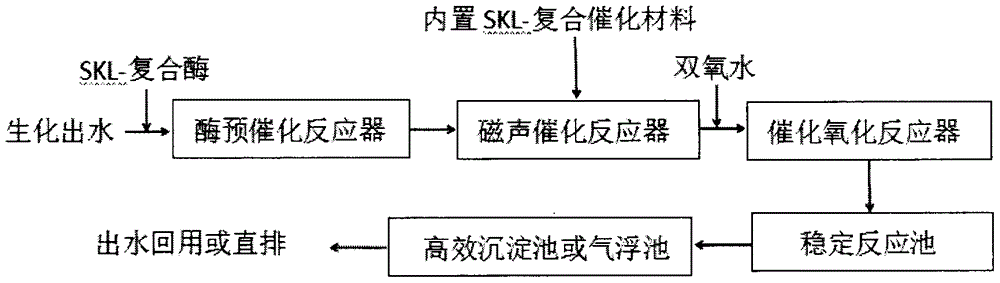
本發明涉及水污染防治研究領域,尤其涉及一種酶預催化-磁聲催化氧化深度水處理方法。
背景技術:
:工業廢水性質復雜、毒性大、鹽份高、B/C低,經生化法(如A2/O)處理后出水中仍含有多環芳烴、鹵代烴、雜環類、苯酚、酚的同系物以及萘、蒽、苯并芘等多環類化合物,這類污染物屬于“三抗”,抗生化、抗光化、抗氧化的難降解性污染物。工業廢水提標升級要求出水達到國家一級A標,從各工程建設運行后的情況調查來看,芬頓、臭氧、活性炭吸附、MBR等常規工藝,處理效果不理想,難以穩定達標且運行成本過高導致反復技改投資。催化氧化法是對化學氧化法的改進與強化,根據所采取的不同改進措施,發展出濕式催化氧化法、光催化氧化法、均相催化氧化法和多相催化氧化法。濕式催化氧化法是利用對系統加壓加溫,可利用已有的工業催化劑,使反應迅速完成。而其對設備與配套設施要求高,需要高溫、高壓;催化劑損耗很大,易發生中毒、致污等現象而失活。光催化氧化法是反應過程中輔以紫外光照,使氧化劑H2O2、O3吸收光能迅速分解形成·OH自由基,攻擊水中有機物基團,使之分解。工藝需要紫外線發生裝置,需拆換,反應選擇性差,廢水有機物的光解常受其他競爭反應的干擾,可能產生更毒的物質。均相催化氧化法是向反應體系中投加可溶性的酸、金屬鹽等物質,通過引發O3、H2O2的自由基型反應并不斷再生而對水中有機物氧化反應起催化作用。但均相催化氧化法采用的催化劑無法回收,藥劑費用偏高,處理過程中向水質帶進其它雜質。多相催化氧化法是一種新型的深度處理技術,其主要向反應體系中裝入固體催化劑,對有機物氧化分解的催化作用在催化劑表面進行,目前其存在著處理效率不穩定,催化劑與廢水性質是否匹配對處理效率影響很大。因此,如何根據目前多相催化氧化法存在的問題進行改進,并尋求一種高效廣譜的多相催化氧化技術成為難點。常規催化氧化工藝僅將廢水中的部分污染物分解成為小分子有機物,而這些小分子有機物(醇、醛、羧酸等)難以完全分解,一些復雜有機物,如苯類、芳香烴類衍生物也很難降解。在本發明之前,針對這類“三抗”廢水實施深度處理,仍然存在著兩大主要問題,一是難以穩定達到日趨嚴格的排放標準;二是處理成本居高不下。技術實現要素:本發明的目的就在于解決上述缺陷,研制一種酶預催化-磁聲催化氧化深度水處理方法。本發明技術方案是:一種酶預催化-磁聲催化氧化深度水處理方法,其主要技術特征在于步驟如下:(1)將經物化+生化二級處理后的廢水泵提升進入酶預催化反應器,在進酶預催化反應器之前的管道上添加SKL-復合酶,通過水力攪拌混合均勻后進入酶預催化反應器進行生物酶催化反應,SKL-復合酶添加量依據廢水濃度變化;(2)酶預催化反應器出水自流進入磁聲催化反應器,磁聲催化反應器由磁化裝置、超聲裝置和SKL-復合催化材料組成,SKL-復合催化材料裝填密度5kg/m3,廢水在磁聲催化反應器中進行多電位差多金屬化學催化反應,降低下一步催化氧化反應的處理負荷;(3)磁聲催化反應器出水自流進入催化氧化反應器,在催化氧化反應器進水主管上添加雙氧水,廢水在催化氧化反應器中進行強氧化反應,催化雙氧水產生的羥基自由基(·OH)與經過酶預催化和磁聲催化處理后的有機污染物發生快速的鏈式反應,無選擇性地把有害物質氧化成CO2、H2O或礦物鹽;(4)催化氧化反應器出水自流進入穩定反應池,進一步調節水質水量,完善反應,將未進行完全的催化氧化反應繼續,達到徹底降解污染物和充分使用藥劑的目的;(5)穩定反應池出水自流進入固液分離系統,固液分離可使用高效沉淀池或氣浮池等,達到去除SS,保證出水達標排放或回用的目的,投加PAM。所述步驟(1)中SKL-復合酶投加量為0.1-1mg/L。