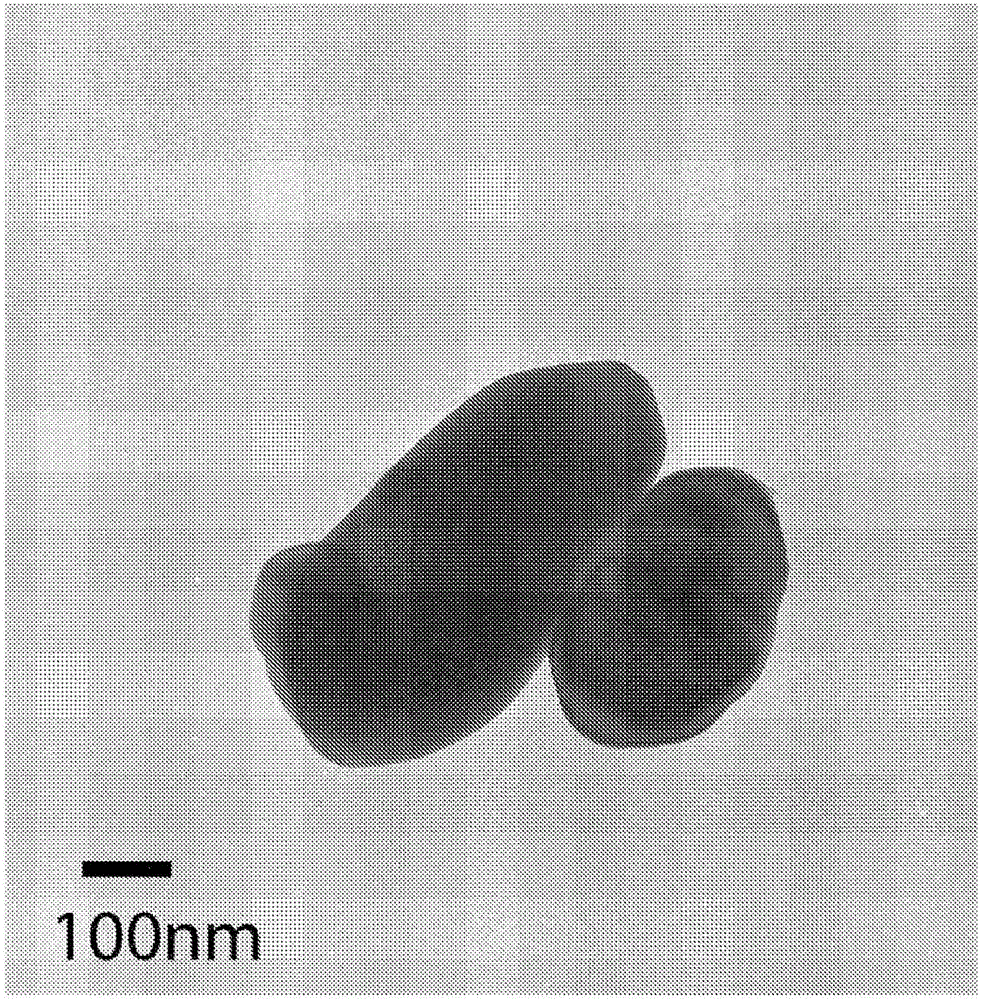
本發明涉及用于生產二氧化鈦顏料產品的方法。特別地,所述方法涉及包含含有顏料的二氧化鈦顆粒的二氧化鈦顏料產品的生產,其適合于在具有優良耐久性的涂料或油墨的制備中使用。本發明的方法允許在不需要干燥步驟的情況下生產這樣的產品。因此,所述方法是能量和成本更高效的。
背景技術:
:通常認為二氧化鈦(TiO2)作為商業中主要的白色顏料。其具有異常高的折射率、可忽略的顏色并且還是惰性的。二氧化鈦通常以兩種主要多晶型體之一(銳鈦礦或金紅石)存在于市場中;對于大多數商業應用,金紅石是所需要的形式。二氧化鈦以可用作涂料、紙張、塑料、陶瓷、油墨等中的乳濁劑而聞名。商業銷售的二氧化鈦通常具有150nm至350nm的平均顆粒尺寸。存在兩種用于制作原始的含有顏料的二氧化鈦的主要工藝:硫酸鹽工藝和氯化物工藝。硫酸鹽工藝基于鈦鐵礦或鈦渣在濃硫酸中的溶出。在鐵作為硫酸鐵去除之后,將溶液加熱并用水稀釋。鈦水解形成含氧硫酸鈦沉淀,其經進一步處理以生產TiO2顏料。氯化物工藝依賴于低鐵的含有鈦的礦石或中間產物的碳氯化形成TiCl4,然后是TiCl4的氣相氧化。通過調節分散體的pH能夠從含有二氧化鈦的分散體中使二氧化鈦絮凝和/或沉淀出來。用于通過任何已知方法獲得的二氧化鈦的精加工工藝,可以包括以下的一種或多種:干法研磨、濕法研磨、分類、過濾、洗滌、干燥、蒸汽微粒化和包裝。通常,在商業工藝中將總是研磨和微粒化二氧化鈦分散體以實現所需要的顆粒尺寸分布。任選地可以存在表面處理步驟。表面處理步驟通常包括將氧化鋁、氧化硅、氧化鋯、和/或其他金屬氧化物沉淀在二氧化鈦的表面上。此涂覆處理的目的是給予光穩定性、保存期、分散性和/或流動性。此步驟通常發生在濕法研磨步驟之后和干燥步驟之前。常見的是將二氧化鈦研磨、表面處理并且然后干燥。認為在表面處理之后的干燥步驟是確保涂層充分地凝結至顆粒上并且具有所需的活性水平。在本領域中通常優選精加工工藝包含:研磨;然后是任何所需的表面處理步驟,例如金屬氧化物涂覆;然后是過濾和/或洗滌;然后是干燥;并且然后是微粒化,以獲得具有所需要的顆粒分布的最終二氧化鈦白色顏料產品。處理和干燥產品的步驟能夠引起顆粒聚集。隨后的微粒化步驟確保在干燥的處理的產品中的顆粒是分開的,使得恢復所需要的顆粒尺寸分布。因此照慣例,總是將二氧化鈦微粒化以便產生適合于作為在涂料、油墨或類似物中使用的白色顏料的所需要的顆粒尺寸分布,其中在涂料或油墨的制備過程中機械能輸入低。在涂料或其他含顏料的產品中的顆粒尺寸分布確定通過含顏料的產品實現的遮蓋力。平均顆粒尺寸(當使用BrookhavenBI-XDCWX射線盤式離心機系統或OD方法確定時)應該位于從0.29至0.32微米的范圍內,且有小于1.45的幾何標準差。如技術人員將意識到的,將顆粒尺寸分布作為對數正態分布建模。可以如下確定使用BrookhavenBI-XDCWX射線盤式離心機系統(XDC)的顆粒尺寸分布測量:將干燥的TiO2材料(0.92g)與1/16%硅酸鈉溶液(16.80g)及去離子水(5.28g)在Bosch研磨罐中混合以產生~4%固體的稀懸浮液。用兩滴氫氧化鈉溶液(2%)將pH調節至10和10.5之間。然后使用Bosch高速旋轉混合器將樣品劇烈研磨10分鐘。設計此方法以代表在大多數的涂料和油墨的生產中使用的機械能。可以如下確定使用OD(光學密度)方法B的顆粒尺寸分布測量:將干燥的TiO2材料(0.92g)與1/16%硅酸鈉溶液(16.80g)及去離子水(5.28g)在Bosch研磨罐中混合以產生~4%固體的稀懸浮液。用兩滴氫氧化鈉溶液(2%)將pH調節至10和10.5之間。然后使用Bosch高速旋轉混合器將樣品劇烈研磨10分鐘。設計此方法以代表在大多數的涂料和油墨的生產中使用的機械能。然后將分散體稀釋至例如用于避免多重散射的濃度。然后使用UV/Vis分光計在一系列波長處測量此稀釋的分散體的光學密度。將這些測量值與在這些波長處使用Mie理論計算的球形顆粒的對數正態分布所預計的光學密度對比。在實驗結果和理論結果之間的最佳擬合給出幾何體積平均顆粒尺寸(PS(OD)或OD顆粒尺寸)和幾何標準差(GSD(OD))。還可以需要顆粒尺寸分布不具有長的“尾部(tail)”,換句話說,不存在顯著量的大尺寸顆粒。例如,通常需要90重量%或更多的顆粒應該具有小于0.5微米的顆粒尺寸。大于0.5微米的高濃度顆粒將對涂料或油墨的光澤有害。使用X射線沉積能夠確定顆粒尺寸直徑。理想地,還是99重量%或更多的顆粒具有小于1.5微米的顆粒尺寸直徑(當使用X射線沉積確定時)的情況。如上指出,處理和干燥產品的步驟能夠引起顆粒聚集,這意味著在傳統二氧化鈦顏料制備途徑中通常需要流體能量研磨(微粒化),以便將顆粒回復至所需要的尺寸。否則,當隨后將最終產品分散(例如通過高速分散)在載色劑中例如形成涂料或油墨時,含有二氧化鈦顆粒的所得產品將不具有所需要的尺寸分布但是反而將具有過高水平的尺寸過大的顆粒。在流體能量研磨機(或微粒機)中進行流體能量研磨。大多數流體能量研磨機在以下基礎構造上變化:由兩個通常平行的限定軸壁的圓形板和確定外圍壁的環形邊緣封閉而成的盤形研磨室,且該室的軸向長度或高度基本上小于直徑。圍繞研磨機的周長設置有許多間隔一致的用于注入研磨流體的噴口,其連同用于供給待粉碎的粒狀材料的供給噴嘴一起供應用于粉碎的額外能量。使噴口取向,使得將研磨流體和粒狀材料切向地注入至小于室周長的圓的周長。能夠通過與研磨室成切向的側進口或以與頂部成角度(通常與研磨室的平面成30°角)引入向研磨室的供給。側供給微粒機通常產生較好的研磨分散體,而頂部供給微粒機能夠產生較高速率。在研磨室內,通過研磨流體(例如壓縮氣)經過供給進口或經過位于圍繞研磨室外圍的環形構造中的流體噴嘴的引入來形成漩渦。切向地供給至室外圍中的研磨流體(壓縮氣,例如空氣、蒸汽、氮等)當其在研磨室內移動時形成高速漩渦。