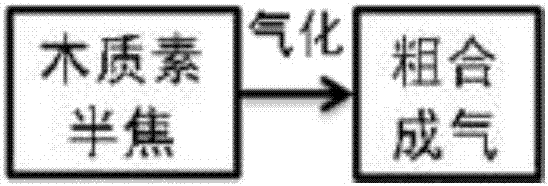
本發明涉及一種生物化工技術,具體說,涉及一種生物基聚α-烯烴合成油的制備方法
背景技術:
:人類使用潤滑劑的歷史本身就是一部社會發展史,從早期簡單地使用環境無害的動植物油脂潤滑劑,發展到大量使用以石油基油為代表的各種高性能的、但對環境有害的潤滑劑,進而尋求現代潤滑的新理念—“潤滑+環保+節能”。現代工業對潤滑劑提出寬溫域、低摩阻、高耐磨、長壽命、環境友好等要求。目前使用的礦物基潤滑劑都有一個共同特點,即由于需求不斷提高,都已達到它們的使用性能極限,經常出現過早磨損破壞、壽命短、能源消耗多、廢液處理難。合成潤滑劑是由種類不同的分離的化合物化學合成的潤滑劑。在滿足嚴格的規格要求和保持對設備防護、環境保護、健康安全的挑戰中,使用合成潤滑劑是最好的方法,可以達到“潤滑+環保+節能”的目的。潤滑油基礎油按api(美國石油學會)分類,劃分為五大類(i、ii、iii、iv、v類),其中,i、ii、iii類為礦物油,iv為聚α-烯烴合成油,v類為其他合成潤滑油。聚α-烯烴合成油先期采用乙烯齊聚和蠟裂解合成法,產品的性能并不太好,粘度指數達到100以上;后來采用費托合成的高級烯烴聚合物,如1-癸烯,碳十二烯,碳十四烯等進行熱聚合,產品的性能比較理想,粘度指數達到150以上。生產商主要集中在美、歐、南非和日本等國家和地區。費托合成的合成氣原料一般來自于煤、天然氣及石油。用木質纖維原料直接生產生物合成氣,因物料熱值低,導致氣化溫度低,氣化過程中產生焦油,堵塞管道,所以至今無成熟的大型連續化氣化設備。而將木質纖維類生物質轉變成木質素半焦后,其熱值接近標煤、碳含量超過90%,可以采用大型煤氣化設備進行氣化,間接地打通了生物質氣化的路徑,具有原料成本低、無需預處理、氣化工藝成熟等特點,可實現生物合成氣的商業化運營。木素基合成氣采經費托合成、聚合、烷基化等工藝生產聚α-烯烴,原料無硫環保、工藝成熟、設備投資少、變換工藝簡單等特點,綜合費效比優于化石基原料氣。聚合工藝所用的催化劑包括齊格勒催化劑、三元催化劑(由堿金屬的氫化物,與鋁及鈦的鹵化物組成)或弗瑞德-克拉夫茲催化劑(bf3,alcl3,sncl4,snf4)等,大都存在過程污染現象。技術實現要素:本發明所解決的技術問題是提供一種生物基聚α-烯烴合成油的制備方法,具有原料廉價易得,過程綠色,產品性能可靠等特點,適合工業化生產。技術方案如下:一種生物基聚α-烯烴合成油的制備方法,包括:木質纖維原料經水解后得到木質素半焦,木質素半焦中,半焦的重量百分含量為88-92%,灰分的重量百分含量為8-12%;木質素半焦氣化得到粗合成氣;粗合成氣經變化、洗脫工藝生產合成氣;合成氣費脫合成生產初餾分;初餾分經兩段聚合、烷基化工藝生產生物基聚α-烯烴合成油。進一步,木質素半焦的生產過程包括:木質纖維原料的第一階段水解,將木質纖維原料中的半纖維素轉化為低聚木糖;第一階段水解:溫度為200-240℃、壓力為2.2-2.4mpa,時間0.5-5分鐘,反應將木質纖維原料中的半纖維素轉化為低聚木糖;木質纖維原料的第二段水解,將木質纖維原料中的纖維素轉化為纖維低聚糖;第二階段水解:溫度為180-200℃、壓力為1.4-1.6mpa,時間10-30分鐘,反應將木質纖維原料中的纖維素轉化為纖維低聚糖。