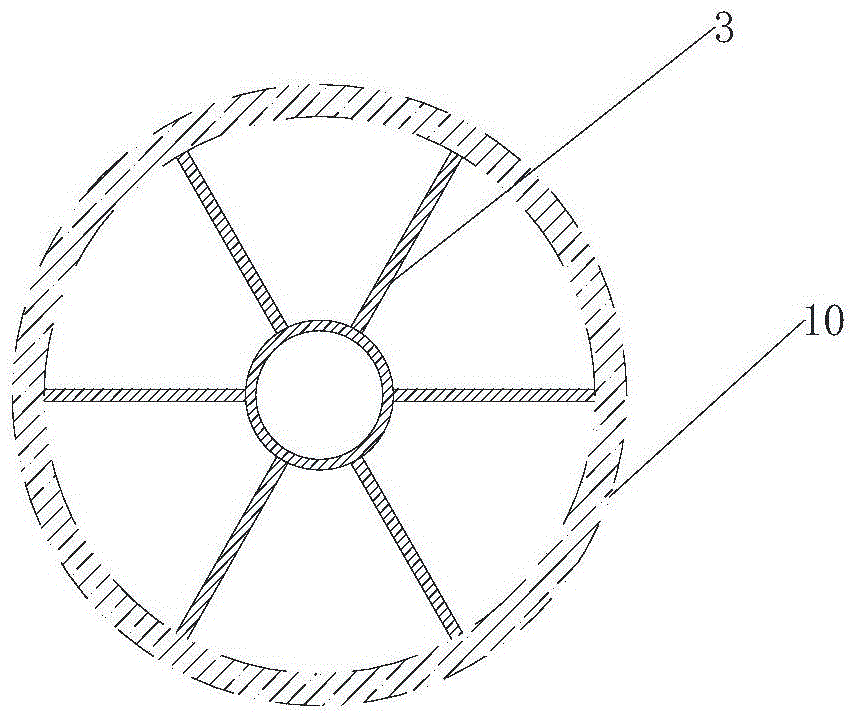
本發明涉及一種實驗室催化裂化催化劑活性穩定的反應器,更具體地說,涉及一種使催化裂化催化劑循環污染、老化處理的反應器。
背景技術:
:催化裂化技術是煉油企業的主要二次加工工藝。該技術將重質烴油原料轉化為汽油、柴油、丙烯和液化氣等產品。在催化裂化裝置運轉過程中,一些重質原料中的金屬鐵、鎳、釩、鈣等金屬會污染催化劑,使催化劑活性降低、催化劑上的重金屬含量增加,影響催化劑的性能及其產物的分布。因此,催化裂化催化劑和工藝的研究過程中,需要在實驗前對催化劑進行水熱老化和重金屬污染,以便使催化劑的物化性能盡可能的接近工業平衡劑,使得到的實驗結果更加可靠,對工業試驗具有更好的指導作用。Mitchell方法是催化裂化領域常用的一種催化劑污染、老化方法。該方法首先將制定含量的鎳、釩等金屬化合物充分溶解于一定量的溶液中,然后用所得到溶劑浸漬催化劑,浸漬后的催化劑經干燥、焙燒、水熱老化后,即可用于催化裂化實驗。該方法雖然操作簡單、廣泛使用,但存在以下不足之處:⑴鎳、釩在催化劑上均勻分布,且鎳、釩等金屬的活性無梯度分布;⑵催化劑上的釩以最具移動性和破壞性的+5價化合物存在,不能準確地考察催化劑的反應性能。美國Grace公司提供的一種催化劑循環污染、老化的方法。該方法首先將制定含量的鎳、釩等金屬化合物,如環烷酸釩和環烷酸鎳,溶解于一定量的原油中,并利用該原料油在固流化床裝置上重復24次逐步沉積在催化劑上;再生過程中,對催化劑及沉積在上面的金屬進行老化。該方法基本上克服了Mitchell方法所存在的不足之處。改用該方法處理后的催化劑基本接近 于工業平衡劑,不僅可以用來進行常規的催化裂化實驗,還可以用來考察鈍化劑、捕釩劑的反應性能。美國Grace公司提供的循環污染、老化方法所采用反應器為實驗室固定流化床裝置反應器,該反應器主要針對實驗室催化裂化(解)實驗而設計,當用于催化劑循環污染、老化處理時存在以下不足:⑴循環污染老化處理溫度高、水蒸氣用量大、處理過程長,反應器的材質及構型設計不能完全滿足要求;⑵固定流化床反應器采用合金鋼材制成,在長時間循環污染過程中反應器材質中的鐵、鎳、釩等金屬會對實驗結果產生干擾,另一方面,原料油中添加的環烷酸及S、Cl元素及其化合物的存在會對反應器產生腐蝕;⑶循環污染老化過程往往與水熱老化過程同時或交替進行,固定流化床反應器的設計很難實現該過程。技術實現要素:本發明的目的主要在于提供一種催化劑重金屬循環污染老化反應器,以克服現有技術中老化反應器水蒸氣用量大、老化處理時間長的問題。本發明的目的是這樣實現的,一種催化劑重金屬循環污染老化反應器,該反應器包括反應器主體,催化劑裝卸口,進料管,出氣管,格柵,球面型塔板和進氣管;所述反應器主體自上而下分為沉降段、老化段和預分布段,所述反應器主體橫截面積自上而下逐漸縮小,所述格柵水平設于所述反應器老化段,所述球面型塔板設于所述格柵和反應器底端之間,所述進料管通過所述反應器上部和所述格柵,貫穿于反應器中,直至所述格柵與所述球面型塔板之間,所述進氣管設置在反應器底端。