高速漩渦掃起粒狀材料,其導致高速顆粒與顆粒碰撞以及與研磨室壁的內部分的碰撞。在二氧化鈦的微粒化中,研磨流體通常是過熱蒸汽。清楚地,較重的顆粒具有在漩渦內較長的停留時間。較輕的顆粒隨著氣體漩渦移動直至到達排出導管。典型地,流體能量研磨機能夠產生細小的(小于10微米直徑)和超細小的(小于5微米直徑)顆粒。然而,在研磨過程中,有時依然能夠發現不需要地大的顆粒尺寸逸入產品中。通常,在白色顏料產業中,特別需要降低過早地進入所得的顏料產品中的尺寸過大材料的量。因此與將其他產品微粒化時對比,在微粒化過程中研磨的強度典型地增加。其具有就流體使用、能量消耗和每個研磨機降低的容量而言的較高成本的后果。進一步,采用這樣的工藝,可以降低尺寸過大材料的量,但是可以存在對顏料性質的不利影響。特別的關注在于傳統的顏料精加工工藝是高度能量密集的工藝。在精加工中最高的能量消耗操作通常是使用過熱蒸汽的干燥產品的流體能量研磨。一旦獲得具有所需要的顆粒尺寸分布的最終二氧化鈦白色顏料產品,就通常將其再制漿。通常,提供的商業產品是處于含水分散體的形式的二氧化鈦白色顏料產品。這將一般為相對濃縮的分散體,并且可以被稱為顏料濃縮物。本發明提供用于獲得這樣的顏料濃縮物的改進方法。技術實現要素:在一方面,本發明提供用于制備二氧化鈦產品的方法,其包含以下步驟:-提供包含二氧化鈦顆粒的分散體,其中分散體含有從50g/l至600g/l的TiO2;并且然后,以任何順序,-向二氧化鈦顆粒施加無機涂層,同時在涂覆步驟之前和/或在涂覆步驟過程中采取一個或多個步驟以維持膠體穩定性;-濃縮分散體:通過使分散體經受橫流式過濾的作用并且持續橫流式過濾工藝直至分散體處于含有800g/l或更多TiO2的濃縮形式;從而提供處于涂覆顆粒的濃縮分散體形式的二氧化鈦產品。此方法的好處是不存在二氧化鈦顆粒的干燥。在該方法的全部步驟過程中,顆粒保持處于濕的形式,即處于分散。避免顆粒的干燥具有降低成本的好處,因為不需要與傳統的干燥工藝相關的加熱。另外,如上指出,包含處理和干燥產品的傳統工藝能夠引起顆粒聚集,這意味著在傳統二氧化鈦顏料制備途徑中通常需要流體能量研磨(微粒化)。因此避免顆粒的干燥具有避免初始發生的聚集。本發明的方法中使用的涂覆步驟還不會導致顆粒的聚集,因為在實施涂覆時維持了膠體穩定性。因此避免對能量密集的微粒化步驟的需要,并且因此該方法是能量和成本更高效的。在本領域中存在傾向:為了最終二氧化鈦產品具有足夠的耐久性以便適合于在涂料或油墨的制備中使用,需要將涂層干燥至顆粒上。因此看上去涂覆和干燥是必要的。因此以下是傳統的:將降低光催化活性的涂層施加至在處于初始的分散體形式時的顆粒,并且然后將顆粒干燥以便通過將涂層凝結至顆粒上來提供有效的表面處理,從而賦予那些顆粒耐氣候性。這樣的降低二氧化鈦的光催化活性(因此當所述產品經受太陽輻射時延長其中納入二氧化鈦的含有顏料的產品的使用期)的表面處理在本領域中是眾所周知的。出人意料地,在本發明的方法中使用的表面處理提供在二氧化鈦顆粒上有效降低二氧化鈦的光催化活性的涂層,因此賦予其中納入二氧化鈦的含有顏料的產品(例如涂料或油墨)優良的耐久性,即使從來沒有干燥此涂層。當二氧化鈦顆粒處于分散體的形式時進行表面處理,并且在處理之后任何時刻不存在干燥二氧化鈦顆粒的要求。因此在表面處理和獲得顏料濃縮物(其為處于涂覆顆粒的濃縮分散體形式的二氧化鈦產品)之間不存在干燥步驟。換句話說,從提供包含二氧化鈦顆粒的分散體的初始步驟直至獲得適合于在涂料和油墨中使用的最終二氧化鈦產品的步驟,二氧化鈦顆粒保持處于分散體的形式。因此在不需要干燥的情況以及不需要隨之發生的微粒化的情況下可獲得適合于在涂料或油墨中使用的顏料濃縮物。因此該方法是能量和成本更高效的。如通過該方法獲得的適合于在涂料或油墨中使用的顏料濃縮物可以容易分散在載色劑中以給出包含二氧化鈦顏料的含有顏料的產品(例如涂料或油墨產品)。二氧化鈦顏料具有降低的光催化活性,并且因此含有顏料的產品具有優良的耐久性。換句話說,甚至當含有顏料的產品經受太陽輻射時,含有顏料的產品的使用期仍是優良的。在一個實施方案中,隨后將所獲得的顏料濃縮物分散在載色劑中,以提供包含分散在所述載色劑中的含有顏料的二氧化鈦顆粒的含有顏料的產品,例如涂料或油墨產品。分散體可以是通過機械攪拌或手動攪拌、或通過高速分散、或通過任何其他合適的方式。對于待實現的分散體不存在特別要求;在本發明的方法中,在不需要施加任何顯著力的情況下容易使顏料顆粒分散。因此可以使用本發明的方法以獲得具有優良的耐久性的含有顏料的產品,例如涂料或油墨產品。附圖說明圖1為顯示以微米計的顆粒尺寸(使用光學密度方法確定)和以mS/cm計的電導率值的圖表,其在用于制備如實施例1中描述的根據本發明具有兩個致密氧化硅涂層的金紅石氧化鈦顆粒的方法過程中進行記錄。圖2為顯示在氧化硅涂層的施加之前在實施例1中使用的金紅石氧化鈦晶體的電子顯微照片。圖3為顯示在氧化硅涂層的施加之后實施例1的金紅石氧化鈦晶體的電子顯微照片。發明詳細說明在本發明的方法中初始提供包含二氧化鈦顆粒的分散體。在此分散體中存在從50g/l至600g/l的TiO2,例如從50g/l至500g/l的TiO2;例如可以存在從100g/l至600g/l的TiO2、或從100g/l至550g/l的TiO2、或從150g/l至550g/l的TiO2、或從150g/l至500g/l的TiO2。在一個實施方案中,在初始的分散體中存在從200g/l至500g/l的TiO2,例如從200g/l至450g/l的TiO2、或從250g/l至450g/l的TiO2、或從250g/l至400g/l的TiO2、或從300g/l至400g/l的TiO2。設想在初始的分散體中的TiO2的濃度范圍用于上面提到的各種下限和上限的全部可能的結合。分散體可以任選地被稀釋或可以被濃縮以提供具有二氧化鈦顆粒的所述濃度的分散體。如下更詳細地討論的,可以通過任何傳統的步驟獲得包含二氧化鈦顆粒的分散體。