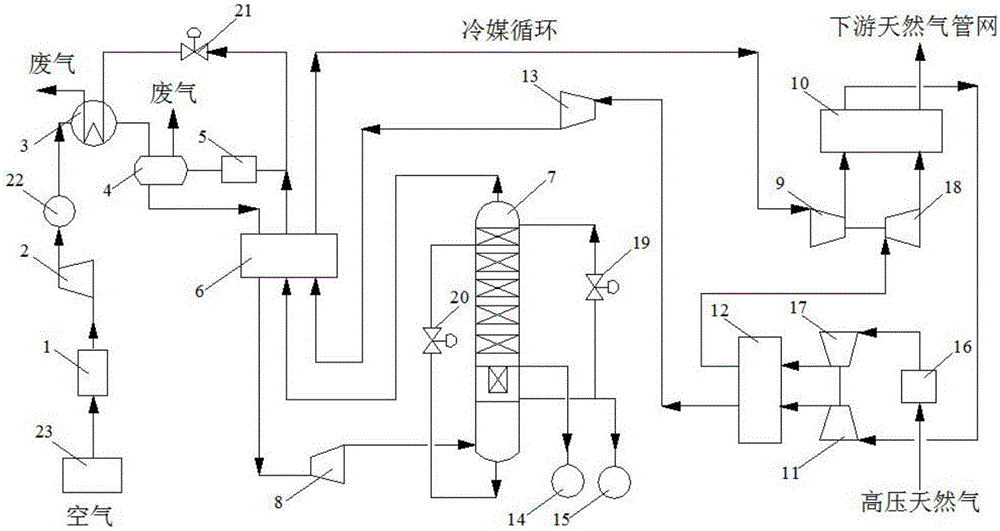
本實用新型涉及高壓天然氣壓差制冷的應用
技術領域:
,尤其涉及一種利用高壓天然氣管網壓力能制冷的低溫空氣分離系統。
背景技術:
:天然氣管網多數以10MPa以上的高壓進行長距離的輸送,而城市燃氣管網設計壓力在0.2~0.4MPa,需進行調壓后輸送至下游管網,在調壓時,一般有一級調壓和二級調壓兩種方式。將超高壓或高壓天然氣直接降壓至0.2MPa~0.4MPa(表壓)的中壓標準為一級調壓;先將超高壓力或高壓天然氣降壓至1.6MPa~2.0MPa(表壓),然后再一次降壓至0.2MPa~0.4MPa(表壓)的中壓標準為二級調壓。調壓過程蘊含著巨大壓力能。目前在城市門站及分輸站采用節流閥調壓時,不僅產生巨大噪音,伴隨的降溫可能會造成下游管道低溫凍堵,最重要的是該調壓過程產生的巨大壓降并未被回收利用,造成能源浪費。回收高壓天然氣管網壓力的一個重要用途是可用于制冷,能有效應用于空氣分離
技術領域:
,可以減少空分系統中由電力驅動的機械制冷產生用于維持低溫環境和生產液體產品所需的大量冷能。降低空氣分離工藝中的制冷成本,對降低電能需求量,促進空氣分離產業發展有重要意義。氧氣和氮氣是常見的空氣分離產品,它們不僅是化學工業的重要生產原料,同時在醫療、電子、冶金、航空、環保等領域也有著非常廣泛的應用。隨著世界科學技術與經濟的高速發展,各行各業對氧氣和氮氣的需求迅速增加,用量也越來越多,推動了空氣分離技術的發展。現有的空氣分離技術主要是用于生產液氧、液氮等工藝氣體產品,雖然最普遍的電壓縮制冷空氣分離技術可以得到各種工業、醫藥業和航空業所需要的氧氣、氮氣等,但由于需要創造及維持—150℃~—191℃的低溫,對電能需求量巨大,設備能耗約占空分成本的70~80%。因而開發節能、高效的空氣分離技術已成為空分行業發展方向。目前,回收的天然氣壓力能已被用于發電、冷庫、冷水空調、制冰、滑冰場、空氣分離、組分分離與凈化、干冰生產、橡膠深冷粉碎以及天然氣輕烴分離等領域。較成熟的高壓天然氣管網壓力能的回收主要是用于制冷和發電,但均存在效率低,設備投資大,余壓無法得到有效利用的缺點。現有技術中已經公開了的利用高壓天然氣壓力能制冷的技術方案有很多,申請號為200810026979.4的中國專利提出了一種利用高壓天然氣直接通過無動力制冷機降壓膨脹制冷的工藝流程,可以得到—40℃~—100℃之間的低溫。但由于該專利中未回收膨脹過程中的機械能,僅利用膨脹產生的冷能,導致壓力能利用率較低,小于50%,且無法獲得—100℃以下的低溫,不適用于空氣分離。申請號為201210128345.6的中國專利和申請號為200510037532.3的中國專利提出了利用高壓天然氣壓力能膨脹制冷液化天然氣的工藝流程。采用預冷及膨脹制冷可以得到—100℃的低溫天然氣,但未考慮大的溫降易造成輸氣管道凍堵,為保證正常生產需增大天然氣處理的投資,運營成本較高。