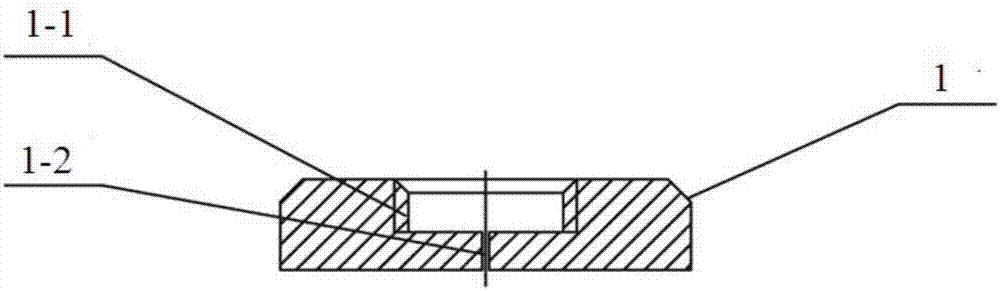
本發明屬于化工萃取
技術領域:
,特別涉及一種微萃取組件、微萃取裝置及萃取方法。
背景技術:
:萃取是利用物質在兩種互不相溶(或微溶)的溶劑中溶解度或分配系數的不同,使物質從一種溶劑內轉移到另外一種溶劑中。作為一種重要的分離單元操作,廣泛應用于化學、化工、冶金、食品加工等領域。目前,工業上主要采用溶劑萃取法,通過將一相在外界作用力下分散到另外一相中進行接觸傳質,與此相對應的常用萃取設備有萃取塔、混合澄清槽(萃取槽)等。這些萃取設備往往不能有效強化微觀傳質,而且萃取設備結構復雜龐大、生產耗能大、效率低下,已經成為萃取過程強化需突破的瓶頸。隨著萃取技術的發展,近年來出現了強化傳質的微萃取技術,所述微萃取技術是利用微尺度效應,在有限的尺度內液體的表面積與體積的比值急劇增大,使得傳質距離減小,傳質所需時間減少。微萃取技術使用的微萃取設備分為膜萃取和微通道兩種類型。cn201410487172.6公開了一種膜萃取裝置與方法,所述膜萃取裝置包括膜萃取組件和固定壓緊膜萃取組件的至少兩個壓緊板,膜萃取組件包括至少一個第一引流片、至少一個第二引流片及插在相鄰兩個引流片之間的濾膜,濾膜與引流片的流道形成封閉腔體,以允許液體在其中流動,第一引流片的過液孔與相鄰第二引流片的進口或出口連通,第二引流片的過液孔與相鄰第一引流片的進口或出口連通。此種膜萃取裝置是通過引流板提高濾膜兩側萃取液和原液的濃度差來提高萃取效率,但由于傳質方式僅靠對流或平行流,因而易滲透,萃取效率提高幅度不大,且需要多級引流板和濾膜連續使用,結構較為復雜。微通道萃取裝置包括輸送泵及與輸送泵連接的微通道,在輸送泵的驅動下水相和有機相液體進入微通道,在微通道中完成萃取。此種結構的微萃取裝置雖然萃取率高,但受微通道的限制,處理量小(處理量一般為微升級),難于在化工、冶金等領域滿足工業化生產的需要,且屬于被動混合傳質,影響傳質性能。技術實現要素:本發明的目的在于克服現有技術存在的不足,提供一種微萃取組件和超重力場微萃取裝置及萃取方法,在保持高萃取率的條件下增大處理量、縮短分相時間,以滿足化工、冶金等領域萃取工業化生產的需要。本發明所述微萃取組件,由親油性上盤和親水性下盤組成,所述上盤的外形為圓臺形、下大上小的階梯圓臺形或下大上小的圓錐臺形,上盤中心部位設置有微流體通道,底面為平面,所述下盤的外形為圓臺形、上大下小的階梯圓臺形或上大下小的圓錐臺形,下盤頂面中心部位設置有進料凹槽,從進料凹槽至下盤頂面邊緣分布有微形槽;組合方式為:上盤設置的微流體通道中心線與下盤頂面設置的進料凹槽中心線重合,上盤的底面與下盤的頂面之間具有0.05~0.25mm的間隙。上述微萃取組件,下盤頂面的微形槽有多種形態,可呈螺旋形、弧形或蜂窩形分布。上述微萃取組件,所述微形槽的寬度為0.25~1mm,深度為0.25~0.75mm。上述微萃取組件,所述微流體通道優選圓孔形通道,圓孔形通道的孔徑為0.25~3mm。上述微萃取組件,所述上盤采用疏水性材料制作或在上盤底面涂抹疏水性修飾劑形成,疏水性材料為聚乙烯或聚四氟乙烯,它們的密度均為0.940~0.976g/cm3,疏水性修飾劑為聚二甲基硅氧烷或氟化硅烷;所述下盤采用親水性材料制作或在下盤頂面涂抹親水性修飾劑形成,親水性材料為不銹鋼,親水性修飾劑為二甲基甲酰胺或丙烯酸脂。