通常,獲得二氧化鈦顆粒的初始分散體是標準的并且沒有被本發明改變。作為本領域中傳統的,考慮到二氧化鈦的預期用途(例如作為在涂料或油墨中的顏料)及因此就尺寸等而言的顆粒的相關特性將獲得分散體。其中提供二氧化鈦顆粒的分散體中的液體載體優選為極性的。在一個實施方案中,液體載體是含水的;其可以是水或含水溶液。然而還可考慮用于顆粒的其他極性載體,例如它們可以選自極性有機溶劑或醇類。液體載體還可以是兩種或更多種極性載體的混合物,例如其可以是水和醇的混合物。在本發明的方法中將無機涂層施加至二氧化鈦顆粒。可以在通過橫向過濾(cross-filtration)將分散體濃縮之前或在通過橫向過濾將分散體濃縮之后施加此涂層。因此將二氧化鈦顏料顆粒表面處理從而用無機材料涂覆。施加處理以降低二氧化鈦的光催化活性,因此當產品經受太陽輻射時延長其中納入二氧化鈦的含有顏料的產品的使用期。技術人員將知道用于二氧化鈦顆粒的這樣的表面處理在本領域中是已知的。然而,如上指出,傳統地認為這樣的處理需要隨后的干燥步驟以實現有效的涂層。與此相反,在本發明中,在處理之后沒有干燥涂覆的顆粒。在本發明中確定,當在涂覆步驟過程中維持膠體穩定性的同時施加涂層時,能夠在不需要隨后干燥步驟的情況下實現有效的涂層。適合于使用的涂覆劑包括無機氧化物與水合氧化物。一般地使用這些材料將無機氧化物或水合氧化物涂覆至顆粒的表面上。可以提及的用作涂覆劑的典型無機氧化物與水合氧化物包括硅、鋁、鈦、鋯、鎂、鋅、鈰、磷或錫的一種或多種氧化物和/或水合氧化物。例如,涂覆劑可以是Al2O3、SiO2、ZrO2、CeO2、P2O5、硅酸鈉、硅酸鉀、鋁酸鈉、氯化鋁、硫酸鋁、或其混合物。還可以提及硅酸。涂層可以是致密的或非致密的。例如,可以使用致密或非致密的氧化硅涂層和/或可以使用致密或非致密的氧化鋁涂層。在一個實施方案中,涂覆劑包含以致密形式施加的二氧化硅。在一個這樣的實施方案中,涂層包含如在US2885366中描述的類型的致密氧化硅涂層。可以僅施加一層涂層,或可以施加多于一層的涂層(例如兩層或三層)。當施加多于一層的涂層時,每層可以是相同的或不同的。在一個實施方案中,僅添加一層致密的氧化硅涂層。在另一個實施方案中,添加兩層致密的氧化硅涂層。在另一個實施方案中,添加一層致密的氧化硅涂層和一層致密的氧化鋁涂層。在一個實施方案中存在用于涂覆顆粒的兩種或更多種涂層材料。可以同時地在單個操作中施加或連續地施加這些涂層。如果同時施加,可以組合使用不同的涂層材料以產生單一層。如果接連施加,可以分別地使用不同的涂層材料以產生兩個或更多個層,每層具有不同的組成。例如,在一個實施方案中,用氧化硅(例如致密的氧化硅)涂覆顆粒以產生一層并且還用氧化鋯涂覆以產生另一層。涂覆在二氧化鈦的表面上的涂層的量可以為涂層(例如無機氧化物和/或水合氧化物)相對于二氧化鈦的總重量的約0.1重量%至約20重量%。在一個實施方案中涂覆劑的量為相對于二氧化鈦的總重量的約0.1至約15重量%或約0.1至約10重量%。例如,可以用處于至多約7重量%水平的涂覆劑涂覆顆粒,例如從約0.1重量%至約7重量%,或例如從約0.5重量%至約7重量%,或例如從約0.5重量%至約6重量%,或例如從約1重量%至約6重量%(相對于二氧化鈦的總重量)。可以用處于從約0.1%重量至約5重量%水平的涂覆劑涂覆顆粒,或例如從約0.5重量%至約5重量%,并且特別地從約1重量%至約5重量%(相對于二氧化鈦的總重量)。在本發明中,當提及在二氧化鈦顆粒上涂層的添加水平時,其作為w/w量給出,即添加的涂層材料的總重量相對于處理的二氧化鈦顆粒的總重量。例如因此當考慮了氧化硅涂層,可以說“SiO2的添加水平對TiO2是1.5%w/w”。通過將涂層材料添加至分散體或通過將分散體添加至涂層材料,涂層材料可以用于處理在提供的分散體中的二氧化鈦顆粒。優選地,使用本領域中已知的傳統混合裝置進行涂層材料和分散體的混合。可以進行混合持續任何合適長度的時間,例如1分鐘或更長、2分鐘或更長、3分鐘或更長、4分鐘或更長、或者5分鐘或更長。可以進行混合持續不多于3小時,例如不多于2小時、例如1小時或更短。在一個實施方案中進行混合持續從5分鐘至1小時,例如從10分鐘至45分鐘、例如從20分鐘至40分鐘。在一個實施方案中,可以施加涂層如下:將包含二氧化鈦的顆粒的含水分散體引入用于攪拌的槽內。然后調節分散體的溫度(例如到75至90℃)并且調節其pH(例如至約10.5)。然后將涂層材料以足夠產生所需要的涂層的量引入攪拌的槽內。例如為了產生1重量%致密的氧化硅涂層,在30分鐘周期內添加1%氧化硅(對二氧化鈦的%wt/wt)至攪拌的槽并且然后混合30分鐘;同時為了產生3重量%致密的氧化硅涂層,以相同的方式添加3%氧化硅(對二氧化鈦的%wt/wt)。在一個實施方案中,可以將氧化硅以作為涂層材料的硅酸鈉的形式添加至攪拌的槽。例如通過將硫酸添加至攪拌的槽,調節pH以將致密的氧化硅涂層沉淀至顆粒上。在一個特別的實施方案中,在60分鐘周期內添加硫酸以使pH達到約8。技術人員將當然意識到根據需要此方法能夠容易被改變以添加不同量的涂層。本發明不在于涂層自身的施加;在本領域中這樣的涂層已經是已知的并且能夠容易地實施。在本發明的方法中實現所述涂層同時維持二氧化鈦顆粒在分散體內的膠體穩定性。這是本發明的關鍵方面。如技術人員將意識到的,這能夠通過控制因素(例如分散體中的電解質濃度和分散體的pH)來實現。可以在開始涂覆工藝之前采取步驟以維持膠體穩定性和/或可以在涂覆過程中采取步驟;例如在第一涂層和第二涂層的施加之間。在一個實施方案中,通過控制以下因素中的一個或多個來實現涂層同時維持二氧化鈦顆粒在分散體內的膠體穩定性:(a)在涂覆步驟之前或在涂覆步驟過程中降低分散體中的電解質濃度;(b)降低在涂覆步驟過程中添加的可溶性鹽的水平;(c)在涂覆步驟之前或在涂覆步驟過程中添加空間穩定劑;(d)在涂覆步驟之前或在涂覆步驟過程中調節分散體的pH離開二氧化鈦的等電點;(e)通過在涂覆步驟之前或在涂覆步驟過程中分散劑的添加,調節二氧化鈦的等電點離開所述分散體的pH。