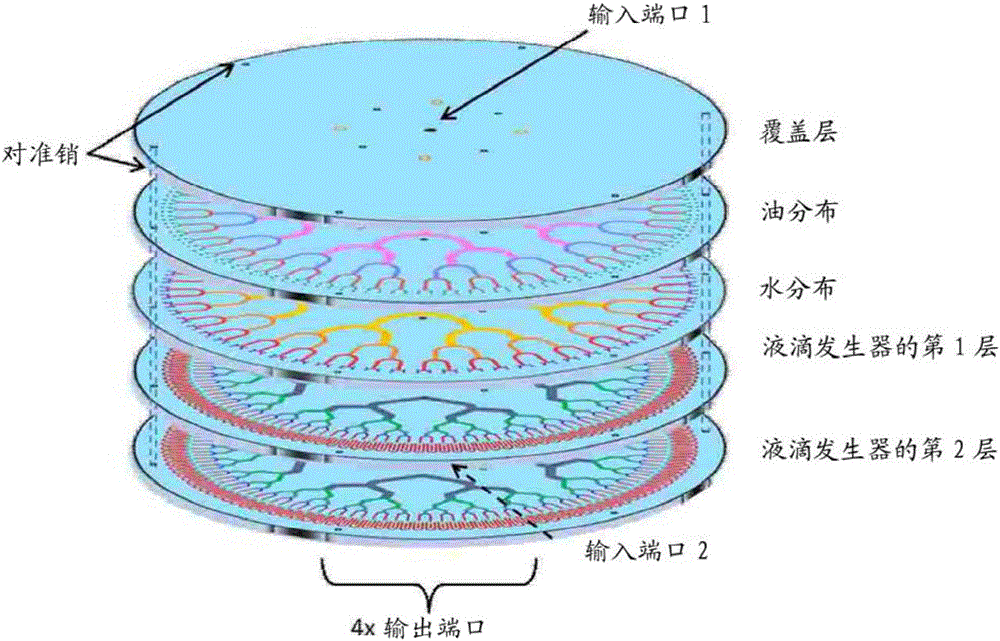
本申請要求2013年11月11日提交的美國臨時申請No.61/902,600的權益,將其全部通過參考引入。
技術領域:
本發明涉及用于制造(生產)單分散的乳液的器件和方法以及連續后處理技術。
背景技術:
:微流控學已獲得越來越多的關注,具有被應用于例如芯片實驗室、燃料電池、診斷系統、微反應器、材料的合成和許多其它的領域中的潛力。微流控學還提供用于制造對于例如藥物遞送和生活消費品的行業有意義的均勻地尺寸化的乳液和膠囊的潛力。高度單分散的乳液的產生對于例如藥物、化妝品、腐蝕性化學品和精細化學品的公司以及食品工業可為非常重要的。技術實現要素:用于微流控系統的并行化(平行化,paralellization)的多層微流控器件可包括包含多個通道以控制流體的流動的分布網絡,所述分布網絡形成于至少兩個板或基材層中以形成通過各層中的通孔在所述層之間對準(align)的流體通道的分形(fractal)圖案。流體通道的分形圖案可同時運行。并行化容許使用者同時運行多個微流控系統,其可以大的量制造微流控乳液。所述器件可包括從所述器件的表面能到達的輸入端。所述通道可在由聚合物塑料材料例如聚(甲基丙烯酸甲酯)、不銹鋼、陶瓷、或玻璃或其組合制成的基材或板上。所述通道可以基于遵循方程p×m×2n的任意數的圖案布置,其中p為代表瓣(petal)的數量的整數,m為代表相同的產生層的數量的整數且n為代表分形支化水平的數量的整數。所述分布網絡可連接形成乳液產生層的板或基材的堆。所述分布網絡可包括至少兩個分布層,各分布層包括流體通道的分形圖案和將它們與乳液產生層的堆互連的通孔。所述器件可包括至少一個入口或輸入端以及至少1個出口或輸出端以容許不混溶的液體的可達性和液滴的離開。在一些實施方式中,所述器件可包括每種不混溶的流體的至少一個入口或輸入端。形成乳液的方法可包括使流體通過包括至少兩個層的多層器件,其中所述兩個層通過通孔連接,其中各層包括分形圖案,和其中各層包括分配所述乳液的與所述器件的通道連接以控制流體到出口的流動的分布網絡。所述乳液可為單分散的或多分散的。用于后處理乳液的方法可包括將流體供應到具有彎曲表面的處理區使得所述流體形成沒有側面邊緣的均勻的且連續的層。所述處理區可包括具有彎曲表面的管。替代地,所述處理區可包括類似于球形噴泉(ball-fountain)的開放的圓形表面。所述方法可包括將乳液輸出端排列在具有彎曲表面的管周圍或在所述開放的圓形表面周圍。所述方法可包括:對所述彎曲表面進行熱處理以形成適合用于藥物、涂料或其它應用的晶體和另外的單分散的顆粒,或對所述彎曲表面進行UV處理以形成晶體和另外的單分散的顆粒。在一個方面,多層微流控器件可包括與所述器件的通道連接以控制流體的流動的分布網絡,所述分布網絡包括至少兩個板或基材層,各層包括和雕刻(蝕刻)有通過孔在所述板或基材層之間對準的通道的圖案以容許不混溶的液體的組合和均勻的液滴的形成。在所述多層器件中,流體可在所述器件中從一個層流動到另一層。在一些實施方式中,所述器件可包括從所述器件的表面能到達的軸對稱的輸入端。如果包含較多的液體,則所述輸入端可從一個位置開始然后被引導至中部用于初始分布。各層的厚度可小于1mm或更多,而所述通道可形成于可由聚合物材料例如聚(甲基丙烯酸甲酯)或任何另外的材料例如金屬例如不銹鋼、硅、玻璃或陶瓷或以上中的任意的組合制成的基材或板上。在一些實施方式中,所述板上的雕刻的圖案可導致范圍從至少2個通道起的低或高數量的通道和更多遵循該方程至少p×m×2n的微流控液滴發生器(MFDG),其中p為代表(下面說明的)瓣的數量的整數,m為代表相同的產生層的數量的整數且n為代表分形支化水平的數量的整數,且因此p×2n為每個層的發生器的數量。例如,所述器件可包括至少128個通道、至少256個通道、至少512個通道、或至少1024個通道。所述器件可包括分布由正被使用的工藝的化學所要求的任意數量的不混溶的流體的多個層。各層可對應于單獨的流體。在一些實施方式中,所述器件可進一步包括水分布層。所述器件可包括油分布層。所述器件可包括覆蓋層。在另一方面,用于處理乳液的系統可包括封閉的彎曲表面或開放的圓形表面以及至少一個輸出端,所述輸出端將所述乳液作為層供應在所述封閉的彎曲表面的表面上。所述系統可包括至少四個供應乳液的輸出端。所述輸出端可包括排列在所述封閉的彎曲表面周圍的多個輸出端。所述乳液可將所述封閉的彎曲表面的橫截面的整個周邊潤濕以消除對于(with)干的對應物的側面邊緣。以這種方式處理容許通過可操控由所述并行化的系統產生的容量的產物的發展的后處理系統以大的量操控微流控乳液。在一些實施方式中,所述系統可連接到包括至少兩個層的多層微流控器件,其中所述兩個層通過通孔連接,其中各層包括分形圖案,和其中各層包括與所述器件的通道連接以控制流體的流動的分布網絡。各層可包括分布通道和通孔。在另一方面,用于制備乳液的方法可包括使用多層微流控器件,所述多層微流控器件包括至少兩個層,其中所述兩個層通過通孔連接,其中各層包括分形圖案,和其中各層包括所述器件的分布網絡和多個通道以控制流體的流動。至少一個層可包括剛性材料。在一些實施方式中,所述乳液可為單分散的。所述乳液的制造速率可為至少300mL/h。在另一方面,用于處理乳液的方法可包括將流體從混合器或乳液源供應到具有彎曲表面的處理區,使得所述流體形成沒有從潤濕的表面到干燥表面的過渡的側面邊緣的層。所述處理區可包括具有彎曲表面的管或開放的圓形表面。所述流體可接觸所述表面的壁以形成薄膜。所述流體可將所述彎曲表面的整個周邊潤濕。所述表面可聚集和均勻地分布乳液供應的輸出端,使得它可被連續地且均勻地處理。該過程的實例可包括熱處理或UV曝光處理。在一個實施方式中,圓柱體可讓其壁均勻地涂覆有向下滑動并且容許后處理的流動著的乳液的薄層。在另一實施方式中,開放的圓形表面可讓其表面均勻地涂覆有流動著的乳液的薄層。在一些實施方式中,所述開放的圓形表面可為開放的球。在一些另外的實施方式中,所述開放的圓形表面可為圓形的柱。在一些實施方式中,所述方法可使用至少四個輸出端以將流體從混合器供應到處理區。所述方法可包括將乳液輸出端排列在具有彎曲表面的管周圍。在一些實施方式中,所述方法可包括加熱所述彎曲表面。所述方法可包括加熱沒有邊緣的流體的層。所述方法可包括使處理區暴露于紫外光。在一個方面,多層微流控器件可包括連接乳液產生層的堆的分布網絡,其中所述分布網絡可包括至少兩個分布層,各分布層包括流體通道的分形圖案和將它們與乳液產生層的堆互連的通孔。所述產生層的數量可為整數,例如,1、2、3、4、5、6、7、8、9、或10個、更多。所述乳液產生層可通過微流控液滴發生器的極陣列(環形陣列,polararray)形成。所述乳液產生層可包括至少128個發生器、或至少256個發生器、或至少512個發生器、或至少1024個發生器。各發生器可為以上描述的通道。根據瓣的數量和每瓣的發生器的數量,所述器件的另外的構造可具有不同數量的發生器。由以下描述、附圖和權利要求書,其它方面、實施方式和特征將是明晰的。附圖說明圖1A顯示以聚(甲基丙烯酸甲酯)("PMMA")制作的具有256個通道的微流控芯片,其包括2個堆疊的各自128個通道的層。圖1B顯示器件的側面圖像。圖2顯示形成用于兩種流體的器件的層的實例設計,其具有兩個用于油和水供應的分布網絡和兩個液滴產生層。圖3顯示組裝的堆。圖4顯示蓋層或頂部層。圖5顯示連續相分布網絡和分布網絡。圖6顯示分散相分布網絡和分布網絡。圖7顯示發生器的第一層、或底部層。圖8顯示發生器的中間層。例如,它可為第二層、第三層、第四層等。圖9顯示形成器件的不同的層。圖10顯示液相如何從輸入端通過分布層流動到發生器的示意圖。圖11顯示當產生層中的發生器同時工作時它們看起來如何的特寫圖像。圖12顯示關于所測試的不同的多層微流控器件的尺寸和變異系數的結果。圖12A為描繪在不同的分散相流動速率下的液滴尺寸的圖。圖12B為描繪作為每個產生層的流動速率的函數的變異系數的圖。圖13A顯示用于微流控液滴發生器的大規模并行化的實驗裝置的實例,其中所述裝置包括其中可處理輸出乳液的后處理臺。為了容易的可視化,圖13B和13D顯示經染色的油包水乳液的實例的圖像。圖13C為描繪有效直徑分布的圖。圖14顯示說明瓣如何在芯片內充當獨立的單位的瓣構造。圖15顯示描繪當關閉不同數量的瓣時對乳液的分散性的影響的圖。圖16和圖17顯示用于微流控液滴發生器的大規模并行化的實驗裝置的實例,其中所述裝置包括其中可處理輸出乳液的后處理臺。