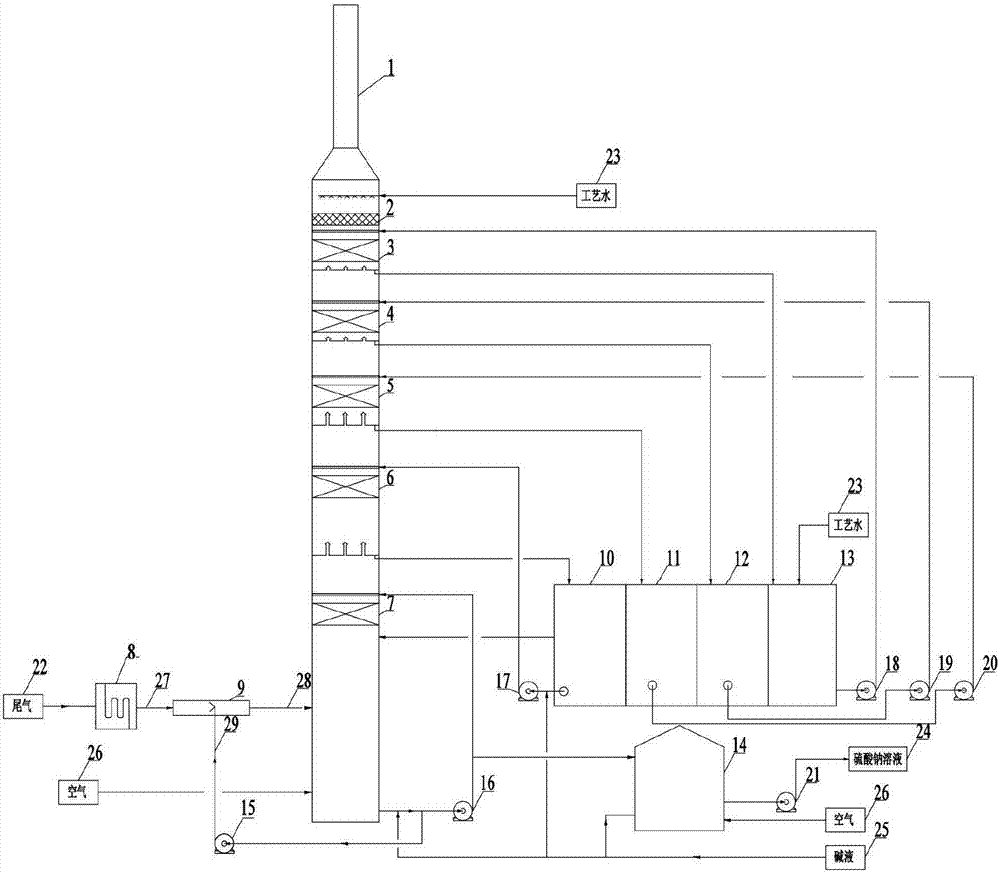
本發明涉及一種廢氣的處理方法,特別是一種含二氧化硫廢氣的處理方法。
背景技術:
:自上世紀30年代改良claus硫磺回收技術實現工業化生產以來,經過了近90年的發展和改進,已經趨于成熟和完善,但常用的二級claus硫磺回收裝置,煙氣中二氧化硫排放濃度通常在300-800mg/nm3,不能滿足現階段標準要求。現階段,硫磺回收裝置的尾氣處理常用的是還原-吸收法,即先把尾氣中含硫化合物全部還原為h2s,然后再將其脫除,最終以酸性氣或元素硫的形式回收,吸收液可循環再生使用。scot是典型的還原-吸收法,此工藝的主要缺陷是裝置投資、操作成本和能量消耗都相當高。氧化-吸收法也是尾氣處理的一種方法,其特點是先將尾氣中的含硫化合物全部氧化為so2,然后用溶液(或溶劑或堿液)吸收so2,最終以硫酸鹽、亞硫酸鹽或so2的形式回收。但大多數用于低so2濃度排煙脫硫或處理冶煉廠、硫酸廠的尾氣。尾氣焚燒部分是把回收硫磺后的尾氣直接灼燒,含硫化合物最終以so2的形式排入大氣,這些工藝尾氣排放的so2濃度均大于300mg/nm3。隨著世界各國保護大氣環境的標準日益嚴格,對硫磺回收裝置的硫回收率要求愈來愈高。中石化積極實施綠色低碳發展戰略,把降低硫磺回收裝置尾氣中的二氧化硫排放濃度作為煉油板塊爭創世界一流企業的重要指標之一,且《石油煉制工業污染物排放標準》(gb31570-2015)規定:現有企業自2017年7月1日起及新建企業自2015年7月1日起執行硫磺回收裝置二氧化硫排放濃度小于400mg/nm3(特定地區小于100mg/nm3)。二氧化硫減排勢在必行。鈉堿吸收工藝采用鈉堿中和的原理,反應速度快,吸收效果好,可大大降低煙氣中so2的排放。該工藝與還原類工藝相比,沒有加氫還原反應,省去了加氫還原反應器和再熱器;利用鈉堿作吸收劑,吸收尾氣中的硫化物,從而使尾氣達標排放;操作簡單;操作費用降低;占地面積也大大降低;排放指標能夠大大低于環保標準水平,處于工藝領先水平。鈉堿脫硫具有以下優點:吸收能力強,生產的鈉鹽溶解度大,可避免設備結垢和淤塞;在較低的循環液下就可得到較高的脫硫率。技術實現要素:發明目的:本發明目的是提供一種廢氣脫硫的方法,該方法可處理較高濃度(50000mg/nm3)的含so2高溫(170~350℃)廢氣,最終排放煙氣中的so2指標降低至50mg/nm3以下。本發明操作簡單,吸收能力強,生產的鈉鹽溶解度大,可避免設備結垢和淤塞等特點;在較低的循環液下就可得到較高的脫硫率;排放出的廢氣較清潔,幾乎不含無機微粒物質,不會造成霧霾天氣。技術方案:本發明目的是提供一種廢氣脫硫的方法,包括以下步驟:1)將廢氣與廢氣換熱器換熱,使廢氣溫度降至190~250℃;2)換熱后的廢氣進入急冷段,與吸收液順流接觸,廢氣經過絕熱飽和吸收溫度降至60-80℃;3)從急冷段流出的廢氣進入吸收塔下部,在吸收塔內上升進入第一吸收段,使廢氣在填料中與噴淋的吸收液接觸,吸收液吸收廢氣中的二氧化硫;4)從第一吸收段流出的廢氣在吸收塔內繼續上升進入第二吸收段,使廢氣在填料中與噴淋的吸收液接觸,除去廢氣中60~99.9%的剩余二氧化硫;5)從第二吸收段流出的廢氣在吸收塔內繼續上升進入多級水洗段,所述多級水洗段包含兩級以上的水洗段,廢氣與各級水洗段內噴淋的水在填料中接觸,除去廢氣中夾帶的鹽溶液;6)將從多級水洗段中流出的廢氣除去液滴后排放;吸收液為可吸收二氧化硫的堿性溶液。