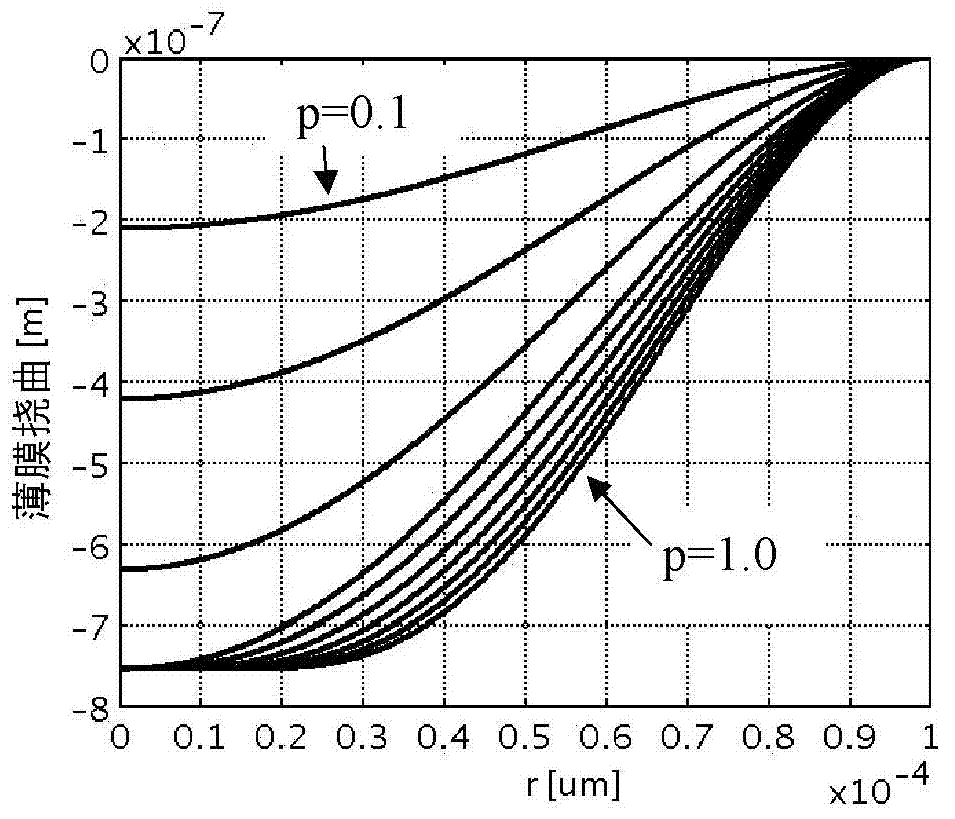
本發明涉及MEMS電容式壓力傳感器。
背景技術:MEMS壓力傳感器典型地具有壓阻式或者電容式讀出,并且是本領域公知的。在圖1中示出了電容式MEMS壓力傳感器一個示例的SEM橫截面。該圖示出了在犧牲層刻蝕以及用2μm厚PECVDSiN膜封閉所述刻蝕孔作為最后一級薄膜制造步驟之一之后的器件。所述傳感器具有懸置SiN薄膜。通過采用PEVCDSiN工藝氣密性地封閉在所述SiN薄膜下方的腔體。所述最終器件性能很大程度上由這個薄膜的幾何、物理、機械和結構特性決定。該薄膜的密度和組成確定所述氣密性、放氣行為和內部應力。所述應力與所述SiN厚度一起確定所述薄膜的剛度以及因此所述壓力傳感器的靈敏度。在醫療應用中的關鍵系統、替代能源、智能樓宇、引擎控制(例如燃氣和燃料進口壓力)和諸如輪胎監測系統的汽車安全應用需要壓力傳感器在其生命周期上提供準確且可預測的輸出,以便在這些變化變成臨界之前跟蹤操作變化。在20世紀70年代末,硅作為感測材料的出現開始影響工業和商業應用中的壓力測量。硅基傳感器使用后來被稱為MEMS(微機電系統)的技術。MEMS傳感器迅速地被應用在良好環境下的汽車和醫療應用中。由于體積小,在大量生產下它們相對低廉。盡管其他壓力感測技術,諸如薄膜、厚膜和陶瓷電容的發展,MEMS仍然是最廣泛使用的技術,并且注定成為新興市場,諸如替代能源、汽車和/或醫療應用中驅動力。隨著不斷的小型化,MEMS壓力傳感器在某種意義上也開始受到其小尺寸和制造方式的影響。例如,出現與不靈敏、不準確和信號漂移相關的問題。盡管正在采用現有技術的沉積工具和光刻技術,但是不能保證所有MEMS器件都被均勻地沉積或者具有相同的幾何尺寸。由于沒有兩個MEMS器件是完全相同的,需要有一些手段來校準它們,以便抵消那些不一致。因為在工業制造環境下測量單個器件參數是非常不切實際的,例如與外部施加力相關的撓曲(deflection)形狀,希望開發用于內部校準的方法,以便保證兩個MEMS器件以完全相同的方式作用或者測量。此外,需要自校準,因為微型器件可能會外露在惡劣的環境中或者長時間處于休眠狀態。在一些情況下,所述器件應當喚醒并且重新校準自己,以便將因溫度差異、所述氣體或者液體環境中的變化或者可能影響所述傳感器特性的其他條件造成的變化考慮在內。目前,大多數微機械壓力傳感器使用氣密性薄膜,所述薄膜密封參考腔體(referencecavity),所述參考腔體處在某個表壓(gaugepressure)(在一些情況下,表壓是真空)。測量外部壓力,因為外部壓力與表壓之間的壓力差在薄膜上產生作用力,造成了薄膜撓曲。然后由壓阻式、電容式或者光學傳感器測量這種撓曲。存在一些與這種常規的壓力傳感器設計相關的困難:參考腔體中的氣體壓力需要非常穩定,以便避免信號漂移。這要求非常高等級的氣密性,薄膜沒有釋氣。為了具有大的撓曲幅度和最佳的靈敏度,薄膜的厚度應當較小(或者它應當具有大的面積)。由于難以使非常薄的薄膜是氣密的,這些是矛盾的要求,并且導致較大的傳感器尺寸。如果參考腔體處在某個壓力,根據波義耳定律(Boyle’s)(P×V=n×R×T),這個壓力將是溫度依賴的。因此,傳感器變成溫度依賴的。壓力傳感器的靈敏度由薄膜變形的幅度確定,所述幅度進而由薄膜的厚度、直徑和屈服強度限定。對于具有電容式讀出的儀表,靈敏度還依賴于極板的分離。