圖18顯示在PMMA上切削的微流控通道的SEM照片。圖19顯示甘氨酸球形晶體附聚物的結晶化。圖19A為甘氨酸球形晶體附聚物的SEM圖像。圖19B為描繪由液滴的快速收縮、成核、球晶生長、和陳化組成的結晶化順序的示意圖。圖19C為甘氨酸晶體附聚物的SEM圖像。圖19D為甘氨酸球形晶體附聚物的光學圖像。圖20顯示分布網絡的實例。圖20A是環形的分布網絡。圖20B是與樹狀結構組合的環形的分布網絡。圖20C是分形樹狀分布網絡。在插圖中,藍色表示水相的進料路線,而橙色表示油相的路徑。對于圖20C,水相和油相具有相同的路徑但在不同的層中且排列以形成瓣。圖21顯示在開放的圓形表面中的后處理的示意圖。圖22顯示在開放的圓形表面中的UV后處理的示意圖。圖23顯示具有6個瓣的器件的實例,其中每個瓣具有八個發生器。具體實施方式在過去二十幾年中的基于液滴的微流控學的發展已經為在若干研究領域中的快速和連續的進步提供機會。在精細化學、藥物發現、和生物學中的應用已得益于它們的整個系統向納升到飛升尺寸液滴的微型化。由于該尺寸減小,給定系統的表面積對體積比變得更大,且表面相關的物理學支配體積現象。該技術已容許新的方法來實現在宏觀尺度上是不可能的實驗。參見,A.B.Theberge,F.Courtois,Y.Schaerli,M.Fischlechner,C.Abell,F.Hollfelder和W.T.S.Huck,Small,2010,49,5846-5868,其全部通過參考引入。例如,液滴中的快速熱傳遞容許在顆粒的合成中的以及對芯片溫度循環的精確溫度控制。參見E.Chan,A.Alivisatos和R.Mathies,J.Am.Chem.Soc.,2005,127,13854-13861,S.Xu,Z.Nie,M.Seo,P.Lewis,E.Kumacheva,H.A.Stone,P.Garstecki,D.B.Weibel,I.Gitlin和G.M.Whitesides,Angew.Chem.,2005,117,734-738,以及Y.Schaerli,R.C.Wootton,T.Robinson,V.Stein,C.Dunsby,M.A.A.Neil,P.M.W.French,A.J.deMello,C.Abell和F.Hollfelder,Anal.Chem.,2009,81,302-306,其各自全部通過參考引入。可在液滴的尺度上控制的其它反應參數包括:試劑的量、混合速率(通過分散或者通過微流控混合器輔助)、停留時間、和與后處理步驟有關的另外的參數(例如UV曝光時間、結晶化溫度等)。參見D.J.Han,J.H.Jung,J.S.Choi,Y.T.Kim和T.S.Seo,LabChip,2013,13,4006-4010,G.T.N.Khalid,M.A.Neves,T.Kuroiwa,M.Nakajima,K.Uemura,S.Ichikawa和I.Kobayashi,Adv.DrugDeliveryRev.,2013,65,1626-1663,以及E.Chan,A.Alivisatos和R.Mathies,J.Am.Chem.Soc.,2005,127,13854-13861,其各自全部通過參考引入。試劑的內在的低消耗和對于液滴環境條件的增強的控制保持使得實現化學和生物實驗室的高通量篩選的希望。例如,基于液滴的微流控學已被用于分子分析方面的研究、以及其中可以較小的量消耗有價值的試劑的單細胞研究。參見J.Hong,J.B.Edel和A.J.deMello,DrugDiscoveryToday,2009,14,134-146;S.-Y.Teh,R.Lin,L.-H.Hung和A.P.Lee,LabChip,2008,8,198;以及M.T.Guo,A.Rotem,J.A.Heyman和D.A.Weitz,LabChip,2012,12,2146-2155,其各自全部通過參考引入。由于反應被限制在微小的量,因此當關注安全性時,還可以低的風險操控反應性試劑和產物。由于液滴微流控學所提供的所有益處,在各種領域中復雜反應動力學的研究和經設計的顆粒的合成已經是可行的。通過該技術設計和合成的顆粒的實例包括:聚合物顆粒,17,18微膠囊,納米顆粒,量子點,光子晶體等。參見M.Seo,Z.Nie,S.Xu,M.Mok,P.C.Lewis,R.Graham和E.Kumacheva,Langmuir,2005,21,11614-11622;J.I.Park,A.Saffari,S.Kumar,A.Günther和E.Kumacheva,Annu.Rev.Mater.Res.,2010,40,415-443;R.K.Shah,H.C.Shum,A.C.Rowat,D.Lee,J.Agresti,A.S.Utada,L.-Y.Chu,J.-W.Kim,A.Fernandez-Nieves,C.J.Martinez和D.A.Weitz,Mater.Today,2008,11,18-27;W.J.Duncanson,T.Lin,A.R.Abate,S.Seiffert,R.K.Shah和D.A.Weitz,LabChip,2012,12,2135-2145;K.-S.Huang,K.Lu,C.-S.Yeh,S.-R.Chung,C.-H.Lin,C.-H.Yang和Y.-S.Dong,J.ControlledRelease,2009,137,15-19;C.H.Yang,K.S.Huang,Y.S.Lin,K.Lu,C.C.Tzeng,E.C.Wang,C.H.Lin,W.Y.Hsu和J.Y.Chang,LabChip,2009,9,961-965;S.A.Khan和S.Duraiswamy,LabChip,2012,12,1807-1812;S.Duraiswamy和S.A.Khan,Small,2009,5,2828-2834;A.M.Nightingale和J.C.deMello,ChemPhysChem,2009,10,2612-2614;以及Y.Zhao,X.Zhao,J.Hu,M.Xu,W.Zhao,L.Sun,C.Zhu,H.Xu和Z.Gu,Adv.Mater.,2008,21,569-572,其各自全部通過參考引入。為了產生這些微反應器,使用微流控液滴發生器(MFDG)。不同類型的MFDG和它們的特性總結在別處。參見例如,C.-X.Zhao,Adv.DrugDeliveryRev.,2013,65,1420-1446;R.K.Shah,H.C.Shum,A.C.Rowat,D.Lee,J.Agresti,A.S.Utada,L.-Y.Chu,J.-W.Kim,A.Fernandez-Nieves,C.J.Martinez和D.A.Weitz,Mater.Today,2008,11,18-27;J.-T.Wang,J.Wang和J.-J.Han,Small,2011,7,1728-1754;以及G.T.I.Kobayashi和M.Nakajima,Microfluid.Nanofluid.,2012,13,151-178,其各自全部通過參考引入。典型的MFDG是將兩種不混溶的流體一起帶到一個位置的一組微通道。在該節點(junction)中,兩種液體的粘性力和界面張力之間的相互作用導致液滴形成。這些器件的產物的分布可通過它們的變異系數(Cv)度量,變異系數(Cv)定義為樣品的標準偏差和平均直徑之間的比率。當所述分布足夠窄(Cv≤5%)時,所述乳液被稱為單分散的。參見A.Jillavenkatesa,S.J.Dapkunas和L.-S.H.Lum,ParticleSzieCharacterization,Washington,2001,其全部通過參考引入。盡管已經展示了在液滴微流控學方面的許多進步,但是與這些研究有關的低容量生產能力已經阻礙了它們在工業中的采用。單個MFDG的典型的制造速率為大約1-10mL/h的液滴,而工業應用經常要求高出若干數量級的制造速率。參見T.Nisisako,T.Ando和T.Hatsuzawa,LabChip,2012,12,3426-3435,其全部通過參考引入。該缺點已使得液滴微流控學技術僅對于高附加值的工業例如藥物、食品、精細化學、和化妝品是有吸引力的。