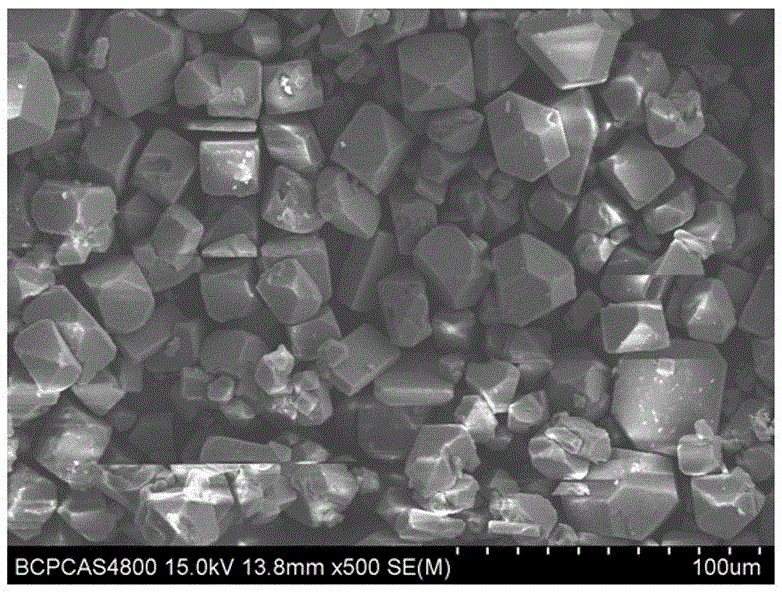
本發明涉及一種紅光熒光粉及其制備方法,具體涉及一種耐高溫高濕的氟化物紅光熒光粉及其制備方法。
背景技術:
:1996年出現了用藍光LED與YAG熒光粉組合而成的白光LED,被譽為是將超越白熾燈、熒光燈和氙氣燈(HID燈)的第四代照明光源。由于其具有節能、環保、安全、壽命長等優點,現已被廣泛用于生產和生活中的各個方面,包括指示、顯示、裝飾、背光源、普通照明等領域。1997年日亞公司首次報道了Y3Al5O12:Ce3+(YAG:Ce)黃色熒光材料與藍光InGaN芯片組合,但由于其光譜的紅色波段較弱,故此白光的色彩還原性較差,顯色指數較低。另一種白光發光二極管則為三波長混合光,它是以無機紫外光芯片發出的紫外光激發三基色(藍光、綠光、紅光)熒光粉所形成,若發出的三基色光的成分適量,則其混合光為白光。然而仍然存在紅光純度不夠或利用效率偏低的問題。因此,業界需要尋求一種性質比較穩定、色純度較高的紅光熒光粉,使其能夠與其它熒光粉有效搭配,用于LED背光源。而窄譜帶的熒光粉其色純度相對來說比較高,因此性能穩定的峰值較窄的紅光熒光粉具有非常廣闊的市場前景。Mn4+是紅色熒光粉常用的激活劑,能夠被紫外或者藍光激發,產生高強度的紅色發射峰。由于Mn4+離子發射鮮艷紅光,發射光譜主要分布在610~680nm范圍,這使光源的顯色性顯著提高,因此Mn4+摻雜的氟化物熒光粉體化合物的研究近來備受人們的關注。目前作為背光源用的紅光熒光粉,為了更高效率的利用熒光粉材料,主要選擇窄譜帶的紅光熒光粉。然而,現有的窄譜帶紅光熒光粉普遍存在熱猝滅性能和耐高溫高濕性能較差,且內量子效率、熱猝滅性和耐高溫高濕性不能同時保持在較高水平的問題,這無疑限制了它們的應用。技術實現要素:本發明的目的之一就是提供一種耐高溫高濕的氟化物紅光熒光粉,以解決現有紅光熒光粉內量子效率低、熱猝滅和耐高溫高濕性能差的問題。本發明的目的之二是提供一種耐高溫高濕的氟化物紅光熒光粉的制備方法,以制備出內量子效率高、熱猝滅性和耐高溫高濕性能好的窄譜帶氟化物紅光熒光粉。該制備方法流程簡單,可在接近常溫和常壓下制得目標產品,有利于大規模的工業化生產。本發明的目的是這樣實現的:一種耐高溫高濕的氟化物紅光熒光粉,該熒光粉的化學通式為KmAnM1-xF6:xMn4+;通式中,A為Cu、Ba、Zn中的一種或兩種;M為Ti、Si、Ge中的至少一種;m+2n=2,且0.05≤n≤0.2,1.6≤m≤1.9;0<x<0.2,優選地,0.02≤x≤0.15,更優選地x=0.05;在所述熒光粉的粉體表面包覆有硅酸鉀-羥甲基纖維素鈉-聚乙二醇混合物。本發明的熒光粉可被激發波長范圍為300~500nm的光有效激發,產生峰值波長為610~650nm的紅光,其半峰寬只有2~9nm,且其具有很高的色純度,主要應用于LED背光源,在提高顯色指數及色彩飽和度上具有很大的優勢。本發明的熒光粉具有更好的晶體形貌和更高的亮度,且內量子效率高,耐高溫高濕性能好。本發明還提供了一種上述耐高溫高濕的氟化物紅光熒光粉的制備方法,包括以下步驟:a、將M的氧化物加入氫氟酸溶液中,制得H2MF6溶液;b、向上述溶液中加入K的氟化物、A的氟化物以及錳的可溶性鹽,并加入K2MF6基質,然后邊攪拌邊向溶液中逐滴滴加過氧化氫,待溶液變色后停止滴加,生成KmAnM1-xF6:xMn4+沉淀;c、將KmAnM1-xF6:xMn4+沉淀進行過濾、洗滌、烘干,最終得到KmAnM1-xF6:xMn4+固體產物;d、將所得固體產物加到硅酸鉀-羥甲基纖維素鈉-聚乙二醇溶膠中,用超聲波分散均勻,攪拌,真空干燥,得到包覆有硅酸鉀-羥甲基纖維素鈉-聚乙二醇溶膠混合物的熒光粉。