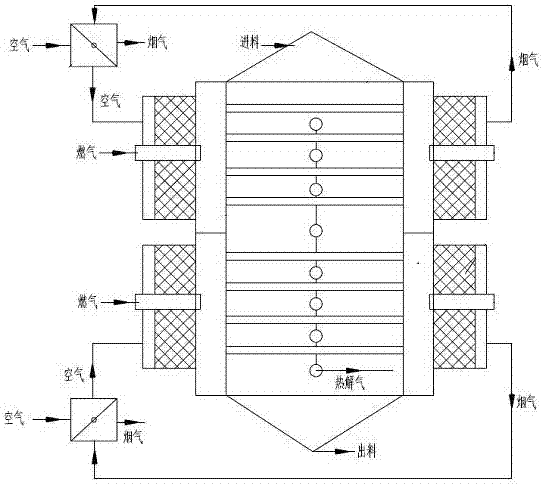
本實用新型屬于含碳物質的熱解處理
技術領域:
,具體涉及一種主要針對低階煤、生物質、油頁巖、廢舊輪胎、污泥等含碳物質的新型蓄熱式熱解反應器,用于提取焦油、可燃氣和半焦產品。
背景技術:
:我國擁有豐富的含碳的低品位能源和廢棄物資源,主要包括低階煤、生物質、油頁巖、廢舊輪胎、污泥等,這些物質很多沒有得到充分有效的利用。熱解的定義是指無氧的環境下,有機含碳物質在高溫下的分解反應,可以生成油氣產品,是對含碳物質的一種有效處理方法,能為我國能源需求提供有力的補充。目前的熱解反應器主要包括內熱式、外熱式及混合加熱式,根據熱載體分類可以分為氣體熱載體、固體熱載體及無熱載體反應器。內熱式熱解反應器由于要采取氣體或固體熱載體進行加熱,涉及的工藝流程長,設備復雜,所以系統的連續和穩定性差;而外熱式熱解反應器采取外壁傳熱,雖然工藝簡單,但存在效率低,規模小缺點。另外單一的熱解反應器要不只能處理粉狀原料,要不只能處理塊狀原料,原料適用范圍小。因此,如何設計一種結構和工藝流程簡單、控溫準確且原料粒徑利用范圍廣的熱解反應器成為本領域亟需解決的問題。技術實現要素:本實用新型針對現有技術的不足,設計并開發出一種新型的蓄熱式熱解反應器,利用蓄熱式輻射管作為加熱源,采取外熱內熱結合布置方式,使系統結構簡單、調溫方便,有利于實現熱解目標產物的調整,并采取模塊化組合方式設計,處理規模可以大型化,提高系統熱效率。為解決上述技術問題,本實用新型采用的技術方案為:本實用新型提供了一種蓄熱式熱解反應器。根據本實用新型的實施例,該反應器包括:熱解室、雙蓄熱式輻射管系統、進料口、出料口和熱解氣出氣系統,其中:所述雙蓄熱式輻射管系統包括:輻射管、蓄熱體、燃氣燒嘴、空氣管線、煙氣管線、燃氣管線和換向閥;所述熱解氣出氣系統包括:設置在所述熱解室側壁上的、位于相鄰兩層輻射管之間的多個熱解氣出口、將多個所述熱解氣出口連接的管路以及位于所述熱解反應器下部的熱解氣導出口,所述管路的下端與所述熱解氣導出口連接;其中:所述輻射管沿所述蓄熱式熱解反應器的高度方向多層布置在所述熱解室內部,每層具有多根沿水平方向布置的所述輻射管,所述輻射管的兩端分別與所述熱解室的側壁固定連接;所述蓄熱體左右對稱的設置在所述蓄熱式熱解反應器的外壁上,所述蓄熱體中心設有所述燃氣燒嘴,用于使通入的燃氣和空氣燃燒,產生煙氣;所述蓄熱式熱解反應器外壁與所述熱解室的側壁之間形成密閉通道,所述密閉通道與所述輻射管連通,用于將所述燃氣燒嘴燃燒產生的煙氣通入所述輻射管中,并使煙氣通過所述熱解室側壁直接加熱所述熱解室;所述空氣管線、煙氣管線與所述換向閥連接,所述換向閥和所述燃氣管線分別與所述燃氣燒嘴連接。發明人發現,根據本實用新型實施例的熱解反應器,利用蓄熱式輻射管作為加熱源,采取外熱內熱結合布置方式,使系統結構和熱解工藝簡單,提高了系統可靠性,同時,多層布置的輻射管,調溫方便、控溫準確,有利于實現熱解目標產物的調整,并采取模塊化組合方式設計,處理規模可以大型化,提高系統熱效率。此外,熱解反應器的原料粒徑利用范圍廣,既能處理粉狀原料,也能處理塊狀原料。根據本實用新型的實施例,所述蓄熱式熱解反應器為立式爐結構。根據本實用新型的實施例,所述蓄熱體沿所述蓄熱式熱解反應器的高度方向多層布置,每層包括左右對稱的位于所述輻射管兩端的兩個蓄熱體。根據本實用新型的實施例,所述換向閥通過空氣/煙氣管線與燃氣燒嘴連接,所述燃氣管線一端連接到所述燃氣燒嘴。根據本實用新型的實施例,所述蓄熱體為陶瓷蜂窩體材料,每層的蓄熱體為4-8層的輻射管提供作為加熱源的所述煙氣。