所述步驟(3)中雙氧水濃度為27.5%,雙氧水投加量100-300mg/L。所述步驟(4)中穩定反應池停留時間為0.5-2h。所述步驟(5)中投加PAM為1-3mg/L。本發明的優點和效果在于利用酶預催化,生物酶由漆酶、木聚糖酶、纖維素酶、半纖維素酶、果膠酶等復配而成,針對廢水的預催化具有廣譜性,且成本低;再利用磁化、超聲聯合催化的作用,超聲波發生空化作用的因素除超聲波強度、頻率外,液體的表面張力也是關鍵因素,液體的表面張力越大,空化強度越高,越不易于產生空化作用,而廢水先通過磁場后,使原來較大締合水分子集團變成較小締合水分子集團,水的表面張力變小,使水在超聲波的作用下更易于發生空化作用,提高了超聲波的催化速度。本發明的優點和效果還在于利用SKL-復合催化材料的多相金屬作為反應活性中心,催化活性點多,催化活性高,氧化反應速率和氧化能力高;與雙氧水異相催化反應后能夠從反應體系中分離并重復利用,解決了傳統均相Fenton反應過程中產生大量鐵污泥的問題,減少二次污染的產生,還降低了處理的成本;實現在接近中性條件下催化降解污染物。本發明的優點和效果還在于聯合生物酶催化-多相金屬化學催化-羥基自由基氧化的機理于一組反應器中,針對經二級生化處理后仍含有多環芳烴、鹵代烴、雜環類、苯酚、酚的同系物以及萘、蒽、苯并芘等多環類化合物的廢水具有高效的降解效率,對COD、色度去除率高并且出水穩定,達到要求的排放標準或回用水水質。處理后的廢水可以循環使用,節約了工業用水。本發明已具備設備成套化和工程規模化應用。本發明主要針對“三抗”廢水實施深度處理,解決其常規工藝存在處理效果較差、費用較高、工藝條件要求較高等問題,能夠將工業廢水出水穩定達到國家一級A標,并具有經濟性、高效廣譜性。附圖說明圖1——本發明的流程示意圖。具體實施方式本發明的技術思路是:提供一種酶預催化-磁聲催化氧化深度水處理方法。主要適用于不同類型不同濃度廢水的三級深度處理,處理后出水達到國家一級A標或超低污染物排放標準,可直排或直接回用。本發明提供的一種酶預催化-磁聲催化氧化深度水處理方法的特征,首先利用高效生物酶進行預催化,SKL-生物酶由漆酶、木聚糖酶等多種酶及介體復配而成,屬生物催化體系,將生物酶催化技術應用于污染物的去除,是采用不同于普通微生物菌的系列生物酶、菌結合技術,通過酶打開污染物質中更復雜的化學鏈,降低后續化學催化氧化處理負荷,噸水處理成本低(0.01-0.02元/噸水),大大降低污水處理費用。再利用SKL-復合催化材料輔以磁化、超聲進一步催化反應,與現有催化劑相比,比表面積大,SKL-復合催化材料以Fe、Cu、Mn、Co、Ni多相金屬作為反應活性中心,催化活性點增多,催化活性提高,氧化反應速率和氧化能力提高。通過磁化、超聲波共同催化作用:一是使水分子與有機污染物分子重新排列,減少了有機污染物分子與藥劑分子的反應屏障,提高了反應效率;二是使廢水中微粒子極性增強,凝聚力減弱,形成分散穩定小晶體,防止大晶體結晶,可有效防止系統結垢;三是使得高分子分解、化學鍵斷裂和產生自由基等。本發明提供的一種酶預催化-磁聲催化氧化深度水處理方法技術原理分析:前端經生化二級處理后的廢水利用SKL-生物酶的催化降解功能,促使廢水中酚、萘、吡啶、喹啉、蒽、苯胺、苯并芘等雜環芳香物的降解,再經超聲/磁化/復合催化材料的聯合催化作用,促使廢水中多鍵、高碳架、硝基、偶氮類等污染物進行開環斷鏈,水分子按照磁力線的方向重新排列,降低有機物活性點與藥劑分子的反應屏障,提高后續催化氧化的反應速度和降解效率,難降解有機污染物經過酶、超聲、磁化和金屬催化后,轉化為羧酸、醇、酯類易氧化的有機物,再通過雙氧水在催化作用下產生的羥基自由基將這些有機物氧化為無機態,最終達到徹底降解污染物的目的。下面具體說明本發明。