本發明方法的所述步驟a中,M的氧化物為TiO2、SiO2、GeO2中的至少一種,氫氟酸的濃度為20wt%~80wt%,優選為30wt%~60wt%,更優選為40wt%;反應溫度為0~100℃,優選為0~70℃,更優選為25℃。本發明方法的所述步驟b中,K的氟化物為KF,A的氟化物為AF2,錳的可溶性鹽為KMnO4,K2MF6基質中的M與步驟a中所用的氧化物中的M相同。本發明方法的所述步驟b中,過氧化氫的濃度為20wt%~40wt%,優選為30wt%。本發明方法的所述步驟b中,攪拌速度為0~1000r/min。本發明方法的所述步驟b中,在停止滴加過氧化氫后,溶液需在0~200℃下靜置0~72h。本發明方法的所述步驟c中,采用醇類溶劑、醚類溶劑、酮類溶劑中的至少一種對沉淀進行洗滌,優選為乙醇或丙酮;烘干是在真空干燥箱中進行,烘干溫度為50~100℃,優選為60~80℃,更優選為70℃。本發明方法的所述步驟d具體包括以下步驟:1)按照硅酸鉀∶羥甲基纖維素鈉水溶液(CMC-Na)∶聚乙二醇水溶液(PEG)=1g∶10~20mL∶5~30mL的比例配制硅酸鉀-羥甲基纖維素鈉-聚乙二醇溶膠,其中,羥甲基纖維素鈉水溶液的質量分數為1~5%,聚乙二醇溶液的質量分數為2~10%;2)將KmAnM1-xF6:xMn4+固體產物加到硅酸鉀-羥甲基纖維素鈉-聚乙二醇溶膠中,兩者的固液比為1g∶5~100mL,采用超聲分散,并加以攪拌,攪拌速度為100~1000r/min,攪拌時間為0.5~5h;3)對所述步驟2)所得混合物進行抽濾,抽濾過程中采用醇類試劑對固體進行洗滌,再對所得濾餅進行真空干燥,即得包覆后的產物。所述步驟2)中,使用的超聲頻率為15KHz~35KHz。所述步驟3)中,真空干燥的溫度為50~250℃,干燥時間為0~72h。本發明方法流程簡單,采用液相法進行制備,可在較低溫度和常壓下制得結晶良好、收率高、晶體形貌好的目標產品,有利于大規模的工業化生產;本發明方法可促進結晶生長,提高結晶速率和結晶效果,所得產品具有更好的晶體形貌、更高的亮度和穩定性;同時,本發明方法采用特殊的包覆工藝,利用有機包覆試劑對粉體進行包覆,在粉體表面形成一層厚度可控的致密的吸附層,形成核-殼結構,即主體熒光粉作為核,包覆試劑作為殼的結構,改變了熒光粉顆粒表面狀態,可有效解決固體顆粒的團聚問題,獲得了分散性能和耐高溫高濕性能均良好的熒光粉產品。附圖說明圖1是本發明實施例2所制備的K1.8Cu0.1Si0.95F6:0.05Mn4+熒光粉的發射光譜圖。圖2是本發明實施例2所制備的K1.8Cu0.1Si0.95F6:0.05Mn4+熒光粉的掃描電鏡圖。圖3是本發明實施例2所制備的K1.8Cu0.1Si0.95F6:0.05Mn4+熒光粉的XRD圖。圖4是本發明實施例1、實施例2制得的產品和對比例1、對比例2的產品熱猝滅曲線圖。圖5是本發明雙85實驗中實施例1、實施例2和對比例1、對比例2的內量子效率變化曲線圖。圖6是本發明雙85實驗中實施例1、實施例2和對比例1、對比例2的X色坐標變化曲線圖。具體實施方式本發明提供了一種耐高溫高濕的氟化物紅光熒光粉,該熒光粉的化學通式為KmAnM1-xF6:xMn4+;通式中,A為Cu、Ba、Zn中的一種或兩種;M為Ti、Si、Ge中的至少一種;m+2n=2,且0.05≤n≤0.2,1.6≤m≤1.9;0<x<0.2,優選地,0.02≤x≤0.15,更優選地x=0.05;在所述熒光粉的粉體表面包覆有硅酸鉀-羥甲基纖維素鈉-聚乙二醇混合物。