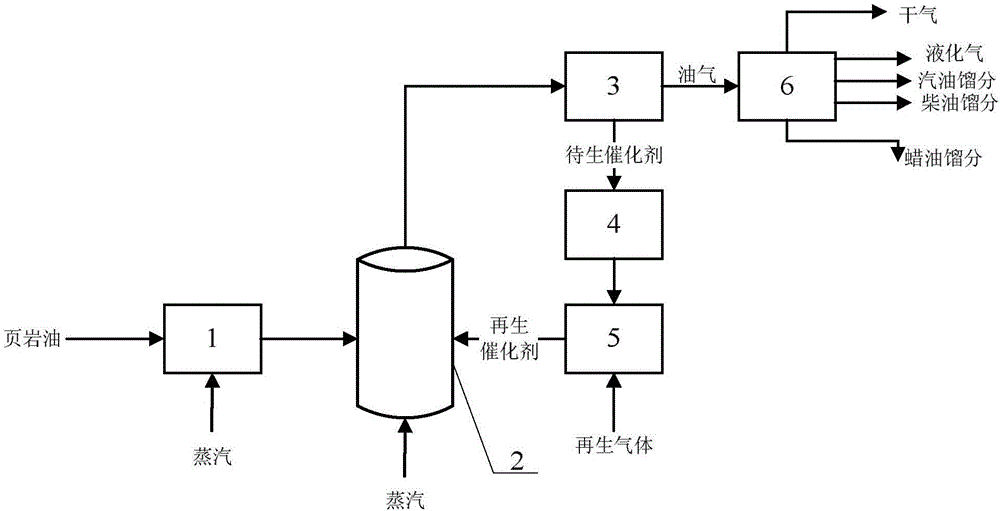
本發明屬于石油化工領域,涉及一種用于頁巖油加工的催化劑及其制備方法和頁巖油加工系統及其加工方法。
背景技術:
:我國油頁巖資源十分豐富,儲量約為160億噸,居世界第4位。頁巖油工業是能源工業的一個重要組成部分,也是天然石油的一種補充能源。與常規原油相比,頁巖油的多環芳烴含量高,氮化物特別是堿性氮化物含量高于常規原油的5~10倍,膠質含量高于常規原油2~8倍,柴油餾分(200~350℃)的質量收率是原油的2倍,并且除含有許多硫、氮和氧等非烴化合物外,還含有大量不飽和烴、砷、鐵以及微量的鋅和硒等雜質。因此,頁巖油在直接作為催化裂化裝置原料加工時,其中的氮化物特別是堿性氮化物在催化裂化反應過程中能和催化劑分子篩的酸性中心作用而降低催化劑活性和選擇性對催化劑毒害較大;同時,其中的膠質等大分子無法進入分子篩孔道進行裂解反應,導致所得輕質油品中氮含量較高,油品的安定性差。如果頁巖油直接作為加氫裂化原料進行加工,會造成氫氣的消耗量較大,并且頁巖油中的砷、鐵以及微量的鋅和硒等雜質導致催化劑活性降低較快。此外,頁巖油在蒸餾時的結焦情況也比天然石油嚴重得多,在較低溫度條件下(如在170~250℃范圍內)有明顯的結焦現象,沉渣淤塞嚴重。其結焦范圍較廣泛,除加熱爐管外,塔和換熱器的結焦情況也嚴重,既影響生產效率,同時又給檢修帶來困難。基于以上原因,頁巖油除了少量用于生產化學藥品外,大部分則是未經二次加工而直接作為燃料油銷售,因此有必要開發更多高效利用頁巖油的技術。如果對頁巖油進行深加工,首先需要降低頁巖油的氮和膠質的含量,脫除砷、鐵以及微量的鋅、硒和灰分等雜質。目前,以脫除氮化物等雜質為目的對頁巖油進一步加工的方法主要有加氫精制、溶劑抽提和催化裂解等。如US4231858中對頁巖油全餾分進行加氫精制,其所用催化劑為CoMo/Al2O3,反應溫度為315~455℃,平均壓力為16.8MPa。所述加氫精制后需要增加一套脫除含氮化合物的裝置,并且反應壓力很高,同時生成油收率低。US4344840公開了一種頁巖油加工方法,先用沸騰床反應器對頁巖油進行脫金屬,再用固定床加氫處理裝置進行處理,得到合格的噴氣燃料和柴油。所述方法采用兩級全氫型工藝,氫耗高,操作費用高,建設投資高;而且沸騰床工藝不夠成熟。EP0026670公開了一種頁巖油生產石油焦和液體產品的方法,所述方法將頁巖油與常壓渣油以5~85%的比例和天然石油常壓渣油混合作為延遲焦化的原料,并在原料中加入少量加氫裂化催化劑,催化劑加入量為0.01~5%(原料重量),含有催化劑的原料油被加熱到468℃,進入焦化塔,在常壓和無氧條件下進行熱解,得到氣體、液體和石油焦產品。由于加氫裂化催化劑的存在,有助于裂解反應,增加輕質油收率。同時,在裂解過程中產生少量氫氣,因此,還有一定的加氫精制效果,但是,該反應壓力低、氫氣純度很低,而且氫氣量也不足,液體產品精制效果不好,質量差;并且,焦體中含有催化劑,影響焦的質量,用途也將受到限制。CN101067089A公開了一種頁巖油的加工方法,所述方法中頁巖油先經加氫處理得到加氫生成油,加氫生成油分離為加氫重油和輕質產品,加氫重油經催化轉化后得到干氣、液化氣、汽油、柴油和催化重油,柴油可返回到加氫處理步驟。CN101492605A公開了一種頁巖油加氫工藝方法,所述方法中頁巖油原料從上部進入反應器,氫氣從下部進入反應器,氣液逆向通過加氫精制催化劑床層,進行油品加氫精制,反應后氣相從反應器上部排出,反應后液相為精制頁巖油,從反應器下部排出。以上兩種加工方法中,頁巖油全餾分加氫反應條件苛刻、氫耗高,催化劑容易中毒,消耗量大,整體投資大。US4338186公開了一種頁巖油加工方法,先將全餾分頁巖油用鹽酸進行處理,然后將抽余油進行加氫處理,再用加氫裂化進行處理以生產航空煤油。該方法工藝流程復雜、投資較高;同時因使用鹽酸產生酸渣,污染環境,反應設備還需使用耐酸材料。USSR652202中用磺酸陽離子交換樹脂吸附石油產品中的堿性氮化物。但由于所用樹脂多數是苯乙烯型,這種樹脂長時間在油中浸泡容易溶脹,從而影響精制效果;而且其交換容量有限,需經常進行吸附和再生,操作比較麻煩。