木質纖維原料的第三階段水解,乙酸為催化劑,溫度為180-200℃,壓力為1.4-1.6mpa,時間5-20分鐘,木質素轉化為木質素半焦。進一步,木質素半焦氣化得到粗合成氣的生產過程包括:以木質素半焦為原料,采用航天爐氣化裝置,空分裝置產量為52000nm3/h,氧提取率超過90%,氣化劑為99.6%的純氧;進料方式為半焦干粉進料,輸送氣體為co2,送入燒嘴自上而下單噴嘴噴射入氣化爐,氣化溫度為1250-1450℃,壓力為3-3.5mpa,生成的粗合成氣和熔渣經水激冷后排渣,粗合成氣在激冷室上部排出,經進一步冷卻、除塵后進入后續工序。進一步,粗合成氣經變化、洗脫工藝生產合成氣的生產過程包括:粗合成氣經水蒸氣變換反應裝置調整h2和co的比例為1.3-1.5,采用鐵為催化劑,壓力0.8-1mpa,反應溫度為220-280℃,生成的變換氣成為:33-39%h2、26-28%co、33-35%co2;變換氣再經低溫甲醇洗工藝脫除co2氣體,將氣體冷卻至10℃進入氨洗塔以降低nh3和hcn含量,然后在溫度-21℃,壓力3.43mpa下噴入co2吸收塔,用-53℃的甲醇吸收co2,得到合成氣。進一步,合成氣費脫合成生產初餾分采用漿態床f-t反應器,原料為合成氣,催化劑為鐵系催化劑,反應溫度230-250℃,壓力2.5-3.5mpa;反應生成初餾分。進一步,初餾分經兩段聚合、烷基化工藝生產生物基聚α-烯烴合成油的步驟包括:一段聚合生產低聚物;原料為初餾分,采用聚合反應釜,包括第一段聚合反應,催化劑為三氟甲磺酸基復合催化劑,用量1-2wt%,反應溫度為50-80℃,壓力為0.1-0.3mpa;反應時間1-2h,一段聚合反應結束后油品進入分離裝置進行分離;分離工藝分為兩段,首段為低溫結晶,溫度為-30℃,固體析出物(c11以上烷烴組分)經過濾工藝除去;次段分離為蒸餾提純,溫度為180℃,蒸出餾分為c10以下烷烴;經兩段分離工藝提純后得到低聚物;二段聚合生產高聚物;以低聚物為原料進行第二段聚合反應,正丁醇為引發劑,氮氣置換后開始反應,反應溫度為150-200℃,壓力為0.3-0.5mpa;時間4-6h,催化劑為三元催化劑,用量1-2wt%,得到高聚物;高聚物含有雙鍵,通過異構烷烴烷基化反應加以飽和;異構烷烴為異戊烷,在釜式反應器內和高聚物進行反應,反應溫度為100-200℃,壓力為1-3mpa,催化劑用量1-2wt%,混合烴和聚α-烯烴摩爾比8-15:1,反應時間1-2h;烷基化反應結束后經減壓蒸餾除去未反應物,得到生物基聚α-烯烴合成油成品。進一步:三元催化劑選用氫氧化鑭、鈰混合物/鉻-硅復合催化劑,異構烷烴烷基化反應的催化劑為三氟甲磺酸基復合催化劑。進一步:乙酸濃度為95%wt,乙酸用量為原料總重量的0.5-0.8%。與現有技術相比,本發明技術效果包括:本發明利用木質纖維原料經管族梯級減壓連續水解工藝生產的木質素半焦為原料,經半焦氣化、費托合成、兩段聚合、烷基化反應生產生物基聚α-烯烴合成油,具有原料廉價易得,過程綠色,產品性能可靠等特點,適合工業化生產。(1)利用木質纖維(城市園林綠地剩余物、農林廢棄物、資源作物等)原料,廉價易得,多為廢棄資源,屬廢物利用。(2)采用管族梯級減壓連續水解工藝將半纖維素、纖維素和木質素分別轉化為低聚木糖、纖維低聚糖和木質素半焦,實現木質資源全組分利用。(3)木質素半焦熱值為5500-6500大卡,接近標煤,并且無硫,有助于其實現在煤氣化裝置的直接利用,大大減少設備投資。