參見C.Haber,LabChip,2006,6,1118-1121,G.M.Whitesides,Nature,2006,442,368-373,G.Muschiolik,Curr.Opin.ColloidInterfaceSci.,2007,12,213-220,以及O.Skurtys和J.M.Aguilera,FoodBiophysics,2007,3,1-15,其各自全部通過參考引入。用于增加液滴的總產量和基于液滴的微流控應用的可能的解決方案是并行化,其由將具有共享的輸入端的同時工作的單獨的MFDG數量提高(number-up)組成。目前在工業中,存在若干種乳液形式的液滴產生方法。參見M.F.Edwards,N.Harnby和A.W.Nienow,MixingintheProcessIndustries,Butterworth-Heinemann,2ndedn.1992,以及P.Walstra,Chem.Eng.Sci.,1993,48,333-349,其各自全部通過參考引入。常規的乳化技術在容器中使用兩種不混溶的相的連續的高剪切混合以導致乳液的間歇制造。這些方法的實例為:高速摻合機、膠體磨機、高壓均化器、和超聲均化器。參見D.J.McClements,FoodEmulsions:Principles,Practice,andTechniques,CRCPressLLC,1999,以及S.M.Joscelyne和G.J.Membr.Sci.,2000,169,107-117,其各自全部通過參考引入。它們典型地以寬的尺寸分布(Cv~30%)和大約100-20,000L/h的制造速率制造在0.1-100μm直徑范圍內的液滴。膜乳化是第二種類型的乳化技術,其中分散相被壓力驅動通過控制尺寸的多孔膜進入連續相中。參見R.A.Williams,S.J.Peng,D.A.Wheeler,N.C.Morley,D.Taylor,M.Whalley和D.W.Houldsworth,Chem.Eng.Res.Des.,1998,76,902-910,以及T.Nakashima,M.Shimizu和M.Kukizaki,Adv.DrugDeliveryRev.,2000,45,47-56,其各自全部通過參考引入。液滴的尺寸和尺寸分布強烈地依賴于膜的孔尺寸。典型地,液滴尺寸范圍在0.1到10μm直徑之間,變異系數為10-20%且制造速率為15-300L/h。類似的方法是所謂的微通道乳化,其利用具有微制作的通道或狹縫的基材代替膜中的孔。參見I.Kobayashi,Y.Wada,K.Uemura和M.Nakajima,Microfluid.Nanofluid.,2010,8,255-262,I.Kobayashi,M.A.Neves,Y.Wada,K.Uemura和M.Nakajima,GreenProcessesSynth.,2012,1,353-362,其各自全部通過參考引入。該技術容許窄得多的尺寸分布(Cv<5%),但處于較低的制造容量。這樣的一個實例是Kobayashi等的工作,報道了1.4L/h的制造速率。在絕緣體晶片上的硅上深反應離子蝕刻微洞。然后將微制作的結構放置在兩個加壓的腔室之間并且與膜乳化的情況相比,分散相通過微洞流動到連續相中。表1.微流控乳液發生器技術的總結*參見T.Nisisako,T.Ando和T.Hatsuzawa,LabChip,2012,12,3426-3435(“Nisisako”);W.Li,J.Greener,D.Voicu和E.Kumacheva,LabChip,2009,9,2715(“Li”);M.B.Romanowsky,A.R.Abate,A.Rotem,C.Holtze和D.A.Weitz,LabChip,2012,12,802(“Romanowsky”);M.Muluneh和D.Issadore,LabChip,2013,13,4750-4754(“Muluneh”);G.Tetradis-Meris,D.Rossetti,C.PulidodeTorres,R.Cao,G.Lian和R.Janes,Ind.Eng.Chem.Res.,2009,48,8881-8889(“Tetradis-Meris”);Y.Zeng,R.Novak,J.Shuga,M.T.Smith和R.A.Mathies,Anal.Chem.,2010,82,3183-3190,(“Zeng”);J.Guzowski,P.M.Korczyk,S.Jakiela和P.Garstecki,LabChip,2011,11,3593-3595(“Guzowski”);R.Dangla,S.C.Kayi和C.N.Baroud,Proc.Natl.Acad.Sci.U.S.A.,2013,110,853-858(“Dangla-PNAS”);R.Dangla和C.N.Baroud,ProductionofMonodisperseBulkEmulsionsinaBeakerUsingaNovelMicrofluidicDevice,Freiburg,2013,pp.83-85(“Dangla-Freiburg”),其各自全部通過參考引入。微流控乳液發生器技術的總結參見表1。Dangla等最近介紹了用于產生單分散的乳液的微通道乳化系統的另一變型。在該工作中,液滴形成通過微通道中的受限梯度調解。這些通道在一個末端具有錐形的壁以產生具有小的傾斜角的液滴產生噴嘴。在該系統中,液滴形成是相對慢的,因為它不依賴于流體流動,而是依賴于這些噴嘴的幾何結構(受限)。盡管256個噴嘴被并行化,但是最大制造速率為約~3.6mL/h。盡管這些方法的一些制造單分散的液滴,但是它們不能充分地引入液滴微流控的優點的全部。平行MFDG乳化器件在所有時候(即在微通道內部)保持對液滴的控制并且保持由單個MFDG系統所給予的其它優點。由于平行系統將若干個MFDG連接在器件中,因此在相鄰的器件之間發生復雜的流體機械耦合。串擾和許多其它因素可使系統失去平衡并且產生多分散的產物。這些變動來源的一些包括:依賴于通道包含的液滴的數量的液壓阻力變動,液滴形成中固有的壓力變動(在液滴夾斷(pinchoff)期間的壓力變化)、通道之間的制作差異、泵送中的不規則性、非均勻的裝載(負載)、氣泡和在特殊通道中俘獲的碎屑等。參見W.Li,J.Greener,D.Voicu和E.Kumacheva,LabChip,2009,9,2715;P.Parthiban和S.A.Khan,Biomicrofluidics,2013,7,044123;P.Parthiban和S.A.Khan,LabChip,2012,12,582-588;C.N.Baroud,F.Gallaire和R.Dangla,LabChip,2010,10,2032-2045;G.Tetradis-Meris,D.Rossetti,C.PulidodeTorres,R.Cao,G.Lian和R.Janes,Ind.Eng.Chem.Res.,2009,48,8881-8889;以及T.Ward,M.Faivre,M.Abkarian和H.A.Stone,Electrophoresis,2005,26,3716-3724,其各自全部通過參考引入。以微流控芯片展示出單分散的O/W乳液(Cv=2.2%)的高容量制造的平行MFDG乳化器件由Nisisako等提出。參見T.Nisisako,T.Ando和T.Hatsuzawa,LabChip,2012,12,3426-3435,其全部通過參考引入。對于在一起工作的144個MFDG的陣列,該系統以180mL/h的最大流動速率制造乳液。所述芯片是在合成二氧化硅玻璃上使用光刻法和深反應離子蝕刻制造的。該制作過程制造僅一個發生器層且需要使用由不銹鋼塊機械加工出的在外部制作的液壓歧管。盡管環形的歧管代表用于使平行MFDG去耦(decouple)的解決方案,但是它限制可擴展性(scalability)的程度。要求N+1個圓柱形塊的組件能夠連接N個共軸的環形的通道,由此將該系統限制到相對低數量的僅對一個發生器層進行進料的環形的通道。而且,該環形的分布網絡被橫向進料且由于管道和各環形的通道之間的非對稱連接,存在跨越器件的流動變動(即存在更接近于接頭的MFDG)。軟光刻法也已被用于使用聚二甲基硅氧烷(PDMS)制作平行MFDG乳化器件。參見X.-H.Ji,N.-G.Zhang,W.Cheng,F.Guo,W.Liu,S.-S.Guo,Z.-K.He和X.