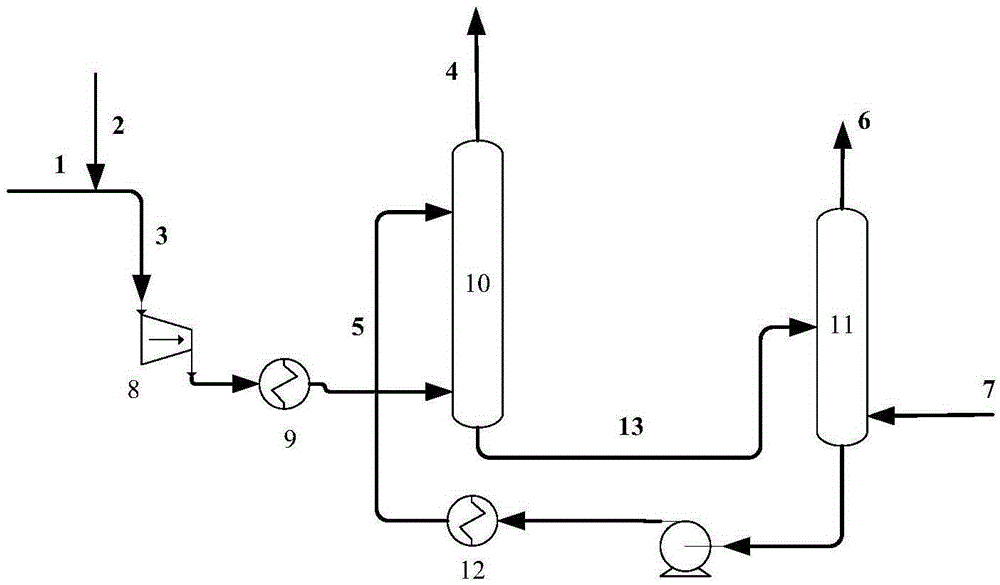
本發明涉及輕烴加工領域,具體地,涉及一種脫除含氧輕烴中氧氣的方法。
背景技術:
:輕烴是寶貴的乙烯、丙烯工業原料和化工資源,是具有較高附加值的大宗化學品。許多工業裝置產出的輕烴氣(如乙烯、丙烯等)都含有不少的氧氣。這種含氧輕烴氣在聚烯烴生產工業中有著巨大的安全隱患。另外,輕烴氣中氧氣的存在不僅會降低聚烯烴反應高效催化劑的活性、選擇性和收率,而且會影響生產出聚合物的性能。因此,輕烴氣的脫氧凈化處理對于下游的聚烯烴生產至關重要。目前對于輕烴氣體的脫氧凈化處理,相關專利文獻和工業生產中均是通過脫氧催化劑實現。脫氧催化劑主要分為兩大類,一類是負載貴金屬的催化加氫脫氧劑。這種脫氧劑活性較高,脫氧容量大,但價格昂貴,容易發生加氫副反應,使用較少。還有一類是化學吸附型脫氧劑,此類脫氧劑不存在副反應,但對原料氣氧含量有限制,脫氧容量小,需要頻繁再生,在工業生產中往往有著需要設計雙塔切換工藝等缺點。現階段國內用于乙烯、丙烯等輕烴氣脫氧凈化的催化劑主要是第二類化學吸附型脫氧劑。但這類脫氧劑只能滿足氧含量低于100ppm的輕烴氣體的精脫氧,而對于氧含量高于500ppm乃至5000ppm的輕烴氣體無法達到脫氧要求。CN102850159A公開了一種采用堿金屬氧化物改性的納米級二氧化鈦為載體的脫氧催化劑,室溫下的脫氧深度較高,但制備工序復雜,且烯烴氣 體含氧量不宜過高。CN101745391A提出了一種以Pd為主活性組分,Ag、Au等為助活性劑組分的脫氧催化劑,具有抗毒能力強,床層不易飛溫的優點。但是這種脫氧催化劑在使用過程中會造成輕烴氣體0.5-1.7%的損耗。CN101165030A公開了Mn-Ag雙活性組分脫氧催化劑,脫氧效果較好。但所使用的混合物載體需要在1000℃以上煅燒3-8h,然后再粉碎、過篩。脫氧催化劑成本較高,且載體的比表面低,單位時間脫氧量較低,也會增加成本。綜上所述,現有的輕烴氣脫氧都是通過脫氧催化劑來實現,存在著催化劑成本昂貴,輕烴氣體有所損耗和脫氧容量低的問題。隨著我國輕烴產能的迅猛增長,對于輕烴氣脫氧的需求也越來越大。針對現在脫氧催化劑產量和性能的不足,研究新的輕烴氣脫氧技術有著巨大的潛在價值和廣闊的應用前景。技術實現要素:本發明的目的在于克服現有技術的上述技術問題,從而提供一種脫除含氧輕烴中氧氣的方法。本發明提供了一種脫除含氧輕烴中氧氣的方法,其中,該方法包括:(1)將含氧輕烴和非活潑性氣體混合,得到稀釋氣;(2)將所述稀釋氣和吸收劑送至吸收塔中進行接觸,得到塔釜物料和塔頂未被吸收的富氧氣,其中,所述吸收劑為碳四餾分和/或碳五餾分;其中,以所述碳四餾分的總重量為基準,所述碳四餾分含有10-50重量%的正丁烷、10-30重量%的異丁烷、1-10重量%的1-丁烯、15-35重量%的反-2-丁烯和15-25重量%的順-2-丁烯;以所述碳五餾分的總重量為基準,所述碳五餾分含有0.2-9重量%的異 戊烷、30-60重量%的正戊烷、10-20重量%的環戊烷、10-30重量%的2-甲基戊烷、5-15重量%的2,3-二甲基丁烷和5-15重量%的正己烷;所述含氧輕烴含有60重量%以上的單烯烴。