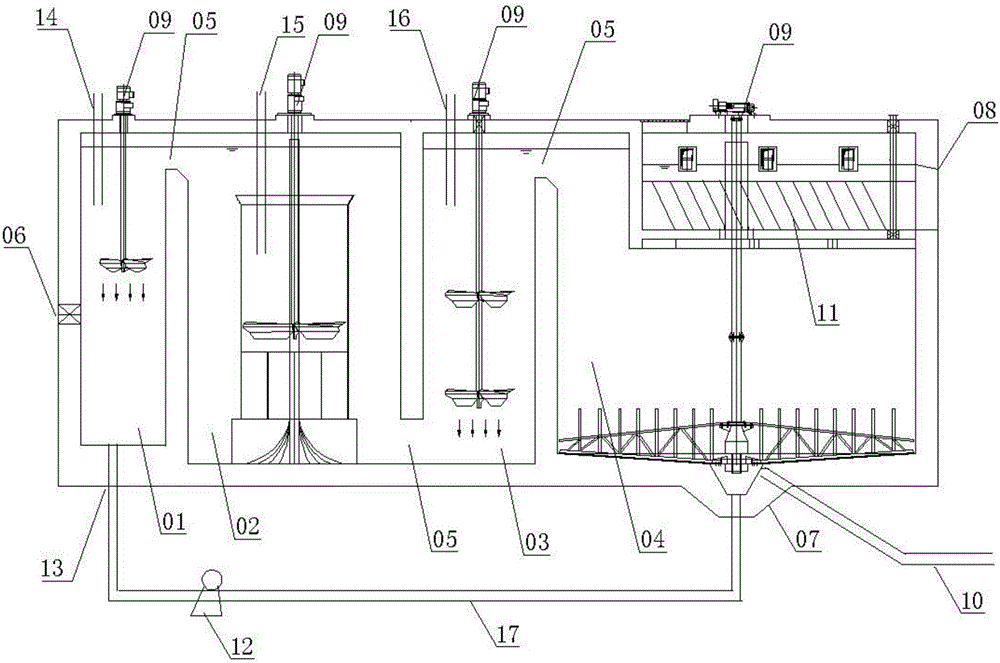
本發明涉及污水處理
技術領域:
,具體是涉及一種多腔式一體化濃水處理反應器。
背景技術:
:隨著膜工藝的廣泛應用與發展,反滲透技術逐漸成為石化、電力、冶金、制藥等諸多行業污水處理及循環水深度回用處理的首選技術。然而,一般反滲透工藝的實際產水量不足75%,同時會產生約25%左右的反滲透濃水,濃水中通常含有較高濃度的有機物、無機物、氨氮類物質,溶液色度大、含鹽量高、可生化性差,因此反滲透濃水一直是較難處理的工業廢水之一。目前,國內外對反滲透濃水處理的方法主要有以下幾種:(1)回流法:RO濃水回流可提高回收率,增大膜表面沖洗流速,減少污堵;(2)回用作生產用水:由于RO濃水中無懸浮物,含阻垢劑且有壓力,可用作過濾系統的反沖洗水、除塵水、沖灰沖渣水、冷卻水;或經過簡單處理后混入原水回收;(3)資源化利用:可采用水力渦輪增壓器、功交換器和壓力交換器等利用余壓產能;海水淡化廠的濃水用于制鹽,可節約鹽田,縮短曬鹽周期;預處理后適當勾兌,可用于海產品養殖;(4)蒸餾濃縮:膜蒸餾技術是一項新技術,在常壓下利用溫差可將濃水盡可能地回收(回收率>95%)甚至結晶化;(5)直接或間接排放。然而上述方法均存在一定局限性:(1)回流法雖可提高回收率,但僅為再次濃縮,其產生的濃水污染物會更高;(2)回用作生產用水或者資源利用,因受制于排放需求,不適于全面推廣;(3)蒸餾濃縮,其成本較高,且目前經濟、高質量的疏水微孔膜尚未研發成熟;(4)直接排放會對土壤、地表水、海洋等產生污染;若排入市政污水反應系統,過高的總溶解性固體對活性污泥的生長也非常不利。技術實現要素:為了解決以上問題,本發明提供以下技術方案:一種多腔式一體化濃水處理反應器,包括:活性炭吸附腔、混凝反應腔、絮凝反應腔和泥水分離腔,所述活性炭吸附腔、混凝反應腔、絮凝反應腔和泥水分離腔集成到一體化反應器中,且所述活性炭吸附腔、所述混凝反應腔、所述絮凝反應腔和所述泥水分離腔依次通過通道相互連通,使濃水能通過通道依次進入活性炭吸附腔、混凝反應腔、絮凝反應腔和泥水分離腔中進行處理;所述活性炭吸附腔包括活性炭進料器,所述混凝反應腔包括混凝劑進料器,所述絮凝反應腔包括絮凝劑進料器;所述反應器還包括濃水進口、凈水出口和污泥出口,所述濃水進口與所述活性炭吸附腔連通;所述凈水出口、污泥出口與所述泥水分離腔連通;所述活性炭吸附腔、混凝反應腔、絮凝反應腔、泥水分離器中均設有攪拌器。進一步地,所述凈水出口外連接有凈水管路,用于將澄清水排出,所述污泥出口連接有污泥管路,用于將污泥絮體排出。進一步地,所述泥水分離腔內部設置有斜板或斜管。進一步地,所述泥水分離腔內設有泥位探測儀。進一步地,所述反應器還包括連接所述泥水分離腔與所述活性炭吸附腔的回流管路。有益效果:(1)本發明通過多腔式設計使多個步驟所需的濃水處理裝置集成到一個一體化反應器中,設備整體性好,使用方便,同時減少占地面積。(2)通過首先利用活性炭吸附反應沉淀,然后進行混凝絮凝的工藝,有效去除了反滲透濃水中的有機污染物、氨氮以及總磷,得到達到一級排放標準的澄清水;(3)通過將泥水分離腔中的活性炭回流到活性炭吸附腔中,既提高了藥劑的利用率,同時又降低了污泥產量;(4)通過安裝泥位探測儀,根據泥位探測情況量化污泥回流量與排出量,在提高了藥劑的利用率,降低污泥產量的同時,又保證了后續反滲透濃水的處理效果。