-Z.Zhao,J.Mater.Chem.,2011,21,13380-13387,以及M.B.Romanowsky,A.R.Abate,A.Rotem,C.Holtze和D.A.Weitz,LabChip,2012,12,802,其各自全部通過參考引入。該制作技術還要求使用潔凈室設備以產生高長徑比的主模,因此它的成本仍是高的。使用該制作方法,Li等制作了用于以50g/h的制造速率進行聚合物顆粒的UV合成的多模態微流控器件。參見W.Li,J.Greener,D.Voicu和E.Kumacheva,LabChip,2009,9,2715,其全部通過參考引入。在該工作中,16個通道的八個單獨的模塊各自平行地運行。這些模塊是需要大量的外部接頭和管道的獨立的芯片,這限制更高規模的并行化。通常,先前的并行化研究主要努力鉆研僅用于陣列擴展的第二維度。然而,如果期望真的并行化,則也必須研究三維擴展。已以PDMS展示了三維并行化,然而僅展示了三層的堆形式的15個MFDG,且由于它們的制作過程,出于以下原因,按比例增加MFDG的數量是有挑戰性的:堆疊層之間的互連通孔是用打孔器手工制作的(即易于出錯的過程),且橡膠狀材料例如PDMS中的可再現的對準是難以實現的。存在其它類型的處理在過去已被并行化的氣-液微反應器的技術。例如,使用硅展示了在三角形通道中產生氣-液分段流動的多層分布器件。N.deMas,A.Günther,T.Kraus,M.A.Schmidt和K.F.Jensen,Ind.Eng.Chem.Res.,2005,44,8997-9013,其全部通過參考引入。類似地,具有模塊化流動分布58的氣-液系統的制造容量對于以Taylor流動制度運行且產生具有在1.5-4.5μL范圍內的體積的液體段的器件已實現高達9L/h的流動速率。微流控液滴發生器(“MFDG”)可用作具有受控的尺寸和內部組成的單分散的單乳液和混合乳液的制造器件。乳液滴可用作通用模板來設計多種具有一定性質的顆粒。然而,對于在工業中的實際應用,MFDG受其生產能力限制。微流控液滴發生器的典型產量為大約10g/h或小于100kg/年,而工業要求典型地為大約若干噸一年。許多公司一直存在開發可將乳液的總產量增加到工業相關規模的微流控解決方案的興趣。為了具有大規模制造,通過MFDG的平行的數量提高的設計來增加生產能力而不增加液壓泵和專門的設備的數量是重要的。本文中公開具有低至~6%的變異系數的可堆疊的微流控乳液發生器的設計、制作和表征。用于單乳液的大規模制造的多層微流控并行化芯片可包括用于大規模并行化的另一維度和分布網絡在所述芯片內的充分(完全)集成,其可固有地擴展到甚至更高的容量。該器件顯示在文獻中對于具有液-液液滴發生器的同時運行的微流控器件所報道的最高的生產能力。在包含以圓形陣列組織的四個各自具有128個發生器的產生層的器件中可產生分散相的高達1L/h的制造速率。這些特別的器件的分散性的最小值出現在每層120mL/h。這些層可經由通孔互連且用設計的分形分布網絡進行進料。可在聚(甲基丙烯酸甲酯)(PMMA)片材上銑削(mill)出所提出的層并且可將堆熱壓縮結合以產生具有高密度的發生器和集成的分布網絡的多層器件。堆疊多層的效果顯示,與向所述堆添加更多的層相比,制作精度對乳液的分散性具有更大的影響。通過堆疊流體分布層和液滴產生層,多層微流控器件同時運行平行的微流控液滴產生單元。形成堆的不同的層可利用通孔和機械壓縮彼此對準。這些層可通過在基材上雕刻微流控通道而形成。所述器件可包括負責將流體均勻地進料到每個平行的液滴產生單元的集成的分布網絡。構成所述分布網絡的通道可使用分形圖案布置,所述分形圖案繼而可以按稱作瓣的功能性子單元組織。制作過程可在任何高精度CNC銑床中容易地實施且不需要使用潔凈室設備。該過程是低成本的且使得實現多層微流控器件的快速成型(原型制造,prototyping)。該制作方法的另一優點是與彈性體例如PDMS相比,聚(甲基丙烯酸甲酯)(PMMA)的更大的剛性。這些芯片的剛性壁使微通道的液壓容(hydrauliccapacitance)最小化且改善對于流動變化的瞬態響應。該器件可經受高達7.5巴的壓力。還使用金屬銷和通孔精確地實現可再現的對準(<5μm)。在一些實施方式中,分布網絡可充分地集成在所述微流控芯片內。在一些另外的實施方式中,不同的類型的分布網絡可用在并行化器件中;可為呈共軸的環形的構造的樹狀、梯狀、或二者的組合。分形樹狀分布網絡可使耦合最小化。MFDG的組可以按內在地獨立的組(瓣)組織,且相鄰的MFDG在最低的分等級的水平(即MFDG節點)處斷開。對于器件公開在不同的總的流速下向堆添加額外的乳液產生層對液滴尺寸分布的影響。分散性未顯示出與堆中的層的數量(例如1-4個產生層)的增加的直接關聯。然而,由于使兩個相都通過相同的分布網絡和連接的通孔,因此當堆疊更多的層時,對于更大的流動速率,預期歧管阻力的增加。樹狀分布網絡的優點是如下事實:層中的所有單獨的MFDG從流體輸入端起接收相同的壓力降,因此跨越器件,產生條件是均勻的。使用較薄的材料片或較大直徑的通孔可使產生層之間的壓力降的差異最小化。在這些器件中,銑削過程的制作可變性可最大地貢獻于液滴尺寸分布的分散性且更精確的圖案化技術可顯著地改善乳液分散性。集中的樹狀分形分布網絡對于改善液滴產生過程顯示出最好的結果,因為其構造促進兩相的均勻的裝載和沒有氣泡的穩態性能。此外,器件的剩余部分的MFDG的組的去耦通過如下展示:將它們以瓣狀結構布置。當使一個或多個構成瓣失活時,測試具有256個通道和四個瓣的雙層并行化芯片。運行部分(分區,section)的變異系數和液滴尺寸保持當MFDG以相當的流動速率運行時的類似的值。提出顆粒結晶化作為可得益于這些平行的MFDG器件的藥物應用。由通過這些微流控器件產生的乳液,可成功地制造甘氨酸球形附聚物。該實例顯示,通過提供處于升/小時的生產能力(其為最終按比例放大過程中的關鍵要求)的受控制的微流控乳化,所述器件可大大促進例如活性藥物成分(“API”)的方法向工業上相關的制造規模的轉化。該乳液發生器連同高生產能力膜蒸發的直接組合可轉化成工業應用。多層微流控器件可配備MFDG的高容量并行化。參見例如T.Nisisakoetal.,LabonaChip,pp.3426-3435,2012年6月,其全部通過參考引入。然而,Nisisako僅制造了一個層且需要使用在外部制作的分布網絡,這限制可擴展性的程度和MFDG的流動分布,這歸因于管道和各環形的通道之間的非對稱連接。分布網絡可包括在分布層中且通過將所述層彼此連接的通孔雕刻的一組分布通道。使用不同的方法,分布網絡可集成在設計臺(designstage)內部且與芯片整體地制作。另外,可使用薄層(1mm)保持系統緊湊且可在單層上制造分布網絡線路以保持流動跨越盤的均勻分布。分布網絡集成在芯片內部且其中軸對稱輸入端位于盤的中心可產生液相的均勻裝載且可避免在進料線路中俘獲氣泡。通過減少不同的通道中的流動變動,該優點對芯片的穩定性做貢獻。軸對稱輸入端可為從所述器件的表面能到達的。利用該方法,多層微流控器件可包括至少兩個層,其中至少一個層包括剛性聚合物,其中所述兩個層通過通孔連接,其中各層包括分形圖案,和其中各層包括與所述器件的通道連接以控制流體的流動的分布網絡。所述兩個層可為平行的。可設計和制作多層微流控器件用于單分散的單乳液的大規模制造,從而以對于單芯片所報道的最高速率(300mL/h)制造液滴。液滴的尺寸可取決于通道的尺寸、流動速率和液體的性質。例如,使用水和十二烷,可獲得l75μm的平均直徑(Cv=0.12)。在另一實例中,可獲得225μm的平均液滴直徑和(Cv=0.09)。圖1A顯示具有256個通道的微流控芯片(110mm直徑),其包括2個堆疊的各自128個通道的層,以聚(甲基丙烯酸甲酯)(PMMA)制作,其中分布網絡和分布網絡也集成在器件上。圖1B顯示形成用于2種流體的器件的層的實例設計,所述器件具有用于供應的油和水的2個分布網絡以及2個液滴產生層。可使用將分布網絡集成在芯片內的低成本過程配備256個交叉節點(cross-junction)微流控液滴發生器(MFDG)的并行化并且將其布置在兩個層中。該設計和制作方法是靈活的,容許制造具有定制的平均直徑的乳液的系統和比其它方法大的生產能力。所述通道可具有不同的幾何結構,且所述幾何結構可影響液滴形成。寬且薄的(淺的,shallow)長方形的通道橫截面幾何結構(例如,長方形的285×61μm)相對于其它幾何結構(即更窄的長方形的和梯形的幾何結構)是優選的,因為隨著改變水/油流動速率比,它顯示出最低的在液滴尺寸方面的可變性。