(4)利用木質素半焦生產生物基聚α-烯烴合成油,原料無硫,工藝成熟,設備投資少,變換工藝簡單等特點,綜合費效比優于化石基原料氣。(5)木質素半焦生產生物合成氣關鍵技術。采用航天爐氣化裝置,半焦尺寸顆粒為40-90μm,可直接采用干粉進料,氣化溫度1350-1500℃,同時實現熱效率95%和碳轉化率99%,生產的合成氣co+h2≥93%,技術成熟,產品穩定。(6)初餾分烷基化關鍵技術。利用異戊烷和異丁烷混合烴進行烷基化反應,采用新型催化劑三氟甲磺酸基復合催化劑,可實現烷基化反應過程綠色、產物分離提純簡單、反應轉化效率高等特點。(7)α-烯烴合成聚α-烯烴關鍵技術采用兩段聚合反應,分別采用新型催化劑三氟甲磺酸基復合物和氫氧化鑭、鈰混合物/鉻-硅復合物,用量1-2wt%。α-烯烴轉化率可達99%。雙鍵去除改變傳統選擇性加氫這一高危、高能耗和低效率處理方式,反而選擇同異戊烷和異丁烷混合烴進行烷基化反應,大大降低能耗、提高安全系數和效率,產品穩定。附圖說明圖1是本發明中木質纖維原料經管族梯級減壓連續水解后得到木質素半焦的工藝路線圖;圖2是本發明中木質素半焦氣化得到粗合成氣的工藝路線圖;圖3是本發明中粗合成氣經變化、洗脫工藝生產合成氣的工藝路線圖;圖4是本發明中合成氣費脫合成生產初餾分的工藝路線圖;圖5是本發明中初餾分經兩段聚合、烷基化工藝生產生物基聚α-烯烴合成油的工藝路線圖。具體實施方式下面參考示例實施方式對本發明技術方案作詳細說明。然而,示例實施方式能夠以多種形式實施,且不應被理解為限于在此闡述的實施方式;相反,提供這些實施方式使得本發明更全面和完整,并將示例實施方式的構思全面地傳達給本領域的技術人員。如圖1所示,是本發明中木質纖維原料經管族梯級減壓連續水解后得到木質素半焦的工藝路線圖。生物基聚α-烯烴合成油的制備方法,具體包括以下步驟:步驟1:木質纖維原料經管族梯級減壓連續水解后得到木質素半焦(含有成分的百分比:半焦含量88-92%,灰分含量8-12%,熱值5500-6500大卡);步驟11:木質纖維原料的第一階段水解,將木質纖維原料中的半纖維素轉化為低聚木糖;第一階段水解:溫度為200-240℃、壓力為2.2-2.4mpa,時間0.5-5分鐘,反應將木質纖維原料中的半纖維素轉化為低聚木糖。步驟12:木質纖維原料的第二段水解,將木質纖維原料中的纖維素轉化為纖維低聚糖;第二階段水解:溫度為180-200℃、壓力為1.4-1.6mpa,時間10-30分鐘,反應將木質纖維原料中的纖維素轉化為纖維低聚糖。步驟13:木質纖維原料的第三階段水解,將木質纖維原料中的木質素(纖維低聚糖、低聚木糖)轉化為木質素半焦。濃度95%wt乙酸催化劑(乙酸用量為原料總量的0.5-0.8%),溫度為180-200℃,壓力為1.4-1.6mpa,時間5-20分鐘,木質素轉化為木質素半焦。半焦木質素顆粒尺寸(μm)含水量(wt%)含碳量(%)40-902-590-95如圖2所示,是本發明中木質素半焦氣化得到粗合成氣的工藝路線圖。步驟2:木質素半焦氣化得到粗合成氣;以木質素半焦為原料,采用航天爐氣化裝置,空分裝置產量為52000nm3/h,氧提取率超過90%,氣化劑為99.6%的純氧。