另外,公開號為CN101245956A、CN101852529B、CN102563958B、CN2791144Y、US5137558的專利也公開了相應回收利用管網壓力的技術方案。但上述技術方案中僅公開了利用回收天然氣管網壓力能發電或制冷,目前天然氣管網壓力能用于空氣分離的技術的發展人處于起步階段,公開號為CN103968640A的專利了一種利用天然氣壓差發電冷能的空氣分離系統,涉及天然氣壓差發電冷能應用
技術領域:
,該專利是將高壓天然氣調壓發電與空氣分離裝置相結合,充分利用天然氣調壓發電過程產生的冷能,但壓力能通過渦輪管回收效率較低,而空氣分離僅為其附屬工藝,而冷媒循環中損耗逐年增加,因而該技術存在空氣分離產量低、設備投資大、僅適用于流量大壓力高的天然氣門站即適用范圍較局限的缺點。因此,尋找一種能回收利用天然氣壓力能且不對管網造成凍堵,并能節約硬件投資的適用于中小型分離站的處理系統,對于實現綠色生產有很大的意義。技術實現要素:針對上述問題,本實用新型的目的是為克服現有技術的不足,提供一種利用高壓天然氣管網壓力能的空氣分離系統。該系統結合天然氣壓力能回收和空氣分離兩種技術,將高壓天然氣的較高的壓力能轉換成空氣分離的冷能,利用膨脹機及換熱器作為能量轉化的中間設備,不僅滿足了壓降的要求,而且能夠將天然氣管網壓力能充分制冷充分利用,并解決現有空氣分離技術能耗高及天然氣管網壓力能再利用中能量利用率低的問題。為達此目的,本實用新型通過以下技術方案實現:一種利用高壓天然氣管網壓力能的空氣分離系統,包括天然氣壓力能回收系統、空氣分離系統、連接天然氣壓力能回收系統同空氣分離系統的冷媒循環回路,該冷媒循環回路用于天然氣管網降壓過程產生的巨大冷能轉換至實用新型中的空氣分離裝置,提供空氣分離系統所需的冷能,并通過吸收空氣冷卻時釋放的能量保證輸出的低壓天然氣溫度不致過低;所述天然氣壓力能回收系統包括天然氣凈化裝置、高壓天然氣膨脹機、高壓冷媒壓縮機、換熱器A、冷媒膨脹機、中壓冷媒壓縮機、中壓天然氣膨脹機、換熱器B;空氣分離系統包括鼓風機、空氣過濾器、空壓機、空壓機后冷卻器、空氣預冷器、分子篩吸附裝置、電加熱器、主換熱器、空氣膨脹機、精餾塔、氧氣儲存裝置、氮氣儲存裝置;天然氣凈化裝置連接高壓天然氣膨脹機,然后連入換熱器A,換熱器A分別連接冷媒膨脹機和中壓天然氣膨脹機,中壓天然氣膨脹機連接換熱器B,換熱器B出口連接下游天然氣管網,同時設有支路連接高壓冷媒壓縮機,高壓冷媒壓縮機接入換熱器A;冷媒膨脹機連接主換熱器,換熱器有三個出口管線,分別連接中壓冷媒壓縮機、電加熱器、空氣膨脹機,中壓冷媒壓縮機連接換熱器B,電加熱器依次連接分子篩吸附裝置和空氣預冷器,空氣膨脹機連接到精餾塔下部;鼓風機依次連接空氣過濾器、空壓機、空壓機后冷卻器,然后連入空氣預冷器;精餾塔上端出口連接主換熱器,下端出口分別連接氧氣儲存裝置和氮氣儲存裝置。