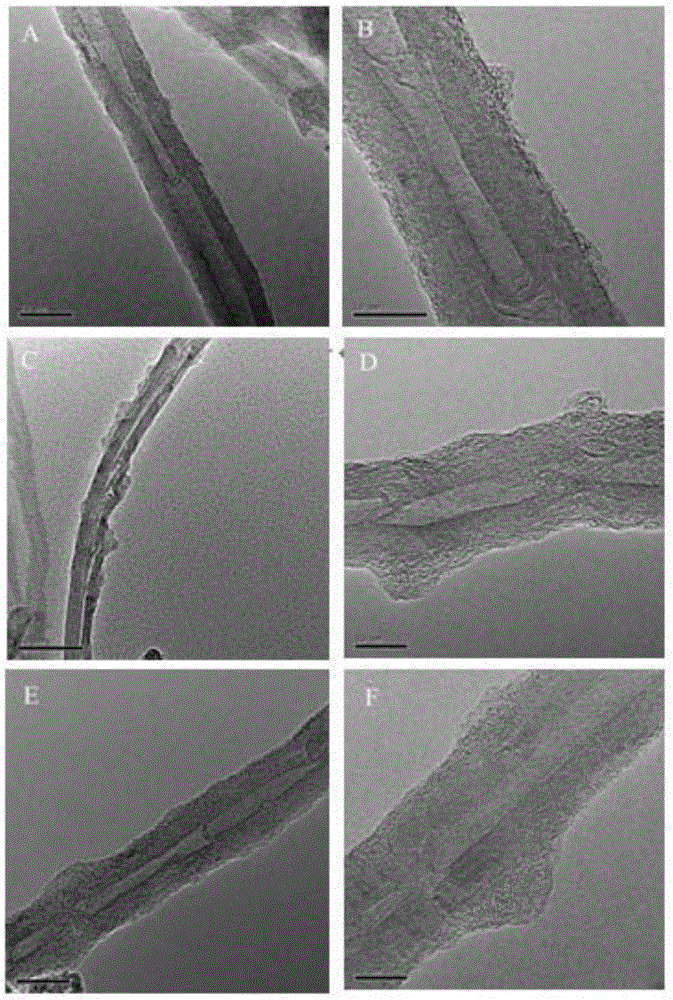
本發明屬于氮摻雜非金屬催化劑
技術領域:
,具體涉及一種氮摻雜非金屬催化劑、其制備方法和用途。
背景技術:
:現今世界能源和環境問題受到越來越多的關注,全球能源和環境正面臨越來越嚴峻的挑戰。石油儲量日益減少,而且原油重質化、劣質化的趨勢越來越嚴重,市場和環境對石油產品質量的要求日益提高。石油化工和精細化工領域內有大量的不飽和化合物、含氧化合物和含氮化合物,需通過一定的還原方法來制備后續產品。例如:芳胺是生產醫藥、農藥、染料、橡膠助劑、感光材料和石油溶劑等重要化工產品的原料和有機中間體,大多數芳胺的生產是通過硝基取代的芳香族化合物加氫還原制得。傳統的化學還原法所產生的廢水和廢渣會給環境帶來很大壓力,嚴重制約了經濟、社會的和諧發展。催化加氫是一項重要的化工生產技術,廣泛應用于各類有機化學品的合成和化工產品的精制過程。同時催化加氫還原法還具有環境友好,催化劑可回收,工藝先進,不涉及強酸、強堿介質等優點。綠色、高效的催化加氫技術在發達國家化工生產中得到了廣泛的應用。因此,具有自主知識產權的先進催化加氫技術的研發,特別是高效加氫催化劑的制備,是我國化學工業中一項十分迫切的任務。而且新型催化劑的研發是實現高效加氫還原和工業化應用的關鍵。電催化方面,目前為止發現的性能最好、使用最廣泛的低溫燃料電池氧還原電催化劑依然是鉑及鉑合金催化劑。然而貴金屬鉑的價格昂貴、資源有限,這嚴重阻礙了低溫燃料電池的商業化應用和發展。氧還原電催化劑在電催化反應過程中的主要作用是加速電極反應和抑制副反應,是提高燃料電池能量輸出效率、降低電池成本的關鍵。氧還原電催化劑的一個重要目標就是降低其中的鉑含量,研究更低價的非貴金屬催化劑來替代鉑基催化劑,同時增加或者保持催化劑的電催化性能和穩定性是推動燃料電池發展的關鍵。目前,許多工業領域的催化劑需要含有金屬,甚至是貴金屬。例如高效加氫催化劑多為活性組分以鉑、鈀、釕、金為代表的貴金屬催化劑和以鐵、鈷、鎳、鎢為代表的非貴金屬催化劑。貴金屬昂貴的價格使得金屬催化劑的應用受到限制,同時金屬催化劑在反應過程中容易中毒。另外,傳統燃料電池的電催化劑主要為貴金屬Pt類催化劑,同催化加氫催化劑一樣,Pt作為貴金屬的儲量低、價格高等一系列問題嚴重阻礙了其商業化進程。目前已有關于制備高效催化加氫催化劑的專利和研究包括的方法主要有:蔣月秀等人在專利CN104475136A中制備了一種非晶態Ni-P合金插層的膨潤土催化劑并將其應用于硝基苯的催化加氫。通過離子交換制得mNi/m膨潤土為0.002~0.098的Ni插層膨潤土,再通過Ni與P之間的靜電吸引作用將P插層進入膨潤土層間得到該非晶態合金催化劑。通過優化條件得到mNi/m膨潤土為0.098的非晶態Ni-P合金插層膨潤土催化劑應用于硝基苯催化加氫時催化活性和選擇性最高。類似的,在專利CN1850330A、CN1546229A、CN1792439A中提到了Ni-B非晶態合金催化劑的制備,并將其應用于催化加氫。這些催化劑在制備過程中均涉及到前驅體還原不徹底的問題,造成活性組分含量下降,活性組分流失。