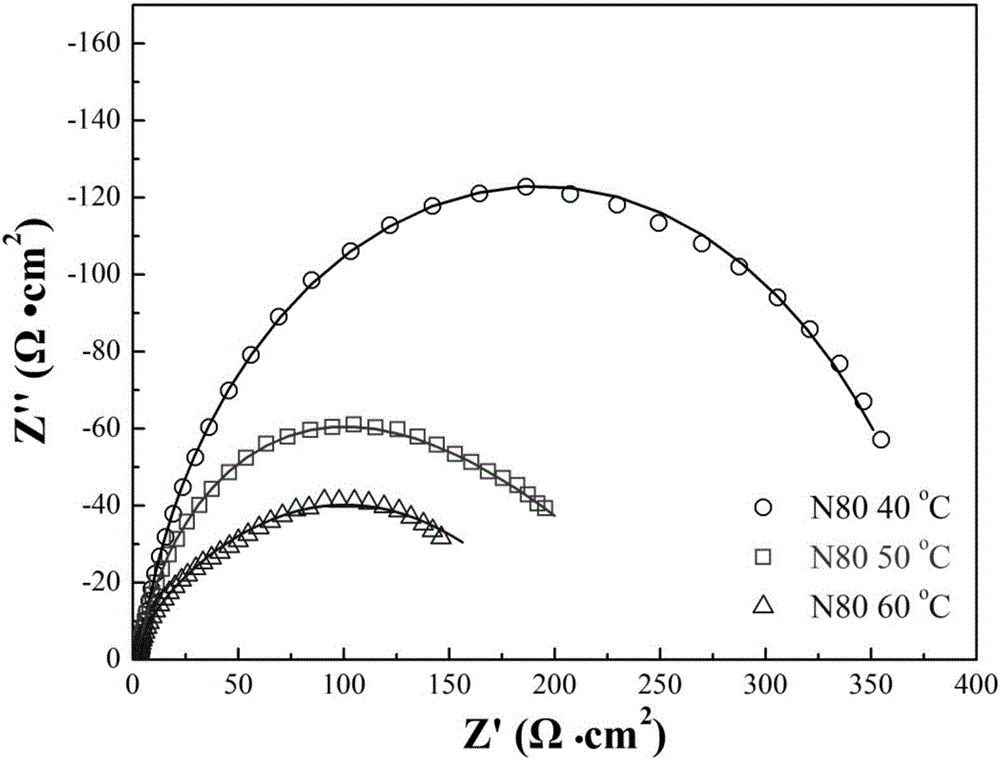
本發明屬于油田注水開發應用
技術領域:
,更具體地,涉及一種油田污水腐蝕結垢特性的測試方法,該測試方法尤其適用于在實驗室內快速、有針對性的預測油田現場注水系統腐蝕和結垢情況,并可依此提出防治措施,可針對具體的現場油田污水(如注水油田所用注水),是一種快速測試方法。
背景技術:
:隨著油田的開采進入中后期油壓下降,注水驅替提高采收率是大多數陸地油田的主要手段之一。在油田注水的過程中,外來水與油田內地層巖石的接觸,會發生各種物理變化和化學變化,極大的造成了地層的損害。同時,在注水過程中,注水管線中的流體由于地層溫度和壓力的變化,有些情況下造成嚴重的管線腐蝕甚至穿孔,還有某些成分容易析出,在注水管線中形成垢層,堵塞注水管線,對油田開采作業產生十分不利的影響。國內外已經有眾多油田注水過程中已出現了不同程度的腐蝕和結垢現象,由于各地水質和地層性質的差異,很難有統一而有效的解決方法,因此,開發一套有針對性、能快速預測并提出有效解決方案的方法十分有實際意義。技術實現要素:針對現有技術的以上缺陷或改進需求,本發明的目的在于提供一種油田污水腐蝕結垢特性的測試方法,其中通過對關鍵的各測試步驟的設置方式以及具體的參數設置等進行改進,與現有技術相比能夠有效解決油田污水腐蝕性、以及結垢性的評價測試問題,并且該測試方法可根據每個具體注水油田其不同的水質和管線情況靈活調整,能很好的反應每個現場不同的情況,使得通過本方法在實驗室內測試得出的測試結論與實際油田現場的實際情況匹配度高。為實現上述目的,按照本發明,提供了一種油田污水腐蝕結垢特性的測試方法,其特征在于,包括以下步驟:(1)靜態電化學分析步驟:在不同溫度下,以現場油田污水為溶液采用3電極系統通過交流阻抗法分別測試管線材料在所述現場油田污水下的電化學阻抗圖譜,并根據不同溫度下得到的所述電化學阻抗圖譜得出所述管線材料的相位角臨界轉變溫度;所述管線材料為現場油田輸送油田污水的管線所采用的材料;(2)CFD軟件模擬步驟:以所述現場油田輸送油田污水的管線為參考,設計模擬管線;接著,運用建模網格劃分軟件對該模擬管線進行計算機建模得到管線模型;然后,運用CFD軟件模擬出在不同進管口流速下該管線模型內的流態信息,得出湍流強度以及壁面剪切應力隨距進管口距離的分布情況;并根據所述湍流強度以及所述壁面剪切應力隨距進管口距離的的分布情況確定實驗測試片的安放位置;接著,根據在不同所述進管口流速下所述湍流強度以及所述壁面剪切應力隨距進管口距離的分布情況得出壁面剪切應力與進管口流速、以及距進管口距離三者的函數關系,湍流動能與進管口流速、以及距離進管口距離三者的函數關系;(3)動態管線模擬步驟:根據所述步驟(2)中的所述模擬管線、以及所述實驗測試片的安放位置,設置動態管線,該動態管線用于安放實驗測試片;接著,將所述實驗測試片安放在所述動態管線上,在不同溫度、以及不同進管口流速下進行水循環開始動態模擬實驗,并在不同的實驗時長下測量不同安放位置處的所述測試片的垢層厚度,所述不同安放位置對應不同的所述距進管口距離;所述實驗測試片與所述現場油田輸送油田污水的管線所采用