本發明所述的催化劑重金屬循環污染老化反應器,其中,所述反應器主體橫截面積優選為圓形,所述沉降段的垂直高度優選為所述反應器垂直高度的32~41%,所述老化段的垂直高度優選為所述反應器垂直高度的58~65%,所述沉降段的垂直高度與所述反應器頂端橫截面直徑的比例優選為1:0.8~2.2。本發明所述的催化劑重金屬循環污染老化反應器,其中,所述反應器沉降段側壁與縱向軸線的夾角γ優選為小于或等于55°,所述反應器老化段 側壁與縱向軸線的夾角β優選為小于或等于30°,所述反應器預分布段側壁與縱向軸線的夾角α/2優選為大于或等于6°,所述夾角α優選為大于或等于所述夾角β的2倍,所述夾角γ優選為大于或等于所述夾角β。本發明所述的催化劑重金屬循環污染老化反應器,其中,優選的是,所述反應器上部設置有進料管固定管,所述進料管固定于所述進料管固定管中。本發明所述的催化劑重金屬循環污染老化反應器,其中,所述催化劑裝卸口優選設置于所述反應器上部。本發明所述的催化劑重金屬循環污染老化反應器,其中,優選的是,所述出氣管位于所述反應器沉降段,所述出氣管與氣體冷凝管相連接,所述氣體冷凝管與所述出氣管連接端設置有過濾介質。本發明所述的催化劑重金屬循環污染老化反應器,其中,所述格柵優選由中心圓環和與圓環相連的2~12根橫桿組成,所述橫桿與圓環所在平面的夾角優選為0~79°,所述橫桿與所述反應器的內壁相連接,所述進料管固定于所述中心圓環內。本發明所述的催化劑重金屬循環污染老化反應器,其中,所述球面型塔板優選為多孔陶瓷板,氣孔率優選為20~45%,球面半徑優選為5~30mm,塔板厚度優選為1~10mm;所述球面型塔板優選凹面向上,所述球面型塔板中心距所述反應器底端的垂直距離優選為所述反應器垂直高度的1/100~1/10,優選為1/50~1/10,所述多孔陶瓷板優選為氧化鋁陶瓷、氮化硅陶瓷、碳化硅陶瓷或六方氮化硼陶瓷。本發明所述的催化劑重金屬循環污染老化反應器,其中,所述進料管直徑優選在距進料管出口1/15~1/2處開始縮小,所述進料管出口處直徑優選為進料管頂部直徑的1/10~9/10。本發明所述的催化劑重金屬循環污染老化反應器,其中,所述反應器的頂端邊緣優選為圓角設計,圓角的半徑優選為10~22mm。本發明所述的催化劑重金屬循環污染老化反應器,其中,所述反應器主體,催化劑裝卸口,進料管,進料管固定管,出氣管,格柵和進氣管均優選為石英材質。本發明的有益效果:本發明提供的催化劑重金屬循環污染老化反應器根據重金屬循環污染老化處理的條件及要求,對傳統固定流化床反應器的材質和構型進行改進,使得該反應器具有結構簡單、水熱老化與重金屬循環污染老化靈活切換、冷卻系統簡單的特點,特別適應循環污染老化處理反應溫度高、水蒸氣量大、處理時間長的要求,以更好地模擬工業平衡劑的性能。附圖說明圖1是本發明的一種具體實施方式的催化劑重金屬循環污染老化反應器的結構示意圖;圖2是本發明的一種具體實施方式的催化劑重金屬循環污染老化反應器內部格柵的俯視圖;其中,附圖標記:1-進氣管;2-球面型塔板;3-格柵;4-進料管;5-出氣管;6-氣體冷凝管;7-氣固分離介質;8-進料管固定管;9-催化劑裝卸口;10-反應器壁;11-反應器主體;I-預分布段;II-老化段;III-沉降段;α-預分布段夾角;β-老化段夾角;γ-沉降段夾角;δ-格柵夾角;具體實施方式以下對本發明的具體實施方式進行詳細說明。