何代平等人在專利CN101658788B中報道了一種負載型雙金屬催化劑,將其應用于催化鹵代芳香硝基化合物加氫制得鹵代芳胺,在室溫、1MPa的加氫條件下,原料轉化率和目標產物選擇性均可達到100%。該催化劑的活性組分為Au和Pt、Pd、Ir、Ru之一的雙組份金屬,載體為TiO2、ZrO2、中性Al2O3或活性炭。另外,李小年等人在專利CN102285891B中提到在抑制劑胺類化合物(氯化銨、溴化銨、氟化銨、硫酸銨、硝酸銨、磷酸銨、甲酸銨、乙酸銨、碳酸銨)的存在下,由芳香硝基化合物催化加氫制備苯胺,催化劑多為負載型貴金屬(Pt、Pd、Ru)催化劑和非貴金屬催化劑(Ni/Al2O3、Ni/SiO2、Raney-Ni)。該方法可顯著減少偶氮類化合物的生成從而提高產品收率。馬磊等人在專利CN103191730A中提供了一種高選擇性催化加氫合成鹵代芳胺的銥炭催化劑。該催化劑在各類鹵代(氟、氯、溴、碘)的芳香硝基化合物催化加氫中均表現出顯著的加氫選擇性(鹵代芳胺產物選擇性均高于99%)。這些催化加氫催化劑的制備均涉及到Au、Pt、Ir等貴金屬,顯然增加了催化劑的制備成本,經濟效益和工業可行性差。陳日志等人在專利CN102091626A中報道了一種新型催化加氫催化劑,將納米級催化顆粒負載于硅烷改性的陶瓷膜表面,提高了催化劑的活性和穩定性。但對陶瓷膜載體進行改性過程中浸漬時間較長(1~100h),使得催化劑制備時耗較常。徐柏慶等人在專利CN200710099071.1中公開了一種負載型納米Au催化劑并將其應用于催化鹵代硝基苯液相加氫制鹵代苯胺,該催化劑能完全避免加氫脫鹵副反應的發生,但缺點是要在較高的溫度才具有較高的活性。MatthiasBeller等人利用Fe(OAc)2和一種有機含氮配體(鄰二氮雜菲)共同合成了一種Fe2O3基負載型催化劑,并將其應用于80余種芳香硝基化合物的催化加氫中,該非貴金屬催化劑在芳胺類化合物的合成中表現出了優越的催化活性和加氫選擇性。該方法成功利用儲量豐富、價格低廉的非貴金屬Fe替代了之前貴金屬作為活性組分在高效催化加氫中的應用,但加氫條件較苛刻(H2壓力≥5MPa,反應溫度為120℃,反應時間≥12h)。通過以上對目前研究現狀的分析可知,現有專利公開的催化劑主要包括非負載型催化劑和金屬負載型催化劑。非負載型催化劑主要包括骨架鎳和納米鎳,另一類應用廣泛的即為金屬負載型催化劑。加氫催化劑的有效活性組分主要是第Ⅵ族和第Ⅷ族的過渡元素,這些元素對氫有較強的親和力。金屬負載型催化劑主要是把活性組分如Ni、Pd、Pt等金屬載于載體上,提高了活性組分的分散性和均勻性,增加了催化劑的強度和耐熱性能。金屬催化劑的優點是活性高,在低溫下也可進行加氫反應,適用于大多數官能團的催化加氫。最常采用的元素有Pt、Pd、Rh、Ru、Ir等貴金屬和Fe、Mo、Co、Ni、W等為代表的非貴金屬。但催化劑中的金屬組分,特別是貴金屬組分,大大提高了催化劑的成本價格。近年來貴金屬價格高漲,且反應之后存在貴金屬催化劑的回收問題。金屬的儲量低、價格高等一系列問題嚴重阻礙了相應催化劑的商業化進程,受其經濟效益的制約目前還多處在實驗室研究階段。除了昂貴的價格使得金屬催化劑的應用受到限制,金屬催化劑另外的缺點是在反應過程中易中毒,例如燃料電池電催化氧還原(ORR)反應中的Pt電極非常容易CO中毒失活。