根據本實用新型的實施例,所述換向閥根據所述蓄熱體溫度變化設置換向時間間隔,以使所述雙蓄熱式輻射管系統的兩側交替進行燃燒-排煙氣。根據本實用新型的實施例,所述時間間隔為20-150秒。根據本實用新型的實施例,燃氣和空氣在所述燃氣燒嘴中燃燒,產生600-1000℃的高溫煙氣;所述煙氣經所述輻射管后,溫度下降至500-700℃。根據本實用新型的實施例,經過所述輻射管后的所述煙氣,將所述蓄熱體加熱到500-650℃,并且所述煙氣的溫度被降至200℃以下排出。根據本實用新型的實施例,所述反應器處理的原料為:0-6mm的粉狀原料或8-100mm的塊狀原料。本實用新型的有益效果在于:1)利用蓄熱式輻射管作為加熱源,采取外熱內熱結合布置方式,使系統結構和熱解工藝簡單,提高了系統可靠性。2)多層布置的輻射管,調溫方便、控溫準確,有利于實現熱解目標產物的調整。3)單蓄熱體帶多個輻射管,進一步簡化了工藝。4)并采取模塊化組合方式設計,處理規模可以大型化,提高系統熱效率。5)原料粒徑利用范圍廣,既能處理粉狀原料,也能處理塊狀原料。附圖說明圖1為本實用新型蓄熱式熱解反應器的結構圖。圖2為本實用新型蓄熱式熱解反應器的工作示意圖。其中,1、熱解室;2、雙蓄熱式輻射管系統;3、熱解氣出氣系統;310、熱解氣出口;320、熱解氣導出口;410、進料口;420、出料口;5、輻射管;6、蓄熱體;7、燃氣燒嘴;8、換向閥;910、空氣管線;920、煙氣管線;930、燃氣管線;10、密閉通道。具體實施方式為了使本領域技術人員更好地理解本實用新型的技術方案,下面結合具體實施例對本實用新型作進一步的詳細說明。下面描述的實施例是示例性的,僅用于解釋本實用新型,而不能理解為對本實用新型的限制。實施例中未注明具體技術或條件的,按照本領域內的文獻所描述的技術或條件或者按照產品說明書進行。根據本實用新型的一個方面,本實用新型提供了一種蓄熱式熱解反應器,圖1為該蓄熱式熱解反應器的結構圖,如圖1所示,熱解反應器包括熱解室1、雙蓄熱式輻射管系統2、進料口410、出料口420和熱解氣出氣系統3,其中:所述雙蓄熱式輻射管系統2包括:輻射管5、蓄熱體6、燃氣燒嘴7、空氣管線910、煙氣管線920、燃氣管線930和換向閥8;所述熱解氣出氣系統3包括:設置在所述熱解室側壁上的、位于相鄰兩層輻射管之間的多個熱解氣出口310、將多個所述熱解氣出口連接的管路以及位于所述熱解反應器下部的熱解氣導出口320,所述管路的下端與所述熱解氣導出口連接。由此,高效、便捷地將熱解室產生的熱解氣進行傳輸和收集。下面進一步描述,本實用新型中雙蓄熱式輻射管系統的具體結構。根據本實用新型的具體實施例,如圖1所示,輻射管5沿所述蓄熱式熱解反應器的高度方向多層布置在所述熱解室1內部,每層具有多根沿水平方向布置的所述輻射管,所述輻射管的兩端分別與所述熱解室的側壁固定連接。由此,利用蓄熱式輻射管作為加熱源,輻射管溫度均勻,排煙溫度低,能量利用率高,使系統結構和熱解工藝簡單,并且,多層布置的輻射管,調溫方便、控溫準確,能夠實現理想的熱解溫度控制和靈活調整,有利于實現熱解目標產物的調整。根據本實用新型的具體實施例,所述蓄熱體左右對稱的設置在所述蓄熱式熱解反應器的外壁上,所述蓄熱體中心設有所述燃氣燒嘴,用于使通入的燃氣和空氣燃燒,產生煙氣。所述蓄熱式熱解反應器外壁與所述熱解室的側壁之間形成密閉通道10,所述密閉通道與所述輻射管連通,用于將所述燃氣燒嘴燃燒產生的煙氣通入所述輻射管中,并使煙氣通過所述熱解室側壁直接加熱所述熱解室。由此,實現了外熱和內熱結合的高效率的布置方式來加熱熱解室,提高了蓄熱式熱解反應器的效率及可靠性。根據本實用新型的具體實施例,所述空氣管線、煙氣管線與所述換向閥連接,所述換向閥和所述燃氣管線分別與所述燃氣燒嘴連接。