基于撓曲壓力傳感器的總動態范圍也由薄膜的最大撓曲限制。薄膜厚度、直徑和應力中的任何變化都會對所得到的薄膜撓曲輪廓具有顯著的影響,不僅影響絕對電容讀數,而且影響讀出的準確度和精確度。由于在制造期間的工藝變化,沒有兩個微觀結構具有相同的幾何尺寸和材料特性,這將會導致尺寸、質量、剛度中的小變化,而這將會顯著地影響性能。例如,如果薄膜包含壓縮和伸張層,薄膜厚度中10%的變化會造成微觀結構剛度和壓力靈敏度中50%-100%的變化。工藝變化使得企業難以準確地預測MEMS的性能并且在沒有逐個測量它們的情況下詳細說明性能。要求校準和頻繁的重新校準以便保證準確、可靠的輸出。目前,沒有方法在工業環境中執行自校準并且校正信號漂移。
技術實現要素:根據本發明,提供了一種壓力傳感器,包括:第一壓力傳感器元件,包括具有可變形上電極的電容式MEMS壓力傳感器,以及由第一腔體部分隔開的固定下電極,其中所述上電極響應于待感測的壓力而變形;以及第二壓力傳感器元件,包封在第二腔體部分內,其中所述第二腔體部分具有剛性的頂蓋,其中連接所述第一和第二腔體部分來限定組合的密封腔體,其中,所述傳感器還包括用于對所述第一和第二壓力傳感器元件輸出進行組合的裝置,使得所述第二壓力傳感器元件輸出提供所述第一壓力傳感器輸出的校準。這種結構提供了連接至所述電容式傳感器腔體的第二壓力傳感器。一個壓力傳感器是基于變形的檢測,而另一個是基于內部壓力。這個內部壓力變化遠小于所述外部壓力,并且所述內部壓力變化是體積變化的函數,所述體積變化由所述電容式傳感器電極的移動導致。因此,所述第二壓力傳感器同樣沒有測量外部壓力,但是它仍然可被用于提供所述主電容式傳感器的自動校準。更具體地,所述第二壓力傳感器元件性能將依賴于所述腔體的釋氣級別,并且因此可用于補償所述電容式壓力傳感器性能隨時間的變化。它也可以補償溫度的變化。所述第一和第二腔體部分可以并排地位于SOI襯底結構上,所述SOI襯底結構包括晶片、在所述晶片上的絕緣體層和在所述絕緣體層上的半導體層,并且所述腔體部分可以由在所述絕緣體層中形成的溝道連接。這樣,兩個壓力傳感器都可以利用共享的工藝步驟成為集成電路的一部分。每一個腔體部分均可以例如通過在所述硅層中形成的相應的通孔連接至所述溝道。所述第一腔體部分可以在所述半導體層上,以及所述第二腔體部分可以形成在所述半導體層中。然后所述壓力感測元件可以成為所述半導體層的一部分。在另外一種構造中,可以將所述第一和第二腔體部分組合在SOI襯底結構上相同的腔體中,所述SOI襯底結構包括晶片、在所述晶片上的絕緣體層和在所述絕緣體層上的半導體層。這樣,可以減小所述形狀因數(formfactor),同時兩個壓力傳感器都可以利用共享的工藝步驟成為集成電路的一部分。在另外一種構造中,可以將所述第一和第二腔體部分形成在CMOS電路上,例如讀出電路。這樣,由于在所述集成電路頂部的所述壓力傳感器功能的集成,可以減小所述形狀因數,同時兩個壓力傳感器都可以利用共享的工藝步驟成為集成電路的一部分。然后所述第一和第二腔體部分可以并排地位于所述CMOS集成電路上。所述CMOS集成電路的上金屬層可用于形成外部壓力傳感器接觸與所述內部壓力傳感器電極之間的電連接。在第一示例中,所述第二壓力傳感器元件包括皮拉尼壓力計(Piranigauge)。在第二示例中,所述第二壓力傳感器元件包括MEMS諧振器,其中使用所述諧振頻率或者所述諧振頻率的品質因數來確定壓力。