附圖說明圖1為本發明第一種實施方式所述多腔式一體化濃水處理反應器的結構示意圖;圖2為本發明第二種實施方式所述多腔式一體化濃水處理反應器的結構示意圖。具體實施方式下面結合具體實施方式和實施例對本發明做進一步說明,但本發明并不限于以下具體實施方式和實施例。如圖1所示,本發明的第一種實施方式提供了一種多腔式一體化濃水處理反應器,包括:活性炭吸附腔01、混凝反應腔02、絮凝反應腔03和泥水分離腔04;所述活性炭吸附腔01、混凝反應腔02、絮凝反應腔03和泥水分離腔04集成到一個一體化反應器中,且所述活性炭吸附腔01、所述混凝反應腔02、所述絮凝反應腔03和所述泥水分離腔04依次通過通道05相互連通,使濃水能通過通道05依次進入活性炭吸附腔01、混凝反應腔02、絮凝反應腔03和泥水分離腔04中進行處理;所述活性炭吸附腔包括活性炭進料器14,所述混凝反應腔包括混凝劑進料器15,所述絮凝反應腔包括絮凝劑進料器16;所述反應器還包括濃水進口06、凈水出口08和污泥出口07,所述濃水進口06與所述活性炭吸附腔01連通;所述凈水出口08、污泥出口07與所述泥水分離腔04連通;所述活性炭吸附腔01、混凝反應腔02、絮凝反應腔03中均設有攪拌器09,使濃水與活性炭、混凝劑、絮凝劑更充分的接觸,同時使反應后的混合液處于流動狀態,便于輸送。所述凈水出口08外連接有凈水管路(圖中未示出),用于將澄清水排出,所述污泥出口07連接有污泥管路10,用于將污泥絮體排出。可選擇地,如圖1所示,所述活性炭吸附腔01、所述混凝反應腔02之間的通道05位于其上部,混凝反應腔02、絮凝反應腔03之間的通道05位于其底部,絮凝反應腔03和泥水分離腔04之間的通道05位于其上部。可選擇地,所述混凝反應腔02和絮凝反應腔03還可連接有加藥裝置(圖中未示出),加藥裝置可選用本領域通用的藥劑添加裝置,用于加入具有沉淀、澄清、分離效果的水處理藥劑,包括但不限于絮凝劑、混凝劑、助凝劑等水處理藥劑。反滲透濃水在未加水處理藥劑,例如混凝劑及絮凝劑之前,水中的膠體和細小懸浮顆粒的本身質量很輕,受水的分子熱運動的碰撞而做無規則的布朗運動。顆粒都帶有同性電荷,它們之間的靜電斥力阻止微粒間彼此接近而聚合成較大的顆粒;而在水中依次加入混凝劑及絮凝劑后,與懸浮物的膠體及分散顆粒發生電中和,形成絮粒沉降,且在沉降過程中它們互相碰撞凝聚,其尺寸和質量不斷變大,沉速不斷增加。絮凝體具有強大吸附力,不僅能吸附懸浮物,還能吸附部分細菌和溶解性物質。優選地,根據淺池理論的原理,所述泥水分離腔04內部可設置有斜板或斜管,在圖1提供的示意性實施例中,為斜管11,在泥水分離腔04有效容積一定的情況下,增加了沉淀面積,可使污泥去除率高;進入泥水分離腔的混合液自下向上流動,穿過斜管或斜板,澄清水在泥水分離腔04的頂部用穿孔集水管或溢流堰收集;污泥則在泥水分離腔04的底部用穿孔排泥管收集,通過污泥出口07排出。利用上述反應器進行反滲透濃水處理的方法,包括以下步驟:(1)活性炭吸附處理:待處理的反滲透濃水首先由濃水進口06進入活性炭吸附腔01,在攪拌器09的快速混合攪拌下,通過活性炭進料器14向活性炭吸附腔中加入活性炭吸附劑,使活性炭與待處理濃水充分接觸發生吸附反應沉淀,以除去大部分機污染物和氨氮,降低濃水的COD值和氨氮含量,其中,本領域技術人員可以根據本發明來選擇適當的活性炭,例如活性炭的目數可以為50-300,優選地,所述活性炭為粉末活性炭,粉末活性炭的接觸面積大,吸附能力更強,效果更顯著;活性炭的投加量可以根據水中污染物的含量等實際情況進行選擇,例如可以為450-500mg/L。