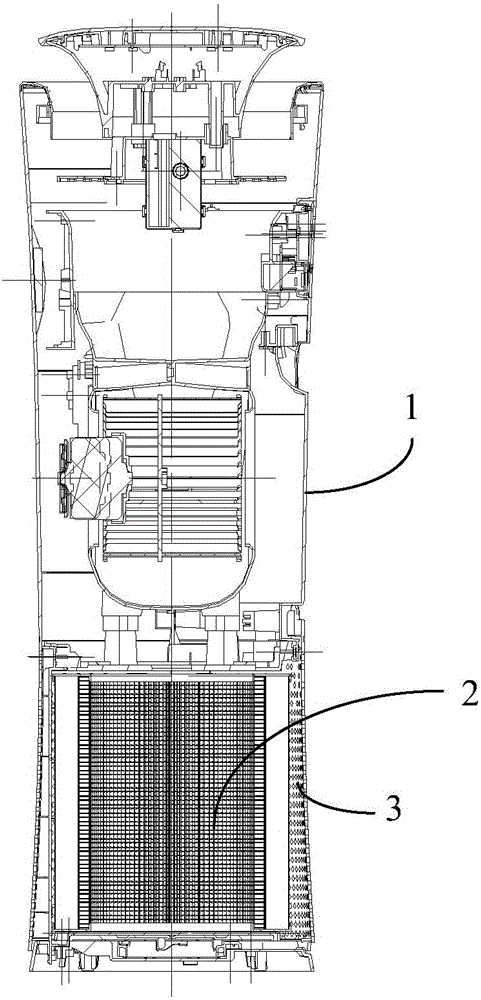
本發明涉及空氣凈化
技術領域:
,特別涉及一種濾芯材料的制備方法、濾芯材料和空氣凈化器。
背景技術:
:在目前常見的空氣凈化器中,常見的濾芯材料有活性炭等,然而,現有的濾芯材料對甲醛等有害氣體的去除方式主要為物理吸附,由于其對有害氣體,尤其是甲醛,容易達到吸附飽和狀態,故吸附性能不高,導致濾芯材料對甲醛的去除效率低且使用壽命較短,進而制約了空氣凈化器的凈化性能的提高。技術實現要素:本發明的主要目的是提供一種濾芯材料的制備方法,旨在提高濾芯材料對甲醛氣體的去除效率的同時,提高濾芯材料的使用壽命。為實現上述目的,本發明提出的濾芯材料的制備方法,包括以下步驟:步驟一、制備包含過渡金屬氧化物前驅體的溶液;步驟二、將包含過渡金屬氧化物前驅體的溶液,在160~220℃以及在0.9~1.1Mpa的壓力條件下,反應18~24小時,以發生水熱晶化反應制成過渡金屬氧化物晶粒的懸浮液;步驟三、對過渡金屬氧化物晶粒的懸浮液進行離心處理,分離得到過渡金屬氧化物的固態產物;步驟四、將過渡金屬氧化物的固態產物經干燥處理后,于450~550℃下進行焙燒處理,得到過渡金屬氧化物的活性粉體;步驟五、將過渡金屬氧化物的活性粉體與成型助劑充分混合后,通過成型機成型成半成品,然后再將半成品經過干燥和焙燒得到濾芯材料。優選地,所述過渡金屬氧化物前驅體的溶液是經過以下步驟制成:將過渡金屬前驅鹽用去離子水完全溶解成濃度40~50g/L的過渡金屬前驅鹽溶液,將堿用去離子水完全溶解成濃度8~10g/L的堿溶液;將過渡金屬前驅鹽溶液和堿溶液按照1:1.6~2的質量比同時注入水熱反應釜中且通過攪拌以混合均勻,并同時控制反應釜中混合液的pH值為9.5~10.5,反應釜溫度為75~85℃,攪拌槳的轉速為50~150轉/分鐘。優選地,所述過渡金屬前驅鹽為氯化錳、醋酸錳、硫酸錳、以及硝酸錳中的至少一種,堿為氫氧化鈉、氫氧化鉀中的至少一種。優選地,步驟二中所述的過渡金屬氧化物晶粒由混合多價態過渡金屬氧化物組成,所述過渡金屬氧化物晶粒的粒徑為納米級。優選地,步驟四中的干燥溫度為80~140℃,且干燥后的過渡金屬氧化物的活性粉體的水分含量在6%~8%。優選地,所述成型助劑為粘土材料。優選地,所述過渡金屬氧化物的活性粉體與成型助劑的質量比為1:2~3。優選地,步驟五中的干燥溫度為100~130℃,干燥后的濾芯材料的水分含量在1%~4%,焙燒溫度為400~500℃。本發明還提出一種濾芯材料,所述濾芯材料為顆粒狀,每一顆粒狀的濾芯材料的表面與內部均具有多個微米級的微孔。其中,所述濾芯材料的制備方法包括以下步驟:步驟一、制備包含過渡金屬氧化物前驅體的溶液;步驟二、將包含過渡金屬氧化物前驅體的溶液,在160~220℃以及在0.9~1.1Mpa的壓力條件下,反應18~24小時,以發生水熱晶化反應制成過渡金屬氧化物晶粒的懸浮液;步驟三、對過渡金屬氧化物晶粒的懸浮液進行離心處理,分離得到過渡金屬氧化物的固態產物;步驟四、將過渡金屬氧化物的固態產物經干燥處理后,于450~550℃下進行焙燒處理,得到過渡金屬氧化物的活性粉體;步驟五、將過渡金屬氧化物的活性粉體與成型助劑充分混合后,通過成型機成型成半成品,然后再將半成品經過干燥和焙燒得到濾芯材料。本發明還提出一種空氣凈化器,包括濾芯材料以及機身,所述機身包括設于機身內部的濾芯,所述濾芯包括多層間隔設置的過濾網材,所述濾芯材料填充于兩過濾網材的夾層中。