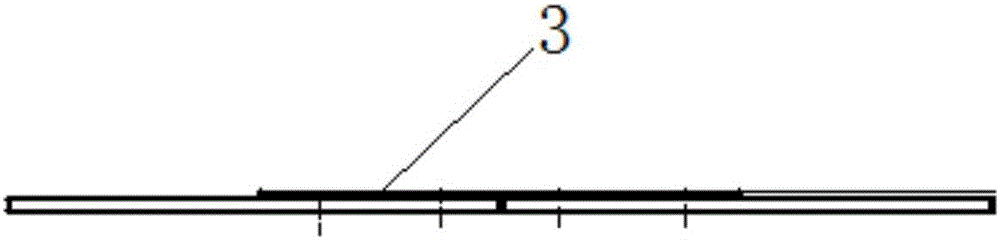
本發明涉及航空制造
技術領域:
,特別是涉及一種腐蝕試驗方法,用于試驗飛機內部封閉結構表面防護體系抗腐蝕防護能力。
背景技術:
:飛機結構腐蝕防護體系抗腐蝕效果驗證一般可采用自然腐蝕試驗和加速腐蝕試驗。自然腐蝕試驗接近實際服役環境,其驗證結果具有真實、可靠等優點,但是自然腐蝕試驗所需周期較長,根據所驗證內容的不同,一般需8~10年。而加速腐蝕試驗,目前主要參考GJB150進行單一環境模塊作用下的加速腐蝕試驗,做出的試驗結果僅能反映該結構腐蝕防護體系在單一的環境加速作用下的抗腐蝕性能,而針對多個環境共同影響的如鹽霧、濕熱、紫外照射等共同作用后的抗腐蝕情況難以驗證。有些飛機服役環境惡劣,是受多種不同環境因素共同作用的,采用單一的加速腐蝕試驗方法無法實際反映飛機的額腐蝕情況,使數據失真。因此,希望有一種技術方案來克服或至少減輕現有技術的至少一個上述缺陷。技術實現要素:本發明的目的在于提供一種腐蝕試驗方法來克服或至少減輕現有技術的中的至少一個上述缺陷。為實現上述目的,本發明提供一種腐蝕試驗方法,用于試驗飛機內部封閉結構表面防護體系抗腐蝕防護能力,所述腐蝕試驗方法包括如下步驟:步驟1:為飛機內部封閉結構表面進行溶液浸泡試驗;步驟2:為飛機內部封閉結構表面進行常溫疲勞試驗;步驟3:重復所述步驟1至步驟2。優選地,所述溶液浸泡試驗的條件為:將溶液為234g/l的NaCl和50g/l的KNO3溶液的混合液,采用濃度為68%的H2SO4調節pH值為2.0,在溫度T=40℃至44℃的條件下,浸泡時間1.5天。優選地,所述常溫疲勞試驗的條件為:在室溫以及大氣條件下,對飛機內部封閉結構軸向加載正弦波,加載頻率f=5Hz,施加500次等幅載荷,疲勞應力:σmax=110MPa,σmin=20MPa。優選地,所述溶液浸泡試驗的條件為:將溶液為234g/l的NaCl和50g/l的KNO3溶液,采用濃度為68%的H2SO4調節pH值為2.0,溫度T=40℃至44℃的,浸泡時間1.5天;所述常溫疲勞試驗的條件為:室溫大氣,正弦波,軸向加載,加載頻率f=5Hz,施加500次等幅載荷,疲勞應力:σmax=110MPa,σmin=20MPa。優選地,所述步驟3的重復周期為8至12個循環周期。優選地,所述飛機內部封閉結構包括機翼翼尖、機翼封閉艙、方向舵、前緣襟翼、襟副翼。本申請的腐蝕試驗方法將多種腐蝕環境因素集成到試驗方法之中,通過采用此試驗方法進行加速試驗,能夠在短時間內更真實的驗證出飛機內部封閉結構表面的腐蝕防護體系抗腐蝕防護能力,避免腐蝕事故的發生。從而達到縮短對比驗證所需時間,提高對比驗證效率,保證飛機使用安全的目的。附圖說明圖1是根據本發明第一實施例的腐蝕試驗方法的流程示意圖。圖2是腐蝕試驗方法的試驗件的結構示意圖。圖3是腐蝕試驗方法的試驗件的另一結構示意圖。附圖標記:1第一基體3第三基體2第二基體4緊固件具體實施方式為使本發明實施的目的、技術方案和優點更加清楚,下面將結合本發明實施例中的附圖,對本發明實施例中的技術方案進行更加詳細的描述。在附圖中,自始至終相同或類似的標號表示相同或類似的元件或具有相同或類似功能的元件。所描述的實施例是本發明一部分實施例,而不是全部的實施例。下面通過參考附圖描述的實施例是示例性的,旨在用于解釋本發明,而不能理解為對本發明的限制。基于本發明中的實施例,本領域普通技術人員在沒有作出創造性勞動前提下所獲得的所有其他實施例,都屬于本發明保護的范圍。下面結合附圖對本發明的實施例進行詳細說明。在本發明的描述中,需要理解的是,術語“中心”、“縱向”、“橫向”、“前”、“后”、“左”、“右”、“豎直”、“水平”、“頂”、“底”“內”、“外”等指示的方位或位置關系為基于附圖所示的方位或位置關系,僅是為了便于描述本發明和簡化描述,而不是指示或暗示所指的裝置或元件必須具有特定的方位、以特定的方位構造和操作,因此不能理解為對本發明保護范圍的限制。圖1是根據本發明第一實施例的腐蝕試驗方法的流程示意圖。如圖1所示的腐蝕試驗方法,用于試驗飛機內部封閉結構表面防護體系抗腐蝕防護能力,該腐蝕試驗方法包括如下步驟:步驟1:為飛機內部封閉結構表面進行溶液浸泡試驗;步驟2:為飛機內部封閉結構表面進行常溫疲勞試驗;步驟3:重復步驟1至步驟2。