的材料相同;所述水循環采用所述現場油田污水;所述動態管線與所述步驟(2)中的所述模擬管線為等比例關系;(4)數據整合分析步驟:根據所述步驟(2)中得到的壁面剪切應力與進管口流速、以及距進管口距離三者的函數關系,湍流動能與進管口流速、以及距離進管口距離三者的函數關系,所述步驟(3)中得到的在不同溫度、不同進管口流速、以及不同實驗時長下的不同安放位置處的垢層厚度,得出垢層厚度與變量之間的關系,從而得出該油田污水的腐蝕結垢特性;所述變量為湍流動能、壁面剪切應力、溫度、進管口流速、實驗時長和距進管口距離中的至少一個。作為本發明的進一步優選,所述步驟(3)中,在測量得到所述垢層厚度后,還包括:將所述實驗測試片干燥,測重后得到最終結垢量;接著再將所述實驗測試片酸洗干燥,測重后得到最終腐蝕程度。作為本發明的進一步優選,所述步驟(3)中的所述水循環以是添加有添加劑的所述現場油田污水進行的;所述添加劑為緩蝕劑、阻垢劑和殺菌劑中的至少一種。作為本發明的進一步優選,所述步驟(1)中通過交流阻抗法測試管線材料的電化學阻抗圖譜的測試時間為至少7天;所述3電極系統是以所述管線材料作為工作電極,以甘汞電極作為參比電極,以鉑電極作為對電極。作為本發明的進一步優選,所述步驟(3)中進行所述動態模擬實驗的溫度包括所述步驟(1)中得到的所述相位角臨界轉變溫度;優選的,所述步驟(3)中進行所述動態模擬實驗的溫度與所述步驟(1)中進行靜態電化學分析所采用的溫度一一對應,所述步驟(3)中進行所述動態模擬實驗的進管口流速與所述步驟(2)中運用CFD軟件模擬所采用的進管口流速一一對應;優選的,所述步驟(1)中進行靜態電化學分析所采用的溫度為40℃~60℃,所述步驟(2)中運用CFD軟件模擬所采用的進管口流速為0.41m/s~1.54m/s;所述步驟(3)中進行所述動態模擬實驗的溫度為40℃~60℃,所述步驟(3)中進行所述動態模擬實驗的進管口流速為0.41m/s~1.54m/s。作為本發明的進一步優選,所述步驟(2)中的所述建模網格劃分軟件為Gambit軟件;所述CFD軟件為Fluent軟件。作為本發明的進一步優選,所述步驟(3)中測量所述測試片的垢層厚度是將所述測試片在超景深顯微鏡觀察得出該測試片的垢層平均厚度。作為本發明的進一步優選,所述步驟(2)中得到的所述實驗測試片的安放位置對應所述湍流強度的極值位置、以及所述壁面剪切應力的極值位置中的至少一種。通過本發明所構思的以上技術方案,與現有技術相比,由于綜合了靜態電化學測試、CFD軟件模擬、動態管線模擬、數據整合分析這四個相對獨立而又相互關聯的測試步驟作為油田污水腐蝕結垢特性的測試方法,能夠對油田污水腐蝕與結垢特性進行快速的綜合測量評價,測量結論與實際情況匹配度高,對實際的油田注水生產具有大的指導作用。本發明中的動態管線模擬步驟是依照現場注水管線按比例縮小制作動態模擬管線模型,根據靜態電化學分析結果確定模擬實驗最佳實驗條件,根據CFD軟件模擬結果在流態信息變化較大的各個區域安裝測試片,應用3D超景深顯微鏡觀察測試鋼片表面形貌,用3D統計分析法測定垢層厚度。