應當理解的是,此處所描述的具體實施方式僅用于說明和解釋本發明,并不用于限制本發明。按照本發明,如圖1所示,一種催化劑重金屬循環污染老化反應器,該反應器包括反應器主體11,催化劑裝卸口9,進料管4,出氣管5,格柵3,球面型塔板2和進氣管1;反應器主體自上而下分為沉降段Ⅲ、老化段Ⅱ和預分布段Ⅰ,反應器主體11橫截面積自上而下縮小,格柵3水平設于反應器老化段Ⅱ,球面型塔板2設于格柵3和反應器底端之間,進料管4通過反應器上部和格柵3,貫穿于反應器中,直至格柵3與球面型塔板2之間,進氣管1設置在反應器底端。本發明所述的催化劑重金屬循環污染老化反應器主體11,催化劑裝卸口9,進料管4,進料管固定管8,出氣管5,格柵3和進氣管1均采用石英材質制得,沉降段III、老化段II、預分布段I自上而下逐漸縮小;進氣管1設置在反應器的底端,進料管4穿過反應器上部進入反應器;反應器內添加球面型塔板2和格柵3內件,從而使得所述催化劑重金屬循環污染老化反應器能夠特別適宜于實驗室催化裂化催化劑的重金屬污染老化處理。根據本發明,為了避免本發明所述催化劑重金屬循環污染老化反應器內沉降段III與老化段II之間存在死角,優選,選沉降段III底端的橫截面積與老化段II頂端的橫截面積相等;老化段II底端的橫截面積與預分布段I頂端的橫截面積相等,由此催化劑可以在本發明的催化劑重金屬循環污染老化反應器內很好地流化和沉降。根據本發明,為了進一步增強催化劑在本發明所述催化劑重金屬循環污染老化反應器內的均勻分布和氣固流態化質量,優選情況下,所述反應器沉降段III側壁與縱向軸線的夾角γ為小于或等于55°,優選為小于或等于48°,所述反應器老化段II側壁與縱向軸線的夾角β為小于或等于30°,優選為小于或等于20°,所述反應器預分布段I側壁與縱向軸線的夾角α/2為大于或等于6°,優選為大于或等于14°,沉降段III的頂端邊緣采用圓角設計,圓角的半徑為5~30mm,優選為10~22mm。為了進一步優化反應器內的流化狀態,加強顆粒自由沉降效果,優選,所述夾角α不小于夾角β的2倍;夾角γ不小于夾角β。按照本發明,為了使催化劑在本發明所述催化劑重金屬循環污染老化反應器內的分布更均勻以更好地實現本發明的發明目的,進一步優選情況下,反應器主體橫截面積為圓形,老化段II的垂直高度與老化段II頂端的橫截面的直徑比為1.8~4.5:1,更優選為2.3~3.7:1;所述老化段II的垂直高度為反應器垂直高度的58~65%。沉降段III的垂直高度與沉降段III頂端的橫截面的直徑比為1:0.8~2.2,更優選為1:1.1~1.7;所述沉降段III的垂直高度為反應器垂直高度的32~41%。根據本發明,如圖1所示,為了對從反應器底部進入的氣體進行預分布,優化反應器內的氣體及催化劑分布,在反應器內部安裝球面型塔板2,現有技術的各種材質、形狀均可實現本發明的目的。優選的,球面型塔板2采用多孔氧化鋁陶瓷材料制得,氣孔率為20~45%,更優選為30~40%;為了減小向上流動氣體對向下流動原料氣的干擾,優選的,該塔板2采用球面型設計,球面半徑為5~30mm,更優選為10~21mm,塔板厚度為1~10mm,更優選為2~6mm;球面型塔板2凹面向上,所述球面型塔板2中心距所述反應器底端的垂直距離為所述反應器垂直高度的1/100~1/10,優選為1/50~1/10,所述多孔陶瓷板可以為氧化鋁陶瓷、氮化硅陶瓷、碳化硅陶瓷或六方氮化硼陶瓷。