CN101967389A公開了一種直接從頁巖油中脫除堿性氮化合物的脫氮劑,脫氮劑按照重量百分比其組成為:B:40~80%,L:0.5~10%,S:0.1~0.5%,余量為水;其中B為磷酸、L為路易斯酸、S為水溶性破乳劑。上述配方中的B可提供H+與堿性氮化物的一對孤對電子絡合成鹽,從而將堿性氮化物從油品中脫除;L可接受堿性氮化物的一對孤對電子絡合成鹽,B和L的協同作用具有良好的脫堿性氮能力;S具有良好的破乳效果,并可提高水溶性B和L劑在油品攪拌過程中與油品的均混程度,從而提高主劑的脫氮效率。該方法中的脫氮率70~87%,但是所述過程溶劑消耗較多,并有大量廢水產生污染環境。CN102079990A公開了一種頁巖油的加工方法,所述方法采用頁巖油與糠醛、N-甲基吡咯烷酮和二甲亞砜或苯酚萃取劑按質量比1:1~1:6混合萃取-蒸餾后抽余油可直接作為催化裂化原料,抽出油用于制備非烴化合物及瀝青產品的輕、重組分。CN104312623A公開了一種頁巖油非加氫催化轉化絡合精制的加工方法。所述催化轉化絡合精制方法包括:將頁巖油與催化劑充分混合接觸發生催化轉化反應,反應后經沉降分出上層催化轉化中間油和下層催化劑,對上層催化轉化中間油進行蒸餾,得到柴油和燃料油餾分,再對餾分油進行絡合精制,可得到合格的柴油及燃料油。但上述方法所涉及的過程中溶劑消耗較大,加入的液體或催化劑分離難度較大。CN105505454A公開了一種頁巖油流化催化裂化方法,所述方法通過引入低溫催化劑將反應器區分為流化床吸附區與提升管裂化區。在非臨氫氛圍下,頁巖油先進入溫度較低的流化床吸附區,吸附脫除其中的堿性氮化物、膠質和重金屬等雜質,然后再進入提升管裂化區接觸高溫高活性的再生劑進行催化裂化反應。所述過程采用的第一催化劑和第二催化劑均為催化裂化催化劑。CN105586080A公開了一種頁巖油催化裂化的加工方法,所述方法采用移動床為預處理反應器,通過將移動床反應器區分為吸附區與裂化區。在非臨氫氛圍下,頁巖油先進入溫度較低的移動床反應器吸附區,吸附脫除其中的堿性氮化物、膠質和重金屬等雜質,然后再進入移動床反應器裂化區接觸高溫高活性的再生劑進行催化裂化反應。所述過程采用的第一催化裂化催化劑和第二催化裂化催化劑為組成相同的分子篩催化裂化催化劑。CN105586081A公開了一種頁巖油催化裂化的加工方法,所述方法采用湍動床,通過將湍動流化床反應器區分為吸附區與裂化區。在非臨氫氛圍下,頁巖油先進入溫度較低的湍動流化床反應器吸附區,吸附脫除其中的堿性氮化物、膠質和重金屬等雜質,然后再進入湍動流化床反應器裂化區接觸高溫高活性的再生劑進行催化裂化反應。然而,以上方法中均采用催化裂化催化劑對高氮含量的頁巖油直接催化裂化,催化劑活性和選擇性很快下降,造成工藝過程催化劑消耗量大,成本較高。綜上所述,上述方法中加氫精制方法需要大量氫源,且設備投資大,催化劑容易中毒消耗較多;頁巖油經溶劑抽提或添加脫氮劑,雖然其抽余油中氮化物及其雜質被脫出可作為較理想的催化原料,但同時部分烴類也會隨抽出油被脫出,造成帶油率增加,浪費石油資源,溶劑耗量較大,能耗高,氮化物殘留較多,溶劑及廢水對環境污染較大等問題。同時,也存在抽出油的再利用問題。技術實現要素:針對現有頁巖油處理方法中存在的需要大量氫源,設備投資大,催化劑容易中毒且消耗量較大,加工過程中帶油率高,溶劑耗量較大,能耗高,氮化物殘留較多,溶劑及廢水對環境污染較大等問題,本發明提供了一種用于頁巖油加工的催化劑及其制備方法和頁巖油加工系統及其加工方法。本發明通過所制備的催化劑對頁巖油進行吸附和裂解,同時去除頁巖油中的氮化物、膠質和重金屬,提高液體收率和頁巖油加工產品的安定性;同時,所述方法頁巖油的加工方法不消耗氫,催化劑成本低且消耗量小。