該步驟可對實驗溫度、使用的流速進行控制,可進行在線垢層厚度測量(垢層厚度測量可借助3D超景深顯微鏡觀察,再利用統計分析法計算,垢樣的平均厚度=體積/采樣面積)。利用該動態管線模擬步驟,可得出管道不同位置處(即,管道上距離進管口距離不同的位置處)電極表面垢層厚度分布。靜態電化學分析步驟是采用3電極系統,測試管線材料的電化學阻抗、極化曲線等,分析在靜態條件下油田現場污水中管線材料的腐蝕與結垢趨勢;根據電化學阻抗譜BODE圖,在高頻區(頻率高于100Hz的區間為高頻區)出現相位角峰對應于材料表面垢層膜厚和膜的致密性信息,在低頻區(頻率低于100Hz的區間為低頻區,即,以100Hz為分界點區分高頻區和低頻區)出現相位角峰對應于材料表面膜下腐蝕相關信息。CFD軟件模擬步驟,是根據實際油田現場運用的管徑和流速特征,計算出管壁剪切應力;是先通過GAMBIT軟件的建模和劃分網格及檢測后,再使用Fluent軟件進行流體動力學模擬,實驗模擬管線GAMBIT建模;統計管線不同位置截面的最大湍流能和不同位置壁面的最大剪切應力。本發明中的油田污水腐蝕結垢特性的測試方法,能夠快速測試,預測、評價油田注水腐蝕性和結垢性;另一方面,通過向油田污水中添加添加劑(如緩蝕劑、阻垢劑等)對水質進行調節,并再次測試,可以對各種添加劑(包括各種不同種類的添加劑、以及不同配比的添加劑)的添加效果(即,添加有添加劑的污水的腐蝕性和結垢性等)進行評價,具有良好的針對性和實際應用價值。本發明中的油田污水腐蝕結垢特性的測試方法通過靜態電化學分析、CFD軟件模擬、動態管線模擬、數據整合分析四大部分,能快速有效的在實驗室內還原油田現場,以油田現場不同的實際狀況(如溫度,壓力,管線材料種類,表面粗糙度,管線內部湍流強度,壁面剪切應力等)為基礎,系統的分析注水管線的腐蝕與結垢趨勢,可建立有效的函數模型對注入水腐蝕和結垢規律進行預測,并對提出的解決方案(如向注水中添加添加劑等)進行評價,測試評價的結論與生產現場實際情況符合較好。本發明中的油田污水腐蝕結垢特性的測試方法能夠快速對油田污水腐蝕結垢特性作出評價,具有簡單,準確性高,針對性強等優點,是一種實驗室內預測油田現場注水系統腐蝕和結垢情況,并能夠預先評價防治措施,具體具有以下優點:(1)本發明的CFD軟件模擬,動態管線模擬等方法有針對性,可以評價不同油田的不同情況,能較好的解決不同油田的實際問題;其中3D統計分析法能很好的獲得垢層厚度信息,準確快速。(2)本發明提出的數據擬合將各個因素對管線結垢和腐蝕的影響關聯了起來,能對現場的腐蝕和結垢情況進行較為準確的預測,為現場的防治提供相關信息。(3)本發明的動態管線模擬還可以對提出的解決方案進行驗證,能在實驗室中找到最佳的解決方案和相關的技術指標,注意事項,為現場實際生產提供指導,節約人力物力。本發明油田污水腐蝕結垢特性的測試方法,可快速預測油田注水的結垢和腐蝕特性,并對相應的解決方案(如向油田注水中添加添加劑、改變管線材料等)進行評價,對每個注水油田不同的水質和管線情況都有針對性,能很好的反應每個現場不同的情況,進一步的,可得到最佳的添加劑使用組合。