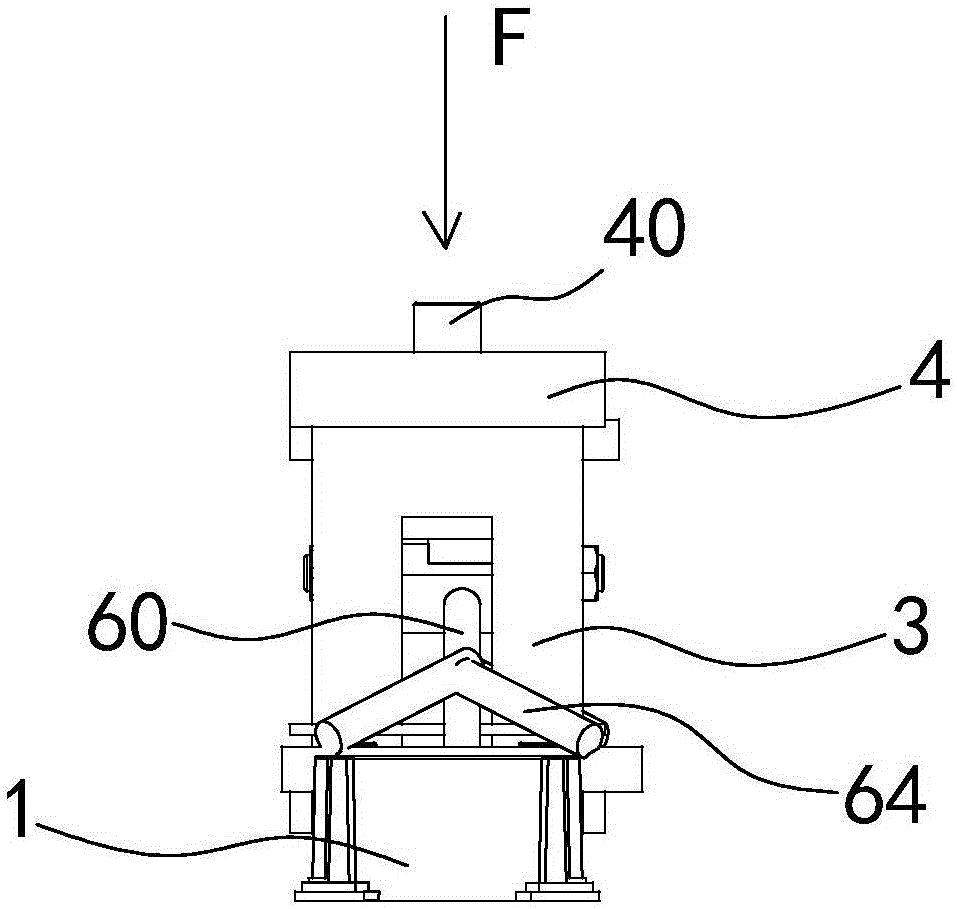
本發明涉及一種檢測工裝和檢測方法,具體涉及用于檢測軌下基板復合載荷的檢測工裝及其檢測方法,尤其是用于檢測軌下基板U型槽面復合載荷的檢測工裝及其檢測方法。
背景技術:
:軌下基板在服役期間,特別是處于線路彎道、緊急剎車、軌下基板在軌道板上無擋肩支撐、車輪與鋼軌嚙合型面存在誤差等因素引起離心力通過鋼軌和彈條等扣件對基板單側沖擊狀態下,軌下基板應該具有很高的強度值。為了保證軌下基板具有承受規定復合載荷的能力,在軌下基板投入使用前,必須對該軌下基板進行嚴格的復合載荷試驗。然而,目前中國市面上還沒有一套完整且對軌下基板進行復合載荷的檢測工裝,因此無法對軌下基板進行有效的檢測試驗。因此,為了填補這一空白,提出一種用于檢測軌下基板復合載荷的檢測工裝及檢測方法是本發明所要研究的課題。技術實現要素:本發明目的是提供一種用于檢測軌下基板復合載荷的檢測工裝及檢測方法,以填補軌下基板的復合載荷檢測的空白。為達到上述目的,本發明采用的技術方案是:一種用于檢測軌下基板復合載荷的檢測工裝,所述的軌下基板包括兩個U型槽,該兩個U型槽分別位于軌下基板的左右兩側,所述檢測工裝包括上壓板基座、上壓板立柱、支撐架、墊板以及連接結構;所述墊板層疊在軌下基板的上方,所述上壓板立柱垂直軌下基板布置,且上壓板立柱一端壓在墊板的頂面,另一端連接在上壓板基座底面,所述上壓板立柱上開設有避讓通孔,所述上壓板基座和軌下基板平行布置;所述連接結構一端為固定端且固定連接上壓板基座,另一端為樞紐端且朝向軌下基板布置,所述樞紐端懸設在上壓板基座和軌下基板之間,且樞紐端設有連接軸;所述支撐架包括兩組支撐架,每組支撐架均至少包括一橫桿和一豎桿,橫桿和豎桿固定連接形成一“T”字形的支撐結構;所述的兩組支撐架中,定義第一組支撐架的橫桿為第一橫桿,第一組支撐架的豎桿為第一豎桿,第二組支撐架的橫桿為第二橫桿,第二組支撐架的豎桿為第二豎桿;在裝配狀態下,所述第一橫桿水平嵌設在軌下基板位于左側的U型槽中,第二橫桿水平嵌設在軌下基板位于右側的U型槽中;所述第一豎桿一端固定連接在第一橫桿的中點,另一端通過避讓通孔連接至連接結構的樞紐端;第二豎桿一端固定連接在第二橫桿的中點,另一端通過避讓通孔連接至連接結構的樞紐端;在試驗狀態下,所述上壓板基座上作用有一試驗機施加在上壓板基座的載荷力F,該載荷力F向下迫使上壓板基座往下壓,上壓板基座受到的載荷力通過第一豎桿和第二豎桿分解且傳遞至第一橫桿和第二橫桿中,第一橫桿和第二橫桿再將各自受到的分解力傳遞給各自所位于的U型槽中。上述技術方案中的有關內容解釋如下:1、上述方案中,針對每組支撐架,均設有加固連接桿。