在這點上,膠體穩定性需要在碰撞顆粒之間的排斥力。然而,在水或其他溶劑中的二氧化鈦顆粒自然地相互吸引。在顆粒上的電荷導致屏蔽此吸引的靜電排斥力。如果將存在膠體穩定性,這樣的靜電排斥因此是所需要的。此靜電排斥的強度取決于具有高表面電荷及低電解質濃度;在高電解質濃度下靜電力的范圍降低并且因此吸引力的屏蔽不太有效。通過H+離子/OH-離子的吸附確定二氧化鈦顆粒上的表面電荷;因此通過其中分散有顆粒的溶液的pH來影響顆粒上的凈表面電荷。在某一pH(所述等電點)下顆粒將不攜帶凈電荷(并且將不存在靜電排斥力);當pH從此pH向上增加時,顆粒將越來越多地變成帶負電荷的并且膠體穩定性將改進。相似地,當pH降低時,顆粒將越來越多地帶正電荷并且膠體穩定性將改進。(a)在涂覆步驟之前或在涂覆步驟過程中降低分散體中的電解質濃度分散體中的電解質(鹽)的濃度影響發生絮凝的程度。因此在一個優選實施方案中,在涂覆步驟之前或在涂覆步驟過程中降低分散體中的電解質濃度。優選地其在開始涂覆步驟之前降低。如果存在施加大于一層涂層,則任選地其可以在施加這些涂層之間降低。通過使用滲濾合適地降低分散體中的電解質濃度。在本領域中此超濾膜技術是眾所周知的。其包含使用小分子可透過的過濾器去除可透過的分子(如鹽)。所述工藝選擇地使用多孔膜過濾器以基于溶液和懸浮液的組分的分子尺寸將它們分離。較小的分子例如鹽自由通過超濾膜,該超濾膜擋住較大分子。可以使用超濾裝置(例如Axium250L“超濾中試設備”)實現滲濾。選擇合適的膜(例如具有6.6m2的膜面積的“KochSUPER-”管狀膜)確保以去除相關的電解質。在一個實施方案中,分散體電導率降低0.5mS/cm或更高,例如1mS/cm或更高、或1.5mS/cm或更高、或2mS/cm或更高,例如2.5mS/cm或更高。換句話說,此為作為處理(例如滲濾)結果出現的分散體電導率的下降。因此其通過從處理之前分散體電導率減去處理之后分散體電導率來計算。在一個實施方案中,降低分散體電導率使得處理之后(例如在滲濾之后)分散體電導率為5mS/cm或更低,例如4.5mS/cm或更低、或4mS/cm或更低、或3.5mS/cm或更低。可以降低分散體電導率至處于3mS/cm或更低的水平,例如2.5mS/cm或更低、或2mS/cm或更低、或1.5mS/cm或更低,例如其可以為從0.1至2mS/cm或從0.5至1.5mS/cm。在一個實施方案中,降低分散體電導率使得在施加涂層之前分散體電導率為5mS/cm或更低,例如4.5mS/cm或更低、或4mS/cm或更低、或3.5mS/cm或更低、或3mS/cm或更低,例如2.5mS/cm或更低、或2mS/cm或更低、或1.5mS/cm或更低。可以任選地在維持分散體電導率在5mS/cm或更低的水平的同時施加涂層。在一個實施方案中,降低分散體電導率使得在施加涂層之前分散體電導率為從0.05至3mS/cm,例如從0.1至2.5mS/cm,例如從0.15至2mS/cm,或從0.2至1.5mS/cm,或從0.25至1mS/cm。甚至允許在無機材料的單一涂覆過程中電解質水平的增加,使用這些水平將確保分散體電導率維持在對于顆粒足夠保留膠體穩定性的水平。如上指出,如果施加多于一個無機材料涂層,可需要在這些涂覆層的施加之間降低分散體電導率。換句話說,在一個實施方案中在施加每個涂覆層之前存在分散體電導率的降低。每個降低可以低至上面指出的水平。然而,每個降低不需要是相同的;在每個涂層施加開始之前將可能達到不同水平的分散體電導率。如技術人員將意識到的,通過確定兩個電極之間的溶液電阻來測量溶液的電導率。這在室內溫度和壓力下使用電導率儀測量。大范圍的這樣的儀器是可商購的。(b)降低在涂覆步驟過程中添加的可溶性鹽的水平在分散體中的電解質(鹽)的濃度影響發生絮凝的程度。鹽的一個來源能夠來自涂覆劑自身。能夠通過添加低水平的處于鹽形式的涂覆劑降低在涂覆過程中添加的可溶性鹽的水平。因此能夠通過使用處于鹽(例如硅酸鈉)形式的涂覆劑但利用相對低水平的涂覆劑來降低在涂覆步驟過程中添加的可溶性鹽的水平。因此在一個實施方案中用處于以下水平的涂覆劑涂覆顆粒:至多約4重量%,例如從約0.1重量%至約4重量%,或例如從約0.5重量%至約3重量%,或例如從約0.5重量%至約2.5重量%(相對于二氧化鈦的總重量)。在一個優選實施方案中用處于從約0.5重量%至約2重量%水平的涂覆劑涂覆顆粒,例如從約1至約1.5%(相對于二氧化鈦的總重量)。或者或此外,能夠通過選擇不處于鹽形式的涂覆劑來降低在涂覆步驟過程中添加的可溶性鹽的水平。例如可以選擇“活性氧化硅”(硅酸)作為涂覆劑。通過使硅酸鈉向下通過離子交換柱能夠產生“活性氧化硅”。此在本領域中是已知的并且在例如US2885366的實施例21中得到描述。(c)在涂覆步驟之前或在涂覆步驟過程中添加空間穩定劑通過添加空間穩定劑能夠降低絮凝的程度,并且因此能夠維持膠體穩定性。能夠在開始涂覆步驟之前或在發生涂覆步驟的同時添加所述穩定劑。能夠添加的空間穩定劑的實例包括但不限于:聚乙烯吡咯烷酮、聚環氧乙烷、聚丙烯酸及其與聚丙烯酸酯和甲基丙烯酸酯的共聚物、聚甲基丙烯酸及其與聚丙烯酸酯和甲基丙烯酸酯的共聚物、及聚乙烯醇、及其組合。可以以任何合適的量添加空間穩定劑。例如可以使用處于以下水平的空間穩定劑:0.2mg每m2的顆粒表面或更多、例如0.5mg每m2的顆粒表面或更多、及優選地1mg每m2的顆粒表面或更多、例如1.5mg每m2的顆粒表面或更多。在一個實施方案中,可以使用處于以下水平的空間穩定劑:10g每m2的顆粒表面或更少、例如7mg每m2的顆粒表面或更少、及優選地5mg每m2的顆粒表面或更少、例如4.5mg每m2的顆粒表面或更少。可以使用處于以下水平的空間穩定劑:從0.2至10mg每m2的顆粒表面、例如從0.5至7mg每m2的顆粒表面及優選地從1至5mg每m2的顆粒表面。