本發明中的測試評價方法以油田現場水為介質,能夠實況反應油田現場情況;靜態電化學分析步驟通過交流阻抗、電化學極化等分析手段,能夠找出管線所用材料在現場水中的腐蝕和結垢趨勢;CFD軟件模擬步驟通過CFD軟件模擬生產現場的情況,模擬出管線的流態、湍流強度、壁面剪切力等相關信息;動態管線模擬步驟則根據現場實際比例建立模擬管線,基于靜態電化學分析部分得到的最適宜實驗條件進行實驗,并可同時檢驗提出的解決方案在實際應用情況下的效用;數據整合分析步驟則是整合前三個步驟的數據,建立相關的簡單函數模型,對生產現場管線結垢和腐蝕的程度進行大致預測,討論腐蝕和結垢程度與溫度、流速、湍流強度、壁面剪切應力等相關因素之間的變化關系,同時評價所提出的解決方案的好壞以及現場可行性。附圖說明圖1A、1B、1C分別是N80鋼不同溫度下交流阻抗數據擬合后曲線圖;圖2A是本發明動態管線模擬實驗裝置結構示意圖,圖2B為安放測試鋼片的動態管線(該動態管線可以采用玻璃材料)的放大示意圖。圖2A中的動態管線其外徑為3cm,內徑為2.8cm,該動態管線自上而下由空心的圓柱體和錐體組合而成(該錐體是為了便于管線連接而設置的,也可不采用),圓柱體的圓形底面與錐體的圓形頂面重合,其中,圓柱體的高度為67cm,錐體的高度為3cm,在距圓柱體圓形頂面7cm、12cm、37cm的圓柱體側面上分別設置有相對的、向外凸出的、凸出寬度為2cm的容納口,這些容納口共計6個,用于容納測試鋼片(這6個容納口均可用活塞密封,待測試的鋼片可以附著在活塞上)。該動態管線模擬實驗的裝置包括水浴鍋(精密測溫探頭、高精度控溫器控溫)、以及相應的連接管路;其中,恒溫水浴鍋配有精密控溫探頭,該探頭還與高精度控溫器相連。圖3是本發明所述的3D統計分析法測試原理;圖4是本發明所述的軟件管線建模示例;圖5A、5B、5C分別是本發明所述的CFD軟件模擬計算結果示例;圖5B自左向右分別為1.38e-03、7.76e-05、1.05e-05,圖5C自左向右分別為3.14e-02、1.29e-02、9.50e-03。圖6是本發明所述的動態模擬實驗測試鋼片示例;圖6(a)(b)(c)(d)均為N80碳鋼,自左向右對應不同的測試片的安放位置(即對應圖2A中所示的自上而下測試鋼片安放位置)。圖7A、7B均是本發明所述的數據整合函數建模示例;圖8是進管口流速0.41m/s不同位置垢層厚度隨時間變化的曲線;圖中的位置1、位置2、位置3依次對應圖2A中所示的自上向下的測試鋼片安放位置;圖9是進管口流速1.06m/s不同位置垢層厚度隨時間變化的曲線;圖中的位置1、位置2、位置3依次對應圖2A中所示的自上向下的測試鋼片安放位置;圖10是進管口流速1.54m/s不同位置垢層厚度隨時間變化的曲線;圖中的位置1、位置2、位置3依次對應圖2A中所示的自上向下的測試鋼片安放位置;圖11A、11B分別是不加阻垢殺菌劑的結垢產物圖、以及添加阻垢殺菌劑的結垢產物圖,即,阻垢殺菌劑添加前后某油田現場管線內壁結垢產物對比圖。具體實施方式為了使本發明的目的、技術方案及優點更加清楚明白,以下結合附圖及實施例,對本發明進行進一步詳細說明。應當理解,此處所描述的具體實施例僅僅用以解釋本發明,并不用于限定本發明。此外,下面所描述的本發明各個實施方式中所涉及到的技術特征只要彼此之間未構成沖突就可以相互組合。