2、上述方案中,所述加固連接桿為一倒V型結構,該倒V型結構的頂端固定連接在豎桿上,該倒V型結構的兩個末端分別固定連接在橫桿的兩端區域,以形成一牢固的三角形結構。3、上述方案中,所述上壓板基座的頂端還設有一上壓板固定軸,通過該上壓板固定軸實現該檢測工裝和試驗機之間的匹配安裝。4、上述方案中,所述連接結構包括連接套、連接軸以及連接芯,所述連接套上端固定在上壓板基座的底面上,下端懸空,所述連接芯中設有插孔,且位于連接套的下端區域;在裝配狀態下,所述第一豎桿和第二豎桿均連接至所述連接芯上,并通過連接軸鎖定。5、上述方案中,所述墊板用于模擬軌底與位于軌底下方的橡膠墊板的組合。6、上述方案中,所述支撐架用于模擬軌道彈條的作用,相當于彈條尾部扣壓在軌下基板的U型槽內。7、上述方案中,用試驗機對檢測工裝加載載荷力,再通過檢測工裝的支撐架傳遞給U型槽的作用力的方向模擬火車車輪傳遞給鋼軌和彈條扣件的力對軌下基板的U型槽接觸點的作用力。8、上述方案中,通過上壓板基座與試驗機匹配連接,該上壓板基座是便于后期試驗而設計的。為達到上述目的,本發明采用的另一種技術方案是:一種用于檢測軌下基板復合載荷的檢測工裝,采用所述的檢測工裝,配合復合載荷試驗機,按以下步驟進行操作:步驟1,將軌下基板安裝在所述檢測工裝的下方,使得檢測工裝的第一橫桿位于左側的U型槽中,第二橫桿位于右側的U型槽中;步驟2,將安裝有軌下基板的檢測工裝的上壓板基座與所述試驗機的壓頭連接,并保證軌下基板相對于試驗機的壓頭中心垂線對稱;步驟3,根據軌枕的類型及我國《鐵道車輛動力學性能評定和試驗鑒定規范》(GB5599-1985)中的施加于軌道上的橫向水平力的限值公式獲得施加于軌道上的橫向水平力F′的值,并根據一經驗公式F=F′*K計算出試驗機的載荷力F的值,將該載荷力F的值作為試驗機作用于上壓板基座的作用力的值,其中K為經驗系數1.35;步驟4,啟動試驗機下行按鈕,所述試驗機通過壓頭向檢測工裝的上壓板基座上加載載荷力F,上壓板基座將受到的載荷力F傳遞給軌下基板的U型槽面,試驗機保載T秒后卸載對上壓板基座的載荷力F;步驟5,重復步驟3進而連續試驗至少兩次:步驟6,將軌下基板從檢測工裝中取下,并檢查經過所述步驟5試驗的軌下基板有無損壞或變形;步驟7,若該步驟6中的軌下基板未發生損壞或變形值小于或等于閾值T,則判定檢測合格;反之判定檢測不合格。上述技術方案中的有關內容解釋如下:1、上述方案中,所述試驗機以1kN/秒的加載速度向軌下基板U型槽面加載。2、上述方案中,所述步驟3中,在計算試驗機的載荷力F的值時,取該載荷力的值大于或等于F′*1.35的值。本發明工作原理是:本發明通過檢測工裝模擬軌下基板在服役期間,特別是處于線路彎道、緊急剎車、塑料基板在軌道板上無擋肩支撐、車輪與鋼軌嚙合型面存在誤差等因素引起離心力通過鋼軌和扣件對軌下基板單側沖擊狀態下,校核軌下基板應該具有的強度值,從而有效實現了對該軌下基板復合載荷的檢測。