為了對高溫廢氣進行快速降溫,提高降溫效率,使急冷段為噴淋管,噴淋管設置為垂直管或水平管;當廢氣壓力較大時,為了提高降溫效率,在急冷管內,使廢氣與吸收液逆流接觸;當廢氣壓力較小時,為了減小廢氣的壓降損失,在急冷管內,使廢氣與吸收液順流接觸。吸收塔塔釜設有吸收液,塔釜的吸收液通過循環泵被輸送至急冷段噴淋,與廢氣接觸后重新回到塔釜;塔釜的吸收液通過飽和循環泵被輸送至第一吸收段上部進行噴淋,與廢氣接觸后重新回到塔釜。為了降低塔釜排出的吸收液中亞硫酸鈉含量,滿足cod排放標準,在塔釜的吸收液中均勻分布氧化性氣體,使吸收液中60~99.9%的亞硫酸鈉氧化為硫酸鈉;為了進一步氧化待排出的吸收液中的亞硫酸鈉,使塔釜與氧化罐相連,氧化罐中盛有堿液,在氧化罐中均勻分布氧化性氣體,使來自塔釜的吸收液在氧化罐內充分氧化后排出;具體地,使吸收液中剩余亞硫酸鈉的60~99.9%在氧化罐內氧化后排出;堿液為質量分數為1~30%的naoh溶液。為了節省成本,提高吸收液的使用率,將第二吸收段與吸收循環槽相連,吸收循環槽內的吸收液通過吸收循環泵輸送至第二吸收段上部進行噴淋,與廢氣接觸后的吸收液重新回到吸收循環槽。為了使吸收液在急冷段、第一吸收段和第二吸收段內充分吸收二氧化硫,將堿液加入到循環泵的入口,使堿液與吸收液充分混合。為了充分除去廢氣夾帶的鹽溶液,使步驟5)中,多級水洗段包括從下到上依次設置的一級水洗段、二級水洗段和三級水洗段,廢氣依次在一級水洗段、二級水洗段和三級水洗段中與噴淋的水逆流接觸;為了節省成本,提高水洗段水的利用率,將各級水洗段分別與水循環槽相連,水循環槽內的水通過循環泵被輸送至各級的水洗段上部進行噴淋,與廢氣接觸后重新回到水循環槽內。有益效果:本發明采用鈉堿吸收方法處理高濃度高溫含so2廢氣,采用鈉堿中和的原理,反應速度快,吸收效果好,可大大降低廢氣中so2的排放。本發明的方法與還原-吸收法相比,沒有加氫還原反應,省去了加氫還原反應器和再熱器;利用鈉堿作吸收劑,吸收尾氣中的硫化物能力強,可處理含二氧化硫濃度為300~50000mg/nm3的廢氣,最終排放的廢氣中二氧化硫濃度小于50mg/nm3,滿足現階段最嚴格的排放要求;產生的鈉鹽溶解度大,可避免設備結垢和淤塞;在循環液使用量較低的情況下就可得到較高的脫硫率,最終排放的廢氣幾乎不含無機微粒物質,不會造成霧霾天氣,煙氣排放蒸汽拖尾現象不明顯。本發明操作簡單,操作費用降低,占地面積也大大降低,排放指標能夠大大低于環保標準水平,處于工藝領先水平。附圖說明圖1為使用實施例1的方法處理含二氧化硫廢氣的流程圖;圖2為使用實施例2的方法處理含二氧化硫廢氣的流程圖。具體實施方式實施例1一種廢氣脫硫的方法,包括換熱、吸收、氧化和循環部分。圖1中,箭頭的方向表示氣體或液體的流動方向。如圖1所示,換熱主要在煙氣換熱器8和急冷段9中進行。來自硫磺回收的高so2濃度的高溫廢氣22首先經過煙氣換熱器8換熱,廢氣從300℃降至220℃。降溫后的廢氣27從急冷段9的頂部進入,急冷段9為垂直的噴淋管,塔底部的吸收液被急冷循環泵15輸送至急冷段9作為急冷循環液29噴淋,氣液兩相逆流接觸,對高溫廢氣進行絕熱飽和降溫,廢氣經過絕熱飽和吸收,溫度由220℃降至75℃,同時廢氣中的部分二氧化硫被循環液吸收。