該趨勢存在于在不同的總的流動速率下進行的研究中,使得薄的長方形的幾何結構最適合用于并行化。在高的總流速(即300μl/分鐘)下,毛細管數較大,該行為比在低的流速(即30μl/分鐘)下更明顯。該行為可歸因于發生器中的側壁的降低的影響。圖2顯示形成用于2種流體的器件的層的實例設計,所述器件具有用于供應的油和水的2個分布網絡以及2個液滴產生層,包括五個層的堆。底部層各自包含128個MFDG,其用通孔連接。油相添加在頂部,而水相從底部輸入。二者都被集中以提供均勻的分布。可引入更多的層以堆疊更大數量的微流控液滴發生器,提供高程度的設計靈活性。系統可具有分形的圖案的任意倍數的量的MFDG。例如,它可具有128、256、512、或1024個MFDG、或128個MFDG的任意倍數。底部層各自可包含128個通道的陣列,其通過通孔互連。在堆疊的MFDG層的頂部上,可覆蓋另外兩層的分形分布網絡(每個相一個)。通過集成這些網絡和連接MFDG的通孔,可配備分布網絡在芯片內的三維并行化和集成。MFDG的實例已被報道。參見例如E.Chanetal.,JAmChernSoc,vol.127,no.40,pp.13854-13861,2005,其全部通過參考引入。當用于制備微流控器件時,材料的實例為聚(甲基丙烯酸甲酯)(PMMA)、環狀烯烴共聚物(COC)、環狀烯烴聚合物(COP)、聚碳酸酯(PC)、聚對苯二甲酸乙二醇酯(PET)、聚二甲基硅氧烷(PDMS)、玻璃或硅。在一些實施方式中,剛性成分可具有對于系統的堆對準、瞬態響應和穩定性的優點。PMMA剛度為大約1.8-3.2GPa,而COC為(2.6-3.2GPa),玻璃為(50-90GPa)且硅為(130-185GPa),因此由它們制成的器件與由其楊氏模量為大約幾百千帕的橡膠狀材料(即PDMS楊氏模量為360-870KPa)制成的器件相比在經歷彈性變形之前可抵抗更大的力/壓力。參見表2。表2.材料和楊氏模量剛性材料楊氏模量聚(甲基丙烯酸甲酯)(PMMA)1.8-3.2GPa環狀烯烴共聚物(COC)2.6-3.2GPa環狀烯烴聚合物(COP)1.7-3.0GPa聚碳酸酯(PC)2.0-2.4GPa聚對苯二甲酸乙二醇酯(PET)2.8-3.1GPa偏離化學計量的硫醇-烯(OSTE)0.25-2.0GPa玻璃50-90GPa硅130-185GPa例如,可使用軟光刻法來制作高生產能力聚二甲基硅氧烷(PDMS)芯片。參見例如M.B.Romanowskyetal.,LabonaChip,vol.12,no.4,p.802,2012;W.Li,etal.,LabonaChip,vol.9,no.18,p.2715,2009,其各自全部通過參考引入。該制作技術要求使用潔凈室設備來產生高的長徑比的主模且因此制作成本增加。與在其中可使用銷和通孔來對準(<5μm)的剛性材料例如PMMA中相比,在橡膠狀材料例如PDMS中的可再現對準可更難以實現。PMMA的較大的剛度還使液壓容最小化且改善瞬態響應。PMMA、COC、玻璃或硅相對于PDMS的另一重要優點是它們對于化學品的低的吸附和吸收以及它們的低的氣體滲透性。可使用PMMA-SU8基材來產生高生產能力微流控器件。參見例如G.Tetradis-Merisetal.,Ind.Eng.Chern.Res.,vol.48,no.19,pp.8881-8889,Oct.2009,其全部通過參考引入。Tetradis-Meris還報道了關于從分布網絡到并行化的器件網絡中的液體分布,梯型布局相對于樹型布置是優選的。出處同上。然而,對于如下的多層微流控器件,該結果是相反的:所述多層微流控器件包括至少兩個層,其中至少一個層包括剛性聚合物,其中所述兩個層通過通孔連接,其中各層包括分形圖案,和其中各層包括與所述器件的通道連接以控制流體的流動的分布網絡。分形圖案包括具有建立于其自身上的特定類型的結構的分形幾何結構。分形圖案可包括若干代的逐漸增加或減小的等級。所述分形圖案的密度隨著各重復水平而增加。多層微流控器件可具有擁有高的密度的分形圖案。所述分形圖案可包括至少128個通道、至少256個通道、至少512個通道、或至少1024個通道。圖3顯示組裝的堆。圖4顯示蓋層或頂部層。該層封閉連續相分布網絡的通道。圖5顯示連續相分布網絡。在該圖中,各通道逐漸地再分成兩個通道;分形的分布網絡具有在中心的單個入口。連續的液體從堆的頂部且從中心進料到盤的邊緣。圖6顯示分散相分布網絡。在該圖中,各通道逐漸地再分成兩個通道;分形的分布網絡具有在中心的單個入口。待分散的液體從堆的底部且從中心進料到盤的邊緣。圖7顯示發生器的第一層、或底部層。該底部層包括128個發生器。通道的寬度從250μm(對于青色交叉物)到2mm(藍灰色)改變。由于通道的尺寸,可裝配128個微流控液滴發生器。利用更窄的通道,可用分布網絡裝配或供應任何可被分形的數量。例如,所述數量可為p×m×2n,其中p為代表瓣的數量的整數,m為代表相同的產生層的數量的整數且n為代表以極陣列布置的分形支化發生器的水平的數量的整數。圖8顯示發生器的第二層。該層可與發生器的第一層相同。該層對于各液滴發生器具有兩個連接通孔(例如:500μm直徑)以將它們與另外的層連通,使分布網絡集成。可多次制作該層以將發生器的數量按比例增加。圖9顯示形成器件的不同的層且描述如何形成堆。底部層為發生器的第一層且堆的頂部為蓋層。堆疊的盤可具有110mm的直徑。所述器件可包括任意兩種將它們自己貢獻于液滴形成的不混溶的流體。一種流體可為“分散相”,即轉變成液滴的流體。例如,水、或水溶液(在水中的甘氨酸)可用作流體。另外的流體可為“連續相”,其為剪切或切割液滴并且運送液滴的相。例如,可使用具有表面活性劑的礦物油或十二烷作為流體。在一個實例中,所述器件可包括水分布層。在另一實例中,所述器件可包括油分布層。所述器件可包括覆蓋層。各層的厚度可小于幾毫米,例如小于1mm。發生器的陣列的堆疊可集成在單個芯片中。三維微流控器件可包括連接乳液產生層的堆的分布網絡。所述分布網絡可包括至少兩個分布層,每一個至少包括流體通道的分形圖案和將它們與其它堆層彼此互連的通孔。所述產生層的數量可為任意整數,優選1-100,優選1-50,優選1-25,且優選1-10。所述產生層可通過微流控液滴發生器的極陣列形成。用于制備乳液的方法包括使用包括至少兩個層的多層微流控器件,其中至少一個層包括剛性聚合物,其中所述兩個層通過通孔連接,其中各層包括分形圖案,和其中各層包括與所述器件的通道連接以控制流體的流動的分布網絡。乳液可為單分散的。乳液的制造速率可為至少300mL/h。瓣組織流動聚焦并行化的MFDG可包括~250μm寬×~100μm深的十字形收縮部(constriction),其與下游的更寬且更深的通道(400μm寬×300μm深)連接(圖18)。先前模擬了寬且薄的長方形的幾何結構(參見D.Conchouso,E.Rawashdeh,D.Castro,A.Arevalo和I.G.Foulds,OptimizedChannelGeometryofaFlow-FocusingDropletGeneratorforParallelization,Rotterdam,2013,其全部通過參考引入)且其證明與具有等效的水力直徑的其它幾何結構相比對流動變化較不敏感,因此使得其適合用于平行系統。MFDG的大規模并行化可包括堆疊方程p×m×2n的層,其中p為代表瓣的數量的整數,m為代表相同的產生層的數量的整數且n為代表以極陣列布置的分形支化發生器的水平的數量的整數。器件可包括一個、兩個、或四個、更多各自包含128個MFDG的產生層。通過使用具有更高的特征分辨率的制作工藝例如光刻法或者通過增加器件的總面積,每層更大數量的MFDG是可能的。使用用于并行化的第三維度帶來相對于二維擴展的重要優點。多層器件的各層可具有依賴于通道的尺寸的任意厚度。所述層可具有為了有效的分布網絡和緊湊的系統設計而采用期望尺寸的通道所需要的最小厚度以用于MFDG的高密度包裝。并行化芯片可由四個基礎層:蓋層、油分布網絡、水分布網絡、和液滴產生層構成。可向堆引入額外的液滴產生層用于MFDG的進一步按比例增加(圖14)。不同的層可全部通過與器件一起制作的通孔彼此連接且容許分布網絡在芯片內的集成。測試了對于分布層的若干設計:樹狀分形分布網絡、環形的分布網絡、和兩者的組合。僅第一種證明是可靠的結構且對于該并行化芯片提供最好的結果。