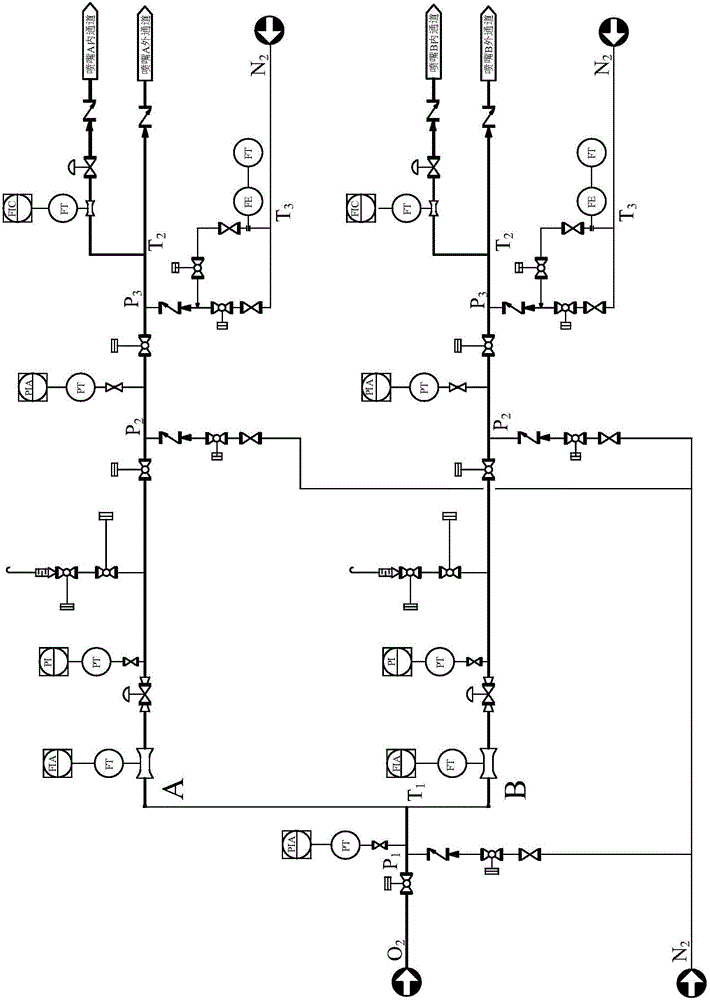
本實用新型涉及一種氧氣進料控制系統及其氣化爐進料系統。
背景技術:煤炭氣化過程是以氧氣(空氣、富氧或工業純氧)、水蒸氣作為氣化劑,在高溫高壓下通過化學反應將煤或煤焦中的可燃部分轉化為可燃性氣體的工藝過程,其中氣流床氣化技術因其良好的技術指標、高處理負荷和環境友好性等特點,成為當今煤炭氣化的主流技術。其中,多噴嘴對置式煤氣化技術是國際先進的大型煤氣化主流技術之一,其以獨特的大型化優勢、優異的工藝性能和安全可靠性,得到了廣泛的工業應用。多噴嘴對置式氣化技術的特點是煤等含碳物質(粉態或漿態)和氧氣分別經過四套流量調節、計量和多道切斷閥后進入氣化爐。與單噴嘴氣化爐相比,其控制閥門與計量系統較復雜,投資較大,尤其是高壓高純氧氣的計量與控制系統。傳統的多噴嘴煤氣化技術中的氣化爐氧氣控制系統分為氧氣流量建立系統和氧氣投料系統,氧氣控制系統還包括四組調節、計量和控制系統,在氣化爐投料與控制中采用兩兩組合的形式得到一套控制系統,分別對每一個燒嘴的氧氣進料進行調節、計量和控制。對于一臺多噴嘴對置式氣化爐,一般有兩套控制系統,其控制閥門與計量系統十分復雜和龐大,由于管道布置、儀器儀表、燒嘴尺寸等存在某些硬件上無法避免的細微差異,常會導致最終一對燒嘴中氧氣進料分配不均勻,影響生產效果,且該控制系統投資成本巨大,長時間運行易出現系統可靠性等問題。
技術實現要素:本實用新型要解決的是現有技術控制系統操作強度大、結構復雜、長時間運行易出現可靠性問題、以及投資成本巨大的缺陷,提供了一種系統較簡化、可靠性較好、投資較低的氧氣進料控制系統及其氣化爐進料系統。本實用新型通過下述技術方案來解決上述技術問題:本實用新型提供了一種氧氣進料控制系統,所述氧氣進料控制系統包括氧氣流量建立系統和氧氣投料系統;所述氧氣流量建立系統的管線由氧氣源依次經第一遠程控制閥和氧氣流量調節閥與所述氧氣投料系統連接;所述氧氣投料系統的管線依次經第一切斷閥和第二切斷閥后分為至少兩條支管,每條所述支管經支管節流元件與噴嘴連接。本實用新型中,所述氧氣流量調節閥和所述第一切斷閥之間的管線上較佳地還設有放空支管,所述放空支管的管線依次經第三切斷閥和第二遠程控制閥接大氣放空。本實用新型中,每條所述支管較佳地分為內通道管線和外通道管線,其中,所述外通道管線經外通道節流元件與噴嘴外通道連接,所述內通道管線經內通道節流元件與噴嘴內通道連接,以實現噴嘴的內通道和外通道之間氧氣進料比例的均勻分配。本實用新型中,所述外通道節流元件與所述噴嘴外通道之間的管線上較佳地設有一止回閥。本實用新型中,所述內通道節流元件與所述噴嘴內通道之間的管線上較佳地設有一止回閥。