吸收主要在吸收塔內進行。吸收塔包含三段,自下而上分別為第一吸收段7,第二吸收段6和水洗段,水洗段又分為一級水洗段5、二級水洗4和三級水洗3,每段每級均設噴頭、液體分布器和填料等。在急冷段中降溫后的廢氣以氣液混合物28的形式從急冷段9進入吸收塔下部,廢氣再由吸收塔下部上升至第一吸收段7,飽和循環泵16將塔底部的吸收液輸送至第一吸收段7上部噴淋,在填料段與上升的廢氣逆流接觸,吸收廢氣中的部分二氧化硫。經第一吸收段7處理的廢氣上升至第二吸收段6,吸收循環泵17將來自吸收段的吸收液輸送至第二吸收段6上部噴淋,充分吸收廢氣中剩余的二氧化硫,除去廢氣中60~99.9%的剩余二氧化硫,反應如下:2naoh+so2→na2so3+h2o;na2so3+h2o+so2→2nahso3;在第二吸收段6中,廢氣中所有的so2被吸收液吸收。廢氣繼續上行至一級水洗段5、二級水洗段4和三級水洗段3,一級水洗泵20、二級水洗泵19和三級水洗泵18分別將一級水循環槽11、二級水循環槽12和三級水循環槽13中的工藝水輸送至各段的填料中,廢氣在一級水洗段5、二級水洗段4和三級水洗段3中分別與來自一級水洗泵20、二級水洗泵19和三級水洗泵18的工藝水逆流接觸,除去尾氣中夾帶的鹽溶液霧滴,廢氣得到進一步凈化;尾氣最后經過除沫器2、煙囪1排放至大氣。工藝水23進入除沫器上方的噴淋器進行噴淋。循環槽用來收集各段各級集液盤上溢流的溶液,吸收液循環槽10與一級水循環槽11、二級水循環槽12和三級水循環槽13是四合一設備,四合一設備的設計可減少占地面積,降低投資。在吸收塔塔釜設置空氣分布管,均勻分布空氣,以充分均勻氧化吸收液,吸收液中部分na2so3氧化成硫酸鈉,具體地,使吸收液中60~99.9%的亞硫酸鈉在塔釜氧化為硫酸鈉;部分氧化后的吸收液再輸送到氧化罐14中,在氧化罐14中加入堿液25和空氣26,將nahso3中和為na2so3,同時在氧化罐底部設計空氣分布管,均勻分布空氣,反應如下:nahso3+naoh→na2so3+h2o;2na2so3+o2→2na2so4;具體地,使吸收液中剩余亞硫酸鈉的60~99.9%在氧化罐內氧化后排出,堿液為質量分數為1~30%的naoh溶液。使得氧化后氧化罐14內的吸收液滿足cod排放標準《石油煉制工業污染物排放標準》(gb31570-2015)的規定,最后通過外送泵21加壓將硫酸鈉溶液24送到污水處理廠。堿液25加入到循環泵15、循環泵16和循環泵17的入口,經過離心泵的高速旋轉使其與吸收液充分混合,更有利于吸收so2;在氧化罐14中加入少量堿液,使得外排鹽水滿足標準《石油煉制工業污染物排放標準》(gb31570-2015)中外排污水ph的要求。各段堿液的注入量均由ph分析儀控制。將本實施方式的方法應用于福建12萬噸/年硫磺回收裝置中,吸收效果較好,吸收洗滌后的尾氣達到下表所列的濃度:表1名稱處理前的二氧化硫濃度二氧化硫排放濃度12萬噸/年硫磺回收裝置3000mg/nm330mg/nm3本方法采用吸收液多級多梯度吸收尾氣中的so2,從而達到降低sθ2排放的目的。實施例2如圖2所示,除將實施例1中作為急冷管9的垂直噴淋管替換為水平噴淋管,使急冷管9內的氣液逆流接觸,并將吸收液循環槽10、一級水循環槽11、二級水循環槽12和三級水循環槽13分開布置外,其余與實施例1相同,在此不再贅述。當前第1頁12