對于圖2和14中描繪的樹狀分形分布網絡,兩種液體的輸入端口都可在芯片的頂部處和底部上軸對稱地放置于堆的中心,以在盤中的所有方向上保持從液體源到MFDG的相同的通道長度。替代地,輸入端口可放置在任意位置處且然后導向中間用于初始分布。兩種液體都從盤的中心流動到邊緣,然后從頂部前進到下部層。如果需要額外的相輸入端,則每個輸入端必須添加兩個額外的層以保持該集中的分布(即一個用于分布且一個從輸入端到盤的中心)。平行MFDG的耦合通過分布網絡發生且發生在系統的輸出端處。設計可包括將MFDG的極陣列以四個組或“瓣”進行組織,所述組或“瓣”可在相同的芯片內作為獨立的液滴產生塊處理,每一個具有其自己的設計的輸出端(圖14)。至關緊要地,這些瓣僅在其中耦合和阻抗是最小的最高水平的層次(鄰近于輸入端口)處彼此連接。由于此,關閉這些部分(瓣)之一對于其它的具有很小影響到沒有影響,且因此對于輸出產量具有很小影響到沒有影響。在圖14中顯示的器件(其中瓣以紅色加亮的盤堆)的情況中,形成2n個MFDG的瓣,各瓣具有32個MFDG/層。圖23顯示具有6個瓣、其中各瓣具有8個發生器的器件。當使用平行系統工作時的主要關注點是堵塞的潛在可能性,尤其是當對付包含樹狀分布網絡的系統時,因為它們被報道對于無規的阻力變化具有較大的敏感性。在所提出的瓣狀結構中,分享公共輸出端的MFDG的組在相同的芯片內充當獨立的單元。如果一個部分變堵塞且其產物突然變成多分散的,則可通過如下將受影響的瓣關閉:關閉其兩個輸入端分支或一個輸入端分支以及輸出端。關閉的瓣的通道阻力變得無窮大且通過調節輸入端壓力以維持每個MDFG的初始流速,其它產物可仍然保持它們的低的分散性和尺寸。具有該類型的瓣結構的平行系統可然后在具有失活的部分的情況下工作并且避免總的制造停止。圖15顯示關閉堵塞的部分的影響,與在所有瓣都起作用的情況下的“256-器件I”的產物相比,當將“256-器件I”的瓣的一個、兩個或三個完全關閉時,測量由“256-器件I”產生的產物的尺寸分布。結果顯示,通過調節到正確的壓力,可保持類似的液滴尺寸和分散性,這證明瓣結構的優點。作為具有弱的相互影響的獨立的功能單元,瓣可被失活和再活化,如果提供恰當的閥的話。還可實施單獨的傳感器以監控瓣運行。使用單獨的傳感器使得實現這樣的系統:其中,可關閉器件的部分(或瓣)的一些之一,同時保持其它部分(或瓣)工作,伴隨著很小的變化到沒有變化。用于檢測堵塞的瓣(部分)的可能的方法的一些可為監控器件中所有的瓣的輸入端或輸出端以查看它們是否全都沒有變化地運行。可幫助檢測最終產物中的變化且可用作用于關閉瓣的反饋系統的傳感器可包括RF結構、電容傳感器、圖像處理(光學檢查)、阻抗測量、流動傳感器、pH傳感器、光散射傳感器(例如激光器)、界面傳感器、和粘度傳感器。預期在具有不同數量的產生層的器件中看到該行為且該行為不依賴于每層的瓣的數量。值得注意的是,這些瓣僅在其中耦合和阻抗是最小的最高水平的層次(鄰近于輸入端口)處彼此連接。由于此,關閉這些瓣之一對于其它瓣具有很小影響到沒有影響,且因此對于生產量具有很小影響到沒有影響。后液滴產生處理通過兩個不混溶的相的剪切力進行的乳液的間歇處理已在工業中使用了長的時間。然而,微流控系統相對于其間歇制造對應物提供優點。例如,微流控學方法可控制試劑的精確的量、混合速率、停留時間、環境條件和這些乳液以單液滴的粒度的后處理。這些方法中的一些已被討論。參見例如G.T.Vladisavljevicetal.,Industriallab-on-a-chip:Design,applicationsandscale-upfordrugdiscoveryanddelivery,AdvancedDrugDeliveryReviews,Jul.2013;C.Holtze,J.Phys.D:Appl.Phys.,vol.46,no.11,p.114008,Feb.2013;C.X.Zhao,Multiphaseflowmicrofluidicsfortheproductionofsingleormultipleemulsionsfordrugdelivery,AdvancedDrugDeliveryReviews,2013;Tetradis-Mairisetal.MethodandapparatusforproducingmicroparticlesWO2010025988A1;Nisisakoetal.Apparatusforproducingmicroliquiddrops,EP2594332A1;Kumachevaetal.Multiplecontinuousmicrofluidicreactorsforthescaledupsynthesisofgelorpolymerparticles,WO2008148200A1;MarkBRomanowskyetal.Scale-upofmicrofluidicdevices,WO2010104597A2,其各自全部通過參考引入。微流控系統可包括通過封閉的彎曲表面例如管、漏斗或圓柱體實施的后液滴產生處理步驟,用于任何種類的顆粒的高容量的連續制造。所述后處理步驟可為可修改液滴的結構和組成的任何過程。例如,該步驟可包括用于加快材料的合成的加熱機構、用于使UV敏感性顆粒或其它材料聚合的UV暴露區、等離子體處理、通過不同的氣體氣氛例如反應性氣體、放電、冷凍、或者可將液滴轉變成顆粒的任何其它處理。所述后處理步驟可包括形成乳液的連續的流,其可在管或漏斗的封閉的彎曲表面的玻璃壁上滑下(圖16、17、21、和22)。圖16顯示用于微流控液滴發生器的大規模并行化的實驗裝置。所述發生器的四個輸出端可排列在玻璃漏斗或管周圍并且它們的通過物料(throughput)在管或漏斗的壁上滑動且潤濕柱的橫截面的整個周邊。漏斗或管可用作用于后處理步驟例如加熱步驟的延長的直徑(橫斷面,diameter)。圖21顯示用于在開放的圓形表面中的后處理的實驗裝置。圖17顯示用于微流控液滴發生器的大規模并行化的實驗裝置。所述發生器的四個輸出端可排列在玻璃漏斗或管周圍并且它們的通過物料在管或漏斗的壁上滑動且潤濕柱的整個周邊。漏斗或管可用作用于后處理步驟例如UV暴露的延長的直徑。圖22顯示用于在開放的圓形表面中的UV后處理的實驗裝置。用于制備乳液的方法可包括將流體從混合器供應到顆粒固定區或處理區,其具有彎曲表面使得所述流體形成沒有側面邊緣的層。用于供應流體的方法可包括加熱沒有邊緣的流體的層。所述區可包括具有彎曲表面的管,其中從輸出端供應的液體通過管,接觸彎曲表面的壁,且可潤濕彎曲表面的整個周邊。可將顆粒固定區或處理區暴露于紫外光或加熱。用于制備乳液的方法可包括將流體從混合器供應到具有彎曲表面的處理區,使得所述流體形成沒有側面邊緣的層。用于處理乳液的系統可包括管和至少一個將乳液供應通過所述管的輸出端。所述系統可包括至少一個供應流體的輸出端;所述系統可包括至少四個供應流體的輸出端。輸出端可包括排列在封閉的彎曲表面周圍的多個輸出端。所述流體可潤濕所述管的整個周邊。所述系統可連接到多層微流控器件。所述系統可加熱沒有邊緣的流體的層。所述后處理步驟可為對于將藥物微晶的微流控制造按比例放大到工業相關規模的主要步驟。器件和系統的優點對于這樣的多層微流控器件,存在優點:所述多層微流控器件包括至少兩個層,其中至少一個層包括剛性材料,其中兩個層通過通孔連接,其中各層包括分形圖案,和其中各層包括與器件的通道連接以控制流體的流動的分布網絡。所述剛性材料可包括聚合物、玻璃、或硅。該器件的優點包括:它可以剛性材料(PMMA)制造。這對制作過程中MDG的適當排列做貢獻且促進器件的堆疊。它還降低由于當施加壓力變化時器件的低的變形所致的液壓容,通過這樣做,它可顯示出更好的且更快的瞬態響應。也可使用玻璃和/或硅或任何聚合物基材。PMMA、COC、COP、PT、PC、玻璃和/或硅相對于PDMS的另一重要優點是它們對化學品的低的吸附和吸收以及它們的低的氣體滲透性。另外,液相的軸對稱輸入端可被集中且可從盤的頂部和底部表面到達,提供流體到液滴發生器的單獨的堆的均勻且直接的分布。這導致液體的清潔的且快速的裝載且避免俘獲不期望的氣泡。所述系統可將分布網絡充分地集成在微流控芯片內,因此它只需要兩個用于以上討論的不同的相的入口。與之前提供的任何其它設計相比,這提供在設計方面的更大的靈活性和用于大規模堆疊的3D集成。該器件和系統可向256個通道的器件提供在文獻中報道的單器件的最大的生產能力(分散相的流動速率FRdp≌300ml/h)。通過在額外的堆疊層中添加更多的微流控液滴發生器陣列,生產能力可進一步改善。