本發明的方法中,用所述碳四餾分、碳五餾分代替脫氧催化劑作為含氧輕烴的吸收劑,大幅提高了脫氧容量,并且該方法工藝簡單,無需使用乙烯、丙烯制冷機和膨脹機,降低了投資和消耗。本發明的其它特征和優點將在隨后的具體實施方式部分予以詳細說明。附圖說明附圖是用來提供對本發明的進一步理解,并且構成說明書的一部分,與下面的具體實施方式一起用于解釋本發明,但并不構成對本發明的限制。在附圖中:圖1為根據本發明的一種實施方式的脫除含氧輕烴中氧氣的流程圖。附圖標記說明1-含氧輕烴氣;2-非活潑性氣體;3-稀釋氣;4-富非活潑性氣體;5-吸收劑;6-輕烴氣;7-補充的吸收劑;8-壓縮機;9-冷卻器;10-吸收塔;11-解吸塔;12-冷卻器;13-塔釜物料。具體實施方式以下對本發明的具體實施方式進行詳細說明。應當理解的是,此處所描述的具體實施方式僅用于說明和解釋本發明,并不用于限制本發明。本發明提供了一種脫除含氧輕烴中氧氣的方法,其中,該方法包括:(1)將含氧輕烴和非活潑性氣體混合,得到稀釋氣;(2)將所述稀釋氣和吸收劑送至吸收塔中進行接觸,得到塔釜物料和 塔頂未被吸收的富氧氣,其中,所述吸收劑為碳四餾分和/或碳五餾分;其中,以所述碳四餾分的總重量為基準,所述碳四餾分含有10-50重量%的正丁烷、10-30重量%的異丁烷、1-10重量%的1-丁烯、15-35重量%的反-2-丁烯和15-25重量%的順-2-丁烯;以所述碳五餾分的總重量為基準,所述碳五餾分含有0.2-9重量%的異戊烷、30-60重量%的正戊烷、10-20重量%的環戊烷、10-30重量%的2-甲基戊烷、5-15重量%的2,3-二甲基丁烷和5-15重量%的正己烷;所述含氧輕烴含有60重量%以上的單烯烴。本發明中,所述含氧輕烴可以為從煉廠工業裝置(例如催化裂化、焦化、雙氧水法制環氧丙烷等工業裝置)回收的含有60重量%以上的單烯烴的C2-C4烴類的混合氣,其單烯烴主要包括乙烯和/或丙烯,C2-C4烴類的其他成分包括:乙烷和丙烷等中的一種或多種。本領域公知的是,由于生產工藝的限制,所述C2-C4的烴類不可避免地含有氧氣,而氧氣的存在會在后續烯烴生產工業中存在例如爆炸的巨大的安全隱患,因此,有必要脫除所述烴類中的氧氣。根據本發明,所述含氧輕烴含有60重量%以上的單烯烴,在滿足該條件下,優選情況下,以所述含氧輕烴的總重量為基準,所述含氧輕烴中,C2-C4的單烯烴的含量為60-95重量%,C2-C4的烷烴的含量為1-25重量%,氧氣的含量為1重量%以上(優選3-10重量%)。此外,還可以含有氮氣、二氧化碳、C1-C3的醇、C4-C5的烷烴等中的一種或多種(作為余量氣體)。在滿足上述范圍的情況下,例如,以所述含氧輕烴的總重量為基準,所述含氧輕烴中,乙烯的含量為40-60重量%,丙烯的含量為15-25重量%,乙烷的含量為10-15重量%,丙烷的含量為2-7重量%,氧氣含量為3-5重量%,余量為氮氣、二氧化碳、C1-C3的醇、C4-C5的烷烴等中的一種或多種。