根據本發明,為了改善催化劑重金屬循環污染老化反應器內催化劑顆粒與氣體的接觸情況,防止催化劑床層內部大氣泡的出現,在反應器老化段II內部設置格柵3,現有技術的各種材質、形狀均可實現本發明的目的。優選的,如圖2所示,格柵3由中心圓環和與圓環相連的橫桿組成,橫桿與圓環所在平面夾角δ為0~79°,優選為15~68°,橫桿的數量為2~12個,優選為3~8個,橫桿均列在圓環周圍,與反應器的內壁相連接,進料管4固定于中心圓環內。圓環與橫桿的厚度為2~10mm,優選為3~5mm。格柵中心圓環主要起到固定進料管4的作用,圓環的直徑與進料管4直徑的關系為:Φ圓環-Φ進料管=0.5~6mm,優選為1~2.5mm。格柵3的安裝位置為由老化段II底端起老化段II垂直高度的0~1/2處,優選為1/10~1/4處。本發明所述出氣管5在反應器上的安裝位置無特殊要求,現有技術的各種安裝位置均可實現本發明的目的,例如,可以安裝在本發明所述金屬循環 污染老化反應器的頂部(如可以穿過反應器主體的頂部與反應器主體連通),也可以安裝在本發明所述金屬循環污染老化反應器的側壁。針對本發明,為了簡化氣固分離裝置,增加催化劑顆粒的自由沉降效果,優選,所述出氣管5設置在沉降段III的側壁,并與反應器主體熔鑄為一體。本發明所述氣體冷凝管6與出口管5相連,為了防止催化劑細粉顆粒進入冷凝管,優選地,冷凝管6與出氣管5連接端通過改變直徑形成一個腔室,在該腔室內放置可更換的氣固分離介質,如:玻璃纖維、脫脂棉、過濾棉、過濾布、多孔陶瓷、分子篩過濾器、過濾網、活性炭,等具有過濾作用的材料,更優選的使用玻璃纖維、脫脂棉、過濾棉進行過濾。氣體冷凝管6與冷凝器相連,對于冷凝器的構型及參數無特殊要求,該領域慣用的冷凝器均可實現本發明的目的。本發明所述的出氣管5與氣體冷凝管6密封相連,現有技術的各種密閉連接方式均可實現本發明的目的。如圖1所示,優選的,出氣管5與氣體冷凝管6的端口采用O型圈密封連接,出氣管5與氣體冷凝管6的端面上設計凹槽,用來放置O型圈,更優選的凹槽為矩形凹槽。出氣管5與氣體冷凝管6也可用該領域慣用的球形玻璃接頭夾進行密封連接。本發明所述的進料管4在反應器上沉降段Ⅲ的安裝位置無特殊要求,現有技術的各種安裝位置均可實現本發明的發明目的,例如可以安裝在本發明所述金屬循環污染老化反應器的沉降段Ⅲ的的頂部,也可以安裝在所述金屬循環污染老化反應器沉降段Ⅲ的側壁。針對本發明,優選情況下,如圖1所示,所述進料管4密封地穿過所述反應器的頂部與反應器主體連通,進料管4密封固定在進料管固定管8上,且穿過柵格3的中心圓環。為了防止底部流化氣體將催化劑顆粒攜帶至進料管4,引起進料管4堵塞,進料管4的出口直徑逐漸縮小,進料管直徑從距進料管4出口1/15~1/2高度處開始縮小,優選為1/10~1/4;進料管4的出口直徑為進料管4頂部直徑的1/10~9/10,優選為1/5~4/5。按照本發明,如圖2所示,所述進料管固定管8安裝在反應器上部,優選在反應器頂部中心;進料管4固定于進料管固定管8中;所述催化劑裝卸口9安裝在反應器的上部,優選在反應器頂部,進料管固定管8、進氣管1、催化劑裝卸口9均可與反應器主體熔鑄為一體。