本實用新型中,所述氧氣進料控制系統較佳地還包括氮氣輔助系統,用于投料前后的管道吹掃以及停車后的系統保護;所述氮氣輔助系統包括前氮氣輔助系統和后氮氣輔助系統;所述前氮氣輔助系統的管線包括第一氮氣支管和第二氮氣支管,所述第一氮氣支管由氮氣源依次經截止閥、第三遠程控制閥和止回閥后與第一氮氣接入點連接,所述第一氮氣接入點位于所述第一遠程控制閥與所述氧氣流量調節閥之間的管線上,所述第二氮氣支管由所述氮氣源依次經截止閥、第四切斷閥和止回閥后與第二氮氣接入點連接,所述第二氮氣接入點位于所述第一切斷閥與所述第二切斷閥之間的管線上;所述后氮氣輔助系統的管線包括第三氮氣支管和第四氮氣支管,所述第三氮氣支管由所述氮氣源依次經截止閥、第五切斷閥和止回閥后與第三氮氣接入點連接,所述第三氮氣接入點位于所述第二切斷閥與所述支管的分叉點之間的管線上,所述第四氮氣支管由所述氮氣源依次經截止閥和第六切斷閥接入于所述第五切斷閥與所述第三氮氣支管上的止回閥之間的管線上。本實用新型中,所述支管節流元件、所述外通道節流元件和所述內通道節流元件較佳地均為標準孔板;所述標準孔板為本領域常規使用的標準孔板,其具體規格在現場管道布置完成后,根據管道內流體流動的雷諾數計算或模擬出管道局部阻力系數,然后根據本領域常規方法計算管道內流體壓降,得到標準孔板的規格選擇。本實用新型中,所述支管節流元件、所述外通道節流元件和所述內通道節流元件的材料與所述氧氣進料控制系統的管線的材料一致,一般為本領域常規使用的氧氣輸送管道材料,例如Inconel600型鎳-鉻-鐵基固溶強化合金或Inconel625型鎳-鉻-鐵基固溶強化合金。本實用新型中,所述第一遠程控制閥、所述第二遠程控制閥和所述第三遠程控制閥均為本領域常規使用的遠程控制閥,其中,所述第二遠程控制閥較佳地為放空背壓閥。本實用新型中,所述第一切斷閥、所述第二切斷閥、所述第三切斷閥、所述第四切斷閥、所述第五切斷閥和所述第六切斷閥均為本領域常規使用的切斷閥。本實用新型中,所述氧氣流量調節閥為本領域常規使用的氧氣流量調節閥。本實用新型中,所述第一氮氣接入點與所述氧氣流量調節閥之間的管線上較佳地設有一主管文丘里管,所述主管文丘里管與總流量計連接。本實用新型中,所述支管的分叉點與所述支管節流元件之間的管線上較佳地設有一支管文丘里管,所述支管文丘里管與支管流量計連接。本實用新型中,所述內通道管線和所述外通道管線的分叉點與所述內通道節流元件之間的管線上較佳地設有一內通道文丘里管,所述內通道文丘里管與內通道流量計連接。本實用新型中,所述第三氮氣支管和所述第四氮氣支管之間的分叉點與所述第四氮氣支管的截止閥之間的管線上較佳地接有一氮氣流量計。本實用新型中,所述總流量計、所述支管流量計、所述內通道流量計和所述氮氣流量計均為本領域常規使用的流量計,其中,所述總流量計較佳地與本領域常規使用的流量報警器連接,所述支管流量計和所述內通道流量計較佳地與本領域常規使用的流量控制器連接,所述氮氣流量計較佳地為孔板流量計。本實用新型中,所述第一氮氣接入點與所述主管文丘里管之間的管線上較佳地經一截止閥接有一第一壓力表。本實用新型中,所述氧氣流量調節閥與所述放空支管之間的管線上較佳地經一截止閥接有一第二壓力表。本實用新型中,所述第二氮氣接入點與所述第二切斷閥之間的管線上較佳地經一球閥接有一第三壓力表。