為達此目的,本發明采用以下技術方案:第一方面,本發明提供了一種用于頁巖油加工的催化劑,所述催化劑為由SiO2、Al2O3和吸附助劑組成的多孔催化劑,其按重量百分比計主要由以下原料制備得到:其中,擬薄水鋁石的重量百分比可為65wt%、70wt%、75wt%、80wt%、85wt%或90wt%等,但并不僅限于所列舉的數值,該數值范圍內其他未列舉的數值同樣適用;粘土的重量百分比可為0wt%、5wt%、10wt%、15wt%、20wt%或25wt%等,但并不僅限于所列舉的數值,該數值范圍內其他未列舉的數值同樣適用;粘結劑的重量百分比可為2wt%、4wt%、6wt%、8wt%、10wt%、12wt%、14wt%、16wt%、18wt%或20wt%等,但并不僅限于所列舉的數值,該數值范圍內其他未列舉的數值同樣適用;吸附助劑的重量百分比可為1wt%、3wt%、5wt%、7wt%、10wt%、13wt%或15wt%等,但并不僅限于所列舉的數值,該數值范圍內其他未列舉的數值同樣適用。以下作為本發明優選的技術方案,但不作為本發明提供的技術方案的限制,通過以下技術方案,可以更好的達到和實現本發明的技術目的和有益效果。作為本發明優選的技術方案,所述催化劑按重量百分比計主要由以下原料制備得到:優選地,所述催化劑的磨損指數<2.0%h-1,例如1.9%h-1、1.6%h-1、1.3%h-1、1.0%h-1、0.9%h-1、0.6%h-1或0.3%h-1,但并不僅限于所列舉的數值,該數值范圍內其他未列舉的數值同樣適用;比表面積為10~180m2/g,例如10m2/g、20m2/g、40m2/g、60m2/g、80m2/g、100m2/g、120m2/g、140m2/g、160m2/g或180m2/g等,但并不僅限于所列舉的數值,該數值范圍內其他未列舉的數值同樣適用;孔體積為0.1~0.35mL/g,例如0.1mL/g、0.15mL/g、0.2mL/g、0.25mL/g、0.3mL/g或0.35mL/g等,但并不僅限于所列舉的數值,該數值范圍內其他未列舉的數值同樣適用。優選地,所述催化劑的粒徑0~750μm且不包括0,例如1μm、10μm、25μm、76μm、93μm、183μm、292μm、325μm、480μm、586μm、600μm、650μm、700μm或750μm等,但并不僅限于所列舉的數值,該數值范圍內其他未列舉的數值同樣適用,進一步優選為10~600μm。優選地,所述催化劑的平均粒徑為40~150μm,例如40μm、50μm、60μm、70μm、80μm、90μm、100μm、110μm、120μm、130μm、140μm或150μm等,但并不僅限于所列舉的數值,該數值范圍內其他未列舉的數值同樣適用。本發明中所述本發明所述催化劑具有適當孔結構、比表面和酸中心,并具有較好的吸附作用,可將頁巖油中的氮化物、膠質和重金屬吸附在催化劑的表面和孔結構中。頁巖油中部分具有較強極性的堿性氮吸附在催化劑上,并與酸中心中和得以脫除。含有部分氮化物、重金屬和膠質的重質餾分在催化劑表面及孔道內發生裂解和縮聚反應。含重金屬和膠質的重質餾分大分子變為小分子和部分積碳,重金屬和積碳一起沉積在催化劑上,從而脫除頁巖油中的氮化物、膠質和重金屬。作為本發明優選的技術方案,所述擬薄水鋁石為一水軟鋁石、三水軟鋁石、拜耳石或η-氧化鋁中任意一種或至少兩種的組合,所述組合典型但非限制性實例有:一水軟鋁石和三水軟鋁石的組合,三水軟鋁石和拜耳石的組合,拜耳石和η-氧化鋁的組合,一水軟鋁石、三水軟鋁石和拜耳石的組合,一水軟鋁石、三水軟鋁石、拜耳石和η-氧化鋁的組合等。優選地,所述擬薄水鋁石的顆粒粒徑為0.1~5μm,例如0.1μm、0.7μm、1.1μm、1.8μm、2.6μm、3.7μm、4.5μm、4.8μm或5μm等,但并不僅限于所列舉的數值,該數值范圍內其他未列舉的數值同樣適用。優選地,所述粘土為高嶺土、埃洛石、膨潤土、蒙脫石、地開石或海泡石中任意一種或至少兩種的組合,所述組合典型但非限制性實例有:高嶺土和埃洛石的組合,埃洛石和膨潤土的組合,蒙脫石和地開石的組合,地開石和海泡石的組合,高嶺土、埃洛石和膨潤土的組合,膨潤土、蒙脫石和地開石的組合,蒙脫石、地開石和海泡石的組合,高嶺土、埃洛石、膨潤土、蒙脫石和地開石的組合,埃洛石、膨潤土、蒙脫石、地開石和海泡石的組合等。優選地,所述粘土的顆粒粒徑為0.1~5μm,例如0.1μm、0.7μm、1.1μm、1.8μm、2.6μm、3.7μm、4.5μm、4.8μm或5μm等,但并不僅限于所列舉的數值,該數值范圍內其他未列舉的數值同樣適用。