本發明的改進主要表現在:(1)反應器主體11(除球面型氣體分布塔板外)和與其相連接的附件均采用石英制得,可以進行長周期的高溫操作,而不會引起反應器的腐蝕、形變以及由此對催化劑循環污染結果的影響。(2)從上而下逐漸縮小的老化段II、預分布段I,有助于形成均一的催化劑流化床層,減少因氣速過大引起的床層密相區上涌的現象。特別是沉降段III的頂端邊緣的圓角設計,使得氣速進一步降低,催化劑可自由沉降進入老化段II,簡化了反應器出口的氣固分離系統。(3)進料管4穿過反應器上部進入反應器內,進料管4出口直徑逐漸縮小,可以防止催化劑進入進料管4與原料油(特別是重質油品)凝結,堵塞進油管。進氣管1設置在反應器底端,氣體從底部進入反應器有助于反應器內顆粒的流態化,更重要的是可以單獨控制水蒸氣的進氣時間和進氣量,以滿足不同循環污染老化處理條件的要求,實現水熱老化和循環污染老化的靈活切換。(4)固定在反應器內壁上的球面型塔板2,一方面作為催化劑的支撐防止因為底部流化氣體氣速減小出現床層塌落現象;另一方面在塔板與反應器底部之間形成流化氣體的預分布腔室,有助于改善氣體分布,形成均一的催化劑流化床層。采用球面型設計,可以減小進料管4向下流出的油氣與進氣管1向上流出的氣體的擾動現象。(5)固定在反應器內壁上的格柵3,有助于確保進料管4處于反應器中心軸線上,更重要的起到破壞催化劑流化床層內部氣泡的作用,改善氣體分布以形成均一的催化劑流化床層。本發明對所處理的催化劑品種沒有限制,任何石油化工領域常用的粒徑小于8mm的球形固體顆粒催化劑均適用于本發明,優選情況下,用于催化裂化催化劑的重金屬循環污染老化處理,例如,含或不含稀土的Y型、HY型或USY型沸石、β沸石、ZSM-5沸石或其他具有五元環結構的高硅沸石的催化劑均可采用本發明所述的反應器進行處理,并且處理的催化劑可以是兩種或兩種以上催化劑的混合物。下面參照圖1,對本發明的一種優選實施方式的催化劑重金屬循環污染老化反應器的工作過程進行詳細地描述。催化劑經催化劑裝卸口9加入反應器中,然后密封催化劑裝卸口9。流化介質(選自空氣、水蒸氣、氮氣或氦氣的一種或幾種的混合氣)自進氣管1進入反應器,在球面型塔板2的分散作用下對催化劑進行流化。待催化劑床層壓降穩定后,將溶解有一種或多種金屬有機化合物的烴油原料與流化氣體的混合物從進料管4注入反應器中,與處于流化狀態的催化劑接觸,并在催化裂化反應條件下進行反應。上述油氣混合物沿反應器上升,催化劑顆粒流化床層頂部的稀相區內的催化劑顆粒在老化段II上部及沉降段III內進行自由沉降,反應油氣和催化劑相分離。油氣經出氣管5流出反應器,油氣中攜帶的少量細小催化劑顆粒在冷凝管6端口腔室內氣固分離介質的作用下進一步分離。留在反應器內、表面沉積有一定量焦炭的催化劑與從進氣管1和進料管4注入的流化介質接觸,將催化劑夾帶的反應油氣盡可能地汽提干凈。汽提后的催化劑在反應器中形成密相床層,溫度為600~850℃的水蒸氣經進氣管1和進料管4均勻的注入催化劑床層,進行水熱老化處理,處理時間為5~30min。含氧氣體經進氣管1注入反應器,使催化劑在含氧氣體作用下燒焦再生。