一種利用高壓天然氣管網壓力能的空氣分離系統,包括以下操作步驟:首先,在高壓天然氣調壓過程中,通過膨脹機將高壓天然氣的壓力能轉換為機械功和冷能,再利用冷媒作為媒介,回收產生的機械能及冷能,一方面利用高壓天然氣膨脹產生的機械功將冷媒壓縮,使其成為高壓制冷工質,另一方面,通過換熱網絡的優化設計,利用高壓天然氣膨脹產生的冷能來冷卻壓縮后的高壓冷媒,同時提高高壓天然氣進入膨脹機的進氣溫度,增加高壓天然氣膨脹產生的機械功,進而利用保溫管線將冷卻后的高壓冷媒輸送至空氣分離裝置區域,再利用高壓冷媒膨脹機膨脹產生的低溫冷能;同時,高壓冷媒膨脹產生的機械功用于冷媒經主換熱器換熱后初步增壓;然后通過保溫管線將初步增壓后的冷媒輸送至換熱器回收高壓天然氣膨脹產生的冷能,形成冷媒循環。一種利用高壓天然氣管網壓力能的空氣分離系統,包括以下步驟。A.高壓天然氣壓力能回收:高壓天然氣管網輸送至調壓站、分輸站的高壓天然氣,壓力在1.5MPa(絕對壓力,下文出現壓力的均為絕對壓力)以上。高壓天然氣流經天然氣凈化裝置初步處理后,進入高壓天然氣膨脹機膨脹降壓至1~7MPa,高壓天然氣膨脹機輸出的機械功用于中壓冷媒壓縮機的驅動,同時獲得溫度降低的中壓天然氣,并通過調節高壓天然氣膨脹機的出口壓力,保證其溫度高于天然氣的水露點。通過高壓天然氣膨脹機膨脹后的中壓天然氣通過換熱器A與經過高壓冷媒壓縮機壓縮后的高壓冷媒換熱,獲得熱量后溫度升高至—15℃~100℃;溫度升高后的中壓天然氣通過中壓天然氣膨脹機,膨脹后壓力降低至0.4~3MPa,得到溫度降低的低壓天然氣,獲得的機械功用于驅動高壓冷媒壓縮機,并保證其溫度高于其水露點。低溫低壓天然氣通過換熱器B同經過中壓冷媒壓縮機壓縮后的中壓冷媒換熱,換熱后的低壓天然氣溫度升高至0℃以上輸送至天然氣管網。B.用于連接天然氣壓差制冷系統同空氣分離系統的冷媒循環:低溫冷媒流經空氣分離系統的主換熱器同預冷后的高壓空氣及精餾塔分流出的低溫廢氣換熱,換熱后冷媒溫度升高至0~20℃。溫度升高后的低壓冷媒流入中壓冷媒壓縮機,增壓至2~3MPa,溫度升高至90~130℃,成為中壓冷媒,其壓力及溫度受高壓天然氣膨脹機的輸出功大小影響。中壓冷媒通過保溫管線輸送至換熱器B與經過中壓天然氣膨脹機膨脹后的低壓低溫天然氣換熱,中壓冷媒溫度降低至0℃~30℃,然后經過高壓冷媒壓縮機增壓至4~6MPa,成為高壓冷媒,其壓力及溫度受中壓天然氣膨脹機的輸出功大小影響。高壓冷媒通過換熱器A同經高壓天然氣膨脹機膨脹后的中壓天然氣換熱,溫度降至—30~0℃,然后通過保溫管線輸送至冷媒膨脹機,膨脹后的冷媒溫度降至—120~—140℃。進入主換熱器為空氣分離裝置提供冷能,中壓天然氣膨脹得到的機械功用于驅動空氣分離裝置的空氣壓縮機,形成冷媒循環。C.空氣分離:空氣通過空氣管線進入空氣過濾器,脫除固體雜質后進入空氣壓縮機組,壓縮至1~2.5MPa。溫度升高至110~200℃,壓縮后的空氣進入空壓機后冷卻器冷卻至90~180℃。