在電催化方面,盡管目前氧還原電催化劑已經取得很多的研究進展,但是其商業化的應用中存在的兩個很大阻礙:過高的成本和差的穩定性,仍然沒有得到完全的解決。近年來,碳納米管、石墨烯等作為一種新興碳材料,以其良好的力學性質、獨特的化學結構、光學性質和熱穩定性等諸多優勢而在各個領域應用廣泛,在催化科學領域也不例外。近年來摻雜碳納米管/石墨烯在燃料電池氧還原電催化方面也表現出了良好的應用前景。摻雜碳納米管以其特殊的電子結構可獨立作為燃料電池氧還原催化劑,與傳統貴金屬催化劑相比,摻雜碳納米管/石墨烯催化劑在保持良好性能的前提下,可以大大降低催化劑的成本、延長使用壽命。本發明研發一種新型氮摻雜非金屬催化劑來降低催化劑的成本、提高其活性、選擇性和穩定性。技術實現要素:本發明的目的在于制備一種可高效應用的新型氮摻雜非金屬催化劑,該催化劑制備方法簡便、成本低廉、環境友好,在催化加氫領域和光電催化領域實現了利用非金屬替代金屬甚至貴金屬的實質性轉變,反應條件溫和,催化選擇性均達到100%,加氫目的產物產率高;同時,該氮摻雜非金屬催化劑在電催化氧還原領域也表現出良好的電催化活性。本發明的目的通過以下技術方案予以實現:本發明第一方面涉及一種氮摻雜非金屬催化劑,其以碳材料為骨架,并在所述碳材料的表面摻雜氮原子,形成包括碳原子和氮原子的涂層。所得催化劑的微觀結構隨所使用的碳材料的微觀結構而變化。在本發明優選的實施方案中,所述包含碳原子和氮原子的涂層是含氮聚合物的熱處理產物;該氮摻雜非金屬催化劑中的氮摻雜量為0.1wt%-2.6wt%。優選地,所述氮摻雜量為0.5wt%-2.6wt%。在本發明進一步優選的實施方案中,所述含氮聚合物為取代或未取代的多巴胺或取代或未取代的多巴胺鹽形成的聚合物、或取代或未取代的多巴(二羥苯丙氨酸)或取代或未取代的多巴(二羥苯丙氨酸)鹽形成的聚合物、或取代或未取代的去甲腎上腺素或取代或未取代的去甲腎上腺素鹽形成的聚合物,或其他類似結構分子形成的聚合物。在本發明優選的實施方案中,所述碳材料為單壁碳納米管、多壁碳納米管、氧化石墨烯、石墨烯、碳納米錐、碳纖維、C60、C70、金剛石或活性炭;所述含氮化合物為含氮可自聚粘附的化合物等。本發明第二方面涉及根據本發明第一方面所述的氮摻雜非金屬催化劑的制備方法,其包括以下步驟:(1)將碳材料、含氮化合物與緩沖液進行混合,得到懸浮液。其中所述緩沖液可以為pH=7-12的三羥甲基氨基甲烷-HCl緩沖液(Tris-HCl緩沖液)或磷酸鹽緩沖液(PBS緩沖液)。可以先將所述碳材料與緩沖液混合進行混合(或超聲處理),然后再加入所述含氮化合物繼續進行混合(或超聲處理),也可以將所述碳材料、所述含氮化合物與緩沖液直接混合(或超聲處理)。(2)將所述懸浮液室溫下攪拌1-48h后離心,將離心后的下層沉淀干燥后研磨成粉末。在該制備過程中通過控制攪拌時間的不同,可使不同量的含氮可自聚粘附化合物的聚合物粘附到碳材料上。(3)將得到的粉末在惰性氣體氣氛下于400-1200℃下煅燒0.5-4h,即得到所述氮摻雜非金屬催化劑。經過煅燒步驟,所述含氮可自聚粘附化合物的聚合物發生碳化,即得到本發明的催化劑。