(d)在涂覆步驟之前或在涂覆步驟過程中調節分散體的pH離開二氧化鈦的等電點如上指出,在等電點(約pH5-6)處氧化鈦顆粒將不攜帶凈電荷并且將不存在靜電排斥力;然而隨著pH離開此等電點pH,顆粒將越來越多地變為帶電的并且膠體穩定性將改進。因此通過調節pH,通過添加酸性材料或添加堿性材料,在開始涂覆步驟之前或在涂覆步驟過程中,pH能夠從等電點離開。這將降低絮凝。在一個實施方案中,添加堿性材料以提高pH并且使其從等電點離開。堿例如KOH、NaOH、NH4OH、及中和胺(例如DMAMP、AMP(氨基-2-甲基丙醇)、MEA(單乙醇胺)及DEAE(二乙氨基乙醇))可以適合用來提高pH。然而,技術人員將意識到可以合適地使用具有堿性特性的各種材料并且本發明不受限于堿性材料的選擇。例如pH可以提高至9或更高、例如9.5或更高、尤其10或更高。例如pH可以提高至從9.5至11或從10至10.5的范圍內。或者,添加酸性材料以減小pH并且使其從等電點離開。可以合適地使用酸例如HCl或HNO3來減小pH。然而,技術人員將意識到可以合適地使用具有酸性特性的各種材料并且本發明不受限于酸性材料的選擇。例如pH可以減小至4或更低、例如3.5或更低、尤其3或更低。例如pH可以減小至從2至3.5或從1.5至3的范圍內。(e)通過在涂覆步驟之前或在涂覆步驟過程中分散劑的添加,調節二氧化鈦的等電點離開所述分散體的pH如上指出,在等電點(約pH5-6)氧化鈦顆粒將不攜帶凈電荷并且將不存在靜電排斥力;然而隨著pH離開此等電點pH,顆粒將越來越多地變為帶電的并且膠體穩定性將改進。因此通過調節等電點,在開始涂覆步驟之前或在涂覆步驟過程中,等電點能夠從分散體的pH離開。這將降低絮凝。通過使用分散劑調節等電點在本領域是已知的。一種合適的分散劑是α-羥基羧酸,例如檸檬酸。在一個優選實施方案中,通過控制一個或多個(例如兩個或更多個,或全部三個)的以下因素在維持二氧化鈦顆粒在分散體內的膠體穩定性的同時實現涂層:(a)在涂覆步驟之前或在涂覆步驟過程中降低分散體中的電解質濃度;(b)降低在涂覆步驟過程中添加的可溶性鹽的水平;(c)在涂覆步驟之前或在涂覆步驟過程中添加空間穩定劑。任選地還可以使用因素(d)和/或因素(e)。在一個優選實施方案中,通過控制以下因素在維持二氧化鈦顆粒在分散體內的膠體穩定性的同時實現涂層:(a)在涂覆步驟之前或在涂覆步驟過程中降低分散體中的電解質濃度。任選地還可以使用因素(b)至因素(e)中的一個或多個。例如還可以使用因素(b)和/或因素(c)。在本方法中通過橫流式過濾濃縮分散體。其可以在施加涂層之前或在施加涂層之后進行。在一個實施方案中在施加涂層之前能進行濃縮步驟并且在施加涂層之后能進行濃縮步驟。如技術人員將意識到的,“橫流式”過濾工藝是一種其中分散體以與膜平行的方向通過、而壓力梯度穿過所述膜的工藝。固體移動經過系統同時保留在膜之上并作為滲余物被收集,而液體通過膜并且作為滲透物被收集。“橫流式”過濾工藝的實例包括切向流過濾,以及其中通過在膜面的切向方向強烈地引起振動而引入附加剪切的橫流式過濾的各種形式。例如當進行橫流式過濾以濃縮分散體時,本發明可以使用切向流過濾工藝。在濃縮步驟之后,濃縮的分散體將具有800g/l或更多的二氧化鈦顆粒濃度,例如900g/l或更多、1000g/l或更多、1100g/l或更多、1200g/l或更多、1300g/l或更多、1400g/l或更多或者1500g/l或更多。在這點上,在濃縮步驟之后,濃縮的分散體可以合適地具有從800g/l至3000g/l的二氧化鈦顆粒濃度,例如從800g/l至2700g/l、或從800g/l至2500g/l、或從800g/l至2000g/l。優選地濃縮的分散體具有從1000g/l至3000g/l的二氧化鈦顆粒濃度,例如從1000g/l至2700g/l、或從1000g/l至2500g/l、或從1000g/l至2000g/l。更優選地濃縮的分散體具有從1200g/l至3000g/l的二氧化鈦顆粒濃度,例如從1200g/l至2700g/l、或從1200g/l至2500g/l、或從1200g/l至2000g/l。濃縮的分散體可以具有從1400g/l至3000g/l的二氧化鈦顆粒濃度,例如從1400g/l至2700g/l、或從1400g/l至2500g/l、或從1400g/l至2000g/l。在一個實施方案中,濃縮的分散體具有從1500g/l至2000g/l的二氧化鈦顆粒濃度。在一個實施方案中在濃縮步驟之前進行涂覆步驟。如上指出,在本發明的方法中初始提供的分散體可以是傳統的。在分散體中提供的二氧化鈦顏料顆粒可以是銳鈦礦、金紅石、或無定形的或其混合。在一個實施方案中,二氧化鈦基本上處于金紅石晶體習性。因此根據一個實施方案,基于粒狀材料的總重量,大于90重量%的二氧化鈦、優選地大于95重量%的二氧化鈦、且甚至更優選地大于99重量%的二氧化鈦處于金紅石晶體習性。可以通過任何已知方法(例如通過測量X射線衍射花樣)確定處于金紅石晶體習性的二氧化鈦的百分比。然而,在一些實施方案中粒狀材料可以包含銳鈦礦晶體形式的二氧化鈦。如技術人員知曉的,晶體尺寸與顆粒尺寸不同。晶體尺寸涉及組成粒狀材料的基礎晶體的尺寸。這些晶體隨后可以聚集至一定程度以形成較大的顆粒。例如處于金紅石晶體形式的傳統二氧化鈦具有約0.17μm-0.29μm的晶體尺寸以及約0.25μm-0.40μm的顆粒尺寸,而處于銳鈦礦晶體形式的傳統二氧化鈦具有約0.10μm-0.25μm的晶體尺寸以及約0.20μm-0.40μm的顆粒尺寸。因此顆粒尺寸受因素例如晶體尺寸以及在制備過程中使用的研磨技術(例如干法研磨、濕法研磨或合并(incorporative)研磨)和引起晶體聚集的隨后處理的影響。二氧化鈦的顆粒尺寸可以因此大于或約等于晶體尺寸。可以通過對于本領域技術人員眾所周知的方法確定二氧化鈦的晶體尺寸和顆粒尺寸。