本發明還提供了一種操作壓力傳感器的方法,包括:利用第一壓力傳感器元件測量外部壓力,所述第一壓力傳感器元件包括電容式MEMS壓力傳感器,所述電容式MEMS壓力傳感器具有可變形的上電極、以及由第一腔體部分隔開的固定下電極,其中所述上電極響應于待感測的壓力而變形;利用第二壓力傳感器元件測量內部腔體壓力,所述第二壓力傳感器包封在第二腔體部分內,其中連接第一和第二腔體部分來限定組合的密封腔體;對所述外部壓力和內部壓力測量進行組合,使得所述第二壓力傳感器元件輸出提供所述第一壓力傳感器輸出的校準。本發明還提供了一種制造壓力傳感器的方法。第一示例包括:提供SOI襯底結構,所述SOI襯底結構包括晶片、在所述晶片上的絕緣體層和在所述絕緣體層上的半導體層,形成第一壓力傳感器元件,所述第一壓力傳感器元件包括電容式MEMS壓力傳感器,所述電容式MEMS壓力傳感器具有可變形的上電極以及由第一腔體部分隔開的固定下電極,所述第一腔體部分在所述半導體層上;形成包封在第二腔體部分內的第二壓力傳感器元件,并且在所述第二腔體部分上形成剛性的頂蓋和在所述半導體層中形成第二腔體部分;以及通過在所述絕緣體層中形成的溝道連接所述第一和第二腔體部分來限定組合的密封腔體。第二示例包括:提供CMOS電路,所述CMOS電路包括具有多級互連結構的晶片;形成第一壓力傳感器元件,所述第一壓力傳感器元件包括電容式MEMS壓力傳感器,所述MEMS壓力傳感器具有可變形的上電極,以及由第一腔體部分隔開的固定的下電極,所述第一腔體部分在所述金屬互連結構上;形成包封在第二腔體部分內的第二壓力傳感器元件,以及在所述第二腔體部分上形成剛性的頂蓋;以及通過溝道連接所述第一和第二腔體部分來限定組合的密封腔體,其中所述互連結構用于形成至所述壓力傳感器元件的電連接的一部分。附圖說明現在將參考附圖詳細描述本發明的示例,其中:圖1示出了電容式MEMS壓力傳感器的一個示例的SEM截面圖;圖2示出了電容壓力傳感器的薄膜撓曲輪廓;圖3示出了作為所施加壓力函數的所述電容;圖4示出了作為所施加外部壓力函數的所述腔體體積減小和壓力增加;圖5示出了作為所施加外部壓力函數的電容和靈敏度的FEM仿真;圖6示出了對于皮拉尼傳感器三種不同構造的歸一化電阻變化;圖7示出了作為諧振器壓力函數的諧振頻率;圖8示出了在SOI中制造的具有壓阻讀出的狗骨頭狀諧振器的示意性頂視圖;圖9示出了在SOI中制造的具有壓阻讀出的狗骨頭狀諧振器的SEM橫截面;圖10示出了作為壓力函數的諧振器諧振頻率的品質因數;圖11示出了狗骨頭狀諧振器平面外運動;圖12A至12K示出了用于制造電容式壓力傳感器的示范性工藝流程的連續步驟,所述電容式壓力傳感器包括皮拉尼壓力計或者諧振器;圖13示出了作為退火溫度函數的從PECVDSiNx:Hy膜的氫水滲出;圖14示出了在封裝之后具有PVDAl插頭SiN覆蓋腔體中壓力的累積分布;圖15A至15G示出了用于制造電容式壓力傳感器的示范性工藝流程的連續步驟,所述電容式傳感器包括在CMOS電路頂部上的皮拉尼壓力計;以及圖16示出了具有所施加壓力并且對于皮拉尼壓力計版本的圖12K的設計。具體實施方式本發明提供了一種能夠執行自校準并且校正信號漂移的壓力傳感器。通過利用電容式讀出方法測量薄膜的撓曲,來感測外部介質與腔體之間的壓力差。存在兩種方式實施本發明。一種方式涉及集成皮拉尼傳感器的使用,以及另一種方式涉及集成諧振器的使用,用作參考壓力傳感器。