在本發明優選的實施方案中,所述碳材料為單壁碳納米管、多壁碳納米管、氧化石墨烯、石墨烯、碳納米錐、碳纖維、C60、C70、金剛石或活性炭;所述含氮化合物為含氮可自聚粘附的化合物。其中,當所述碳材料為碳納米管時,所述碳納米管需具有一定的孔徑,例如外徑為8-15nm,10-20nm,20-30nm,30-50nm。在本發明優選的實施方案中,所述含氮化合物為含氮可自聚粘附的化合物。這類含氮化合物更有利于附著在碳材料的表面,雖然碳材料具有疏水性,但該類含氮化合物也能夠簡易地沉積并附著于碳材料的表面。隨著制備過程中攪拌時間的延長,含氮聚合物涂層厚度逐漸增加。經XPS分析得,攪拌24小時后得到的該非金屬催化劑表面聚合物涂層中氮含量為0.98%,攪拌36小時后得到的該非金屬催化劑表面聚合物涂層中氮含量為1.25%。經元素分析(EA)分析得,攪拌24小時后該非金屬催化劑中氮含量為1.66%。即所述氮摻雜非金屬催化劑中的氮摻雜量隨制備過程中攪拌時間的延長而增加。在本發明進一步優選的實施方案中,所述含氮可自聚粘附的化合物為取代或未取代的多巴胺或取代或未取代的多巴胺鹽、或取代或未取代的多巴(二羥苯丙氨酸)或取代或未取代的多巴(二羥苯丙氨酸)鹽、或取代或未取代的去甲腎上腺素或取代或未取代的去甲腎上腺素鹽。本發明第三方面涉及根據本發明第一方面所述的氮摻雜非金屬催化劑用于催化加氫反應中的用途。在本發明優選的實施方案中,所述用途為氮摻雜非金屬催化劑用于硝基取代的芳香族化合物選擇性催化加氫中的用途。本發明第四方面涉及根據本發明第一方面所述的氮摻雜非金屬催化劑用于電催化氧還原反應中的用途。相對于現有技術,本發明的優點如下:1、本發明的催化劑僅含有C、N、O、H四種元素(其中O、H僅微量存在),制備過程完全不使用金屬,僅以碳材料和含氮化合物(例如為取代或未取代的多巴胺或取代或未取代的多巴胺鹽)為原料合成環境友好的氮摻雜非金屬催化劑。2、本發明的催化劑制備方法操作安全簡便,對設備要求寬松,僅僅需要簡單焙燒即可,成本低廉、環境友好。而且合成過程中利用超純水配制的Tris-HCl緩沖液作為溶劑,環境污染小,合成工藝綠色環保,符合可持續發展的戰略目標。3、本發明的催化劑催化活性高,性能穩定,催化劑壽命較長,高效應用范圍廣泛,在催化加氫領域和電催化氧還原領域實現了利用非金屬替代金屬甚至貴金屬的實質性轉變,反應條件溫和,原料轉化率和目標產物收率都很高,催化選擇性均可達到100%,加氫目的產物產率高;同時,該氮摻雜非金屬催化劑在電催化氧還原領域也表現出良好的電催化活性,具有良好的工業應用前景。附圖說明圖1為實施例1和實施例3制得的氮摻雜非金屬催化劑的X射線衍射(XRD)表征譜圖。圖2為實施例1-3制得的氮摻雜非金屬催化劑的透射電子顯微鏡(TEM)圖;其中圖A和B表示實施例2;圖C和D表示實施例1;圖E和F表示實施例3。圖3為實施例1和實施例3制得的氮摻雜非金屬催化劑的拉曼(Raman)表征譜圖,其中以碳納米管的Raman譜圖作為對照;其中圖A表示碳納米管,圖B表示實施例1,圖C表示實施例3。圖4為實施例1制備的氮摻雜非金屬催化劑在0.5M的H2SO4氧飽和溶液中不同旋轉速率下的旋轉圓盤伏安圖,掃描速率為10mVs-1。