本實用新型中,所述第一壓力表、所述第二壓力表和所述第三壓力表均為本領域常規使用的壓力表。本實用新型中,其他未特指的閥門如截止閥、止回閥和球閥等均為本領域常規使用的閥門。本實用新型還提供了一種多噴嘴對置式水煤漿或煤粉氣化爐進料系統,其包括如上所述的氧氣進料控制系統。在符合本領域常識的基礎上,上述各優選條件,可任意組合,即得本實用新型各較佳實例。本實用新型的積極進步效果在于:本實用新型在不影響氧氣在兩個噴嘴間均勻分配進料與系統安全穩定控制的前提下,大大降低了一套氧氣進料控制系統中閥門和計量系統的硬件投資,進而降低了整個氣化爐系統的投資成本以及系統的操作強度和復雜性,減少了因閥門和計量系統的部分損壞導致的系統故障停車概率,增強了整個氣化爐進料系統的可靠性。附圖說明圖1為實施例1的氧氣進料控制系統的工藝流程示意圖。圖2為對比例1的氧氣進料控制系統的工藝流程示意圖。具體實施方式下面通過實施例的方式進一步說明本實用新型,但并不因此將本實用新型限制在所述的實施例范圍之中。實施例1一種如圖1所示的氧氣進料控制系統,所述氧氣進料控制系統包括氧氣流量建立系統和氧氣投料系統;所述氧氣流量建立系統的管線由氧氣源依次經第一遠程控制閥101和氧氣流量調節閥111與所述氧氣投料系統連接;所述氧氣投料系統的管線依次經第一切斷閥121和第二切斷閥122后分為支管A和支管B,每條所述支管經支管節流元件131與噴嘴連接。所述氧氣流量調節閥111和所述第一切斷閥121之間的管線上還設有放空支管,所述放空支管的管線依次經第三切斷閥123和第二遠程控制閥102接大氣放空。每條所述支管分為內通道管線和外通道管線,其中,所述外通道管線經外通道節流元件132與噴嘴外通道連接,所述內通道管線經內通道節流元件133與噴嘴內通道連接。所述外通道節流元件132與所述噴嘴外通道之間的管線上設有一止回閥。所述內通道節流元件133與所述噴嘴內通道之間的管線上設有一止回閥。所述支管節流元件131、所述外通道節流元件132和所述內通道節流元件133均為標準孔板。所述氧氣進料控制系統還包括氮氣輔助系統,所述氮氣輔助系統包括前氮氣輔助系統和后氮氣輔助系統;所述前氮氣輔助系統的管線包括第一氮氣支管和第二氮氣支管,所述第一氮氣支管由氮氣源依次經截止閥、第三遠程控制閥103和止回閥后與第一氮氣接入點P1連接,所述第一氮氣接入點P1位于所述第一遠程控制閥101與所述氧氣流量調節閥111之間的管線上,所述第二氮氣支管由所述氮氣源依次經截止閥、第四切斷閥124和止回閥后與第二氮氣接入點P2連接,所述第二氮氣接入點P2位于所述第一切斷閥121與所述第二切斷閥122之間的管線上;所述后氮氣輔助系統的管線包括第三氮氣支管和第四氮氣支管,所述第三氮氣支管由所述氮氣源依次經截止閥、第五切斷閥125和止回閥后與第三氮氣接入點P3連接,所述第三氮氣接入點P3位于所述第二切斷閥122與所述支管的分叉點T1之間的管線上,所述第四氮氣支管由所述氮氣源依次經截止閥和第六切斷閥126接入于所述第五切斷閥125與所述止回閥之間的管線上。