進料方式為半焦干粉進料(40-90μm顆粒),輸送氣體為co2,輸送壓力為4.0mpa,送入燒嘴自上而下單噴嘴噴射入氣化爐,氣化溫度為1250-1450℃,壓力為3-3.5mpa,生成的粗合成氣和熔渣經水激冷后排渣,粗合成氣在激冷室上部排出,經進一步冷卻、除塵后進入后續工序。粗合成氣主要組分為:coh2co2ch4硫化物59-61%31-33%4-8%0.1%-0.5%小于0.05ppm如圖3所示,是本發明中粗合成氣經變化、洗脫工藝生產合成氣的工藝路線圖。步驟3:粗合成氣經變化、洗脫工藝生產合成氣;粗合成氣經水蒸氣變換反應裝置調整h2和co的比例為1.3-1.5,采用鐵為催化劑,壓力0.8-1mpa,反應溫度為220-280℃;生成的變換氣基本參數如下:流量178000m3/h,溫度40℃,壓力3.5mpa,氣體組成為:33-39%h2、26-28%co、33-35%co2。變換氣再經低溫甲醇洗工藝脫除co2氣體,將氣體冷卻至10℃進入氨洗塔以降低nh3和hcn含量,然后噴入co2吸收塔(溫度-21℃,壓力3.43mpa)用甲醇(-53℃)吸收co2,得到合成氣。反應方程式如下:ch4+h2o→co+h2co+h2o→co2+h2合成氣氣體成分如下:coh2co2硫化物40-41.4%58-59%小于0.064小于0.05ppm如圖4所示,是本發明中合成氣費脫合成生產初餾分的工藝路線圖。步驟4:合成氣費脫合成生產初餾分;采用漿態床f-t反應器,原料為合成氣,催化劑為中科icc-ii型鐵系催化劑,反應溫度230-250℃,壓力2.5-3.5mpa;反應生成初餾分。反應方程式如下:nco+2nh2→cnh2n+nh2o2nco+nh2→cnh2n+nco23nco+nh2o→cnh2n+2nco2nco2+3nh2→cnh2n+2nh2o初餾分(c5-c16為主)組成如下:總烯烴總烷烴含氧化合物56-62%35-38%2-4%如圖5所示,是本發明中初餾分經兩段聚合、烷基化工藝生產生物基聚α-烯烴合成油的工藝路線圖。步驟5:初餾分經兩段聚合、烷基化工藝生產生物基聚α-烯烴合成油。反應物為初餾分,包括:步驟51:一段聚合生產低聚物:原料為初餾分,采用聚合反應釜,包括第一段聚合反應,催化劑為三氟甲磺酸基復合催化劑,用量1-2wt%,反應溫度為50-80℃,壓力為0.1-0.3mpa;反應時間1-2h,一段聚合反應結束后油品進入分離裝置進行分離;步驟52:分離工藝分為兩段,首段為低溫結晶,溫度為-30℃,固體析出物(c11以上烷烴組分)經過濾工藝除去;次段分離為蒸餾提純,溫度為180℃,蒸出餾分為c10以下烷烴;經兩段分離工藝提純后得到低聚物;步驟53:二段聚合生產高聚物:以低聚物為原料進行第二段聚合反應,正丁醇為引發劑,氮氣置換后開始反應,反應溫度為150-200℃,壓力為0.3-0.5mpa;時間4-6h,催化劑為三元催化劑(氫氧化鑭、鈰混合物/鉻-硅復合催化劑),用量1-2wt%。α-烯烴轉化率為99%,得到高聚物;步驟54:上述高聚物含有雙鍵,通過異構烷烴烷基化反應加以飽和。異構烷烴為異戊烷,在釜式反應器內和高聚物進行反應,反應溫度為100-200℃,壓力為1-3mpa,催化劑為三氟甲磺酸基復合催化劑,用量1-2wt%,混合烴和聚α-烯烴摩爾比8-15:1,反應時間1-2h。烷基化反應結束后經減壓蒸餾除去未反應物,得到生物基聚α-烯烴合成油成品。