本發明的技術方案中,相較于目前常見的主要由活性炭組成的濾芯材料,本發明的制備方法所制成的濾芯材料對甲醛的凈化性能的提高主要由以下兩方面實現:一方面,由于濾芯材料以混合多價態過渡金屬氧化物為催化活性組分,其價態的不斷循環轉化,可使晶粒表面的晶格氧原子有相當強的可移動性,因而催化的活性較高,同時,晶粒的納米級結構也有利于催化活性的提高,如此,就使得其對甲醛進行催化而去除的效率提高,且由于能循環反應,不易出現吸附飽和的現象,故其材料使用壽命也得到提高;另一方面,由于多個晶粒團聚成活性粉體的顆粒,每一活性粉體的顆粒的微觀結構中存在晶粒之間的通道或微孔等,同時,每一顆粒狀的濾芯材料的成品的表面與內部也存在眾多微孔,可以理解,如此高的孔隙率可使濾芯材料對甲醛的吸附能力以及吸附容量等大大提高,從而可提高去除甲醛的效率以及材料的使用壽命。附圖說明為了更清楚地說明本發明實施例或現有技術中的技術方案,下面將對實施例或現有技術描述中所需要使用的附圖作簡單地介紹,顯而易見地,下面描述中的附圖僅僅是本發明的一些實施例,對于本領域普通技術人員來講,在不付出創造性勞動的前提下,還可以根據這些附圖示出的結構獲得其他的附圖。圖1為本發明濾芯材料的制備方法一實施例的工藝流程圖;圖2為本發明空氣凈化器的結構示意圖。附圖標號說明:標號名稱標號名稱1機身2濾芯3進風格柵板本發明目的的實現、功能特點及優點將結合實施例,參照附圖做進一步說明。具體實施方式下面將結合本發明實施例中的附圖,對本發明實施例中的技術方案進行清楚、完整地描述,顯然,所描述的實施例僅僅是本發明的一部分實施例,而不是全部的實施例。基于本發明中的實施例,本領域普通技術人員在沒有作出創造性勞動前提下所獲得的所有其他實施例,都屬于本發明保護的范圍。需要說明,若本發明實施例中有涉及方向性指示(諸如上、下、左、右、前、后……),則該方向性指示僅用于解釋在某一特定姿態(如附圖所示)下各部件之間的相對位置關系、運動情況等,如果該特定姿態發生改變時,則該方向性指示也相應地隨之改變。另外,若本發明實施例中有涉及“第一”、“第二”等的描述,則該“第一”、“第二”等的描述僅用于描述目的,而不能理解為指示或暗示其相對重要性或者隱含指明所指示的技術特征的數量。由此,限定有“第一”、“第二”的特征可以明示或者隱含地包括至少一個該特征。另外,各個實施例之間的技術方案可以相互結合,但是必須是以本領域普通技術人員能夠實現為基礎,當技術方案的結合出現相互矛盾或無法實現時應當認為這種技術方案的結合不存在,也不在本發明要求的保護范圍之內。本發明提出一種濾芯材料的制備方法。如圖1所示,在實施例1中,本發明提出的濾芯材料的制備方法如下:步驟一、于水熱反應釜中制備包含過渡金屬氧化物前驅體的溶液;步驟二、在水熱反應釜中,將包含過渡金屬氧化物前驅體的溶液在220℃以及在1.1Mpa的壓力條件下,反應18小時,以發生水熱晶化反應制成過渡金屬氧化物晶粒的懸浮液;步驟三、將過渡金屬氧化物晶粒的懸浮液降至室溫后取出,離心分離得到過渡金屬氧化物的固態產物;步驟四、將過渡金屬氧化物的固態產物經干燥處理后,于550℃下進行焙燒處理,得到過渡金屬氧化物的活性粉體;步驟五、將過渡金屬氧化物的活性粉體與成型助劑充分混合后,通過成型機成型成半成品,然后再將半成品經過干燥和焙燒得到濾芯材料。具體地,包含過渡金屬氧化物前驅體的溶液是經過以下步驟制成:首先,將過渡金屬前驅鹽粉體用去離子水完全溶解成濃度40~50g/L的過渡金屬前驅鹽溶液,將堿用去離子水完全溶解成濃度38~45g/L的堿溶液;然后,將過渡金屬前驅鹽溶液和堿溶液按照1:2的質量比同時注入水熱反應釜中且通過攪拌以混合均勻,并同時控制反應釜中混合液的pH值為9.5~10.5,反應釜溫度為75~85℃,攪拌槳的轉速為50~150轉/分鐘。