所述第一氮氣接入點P1與所述氧氣流量調節閥111之間的管線上設有一主管文丘里管,所述主管文丘里管與總流量計141連接。所述支管的分叉點T1與所述支管節流元件之間的管線上設有一支管文丘里管,所述支管文丘里管與支管流量計142連接。所述內通道管線和所述外通道管線的分叉點T2與所述內通道節流元件之間的管線上設有一內通道文丘里管,所述內通道文丘里管與內通道流量計143連接。所述第三氮氣支管和所述第四氮氣支管之間的分叉點T3與所述第四氮氣支管的截止閥之間的管線上接有一氮氣流量計144。所述總流量計141與流量報警器連接,所述支管流量計142和所述內通道流量計143與流量控制器連接,所述氮氣流量計144為孔板流量計。所述第一氮氣接入點P1與所述主管文丘里管之間的管線上經一截止閥接有一第一壓力表151。所述氧氣流量調節閥與所述放空支管之間的管線上經一截止閥接有一第二壓力表152。所述第二氮氣接入點P2與所述第二切斷閥之間的管線上經一球閥接有一第三壓力表153。本實施例的工作流程如下:(1)氧氣流量建立氧氣通過第一遠程控制閥101引氧后,分別通過總流量計141、氧氣流量調節閥111、第三切斷閥123和第二遠程控制閥102后進行放空,氧氣投料流量通過氧氣流量調節閥111進行調節;(2)氧氣投料準備氧氣依次通過第一切斷閥121、第二切斷閥122、支管流量計142和支管節流元件131后經外通道節流元件132或內通道流量計143和內通道節流元件133后進入氣化爐。(3)投料過程先關閉第五切斷閥125,打開第二切斷閥122,關閉第四切斷閥124,通過設定好的延時時間后,同時打開第一切斷閥121和關閉第三切斷閥123,最后關閉第六切斷閥126完成投料。在投料過程中,嚴格監控第二壓力表152和第三壓力表153。對比例1如圖2所示,現有的多噴嘴煤氣化技術的氧氣進料控制系統包括四組調節、計量和控制系統,兩兩組合成一套控制系統。現有的氧氣進料控制系統的管路設置和工作流程與實施例1基本相同,在此不作贅述;其與實施例1的主要區別在于支管節流元件、外通道節流元件和內通道節流元件的設置,噴嘴的內通道支管上設有流量調節閥,以及支管A和支管B的分叉點T1在氧氣流量調節閥前。由圖2可以看出,除去截止閥、止回閥和球閥等常規閥門,對于一套現有氧氣進料控制系統,共有4個遠程控制閥、12個切斷閥、6個流量計、4個流量調節閥和5個壓力表;若是對于一臺氣化爐的兩套控制系統,則共有8個遠程控制閥、24個切斷閥、12個流量計、8個流量調節閥和10個壓力表,系統十分復雜和龐大。而如實施例1所述,實施例1的一套氧氣進料控制系統僅包括3個遠程控制閥、6個切斷閥、6個流量計、1個流量調節閥、3個壓力表。與現有氧氣進料控制系統相比,本實用新型的一套氧氣進料控制系統復雜性降低50%,系統投資降低約40%,大大降低了一套氧氣進料控制系統的硬件投資,進而降低了整個氣化爐系統的投資成本以及系統的操作強度和復雜性,減少了系統因閥門等元件導致的故障停車概率,增強了整個氣化爐進料系統的可靠性。