本發明中,制備催化劑原料中的擬薄水鋁石和粘土的粒徑都必須控制在一定范圍內,目的在于可以保持噴霧干燥成型的催化劑顆粒具有較好的球形度、孔徑分布和強度。優選地,所述粘結劑為硅溶膠和/或鋁溶膠。優選地,所述吸附助劑為氧化鈣、氧化鎂、氫氧化鈣、氫氧化鎂、白云石或石灰石中任意一種或至少兩種的組合,所述組合典型但非限制性實例有:CaO和MgO的組合、MgO和Ca(OH)2的組合、Mg(OH)2和石灰石的組合、CaO和白云石的組合、白云石和石灰石的組合、CaO、Ca(OH)2和MgO的組合等。第二方面,本發明提供了上述催化劑的制備方法,所述方法包括以下步驟:(1)將一部分的擬薄水鋁石與吸附助劑混合制漿,使漿液的固含量為30~50wt%,并調節漿液的pH至3~5,得到漿液I;(2)將另一部分的擬薄水鋁石與粘土混合制漿,使漿液的固含量為30~50wt%,并調節漿液的pH至1~3,得到漿液II;(3)將得到的漿液I和漿液II混合,加入粘結劑,使漿液的固含量為20~50wt%,并調節漿液的pH至3~5,然后噴霧干燥成型;(4)將步驟(3)中經噴霧干燥成型得到的物料進行焙燒,制得催化劑。其中,步驟(1)中的固含量可為30wt%、33wt%、35wt%、37wt%、40wt%、43wt%、45wt%、47wt%或50wt%等,但并不僅限于所列舉的數值,該數值范圍內其他未列舉的數值同樣適用;步驟(1)中調節pH可為3、3.5、4、4.5或5等,但并不僅限于所列舉的數值,該數值范圍內其他未列舉的數值同樣適用;步驟(2)中的固含量可為30wt%、33wt%、35wt%、37wt%、40wt%、43wt%、45wt%、47wt%或50wt%等,但并不僅限于所列舉的數值,該數值范圍內其他未列舉的數值同樣適用;步驟(2)中調節pH可為3、3.5、4、4.5或5等,但并不僅限于所列舉的數值,該數值范圍內其他未列舉的數值同樣適用;步驟(3)中的固含量可為20wt%、25wt%、30wt%、35wt%、40wt%、45wt%或50wt%等,但并不僅限于所列舉的數值,該數值范圍內其他未列舉的數值同樣適用;步驟(3)中調節pH可為3、3.5、4、4.5或5等,但并不僅限于所列舉的數值,該數值范圍內其他未列舉的數值同樣適用。作為本發明優選的技術方案,步驟(1)中所述將一部分擬薄水鋁石與吸附助劑混合制漿為:將配方量中擬薄水鋁石的30~40wt%與吸附助劑混合制漿,其中擬薄水鋁石的用量可為30wt%、32wt%、34wt%、36wt%、38wt%或40wt%等,但并不僅限于所列舉的數值,該數值范圍內其他未列舉的數值同樣適用。優選地,步驟(1)中混合制漿為:將擬薄水鋁石與吸附助劑混合后,加入去離子水打漿。優選地,步驟(1)中用無機酸調節漿液的pH值。優選地,步驟(2)中所述將另一部分擬薄水鋁石與粘土混合制漿為:將配方量中擬薄水鋁石的60~70wt%與粘土混合制漿,其中擬薄水鋁石的用量可為60wt%、62wt%、64wt%、66wt%、68wt%或70wt%等,但并不僅限于所列舉的數值,該數值范圍內其他未列舉的數值同樣適用。優選地,步驟(2)中混合制漿為:將擬薄水鋁石與粘土混合后,加入去離子水打漿。優選地,步驟(2)中用無機酸調節漿液的pH值。優選地,步驟(3)中無機酸調節漿液的pH值。優選地,步驟(4)中焙燒溫度為600~1000℃,例如600℃、650℃、700℃、750℃、800℃、850℃、900℃、950℃或1000℃等,但并不僅限于所列舉的數值,該數值范圍內其他未列舉的數值同樣適用,進一步優選為700~1000℃。本發明中,催化劑的焙燒溫度需控制在一定范圍內,若焙燒溫度過低(<600℃),會使催化劑孔體積較小,孔徑分布不集中,無法滿足油品裂解需要;若焙燒溫度過高(>1000℃),會使催化劑結構改變,造成比表面過小無法提供油品吸附、裂解所需表面和孔道。進一步的,又以在700~1000℃范圍內焙燒制得的催化劑的性能最優。優選地,步驟(4)中焙燒時間為0.5~4h,例如0.5h、1h、2h、3h或4h等,但并不僅限于所列舉的數值,該數值范圍內其他未列舉的數值同樣適用。本發明中,所用無機酸為鹽酸和/或硝酸。