在注入完成后即可進入步驟2,此時,在反應釜中的混合液應包含過渡金屬氧化物的前驅體及堿等。在本實施例中,過渡金屬前驅鹽為氯化錳,堿為氫氧化鈉,在堿性環境下,可生成非晶態的錳的氧化物前驅體,該非晶態的錳的氧化物前驅體在步驟二中可發生水熱晶化反應,從而制得錳的氧化物晶粒。在本實施例的步驟一中,將過渡金屬前驅鹽溶液與堿溶液同時注入,且控制反應釜中混合液的pH值為9.5~10.5可使得反應更充分;而反應釜溫度范圍優選設置為75~85℃,是為了提高反應物的生成率,當溫度低于75℃時,其反應速率降低,且會產生其他雜質,當溫度低于85℃時,其雜質產生率也會提高;通過攪拌槳的攪拌,且攪拌槳的轉速優選設為為50~150轉/分鐘,可使兩溶液混合更均勻,以使得反應更充分,在此,轉速應低于150轉/分鐘,若轉速太高,則會增加對攪拌設備的損耗。在步驟二中,錳的氧化物晶粒由混合多價態錳的氧化物組成,例如二價態、三價態的錳的氧化物,且錳的氧化物晶粒的粒徑為納米級。可以理解,由于比表面積增大,故納米級的錳的氧化物晶粒將會有更好的催化活性。在本步驟中,水熱晶化反應的溫度范圍為160~220℃,若溫度太低,則會發生反應不充分的情況,若溫度太高,則會促進晶粒增長,使得晶粒粒徑過大,從而降低催化活性。另外,水熱晶化反應的時間范圍為18~24小時,若反應時間過短,則會使反應不充分,導致目標生成物的純度降低,反應時間太長,則也會促進晶粒增長,并不利于節約能源以及降低生產效率。在步驟三中,錳的氧化物晶粒的懸浮液的降溫方式優選自然降溫,此降溫方式有利于晶粒形態的控制并節省能源。在步驟四中,錳的氧化物的固態產物的干燥溫度范圍具體為80~140℃,干燥方式優選使用電熱干燥以去除大部分水分,且干燥后的錳的氧化物的活性粉體的水分含量在6%~8%,當然,本步驟中,干燥方式也可使用自然干燥,但其干燥速率較慢,進而會降低生產效率。另外,本步驟中,在550℃的溫度下進行焙燒,可使多個晶粒之間團聚為活性粉體的粉顆粒,且由于晶粒間結晶水的逸出,每一活性粉體的顆粒的微觀結構中存在晶粒之間的通道或微孔等。在步驟五中,出于成本以及成型效果等方面綜合考慮,成型助劑為粘土材料,在本實施例中,該成型助劑具體為凹凸棒粘土,當然,于其他實施例中,成型助劑還可為其他材料,例如但不限于彭潤土等。另外,本步驟的對于半成品的干燥溫度范圍為100~130℃,干燥后的濾芯材料的水分含量在1%~4%;其焙燒溫度范圍為400~500℃,且最后得到的濾芯材料為尺寸均勻的圓柱狀顆粒。微觀結構觀察可知,由于在干燥與焙燒時水分子的逸出,該顆粒的表面及內部均具有很多蜂窩狀的微孔,且這些微孔通常為微米級。在此需特別說明的是,本發明的制備方法制成的濾芯材料對甲醛的凈化以氣固相催化氧化反應原理進行,以錳的氧化物為例,其反應機理如下:MnOx-1-O(s)+CH2O(ads)→MnOx-1(s)+2H(ads)+CO2(g)(1)MnOx-1(s)+2H(ads)+O2(g)→MnOx-1-O(s)+H2O(g)(2)其中,濾芯材料以納米結構的混合多價態過渡金屬氧化物(本實例中為MnOx-1-O)為催化活性組分,因此能夠在室溫下有效氧化分解甲醛。在此反應機理中,晶粒表面上的可移動晶格氧原子會參與反應,隨后這些被消耗掉的晶格氧原子由氣態氧分子在晶粒上的吸附和離解所補充。由此可見,晶格氧原子在顆粒的表面的移動性對反應活性至關重要,而這些氧原子的移動性則由晶粒中可變化合價的過渡金屬氧化物MnOx-1-O自身的氧化態、還原態的循環反應來完成。