進一步的,所述換向閥通過空氣/煙氣管線與燃氣燒嘴連接,所述燃氣管線一端連接到所述燃氣燒嘴。由此,為燃氣燒嘴的燃燒提供了燃氣和空氣,并經煙氣通道進行排氣。本實用新型中的空氣管線和煙氣管線并不特殊限定,當雙向交替燃燒時,可以根據工作模式調整使用,來對應的傳輸空氣或煙氣。發明人發現,根據本實用新型實施例的熱解反應器,利用蓄熱式輻射管作為加熱源,采取外熱內熱結合布置方式,使系統結構和熱解工藝簡單,提高了系統可靠性,同時,多層布置的輻射管,調溫方便、控溫準確,有利于實現熱解目標產物的調整,并采取模塊化組合方式設計,處理規模可以大型化,提高系統熱效率。此外,熱解反應器的原料粒徑利用范圍廣,既能處理粉狀原料,也能處理塊狀原料。根據本實用新型的具體實施例,適用于該熱解反應器的爐型不受特別限制,在本實用新型的一些優選實施例中,蓄熱式熱解反應器為立式爐結構。利用原料自重力從上往下落下來,邊熱解邊把熱解氣導出。根據本實用新型的具體實施例,適用于該熱解反應器的熱解料的具體種類和粒徑不受特別限制,根據本實用新型的一些優選實施例,熱解料為低階煤、生物質、油頁巖、廢舊輪胎、污泥等,熱解料可以為塊狀熱解料也可以為小顆粒熱解料,在本實用新型的一些優選實施例中,該反應器采用的熱解料為粒徑0-6mm的粉狀原料或8-100mm的塊狀原料。處理粒徑0-6mm范圍的粉狀原料時,利用原料自重力從上往下落下來,邊熱解邊把熱解氣導出,處理粒徑8-100mm范圍的塊狀原料時,利用出料系統(未示出)的出料速度控制原料下行速度,而熱解氣從原料間隙中出來,沿著輻射管的間隙導入到熱解氣出口中。由此,原料粒徑利用范圍廣,使得資源利用率高,解決大量堆積污染環境的問題。根據本實用新型的具體實施例,適用于該熱解反應器的蓄熱體的材質和設置方式不受特別限制,在本實用新型的一些優選實施例中,所述蓄熱體沿所述蓄熱式熱解反應器的高度方向多層布置,每層包括左右對稱的位于所述輻射管兩端的兩個蓄熱體,其中,每層的蓄熱體為4-8層的輻射管提供作為加熱源的所述煙氣。由此,單蓄熱體帶多個輻射管,進一步簡化了結構和工藝。在本實用新型的一些優選實施例中,蓄熱體為陶瓷蜂窩體材料,具有單位體積表面大,熱穩定好、耐腐蝕等優點。根據本實用新型的具體實施例,換向閥的換向方式不受特別限制,在本實用新型的一些優選實施例中,換向閥根據所述蓄熱體溫度變化設置換向時間間隔,以使所述雙蓄熱式輻射管系統的兩側交替進行燃燒-排煙氣,優選的,所述時間間隔為20-150秒。根據本實用新型的具體實施例,燃氣和空氣在所述燃氣燒嘴中燃燒,產生600-1000℃的高溫煙氣;所述煙氣經所述輻射管后,溫度下降至500-700℃。經過所述輻射管后的所述煙氣,將所述蓄熱體加熱到500-650℃,并且所述煙氣的溫度被降至200℃以下排出。圖2是本實用新型蓄熱式熱解反應器的工作示意圖,下面結合圖2介紹本實用新型熱解反應器的工作方式。如圖2所示,原料通過進料系統(未示出)進入熱解反應器的上部,在物料在下行過程中,經過輻射管加熱,在隔絕空氣的氛圍發生熱解反應,產生熱解氣和熱半焦,熱解氣匯集后從熱解反應器下方側部的熱解氣導出口導出,而熱半焦從爐底排出。燃氣和空氣在左邊燒嘴中燃燒產生600-1000℃高溫煙氣,煙氣經4-8個輻射管進入熱解反應中作為加熱源提供熱解反應需要的能量,煙氣溫度下降至500-700攝氏度后,經過右邊蓄熱體把煙氣溫度降至200℃以下后排出,而右邊蓄熱體被加熱到500-650℃;換向閥根據蓄熱體溫度變化設置了換向時間間隔,一般為20-150s,當換向閥換向后,左邊蓄熱式的燒嘴停止供燃氣,而右邊燒嘴開始供燃氣燃燒,空氣經原先煙氣管線進入右邊蓄熱體,經蓄熱式加熱,常溫空氣加熱至500-650℃后,與燃氣混合在右邊燒嘴中燃燒,產生高溫煙氣通過輻射管進入熱解反應器中,進行熱解反應。