本發明所提供的耐高溫高濕氟化物紅光熒光粉的制備方法為:粉體的制備:將M的氧化物加到20~60wt%的氫氟酸溶液中,待固體全部溶解后,向上述溶液中繼續加入KF、AF2、KMnO4和K2MF6基質,向溶液中逐滴滴加20~40wt%的過氧化氫溶液,待溶液變色后停止滴加,整個過程在100~1000r/min的攪拌下進行,停止滴加過氧化氫溶液后,將反應物在0~200℃下干燥0~72h,干燥完畢后取出濾餅,研磨破碎過100目篩后即得到KmAnM1-xF6:xMn4+固體產物。粉體的包覆:按照硅酸鉀∶羥甲基纖維素鈉水溶液(CMC-Na)∶聚乙二醇水溶液(PEG)=1g∶10~20mL∶5~30mL的比例分別量取質量分數為1~5%的CMC-Na、質量分數為2~10%的PEG,并于室溫下攪拌充分溶脹,加入硅酸鉀,攪拌0.5~1h形成混合溶膠。按照1g∶5~100mL的固液比稱取所得KmAnM1-xF6:xMn4+固體產物,加到相應量的上述混合溶膠中,室溫下攪拌0.5~1h,用頻率為15KHz~35KHz的超聲波進行分散,同時輔以攪拌,攪拌速率為100r/min-1000r/min,攪拌0.5~5h后,對所得混合物進行抽濾,抽濾過程中,用醇類試劑對粉體進行洗滌,抽濾結束后,將濾餅放置在真空干燥箱中,于50~250℃下干燥0~72h,即得到核-殼結構的氟化物紅光熒光粉。下面結合具體實施例進一步闡述本發明,在以下各實施例中,未詳細描述的各種過程和方法是本領域中公知的常規方法,所用試劑為市售分析純或化學純。實施例1:K1.8Cu0.1Si0.95F6:0.05Mn4+熒光粉的制備。將10gSiO2加到100mL40wt%氫氟酸溶液中,將聚四氟乙烯燒杯置于25℃水浴中,固體全部溶解后,向該溶液中繼續加入1.8gKF、2gCuF2、14gKMnO4和10gK2SiF6,向溶液中逐滴滴加30%的過氧化氫溶液,溶液變為金黃色后停止滴加,整個過程在100r/min的攪拌下進行,停止滴加過氧化氫溶液后,將反應物在25℃下靜置2h后再將產生的沉淀過濾,用乙醇洗滌三次,將濾餅置于真空干燥箱中,于70℃下干燥1h,干燥完畢后取出濾餅,研磨破碎過100目篩后即得黃色的K1.8Cu0.1Si0.95F6:0.05Mn4+熒光粉。在顯微鏡下觀察,得到的熒光粉為一種形貌規則的透明晶體,在藍光熒光顯微鏡下,發射出紅光,經光譜檢測,其半峰寬為2.8nm。實施例2:K1.8Cu0.1Si0.95F6:0.05Mn4+熒光粉的包覆。量取質量分數為1%的CMC-Na10mL,量取5%的PEG10mL,并于室溫下攪拌充分溶脹,將1g硅酸鉀加入上述混合溶液,攪拌30min形成混合溶膠。稱取實施例1中制備的熒光粉2g加到上述溶膠中,室溫下攪拌30min,用頻率為20KHz的超聲波進行分散,同時輔以攪拌,攪拌速率為110r/min,攪拌1h,對其進行抽濾,抽濾過程中,用乙醇進行洗滌,抽濾結束后,將濾餅放置在真空干燥箱中,于70℃下真空干燥2h,即得到核-殼結構的氟化物紅光熒光粉。經包覆后的熒光粉為一種微黃色晶體,在掃描電鏡下可看到表面包覆的絨毛狀物質,如圖2所示,該熒光粉的晶粒粒徑為20~35μm,呈六面晶型結構;采用460nm激發光源激發該熒光粉得到的發射光譜如圖1所示,其發射峰值為631.8nm,半峰寬為2.8nm;該熒光粉的X射線衍射圖如圖3所示;采用熒光光譜儀測得該熒光粉的內量子效率為98%。對比例1:根據文獻CN105038776A制備K2SiF6:Mn4+熒光粉。