從1906年發明至今,皮拉尼壓力計已經被廣泛地用于真空測量。具有高電阻溫度系數的加熱導線被放置在真空環境下。導線(其電阻與其溫度成正比,)形成平衡惠斯通電橋的一個臂。氣體分子與導線碰撞,從導線傳遞熱量并且使電橋相對于參考狀態不平衡。由于分子碰撞頻率與氣體壓力成正比,因此維持電橋平衡所需的電壓與壓力成正比。由于其可靠性、低成本和相對廣泛的壓力范圍,皮拉尼壓力計已經成為一個行業標準。能夠監測真空等級的微皮拉尼傳感器已經是深入的研究工作的主題。與基于皮拉尼壓力計的傳統細絲相比,它們具有尺寸小、成本低、響應快和壓力感測范圍大的優勢。基于SOI的工藝過程允許長且薄的結構,對測量低氣壓是必要的。傳感器例如可以設置作為導線,在導線與側面熱沉之間具有間隙。在根據本發明的第一示例中,將具有氣密性密封腔體的電容式壓力傳感器與連接至相同腔體或者在相同腔體內的微皮拉尼壓力計組合。然后利用自由懸掛結構(即具有或者沒有散熱片的導線或者Si梁)的電阻來測量內部壓力。從這個結構至周圍氣體的熱傳導依賴于結構周圍的氣體壓力。如果由于釋氣或者由于氣密性密封腔體內部氣體的壓縮導致內部壓力有變化,那么可以通過電阻變化來感測。利用腔體內部皮拉尼壓力計的目的是針對內部壓力變化(例如由于釋氣、溫度或者由于壓縮)而校正薄膜電容測量。可以利用惠斯通電橋構造作為讀出來校正由于外部溫度變化所導致的皮拉尼壓力計內電阻變化。如果獨立地測量芯片上溫度,不僅可以補償導線的電阻變化,還可以補償腔體內的體積膨脹/壓力增加。在根據本發明的第二示例中,將具有氣密性密封腔體的電容式壓力傳感器與在相同腔體內的諧振器組合。然后利用諧振結構的頻率偏移/品質因數測量內部壓力。如果由于釋氣或者由于氣密性密封腔體內部氣體的壓縮內部壓力有變化,那么可以通過諧振頻率的峰加寬來感測。利用內部諧振器的目的再次是針對內部壓力變化(例如由于釋氣、溫度或者由于壓縮)來校正薄膜電容測量。如果將參考諧振器構建在獨立的腔體中,那么可以差分地測量主諧振器的諧振頻率,使得諧振頻率的環境溫度依賴性不會限制準確度。在這兩種情況下,由于例如不均勻的薄膜厚度、應力和釋氣所造成的工藝過程條件變化將導致撓曲輪廓中的較大展寬,并且因此可以利用芯片上加工分別地確定和校準。目前,大多數微機械壓力傳感器利用氣密性密封參考腔體的薄膜,腔體處在某個表壓下。測量外部壓力,因為在外部壓力與內部表壓之間的壓力差在薄膜上產生一個作用力,造成了薄膜撓曲。理想地,內部參考壓力是真空,這樣可以抵消內部腔體壓力的影響。然后利用反電極以電容的方式測量薄膜撓曲。在圖2中,根據有限元模型(FEM)仿真,將用于電容式壓力傳感器的薄膜撓曲輪廓表示為壓力的函數。壓力從上到下以0.1巴的步長從0.1巴增加至1巴(以10kPa的步長從10kPa增加至100kPa)。對于750nm的間隙,薄膜“倒塌”發生在0.35巴(35kPa)。腔體內的壓力為零并且假定沒有殘余應力。在某個壓力下,上薄膜將開始接觸腔體的底部。對于所建模的半徑為100μm、厚度為1.5μm的SiN薄膜,在0.35巴(35kPa)下已經發生這種情況。在圖3中,描述了電容作為所施加壓力的函數,表示出當撓曲薄膜接近下電極時非線性的C~1/P行為以及在下降階段薄膜“向下接觸”之后差不多線性的C~P行為。從該圖可以明顯看出,就在“向下接觸”之前壓力靈敏度最大(較大C-P斜率)。