再例如,以所述含氧輕烴的總重量為基準,所述含氧輕烴中,丙烯的含 量為80-95重量%,丙烷的含量為2-10重量%,氧氣含量為3-5重量%,甲醇的含量為2重量%以下,余量為氮氣、二氧化碳、C2-C3的醇、C4-C5的烷烴等中的一種或多種。本領域熟知的是,所述含氧輕烴在常溫常壓下為氣體。為了便于描述,本發明以下將氣體狀態的含氧輕烴稱為含氧輕烴氣。類似地,將脫氧得到的氣體狀態的輕烴稱為輕烴氣。步驟(1)中,所述含氧輕烴氣與非活潑性氣體混合,能夠降低輕烴和氧氣的濃度,使所述含氧輕烴氣遠離爆炸極限,保證后續步驟的安全進行。所述非活潑性氣體可以為本領域常規的不與或不促進氧氣和輕烴發生化學反應的任何氣體。從原料易得的角度出發,優選所述非活潑性氣體為氮氣。本發明對所述非活潑性氣體的用量沒有特別的限定,所述非活潑性氣體與所述富氧氣混合后,得到的稀釋氣中的氧濃度是越小越好。其中,優選情況下,步驟(1)中,所述含氧輕烴和非活潑性氣體的質量流量之比為1-6:1,更優選為3-6:1。本發明中,為了使步驟(1)得到稀釋氣進一步滿足吸收塔裝置的處理需要并降低吸收劑的使用量,將所述稀釋氣送至吸收塔之前,優選地,所述方法還包括將所述稀釋氣進行淺冷處理,更優選地,所述淺冷的過程包括:將所述稀釋氣的壓力壓縮為3-6MPa,然后將壓縮后的稀釋氣冷卻至5-20℃。該壓縮可以在壓縮機上進行,一般需要逐級提高壓力,本發明對壓縮的段數沒有特別限定,優選采用三段壓縮。根據本發明的脫氧方法,所述冷卻無需采用本領域常規使用的乙烯、丙烯制冷機和膨脹機,可以選用由溴化鋰吸收式制冷機提供的5℃左右的冷卻水為制冷劑,所述溴化鋰制冷機可以以工廠的廢熱蒸汽或熱水為熱源,具有能耗低的優點。因此,本發明的冷卻優選使用的冷卻器為溴化鋰吸收式制冷機。根據本發明,所述碳四餾分可以源自煉廠醚化反應后的碳四餾分。優選 情況下,以所述碳四餾分的總重量為基準,所述碳四餾分含有20-30重量%的正丁烷、10-20重量%的異丁烷、6-9重量%的1-丁烯、25-30重量%的反-2-丁烯和15-20重量%的順-2-丁烯。本發明中,所述碳五餾分可以源自戊烷油。優選情況下,以所述碳五餾分的總重量為基準,所述碳五餾分含有0.2-5重量%的異戊烷、30-40重量%的正戊烷、15-20重量%的環戊烷、20-30重量%的2-甲基戊烷、5-10重量%的2,3-二甲基丁烷和5-15重量%的正己烷。步驟(2)中,所述吸收塔的溫度可以根據吸收劑的種類和用量進行選擇,從提高吸收效果并降低能耗的角度出發,優選地,所述吸收塔的塔頂溫度為5-60℃(優選為10-20℃),塔釜溫度為80-200℃(優選為100-160℃)。在吸收塔中,所述吸收劑吸收含氧輕烴中的輕烴和可能存在的更重組分,得到塔釜物料,而未被吸收的更輕的含有氮氣富氧氣進入塔頂。本發明對所述吸收塔的理論板數和操作壓力沒有特別限定,通常隨著理論塔板數、操作壓力的提高,脫氧效果越好。為了在保證脫氧效果的同時,降低能耗,優選所述吸收塔的操作壓力為3-5MPa,理論塔板數為40-50。根據本發明,該方法還可以包括:將所述塔釜物料送至解析塔進行解析,從塔頂得到回收的輕烴,其中,所述塔釜物料可以依靠所述吸收塔與解吸塔之間的壓差進入到所述解析塔中,而無需額外施加壓力。