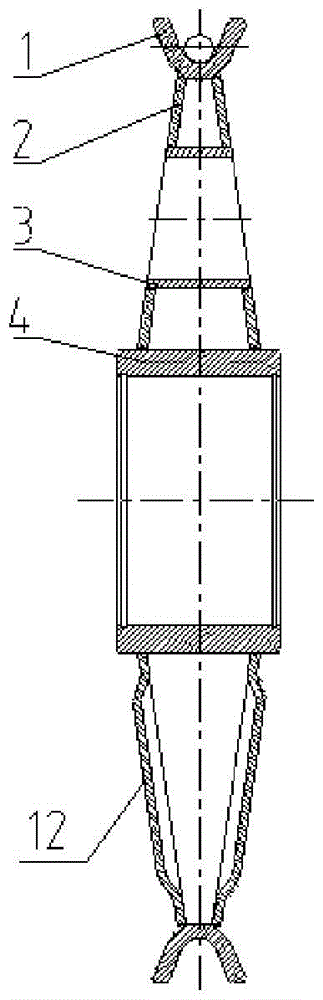
本發明屬于機械技術領域,涉及滑輪裝置。
背景技術:眾所周知,滑輪為鋼絲繩的伴生物,鋼絲繩依靠滑輪支承實現各種運動。根據相關資料,世界鋼產量的0.3%用于制造鋼絲繩(400萬噸左右)。由此可以推知,盡管滑輪為耐用工業品,不似鋼絲繩那樣需定期更換,但每年世界上在用的滑輪仍是個巨大數字,數量上以百萬只計,每年還要增加數十萬只,僅我國年需大中型滑輪(暫不計小滑輪、塑料滑輪)二十萬只以上。現有各種滑輪雖基本勝任不同工況工作,但存在以下共同缺點:與鋼絲繩伴生的滑輪“必須定期加油維護”已成為300年來金屬滑輪問世后人們的習慣之舉。至今,對滑輪軸承定期維護、加潤滑脂脂,仍被工程技術人員視為“理所當然”,視為是減小滑輪運行阻力、延長滑輪壽命的必須手段,對滑輪的例行保養受客觀條件制約(例如高空、起重臂端頭、狹窄處等),作業具有一定難度。因此,如何提高滑輪質量,延長其使用壽命,減少其維護保養工作量是業內研究者多年來不斷研究的課題。
技術實現要素:本發明的目的主要是提供一種免維護的滑輪裝置,維護保養工作量小,工作壽命長。為了達到上述目的,本發明的解決方案是:一種免維護的滑輪裝置,包括從內到外依次連接的均為環狀的端蓋、輪轂、兩塊腹板和繩槽;還包括位于所述端蓋的內圈以內的軸,支撐所述軸的軸承以及定位所述軸承的內圈支套;所述兩塊腹板處于所述滑輪裝置的兩側面的位置,且在所述滑輪裝置上處于相同的徑向位置;所述輪轂與所述端蓋通過金屬圈(例如不銹鋼絲圈)固定,所述端蓋的外圈與所述輪轂連接;所述輪轂、端蓋、內圈支套與軸構成的內腔中充滿潤滑脂,以形成封閉結構。所述端蓋的內圈與所述內圈支套之間具有不大于0.1毫米的間隙。腹板上設有補油孔,五年后通過該補油孔補油一次可繼續使用到十年。經過大量實驗及實踐發現,滑輪繩槽的磨損原因有四:其一是繩與槽表面有微滑動,鋼繩如銼一樣損傷繩槽表面;其二是槽形與理論值有較大誤差;或是槽型的端跳徑跳偏大;其三是材質疏松,抗重壓能力差,鑄鉄鑄鋼絲滑輪往往如此;其四是鋼繩的進入或引出滑輪的偏角過 大。客觀上需要減少滑輪繩槽的磨損,以使它與滑輪軸承壽命相匹配。為此,本發明采取了如下的提高質量減小滑輪繩槽磨損的措施:其一是提高繩槽硬度,首先改變繩槽材料(例如采用Q345、Q35CrMo等),并進行熱處理,滑輪繩槽表面硬度為HB160~260或HRC30~62,一般選擇HB220-260,進一步可以選擇HRC45-48或HRC58-62,根據滑輪的不同工況選擇不同的硬度以提高繩槽的抗磨損能力;其二是繩槽均經過機加工,實現徑向跳動小于1/1000直徑和端跳小于1/2000直徑,并保證繩槽形狀和光潔度滿足行業標準。其三是限制偏角;眾所周知:滑輪的線速度隨半徑的加大而變大,但鋼繩只有一個固定的線速度,此偏角加大,將造成繩與繩槽內端面接觸,滑動加大而劇烈磨損。這個問題如果不加以解決,滑輪邊緣磨損將很快,像個環形刀口,最終造成提前報廢。優選的,限制繩的偏角不得大于2度,減少繩與滑輪槽內壁端面的滑動,減少繩槽磨損,延長繩槽壽命。所述潤滑脂為具有抗氧化能力的潤滑脂。所述潤滑脂的錐入度為150到170。由于采用上述方案,本發明的有益效果是:本發明免維護的滑輪裝置采用上述方案,能夠有效實現免維護功能,一次性加滿潤滑脂,至少可以5年不需要更換。腹板上設有補油孔,五年后補油一次可延長到十年。由于繩槽采用機加工并使表面硬化,所以繩槽承載抗磨損能力大大提高,且會減少對鋼絲繩的磨損,因此可以延長滑輪以及鋼絲繩的使用壽命。附圖說明圖1a是本發明實施例中滑輪結構的主視圖;圖1b是本發明實施例中滑輪結構的側視圖;圖2是本發明實施例中繩槽精度測量示意圖;圖3a是本發明實施例中免維護的滑輪裝置的主視圖;圖3b是本發明實施例中免維護的滑輪裝置的側視圖;圖3c是圖3b中所圈部分的放大圖;圖4是本發明實施例中免維護的滑輪裝置安裝在滑輪架上的示意圖。附圖說明:1、繩槽;2、腹板;3、穿管;4、輪轂;5、端蓋;6、螺釘;7、內圈支套;8、軸承;9、閉鎖鋼絲圈;10、軸承隔套;11、軸;12、凸筋;13、滑輪架。