本發明提供一種酶預催化-磁聲催化氧化深度水處理方法的步驟并結合圖1說明如下:1、將經物化+生化二級處理后的廢水泵提升進入酶預催化反應器,在進酶預催化反應器之前的管道上添加SKL-復合酶,通過水力攪拌混合均勻后進入酶預催化反應器進行生物酶催化反應;2、酶預催化反應器出水自流進入磁聲催化反應器,磁聲催化反應器由磁化裝置、超聲裝置和SKL-復合催化材料組成,廢水在磁聲催化反應器中進行多電位差多金屬化學催化反應,降低下一步催化氧化反應的處理負荷;3、磁聲催化反應器出水自流進入催化氧化反應器,在催化氧化反應器進水主管上添加雙氧水,廢水在催化氧化反應器中進行強氧化反應,催化雙氧水產生的羥基自由基(·OH)與經過酶預催化和磁聲催化處理后的有機污染物發生快速的鏈式反應,無選擇性地把有害物質氧化成CO2、H2O或礦物鹽;4、催化氧化反應器出水自流進入穩定反應池,進一步調節水質水量,完善反應,將未進行完全的催化氧化反應繼續,達到徹底降解污染物和充分使用藥劑的目的;5、穩定反應池出水自流進入固液分離系統,固液分離可使用高效沉淀池或氣浮池等,達到去除SS,保證出水達標排放或回用的目的。上述步驟1中的SKL-復合酶添加量依據廢水濃度變化,SKL-復合酶投加量0.1-1mg/L。上述步驟2中的SKL-復合催化材料為由Fe、Cu摻雜Mn、Co、Ni取代缺位多金屬氧酸鹽PW11后負載在修飾后的載體APS-SiO2上,制得的一種復合催化材料,復合催化材料的裝填密度為5kg/m3。上述步驟2中的磁化采用內置永磁材料的方式,永磁材料選用稀土永磁材料釹鐵硼Nd2Fe14B,其剩磁為1.12-1.37T,矯頑力836-915kA/m,最大磁能積239-358kJ/m3,工作溫度≤80℃。上述步驟2中的超聲采用內置超聲波換能器,超聲波發生器外置的方式,超聲波發生器發出的頻率f為35-50kHz。上述步驟3中的雙氧水投加濃度為27.5%,投加量依據廢水濃度變化,雙氧水投加量100-300mg/L。上述步驟4中的穩定反應池停留時間為0.5-2h,選用曝氣攪拌,穩定池底部安裝穿孔曝氣管,風機選用羅茨風機。上述步驟5中的固液分離投加助凝劑PAM1-3mg/L。實施例1:印染廢水浙江某綜合污水處理廠,其中印染廢水占比75%,化工廢水占比15%,生活廢水占比10%,日處理水量32萬噸。生化后二沉池出水COD130~160mg/L,色度較重,電導率大于4000us/cm,生化后二沉池出水通過GC-MS檢出:多為分子結構復雜、分子量大的有機物,相對含量超過1%較大分子量的有機污染物有14種,合計占88.83%,苯胺類有機污染物含量為34.79%等。本發明人對該廢水實施了酶預催化-磁聲催化氧化深度水處理方法的中試,取得了良好的處理效果,COD、TOC、色度、苯胺類等指標降解效果明顯,出水水質指標滿足提標升級要求的《城鎮污水處理廠污染物排放標準》GB18918-2002一級A標,由此該廠實施了本
發明內容的工程規模化應用。技術參數:每天深度水處理規模32萬噸。酶預催化時間8min,酶預催化反應器容積115m3;磁聲催化時間8min,磁聲催化反應器容積115m3,所選永磁材料為釹鐵硼Nd2Fe14B(NNF45),磁性能為剩磁為1.37T,矯頑力876kA/m,最大磁能積358kJ/m3,工作溫度≤80℃,超聲波發生器頻率為38kHz,復合催化材料裝填密度5kg/m3;催化氧化反應器氧化時間7min,氧化反應器容積100m3。藥劑投加:依據設計水質要求,進水COD<160mg/L,出水COD<45mg/L,SKL-復合酶投加量為0.6mg/L,氧化劑H2O2(濃度27.5%)投加量為250mg/L,助凝劑PAM投加量2mg/L。配套3套加藥裝置。土建工程:依據設計反應時間,建造穩定反應池單個容積12500m3,2座;高效沉淀池單個容積2000m3,14座。