獲得的高溫高壓空氣進入空氣預冷器,在空氣預冷器中同經主換熱器換熱后的低溫空氣換熱,溫度降至10~20℃,預冷后的空氣進入分子篩吸附裝置,脫除水及雜質后進入主換熱器,同低溫冷媒及精餾塔頂分流出的低溫廢氣進行換熱,溫度降至—120~—140℃,經保溫管線輸送至空氣膨脹機,膨脹后壓力0.3~1MPa,溫度降至該壓力下的飽和溫度,從精餾塔底部進入,低溫低壓空氣在精餾塔中反復冷凝和蒸發,含液氧成分較多的富氧液空集聚于精餾塔上塔及下塔底部,氮氣則集聚于上塔及下塔頂部。高純液氧(含氧99.80%)從精餾塔上塔底部出口流出經保溫管道輸送至氧氣儲存裝置;高純氮(含氮99.99%)在下塔頂部冷凝蒸發器中冷凝為液氮,引出后分為兩股,一股作為回流液從上塔頂部下流為上塔上升的蒸氣提供冷量,以便得到純度更高的液態產品;另一股導入液氮儲存裝置被儲存;從精餾塔塔頂分流一股低溫廢氣,輸送至主換熱器,同預冷凈化后的空氣及冷媒換熱后,分為兩股一部分經調壓閥調壓至常壓,進入空氣預冷器,為空氣提供冷量,外排,另一股低溫廢氣經管路輸送至電加熱器,為分子篩吸附裝置再生提供氣源,后外排至大氣;精餾塔底部聚集的富氧液空(含氧約38%)約—180℃,節流后約—190℃進入精餾塔上部回流,一方面增加液空在精餾塔中的蒸發冷流次數,另一方面為上塔上升的蒸氣提供冷量,以便得到純度更高的液態產品。進入高壓天然氣回收系統的天然氣壓力介于1.6~10MPa,采用兩級膨脹換熱的方式,包括高壓天然氣膨脹機及中壓天然氣膨脹機,高壓天然氣經兩級降壓,壓力降至下游天然氣管網輸送壓力。且通過調節高壓天然氣膨脹機及中壓天然氣膨脹機出口壓力及冷媒循環的流量控制天然氣出口溫度,保證其高于天然氣水露點。高壓天然氣膨脹機、中壓天然氣膨脹機、空氣膨脹機及冷媒膨脹機為透平膨脹。冷媒循環中冷媒經中壓冷媒壓縮機、高壓冷媒壓縮機二級增壓。中壓冷媒壓縮機由高壓天然氣膨脹機產生的機械能驅動,高壓冷媒壓縮機由中壓天然氣膨脹機產生的機械能驅動。冷媒經壓縮機壓縮增壓產生的熱能均通過換熱器A、換熱器B用于加熱經膨脹機膨脹后的天然氣。而高壓天然氣膨脹產生的冷能均通過換熱器用于冷卻壓縮后升溫的冷媒。冷媒循環在空氣分離系統提供的冷能溫度,一方面可通過調節冷媒循環量,另一方面可以改變精餾塔頂低溫廢氣分流的量,減少冷媒循環量、增大精餾塔頂分流低溫廢氣量、增大冷媒二級壓縮壓縮比均可降低制冷溫度。相反則會提高制冷溫度。高壓天然氣調壓及壓力能回收裝置同空氣分離裝置通過制冷循環相連接,保證兩區域的安全間隔。