具體實施方式以下結合附圖所示實施例對本發明作進一步的說明。本發明提出了一種免維護的滑輪裝置,該滑輪裝置包括滑輪結構和與其配合的軸等部件。 圖1a是該滑輪裝置中滑輪結構的主視圖,圖1b是其剖視圖。該滑輪結構包括均為環狀的輪轂4、腹板結構2和繩槽1。輪轂4、腹板結構2和繩槽1從內到外依次嵌套并焊接連接。繩槽1同樣為環狀體結構,其內圈的半徑等于腹板結構2的外圈的半徑。繩槽1的截面則為U型,且U型開口朝外,U型底部焊接連接腹板結構2的外圈面,因此該繩槽1具有朝向外側的槽體,以用于容納繩體。繩槽1適合直徑從到(單位為毫米)的鋼絲繩,繩槽直徑和鋼絲繩直徑的比不小于30,其張開度約為50度,符合國家標準。繩槽1的硬度則根據載荷和不同工況的耐磨要求,通過不同材料和熱處理工藝得到。本實施例中,該繩槽根據滑輪的不同工況選擇不同的硬度,通過熱處理,其表面硬度達到HB220-260,進一步可以選擇HRC45-48或HRC58-62,以提高繩槽的抗磨損能力。本發明免維護的滑輪裝置除了包含上述滑輪結構外,還包括處于輪轂4的內圈之內的環狀的端蓋5、位于端蓋5的內圈以內的軸11,支撐該軸11的軸承8以及定位該軸承8的內圈支套7。圖3a是該裝置的主視圖;圖3b為其側視圖;圖3c為圖3b中所圈部分的放大圖。從中可以看出,兩個端蓋5的外圈均連接輪轂4,內圈與內圈支套7之間具有不大于0.1毫米的間隙;具體為端蓋5靠近輪轂4的外圈與輪轂4靠近內圈含有安裝槽,通過在該安裝槽中設置環狀不銹鋼絲連接端蓋5和輪轂4。從而,輪轂4、端蓋5、內圈支套7和軸11包圍構成具有內腔的結構;軸承8位于該內腔內。本實施例中,共包含兩個軸承8,軸11位于這兩個軸承8上,這兩個軸承8之間用軸承隔套10隔開。為了降低上述滑輪裝置的維護難度和成本,本實施例采取的措施是最大限度地封閉其形成的內腔。還在該內腔(包括上述間隙)中注滿潤滑脂,該潤滑脂的錐入度為150到170。鑒于世界起重運輸機械現用滑輪的速度不高,基本都在100轉每分鐘左右,屬于低速型,運行時內部生熱很小,所以采用錐入度為150左右的潤滑脂即可實現本發明所需的封閉程度。傳統滑輪在軸和輪轂上均設有注油孔,通過注油孔更換潤滑脂。本實施例中,為了提高滑輪裝置的密封性,輪轂4為實體結構,與輪轂4配套使用的軸11亦為實體結構,在輪轂4和軸11上均沒有注油孔。該滑輪裝置的注油孔設置在端蓋5中,為端蓋5上設置的通孔,并通過螺栓封堵,用于供大修和清洗時使用。除了在密封性上的改善外,不設注油孔使得本實施例中輪轂4和軸11的生產工藝更為簡單,將注油孔設置在端蓋5上使得油路距離短,方便沖油。上述滑輪裝置中,端蓋密封,不采用橡膠件,因而沒有老化問題;不用螺釘緊固,而是用不銹鋼絲圈固定,因而結構極為緊湊。同時,輪轂、端蓋以及軸組成的內腔與外部空氣基本隔離,使得灰土、濕氣、鹽霧等難以進入。此外,該裝置內部填滿潤滑脂,基本無空腔,因此當溫度變化時,不會因為空氣的呼吸作用而帶入灰塵、濕氣、鹽霧等。也正是基于上述結構,該裝置干凈且環境友好。該滑輪裝置在生產時,一次充足潤滑脂,使之可持續工作5年,具有免維護的優點,大大節約了維護產生的成本。綜上,該滑輪裝置裝有滾動軸承的滑輪輪轂對外界基本密閉,令輪轂內外的空氣不交換, 使灰土、粉塵和鹽霧不得入侵輪轂內,當晝夜溫差較大時,亦不會結露。所采用的措施包括:(1)盡量減小輪轂與軸的間隙,例如于小于0.1毫米;(2)在滑輪輪轂內、端蓋、內圈支套與軸構成的內腔中充滿有添加劑抗氧化能力極強的潤滑脂以形成封閉結構;(3)出廠前完成無空腔密閉式裝配;滑輪結構中繩槽按照需要具有合適的硬度和精度,具有良好的抗磨損能力,使用壽命較長。上述的對實施例的描述是為便于該技術領域的普通技術人員能理解和應用本發明。熟悉本領域技術的人員顯然可以容易地對這些實施例做出各種修改,并把在此說明的一般原理應用到其他實施例中而不必經過創造性的勞動。因此,本發明不限于這里的實施例,本領域技術人員根據本發明的揭示,不脫離本發明范疇所做出的改進和修改都應該在本發明的保護范圍之內。