本發明所述超重力場微萃取裝置包括上述微萃取組件、進料混合器、聯接體、接料槽、防護罩、軸套、減速器、電機和支撐系統;所述支撐系統由底座、固定在底座上的立柱及安裝在立柱上的第一承載板和第二承載板組成,所述聯接體安裝在第二承載板底面,聯接體的中心部位設置有插孔,所述進料混合器設置有兩個進料口和一個出料口,進料混合器設置出料口的部段穿過第二承載板上的通孔插裝在聯接體中心部位設置的插孔內,所述接料槽安裝在第一承載板頂面,接料槽上設置有出料口,所述防護罩安裝在第一承載板頂面并位于接料槽內,所述減速器安裝在第一承載板底面,且減速器的動力輸出軸軸線與連接體的中心線重合,減速器的動力輸出軸穿過第一承載板上設置的通孔進入防護罩,所述電機通過支架安裝在第一承載板底面或由立柱支承,電機的動力輸出軸與減速器的動力輸入軸連接,所述軸套固定在微萃取組件中的下盤底面,且軸套的中心線與下盤的中性線重合,微萃取組件中的下盤通過軸套與減速器的動力輸出軸連接并位于接料槽內,萃取組件中的上盤與聯接體連接,連接時應使上盤設置的微流體通道的中心線與聯接體設置的插孔的中心線重合,且符合上盤與下盤的組合方式,即上盤設置的微流體通道中心線與下盤頂面設置的進料凹槽中心線重合,上盤的底面與下盤的頂面之間具有0.05~0.25mm的間隙。上述超重力場微萃取裝置,所述進料混合器為內徑是0.25~3mm的圓管組合成的三通管,有兩個進料管和一個出料管,兩個進料管的中心線之間的夾角α為30°~330°;所述聯接體中心部位設置的進料件安裝孔為圓形通孔,該圓形通孔的孔徑與料混合器的出料管外徑匹配。上述超重力場微萃取裝置,所述軸套與減速器動力輸出軸的連接方式為鍵連接,且軸套中配置有萃取過程中調節上盤與下盤之間間隙的彈簧,彈簧套裝在減速器動力輸出軸上,其下端由軸套內壁設置的臺階支承,其上端與下盤的底面接觸。使用本發明所述重力場微萃取裝置進行萃取的操作如下:(1)啟動電機,使減速器的動力輸出軸帶動下盤轉動;(2)將有機相和水相分別通過進料混合器的兩個進料口送入進料混合器,有機相和水相依次經進料混合器出料口、上盤中心部位設置的微流體通道進入上盤底面和下盤頂面之間的間隙區間,有機相附著在親油性上盤底面,水相附著在親水性下盤頂面,它們在下盤旋轉產生的離心力作用下不斷更新接觸表面積進行流動傳質,流動傳質后的水相和有機相在離心力作用下被甩出至接料槽中,并從接料槽設置的出料口排出;(3)收集接料槽出料口的排出物,并將所述排出物靜置分相。本發明具有以下有益效果:1、使用本發明所述超重力場微萃取裝置和萃取方法,由于有機相和水相進入萃取組件的親油性上盤底面和親水性下盤頂面之間的間隙區間并分別附著在親油性上盤底面和親水性下盤頂面,在下盤旋轉產生的離心力作用下不斷更新接觸表面積進行流動傳質,因而萃取率高,經一級萃取后萃取率基本可達到平衡,實驗表明,對濕法磷酸進行萃取,萃取率高于傳統液-液萃取的萃取率(見實施例3和對比例)。2、使用本發明所述超重力場微萃取裝置和萃取方法,由于有機相和水相在下盤旋轉的狀態下位于上盤底面和下盤頂面之間進行流動傳質,增大了兩相的接觸面積,加快了兩相接觸流動速度,縮短了萃取時間,因而增大了處理量,實驗表明,對濕法磷酸進行萃取,處理量可達60m3·h-1·m-2,達到了工業化生產水平標準。3、使用本發明所述超重力場微萃取裝置和萃取方法,由于有機相和水相分別附著在親油性上盤底面和親水性下盤頂面,在下盤旋轉產生的離心力作用下進行流動傳質,因而在萃取過程中不會導致兩相乳化。4、使用本發明所述超重力場微萃取裝置和萃取方法,流動傳質后的水相和有機相分相時間短,實驗表明,對濕法磷酸進行萃取時,通過接料槽出料口收集的排出物,靜置后可立即分相。5、由于本發明所述萃取組件的親水性下盤頂面設置有微形槽,因而可增大下盤頂面的表面積,有利于提高處理量。6、由于本發明所述超重力場微萃取裝置中軸套與減速器動力輸出軸的連接方式為鍵連接,且軸套中配置有萃取過程中調節上盤與下盤之間間隙的彈簧,因而有利于萃取的正常進行。