(2)混凝處理:經活性炭吸附處理后,吸附腔中的混合液,即吸附反應產生的沉淀物和濃水,由通道05進入混凝反應腔02中,通過混凝劑進料器15向混凝反應腔02中投加混凝劑,與活性炭及濃水中的污染物發生混凝沉淀反應,形成絮體,同時除去總磷,降低總磷含量;其中,混凝劑的類型和濃度可以根據實際需要進行選擇,例如可以為聚合氯化鋁、三氯化鐵、聚合氯化鐵、硫酸鋁、硫酸亞鐵、硫酸鋁鉀(明礬)、鋁酸鈉或硫酸鐵等,混凝劑的濃度可以為15-20mg/L;(3)絮凝處理:經混凝劑處理后,混凝反應腔02中的混合液由通道05進入絮凝反應腔03中,通過絮凝進料器16向絮凝反應腔03中投加絮凝劑進行絮凝反應,使絮體不斷增大,以便于泥水分離,并進一步降低濃水中COD值以及總磷、氨氮的含量;其中,絮凝劑的類型和濃度可以根據實際需要進行選擇,例如可以為聚丙烯酸、聚丙烯酸鈉、聚丙烯酸鈣或聚丙烯酰胺等,絮凝劑的濃度可以為0.5-1mg/L;(4)泥水分離處理:經絮凝處理后的混合液由通道05進入泥水分離腔04進行污泥和澄清水的分離,分離出的污泥通過污泥管路10外排,澄清水通過凈水管路外排;如圖2所示,本發明的第二種實施方式提供了一種多腔式一體化濃水處理反應器,包括:活性炭吸附腔01、混凝反應腔02、絮凝反應腔03和泥水分離腔04;所述活性炭吸附腔01、混凝反應腔02、絮凝反應腔03和泥水分離腔04集成到一個一體化反應器中,且所述活性炭吸附腔01、所述混凝反應腔02、所述絮凝反應腔03和所述泥水分離腔04依次通過通道05相互連通,使濃水能通過通道05依次進入活性炭吸附腔01、混凝反應腔02、絮凝反應腔03和泥水分離腔04中進行處理;所述活性炭吸附腔包括活性炭進料器14,所述混凝反應腔包括混凝劑進料器15,所述絮凝反應腔包括絮凝劑進料器16;所述反應器還包括濃水進口06、凈水出口08、污泥進口13和污泥出口07,所述濃水進口06、污泥進口13與所述活性炭吸附腔01連通;所述凈水出口08、污泥出口07與所述泥水分離腔04連通;所述凈水出口08外接有凈水管路,所述污泥出口07外接有污泥管路10和回流管路17,所述污泥出口07通過回流管路17與所述污泥進口13連通,所述回流管路17上還可設有回流泵12,污泥通過回流泵12抽送到活性炭吸附腔01中。所述活性炭吸附腔01、混凝反應腔02、絮凝反應腔03內部均設有攪拌器09,使濃水與活性炭、混凝劑、絮凝劑更充分的接觸,同時使反應后的混合液處于流動狀態,便于輸送。優選地,所述泥水分離腔04中設置有攪拌器09,使污泥呈流動狀態,便于抽送。優選地,所述泥水分離腔04內設有泥位探測儀(圖中未示出),根據泥位探測儀探測到的泥位的高低,以及污泥的回流量調節污泥的外排量,以使得泥水分離腔中具有合適的污泥量,確保最佳的濃水處理操作點;其中,可以根據活性炭的利用率等因素來確定污泥的回流量。通過量化污泥回流量與外排量,既提高了藥劑的利用率,同時又保證了后續反滲透濃水處理得到澄清水的質量。可選擇地,如圖2所示,所述活性炭吸附腔01、混凝反應腔02之間的通道05位于其上部,混凝反應腔02、絮凝反應腔03之間的通道05位于其底部,絮凝反應腔03和泥水分離腔04之間的通道05位于其上部。