實施步驟1:電化學靜態分析準備拋光好的現場管線所用材料的電極用作測試用工作電極,甘汞電極用作參比電極,鉑電極為對電極,組成3電極體系,待3電極體系在現場水溶液中開路電位穩定后,在開路電位正負20mV下進行EIS測試,測試的頻率區間為105Hz至10-3Hz,之后測定在開路電位下測極化曲線,利用科斯特電化學工作站ZView中電化學阻抗擬合分析軟件擬合出等效電路和相應的電化學參數;分別測定在40℃,50℃,60℃條件下,碳鋼電極在現場水中的阻抗圖譜和極化曲線;連續7天測電極在60℃現場水中的阻抗圖譜,分析長時間浸泡電極表面結垢和腐蝕的變化規律(由于40℃、50℃、60℃下的阻抗圖譜中,60℃下鋼片的腐蝕和結垢更加明顯,因此可以僅以60℃下阻抗圖譜,分析長時間浸泡電極表面結垢和腐蝕的變化規律)。見圖1和表1。從圖上可以看出,高頻區(頻率大于100Hz的區間定義為高頻區)相位角在實驗溫度超過50℃后,相位角突破-50°,說明臨界轉變溫度Tc為50℃(該臨界轉變溫度即相位角突變溫度,當溫度高于此溫度時,結垢速率大于腐蝕速率,宏觀體現出結垢為主;而當溫度低于此溫度時,腐蝕反應速率大于結垢速率,宏觀則體現出腐蝕反應為主)。這是后續動態模擬實驗步驟最關注的溫度點。通過阻抗圖譜可判斷結垢和腐蝕的趨勢,而利用極化曲線可以得出管道材料(如碳鋼)的腐蝕速率大小。表1N80鋼在不同溫度下的交流阻抗擬合數據結果電化學靜態分析的結果表明,溫度低于60℃條件下管線結垢速率不高,不易結垢,當溫度高于60℃條件下,管線結垢趨勢隨著溫度的逐漸增加;試樣隨著溫度的增加試樣腐蝕速率增加。實施步驟2:CFD建模模擬參考油田注水現場的輸水管線的實際尺寸,設計模擬管線(該模擬管線的長度與管線直徑的比值不小于10,例如,模擬管線的直徑可以小于實際油田注水管線的直徑,只要模擬管線的長度與直徑兩者的比值大于10即可;為了便于管線連接,可在該模擬管線的一端可設置錐體結構,在該錐體內部以及靠近該錐體的管線部分均不設置樣品點,以免整體管線模擬實驗;該模擬管線的長度可靈活調整,只要能夠獲得相對穩定的流態即可,一般模擬管線的長度與管線直徑的比值不小于10就能滿足要求,當然長度越長越有利)。運用Gambit軟件等建模網格劃分軟件對管線進行計算機建模,再用Fluent(CFD)軟件在不同流速下模擬出管線中流態信息,如湍流強度,壁面剪切應力等的分布情況(尤其是湍流強度和剪切應力的最大值和最小值位置,即極值位置)并初步確定實驗測試片安放位置(由于湍流強度和剪切應力的極值位置一般腐蝕或結垢都相對嚴重,這樣獲得的數據更加有參考性)。軟件建模示范見圖4。在該步驟中,利用CFD軟件模擬,可找出現場管線的流態信息分布,確定下步動態管線模擬測試的具體測試條件(如流速、試片安裝的位置等,在該CFD軟件模擬步驟中采用的流速主要是根據油田現場實際的速度為參考,例如,可以圍繞實際速度上下取若干個點進行CFD模擬;在下步動態管線模擬實驗中所采用的流速,可以與該CFD模擬步驟中的流速保持一致;CFD模擬步驟中初步確定實驗測試片安放位置一般就是動態管線模擬步驟中的試片安裝位置,如果遇到一些無法安裝試片的情況,比如模擬出兩個試片安放位置過于接近,則可以根據模擬結果重新考慮其中一個位置)。