7、本發明所述超重力場微萃取裝置結構簡單,萃取組件易于拆卸清洗,不會造成堵塞,且萃取時操作方便,因而易于推廣使用。附圖說明圖1是本發明所述微萃取組件的一種結構示意圖;圖2是微萃取組件中親油性上盤的一種示意圖;圖3是微萃取組件中親水性下盤的一種示意圖;圖4是親水性下盤頂面設置的微型槽的第一種形態示意圖,微型槽呈螺旋形分布;圖5是親水性下盤頂面設置的微型槽的第二種形態示意圖,微型槽呈弧形分布;圖6是親水性下盤頂面設置的微型槽的第三種形態示意圖,微型槽呈蜂窩形分布;圖7是本發明所述超重力場微萃取裝置的一種結構示意圖;圖8是圖7的俯視圖;圖9是本發明所述超重力場微萃取裝置中進料混合器的第一種示意圖;圖10是本發明所述超重力場微萃取裝置中進料混合器的第二種示意圖;圖11是本發明所述超重力場微萃取裝置中進料混合器的第三種示意圖;圖12是本發明所述超重力場微萃取裝置中聯接體的示意圖;圖13是本發明所述超重力場微萃取裝置中親水性下盤、軸套、減速器動力輸出軸和彈簧的組合示意圖。圖中,1—上盤、1-1—第一螺孔、1-2—微流體通道、2—下盤、2-1—進料凹槽、2-2—微形槽、3—接料槽出料口、4—減速器動力輸出軸、5—底座、6—立柱、7—電機、8—減速器、9—第一承載板、10—防護罩、11—接料槽、12—軸套、13—第二承載板、14—進料混合器、15—聯接體、15-1—插孔、15-2—第二螺孔、15-3—外螺紋段、16—平鍵、17—彈簧。具體實施方式下面通過實施例并結合附圖對本發明所述微萃取組件、超重力場微萃取裝置及萃取方法作進一步說明。實施例1本實施例中,微萃取組件如圖1、圖2、圖3所示,由親油性上盤1和親水性下盤2組成;所述上盤1用密度為0.950g/cm3的聚乙烯制作,其外形為圓臺形,圓臺的直徑為90mm,上盤的底面為平面,中心部位從上至下依次設置有第一螺孔1-1和微流體通道1-2,微流體通道1-2為圓孔形通道,其孔徑為1mm,第一螺孔1-1用于安裝固定;所述下盤2用不銹鋼制作,其外形為上大下小的階梯圓臺形,位于最上部的圓臺的直徑為100mm,下盤頂面中心部位設置有進料凹槽2-1,從進料凹槽至下盤頂面邊緣分布有螺旋形微形槽2-2,如圖4所示,螺旋形微形槽的寬度為0.5mm,深度為0.25mm;上盤與下盤的組合方式為:上盤設置的微流體通道1-2中心線與下盤頂面設置的進料凹槽2-1中心線重合,上盤1的底面與下盤的頂面之間具有0.07mm的間隙。實施例2本實施例中,超重力場微萃取裝置如圖8、圖9所示,包括實施例1所述微萃取組件、進料混合器14、聯接體15、接料槽11、防護罩10、軸套12、減速器8、電機7、平鍵16和支撐系統;所述支撐系統由圓臺形底座5、均勻分布且固定在底座上的四根橫截面為圓形的立柱6及相隔一定間距安裝在立柱上的圓形第一承載板9和圓形第二承載板13組成;所述進料混合器如圖10所示,為內徑0.8mm、外徑1mm的圓管組合成的三通管,有兩個進料管和一個出料管,兩個進料管的中心線之間的夾角α為120°;所述聯接體15如圖13所示,為上大下小的階梯圓臺體,中心部位設置有插孔15-1,頂面設置有第二螺孔15-2,下部段為外螺紋段15-3,所述插孔15-1為圓形通孔,該圓形通孔的孔徑與進料混合器的出料管外徑匹配,所述外螺紋段15-3與實施例1中上盤設置的第一螺孔1-1匹配;所述軸套12如圖13所示,內孔為階梯孔,其中大孔部段的孔徑與彈簧17的外徑匹配,小孔部段的孔徑與減速器動力輸出軸4的外徑匹配,并設置有平鍵槽;所述減速器8為齒輪減速器,齒輪減速器應滿足在電機帶動下其動力輸出軸的轉速為250rad/min。