第三方面,本發明提供了一種應用上述催化劑進行頁巖油加工的系統,所述系統包括:加熱爐、流化床反應器、分離系統、氣提系統、再生裝置和分餾系統,其中加熱爐、流化床反應器和分離系統依次相連,分離系統的氣相出料口與分餾系統相連,分離系統的固相出料口依次與氣提系統和再生裝置相連,再生裝置的固體出料口與流化床反應器的固體進料口相連,流化床反應器中采用權利要求1-3任一項所述的催化劑。作為本發明優選的技術方案,所述再生裝置為提升管、流化床或移動床中任意一種或至少兩種的組合,所述組合典型但非限制性實例有:提升管和流化床的組合,流化床和移動床的組合,提升管和移動床的組合,提升管、流化床和移動床的組合等。第四方面,本發明提供了一種應用上述催化劑進行頁巖油加工的方法,所述方法包括以下步驟:(1)將頁巖油與部分蒸汽經預熱后和另一部分蒸汽一起在催化劑作用下進行裂解反應,反應產物經分離處理后得到產物油氣和積碳的待生催化劑;(2)將步驟(1)中所得產物油氣經分餾處理得到氣體、汽油餾分、柴油餾分和蠟油餾分;(3)將步驟(1)中所得積碳的待生催化劑經氣提和再生處理后,得到再生催化劑返回參與裂解反應。本發明步驟(1)中所述“部分”和“另一部分”是指將所用蒸汽整體分為兩部分,為“部分”和“另一部分”,屬于清楚表述。本發明中,步驟(1)中將頁巖油先與部分蒸汽進行預熱后,再與蒸汽進行混合的目的在于預防油品預熱過程爐管結焦,維持流化床反應器內催化劑的流化狀態,減少催化劑積碳等;步驟(1)中頁巖油在催化劑的作用下進行吸附、裂解和縮聚反應,脫除氮化物、膠質及重金屬;步驟(3)中待生催化劑在再生處理過程中,催化劑上的積碳在氧化氣氛的作用下轉化成CO2而去除,使催化劑的比表面和/或活性中心再生。作為本發明優選的技術方案,步驟(1)中所述頁巖油為頁巖油和/或頁巖油與劣質油的混合物。本發明中,所述頁巖油包括各種油頁巖加工所得的頁巖油,以及頁巖油與其他劣質油的混合物;同時,本發明所述系統和方法并不僅限于處理頁巖油,還可處理煤焦油、油砂油或重質油等。優選地,步驟(1)中所述催化劑與頁巖油的質量比為(1~20):1,例如1:1、3:1、5:1、7:1、10:1、13:1、15:1、17:1或20:1等,但并不僅限于所列舉的數值,該數值范圍內其他未列舉的數值同樣適用,進一步優選為(2~15):1。優選地,步驟(1)中所用蒸汽整體與頁巖油的質量比為(0.01~0.4):1,例如0.01:1、0.03:1、0.05:1、0.1:1、0.15:1、0.2:1、0.25:1、0.3:1、0.35:1或0.4:1等,但并不僅限于所列舉的數值,該數值范圍內其他未列舉的數值同樣適用,進一步優選為(0.02~0.3):1。優選地,步驟(1)中所述預熱溫度為150~400℃,例如150℃、200℃、250℃、300℃、350℃或400℃等,但并不僅限于所列舉的數值,該數值范圍內其他未列舉的數值同樣適用。優選地,步驟(1)中所述裂解反應的反應溫度為350~650℃,例如350℃、400℃、450℃、500℃、550℃、600℃或650℃等,但并不僅限于所列舉的數值,該數值范圍內其他未列舉的數值同樣適用,進一步優選為400~650℃。優選地,步驟(1)中所述裂解反應的反應壓力0.1~0.6MPa,例如0.1MPa、0.2MPa、0.3MPa、0.4MPa、0.5MPa或0.6MPa等,但并不僅限于所列舉的數值,該數值范圍內其他未列舉的數值同樣適用,進一步優選為0.1~0.5MPa。優選地,步驟(1)中所述裂解反應的反應時間為2s~10min,例如2s、5s、30s、1min、3min、5min、7min或10min等,但并不僅限于所列舉的數值,該數值范圍內其他未列舉的數值同樣適用,進一步優選為2s~6min。優選地,步驟(3)中所述再生處理過程中通入再生氣體。優選地,所述再生氣體中氧氣的體積含量為10~50%,例如10%、15%、20%、25%、30%、35%、40%、45%或50%等,但并不僅限于所列舉的數值,該數值范圍內其他未列舉的數值同樣適用,進一步優選為15~50%。優選地,所述再生氣體為氧氣、水蒸氣或空氣中任意一種或至少兩種的組合,所述組合典型但非限制性實例有:氧氣和空氣的組合、空氣和水蒸氣的組合、氧氣、空氣和水蒸氣的組合等。