再生后的催化劑在反應器內重復進行反應-老化-再生的過程,該過程重復1~72次。下面通過實施例進一步說明本發明提供的反應器及其使用方法,但本發明并不因此受到任何限制。對比例1該對比例采用中國石油撫順石化公司150萬t/a(噸/年)重油催化裂化裝置上的LBO催化劑的工業平衡劑進行固定流化床評價,并詳細分析該工業平衡劑的各項物化性質。以該對比例得到數據及分析結果作為催化劑污染、老化方法的比較基準。取上述LBO工業平衡劑200g進行固定流化床評價實驗,所用原料油為大慶原油的混合重質油,其性質見表1。固定流化床評價條件為:反應溫度500℃、劑油比4、空速8h-1、霧化蒸汽(占原料的重量百分比)6.6wt%。固定流化床評價實驗的結果及LBO工業平衡劑的物化性質見表2。對比例2采用美國Grace公司提供的催化劑循環污染、老化方法對500gLBO新鮮催化劑進行金屬污染和水熱老化,使催化劑的微反活性及鎳、釩含量與對比劑1中的工業平衡劑相當。主要實驗步驟如下:將500gLBO新鮮催化劑加入固定流化床裝置中,升溫、流化;溶解有環烷酸釩、環烷酸鎳和環烷酸鐵的直餾柴油,鎳的含量為600ppm,釩的含量為500ppm,鐵的含量為500ppm,原料以50g/min的流速注入固定流化床中,與LBO新鮮催化劑接觸,并在500℃下進行反應;用水蒸汽氣提反應后的催化劑,汽提后的催化劑在由空氣和蒸汽組成的混合氣體的作用下燒焦再生,再生溫度為700℃,上述反應-再生過程重復32次;收集實驗裝置內的催化劑,并對其進行物化性質分析和小型固定流化床評價實驗,評價實驗所用原料及操作條件與對比例相同。催化劑的各項物化性質以及評價實驗的結果見表2。實施例1本實施例用于說明本發明提供的催化劑重金屬循環污染老化反應器及其應用。本實施例所用的原料油為添加有環烷酸鎳、環烷酸釩和環烷酸鐵的大慶直餾柴油,該柴油原料中,鎳的含量為600ppm,釩的含量為500ppm,鐵含量為500ppm。所用實驗裝置為本發明所述的重金屬循環污染老化反應器裝置。按照圖1所示的催化劑重金屬循環污染老化反應器,所述的反應器主體11自上而下包括沉降段III、老化段II、預分布段I,反應器主體11橫截面積自上而下均逐漸縮小,沉降段III下端橫截面積與老化段II上端橫截面積相等,老化段II下端的橫截面積與預分布段I上端橫截面積相等。反應器沉降段III側壁與縱向軸線的夾角γ為33°,反應器老化段II側壁與縱向軸線的夾角β為25°,反應器預分布段I側壁與縱向軸線的夾角α/2為9°,且沉降段III的頂部邊緣采用圓角設計,圓角的半徑為12mm;老化段II的垂直高度與其頂端的橫截面的直徑比為3:1,老化段II的垂直高度為反應器垂直高度的60%,沉降段III的垂直高度與其頂端的橫截面的直徑比1:1.3,沉降段III的垂直高度為反應器垂直高度的36%。按照圖1所述,球面型塔板2用多孔氧化鋁陶瓷材料制得的氣孔率為35%、厚度為4mm、球面半徑為18mm。所述反應器內部的格柵3由中心圓環和均列在圓環周圍、與反應器內壁相連的橫桿組成,橫桿與圓環所在平面夾角δ為30°,橫桿數量為6個,圓環與橫桿的高度為4mm。氣體出口管5設置在沉降段III側壁、進料管固定管8設置在反應器頂部中心、頂部催化劑裝卸管9設置在反應器頂部,進氣管1與預分布段I的底部端口連通,并與反應器熔鑄為一體。