稱取30gKHF2,溶解于100mL40wt%的氫氟酸中,加入1.5gKMnO4,待全部溶解后,將聚四氟乙烯燒杯置于冰鹽水浴中,冷卻至20℃下,溫度達到要求后逐滴加入30wt%的H2O2,直至紫色溶液變成金黃色時停止滴加,滴加過程中析出沉淀物,然后過濾,研磨破碎即得到K2MnF6。稱取10mL35wt%H2SiF6加入60mL49wt%的氫氟酸中,然后加入0.6g合成的K2MnF6作為第一溶液,將4.9gKHF2溶解在15mL49wt%的氫氟酸中作為第二溶液,待第一溶液由最開始的明亮黃色變為棕色后,控制溫度在20℃以下,開始逐滴滴加第二溶液,滴加完畢后,攪拌反應30min,棕色溶液顏色變淡并有沉淀物析出,過濾沉淀物,并用丙酮洗滌三次,然后置于100℃烘箱中干燥30min。將干燥后的粉末置于體積比VETOH:VHCl=10:1的溶液中處理10min,然后過濾,丙酮洗滌三次,再次在100℃烘箱中干燥30min,得到外觀呈深黃色的晶體粉末。稱取正硅酸乙酯13.8g,溶解于15mL無水乙醇中,并向溶液中加入1.2mL去離子水,0.5mL49%的氫氟酸,攪拌水解1h,然后加入0.5mL七氟丁酸,繼續水解縮合1h。稱取5g制得的K2SiF6:Mn4+晶體粉末加入水解液中,充分攪拌30min后,用無水乙醇洗滌三次,然后放置于100℃烘箱中烘干1h,之后再將樣品置于250℃烘箱中烘干1h,將烘干后的樣品研磨破碎分散,將分散物過80目篩即得無機材料SiO2包覆的K2SiF6:Mn4+熒光粉。對比例2:根據文獻CN105505384A中公布的燒結法制備K1.8Cu0.1Si0.95F6:0.05Mn4+熒光粉。按照通式K1.8Cu0.1Si0.95F6:0.05Mn4+中各元素的化學計量比,分別稱取1.8摩爾的KF,0.95摩爾的SiO2,0.05摩爾的MnO2,4摩爾的NH4F,0.1摩爾的CuF2,并加入3%wt的AlF3作為助劑,將所稱取的所有原料置于剛玉研缽中混合均勻,混料時間一般不少于0.5h,整個混合過程需在通風櫥中進行。將混合好的原料放入鉬坩堝中壓實,并將坩堝放入燒結爐中。在燒結爐中通入F2和N2的混合氣體作為保護氣氛,其中F2和N2的體積比為10:90;以10℃/min的升溫速率升至760℃,于760℃下進行燒結,保溫時長(即燒結時長)為8h。之后再以5℃/min的降溫速率降至100℃,再自然降至室溫,得到燒結產物。將燒結產物取出,經研磨后過50目篩;再用丙醇進行洗滌,并于120℃下干燥1.5h,得到成品熒光粉K1.8Cu0.1Si0.95F6:0.05Mn4+。【熱猝滅測試】:分別對實施例1、實施例2制得的產品和對比例1、對比例2制得的產品進行熱猝滅檢測,檢測溫度從300K到500K,溫度每變化50K測定一次發光強度變化情況,結果見表1和圖4。表1溫度/K對比例1對比例2實施例2(包覆后的)實施例1(未經包覆的)300100.00%100.00%100.00%100.00%350103.00%99.00%101.80%99.50%400105.00%98.50%102.60%98.00%45096.00%88.00%98.80%86.00%50086.00%81.00%89.00%80.00%由上表中的數據以及圖4可以看出,本發明實施例2所得產品的熱猝滅效果明顯優于其他產品。【雙85實驗測試】:分別稱取實施例1、實施例2中所得產品和對比例1、2中所得產品,在溫度為85℃、濕度為85%的環境下進行雙85實驗,間斷進行1000h,以內量子效率和x色坐標為檢測指標,每隔200h檢測一次,測試結果見表2、圖5和圖6。