在熱解過程中,循環重復上述過程,直至反應結束。實施例一:利用蓄熱式熱解反應系統對澳大利亞褐煤進行處理,其褐煤分析數據、工藝操作參數和物料平衡見表1-表3,褐煤的粒徑范圍為0-6mm。采取三層蓄熱體布置,每層蓄熱體布置4層輻射管,從表3得出的焦油產率高達12.3%,是葛金法得到的焦油產率110%,熱解氣產率為16.7%。表1:澳大利亞褐煤分析數據表2:工藝操作參數序號參數名稱參數值序號參數名稱參數值1一層輻射管壁溫650℃6一層輻射管排煙溫度180℃2二層輻射管壁溫600℃7二層輻射管壁溫160℃3三層輻射管壁溫550℃8三層輻射管壁溫140℃4換向閥設置時間60s表3:物料平衡表實施案例2:把褐煤的粒徑改為6-100mm,改變輻射管壁溫及換向閥停留時間,得到的焦油產率為8.6%,熱解氣產率為19.4%,通過熱解溫度的提高,熱解油的產率下降了,但熱解氣的產率比案例1提高了。表4:工藝操作參數序號參數名稱參數值序號參數名稱參數值1一層輻射管壁溫700℃6一層輻射管排煙溫度190℃2二層輻射管壁溫660℃7二層輻射管壁溫170℃3三層輻射管壁溫600℃8三層輻射管壁溫150℃4換向閥設置時間80s表5:物料平衡表由此,本實用新型新型的蓄熱式熱解反應器,利用蓄熱式輻射管作為加熱源,采取外熱內熱結合布置方式,使系統結構簡單、調溫方便,有利于實現熱解目標產物的調整,并采取模塊化組合方式設計,處理規模可以大型化,提高系統熱效率。在本實用新型的描述中,需要理解的是,術語“第一”、“第二”僅用于描述目的,而不能理解為指示或暗示相對重要性或者隱含指明所指示的技術特征的數量。由此,限定有“第一”、“第二”的特征可以明示或者隱含地包括一個或者更多個該特征。在本實用新型中,除非另有明確的規定和限定,術語“安裝”、“相連”、“連接”、“固定”等術語應做廣義理解,例如,可以是固定連接,也可以是可拆卸連接,或成一體;可以是機械連接,也可以是電連接;可以是直接相連,也可以通過中間媒介間接相連,可以是兩個元件內部的連通或兩個元件的相互作用關系。對于本領域的普通技術人員而言,可以根據具體情況理解上述術語在本實用新型中的具體含義。在本實用新型中,除非另有明確的規定和限定,第一特征在第二特征“上”或“下”可以是第一和第二特征直接接觸,或第一和第二特征通過中間媒介間接接觸。而且,第一特征在第二特征“之上”、“上方”和“上面”可是第一特征在第二特征正上方或斜上方,或僅僅表示第一特征水平高度高于第二特征。第一特征在第二特征“之下”、“下方”和“下面”可以是第一特征在第二特征正下方或斜下方,或僅僅表示第一特征水平高度小于第二特征。在本說明書的描述中,參考術語“一個實施例”、“一些實施例”、“示例”、“具體示例”、或“一些示例”等的描述意指結合該實施例或示例描述的具體特征、結構、材料或者特點包含于本實用新型的至少一個實施例或示例中。在本說明書中,對上述術語的示意性表述不必針對的是相同的實施例或示例。而且,描述的具體特征、結構、材料或者特點可以在任一個或多個實施例或示例中以合適的方式結合。此外,在不相互矛盾的情況下,本領域的技術人員可以將本說明書中描述的不同實施例或示例以及不同實施例或示例的特征進行結合和組合。盡管上面已經示出和描述了本實用新型的實施例,可以理解的是,上述實施例是示例性的,不能理解為對本實用新型的限制,本領域的普通技術人員在本實用新型的范圍內可以對上述實施例進行變化、修改、替換和變型,同時,對于本領域的一般技術人員,依據本申請的思想,在具體實施方式及應用范圍上均會有改變之處。當前第1頁1 2 3