可以理解的是,飛機內部封閉結構可以是真實的各個飛機內部封閉結構,也可以是仿制的試驗件。本申請的腐蝕試驗方法將多種腐蝕環境因素集成到試驗方法之中,通過采用此試驗方法進行加速試驗,能夠在短時間內更真實的驗證出飛機內部封閉結構表面的腐蝕防護體系抗腐蝕防護能力,避免腐蝕事故的發生。從而達到縮短對比驗證所需時間,提高對比驗證效率,保證飛機使用安全的目的。在一個實施例中,溶液浸泡試驗的條件為:將溶液為234g/l的NaCl和50g/l的KNO3溶液的混合液,采用濃度為68%的H2SO4調節pH值為2.0,溫度T=40℃至44℃,浸泡時間1.5天。在一個實施例中,常溫疲勞試驗的條件為:在室溫以及大氣條件下,對飛機內部封閉結構軸向加載正弦波,加載頻率f=5Hz,施加500次等幅載荷,疲勞應力:σmax=110MPa,σmin=20MPa。在本實施例中,溶液浸泡試驗的條件為:將溶液為234g/l的NaCl和50g/l的KNO3溶液,采用濃度為68%的H2SO4調節pH值為2.0,溫度T=40℃至44℃,浸泡時間1.5天;常溫疲勞試驗的條件為:室溫大氣,正弦波,軸向加載,加載頻率f=5Hz,施加500次等幅載荷,疲勞應力:σmax=110MPa,σmin=20MPa。同時采用上述條件,是以飛機一年內主要經受的環境要素包括溫度、濕度、降水量、固體沉降物、風、霧、鹽霧、海水、空氣中氯離子濃度、硫離子濃度及大氣污染物和工業廢氣等進行統計分析,將這些環境要素的主要作用時間、頻次等進行當量折算所得到的,一個周期的加速腐蝕試驗作用效果,相當于該部位在外場服役一年所遭受到的腐蝕環境作用效果,突出體現了外部結構外露部位且經常受紫外線照射區域紫外線、濕熱、鹽霧、熱沖擊和低溫疲勞等的綜合作用,具有針對性和加速性特點。有利的是,本申請的步驟3的重復周期為8至12個循環周期。本申請的飛機內部封閉結構包括機翼翼尖、機翼封閉艙、方向舵、前緣襟翼、襟副翼。圖2是腐蝕試驗方法的試驗件的結構示意圖。圖3是腐蝕試驗方法的試驗件的另一結構示意圖。下面以舉例的方式對本申請的用于試驗飛機內部封閉結構表面防護體系抗腐蝕防護能力的腐蝕試驗方法進行詳細闡述。可以理解的,該舉例并不構成對本申請的任何限制。以飛機某一封閉結構為例。參見圖1及圖2,制作仿真試驗件,該仿真試驗件包括第一基體1、第二基體2以及第三基體3,該仿真試驗件的主要結構用材和主要連接形式為:第一基體1以及第二基體2采用7B04鋁合金制作,第三基體3采用TA15鈦合金,緊固件采用30CrMnSiA螺栓,第一基體以及第二基體表面采用待考核的腐蝕防護體系進行防護。試驗件的腐蝕防護體系:1)第一基體1、第二基體2表面硫酸陽極化,重鉻酸鹽填充處理;2)處理后噴涂底漆,涂層厚度控制在25μm~35μm;3)第三基體3不進行處理;4)將第一基體1、第二基體2、第三基體3以及緊固件4進行連接裝配,裝配過程中,第一基體1、第二集體2與第三集體3之間的接觸面采用涂膠布進行隔離;5)將緊固件4粘絕緣涂料進行濕態裝配;6)裝配后內、外表面噴涂磁漆,涂層厚度控制在40μm~60μm。進行本申請的飛機外表面抗腐蝕防護能力的腐蝕試驗方法。驗證效果:腐蝕試驗方法共進行12個周期,約2個月。仿真試驗件在第2周期結束后,在仿真試驗件周圍出現了輕微的起泡,涂層出現輕微的變色和失光,而后,隨著試驗周期的延長,約第6個周期結束后,在仿真試驗件周圍已經出現了比較明顯的起泡現象,到10個周期后,涂層起泡比較嚴重,到12個周期,已經產生大量腐蝕產物,部分仿真試驗件周圍漆層有脫落,已經完全達到失效狀態。通過此試驗,可以驗證此結構試驗件的防護體系的抗腐蝕防護性能,并進一步推算其防護性能是否能滿足艦載飛機內部封閉結構的設計使用需求,其抗腐蝕性能在使用多長時間后失效等。通過本申請的腐蝕試驗方法,相對于現有技術的試驗方法,能夠更加全面、快速的掌握抗腐蝕性能。最后需要指出的是:以上實施例僅用以說明本發明的技術方案,而非對其限制。盡管參照前述實施例對本發明進行了詳細的說明,本領域的普通技術人員應當理解:其依然可以對前述各實施例所記載的技術方案進行修改,或者對其中部分技術特征進行等同替換;而這些修改或者替換,并不使相應技術方案的本質脫離本發明各實施例技術方案的精神和范圍。當前第1頁1 2 3