配套羅茨風機、配套泵管等輔助設施并進行安裝。具體實施情況如下:1、將經物化+生化二級處理后的廢水泵提升進入酶預催化反應器,在進酶預催化反應器之前的管道上添加SKL-復合酶,SKL-復合酶投加量為0.6mg/L,通過水力攪拌混合均勻后進入酶預催化反應器進行生物酶催化反應,反應時間為8min;2、酶預催化反應器出水自流進入磁聲催化反應器,磁聲催化反應器由磁化裝置、超聲裝置和SKL-復合催化材料組成,廢水在磁聲催化反應器中進行多電位差多金屬化學催化反應,反應時間8min,降低下一步催化氧化反應的處理負荷;3、磁聲催化反應器出水自流進入催化氧化反應器,在催化氧化反應器進水主管上添加雙氧水,氧化劑H2O2(濃度27.5%)投加量為250mg/L,廢水在催化氧化反應器中進行強氧化反應,催化雙氧水產生的羥基自由基(·OH)與經過酶預催化和磁聲催化處理后的有機污染物發生快速的鏈式反應,無選擇性地把有害物質氧化成CO2、H2O或礦物鹽;4、催化氧化反應器出水自流進入穩定反應池,進一步調節水質水量,完善反應,穩定反應池反應時間2h,將未進行完全的催化氧化反應繼續,達到徹底降解污染物和充分使用藥劑的目的;5、穩定反應池出水自流進入固液分離系統,固液分離使用高效沉淀池,助凝劑PAM投加量為2mg/L,高效沉淀池沉降時間2h,達到去除SS,保證出水達到國家一級A標。(1)表2-1所示為酶預催化+磁聲催化氧化反應器出水以及總出水的COD、色度、SS和pH水質指標處理前后的變化情況,酶預催化+磁聲催化氧化反應器出水COD去除率達到51.6%,通過穩定反應池進一步完善反應后總出水COD去除率達到73.5%,總出水COD<50mg/L,色度10倍,SS<10mg/L,pH7.6,優于《城鎮污水處理廠污染物排放標準》GB18918-2002一級A標準。表2-1(2)表2-2所示為對同一種水質實施芬頓流化床催化氧化工藝與酶預催化+磁聲催化氧化工藝(對照組)后水質指標COD、色度、苯胺類和TOC的去除效果。表2-2為了驗證酶預催化-磁聲催化氧化深度水處理方法的高效性,對同一水質分別實施酶預催化-磁聲催化氧化深度處理和芬頓流化床催化氧化深度處理的中試對比,中試裝置分別為自主研發的酶預催化-磁聲催化氧化中型試驗裝置和購買的芬頓流化床中型試驗裝置,中試采用該污水處理廠生化后二沉池出水作為兩對照組的中試裝置的進水,中試周期為1個月。由此可以看出,傳統催化氧化工藝改進后的芬頓流化床深度水處理方法對COD的去除率在48%-53%,對色度去除率在53%,對印染廢水中苯胺類去除率在70%,對TOC的去除率在65.5%;而酶預催化-磁聲催化氧化深度水處理方法對COD的去除率在70%-80%,對色度去除率在90%,對印染廢水中苯胺類去除率在93.2%,對TOC的去除率在83.4%,大大提高了廢水中污染指標的去除效率,達到了徹底降解污染物的目的。從經濟指標出發,本次中試酶預催化-磁聲催化氧化運行成本在1.35元/噸水(含藥劑費、電費、污泥費),芬頓流化床運行成本在2.8元/噸水(含藥劑費、電費、污泥費),由此,本發明酶預催化-磁聲催化氧化深度水處理方法運行成本較芬頓流化床催化氧化深度水處理方法節約50%,大大減少了藥劑投加量和污泥產生量,節約了運行成本。實施例2:制藥廢水石家莊某污水處理廠,日處理水量10萬噸,實施深度處理廢水來源為改污水處理廠上游制藥企業廢水與城鎮生活污水,經生化(水解、好氧)處理后的二沉池出水,深度處理后要求出水達到:城鎮污水處理廠污染物排放標準(GB18918-2002)一級A標準。該廠原深度處理采用臭氧/活性炭濾池工藝,運行一段時間后未能穩定達標,且隨著活性炭的吸附飽和,出水效果變差。