優選地,步驟(3)中所述再生處理的溫度為600~900℃,例如600℃、630℃、670℃、700℃、720℃、767℃、815℃、876℃、892℃或900℃等,并不僅限于所列舉的數值,該數值范圍內其他未列舉的數值同樣適用,進一步優選為600~850℃。本發明中,若再生處理溫度過低(<600℃),會使再生時間較長或再生后催化劑積碳殘留較多;若再生處理溫度過高(>900℃),會使催化劑破碎較多,同時易造成重金屬沉積較多的催化劑燒結。優選地,步驟(3)中所述再生處理中床層壓力為130~750kPa,例如130kPa、200kPa、300kPa、400kPa、500kPa、600kPa、700kPa或750kPa等,并不僅限于所列舉的數值,該數值范圍內其他未列舉的數值同樣適用。優選地,步驟(3)中所述再生處理的時間為2~300s,例如2s、10s、15s、19s、30s、43s、78s、120s、190s、215s或278s等,并不僅限于所列舉的數值,該數值范圍內其他未列舉的數值同樣適用。作為本發明優選的技術方案,所述方法包括以下步驟:(1)將頁巖油與部分蒸汽經加熱爐預熱至150~400℃后和另一部分蒸汽一起進入流化床反應器在催化劑作用下于400~650℃進行裂解反應2s~6min,反應壓力為0.1~0.5MPa,反應產物經分離系統進行分離處理后得到產物油氣和積碳的待生催化劑,其中所述催化劑與頁巖油的質量比為(2~15):1,所用蒸汽與頁巖油的質量比為(0.02~0.3):1;(2)將步驟(1)中所得產物油氣經分餾系統進行分餾處理得到氣體、汽油餾分、柴油餾分和蠟油餾分;(3)將步驟(1)中所得積碳的待生催化劑經氣提系統的氣提處理和再生裝置于600~850℃下再生處理2~300s后,得到再生催化劑返回反應器參與裂解反應。其中再生處理過程中通入再生氣體,再生氣體中氧氣的體積含量為15~50%,再生處理中床層壓力為130~750kPa。與現有技術相比,本發明具有以下有益效果:(1)本發明提供了的催化劑不含有分子篩和貴金屬,所述催化劑在催化裂解過程中不易中毒,使用壽命較長,價格低廉,使用后的催化劑經簡單再生后可循環使用;(2)本發明所述頁巖油的加工系統和方法,通過采用本發明所制催化劑可以同時脫除頁巖油中的氮化物、膠質和重金屬,使頁巖油中氮含量下降約80%,重金屬降低約90%,總液體收率提高約5個百分點,明顯優于通過催化裂化催化劑進行頁巖油加工的效果;并且,本發明所述頁巖油的加工系統和方法降低了油品中的氮化物,從而提高了柴油的安定性。(3)通過本發明所述系統和方法對頁巖油進行加工,所得柴油和總液體的收率有較大提高,充分發揮了頁巖油柴油含量高的特點。(4)本發明提供的頁巖油加工方法沒有氫氣和溶劑消耗,環境友好,工藝過程的安全性和經濟性較高。(5)本發明由于重質餾分和膠質在流化床反應器中發生裂解和縮聚反應生成積碳,將油品輕質化的同時也減少了后續設備的結焦。附圖說明圖1是本發明所述的頁巖油加工的系統的結構示意圖;其中,1-加熱爐,2-流化床反應器,3-分離系統,4-氣提系統,5-再生裝置,6-分餾系統。具體實施方式為更好地說明本發明,便于理解本發明的技術方案,下面對本發明進一步詳細說明。但下述的實施例僅僅是本發明的簡易例子,并不代表或限制本發明的權利保護范圍,本發明保護范圍以權利要求書為準。本發明具體實施例部分提供了一種用于頁巖油加工的催化劑及其制備方法,以及應用該催化劑進行頁巖油加工的系統及方法。所述催化劑為由SiO2、Al2O3和吸附助劑組成的多孔催化劑,其按重量百分比計主要由以下原料制備得到:所述催化劑的制備方法,所述方法包括以下步驟:(1)將一部分的擬薄水鋁石與吸附助劑混合制漿,使漿液的固含量為30~50wt%,并調節漿液的pH至3~5,得到漿液I;(2)將另一部分的擬薄水鋁石與粘土混合制漿,使漿液的固含量為30~50wt%,并調節漿液的pH至1~3,得到漿液II;(3)將得到的漿液I和漿液II混合,加入粘結劑,使漿液的固含量為20~50wt%,并調節漿液的pH至3~5,然后噴霧干燥成型;(4)將步驟(3)中經噴霧干燥成型得到的物料進行焙燒,制得催化劑。