可選擇地,所述混凝反應腔02、絮凝反應腔03還可連接有加藥裝置(圖中未示出),加藥裝置可選用本領域通用的藥劑添加裝置,用于加入具有沉淀、澄清、分離效果的水處理藥劑,包括但不限于混凝劑、絮凝劑、助凝劑等水處理藥劑。優選地,根據淺池理論的原理,所述泥水分離腔04內部可設置有斜板或斜管,在圖2提供的示意性實施例中,為斜管11,在泥水分離腔04有效容積一定的情況下,增加了沉淀面積,可使污泥去除率高;進入泥水分離腔的混合液自下向上流動,穿過斜管或斜板,澄清水在泥水分離腔04的頂部用穿孔集水管或溢流堰收集;污泥則在泥水分離腔04的底部用穿孔排泥管收集,通過污泥出口07排出。利用上述反應器進行反滲透濃水處理的方法,包括以下步驟:(1)活性炭吸附處理:待處理的反滲透濃水首先由濃水進口06進入活性炭吸附腔01,在攪拌器09的快速混合攪拌下,通過活性炭進料器14向活性炭吸附腔中加入活性炭吸附劑,使活性炭與待處理濃水充分接觸發生吸附反應沉淀,以除去大部分機污染物和氨氮,降低濃水的COD值和氨氮含量,其中,本領域技術人員可以根據本發明來選擇適當的活性炭,例如活性炭的目數可以為50-300,優選地,所述活性炭為粉末活性炭,粉末活性炭的接觸面積大,吸附能力更強,效果更顯著;活性炭的投加量可以根據水中污染物的含量等實際情況進行選擇,例如可以為450-500mg/L;(2)混凝處理:經活性炭吸附處理后,吸附腔中的混合液,即吸附反應產生的沉淀物和濃水,由通道05進入混凝反應腔02中,通過混凝劑進料器15向混凝反應腔02中投加混凝劑,與粉末活性炭及濃水中的污染物發生混凝沉淀反應,形成絮體,同時除去總磷,降低總磷含量;其中,混凝劑的類型和濃度可以根據實際需要進行選擇,例如可以為聚合氯化鋁、三氯化鐵、聚合氯化鐵、硫酸鋁、硫酸亞鐵、硫酸鋁鉀(明礬)、鋁酸鈉或硫酸鐵等,混凝劑的濃度可以為15-20mg/L;(3)絮凝處理:經混凝劑處理后,混凝反應腔02中的混合液由通道05進入絮凝反應腔03中,通過絮凝劑進料器16向絮凝反應腔03中投加絮凝劑進行絮凝反應,使絮體不斷增大,以便于泥水分離,并進一步降低濃水中COD值以及總磷、氨氮的含量;其中,絮凝劑的類型和濃度可以根據實際需要進行選擇,例如可以為聚丙烯酸、聚丙烯酸鈉、聚丙烯酸鈣或聚丙烯酰胺等,絮凝劑的濃度可以為0.5-1mg/L;(4)泥水分離處理:經絮凝處理后的混合液由通道05進入泥水分離腔04進行污泥和澄清水的分離,分離出的澄清水通過凈水管路外排;(5)將步驟(4)分離出的污泥通過回流管路輸送到活性炭吸附腔中。優選地,在步驟(5)中,將步驟(4)分離出的污泥通過回流管路17定量輸送到活性炭吸附腔01中,并根據泥位探測儀探測到的泥位以及污泥回流量,將剩余部分通過污泥管路定量外排。以下通過實施例對本發明作進一步地詳細說明。實施例1經取樣化驗分析,待處理進水水質條件如下:表1檢測項目COD氨氮總磷含量(mg/L)107.437.742采用本發明第一種實施方式所述的多腔式一體化濃水處理反應器,處理工藝流程參見圖1,具體如下:(1)待處理的反滲透濃水首先由濃水進口06進入活性炭吸附腔01,啟動攪拌器09進行混合攪拌,同時通過活性炭進料器14向活性炭吸附腔01中加入粉末活性炭,混合攪拌約10-20min,使粉末活性炭與待處理濃水充分接觸發生吸附反應沉淀,以除去大部分機污染物和氨氮,降低濃水的COD值和氨氮含量,其中,粉末活性炭目數為200,投入量約為450mg/L;(2)經活性炭吸附處理后,活性炭吸附腔中的混合液,即吸附反應產生的