該廠進水水質復雜且波動大,惰性COD增加,可生化性、可氧化性等大大降低,生化后二沉池出水的COD基本在80~120mg/L之間波動,且色度偏重,偶爾COD上升到150mg/L。氨氮在5.8~7.4mg/L之間,總磷在0.93~1.73mg/L之間。針對國家一級A級標,本次技改深度水處理重點處理COD、色度、總磷等。技改通過多項技術的比選,最終實施本發明的酶催化-磁聲催化氧化深度水處理工藝。技術參數:每天深度水處理規模10萬噸。酶預催化時間8min,酶預催化反應器容積115m3;磁聲催化時間8min,磁聲催化反應器容積115m3,所選永磁材料為釹鐵硼Nd2Fe14B(NNF45),磁性能為剩磁為1.21T,矯頑力915kA/m,最大磁能積358kJ/m3,工作溫度≤80℃,超聲波發生器頻率為45kHz,復合催化材料裝填密度5kg/m3;催化氧化反應器氧化時間7min,氧化反應器容積100m3。藥劑投加:依據設計水質要求,進水COD<120mg/L,出水COD<45mg/L,SKL-復合酶投加量為0.4mg/L,氧化劑H2O2(濃度27.5%)投加量為150mg/L,助凝劑PAM投加量1.5mg/L。配套3套加藥裝置。土建工程:依據設計反應時間,建造穩定反應池單個容積3125m3,2座;高效沉淀池單個容積1500m3,5座。配套羅茨風機、配套泵管等輔助設施并進行安裝。具體實施情況如下:1、將該廠生化后二沉池出水經泵提升進入酶預催化反應器,在進酶預催化反應器之前的管道上添加SKL-復合酶,SKL-復合酶投加量為0.4mg/L,通過水力攪拌混合均勻后進入酶預催化反應器進行生物酶催化反應,反應時間為8min;2、酶預催化反應器出水自流進入磁聲催化反應器,磁聲催化反應器由磁化裝置、超聲裝置和SKL-復合催化材料組成,廢水在磁聲催化反應器中進行多電位差多金屬化學催化反應,反應時間8min,降低下一步催化氧化反應的處理負荷;3、磁聲催化反應器出水自流進入催化氧化反應器,在催化氧化反應器進水主管上添加雙氧水,氧化劑H2O2(濃度27.5%)投加量為150mg/L,廢水在催化氧化反應器中進行強氧化反應,催化雙氧水產生的羥基自由基(·OH)與經過酶預催化和磁聲催化處理后的有機污染物發生快速的鏈式反應,無選擇性地把有害物質氧化成CO2、H2O或礦物鹽;4、催化氧化反應器出水自流進入穩定反應池,進一步調節水質水量,完善反應,穩定反應池反應時間1.5h,將未進行完全的催化氧化反應繼續,達到徹底降解污染物和充分使用藥劑的目的;5、穩定反應池出水自流進入固液分離系統,固液分離使用高效沉淀池,助凝劑PAM投加量為1.5mg/L,高效沉淀池沉降時間2h,達到去除SS,保證出水達到國家一級A標。表3從表3可以看出,本發明將進水COD80-150mg/L處理到出水25-50mg/L,去除率達到68.8%-80%,色度降至10倍以下,去除率達到90%,總磷降至0.1mg/L以下,SS降至10mg/L以下,各項指標均達到一級A標排放要求。充分體現了本發明抗負荷沖擊能力強,用于深度處理可確保出水水質達標,這也是本發明的優勢之一。從經濟指標出發,該污水處理廠實施本發明的酶催化-磁聲催化氧化深度水處理工藝后,深度處理段的綜合運行成本在1.0-1.2元/噸水,出水穩定達到一級A標排放要求,較技改之前臭氧/活性炭濾池深度水處理工藝,深度處理段綜合運行成本降低50%,且抗負荷沖擊能力強,已穩定達標運行一年多。實施例3:化纖廢水新疆某污水處理站,主要處理來自新疆某纖維有限公司的纖維廢水及漿粕廢水,日處理8萬噸。實施深度水處理水量為4萬噸/日,目標COD≤30mg/L進中水回用系統處理后回用于生產,達到新疆自治區環保部門中水回用要求。經物化+生化(曝氣活性污泥法)處理后,現生化出水COD在70-120mg/L。