如圖1所示,頁巖油加工的系統包括:加熱爐1、流化床反應器2、分離系統3、氣提系統4、再生裝置5和分餾系統6,其中加熱爐1、流化床反應器2和分離系統3依次相連,分離系統3的氣相出料口與分餾系統6相連,分離系統3的固相出料口依次與氣提系統4和再生裝置5相連,再生裝置5的固體出料口與流化床反應器2的固體進料口相連,流化床反應器2中采用權利要求1-3任一項所述的催化劑。所述頁巖油加工的方法包括以下步驟:(1)將頁巖油與部分蒸汽經預熱后和另一部分蒸汽一起在催化劑作用下進行裂解反應,反應產物經分離處理后得到產物油氣和積碳的待生催化劑;(2)將步驟(1)中所得產物油氣經分餾處理得到氣體、汽油餾分、柴油餾分和蠟油餾分;(3)將步驟(1)中所得積碳的待生催化劑經氣提和再生處理后,得到再生催化劑返回參與裂解反應。本發明具體實施例部分所用的分析測定方法如下:(1)比表面積和孔體積的測定:低溫氮吸附容量法(GB/T19587-2004);(2)磨損指數的測定:磨損指數的測定(直管法)(ASTMD5757-00);(3)總液體收率的測定:液化氣收率+汽油收率+柴油收率+蠟油收率。(4)反應性能評價:采用本發明提供的頁巖油加工的方法,所用原料油為頁巖油,其原料油性質見表2。反應條件為預熱溫度150~400℃,反應溫度350~650℃,劑油比(1~20):1,水蒸氣與油品重量比為(0.01~0.4):1,反應壓力0.1-0.6MPa。催化劑再生反應條件為:溫度600~850℃,床層壓力130~750kPa,再生氣體氧含量10~50%。以下為本發明典型但非限制性實施例:實施例1:本實施例提供了一種催化劑的制備方法及制得的催化劑,所述方法為:(1)將1.4kg擬薄水鋁石磨至0.1~5μm和0.9kg的CaO混合,加入去離子水打漿,使漿液固含量為40wt%,用鹽酸調節漿液的pH=3.4,攪拌30min,得到漿液I;(2)將0.3kg高嶺土和3.2kg擬薄水鋁石磨至0.1~5μm,加入去離子水打漿,使漿液固含量為40wt%,用鹽酸調節漿液的pH=2.5,攪拌15min,得到漿液II;(3)將得到的漿液I和漿液II混合,加入0.5kg鋁溶膠,使漿液的固含量為30~40wt%,并用鹽酸調節漿液的pH=3.6,攪拌50min,然后噴霧干燥成型;(4)將步驟(3)中經噴霧干燥成型得到的物料在600℃焙燒4h,制得催化劑。所得催化劑的組成和物理性質如表1所示。實施例2:本實施例提供了一種催化劑的制備方法及制得的催化劑,所述方法為:(1)將1.8kg擬薄水鋁石磨至0.1~5μm和0.3kg的白云石以及0.3kg的石灰石混合,加入去離子水打漿,使漿液固含量為30wt%,用鹽酸調節漿液的pH=3.5,攪拌10min,得到漿液I;(2)將1.0kg蒙脫石和3.4kg擬薄水鋁石磨至0.1~5μm,加入去離子水打漿,使漿液固含量為30wt%,用鹽酸調節漿液的pH=2.7,攪拌15min,得到漿液II;(3)將得到的漿液I和漿液II混合,加入1.2kg硅溶膠,使漿液的固含量為20~30wt%,并用鹽酸調節漿液的pH=3.2,攪拌60min,然后噴霧干燥成型;(4)將步驟(3)中經噴霧干燥成型得到的物料在700℃焙燒2h,制得催化劑。所得催化劑的組成和物理性質如表1所示。實施例3:本實施例提供了一種催化劑的制備方法及制得的催化劑,所述方法為:(1)將0.8kg擬薄水鋁石磨至0.1~5μm和0.05kgMgO以及0.1kg石灰石混合,加入去離子水打漿,使漿液固含量為50wt%,用硝酸調節漿液的pH=4,攪拌20min,得到漿液I;(2)將0.1kg膨潤土和1.3kg擬薄水鋁石磨至0.1~5μm,加入去離子水打漿,使漿液固含量為50wt%,用硝酸調節漿液的pH=3,攪拌20min,得到漿液II;(3)將得到的漿液I和漿液II混合,加入0.27kg硅溶膠,使漿液的固含量為40~50wt%,并用硝酸調節漿液的pH=3.8,攪拌40min,然后噴霧干燥成型;(4)將步驟(3)中經噴霧干燥成型得到的物料在900℃焙燒2h,制得催化劑。所得催化劑的組成和物理性質如表1所示。