例如可以通過在擦掉的樣品上的透射電子顯微鏡法與所得照片的圖像分析來確定晶體尺寸。通過引用,使用乳膠NANOSPHERETM尺寸標準(從ThermoScientific可獲得)可以進一步驗證晶體尺寸的結果。可以用于確定二氧化鈦的顆粒尺寸的方法是X射線沉積。其中提供二氧化鈦顆粒的分散體中的液體載體優選地為極性的。在一個實施方案中,液體載體是含水的;其可以是水或含水溶液。然而還能考慮用于顆粒的其他極性載體,例如它們可以選自極性有機溶劑或醇類。液體載體還可以是兩種或更多種極性載體的混合物,例如其可以是水和醇的混合物。為了生產二氧化鈦,可以使用天然礦石(例如鈦鐵礦及金紅石礦)、富集礦石(例如鈦礦渣及精選鈦鐵礦)或其混合物作為起始原料。可以通過任何合適的方式(例如硫酸鹽工藝或氯化物工藝)加工這些礦石以生產具有所需的純度和尺寸的二氧化鈦晶體。然而,將意識到能夠通過任何合適的技術最終獲得在本發明的方法中以分散體形式提供的二氧化鈦,并且本發明不受限于任何制造方法。如上指出,顆粒尺寸與晶體尺寸是不相同的。作為在本領域中傳統的,可以研磨二氧化鈦以確保獲得所需要的顆粒尺寸分布。因此可以已經研磨在本發明的方法中提供的分散體形式的二氧化鈦以確保在那樣的二氧化鈦分散體中獲得所需要的顆粒尺寸分布。在這點上,在分散成分散體形式之前可以干法研磨二氧化鈦顆粒。或者或此外,可以例如在細介質研磨機中在濕狀態下研磨了處于分散體形式的二氧化鈦顆粒。在任一情況下,本發明在于包含在本發明的方法中提供的二氧化鈦顆粒的分散體具有用于預期最終用途所需要的顆粒尺寸分布。包含在本發明的方法中提供的二氧化鈦顆粒的分散體可以含有滿足下列尺寸標準中的一個或多個的二氧化鈦顆粒:a)平均顆粒尺寸(當使用BrookhavenBI-XDCWX射線盤式離心機系統確定時)為從0.29至0.32微米,且有小于1.45的幾何標準差。b)90重量%或更多的顆粒具有小于0.5微米的顆粒尺寸(直徑)。c)99重量%或更多的顆粒具有小于1.5微米的顆粒尺寸(直徑)。優選地包含在本發明的方法中提供的二氧化鈦顆粒的分散體含有滿足那些尺寸標準中的兩個或更多個的二氧化鈦顆粒;最優選地其含有滿足全部那些尺寸標準的二氧化鈦顆粒。如上討論,本發明的好處在于不存在可引起二氧化鈦顆粒的聚集的干燥步驟。因此保持所需要的顆粒尺寸特性。因此能夠使用最終二氧化鈦產品來制備具有合適的特性(例如優良的遮蓋力和光澤性質)的含有顏料的產品,例如涂料或油墨產品。本發明的方法在任何階段都不包括干燥分散體的步驟。因此在一個實施方案中在室溫或接近室溫下進行本方法的全部步驟。例如,可以在從10至30℃的溫度(例如從15至25℃,例如從18至23℃)下進行本方法的全部步驟。可以使用處于涂覆顆粒的濃縮分散體(顏料濃縮物)形式的二氧化鈦產品作為將會通常使用的二氧化鈦顏料濃縮物。在一個實施方案中,將涂覆顆粒的濃縮分散體包裝在用于儲存的容器內。在濃縮步驟之后可以直接進行此步驟;不需要干燥步驟。本發明因此提供包含在包裝容器內容納的涂覆二氧化鈦顆粒的濃縮分散體的包裝產品。清楚地,包裝容器應該適合于容納分散體。優選地其是防水的。本發明還提供用于制備包含在包裝容器內容納的涂覆二氧化鈦顆粒的濃縮分散體的包裝產品的方法,所述方法包含:-進行第一方面的方法(其包括上面描述的任選步驟的任何一個或多個);并且然后-將涂覆二氧化鈦顆粒的濃縮分散體放置在包裝容器內。因此本發明提供用于制備包含在包裝容器內容納的涂覆二氧化鈦顆粒的濃縮分散體的包裝產品的方法,所述方法包含以下步驟:-提供包含二氧化鈦顆粒的分散體,其中分散體含有從50g/l至600g/l的TiO2;并且然后,以任何順序,-向二氧化鈦顆粒施加無機涂層,同時在涂覆步驟過程中維持膠體穩定性;-濃縮分散體:通過使分散體經受橫流式過濾的作用并且持續橫流式過濾工藝直至分散體處于含有800g/l或更多TiO2的濃縮形式;從而提供處于涂覆顆粒的濃縮分散體形式的二氧化鈦產品;并且然后-將涂覆顆粒的濃縮分散體放置在包裝容器內。在另一個實施方案中,將涂覆顆粒的濃縮分散體分散至載色劑內以獲得所需要的含有顏料的產品。可以在濃縮步驟之后直接進行此步驟;不需要干燥步驟。載色劑可以是在其中能夠分散粒狀材料的任何組分或組分組合,并且包括但不限于樹脂、載體、粘合劑或其混合物。本發明因此提供包含分散在載色劑中的涂覆二氧化鈦粒狀材料的顏料產品。本發明還提供用于制備包含分散在載色劑中的涂覆二氧化鈦粒狀材料的顏料產品的方法,所述方法包含:-進行第一方面的方法(其包括上面描述的任選步驟的任何一個或多個);并且-將涂覆顆粒的濃縮分散體分散在載色劑內。因此本發明提供用于制備包含分散在載色劑中的二氧化鈦粒狀材料的顏料產品的方法,所述方法包含以下步驟:-提供包含二氧化鈦顆粒的分散體,其中分散體含有從50g/l至600g/l的TiO2;并且然后,以任何順序,-向二氧化鈦顆粒施加無機涂層,同時在涂覆步驟過程中維持膠體穩定性;-濃縮分散體:通過使分散體經受橫流式過濾的作用并且持續橫流式過濾工藝直至分散體處于含有800g/l或更多TiO2的濃縮形式;從而提供處于涂覆顆粒的濃縮分散體形式的二氧化鈦產品;并且然后-將涂覆顆粒的濃縮分散體分散在載色劑內以獲得顏料產品。例如,二氧化鈦粒狀材料可以以基于顏料產品的總體積的從約1體積%至約40體積%(例如從2%至35%或從5%至30%)的濃度存在于顏料產品中。在一個實施方案中,載色劑為合成的或天然的樹脂。所述樹脂可以是但不限于聚烯烴樹脂、聚氯乙烯樹脂、ABS樹脂、聚苯乙烯樹脂、甲基丙烯酸樹脂、聚碳酸酯樹脂、聚對苯二甲酸乙二醇酯樹脂、聚酰胺樹脂、醇酸樹脂、丙烯酸樹脂、聚氨酯樹脂、聚酯樹脂、蜜胺樹脂、氟聚合物或環氧樹脂。在另一個實施方案中,載色劑為載體。載體可以是但不限于含水溶劑。例如載體可以是水或可以基本上由水組成。然而,載體可以任選地包含非水溶劑,例如其可以是或可以包含有機溶劑,例如石油餾分、醇、酮、酯、二醇醚及類似物。