本實用新型相對于現有技術具有如下優點:(1)本實用新型提出的一種利用高壓天然氣管網壓力能的空氣分離系統,是基于能量轉換原理,利用膨脹機將壓力能轉換為冷能及機械功,通過冷媒循環,同時回收高壓天然氣膨脹產生的冷能及機械能,而且可以產生—120℃以下的低溫冷能用于空氣分離,為空氣分離提供廉價的冷源,降低了空分產品的能耗;(2)本實用新型通過優化換熱網絡,實現對高壓天然氣膨脹產生的冷能及冷媒壓縮產生的熱能的梯級利用,一方面,回收冷媒壓縮產生的熱能用于提高中壓天然氣膨脹機的入口溫度及進入下游天然氣管網的溫度,增加天然氣膨脹過程產生的機械功,保證進入下游天然氣管網的天然氣溫度高于其水露點;另一方面利用高壓天然氣膨脹產生的冷能冷卻冷媒,可以節約冷媒循環過程中冷媒壓縮后冷卻設備的投資及操作費用。降低冷媒循環的運行成本;(3)本實用新型通過冷媒作為能量傳遞的紐帶,將天然氣調壓過程及壓力能回收過程設備同空氣分離設備分開,并保證安全距離,避免兩環節在同一區域,而引起的消防安全等方面的隱患,有利于安全運營;(4)本實用新型通過回收高壓天然氣管網壓力能制冷為空氣分離提供—120℃以下的冷能,不需消耗外界能量,制冷能耗很低。并且通過對系統地優化設計,利用高壓天然氣膨脹制冷部分具有較強操作柔性,在天然氣氣流量波動及空氣分離生產負荷波動時,均能保持正常操作。該過程不需外界提供冷、熱源,并且保證天然氣外輸溫度高于水露點,避免冰堵;(5)采用氮氣作為冷媒循環的工質,氮氣為該系統的產物,可以降低生產成本的同時,可以避免換熱過程空氣與天然氣接觸而發生安全事故。附圖說明附圖1為本實用新型的結構示意圖。圖中1、空氣過濾器,2、空壓機,3、空氣預冷器,4、分子篩吸附裝置,5、電加熱器,6、主換熱器,7、精餾塔,8、空氣膨脹機,9、中壓冷媒壓縮機,10、換熱器B,11、高壓冷媒壓縮機,12、換熱器A,13、冷媒膨脹機,14、氧氣儲存裝置,15、氮氣儲存裝置,16、天然氣凈化裝置,17、高壓天然氣膨脹機,18、中壓天然氣膨脹機,19、節流閥A,20、節流閥B,21、節流閥C,22、空壓機后冷卻器,23、鼓風機。具體實施方式下面結合附圖,對本實用新型的技術方案進一步作具體描述:本實用新型提供的一種利用高壓天然氣管網壓力能的空氣分離系統,主要由空氣過濾器1、空壓機2、空氣預冷器3、分子篩吸附裝置4、電加熱器5、主換熱器6、精餾塔7、空氣膨脹機8、中壓冷媒壓縮機9、換熱器B10、高壓冷媒壓縮機11、換熱器A12、冷媒膨脹機13、氧氣儲存裝置14、氮氣儲存裝置15、天然氣凈化裝置16、高壓天然氣膨脹機17、中壓天然氣膨脹機18、節流閥A19、節流閥B20、節流閥C21、空壓機后冷卻器22、鼓風機23構成。一種利用高壓天然氣管網壓力能的空氣分離系統,具體實施包括以下步驟:(1)高壓天然氣壓力能回收壓力為1.5~10MPa的高壓天然氣經天然氣管道輸送至天然氣凈化裝置16,凈化處理后進入高壓天然氣膨脹機17膨脹降壓至1~7MPa,高壓天然氣膨脹機輸出的機械功用于中壓冷媒壓縮機9的驅動,輸出的中壓天然氣進入換熱器A12與經過高壓冷媒壓縮機8輸出的高壓冷媒換熱,升溫至—15℃~100℃;進入中壓天然氣膨脹機18膨脹降壓至0.4~3MPa,獲得的機械功用于高壓冷媒壓縮機8的驅動;輸出的低溫低壓天然氣經天然氣管線輸送至換熱器B10與經過中壓冷媒壓縮機9輸出的中壓冷媒換熱,換熱后的天然氣經輸氣管道輸送至下游天然氣管網。