在試驗過程中個,通過試驗機傳遞給支撐架、支撐架再作用在軌下基板的力,模擬車輪壓到鋼軌,然后鋼軌傳遞到彈條扣件的力、彈條扣件再作用在軌下基板上的力。由于上述技術方案運用,本發明與現有技術相比具有下列優點:本發明構思巧妙、結構簡單、成本低廉,使用操作便捷,加大了測量結果的可靠性,通過檢測工裝及檢測方法,有效實現了軌下基板的復合載荷的精確檢測,保證了質量、間接地提高了產品生產效率,填補了軌下基板復合載荷測試的這一空白,起到了意料不到的效果。附圖說明附圖1為本實施例中主視結構示意圖;附圖2為本實施例中側視結構示意圖;附圖3為本實施例中側視立體結構圖。以上附圖中:1、軌下基板;2、墊板;3、上壓板立柱;4、上壓板基座;40、上壓板固定軸;5、連接結構;50、連接套;51、連接軸;52、連接芯;6、支撐架;60、第一橫桿;61、第二橫桿;62、第一豎桿;63、第二豎桿;64、加固連接桿。具體實施方式下面結合附圖及實施例對本發明作進一步描述:實施例:一種用于檢測軌下基板復合載荷的檢測工裝參見附圖1-3,所述的軌下基板1包括兩個U型槽,該兩個U型槽分別位于軌下基板1的左右兩側,所述檢測工裝包括上壓板基座4、上壓板立柱3、支撐架6、墊板2以及連接結構5。本實施例中,為了與試驗機連接,上壓板基座4的頂端還設有一上壓板固定軸40,通過該上壓板固定軸40實現該檢測工裝和試驗機之間的匹配安裝。所述墊板2層疊在軌下基板1的上方,所述上壓板立柱3垂直軌下基板1布置,且上壓板立柱3一端壓在墊板2的頂面,另一端連接在上壓板基座4底面,所述上壓板基座4和軌下基板1平行布置,所述上壓板立柱3上開設有避讓通孔。所述連接結構5一端為固定端且固定連接上壓板基座4,另一端為樞紐端且朝向軌下基板1布置,所述樞紐端懸設在上壓板基座4和軌下基板1之間,且樞紐端設有連接軸51。所述連接結構5包括連接套50、連接軸51以及連接芯52,所述連接套50上端固定在上壓板基座4的底面上,下端懸空,所述連接芯52中設有插孔,且位于連接套50的下端區域;在裝配狀態下,所述第一豎桿62和第二豎桿63均連接至所述連接芯52上,并通過連接軸鎖定。所述支撐架6包括兩組支撐架6,每組支撐架6均至少包括一橫桿和一豎桿,橫桿和豎桿固定連接形成一“T”字形的支撐結構;所述的兩組支撐架6中,定義第一組支撐架6的橫桿為第一橫桿60,第一組支撐架6的豎桿為第一豎桿62,第二組支撐架6的橫桿為第二橫桿61,第二組支撐架6的豎桿為第二豎桿63。