反應方程式如下:聚合反應烷基化反應生物基聚α-烯烴性能指標如下表:聚α-烯烴油技術條件及試驗方法實施例1:(1)200kg玉米秸稈(含水率25%)粉碎至1cm以下,進入管族梯級減壓連續水解反應器,包括第一階段水解:溫度為205-210℃、壓力為2.2-2.3mpa,時間3分鐘,秸稈中的半纖維素轉化為低聚木糖滲濾出來;纖維素和木質素進入第二階段水解:溫度為180-185℃、壓力為1.4-1.5mpa,時間20分鐘,將秸稈中的纖維素轉化為纖維低聚糖滲濾出來;木質素進入第三階段水解:95%wt乙酸催化劑,溫度為180-185℃、壓力為1.4-1.5mpa,時間10分鐘,木質素轉化為木質素半焦114.2kg(含水37-40%)。(2)以72kg干木質素半焦為原料(含水2-5%),采用航天爐氣化裝置,空分裝置產量為52000nm3/h,氧提取率超過90%,氣化劑為99.6%的純氧。進料方式為半焦干粉進料(40-90μm顆粒),輸送氣體為co2,輸送壓力4.0mpa,送入燒嘴自上而下單噴嘴噴射入氣化爐,氣化溫度1250-1450℃,壓力為3-3.5mpa,生成的粗合成氣和熔渣經水激冷后排渣,粗合成氣在激冷室上部排出,經進一步冷卻、除塵后進入后續工序。粗合成氣主要組分為:35%h2、39%co、11%co2、14%h2o及微量的h2s、n2、ch4等氣體。(3)粗合成氣經水蒸氣變換反應裝置調整h2和co的比例為1.38,采用鐵為催化劑,壓力0.8-1mpa,反應溫度為220-280℃;生成的變換氣基本參數如下:流量178000m3/h,溫度40℃,壓力3.5mpa,氣體組成為:36%h2、26%co、38%co2。變換氣再經低溫甲醇洗工藝脫除co2氣體,將氣體冷卻至10℃進入氨洗塔以降低nh3和hcn含量,然后噴入co2吸收塔(溫度-21℃,壓力3.43mpa)用甲醇(-53℃)吸收co2,得到合成氣。(4)采用漿態床f-t反應器,原料為合成氣,催化劑為中科icc-ii型鐵系催化劑,反應溫度230-250℃,壓力2.5-3.5mpa;反應生成初餾分18kg。(5)一段聚合生產低聚物:原料為18kg初餾分,采用聚合反應釜,包括第一段聚合反應,催化劑為三氟甲磺酸基復合催化劑,用量1-2wt%,反應溫度為50-80℃,壓力為0.1-0.3mpa;反應時間1.5h,一段聚合反應結束后油品進入分離裝置進行分離。分離工藝分為兩段,首段為低溫結晶,溫度為-30℃,固體析出物(c11以上烷烴組分)經過濾工藝除去;次段分離為蒸餾提純,溫度為180℃,蒸出餾分為c10以下烷烴;經兩段分離工藝提純后得到低聚物9.5kg。二段聚合生產高聚物:以低聚物為原料進行第二段聚合反應,正丁醇為引發劑,氮氣置換后開始反應,反應溫度為150-200℃,壓力為0.3-0.5mpa;時間5h,催化劑為三元催化劑(氫氧化鑭、鈰混合物/鉻-硅復合催化劑),用量1.2wt%。α-烯烴轉化率為99%,得到9.2kg高聚物。上述高聚物含有雙鍵,通過異構烷烴烷基化反應加以飽和。異構烷烴為異戊烷,在釜式反應器內和高聚物進行反應,反應溫度為100-200℃,壓力為1-3mpa,催化劑為三氟甲磺酸基復合催化劑,用量1.5wt%,混合烴和聚α-烯烴摩爾比9:1,反應時間1.5h。烷基化反應結束后經減壓蒸餾除去未反應物,得到10kg生物基聚α-烯烴合成油。