實施例4:本實施例提供了一種催化劑的制備方法及制得的催化劑,所述方法為:(1)將0.9kg擬薄水鋁石磨至0.1~5μm和0.05kgCaO以及0.15kg白云石混合,加入去離子水打漿,使漿液固含量為30~50wt%,用硝酸調節漿液的pH=4,攪拌20min,得到漿液I(2)將1.9kg擬薄水鋁石磨至0.1~5μm,加入去離子水打漿,使漿液固含量為30~50wt%,用硝酸調節漿液的pH=2.4,攪拌20min,得到漿液II;(3)將得到的漿液I和漿液II混合,加入0.25kg硅溶膠,使漿液的固含量為40~50wt%,并用硝酸調節漿液的pH=3.5,攪拌30min,然后噴霧干燥成型;(4)將步驟(3)中經噴霧干燥成型得到的物料在200℃焙燒1h,然后升溫至600℃焙燒1h,最后升溫至1000℃焙燒1h,制得催化劑。所得催化劑的組成和物理性質如表1所示。對比例1:本對比例1提供一種現有技術中常用催化裂化催化劑樣品,其具體組成和物料性質如表1中所示。本對比例和實施例中頁巖油經裂化后所得產物分布如表3中所示。本發明具體實施例部分所用頁巖油的油品性質如表2中所示。表1:實施例1-4和對比例1中催化劑及再生后催化劑的組成和物理性質表從表1可以看出,本發明所提供的催化劑具有較大的比表面和孔體積,為頁巖油中的氮化物、膠質、重金屬的重質餾分提供了吸附和裂化的空間、表面和酸中心。對比例1中的催化劑反應再生后,其比表面下降26.8%,孔體積下降40%,總酸量下降48%。而實施例1中的催化劑的比表面下降11%,孔體積僅下降約10%,總酸量僅下降約9%;實施例2中催化劑的比表面下降10%,孔體積僅下降約7%,總酸量僅下降約10%;實施例3中催化劑的比表面下降6%,孔體積僅下降約10%,總酸量僅下降約11%;實施例4中催化劑的比表面下降7%,孔體積僅下降約10%,總酸量僅下降約7%。這充分說明了頁巖油加工過程對本發明實施例1-4中所述催化劑的比表面、孔體積和總酸量的影響較小,本發明實施例中所制得的催化劑具有更好的使用壽命;而頁巖油加工過程對對比例1中所述催化劑的比表面、孔體積和總酸量的影響較大,明顯縮短催化裂化催化劑的使用壽命。表2:具體實施例部分所用頁巖油的油品性質表從表2中可以看出,頁巖油中膠質、氮和金屬含量較多,尤其是堿性氮化物在催化裂化反應過程中能和催化劑分子篩的酸性中心作用而降低催化劑活性和選擇性對催化劑毒害較大。表3:實施例1-4和對比例1中頁巖油經裂化后所得產物分布表催化劑編號對比例1實施例1實施例2實施例3實施例4物料平衡(%)干氣4.31.81.211.62.0液化氣20.415.413.814.514.4汽油餾分27.424.324.625.125.9柴油餾分29.434.935.136.735.3油漿/蠟油餾分6.314.114.7913.112.1焦炭12.29.510.59.010.3總液體收率(%)83.588.788.2989.487.7膠質含量(%)13.20000氮含量(%)0.60.050.070.030.1重金屬(ppm)Fe4.21.71.91.52.0Ni1.80.30.20.10.3V0.30.060.030.040.05Na0.60.20.10.10.2從表3中可以看出,采用本發明所述催化劑對頁巖油進行加工,干氣產率比對比例降低約2個百分點,液化氣產率降低約5個百分點,柴油產率提高約6個百分點,焦炭產率下降約2個百分點,膠質含量下降約6個百分點;氮含量下降約80%,重金屬降低約90%,總液體收率提高約5個百分點。與采用催化裂化催化劑進行頁巖油加工的結果相比,干氣、液化氣和焦炭產率明顯下降;柴油產率和總液體收率上升;膠質、氮化物和重金屬明顯下降。由此可以看出,本發明提供的用于頁巖油加工的催化劑以及應用該催化劑進行頁巖油加工的系統及方法可以發揮頁巖油柴油含量高的特點,多產柴油;并能有效去除頁巖油中含量較高的膠質、氮化物和重金屬,從而實現了頁巖油資源的高效利用。申請人聲明,本發明通過上述實施例來說明本發明的詳細方法,但本發明并不局限于上述詳細方法,即不意味著本發明必須依賴上述詳細方法才能實施。所屬
技術領域:
的技術人員應該明了,對本發明的任何改進,對本發明產品各原料的等效替換及輔助成分的添加、具體方式的選擇等,均落在本發明的保護范圍和公開范圍之內。當前第1頁1 2 3