在裝配狀態下,所述第一橫桿60水平嵌設在軌下基板1位于左側的U型槽中,第二橫桿61水平嵌設在軌下基板1位于右側的U型槽中;所述第一豎桿62一端固定連接在第一橫桿60的中點,另一端通過避讓通孔連接至連接結構5的樞紐端;第二豎桿63一端固定連接在第二橫桿61的中點,另一端通過避讓通孔連接至連接結構5的樞紐端。在試驗狀態下,所述上壓板基座4上作用有一試驗機施加在上壓板基座4的載荷力F,該載荷力F向下迫使上壓板基座4往下壓,上壓板基座4受到的載荷力通過第一豎桿62和第二豎桿63分解且傳遞至第一橫桿60和第二橫桿61中,第一橫桿60和第二橫桿61再將各自受到的分解力傳遞給各自所位于的U型槽中。本實施例中,針對每組支撐架6,均設有加固連接桿64,每個加固連接桿64為一倒V型結構,該倒V型結構的尖端固定連接在豎桿上,該倒V型結構的兩個末端分別固定連接在橫桿的兩端區域,以形成一牢固的三角形結構。上述實施例檢測軌下基板1復合載荷的檢測工裝,所對應的方法如下:采用所述檢測工裝,并配合復合載荷試驗機使用,按以下步驟進行操作:步驟1,將軌下基板1安裝在所述檢測工裝的下方,使得檢測工裝的第一橫桿60位于軌下基板1左側的U型槽中,第二橫桿61位于軌下基板1右側的U型槽中。步驟2,將安裝有軌下基板1的檢測工裝的上壓板基座4與所述試驗機的壓頭連接,并保證軌下基板1相對于試驗機的壓頭中心垂線對稱。步驟3,根據軌枕的類型及我國《鐵道車輛動力學性能評定和試驗鑒定規范》(GB5599-1985)中的施加于軌道上的橫向水平力的限值公式獲得施加于軌道上的橫向水平力F′的值,并根據一經驗公式F=F′*K計算出試驗機的載荷力F的值,將該載荷力F的值作為試驗機作用于上壓板基座1的作用力的值,其中K為經驗加載系數1.35。步驟4,啟動試驗機下行按鈕,所述試驗機通過壓頭向檢測工裝的上壓板基座4上加載載荷力F,上壓板基座4將受到的載荷力F傳遞給軌下基板1的U型槽面,試驗機保載T秒后卸載對上壓板基座4的載荷力F。步驟5,重復步驟3進而連續試驗至少兩次,本實施例中,重復步驟3進行試驗三次。步驟6,將軌下基板1從檢測工裝中取下,并檢查經過所述步驟5試驗的軌下基板1有無損壞或變形。步驟7,若該步驟6中的軌下基板未發生損壞或變形值小于或等于閾值T,則判定檢測合格;反之判定檢測不合格。本實施例中,閾值T取0.8mm,若經過以上測試的軌下基板1變形值小于或閾值0.8mm,則說明該軌下基板1合格,若軌下基板的也就是說如果測試過的軌下基板1的變形值大于或等于0.8mm,則說明該軌下基板1不合格。本實施例的工作原理如下:采用如上試驗機和檢測工裝配合使用對軌下基板1進行復合載荷試驗。其中,每組支撐架6相當于軌道彈條,而本實施例中的墊板2模擬鋼軌軌底和軌底下方的橡膠墊板2的組合。假定:軸重F1=12.7噸,折合F1=124.46kN,在車輪與鋼軌接觸點處以法線方向傳遞給鋼軌。