生物基聚α烯烴合成油特性指標:實施例2:(1)200kg玉米秸稈(含水率25%)粉碎至1cm以下,進入管族梯級減壓連續水解反應器,包括第一階段水解:溫度為205-210℃、壓力為2.2-2.3mpa,時間3分鐘,秸稈中的半纖維素轉化為低聚木糖滲濾出來;纖維素和木質素進入第二階段水解:溫度為180-185℃、壓力為1.4-1.5mpa,時間20分鐘,將秸稈中的纖維素轉化為纖維低聚糖滲濾出來;木質素進入第三階段水解:95%wt乙酸催化劑,溫度為180-185℃、壓力為1.4-1.5mpa,時間10分鐘,木質素轉化為木質素半焦118.2kg(含水37-40%)。(2)以74kg干木質素半焦為原料(含水2-5%),采用航天爐氣化裝置,空分裝置產量為52000nm3/h,氧提取率超過90%,氣化劑為99.6%的純氧。進料方式為半焦干粉進料(40-90μm顆粒),輸送氣體為co2,輸送壓力4.0mpa,送入燒嘴自上而下單噴嘴噴射入氣化爐,氣化溫度1250-1450℃,壓力為3-3.5mpa,生成的粗合成氣和熔渣經水激冷后排渣,粗合成氣在激冷室上部排出,經進一步冷卻、除塵后進入后續工序。粗合成氣主要組分為:35%h2、38%co、10%co2、16%h2o及微量的h2s、n2、ch4等氣體。(3)粗合成氣經水蒸氣變換反應裝置調整h2和co的比例為1.39,采用鐵為催化劑,壓力0.8-1mpa,反應溫度為220-280℃;生成的變換氣基本參數如下:流量178000m3/h,溫度40℃,壓力3.5mpa,氣體組成為:39%h2、28%co、33%co2。變換氣再經低溫甲醇洗工藝脫除co2氣體,將氣體冷卻至10℃進入氨洗塔以降低nh3和hcn含量,然后噴入co2吸收塔(溫度-21℃,壓力3.43mpa)用甲醇(-53℃)吸收co2,得到合成氣。(4)采用漿態床f-t反應器,原料為合成氣,催化劑為中科icc-ii型鐵系催化劑,反應溫度230-250℃,壓力2.5-3.5mpa;反應生成初餾分18.5kg。(5)一段聚合生產低聚物:原料為18.5kg初餾分,采用聚合反應釜,包括第一段聚合反應,催化劑為三氟甲磺酸基復合催化劑,用量1.2wt%,反應溫度為50-80℃,壓力為0.1-0.3mpa;反應時間1.2h,一段聚合反應結束后油品進入分離裝置進行分離。分離工藝分為兩段,首段為低溫結晶,溫度為-30℃,固體析出物(c11以上烷烴組分)經過濾工藝除去;次段分離為蒸餾提純,溫度為180℃,蒸出餾分為c10以下烷烴;經兩段分離工藝提純后得到低聚物9.8kg。二段聚合生產高聚物:以低聚物為原料進行第二段聚合反應,正丁醇為引發劑,氮氣置換后開始反應,反應溫度為150-200℃,壓力為0.3-0.5mpa;時間4-6h,催化劑為三元催化劑(氫氧化鑭、鈰混合物/鉻-硅復合催化劑),用量1.2wt%。α-烯烴轉化率為99%,得到9.5kg高聚物。上述高聚物含有雙鍵,通過異構烷烴烷基化反應加以飽和。異構烷烴為異戊烷,在釜式反應器內和高聚物進行反應,反應溫度為100-200℃,壓力為1-3mpa,催化劑為三氟甲磺酸基復合催化劑,用量1.4wt%,混合烴和聚α-烯烴摩爾比10:1,反應時間1.2h。烷基化反應結束后經減壓蒸餾除去未反應物,得到10.2kg聚α-烯烴合成油。