通過控制所述解析塔中的條件可以將所述塔釜物料分離為吸收劑和輕烴,塔頂得到輕烴氣,塔釜為吸收劑。本發明對所述解析塔中的條件沒有特別限制,只要能將吸收劑和輕烴分離即可。優選地,所述解析塔的塔頂溫度為5-60℃(優選為10-20℃),塔釜溫度為80-200℃(優選為100-160℃)。從保證兩者的分離效果并降低能耗的角度出發,更優選地,所述解析塔的操作壓力為1-2.5MPa(優選為1.2-2.5MPa),理論塔板數為25-35。根據本發明的方法,優選所述方法還包括:從解析塔的塔釜回收吸收劑,并循環使用。但是為了能夠獲得較高的氧氣除去效果,還可以向解析塔的塔釜和/或吸收塔補充未經過吸收環節的新鮮的吸收劑,以使得吸收劑足以用于完成對含氧輕烴氣的吸收,例如補充的新鮮的吸收劑的質量流量與吸收塔中加入的吸收劑的質量流量比為1:500-2000。該補充的吸收劑也為所述碳四餾分和/或碳五餾分,補充的碳四餾分和/或碳五餾分的組成可以與之前采用的吸收劑的組成相同或不同。根據本發明的一種優選實施方式,采用如圖1所示的流程對含氧輕烴進行脫氧。其中,將來自工業裝置的含氧輕烴氣1與非活潑性氣體2混合,得到稀釋氣3,將稀釋氣3經過壓縮機8將壓力提高到3-6MPa;然后經冷卻器9冷卻至5-20℃,并送至吸收塔10中。將吸收劑5從吸收塔10的塔頂噴入,以吸收含氧輕烴氣1中的輕烴及更重組分,得到塔釜物料13和塔頂未被吸收的富非活潑性氣體4。將所述富非活潑性氣體4從塔頂排出。依靠壓差將塔釜物料13送至解吸塔11進行處理,從塔頂得到脫氧凈化后的輕烴氣6,并將其排出;塔釜得到貧吸收劑,經冷卻器12冷卻返回吸收塔循環使用。根據貧收劑的組成,任選在解吸塔11的塔釜加入補充的吸收劑7。步驟(2)中,進入到所述吸收塔的稀釋氣的流量可以根據吸收塔的設計和選型進行選擇。在此情況下,優選所述稀釋氣與所述吸收劑的質量流量之比為1:1-5,更優選為1:3-5。以下將通過實施例對本發明進行詳細描述。實施例1本實施例用于說明本發明的含氧輕烴的脫氧方法。本實施例處理的是雙氧水法制環氧丙烷工業裝置產生的含氧輕烴氣,含氧輕烴氣和碳四吸收劑的組成見表1所示。表1質量組成(重量%)含氧輕烴氣碳四吸收劑氮氣0.24-氧氣4.34-二氧化碳0.48-乙烷14.58-乙烯56.78-丙烷5.37-丙烯18.15-正丁烷0.0627.91異丁烷-15.591-丁烯-7.72異丁烯-0.04反-2-丁烯-28.44順-2-丁烯-20.23水-0.01二甲醚-0.06采用如圖1所示的流程將含氧輕烴進行脫氧,不同的是,不包括解析塔部分:將壓力為1.5MPa的表1所示的含氧輕烴氣與氮氣(質量流量比為6:1)混合,得到稀釋氣。將稀釋氣送至壓縮機8,將壓力提高至6MPa。增壓后的稀釋氣經冷卻器9冷卻到13℃,再以2613.56kg/h送入吸收塔10內,并將碳四吸收劑從塔頂以8000kg/h噴入,吸收含氧輕烴氣中的輕烴及更重的組分。吸收塔10的理論板數為40,操作壓力為5MPa,塔頂溫度為13.4℃,塔釜溫度為110.7℃,得到塔釜物料和塔頂未被吸收的富氮氣,富氮氣以588.55kg/h從塔頂排出。