(2)用于連接天然氣壓差制冷系統同空氣分離系統的冷媒循環低溫冷媒進入主換熱器6同分子篩吸附裝置4輸出的空氣及精餾塔7分流出的低溫廢氣換熱,換熱后溫度升至0~20℃后經冷媒管道輸送至中壓冷媒壓縮機9增壓至2~3MPa,輸出的中壓冷媒通過冷媒保溫管道輸送至換熱器B10與中壓天然氣膨脹機18輸出的低溫低壓天然氣換熱,輸出的中壓冷媒溫度降低至0℃~30℃,進入高壓冷媒壓縮機8增壓至4~6MPa,輸出的高壓冷媒進入換熱器A12同經高壓天然氣膨脹機17輸出的中壓天然氣換熱,輸出的冷媒溫度降至—30~0℃,然后經過冷媒管道輸送至冷媒膨脹機13,輸出的冷媒溫度降低至—120~—140℃,進入主換熱器6形成冷媒循環回路。(3)空氣分離空氣經鼓風機23輸送入空氣過濾器1,輸出的脫出固體雜質的空氣輸送至空壓機組2,輸出的1~2.5MPa空氣經空氣管道輸送至空壓機后冷卻器22冷卻至90~180℃,輸送至空氣預冷器3同主換熱器6輸出的低溫空氣換熱,輸出的空氣溫度降至10~20℃,輸送至分子篩吸附裝置4脫除水及雜質后進入主換熱器6同冷媒膨脹機13輸出的低溫冷媒及精餾塔7頂分流出的低溫廢氣進行換熱,輸出的空氣溫度降低至—120~—140℃,經保溫管線輸送至空氣膨脹機8,輸出的0.3~1MPa空氣從精餾塔7底部進入,低溫低壓空氣在精餾塔7中反復冷凝和蒸發,高純液氧(含氧99.80%)從精餾塔7上塔底部出口流出經保溫管道輸送至氧氣儲存裝置;高純氮(含氮99.99%)在下塔頂部冷凝蒸發器中冷凝為液氮引出后分為兩股,一股經調壓閥A19調壓后輸送至精餾塔7頂部作為回流液為上塔上升的蒸氣提供冷量,另一股導入液氮儲存裝置被儲存;從精餾塔7塔頂分流一股低溫廢氣,輸送至主換熱器6同分子篩吸附裝置4輸出的空氣及冷媒膨脹機13輸出的冷媒換熱后,分為兩股物流一部分經調壓閥C21調壓至常壓后輸送至空氣預冷器3與空壓機后冷卻器22輸出的空氣換熱后外排至大氣;另一股則經管路輸送至電加熱器5加熱后輸送至分子篩吸附裝置4作為再生氣后外排至大氣。精餾塔7底部聚集的富氧液空(含氧約38%)約—180℃自塔底輸出,調壓后約—190℃從精餾塔7上部輸入。下面結合四川某天然氣分輸站天然氣的狀態參數及附圖,對本實用新型的技術方案作進一步的詳述,但本實用新型的實施方式不限于此,對于未注明的工藝參數,可參照常規技術進行。實施例一種利用高壓天然氣管網壓力能的空氣分離系統,其工藝流程如圖1所示,采用二級膨脹降壓的方式,冷媒循環選擇為氮氣。某天然氣分輸站,總分輸量為100×104Nm3/d,從天然氣主干管網輸送至分輸站的高壓天然氣壓力為7.0MPa,溫度為20.0℃,天然氣的體積組成見表1,環境溫度為25.0℃,該管輸天然氣在7.0MPa下的水露點為15.0℃,在分輸站內7.0MPa的高壓天然氣需要被降至2.0MPa后進入中壓天然氣管網分輸。