聚α烯烴油特性指標如下:實施例3:(1)200kg玉米秸稈(含水率25%)粉碎至1cm以下,進入管族梯級減壓連續水解反應器,包括第一階段水解:溫度為205-210℃、壓力為2.2-2.3mpa,時間3分鐘,秸稈中的半纖維素轉化為低聚木糖滲濾出來;纖維素和木質素進入第二階段水解:溫度為180-185℃、壓力為1.4-1.5mpa,時間20分鐘,將秸稈中的纖維素轉化為纖維低聚糖滲濾出來;木質素進入第三階段水解:95%wt乙酸催化劑,溫度為180-185℃、壓力為1.4-1.5mpa,時間10分鐘,木質素轉化為木質素半焦115.2kg(含水37-40%)。(2)以73kg干木質素半焦為原料(含水2-5%),采用航天爐氣化裝置,空分裝置產量為52000nm3/h,氧提取率超過90%,氣化劑為99.6%的純氧。進料方式為半焦干粉進料(40-90μm顆粒),輸送氣體為co2,輸送壓力4.0mpa,送入燒嘴自上而下單噴嘴噴射入氣化爐,氣化溫度1250-1450℃,壓力為3-3.5mpa,生成的粗合成氣和熔渣經水激冷后排渣,粗合成氣在激冷室上部排出,經進一步冷卻、除塵后進入后續工序。粗合成氣主要組分為:36%h2、37%co、10%co2、16%h2o及微量的h2s、n2、ch4等氣體。(3)粗合成氣經水蒸氣變換反應裝置調整h2和co的比例為1.39,采用鐵為催化劑,壓力0.8-1mpa,反應溫度為220-280℃;生成的變換氣基本參數如下:流量178000m3/h,溫度40℃,壓力3.5mpa,氣體組成為:39%h2、28%co、33%co2。變換氣再經低溫甲醇洗工藝脫除co2氣體,將氣體冷卻至10℃進入氨洗塔以降低nh3和hcn含量,然后噴入co2吸收塔(溫度-21℃,壓力3.43mpa)用甲醇(-53℃)吸收co2,得到合成氣。(4)采用漿態床f-t反應器,原料為合成氣,催化劑為中科icc-ii型鐵系催化劑,反應溫度230-250℃,壓力2.5-3.5mpa;反應生成初餾分18.2kg。(5)一段聚合生產低聚物:原料為18.2kg初餾分,采用聚合反應釜,包括第一段聚合反應,催化劑為三氟甲磺酸基復合催化劑,用量1.2wt%,反應溫度為50-80℃,壓力為0.1-0.3mpa;反應時間1.2h,一段聚合反應結束后油品進入分離裝置進行分離。分離工藝分為兩段,首段為低溫結晶,溫度為-30℃,固體析出物(c11以上烷烴組分)經過濾工藝除去;次段分離為蒸餾提純,溫度為180℃,蒸出餾分為c10以下烷烴;經兩段分離工藝提純后得到低聚物9.6kg。二段聚合生產高聚物:以低聚物為原料進行第二段聚合反應,正丁醇為引發劑,氮氣置換后開始反應,反應溫度為150-200℃,壓力為0.3-0.5mpa;時間4-6h,催化劑為三元催化劑(氫氧化鑭、鈰混合物/鉻-硅復合催化劑),用量1.2wt%。α-烯烴轉化率為99%,得到9.4kg高聚物。上述高聚物含有雙鍵,通過異構烷烴烷基化反應加以飽和。異構烷烴為異戊烷,在釜式反應器內和高聚物進行反應,反應溫度為100-200℃,壓力為1-3mpa,催化劑為三氟甲磺酸基復合催化劑,用量1.4wt%,混合烴和聚α-烯烴摩爾比10:1,反應時間1.2h。烷基化反應結束后經減壓蒸餾除去未反應物,得到10.1kg聚α-烯烴合成油。