其中,富氮氣和塔釜物料的組成如表2所示。表2質量組成(重量%)富氮氣塔釜物料氮氣69.02-氧氣19.261ppm二氧化碳-0.12乙烷-3.66乙烯-14.23丙烷-1.35丙烯-4.55正丁烷3.1421.26異丁烷2.4811.821-丁烯1.045.87異丁烯0.010.03反-2-丁烯3.0221.66順-2-丁烯1.9915.41水0.03-二甲醚0.010.05實施例2本實施例用于說明本發明的含氧輕烴的脫氧方法。本實施例處理的是雙氧水法制環氧丙烷工業裝置產生的含氧輕烴氣,含氧輕烴氣和碳五吸收劑的組成如表3所示。表3質量組成(重量%)含氧輕烴氣碳五吸收劑氮氣0.36-氧氣4.39-二氧化碳0.23-甲醇1.04-丙烷4.780.02丙烯89.130.26正丁烷0.070.01異戊烷-0.63正戊烷-34.03環戊烷-17.052,3-二甲基丁烷-8.832-甲基戊烷-27.42正己烷-11.76采用如圖1所示的流程將含氧輕烴進行脫氧:將壓力為1MPa的表3所示的含氧輕烴氣與氮氣(質量流量比為5:1)混合,得到稀釋氣。將稀釋氣送至壓縮機8,將壓力提高至3.3MPa。增壓后的稀釋氣經冷卻器9冷卻到13℃,再以2382.17kg/h送入吸收塔10內,并將碳五吸收劑從塔頂以10000kg/h噴入,吸收含氧輕烴氣中的輕烴及更重的組分。吸收塔10的理論板數為40,操作壓力為3MPa,塔頂溫度為12.6℃,塔釜溫度為153.8℃,得到塔釜物料和塔頂未被吸收的富氮氣,富氮氣以534.3kg/hr從塔頂排出。依靠壓差將吸收塔的塔釜物料以12247.83kg/h送至解吸塔11處理。解吸塔11的理論板數為31,操作壓力為1.2MPa,塔頂溫度為26.9℃,塔釜溫度為151.5℃。從塔頂得到脫氧凈化后的輕烴氣,以2272.2kg/h排出;塔釜得到貧吸收劑,將其經冷卻至13℃,返回吸收塔10循環利用。在解吸塔釜補充24.33kg/h碳五餾分。富氮氣和輕烴氣的組成如表4所示。表4質量組成(重量%)富氮氣輕烴氣氮氣76.47-氧氣19.583ppm二氧化碳-0.24甲醇-1.09丙烷0.025.01丙烯0.2393.39正丁烷-0.08異戊烷0.010.02正戊烷1.940.17環戊烷0.6-2,3-二甲基丁烷0.24-2-甲基戊烷0.69-正己烷0.22-實施例3本實施例用于說明本發明的含氧輕烴的脫氧方法。本實施例處理的是雙氧水法制環氧丙烷工業裝置產生的含氧輕烴氣,含氧輕烴氣和碳四吸收劑,其組成見表5所示。表5質量組成(重量%)含氧輕烴氣碳四吸收劑氮氣0.24-氧氣3.21-二氧化碳0.31-甲醇1.33-丙烷1.91-丙烯92.94-正丁烷0.0627.91異丁烷-15.591-丁烯-7.72異丁烯-0.04反-2-丁烯-28.44順-2-丁烯-20.23水-0.01二甲醚-0.06采用如圖1所示的流程將含氧輕烴進行脫氧:將壓力為1.5MPa的表5所示的含氧輕烴氣與的氮氣(質量流量比為6:1)混合,得到稀釋氣。