圖A和圖B分別為標準氫電極下,單位質量和單位面積催化劑上的電流密度。具體實施方式下面結合具體實施例和附圖對本發明進行進一步描述,但本發明并不局限于這些實施例。實施例1配制pH為8.5的Tris-HCl緩沖液(10mM)并定容于容量瓶中。將250mg的碳納米管(CNTs)(外徑OD為10-20nm)和250mL新鮮配制的上述Tris-HCl緩沖液加入圓底燒瓶中,超聲處理10min。再加入132.5mg的鹽酸多巴胺,繼續超聲處理30min,在室溫下攪拌24h。之后離心棄上層清液,將得到的沉淀置于真空干燥箱中在60℃下干燥12h,將其研磨成粉末,在N2氣氛下、800℃下煅燒2h,待冷卻至室溫后將得到的催化劑存放在干燥器中備用。實施例2在實施例1的基礎上,加入鹽酸多巴胺且超聲處理后,在室溫下攪拌6h,其余制備步驟與實施例1相同。實施例3在實施例1的基礎上,加入鹽酸多巴胺且超聲處理后,在室溫下攪拌36h,其余制備步驟與實施例1相同。實施例4在實施例1的基礎上,將研磨得到的粉末在N2氣氛下、600℃下煅燒2h,其余制備步驟與實施例1相同。實施例5在實施例1的基礎上,將研磨得到的粉末在N2氣氛下、800℃下煅燒2h,其余制備步驟與實施例1相同。實施例6在實施例1的基礎上,將研磨得到的粉末在N2氣氛下、1000℃下煅燒2h,其余制備步驟與實施例1相同。實施例7配制PH為8.5的Tris-HCl緩沖液(10mM)并定容于容量瓶中。將159.2mg的氧化石墨烯(GO)和35mg鹽酸多巴胺加入到140mL新鮮配制的上述Tris-HCl緩沖液加入圓底燒瓶中,超聲處理16min,在室溫下攪拌24h。之后離心棄上層清液,將得到的沉淀置于真空干燥箱中在60℃下干燥12h,將其研磨成粉末,在N2氣氛下、800℃下煅燒2h,待冷卻至室溫后將得到的催化劑存放在干燥器中備用。實施例8在實施例1的基礎上,將碳納米管(CNTs)(外徑OD為10-20nm)換為碳粉,其余制備步驟與實施例1相同。實施例9在實施例1的基礎上,將132.5mg的鹽酸多巴胺換為137.8mg的多巴(二羥苯丙氨酸),其余制備步驟與實施例1相同。實施例10在實施例1的基礎上,將132.5mg的鹽酸多巴胺換為118.2mg的去甲腎上腺素,其余制備步驟與實施例1相同。對比實施例1在實施例1的基礎上,將研磨得到的粉末在N2氣氛下、200℃下煅燒2h,其余制備步驟與實施例1相同。對比實施例2在實施例1的基礎上,將研磨得到的粉末不經煅燒直接作為催化劑存放在干燥器中備用。圖1為實施例1和實施例3制得的氮摻雜非金屬催化劑的XRD表征譜圖。圖1中26°和43.5°分別對應石墨的(002)和(100)特征衍射峰,由圖可以看出碳納米管在摻雜非金屬N原子后,其晶型并沒有發生明顯變化,說明碳納米管在摻雜非金屬N原子后還保持著高度石墨化結構。由XRD表征結果可知,攪拌24小時得到的催化劑比攪拌36小時得到的催化劑晶化程度更高。氮摻雜會引起碳納米管表面的缺陷增多,增大了其無序性,使原本完美的石墨結構被破壞,降低了晶化程度。該結果與圖3中的Raman譜圖表征結果相吻合。圖2為實施例1-3制得的氮摻雜非金屬催化劑的TEM圖;其中圖A和B表示實施例2;圖C和D表示實施例1;圖E和F表示實施例3。