實施步驟3:動態管線模擬動態模擬管線示意如圖2所示(該動態模擬管線的尺寸可以與CFD模擬管線的尺寸保持一致),實驗實物按照該圖對應設置。每一塊膠塞上可安放不同種類的測試鋼片,一次用丙酮和乙醇清洗安裝好的鋼片表面備用,測試開始前,先將油田現場水樣加熱恒溫至所需溫度1小時,再插入測試鋼片進行水循環,循環初始時期,在鋼片表面易有較多氣泡附著,此時應暫停循環水,使鋼片裸露,氣泡隨之破裂,再開啟循環水,如此反復直至鋼片表面不再有氣泡附著。在測試過程中,由于水中原有氣體溢出和液體揮發作用易在測試管線頂端產生氣體,這時應及時用止水夾夾住底部出水口,從上部預留的溢水口排除氣泡并接收上部溢出的帶有泡沫的液體,并倒回現場水瓶中。開啟動態模擬實驗后,在第24h,48h,72h,120h,168h,216h時暫停水循環,取出測試鋼片,分別用3D超景深顯微鏡觀察測試鋼片的表面形貌,用3D超景深顯微鏡的平均厚度法測量垢層的平均厚度。體積平均厚度即用3D照相機獲取一定面積內垢樣的體積,然后除以底面積,從而獲得垢樣的平均厚度,低放大倍數,在試片不同部位進行3d井深照相進行采樣,通過多個采樣點的厚度數值取平均,從而能夠較為準確的反映整個試片的結垢厚度信息。統計分析方法,如圖3所示。變換測試片材料種類和表面粗糙度等因素(表面粗糙度也可參考實際管道的粗糙度指標),分析不同因素對測試片表面腐蝕和結垢規律的影響(圖6所示為動態模擬試片表面結垢后的形貌圖)。測試結束后,測試片干燥后測增重確定結垢量,酸洗后測失重確定腐蝕程度,3D照相機觀察采集腐蝕形貌。測試片還可進行SEM,EDAX,XRD,XPS等分析確定腐蝕產物和垢樣的成分信息。該動態管線模擬實驗可以用于檢測備選解決方案(如向油田注水中添加添加劑等),確定其有效性以及相關技術指標和注意事項(如構成添加劑的具體成分、及相應試劑的配比等),例如,某油田擬使用某緩蝕劑減緩管道腐蝕,可以在此模擬管線中先進行模擬實驗。該步驟是將現場管線按比例縮小制作模擬管線,根據電化學分析結果確定最佳測試條件,根據軟件模擬結果確定測試鋼片分布位置;通過3D超景深顯微鏡觀察測試鋼片表面腐蝕和結垢形貌;應用3D統計分析發采集垢層厚度隨時間變化的規律;實驗結束后通過增重計算結垢量,酸洗后通過失重計算腐蝕程度。中低流速環境下,距離管口較近的位置結垢較薄,但隨著流速的加大,厚度急劇上升,而管中部和后部的區域呈先增大后減小的趨勢。通過在動態管線模擬步驟中采用不同溫度、不同進管口流速,可系統的分析在油田污水作用下某一管道的結垢和腐蝕趨勢;以溫度為例,該動態管線模擬步驟所采用的多個不同的溫度,可以是在現場溫度(即,實際油田現場的溫度)和臨界轉變溫度(即,步驟1電化學靜態分析實驗所得的臨界轉變溫度)附近的多個溫度點,從而能夠系統分析油田現場溫度和臨界轉變溫度附近的結垢和腐蝕趨勢,并進一步的提出可以減少腐蝕或者結垢的參考意見。實施步驟4:數據整合分析以CFD軟件模擬和動態管線模擬為主要數據來源,考察相關變量,建立溫度,管線材料種類,表面粗糙度,管線內部湍流強度,壁面剪切應力等相關變量與管線材料表面腐蝕結垢的關系,以函數關系式方式表達,并用公式或圖像、表示其間的函數關系,對油田現場的管線腐蝕和結垢情況進行分析和預測。