在又一個實施方案中,載色劑為粘合劑。粘合劑可以是金屬硅酸鹽粘合劑,例如鋁硅酸鹽粘合劑。粘合劑還可以是聚合物粘合劑,例如丙烯酸類聚合物或共聚物粘合劑。顏料產品可以任選地包括一種或多種通常的添加劑。適合于使用的添加劑包括但不限于增稠劑、穩定劑、乳化劑、調質劑(texturizer)、助粘劑、UV穩定劑、去光澤劑(de-glossingagent)、分散劑、消泡劑、潤濕劑、聚結劑、間隔顆粒(spacerparticle)及殺蟲劑/殺真菌劑。含有粒狀材料的顏料產品可以在任何類型的施加中使用,并且可以施加至材料或基材的任何一個或多個表面。例如,顏料產品可以是涂料、清漆、油墨、塑料、涂層、橡膠或類似物或可以在涂料、清漆、油墨、塑料、涂層、橡膠或類似物中使用。此外,可以將顏料產品施加(通過任何已知方式)至的材料基材和它們的表面基本上是無限制的;這些包括但不限于建筑物表面、汽車、水塔、便攜式容器、路面、織物、飛行器、艇、船、其他類型的船舶、窗戶型材、壁板、指示牌、家具、柵欄、蓋板及欄桿。顏料產品還可以用作為獨立(standalone)組合物,能夠由其形成制品。現在將參考下列實施例以非限制的方式進一步描述本發明。對比實施例1通過氯化物途徑生產金紅石二氧化鈦顆粒。隨后使這些二氧化鈦顆粒經受實驗室規模的細介質研磨以實現目標顆粒尺寸分布。起始分散體具有0.31微米的顆粒尺寸及1.42的幾何標準差。起始材料的TiO2濃度為390g/l。然后通過使用超濾中空纖維濾芯(UltrafiltrationHollowFiberCartridge,UFP-500-E-4MAGEHealthcare)的實驗室規模橫流式過濾來濃縮分散體。測量pH、TiO2濃度和顆粒尺寸分布。使用如上描述的OD(光學密度)方法確定后者。在濃縮之后分散體具有下列性質:對比實施例2通過氯化物方式生產金紅石二氧化鈦顆粒。隨后使這些二氧化鈦顆粒經受實驗室規模的細介質研磨以實現目標顆粒尺寸分布。起始分散體具有0.31微米的顆粒尺寸及1.42的幾何標準差。起始材料的TiO2濃度為350g/l。使用在附錄1中描述的方法將3%氧化硅涂層(SiO2在TiO2顆粒上的w/w添加水平)施加至這些顆粒。在涂覆步驟結束時測量的電導率為8.4mS/cm。然后通過使用超濾中空纖維濾芯(UltrafiltrationHollowFiberCartridge,UFP-500-E-4MAGEHealthcare)的實驗室規模橫流式過濾來濃縮分散體。測量pH、TiO2濃度和顆粒尺寸分布。使用如上描述的OD(光學密度)方法確定后者。在濃縮之后分散體具有下列性質:能夠看出對比實施例2的問題是在涂覆和濃縮之后顆粒尺寸的增加。認為這由絮凝所致。實施例1通過氯化物途徑生產金紅石二氧化鈦顆粒。隨后使這些二氧化鈦顆粒經受工廠規模的細介質研磨以實現目標顆粒尺寸分布。起始分散體具有使用如上描述的OD(光學密度)方法確定的0.31微米的顆粒尺寸及1.42的幾何標準差。使用此細介質研磨反應器排出物(取自生產蒸汽)的分散體作為用于此實施例的起始材料。起始材料的TiO2濃度為350g/l。然后通過添加NaOH使此涂層供給材料的pH增加至10。pH調節過的材料的電導率為3.97mS/cm。然后使用實驗室規模橫流式滲濾將其降低至0.93mS/cm,從而維持膠體穩定性。然后通過附錄1的方法施加1.5%致密的氧化硅涂層(SiO2在TiO2顆粒上的w/w添加水平)。在涂覆之后電導率增加至4.8mS/cm。然后使用橫流式滲濾使電導率降低至0.5mS/cm,從而維持膠體穩定性。然后通過附錄1的方法施加第二1.5%氧化硅涂層(SiO2在TiO2顆粒上的w/w添加水平)。在每個涂覆之前和在每個涂覆之后的不同時刻,使用如上描述的OD(光學密度)方法測量顆粒尺寸分布。還測量在這些時刻的每個的電導率。在圖1中顯示對于涂層記錄的顆粒尺寸和電導率。能夠看到避免了如在對比實施例2中看到的在涂覆過程中顆粒尺寸的增加。因此通過維持膠體穩定性、通過保持分散體的電導率小于5mS/cm,解決了絮凝問題。電子顯微照片顯示在施加氧化硅涂層之前(圖2)和之后(圖3)的TiO2晶體。然后將含有涂覆顆粒的分散體洗滌至1mS/cm的電導率,并且然后使用橫流式過濾濃縮至1300g/l。測量pH、TiO2濃度和顆粒尺寸分布。使用如上描述的OD(光學密度)方法確定后者。在濃縮之后分散體具有下列性質:在實施例的全部步驟過程中顆粒保持處于濕的形式,即處于分散。因此能夠意識到當涂覆時通過維持膠體穩定性,在此情況下通過確保在涂覆工藝過程中分散體的電導率保持小于5mS/cm,能夠在不引起顆粒尺寸的任何顯著增加的情況下施加氧化硅涂層。然后能夠成功地將顆粒濃縮以形成適合直接在最終應用中使用的涂覆顆粒的濃縮分散體(顏料濃縮物)。實施例2用于此實施例的起始材料與在實施例1中描述的相同。起始材料的TiO2濃度為390g/l。通過在使用具有6.6m2膜面積的“KochSUPER-COR”管狀膜的Axium250L“超濾中試設備”上稀釋來洗滌分散體。此洗滌將分散體電導率從3.5mS/cm降低至1mS/cm,從而維持膠體穩定性。然后通過稀釋將在洗滌的分散體內的TiO2濃度調節至350g/l。然后涂覆顆粒。在這點上,將分散體的pH調節至10并且將它的溫度升高至90℃。在45分鐘內將硅酸鈉添加至分散體并且允許混合30分鐘。SiO2的添加水平為對TiO21.5w/w%。通過添加硫酸在90分鐘周期內將分散體的pH從10降低至8。然后將分散體冷卻至室溫。在涂覆之后洗滌分散體以產生1mS/cm的電導率。然后使用“KochSUPER-COR”膜將分散體濃縮至1000g/l。額外的濃縮步驟:使用具有1.4m2的膜面積的“KochABCOR-FEG”管狀膜將一部分此濃縮物進一步濃縮至1800g/l。使用如上描述的BrookhavenBI-XDCWX射線盤式離心機系統(XDC)方法和OD(光學密度)方法兩者測量顆粒尺寸分布。