由圖2可見,碳納米管為空心狀結構,其外徑為10-20nm,壁厚大約為7nm。從圖中可清晰的觀察到碳納米管外表面的一層附著物即是聚多巴胺煅燒后的附著物。比較TEM圖像可知,本發明的氮摻雜非金屬催化劑制備過程中的攪拌時間會影響碳納米管外表面附著物的附著量,即氮元素在碳納米管上的摻雜量,攪拌時間越長附著物層越厚,氮摻雜量越多。圖3為實施例1和實施例3制得的氮摻雜非金屬催化劑的Raman表征譜圖,其中以碳納米管的Raman譜圖作為對照;其中圖A表示碳納米管,圖B表示實施例1,圖C表示實施例3。圖3顯示碳納米管和摻氮碳納米管的Raman光譜圖,兩條譜線在1340cm-1和1576cm-1附近都有兩個明顯的譜峰,分別對應碳納米管的D峰和G峰。D峰是由結構缺陷和雜質誘導產生,而G峰是石墨層片間的振動模式產生。一般認為D峰和G峰的積分強度之比反比于材料的石墨化度。Raman得到的ID/IG常被用來量化碳材料的無序或缺陷程度;ID/IG反映了CNTs結構的無序性。由圖中數據可知,N摻雜后,ID/IG增大,N原子的摻雜破壞了CNs原本完美的對稱結構,引起缺陷,從而降低了CNTs的晶化程度,這與XRD表征結果一致。實施例9-催化對硝基苯酚催化加氫反應配制0.125mM的對硝基苯酚溶液(溶劑為叔戊醇)10mL于玻璃帶蓋小瓶中,分別加入105mg上述實施例1-8及對比實施例1-2中制得的催化劑,攪拌1h,待催化劑吸附飽和后,離心棄上層清液后待用。在反應釜中加入同濃度(0.125mM)的對硝基苯酚溶液10mL,將離心后得到的催化劑加入,使反應物和催化劑混合均勻后取樣待測。安裝好反應裝置,檢查反應體系的氣密性,氣密性良好后用氫氣排空3-4次,然后調節氫氣壓力達到2MPa,壓力穩定后升溫至120℃,開啟攪拌(轉速為800rpm),開始計時,反應時間為4h。反應結束后離心分離催化劑,用氣質聯用儀和氣相色譜分析反應產物。對硝基苯酚催化加氫反應的反應式如下所示(其中P代表壓力,T代表溫度):反應結果見下表:表1:催化對硝基苯酚催化加氫反應結果實施例11-催化其他化合物加氫反應以叔戊醇作溶劑,配置一定濃度的不飽和化合物的反應溶液于玻璃小瓶中,分別加入一定量的實施例1制得的摻氮非金屬催化劑,攪拌1h,待催化劑吸附飽和后,離心洗滌待用。在反應釜中加入配置好的一定量的不飽和化合物反應物溶液(叔戊醇作溶劑),再加入吸附飽和后的催化劑,使反應物和催化劑混合均勻后取樣待測。安裝好反應裝置,檢查反應體系的氣密性,氣密性良好后用氫氣排空3-4次,然后調節氫氣壓力達到2MPa,壓力穩定后升溫至120℃,開啟攪拌(轉速為800rpm),開始計時,反應時間為4h。反應結束后離心分離催化劑,用氣質聯用儀和氣相色譜分析反應產物。反應結果見下表:表2:催化其他硝基取代的芳香族化合物催化加氫反應結果實施例12-摻氮非金屬催化劑在催化加氫反應中的重復使用情況選擇對硝基苯酚催化加氫作為模型反應測試實施例1中制備的摻氮非金屬催化劑的重復使用性能。催化加氫反應條件如前所述:對硝基苯酚:1.25mmol(叔戊醇為溶劑,體積為10mL),催化劑:105mg,H2壓力:2MPa,反應溫度:120℃,攪拌速率:800rpm。將每次反應后得到的混合物逐次轉移至2mL離心管中離心,棄去上層清液。