沉淀物和濃水,由通道05進入混凝反應腔02中,在混凝反應腔02中投加聚合氯化鋁混凝劑,反應2-5min,使活性炭及濃水中的污染物反應形成絮體,同時除去總磷,降低總磷含量,其中,聚合氯化鋁投加量為18mg/L;(3)經混凝劑處理后,混凝反應腔02中的混合液由通道05進入絮凝反應腔03中,在絮凝反應腔03中投加聚丙烯酰胺絮凝劑,進行絮凝反應2-5min,使絮體不斷增大,以便于泥水分離,并進一步降低濃水中COD值以及總磷、氨氮的含量,其中,聚丙烯酰胺的投加量為0.8mg/L;(4)經絮凝處理后的混合液由通道05進入泥水分離腔04進行污泥和澄清水的分離,分離出的污泥通過污泥管路10外排,澄清水通過凈水管路外排;反滲透(RO)濃水反應器的運行參數如下:活性炭吸附裝置中反滲透濃水的進入量為353m3/h,泥水分離裝置中澄清水的排出量為350m3/h,污泥的排出量為8m3/h。反滲透濃水經過上述處理后,COD穩定降至42.97mg/L,氨氮的含量降至4.22mg/L,總磷的含量降至0.25mg/L,出水達到了一級排放標準,系統濃水的處理量為353m3/h。實施例2采用本發明第二種實施方式所述的多腔式一體化濃水處理反應器,處理工藝流程參見圖2,具體如下:(1)待處理的反滲透濃水首先由濃水進口06進入活性炭吸附腔01,啟動攪拌器09進行混合攪拌,同時通過活性炭進料器14向活性炭吸附腔01中加入粉末活性炭,混合攪拌約10-20min,使粉末活性炭與待處理濃水充分接觸發生吸附反應沉淀,以除去大部分機污染物和氨氮,降低濃水的COD值和氨氮含量,其中,粉末活性炭目數為200,投入量約為400mg/L;(2)經活性炭吸附處理后,活性炭吸附腔中的混合液,即吸附反應產生的沉淀物和濃水,由通道05進入混凝反應腔02中,在混凝反應腔02中投加聚合氯化鋁混凝劑,反應2-5min,使活性炭及濃水中的污染物反應形成絮體,同時除去總磷,降低總磷含量,其中,聚合氯化鋁投加量為18mg/L;(3)經混凝劑處理后,混凝反應腔02中的混合液由通道05進入絮凝反應腔03中,在絮凝反應腔03中投加聚丙烯酰胺絮凝劑,進行絮凝反應2-5min,使絮體不斷增大,以便于泥水分離,并進一步降低濃水中COD值以及總磷、氨氮的含量,其中,聚丙烯酰胺的投加量為0.8mg/L;(4)經絮凝處理后的混合液由通道05進入泥水分離腔04進行污泥和澄清水的分離,分離出的澄清水通過凈水管路外排;(5)活性炭污泥根據泥位探測儀探測到的泥位情況,將步驟(4)中分離出的污泥分為兩部分,一部分由污泥出口07排出并由回流管路17、污泥進口13進入到活性炭吸附腔01中,另一部分作為失效炭泥外排。反滲透(RO)濃水處理腔的運行參數如下:活性炭吸附裝置中反滲透濃水的進入量為353m3/h,泥水分離裝置中澄清水的排出量為350m3/h,回流至活性炭吸附裝置的污泥量為20m3/h,失效炭泥排出量為5m3/h。反滲透濃水經過上述處理后,COD值降至45mg/L,氨氮的含量降至4.57mg/L,總磷的含量降至0.26mg/L,出水均達到了一級排放標準,系統濃水的處理量為353m3/h。本文中應用了具體個例對本發明的原理及實施方式進行了闡述,以上實施例的說明只是用于幫助理解本發明的系統及其核心思想;同時,對于本領域的一般技術人員,依據本發明的思想,在具體實施方式及應用范圍上均會有改變之處,綜上所述,本說明書內容不應理解為對本發明的限制。當前第1頁1 2 3