現用分輸站全部來氣調壓釋放的壓力能用于制冷,為天然氣分輸站外的空氣分離裝置提供冷源。冷媒循環流量為7000Nm3/h,冷媒選擇為氮氣。膨脹機、壓縮機等設備的等熵效率取0.8。表1某天然氣分輸站來氣的氣體組成組成CH4C2H6C3H8i-C4H10n-C4H10i-C5H12n-C5H12CO2mol%97.561.440.200.020.070.010.020.64一種利用高壓天然氣管網壓力能的空氣分離系統的具體步驟如下:(1)高壓天然氣壓力能回收該分輸站高壓天然氣來氣的氣量為100×104Nm3/d,先進入天然氣凈化裝置16,除去水及固體雜質后,進入高壓天然氣膨脹機17膨脹,高壓天然氣由7.0MPa降壓至3.0MPa,高壓天然氣膨脹機17輸出功為578.2kW,用于驅動中壓冷媒壓縮機9,膨脹后的中壓天然氣溫度降至—29.8℃,在經過換熱器A12與高壓冷媒壓縮機11流出的174.9℃、5MPa高壓氮氣進行換熱,吸收其熱量后溫度升高至—8.9℃,中壓天然氣在換熱器A中的壓降0.5MPa,然后進入中壓天然氣膨脹機18中膨脹至2MPa,中壓天然氣膨脹機18的輸出功為280.7kW,用于驅動高壓冷媒壓縮機11,從中壓天然氣膨脹機18中輸出的低壓天然氣溫度為—30.4℃,然后進入換熱器B10同中壓冷媒壓縮機9流出的233.2℃、1.6MPa中壓氮氣換熱,吸收熱量后溫度升高至3.4℃,進入下游天然氣管網。(2)用于連接天然氣壓差制冷系統同空氣分離系統的冷媒循環7000Nm3/h、—131.2℃、300kPa的低溫循環氮氣進入主換熱器6,同精餾塔7塔頂分流出的—191℃、0.13MPa的低溫廢氣及經分子篩吸附裝置4過濾后的10℃、2MPa的空氣進行換熱,吸收熱量后升溫至8℃,然后進入中壓冷媒壓縮機9壓縮至1.6MPa,中壓冷媒壓縮機9功耗約為550.6kW,循環氮氣溫度升高至233.2℃,然后進入換熱器B10同中壓天然氣膨脹機18輸出的—30.4℃、2MPa的低壓天然氣進行換熱,釋放熱量后溫度降低至18℃,然后進入高壓冷媒壓縮機11壓縮至4MPa,高壓冷媒壓縮機11功耗約為279.2kW,然后進入換熱器A12同高壓天然氣膨脹機17流出的—29.8℃、3MPa的中壓天然氣換熱,釋放熱量,溫度降低至—27℃,然后進入冷媒膨脹機13膨脹后壓力降至0.3MPa,冷媒膨脹機13的輸出功為215.4kW,循環氮氣溫度降至—131.2℃,循環氮氣在主換熱器6、換熱器A12、換熱器B10的壓降分別為0.5MPa、0.3MPa、0.3MPa。(3)空氣分離溫度為15℃的原料空氣經鼓風機23輸入自潔式空氣過濾器1除去灰塵等細小顆粒固體雜質后,進入空氣壓縮機組2,在空氣壓縮機組2中的低壓空氣壓縮機增壓至0.8MPa,低壓空氣壓縮機功耗約為408.5kW,溫度升高至空氣壓縮機組2中的中壓空氣壓縮機組進行壓縮,壓力升高至2MPa,中壓空氣壓縮機功耗約為416.3kW,溫度升高至182.9℃,進入空壓機后冷卻器22溫度降至164℃。