圖3再次涉及厚度為1.5μm、間隙為750nm、半徑為100μm的SiN薄膜(楊氏模量為250GPa、泊松比為0.23)。在電極之間是εr=6的200nm的SiN電介質層。可以設計膜片尺寸,以便設定壓力范圍。下面給出了對于圓形薄膜的撓曲作為壓力、薄膜厚度、薄膜半徑和間隙高度的函數的關系式。在抗撓剛度支配機制中作為壓力P的函數的圓形薄膜的撓曲w(r)由下式給出:其中,R是薄膜的半徑,r是從邊緣至實際撓曲點的距離,v是泊松比,E是楊氏模量,h是薄膜厚度。從上述關系式中可以看出,撓曲與R4和1/h3成正比。薄膜厚度和/或尺寸中的較小變化已經對撓曲輪廓產生巨大影響。這個關系對沒有任何內部應力的薄膜是有效的。如果考慮內部應力,薄膜變得更硬并且達到接觸點的壓力變得更大。如果在腔體內部存在某個殘余壓力,根據波義耳定律內部壓力將與體積變化成反比變化。例如考慮直徑為75μm、高度為500nm的腔體,腔體由2.2μm厚的SiN薄膜覆蓋。其體積為~9000μm3,在1巴(100kPa)的外部壓力下(假定腔體真空),體積減小至~7600μm3。這由圖4中的圓圈表示,示出了對于腔體真空腔體體積減小作為所施加外部壓力的函數。輸入參數為厚度為2.2μm、半徑為75μm的SiN薄膜(楊氏模量為220GPa、泊松比為0.3),間隙高度為500nm。如果在腔體中的殘余氣體壓力是100毫巴(10kPa)而不是真空(用外部真空測量),那么如果施加1巴(100kPa)的外部壓力,該氣壓將上升至120毫巴(12kPa)。這也在圖4中利用三角形點示出,表示了對于100毫巴的初始壓力(10kPa,并且是對于所施加外部壓力為0.0巴的壓力)的內部壓力變化。如果在腔體中的壓力隨時間變化不是恒定的,例如由于釋氣,那么薄膜將經受對抗外部施加壓力的額外的但是未知的作用力。如果在校準期間不考慮腔體內部的壓力增加(在上述示例中為100毫巴(10kPa))的影響,那么誤差隨壓力而增大。例如,由于薄膜撓曲,內部壓力在1巴下增加至120毫巴(12kPa)以及在2巴(200kPa)下增加至145毫巴(14.5kPa)。如果沒有在受控環境中規律地校準傳感器,那么這會導致隨時間變化的不可接受的信號漂移。在實際日常生活的情況下,難以執行傳感器校準,因為通常不能將傳感器從其環境中取出(例如醫學植入、汽車壓力傳感器等)。此外,如果腔體內部的氣體由于溫度增加而膨脹,那么如果內部壓力是未知的,將不能校正影響。校準為潛在的信號漂移提供了解決方法。出于這個原因,在校準程序中確定薄膜的初始狀態和撓曲行為并且時常檢查是否發生任何變化是重要的。在標準校準期間,會向薄膜施加幾個參考壓力,并且會測量電容。校正和校準參數會從測量結果中提取并且被存儲在芯片上的存儲器中或者會修整(trim)電路元件。這些校準數據例如可以由在適當的壓力感測范圍內獲取的電容-電壓(C-P)數據點組成。典型地,需要三個或者更多的C-P點,以便通過數據點推導高階多項式擬合。因為C-P關系是非線性的(參見下面的公式),那么校準點越多,多項式擬合就會越準確。其他的校準可能性例如是電容電壓(C-V)掃描。這種掃描包括在不同偏置電壓下準確的電容測量。通常,在+20與-20V之間以1V的間隔繪制C-V曲線。由于靜電引力,薄膜朝向另一個電極撓曲,隨著電壓偏置增大(負或正)而增大電容。可以利用通過C-V數據擬合來推導薄膜柔量,薄膜柔量是薄膜壓力靈敏度的一個量度。C-V校準方法是一種相對快速的校準方法,可以在不使用專...