表2由上表中的數據可以看出,本發明實施例2所得產品的穩定性明顯優于對比例1、對比例2所得產品,且經包覆后的產品的耐濕熱性能有很大提高。實施例3~13制備方法與實施例1相同,不同之處在于改變了氫氟酸溶液的濃度、反應溫度,并采用實施例2的方式對粉體進行包覆。對實施例3~13所得產品進行相關性能測試,所得結果見表3,表中,QE代表內量子效率,Cx、Cy代表色度參數。表3實施例14~20制備方法與實施例1相同,并采用實施例2的方式對粉體進行包覆。不同之處在于改變了對粉體進行包覆所用的羥甲基纖維素鈉的有機混合溶膠的比例。包覆結束后對粉體進行相關性能測試,所得性能參數見表4。表4實施例硅酸鉀:CMC-Na∶PEG(g:mL:mL)發光強度D50實施例21:10:1011020μm實施例141:10:511318μm實施例151:10:1510821μm實施例161:10:3010523μm實施例171:15:1010821μm實施例181:20:1010521.5μm實施例191:20:1510524μm實施例201:20:3010328μm實施例21~27制備方法與實施例1相同,并采用實施例2的方式對粉體進行包覆。不同之處在于改變了熒光粉體與羥甲基纖維素鈉的有機混合溶膠的固液比(g/mL)。對實施例21~27所得產品進行相關性能測試,所得性能參數見表5。表5實施例G:M(g/mL)發光強度D50實施例21:1011020μm實施例211:511518μm實施例221:2010821μm實施例231:4010523μm實施例241:6010325μm實施例251:8010526μm實施例261:9010328μm實施例271:10010130μm實施例28將17.4gGeO2加入100mL40wt%氫氟酸溶液中,將聚四氟乙烯燒杯置于25℃水浴中,固體全部溶解后,向該溶液中繼續加入1.8gKF、2gCuF2、14gKMnO4和13gK2GeF6,向溶液中逐滴滴加30%的過氧化氫溶液,溶液變為金黃色后停止滴加,整個過程在100r/min的攪拌下進行,停止滴加過氧化氫溶液后,將反應物在25℃下靜置2h后將產生的沉淀過濾,用乙醇洗滌三次,將濾餅置于真空干燥箱70℃干燥1h,干燥完畢后取出濾餅,研磨破碎過100目篩后即得黃色的K1.8Cu0.1Ge0.95F6:0.05Mn4+熒光粉。量取質量分數為1%的CMC-Na10mL,量取5%的PEG10mL,并于室溫下攪拌充分溶脹,將1g硅酸鉀加入上述混合溶液,攪拌30min形成混合溶膠。稱取實施例1中制備的熒光粉2g加到上述溶膠中,室溫下攪拌30min,用頻率為20KHz的超聲波進行分散,同時輔以攪拌,攪拌速率為110r/min,攪拌時長1h后,對其進行抽濾,抽濾過程中,用乙醇進行洗滌,抽濾結束后,將濾餅放置在真空干燥箱中70℃真空干燥2h,即得到核-殼結構的氟化物紅光熒光粉。實施例29~43制備方法與實施例28相同,所不同的是制備的熒光粉結構式有所改變。對實施例29-43進行相關性能測試。所得性能參數見表6。表6【雙85實驗測試】分別稱取實施例39所制得的包覆前后的K1.8Ba0.1Si0.95F6:0.05Mn4+熒光粉粉體各10g,在溫度為85℃、濕度為85%的環境下進行雙85實驗,間斷進行1000h,以內量子效率和x色坐標為檢測指標,每隔200h檢測一次,測試結果見表7。表7由上表可以看出,包覆后的熒光粉分體的穩定性優于未經包覆的熒光粉粉體。當前第1頁1 2 3