軌枕為混凝土軌枕,根據我國《鐵道車輛動力學性能評定和試驗鑒定規范》(GB5599-1985)規定,對施加于軌道上的橫向水平力F′采用如下的限值公式:F′≤0.85*(15+F/2)=0.85*(15+124.46/2)=65.65(kN),得到限值載荷的水平分力F′大約為65.65kN。也就是說,此時,理論上軌下基板1的限值載荷的水平分力F′不能超過65.65kN。定量測定值:U型槽面復合載荷檢測:U型槽面經復合載荷試驗后不得有傷損,其彎曲變形量不得超過0.8mm。考慮本項試驗為扣件零件模擬試驗、車輪對鋼軌的沖擊、軌下基板1制造誤差、試驗裝置制造誤差、扣件安裝誤差以及電液伺服材料試驗機加載速度較慢等因素,所以,本項試驗經驗加載系數1.35。因此,試驗機載荷F=F′*1.35=65.65*1.35=88.63kN,取值90kN。其中,經驗加載系數取1.35,大于系數1,而90kN大于88.63kN,這樣取值是為了對嚴格把關試驗條件,從而保證軌下基板試驗的有效性,但是試驗機載荷的取值也不能過于苛刻,否則生產的軌下基板1就不會合格了。將軌下基板1放置在電液伺服材料試驗機的平臺上,保證軌下基板1相對于試驗機壓頭中心垂線處于對稱條件,并將試驗工裝的兩撐桿頂分別靠在軌下基板1U型槽面的外側面,啟動下行按鈕,試驗機以1kN/秒的加載速度通過壓頭向軌下基板1U型槽面加載,當試驗機載荷F=90kN時,保載60秒,然后卸載,連續進行該試驗3次。此后,取下軌下基板,檢查有無損壞或變形,當沒發生損壞或變形值≤0.8mm,則判定檢測合格。參見下表為軌下基板U型槽面復合載荷試驗參數。表:軌下基板U型槽面復合載荷試驗參數序號項目名稱符號數值單位1試驗機載荷F90kN2保載時間T60S3循環次數n3次4加載速度V1kN/s針對上述實施例,本實施例進一步解釋及可能產生的變化描述如下:1、上述實施例中,試驗機采用1kN/秒的加載速度,事實上,試驗機的加載速度可以為除了1kN/秒以外的其它值,不僅限于11kN/秒,試驗員可以根據需求調整該加載速度。2、上述實施例中,在通過檢測軌下基板1有無形變及形變大小從而判定軌下基板1是否合格時,閾值T取0.8mm,事實上閾值T除了取0.8mm外,還可以取其它值,不僅限于0.8mm,試驗員可以根據需求調整閾值大小。3、上述實施例中,復合載荷試驗進行3次,事實上,該試驗還可以是2次、4次及4次以上,理論上是試驗次數越多,越精確,其實,試驗1次也是可行的,只是,試驗1次可能存在一定誤差,試驗員可以根據需求調整試驗次數。上述實施例只為說明本發明的技術構思及特點,其目的在于讓熟悉此項技術的人士能夠了解本發明的內容并據以實施,并不能以此限制本發明的保護范圍。凡根據本發明精神實質所作的等效變化或修飾,都應涵蓋在本發明的保護范圍之內。當前第1頁1 2 3