上述構件或部件的組合方式:所述聯接體15安裝在第二承載板13底面,與第二承載板螺紋連接,所述進料混合器14的出料管穿過第二承載板上的通孔插裝在聯接體中心部位設置的插孔15-1內,所述接料槽11安裝在第一承載板9頂面,接料槽側面設置有出料口3,所述防護罩10安裝在第一承載板頂面并位于接料槽11內,所述減速器8安裝在第一承載板底面,且減速器的動力輸出軸軸線與連接體15的中心線重合,減速器的動力輸出軸4穿過第一承載板上設置的通孔進入防護罩10,所述電機7通過支架安裝在第一承載板底面,電機7的動力輸出軸與減速器的動力輸入軸連接,所述軸套12位于微萃取組件中的下盤2底面,與下盤為一體化結構,且軸套12的中心線與下盤2的中性線重合,微萃取組件中的下盤2通過軸套12與減速器的動力輸出軸4連接并位于接料槽11內,所述軸套12與減速器動力輸出軸4的連接方式為鍵連接(通過平鍵16),軸套內配置有彈簧17,所述彈簧17套裝在減速器動力輸出軸4上,其下端由軸套內壁的臺階支承,其上端與下盤的底面接觸,萃取組件中的上盤1與聯接體連接,連接時應使上盤1設置的微流體通道1-2的中心線與聯接體設置的插孔15-1的中心線重合,從而保證上盤1設置的微流體通道1-2中心線與下盤頂面設置的進料凹槽2-1中心線重合,并使上盤1的底面與下盤的頂面之間具有0.07mm的間隙。實施例3本實例使用實施例2所述超重力場微萃取裝置萃取濕法磷酸,被凈化濕法磷酸的主要組成見表1。表1被凈化濕法磷酸的組成組分p2o5fe3+so42-f-含量wt%45.410.575.060.13萃取劑由磷酸三丁酯(tbp)與煤油按體積比5:1配制而成,有機相(萃取劑)與水相(被凈化濕法磷酸)的相比為4:1。操作如下:(1)將磷酸三丁酯(tbp)與煤油按體積比5:1配制而成萃取劑并將萃取劑預熱至50℃;(2)啟動電機,使減速器的動力輸出軸帶動下盤2以250rad/min的轉速轉動;(3)將預熱后的萃取劑和處于常溫下的被凈化濕法磷酸分別以400ml/min、100ml/min的流量通過進料混合器14的兩個進料口送入進料混合器,萃取劑和被凈化濕法磷酸依次經進料混合器出料口、上盤中心部位設置的微流體通道1-2進入上盤底面和下盤頂面之間的間隙區間,萃取劑附著在親油性上盤底面,被凈化濕法磷酸附著在親水性下盤頂面,它們在下盤旋轉產生的離心力作用下不斷更新接觸表面積進行流動傳質,流動傳質后形成的混合液在離心力作用下被甩出至接料槽中,并從接料槽設置的出料口排出;(4)收集接料槽出料口排出的萃取液,并將所述萃取液靜置分相。本實施例中,濕法磷酸的處理量為100ml/min。實驗結果表明,所述萃取液靜置后可立即分相。對傳質形成的萃取液進行磷酸萃取率測定與計算(萃取率e%=有機相中磷酸質量/原料酸中磷酸質量×100%),計算結果:磷酸的萃取率為63.72%。對比例本對比例被凈化濕法磷酸與實施例3相同,萃取裝置采用現有常規槽式萃取裝置,萃取方法為普通萃取攪拌法。萃取劑及萃取時的工藝參數:萃取劑由磷酸三丁酯(tbp)與煤油按體積比5:1配制而成,有機相(萃取劑)與水相(被凈化濕法磷酸)的相比為4:1,萃取溫度為50℃,攪拌漿在轉速為250rad/min,萃取時間為10min。對在50℃經過10min傳質形成的萃取液靜置分相,分相時間為5min。對在50℃經過10min傳質形成的萃取液進行磷酸萃取率測定與計算(萃取率e%=有機相中磷酸質量/原料酸中磷酸質量×100%),計算結果:磷酸的萃取率為53.13%。實施例3和對比例表明,本發明所述超重力場微萃取裝置和萃取方法的萃取率和分相時間都優于目前的常規萃取設備。本發明不限于上述實施例,根據本發明的技術方案可設計出多種具體結構的微萃取組件和超重力場微萃取裝置。當前第1頁12