見圖5、圖7-圖10。例如,0.41m/s流速下動態管線模擬實驗獲得的最大結垢速率是1.0543μm/h,1.54m/s流速下流速更大,高流速下壁面剪切應力很大,垢層形成速度具有不確定性和偶然性,垢層厚度隨時間變化并不很好的符合線性關系。在CFD軟件模擬和動態管線模擬中,還可進一步的建立壓力與管線材料表面腐蝕結垢的關系,并相似的以函數關系式方式表達;考慮到油田注水管路中,不同高度處的管路往往具有不同的水壓,因此本發明的動態管線模擬中的動態管線按豎直方向設置;尤其當動態管線較長時,靠近底部的試樣點就會因為水柱高度壓力較大,與靠近頂部的試樣壓力有區別,導致壓力不同;但是受動態管線的長度限制,動態管線內的壓力增加并沒有實際油田埋設管線內增加的壓力大,因此在動態模擬管線允許的情況下,可適當增加動態管線的壓力,并得出壓力與管線材料表面腐蝕結垢的關系。本發明模擬條件下建立的垢層厚度與各變量之間的最終函數模型如下式,其中湍流能k(m2/s2)和壁面剪切應力p(Pa)與進管口流速v(m/s),距離進管口距離d(cm)的函數關系可由CFD軟件模擬獲得。H=F(k,p,T)k=F(v,d)p=F(v,d)---(1)]]>式中,H為垢層厚度(μm),k為湍流能(m2/s2),p為壁面剪切應力(Pa),v為進管口流速(m/s),d為距離進管口距離(cm),T為溫度(℃)。通過靜態電化學分析,CFD軟件模擬,動態管線模擬的數據找出影響管線材料腐蝕或結垢的因素,建立函數模型,并用公式或圖像等表述函數關系,應用所得函數關系,對油田現場的腐蝕和結垢進行預測。實施步驟5:勝利油田現場某油田聚合物驅產出水通過實驗室快速評價,結果表明其微生物誘導結垢嚴重;實驗室篩選阻垢劑和殺菌劑組合添加后可以明顯抑制結垢(即,將添加有不同阻垢劑和/或殺菌劑的現場水作為上述步驟1-4,尤其是動態管線模擬的實驗用水,由此篩選出最佳的阻垢劑和殺菌劑組合)。油田現場采用實驗室篩選配方,經過現場3個月驗證實驗,結垢問題得到控制,阻垢率達到90%。現場結垢對比圖見圖11A和11B。圖中可以看出添加阻垢殺菌劑后,管線內壁微生物誘導結垢產物較少。通過本發明中的測試方法可以判斷某油田污水的腐蝕性(即腐蝕傾向)以及結垢性(即結垢傾向)強弱。本發明中的動態管線模擬步驟是以靜態電化學分析步驟所采用的溫度、CFD軟件模擬步驟所采用的流速為實驗條件,通過實驗數據分析,可以檢測理論計算與實際模擬之間大趨勢上的統一性,從而使得出的結論更加有參考性。例如,通過靜態電化學分析(如相位角信息等),可以判斷材料腐蝕和結垢的趨勢,即預先判斷材料在特定溫度下的腐蝕和結垢趨勢;而在動態管線模擬步驟中則通過3d照相機來實際的觀察管線在實際使用中的結垢和腐蝕趨勢,從而檢測理論計算與實際模擬之間大趨勢上的統一性,從而使得出的結論更加有參考性。本領域的技術人員容易理解,以上所述僅為本發明的較佳實施例而已,并不用以限制本發明,凡在本發明的精神和原則之內所作的任何修改、等同替換和改進等,均應包含在本發明的保護范圍之內。當前第1頁1 2 3