獲得的高溫高壓空氣進入空氣預冷器3,在空氣預冷器3中同經主換熱器6換熱后的—8.9℃、0.13MPa低溫廢氣換熱,溫度降至10℃,預冷后的空氣進入分子篩吸附裝置4,脫除水及雜質后進入主換熱器6,不計空氣在分子篩吸附裝置4中的壓降及溫降。同冷媒膨脹機13流出的—131.2℃、300kPa低溫冷媒及精餾塔7頂分流出的—191℃、0.13MPa低溫廢氣進行換熱,溫度降至—137℃,經保溫管線輸送至空氣膨脹機8,膨脹后壓力0.35MPa,空氣膨脹機8輸出的機械功為93.2kW,膨脹后空氣的溫度為—179.3℃輸送至精餾塔7底部。低溫低壓空氣在精餾塔7中反復冷凝和蒸發,上塔底部獲得的—180.2℃、0.135MPa高純度液氧(含氧99.80%)被導入液氧儲存裝置儲存14。高純氮(含氮99.99%)在下塔頂部冷凝蒸發器中冷凝為液氮(183.4℃、0.35MPa),引出后分為兩股,一股經調壓閥19調壓至0.13MPa作為回流液從上塔頂部下流為上塔上升的蒸氣提供冷量,以便得到純度更高的液態產品;另一股導入液氮儲存裝置15被儲存;在液空進料口處,下塔富氧液空(含氧約38%)約—180℃,經調壓閥20調壓后約—190℃進入上塔上部回流。精餾塔7頂部分流出的5×104Nm3/d、—191.5℃、0.132MPa低溫廢氣,進入主換熱器6同經分子篩吸附裝置4吸附后的10℃、2MPa的空氣及冷媒膨脹機8流出的—131.2℃、300kPa循環氮氣換熱,換熱后低溫廢氣的溫度升高至—8.9℃,分為兩股一股4×104Nm3/d的低溫廢氣進入空氣預冷器3為壓縮機輸出的182.9℃、2MPa高溫高壓空氣提供冷能,吸收熱量后的廢氣外排至大氣。另一股則經節流閥21進入分子篩吸附裝置4,輸送至電加熱器5,為分子篩吸附裝置4再生提供氣源,后外排至大氣。采用本實用新型所述的利用高壓天然氣管網壓力能的空氣分離系統,100×104Nm3/d的高壓天然氣由7MPa調壓至2MPa可回收的壓力能約為5650kW,在該實例中回收高壓天然氣膨脹過程產生的機械功約829.6kW,同時為空氣分離過程提供低溫冷能,可將3.09×104Nm3/h的空氣降至350MPa的飽和溫度—179.6℃,相對出傳統的電制冷低溫空氣分離方法可節約電能約726.72×104kWh,節能價值約581.36×104元。以上所述,僅是本實用新型的較佳實施例而已,并非對本實用新型作任何形式上的限制,雖然本實用新型已以較佳實施例揭露如上,然而并非用以限定本實用新型,任何熟悉本專業的技術人員,在不脫離本實用新型技術方案范圍內,當可利用上述揭示的技術內容作出些許更動或修飾為等同變化的等效實施例,但凡是未脫離本實用新型技術方案的內容,依據本實用新型的技術實質對以上實施例所作的任何簡單修改、等同變化與修飾,均仍屬于本實用新型技術方案的范圍內。當前第1頁1 2 3