在濃縮之后分散體具有下列性質(對于兩種濃縮物):20在實施例的全部步驟過程中顆粒保持處于濕的形式,即處于分散。因此能夠意識到當涂覆時通過維持膠體穩定性,在此情況下通過確保在涂覆工藝過程中分散體的電導率保持小于5mS/cm,能夠在不引起顆粒尺寸的任何增加的情況下施加氧化硅涂層。然后能夠成功地將顆粒濃縮以形成適合直接在最終應用中使用的涂覆顆粒的濃縮分散體(顏料濃縮物)。對比實施例3用于此實施例的起始材料與在實施例1中描述的相同。起始材料的TiO2濃度為390g/l。通過在使用具有6.6m2膜面積的“KochSUPER-COR”管狀膜的Axium250L“超濾中試設備”上稀釋來洗滌分散體。此洗滌將分散體電導率從3.5mS/cm降低至1mS/cm,從而維持膠體穩定性。然后通過稀釋分散體將在洗滌的分散體內的TiO2濃度調節至350g/l。然后涂覆顆粒。在這點上,將分散體的pH調節至10并且將它的溫度升高至90℃。在45分鐘內將硅酸鈉添加至分散體并且允許混合30分鐘。SiO2的添加水平為對TiO21.5%w/w。通過添加硫酸在90分鐘周期內將分散體的pH從10降低至8。然后將分散體冷卻至室溫。在涂覆之后洗滌分散體以產生1mS/cm的電導率。然后使用“KochSUPER-COR”膜將分散體濃縮至1000g/l。換句話說,進行與實施例2相同的方法以獲得涂覆顆粒的分散體,其中將分散體濃縮至1000g/l。然后將此濃縮的分散體噴霧干燥并且然后經受雙重流體能量研磨機(FEM)微粒化處理。使用如上描述的BrookhavenBI-XDCWX射線盤式離心機系統(XDC)方法和OD(光學密度)方法兩者測量顆粒尺寸分布。在噴霧干燥和微粒化之后分散體具有下列性質:因此能夠看出不需要在當前工藝中是傳統的噴霧干燥和微粒化的額外步驟。出人意料地,在不需要干燥和微粒化顆粒的情況下本發明的方法給出用于涂覆顆粒的所需要的顆粒尺寸性質。因此本發明的方法使在沒有干燥步驟的情況下能夠直接在最終應用中使用的待獲得的涂覆顆粒的濃縮物成為可能。實施例3:應用測試使用在附錄2中給出的改進配方將來自實施例1、實施例2以及對比實施例1和2的濃縮物連同來自對比實施例3的微粒化的顏料的每一個制成涂料。將涂料施加至金屬板上并且經受加速的氣候老化。通過測量如附錄3中描述的耐久性比(DurabilityRatio)評估了顏料的光催化活性。涂料的耐久性比如下:使用以下顆粒制作的涂料耐久性比對比實施例13.06對比實施例21.47實施例10.91實施例21.1對比實施例31.49作為參比點,使用相同的測試測量三種商用耐久顏料的耐久性比。在此測試中這三種商用耐久顏料的平均(均)耐久性比為0.86。因此能夠意識到由根據本發明的涂覆顆粒的濃縮物制作的涂料具有商用可接受的耐久性比。根據本發明,實施例2中的從未干燥的分散體樣品具有低于對比實施例3的干燥且微粒化的樣品的耐久性比,其表明在顏料制備中干燥步驟對于氧化硅涂層降低光催化活性的能力不是關鍵性的。因此本發明提供一種方法,其允許在沒有任何干燥步驟的情況下制作有用的產品,因此降低能量需求和成本并且使工藝更高效。在全部步驟過程中顆粒保持處于濕的形式,即處于分散。如在實施例1中顯示的,根據本發明生產的更加重度涂覆的樣品具有優于對比實施例2(其具有與實施例1相似的涂覆水平,但是在涂覆過程中沒有控制膠體穩定性)的耐久性比。所有涂覆產品具有低于對比實施例1的未涂覆顏料的耐久性比。附錄1-致密氧化硅涂層配方附錄2-涂料組成的制劑漆漿來自BASF的N40溶液(現在以AA4140的名稱出售)是用于水性涂覆系統的分散劑并且尤其適合用于分散無機顏料。其為丙烯酸類聚合物的鈉鹽在水中的溶液。將2.6g的此分散劑添加至300g的處于880g/l濃度的顏料分散體。將其攪拌5分鐘然后放置在手推車(trundler)上。擱置其以混合過夜。然后將223g此分散體添加至合適的不銹鋼研磨罐內。使用旋轉混合器將分散體在溶解器(用于將顏料分散至涂料制劑中的高黏滯產品的溶解器,由VMA-GETZMANN制造)上以2500rpm攪拌10分鐘。然后添加下列,且在1200rpm下持續攪拌:Tektamer38AD(ActicideBX(N))0.5g(含有1,2-二溴-2,4-二氰基丁烷的殺蟲劑,可從LanxessCorporation獲得)FoamasterNXZ0.5g(用于乳膠涂料的液體消泡劑,其基于苯乙烯-丁二烯、丙烯酸類、聚氯乙烯及其共聚物、乙烯乙酸乙烯酯、偏二氯乙烯和水溶性醇酸,可從BASF獲得)苯甲酸鈉0.5g丁基溶纖劑乙酸酯3.5g(高沸騰、慢蒸發的酯類溶劑,可從Dow獲得)乙二醇3.5g然后將速度增加至2Krpm并且在大約1分鐘內緩慢地添加1.2g的MethocelJ75CMS增稠劑(冷水可分散的羥丙基甲基纖維素,可從Dow獲得)。然后將速度增加至2.5K持續10分鐘,確保全部Methocel已溶解。然后添加氨(28%)以確保pH>9。然后將速度增加至3.5Krpm持續15分鐘(分散階段)。最終涂料將180g的漆漿轉移至500ml的噴漆罐中并且使用50mm旋轉混合器以750rpm攪拌。添加208g的PrimalEP2596(設計用于具有觸變能力的高耐久外部半光澤和光澤涂料的丙烯酸類乳液粘合劑,可從Dow獲得)。將其攪拌5分鐘然后放置在手推車上。擱置其以混合過夜。將如此獲得的涂料施加至金屬基材上。附錄3-耐久性比的測量從關于暴露在AtlasCi65a氙弧耐氣候牢度試驗儀中3000小時的有涂料的金屬板的質量損失數據計算耐久性比。記錄在250小時內的質量損失。對于測試顏料,從使用g表達的質量損失(ml)計算耐久性比(DR)。使用下列等式,相對于主要標準(采用已知的DR)確定耐久性比:DR(測試)=ml(測試)×DR(標準)/ml(標準)因此耐久性比的較高值意指來自涂料的較大質量損失以及因此更加光化學活性的顏料。具有優良耐久性的涂料或油墨將具有較小的耐久性比。當前第1頁1 2 3