將得到的催化劑進行洗滌,在離心管中加入叔戊醇搖勻超聲洗滌后,離心后棄去上層清液。反復洗滌數次后將催化劑直接用于下一次反應,加氫反應前取樣分析。摻氮非金屬催化劑的重復使用情況見表3:表3:摻氮非金屬催化劑的重復使用情況編號回用次數轉化率/%選擇性/%1回用第一次1001002回用第二次1001003回用第三次1001004回用第四次1001005回用第五次69.01006回用第六次56.5100實施例13-摻氮非金屬催化劑的電化學性能測試催化劑的氧還原電催化活性測試主要通過電化學工作站AUTOLAB302N型恒電位儀和旋轉圓盤裝置進行測試。本實驗采用三電極體系:工作電極為表面負載著實施例1中制備的摻氮非金屬催化劑的玻璃碳電極,參比電極為Ag/AgCl電極,對電極為鉑絲。本實驗中用于循環伏安(CyclingVoltammertry,CV)測試的玻璃碳電極直徑為5.0mm,用于線性伏安掃描(LinearSweepVoltammetry,LSV)的玻璃碳電極為旋轉圓盤的電極,直徑為5.0mm。電極的制備包括以下步驟:(1)催化劑分散液的制備:準確稱取6mg實施例1中制備的摻氮非金屬催化劑樣品,分散到2mL75%的異丙醇水溶液中,超聲30min后,滴加50μL的Nafion溶液,超聲數小時后使其充分分散均勻,得到催化劑分散液墨水;(2)工作電極的制備:準確稱取一定量(15μL)的上述催化劑分散液墨水,滴到玻璃碳電極表面,用蓋子覆蓋8h,充分干燥,將蓋子覆蓋的電極于60℃真空干燥箱中真空干燥30min。測量流程包括以下步驟:(1)連接好旋轉圓盤裝置,通入氬氣30min。(2)進行循環伏安(CV)測掃:循環伏安法是一種常見的電化學研究方法,CV通過在工作電極上施加一個三角波形的電壓信號,并同時測量其電流響應。對于氧還原反應過程,我們主要通過循環伏安反向掃描峰的起始電位和峰電流值對催化劑的電催化氧還原能力進行評價,氧還原峰的起始電位越正、峰電流值越大,則催化劑的氧還原電催化性能越好。循環伏安曲線的測試條件為:酸性條件下為-0.197~+0.803V(vsAg/AgCl),掃描速率為50mV·s-1。線性伏安掃描法(LSV)是一種將一快速線性變化電壓施加于電極上,并根據所得的I-E曲線對樣品電化學性能進行分析的方法。通過線性伏安掃描法可以得到樣品的極化曲線,通過分析極化曲線可以得到電極電位與極化電流或者極化電流密度之間的關系。測試條件為:在0.5MH2SO4中,掃描范圍為--0.197~+0.803V(vsAg/AgCl);掃描速率為10mV/s;旋轉圓盤電極的轉速為400、600、800、1200、1600、2000、2400、2800以及3600rpm。測試結果如圖4所示。圖4為實施例1制備的氮摻雜非金屬催化劑在0.5M的H2SO4氧飽和溶液中不同旋轉速率下的旋轉圓盤伏安圖,掃描速率為10mVs-1。圖A和圖B分別為標準氫電極下,單位質量和單位面積催化劑上的電流密度。從圖中可以看出,在酸性電解液中,參比電極換算為標準氫電極時,起始電位為0.51V,說明本發明的氮摻雜非金屬催化劑對燃料電池中的氧還原反應(ORR)有很好的電催化活性。當前第1頁1 2 3