增加數量的輸出端(4個或更多個)容許控制單分散的乳液的物流并且引導它們形成薄的乳液層,所述薄的乳液層在大直徑的漏斗或管之上滑動以應付高級制造和后處理步驟。后處理步驟包括加熱、暴露于紫外光等。實施例制作過程由1mm厚的流延PMMA片即在微流控學中通常使用的便宜材料制成多層并行化芯片。本文中提供的計算機數字控制(CNC)微細銑削和熱壓粘合構成用于三維微流控器件的快速成型的制作方法。微流控通道的直接微細銑削工藝可在任何高精度CNC機床中容易地實施且不需要潔凈室設備。而且,已使用范圍從熱壓粘合、微波粘合、低溫超聲粘合、和通過表面改性的若干種成功的方法展示了便宜的PMMA粘合。參見X.Zhu,G.Liu,Y.Guo和Y.Tian,Microsyst.Technol.,2006,13,403-407;Y.Sun,Y.C.Kwok和N.-T.Nguyen,J.Micromech.Microeng.,2006,16,1681-1688;M.Rahbar,S.Chhina,D.Sameoto和M.Parameswaran,J.Micromech.Microeng.,2009,20,015026;R.J.Holmes,C.McDonagh,J.McLaughlin,S.Mohr,N.J.Goddard和P.R.Fielden,J.Phys.Chem.Solids,2011,72,626-629;S.W.Li,J.H.Xu,Y.J.Wang,Y.C.Lu和G.S.Luo,J.Micromech.Microeng.,2009,19,015035;以及L.Brown,T.Koerner,J.H.Horton和R.D.Oleschuk,LabChip,2006,6,66,其各自全部通過參考引入。MFDG可包括100μm深的十字形收縮部,其與下游的更寬和更深的通道連接。圖18顯示使用用于制造快速的原型的標準PCB銑床在PMMA上切削的微流控通道的SEM照片。所述十字形收縮部為1000μm長×260μm寬×100μm深。進料管線和輸出端為400μm寬×300μm深。可在1mm厚的流延PMMA片上使用LPKFProtoMat-S103PCB繪圖機直接機加工芯片。LPKF系統具有±0.5μm的x-y分辨率且裝備有深度限定器,取決于基材平面度,所述深度限定器將跨越芯片的深度變動降低到低于±10μm。還對堆疊層之間的所有互連進行CNC鉆孔作為同一工藝的部分。使用AmbiosXP-200臺階儀測量通道的表面粗糙度且在十字形的收縮部處的表面粗糙度為~140nm且在分布通道處的表面粗糙度為~350nm,其與所測量的器件制作誤差(表3)相比是可忽略的。表3.測試其各自的制作可變性的器件一旦發生器和分布層被銑削,便可然后將層的堆用肥皂水涂刷、清洗和用銷對準用于粘合。為了保證沒有從銑削工藝留下的殘余物阻塞任何通道,目視檢查是必要的。然后將所述層的堆使用對準銷組裝(以進行≤5μm的精確對準)并且使用裝配有環境艙的Instron5900-Series熱壓粘合。然后將所述層的堆使用提供有環境艙的Instron5900-Series在150℃下在壓縮應力(12N/cm2)下熱粘合45分鐘。然后使溫度逐漸降低到低于50℃,同時保持壓縮應力恒定另外的15分鐘。最后,在并行化盤上粘貼世界到芯片(worldtochip)接口(界面,interface)和管道。芯片到世界(chip-to-world)連接機構可包括在頂部層和底部層中。盡管在粘合之后在微通道中不存在明顯的變形,但是應注意,蓋層可被擠入通道5-10μm。因此,非常薄且寬的通道可通過該粘合過程阻塞。然而,粘合強度被測試為經得住高的壓力(~7.5巴),充分高于在器件的裝載順序中通常使用的壓力,以消除俘獲的氣泡。該過程是低成本的且提供以精確的對準在第三維度中并行化的能力。材料為了成像和液滴表征,使用具有2%(重量/重量)的由70%Span-20和30%Span-80(重量/重量)組成的表面活性劑混合物的癸烷(≥99%)作為連續相(CP)。分散相(DP)為具有紅色食物色彩的UltrapureMilliporeMilli-Q去離子水(18.3MΩ)的溶液,所述紅色食物色彩被添加以增強對比和促進通過圖像處理軟件對單乳液的表征。參見A.S.Basu,LabChip,2013,13,1892-1901,其全部通過參考引入。顆粒結晶化也使用具有以上描述的相同的表面活性劑含量的十二烷(≥99%)作為CP且使用在室溫(22℃)下飽和的甘氨酸(>99%)溶液作為DP實現。該溶液為大約24.4g的甘氨酸含量/100g的去離子水。參見K.Allen,R.J.Davey,E.Ferrari,C.Towler,G.J.Tiddy,M.O.Jones和R.G.Pritchard,Cryst.GrowthDes.,2002,2,523-527,其全部通過參考引入。所有溶液都在各實驗之前使用Cole-Parmer注射器過濾器(0.45μm)進行過濾。實驗裝置實驗裝置的示意圖提供于圖13中。將CP和DP兩者都裝載到獨立的容器中,然后連接到ElveflowOB1壓力泵以將流體儲蓄器中的壓力控制在0-2000毫巴的范圍內。使用連接到OB1的流量傳感器監控流動速率。為了進行實驗,將并行化芯片放置在玻璃漏斗上面,所述玻璃漏斗幫助將輸出流引導到白色塑料表面用于成像。該表面作為良好的光擴散體工作以促進均勻的照明條件。使用具有流量傳感器的ElveflowOB1壓力泵將流體儲蓄器中的壓力控制在0.03-0.7巴的范圍內以填充系統且然后將所述系統帶到穩態制造。為了實現高生產能力的油包水乳液,連續相為具有2%的由70%Span20和30%Span80構成的表面活性劑的>99%的十二烷的溶液且水相溶液為染色的水之一以及負載了甘氨酸的水之一。對油包染色的水乳液進行成像,如圖19中所示,以研究所述乳液的分散性。使用DMV軟件研究所述乳液的分散性。參見例如A.S.Basu,"DropletMorphometryandVelocimetry(DMV):Avideoprocessingsoftwarefortime-resolved,label-freetrackingofdropletparameters,"LabonaChip,2013,其全部通過參考引入。圖19顯示油包染色的水乳液的實例用于容易的可視化。使用具有MPG65mm微鏡頭的Canon5D照相機對產物進行成像。在測試期間,對于各數據點拍攝平均100張高品質照片(21Mpx)。然后將這些照片轉變成AVI視頻文件并且通過液滴形態測量學和測速軟件(DMV)進行處理。典型地,由~8000個液滴的樣品獲得實驗的有效液滴直徑分布,所述~8000個液滴的樣品對于非常大的種群代表在統計學上顯著的樣品。裝載順序和分布網絡構造均勻的液體裝載在MFDG的并行化中起到最關鍵的作用之一。裝載問題可包括:在非對稱分布網絡中跨越芯片的壓力梯度、改變流量的俘獲的氣泡、相之一到另外的相中的回流、依賴于流動著的液體的通道阻力的變化、堵塞的通道、和許多其它的。參見G.T.N.Khalid,M.A.Neves,T.Kuroiwa,M.Nakajima,K.Uemura,S.IchikawaandI.Kobayashi,Adv.DrugDeliveryRev.,2013,65,1626-1663,andC.Holtze,J.Phys.D:Appl.Phys.,2013,46,114008,其各自全部通過參考引入。為了使這些問題最小化,對于該高生產能力微流控芯片測試三種不同的構造:共軸的環形的網絡、與樹狀網絡組合的環形的網絡、和分形樹狀分布網絡(圖20)。所有網絡構造都是使用類似的裝載條件測試的。首先,將油相和水相以高的壓力(例如~1000毫巴)推動以清除所有俘獲的氣泡和確保對所有微流控通道的完全裝載。然后,施加逐漸降低的斜線下降(ramp)(-65毫巴/s)并且將壓力平穩地降低到50毫巴。在照相機和流量傳感器的幫助下通過小的壓力變化(1毫巴)完成最后的適當的調整。由于PMMA的透明性,液滴形成的光學檢查是可能的,并且容許我們檢測系統中的可能的問題。如果注意到不規則性,則以短的脈沖施加高壓力(1-2巴)的清潔循環以清除障礙物。與PDMS和另外的彈性材料相比使用PMMA的優點是它的較大的剛度(楊氏模量2.4-3.3GPa),其對具有良好的動態響應和低的液壓容的微流控通道做貢獻。可對ElveflowOB1壓力泵進行編程以自動地進行整個順序,包括經常需要1-3次的清潔循環。