將稀釋氣送至壓縮機8,將壓力提高至3.6MPa。增壓后的稀釋氣3經冷卻器9冷卻到13℃,再以2543.92kg/h送入吸收塔10內,并將碳四吸收劑從塔頂以8000kg/h噴入,吸收含氧輕烴氣中的輕烴及更重的組分。吸收塔10的理論板數為40,操作壓力為3.4MPa,塔頂溫度為13.7℃,塔釜溫度為121.6℃,得到塔釜物料和塔頂未被吸收的富氮氣,富氮氣以566.42kg/h從塔頂排出。依靠壓差將塔釜物料以10377.50kg/h從解吸塔11的上部送入處理。解吸塔的理論板數為31,操作壓力為1.7MPa,塔頂溫度為40.9℃,塔釜溫度為105.5℃。從塔頂得到脫氧凈化后的輕烴氣,以2459.57kg/h排出;塔釜得到貧吸收劑,將其冷卻至13℃,返回吸收塔10循環利用。在解吸塔釜以82.07kg/h補充碳四餾分。富氮氣和輕烴氣的組成如表6所示。表6質量組成(%)富氮氣輕烴氣氮氣71.68-氧氣14.423ppm二氧化碳-0.32甲醇-1.37丙烷0.011.98丙烯0.1396.1正丁烷4.260.01異丁烷1.530.161-丁烯10.04異丁烯0.01-反-2-丁烯4.070.01順-2-丁烯2.890.01對比例1根據實施例2所述的方法,所不同的是,采用碳四餾分作為吸收劑,所 采用的碳四餾分如表7所示:表7質量組成(重量%)碳四餾分正丁烷29.56異丁烷0.141-丁烯11.86反-2-丁烯33.25順-2-丁烯24.23C5以上的烴類1富氮氣和輕烴氣的組成如表8所示:表8質量組成(重量%)富氮氣輕烴氣氮氣72.71-氧氣14.6311ppm二氧化碳-0.3甲醇-1.26丙烷-1.81丙烯0.1488.35正丁烷3.252.60異丁烷--1-丁烯0.361.23反-2-丁烯3.562.87順-2-丁烯5.171.58C5以上的烴類--對比例2根據實施例2所述的方法,所不同的是,采用的碳五餾分見表9所示:表9質量組成(重量%)碳五餾分異戊烷10正戊烷20.1異戊烯28.9正戊烯14.72-戊烯26.3富氮氣和輕烴氣的組成如表10所示:表10質量組成(重量%)富氮氣輕烴氣氮氣75.28-氧氣19.278ppm二氧化碳-0.22甲醇-1.02丙烷0.024.71丙烯0.1987.83正丁烷-0.07異戊烷0.150.73正戊烷1.481.22異戊烯0.531.98正戊烯1.260.722-戊烯1.951.5由以上的實施例1-3和對比例1-2可以看出,本發明的方法回收的輕烴氣中氧含量在3ppm以下,脫氧容量高,且輕烴基本沒有損耗。以上詳細描述了本發明的優選實施方式,但是,本發明并不限于上述實施方式中的具體細節,在本發明的技術構思范圍內,可以對本發明的技術方案進行多種簡單變型,這些簡單變型均屬于本發明的保護范圍。另外需要說明的是,在上述具體實施方式中所描述的各個具體技術特征,在不矛盾的情況下,可以通過任何合適的方式進行組合,為了避免不必 要的重復,本發明對各種可能的組合方式不再另行說明。此外,本發明的各種不同的實施方式之間也可以進行任意組合,只要其不違背本發明的思想,其同樣應當視為本發明所公開的內容。當前第1頁1 2 3