聚α烯烴油特性指標如下:實施例4:(1)200kg玉米秸稈(含水率25%)粉碎至1cm以下,進入管族梯級減壓連續水解反應器,包括第一階段水解:溫度為205-210℃、壓力為2.2-2.3mpa,時間3分鐘,秸稈中的半纖維素轉化為低聚木糖滲濾出來;纖維素和木質素進入第二階段水解:溫度為180-185℃、壓力為1.4-1.5mpa,時間20分鐘,將秸稈中的纖維素轉化為纖維低聚糖滲濾出來;木質素進入第三階段水解:95%wt乙酸催化劑,溫度為180-185℃、壓力為1.4-1.5mpa,時間10分鐘,木質素轉化為木質素半焦119.2kg(含水37-40%)。(2)以74.5kg干木質素半焦為原料(含水2-5%),采用航天爐氣化裝置,空分裝置產量為52000nm3/h,氧提取率超過90%,氣化劑為99.6%的純氧。進料方式為半焦干粉進料(40-90μm顆粒),輸送氣體為co2,輸送壓力4.0mpa,送入燒嘴自上而下單噴嘴噴射入氣化爐,氣化溫度1250-1450℃,壓力為3-3.5mpa,生成的粗合成氣和熔渣經水激冷后排渣,粗合成氣在激冷室上部排出,經進一步冷卻、除塵后進入后續工序。粗合成氣主要組分為:36%h2、37%co、10%co2、16%h2o及微量的h2s、n2、ch4等氣體。(3)粗合成氣經水蒸氣變換反應裝置調整h2和co的比例為1.36,采用鐵為催化劑,壓力0.8-1mpa,反應溫度為220-280℃;生成的變換氣基本參數如下:流量178000m3/h,溫度40℃,壓力3.5mpa,氣體組成為:38%h2、28%co、34%co2。變換氣再經低溫甲醇洗工藝脫除co2氣體,將氣體冷卻至10℃進入氨洗塔以降低nh3和hcn含量,然后噴入co2吸收塔(溫度-21℃,壓力3.43mpa)用甲醇(-53℃)吸收co2,得到合成氣。(4)采用漿態床f-t反應器,原料為合成氣,催化劑為中科icc-ii型鐵系催化劑,反應溫度230-250℃,壓力2.5-3.5mpa;反應生成初餾分18.7kg。(5)一段聚合生產低聚物:原料為18.7kg初餾分,采用聚合反應釜,包括第一段聚合反應,催化劑為三氟甲磺酸基復合催化劑,用量1.2wt%,反應溫度為50-80℃,壓力為0.1-0.3mpa;反應時間1.5h,一段聚合反應結束后油品進入分離裝置進行分離。分離工藝分為兩段,首段為低溫結晶,溫度為-30℃,固體析出物(c11以上烷烴組分)經過濾工藝除去;次段分離為蒸餾提純,溫度為180℃,蒸出餾分為c10以下烷烴;經兩段分離工藝提純后得到低聚物9.9kg。二段聚合生產高聚物:以低聚物為原料進行第二段聚合反應,正丁醇為引發劑,氮氣置換后開始反應,反應溫度為150-200℃,壓力為0.3-0.5mpa;時間4-6h,催化劑為三元催化劑(氫氧化鑭、鈰混合物/鉻-硅復合催化劑),用量1.3wt%。α-烯烴轉化率為99%,得到9.6kg高聚物。上述高聚物含有雙鍵,通過異構烷烴烷基化反應加以飽和。異構烷烴為異戊烷,在釜式反應器內和高聚物進行反應,反應溫度為100-200℃,壓力為1-3mpa,催化劑為三氟甲磺酸基復合催化劑,用量1.4wt%,混合烴和聚α-烯烴摩爾比10:1,反應時間1.5h。烷基化反應結束后經減壓蒸餾除去未反應物,得到10.5kg聚α-烯烴合成油。聚α烯烴油特性指標如下:本發明所用的術語是說明和示例性、而非限制性的術語。由于本發明能夠以多種形式具體實施而不脫離發明的精神或實質,所以應當理解,上述實施例不限于任何前述的細節,而應在隨附權利要求所限定的精神和范圍內廣泛地解釋,因此落入權利要求或其等效范圍內的全部變化和改型都應為隨附權利要求所涵蓋。當前第1頁12