在所有測試的構造中一貫地出現的問題是在MFDG中無規地俘獲氣泡。在環形的構造的情況下,該問題甚至在若干次高壓力清潔循環之后也繼續存在,導致不規則的進料和多分散的液滴產生。相反,分形樹狀網絡工作得最好以通過突然的壓力變化清潔通道且由于軸對稱輸入端而顯示出流體的均勻裝載。該分布網絡顯示出將MFDG布置成瓣的最好結果,其使得實現關閉芯片的部分而不影響產物,而且其裝載響應對芯片的穩定性做貢獻且改善產物的分散性。在不同流動條件下的液滴產生進行第一組實驗以表征所產生的液滴的尺寸和尺寸分布。對于該部分,使用具有食物色彩的去離子水作為DP。對于包含不同數量的產生層的器件,拍攝所產生的乳液的圖像,然后對其進行處理。在保持水/油流動速率比常數1:5的同時,將具有一個(128個MFDG)、兩個(256個MFDG)和四個(512個MFDG)產生層的器件在不同的總的流速下進行測試(圖12)。對于以固定的總的流動速率和不同的水/油比(1:2、1:5、1:10)運行的具有128和256個MFDG的器件完成的實驗未顯示出對乳液的尺寸分布的任何顯著影響。對于單層,最大生產能力為~300ml/h,對于雙層,最大生產能力為~600ml/h,且對于四重層,應預期~1.2L/h的產量。流量傳感器能夠精確地測量最高達~1L/h。誤差棒顯示對于~8000個液滴的平均樣品尺寸的乳液的標準偏差(圖12A)。在所測試的所有器件中,變異系數(圖12B)顯示類似的U形曲線。在不同的器件之中,雙層器件“256-器件I”顯示出最小的變異系數(Cv=0.06)。該器件還具有最小的在制作中的標準偏差,這表明在制造可變性和尺寸分布可變性之間的密切關系。在較高數量的產生層下,通過器件的總的流量增加,且因此跨越分布網絡的壓力降也增加。由于此,需要較高的壓力來驅動器件。然而,這看起來對液滴制造不具有影響。由于分散性的變化看起來由制作可變性支配,因此在變異系數和產生層的數量之間未發現直接關聯。具有1個、2個和4個層的器件的最大運行壓力分別為83、203、和500毫巴。甚至對于高的層計數的器件,驅動壓力的該增加也不增加對于分層的擔憂。例如,通過從壓力測量值進行外推,10層的器件將需要~1.8巴。該估值仍充分低于器件可經得住而沒有分層的7.5巴的最大測試壓力。使用兩個各自具有128個MFDG的器件來研究制作可變性是如何影響產物的分散性的(表3)。“128-器件I”與“128-器件II”(σfab=7.9%)相比具有4.8%的低的制作標準偏差。兩個器件都顯示出類似的表征曲線;然而,由第二種器件產生的變異系數在各點處增加并且與制作變動變化一致(圖12B)。將預期由于制作公差所致的在產物的分散性方面的變化。對于平行器件的按比例放大的情況,已討論了該問題,因為具有方形橫截面的通道中的流體阻力與通道尺寸的四次方成比例。參見G.Tetradis-Meris,D.Rossetti,C.PulidodeTorres,R.Cao,G.Lian和R.Janes,Ind.Eng.Chem.Res.,2009,48,8881-8889,以及H.Bruus,TheoreticalMicrofluidics,OxfordUniversityPress,2007,vol.18,其各自全部通過參考引入。MFDG的通過瓣的去耦當用平行系統進行工作時的主要關注點是堵塞的潛在可能性,尤其是當對付包含樹狀分布網絡的系統時,因為它們被報道對于無規的阻力變化具有較大的敏感性。參見G.Tetradis-Meris,D.Rossetti,C.PulidodeTorres,R.Cao,G.Lian和R.Janes,Ind.Eng.Chem.Res.,2009,48,8881-8889,其全部通過參考引入。在所提出的瓣狀結構中,分享公共輸出端的MFDG的組在相同的芯片內充當獨立的單元。如果一個部分變堵塞且其產物突然變成多分散的,則可通過如下將受影響的瓣關閉:關閉其兩個輸入端分支或者一個輸入端分支以及輸出端。關閉的瓣的通道阻力變得無窮大且通過調節輸入端壓力以維持每個MDFG的初始流速,其它產物可仍然保持它們的低的分散性和尺寸。具有該類型的瓣結構的平行系統可然后在具有失活的部分的情況下工作并且避免總的制造停止。為了研究關閉堵塞的部分的影響,與在所有瓣都起作用的情況下的“256-器件I”的產物相比,當將“256-器件I”的瓣的一個、兩個或三個完全關閉時,測量由“256-器件I”產生的產物的尺寸分布。圖15顯示該比較且表4總結所述實驗以及在關閉輸出端之后保持每個工作的MFDG的類似的流動速率所需要的壓力方面的調節。液滴尺寸的誤差是由于作為壓力調節以及在整個實驗中需要的停止和再裝載步驟的結果的在流動速率方面的小的變動。表4.對于“256器件I”在不同的工作容量下的實驗的總結(%)PoPwFRo(mL/h)FRw(m/h)FRo/FRw液滴尺寸(μm)100731415563384.6199.9775601311312304.9190.585050137951724.6192.62253712403844.8186.99該研究證明,瓣是具有弱的相互影響的獨立的功能單元且它們可被失活和再活化,如果提供恰當的閥的話。預期在具有不同數量的產生層的器件中看到該行為且該行為不依賴于每層的瓣的數量。值得注意的是,這些瓣僅在其中耦合和阻抗是最小的最高水平的層次(鄰近于輸入端口)處彼此連接。由于此,關閉這些瓣之一對于其它瓣具有很小影響到沒有影響,且因此對于生產量具有很小影響到沒有影響。球形藥物晶體附聚物的制造可使用微流控器件制造藥物微晶。將負載了甘氨酸的乳液在加熱的玻璃蓋玻片上蒸發以產生球形晶體附聚物(圖19),其為活性藥物微晶的模型(典型)。球形附聚物形式的活性藥物成分(“API”)的結晶化和配制對于連續的和可持續的藥物制造是關鍵步驟且在近年來已在科學和工業上被大量地關注。參見例如A.I.Toldyetal.,SphericalCrystallizationofGlycinefromMonodisperseMicrofluidicEmulsions,Cryst.GrowthDes.,2012,12(8),3977-3982;R.A.Leon,W.Y.Wan,A.Z.M.Badruddoza,T.A.Hatton和S.A.Khan,Cryst.GrowthDes.,2013,14,140–146;以及A.Z.MdBadruddoza,A.I.Toldy,T.A.HattonandS.A.Khan,Cryst.GrowthDes.,2013,13,2455–2461,其各自全部通過參考引入。微流控乳液產生與快速的基于薄膜的蒸發結晶化的結合是用于經設計的藥物配制物的精確制造的有前景的路線。通過提供處于升/小時的生產能力(其為最終按比例放大過程中的關鍵要求)的受控制的微流控乳化,所公開的系統大大地促進這樣的方法向工業上相關的生產規模的轉化。圖19A顯示在藥物工業中作為參考模型使用的甘氨酸球形晶體附聚物的SEM照片。液滴在結晶化過程期間收縮。可通過使用該系統展示甘氨酸晶體附聚物的形成。甘氨酸(>99%)是可從乳液結晶化的氨基酸的實例且通常在藥物結晶化中用作模型分子。使用“128-器件I”產生具有150μm的有效直徑的負載了甘氨酸的乳液。然后,將~100μL的樣品從乳液發生器的輸出端引導至加熱的顯微鏡玻璃載玻片(Corning75×50mm)上以形成具有~0.2到0.4mm的估計厚度的甘氨酸的薄膜。將顯微鏡載玻片放置于TorreyPinesScientificEchoThermTMHS65熱板上面并且將設定到90℃的溫度以制造甘氨酸晶體附聚物(圖19)。結晶化順序細節提供在A.I.Toldy,A.Z.M.Badruddoza,L.Zheng,T.A.Hatton,R.Gunawan,R.Rajagopalan和S.A.Khan,Cryst.GrowthDes.,2012,12,3977-3982中,其全部通過參考引入。簡要地說,它由四個步驟組成,所述四個步驟通過由加熱的基材遞送到負載了甘氨酸的液滴的外部熱引發。首先,液滴直徑迅速收縮到大約50%,然后產生局部的成核,隨后是從核到液滴邊界的快速的輻射狀生長,且最后是球形附聚物的陳化(圖19B)。使用如下兩種方法對所述球形晶體附聚物進行表征:光學顯微鏡和使用Quanta3DFeg系統的掃描電子顯微鏡。該方法容許單分散的甘氨酸晶體附聚物的制造且提供用于控制快速的晶體生長的優異方法,因為晶體形成被限制在液滴內。其它實施方式在所附權利要求的范圍內。當前第1頁1 2 3