氣體出口管5以O型圈密封連接方式與氣體冷凝管6連接,出口管5與氣體冷凝管6的端面上設計矩形O型圈凹槽。冷凝管6與出口管5連接端通過改變直徑形成一個腔室,在該腔室內放置玻璃纖維進行過濾,氣體冷凝管6與冷凝器相連。進料管4固定在進料管固定管8上,密封地穿過所述反應器的頂部與反應器主體連通,并穿過柵格3的中心圓環。進料管直徑從距進料管4出口1/5高度處開始縮小,進料管4的出口直徑為進料管4頂部直徑的1/2。本發明所述的除球面型塔板2外的反應器主體和連接構建均采用石英材質制得。實驗步驟如下:將500gLBO新鮮催化劑經催化劑裝卸管9加入反應器中,然后密封催化劑裝卸管9。水蒸氣自進氣管1進入反應器,在球面型塔板2的分散作用對催化劑進行流化。待催化劑床層壓降穩定后,將含有鎳和釩的上述大慶直餾柴油預熱至120℃后,以50g/min的質量流率與水蒸氣混合后從原料管4注入反應器中,與處于流化狀態的催化劑接觸,并反應,反應溫度為500℃,劑油比5。油劑混合物沿反應器上升,催化劑顆粒床層頂部的稀相區內的催化劑顆粒在老化段II上部及沉降段III內進行自由沉降,反應油氣和催化劑相分離。油氣經出口管5流出反應器,油氣中攜帶的少量細小顆粒在冷凝管6端口腔室內玻璃纖維的作用下進一步分離。水蒸氣從進氣管1和進料管4注入與沉積有一定量焦炭的催化劑接觸,將催化劑夾帶的反應油氣盡可能地汽提干凈。汽提后的催化劑在老化段II形成密相床層,溫度為800℃的水蒸氣經進氣管1和進料管4均勻的注入催化劑床層,進行水熱老化處理,處理時間為10min。高純空氣經進氣管1注入反應器,使催化劑在含氧氣體作用下燒焦再生。再生后的催化劑在反應器內重復進行反應-老化-再生的過程,該過程重復32次。裝置降溫,對裝置內的催化劑進行物化性質分析,分析結果見表2。表1項目數據密度(20℃)(kg·m-3)900.8餾程(℃)初餾點21310%34330%38750%483殘炭質量分數(%)4.74總硫質量分數(%)0.16表2由上表2的結果可知,在其他條件均不改變的條件下,采用本發明所述的催化劑重金屬循環污染老化反應器對新鮮催化劑進行處理,得到催化劑物化性能和反應評價結果與工業平衡劑接近;本發明所述的催化劑重金屬循環污染老化反應器的使用方法可在較短的老化時間內完成污染老化處理。由此可見,采用本發明所述的催化劑重金屬循環污染老化反應器具有結構簡單、水熱老化與重金屬循環污染老化靈活切換、冷卻系統簡單的特點,特別適應循環污染老化處理反應溫度高、水蒸氣量大、處理時間長的要求,可以更好地模擬工業平衡劑的性能。而這些優點是在常規的固定流化床反應器中無法實現的。以上詳細描述了本發明的優選實施方式,但是,本發明并不限于上述實施方式中的具體細節,在本發明的技術構思范圍內,可以對本發明的技術方案進行多種簡單變型,這些簡單變型均屬于本發明的保護范圍。另外需要說明的是,在上述具體實施方式中所描述的各個具體技術特征,在不矛盾的情況下,可以通過任何合適的方式進行組合,為了避免不必要的重復,本發明對各種可能的組合方式不再另行說明。此外,本發明的各種不同的實施方式之間也可以進行任意組合,只要其不違背本發明的思想,其同樣應當視為本發明所公開的內容。當前第1頁1 2 3