而在本發明的制備方法所制成的濾芯材料中,由于其活性組分過渡金屬氧化物MnOx-1-O存在著多種價態,且易于相互轉化,從而使晶粒表面的晶格氧原子有相當強的可移動性,因此本濾芯材料具有很好的甲醛催化氧化活性。具體地,本濾芯材料對甲醛的凈化過程如下,首先,環境空氣中的氣態甲醛CH2O(g)吸附到顆粒表面形成吸附態的CH2O(ads),然后在反應式(1)中吸附態的CH2O(ads)在活性組分MnOx-1-O(s)的催化作用下生成氣態CO2(g)釋放到空氣中,同時也產生吸附態的H(ads);在反應式(2)中失去晶格氧原子的MnOx-1(s)、吸附態H(ads)和氣態氧分子O2(g)共同作用,重新生成MnOx-1-O(s)和氣態H2O(g)。隨著(1)、(2)兩個反應在MnOx-1-O(s)表面進行,不斷的將CH2O(ads)轉化成無害的CO2(g)和H2O(g),從而達到凈化空氣中甲醛的目的。在本實施例中,相較于目前常見的活性炭的濾芯材料,本發明的制備方法所制成的濾芯材料對甲醛的凈化性能的提高主要由以下兩方面實現:一方面,由于濾芯材料以混合多價態過渡金屬氧化物為催化活性組分,其價態的不斷循環轉化,同時,晶粒的納米級結構也有利于催化活性的提高,如此,就使得其對甲醛進行催化而去除的效率提高,且由于能循環反應,不易出現吸附飽和的現象,故其材料使用壽命也得到提高;另一方面,由于多個晶粒團聚成活性粉體的顆粒,每一活性粉體的顆粒的微觀結構中存在晶粒之間的通道或微孔等,同時,每一顆粒狀的濾芯材料的成品的表面與內部也存在眾多微孔,可以理解,如此高的孔隙率可使濾芯材料對甲醛的吸附能力以及吸附容量等大大提高,從而可提高去除甲醛的效率以及材料的使用壽命。實施例2一種濾芯材料的制備方法,具體步驟如下:首先,將硫酸錳粉體用去離子水完全溶解成濃度40~50g/L的硫酸錳溶液,將氫氧化鉀用去離子水完全溶解成濃度38~45g/L的堿溶液;然后,重復實施例1中的制備步驟,但其步驟二中的水熱晶化反應溫度為160℃,反應時間為24小時。在上述實施例中,濾芯材料采用以下方法進行評價,其數據及評價結論具體請參照表1、表2、以及表3。當然,本濾芯材料除了可高效率的去除甲醛氣體外,還可以有效去除乙醛、乙酸、氨、硫化氫、臭氧等有害氣體,其適用范圍廣泛。表1甲醛吸附量實驗數據對照表如表1所示,通過實驗數據對照可知,相較于目前常見的濾芯材料,例如活性炭或竹炭,本發明制備方法所制備的濾芯材料對甲醛具有明顯的吸附效果。表2甲醛穿透吸附時間實驗數據對照表表3甲醛一小時去除率實驗數據對照表本發明還提出一種濾芯材料和具有該濾芯材料的空氣凈化器,該空氣凈化器包括由濾芯材料以及機身1,具體地,機身1內腔的下部設有濾芯2,機身的外殼上對應該濾芯2設有進風格柵板3,其中,濾芯2包括多層間隔設置的過濾網材(未標示),濾芯材料(未標示)則填充于兩過濾網材的夾層中。該濾芯材料的制備方法具體參照上述實施例,由于本濾芯材料和本空氣凈化器采用了上述所有實施例的全部技術方案,因此至少具有上述實施例的技術方案所帶來的所有有益效果,在此不再一一贅述。另外,本濾芯材料除了可以應用于空氣凈化器之外,還可應用于其他需對空氣進行凈化的產品,例如但不限于空調等,也可以做成單獨的空氣凈化產品,例如吸附包等。以上所述僅為本發明的優選實施例,并非因此限制本發明的專利范圍,凡是在本發明的發明構思下,利用本發明說明書及附圖內容所作的等效結構變換,或直接/間接運用在其他相關的
技術領域:
均包括在本發明的專利保護范圍內。當前第1頁1 2 3