深度處理實施本發明的酶催化-磁聲催化氧化深度水處理工藝。技術參數:每天深度水處理規模4萬噸。酶預催化時間8min,酶預催化反應器容積115m3;磁聲催化時間8min,磁聲催化反應器容積115m3,所選永磁材料為釹鐵硼Nd2Fe14B(NNF45),磁性能為剩磁為1.13T,矯頑力836kA/m,最大磁能積238kJ/m3,工作溫度≤80℃,超聲波發生器頻率為50kHz,復合催化材料裝填密度5kg/m3;催化氧化反應器氧化時間7min,氧化反應器容積100m3。藥劑投加:依據設計水質要求,進水COD70-120mg/L,出水COD<30mg/L,SKL-復合酶投加量為0.8mg/L,氧化劑H2O2(濃度27.5%)投加量為150mg/L,助凝劑PAM投加量2mg/L。配套3套加藥裝置。土建工程:依據設計反應時間,建造穩定反應池單個容積1500m3,1座;高效沉淀池單個容積1500m3,2座。配套羅茨風機、配套泵管等輔助設施并進行安裝。具體實施情況如下:1、將該廠生化后二沉池出水經泵提升進入酶預催化反應器,在進酶預催化反應器之前的管道上添加SKL-復合酶,SKL-復合酶投加量為0.8mg/L,通過水力攪拌混合均勻后進入酶預催化反應器進行生物酶催化反應,反應時間為8min;2、酶預催化反應器出水自流進入磁聲催化反應器,磁聲催化反應器由磁化裝置、超聲裝置和SKL-復合催化材料組成,廢水在磁聲催化反應器中進行多電位差多金屬化學催化反應,反應時間8min,降低下一步催化氧化反應的處理負荷;3、磁聲催化反應器出水自流進入催化氧化反應器,在催化氧化反應器進水主管上添加雙氧水,氧化劑H2O2(濃度27.5%)投加量為150mg/L,廢水在催化氧化反應器中進行強氧化反應,催化雙氧水產生的羥基自由基(·OH)與經過酶預催化和磁聲催化處理后的有機污染物發生快速的鏈式反應,無選擇性地把有害物質氧化成CO2、H2O或礦物鹽;4、催化氧化反應器出水自流進入穩定反應池,進一步調節水質水量,完善反應,穩定反應池反應時間50min,將未進行完全的催化氧化反應繼續,達到徹底降解污染物和充分使用藥劑的目的;5、穩定反應池出水自流進入固液分離系統,固液分離使用高效沉淀池,助凝劑PAM投加量為2mg/L,高效沉淀池沉降時間2h,達到去除SS,保證出水COD<30mg/L,滿足中水回用要求。表4-1所示為實施本發明工藝的設計進水指標和設計出水指標,設計進水pH6-9,出水pH6-9;進水COD70-120mg/L處理到出水COD≤30mg/L;設計進水SS≤50mg/L處理到出水SS≤15mg/L,設計進水色度≤50倍處理到出水色度≤30倍。表4-1指標pHCOD(mg/L)SS(mg/L)色度(倍)進水6~970~120≤50≤50出水6~9≤30≤15≤30原設計實施本發明后將現有生化出水COD70-120mg/L處理到出水COD<30mg/L,達到中水回用要求。實施本發明后,由于企業增產導致約2萬噸/日漿粕廢水直接排放至現有生化系統,導致生化后出水COD上升至200mg/L以上,甚至高達300mg/L。通過調整工藝參數和提高藥劑投加量,實施本發明深度水處理工藝仍然能滿足出水COD<30mg/L的回用水標準。實際藥劑投加:SKL-復合酶投加量為1mg/L,氧化劑H2O2(濃度27.5%)投加量為300mg/L,助凝劑PAM投加量3mg/L。表4-2所示為實施本發明后實際運行情況下的處理前后進出水的COD變化,從7月份到10月份,近4個月運行的COD均值看,實際進水COD232.6-285.3mg/L,實施本發明深度水處理工藝后出水COD23.2-30.7mg/L,COD去除率高達90%,充分驗證了本發明酶催化-磁聲催化氧化深度水處理工藝的高效性。表4-2當前第1頁1 2 3