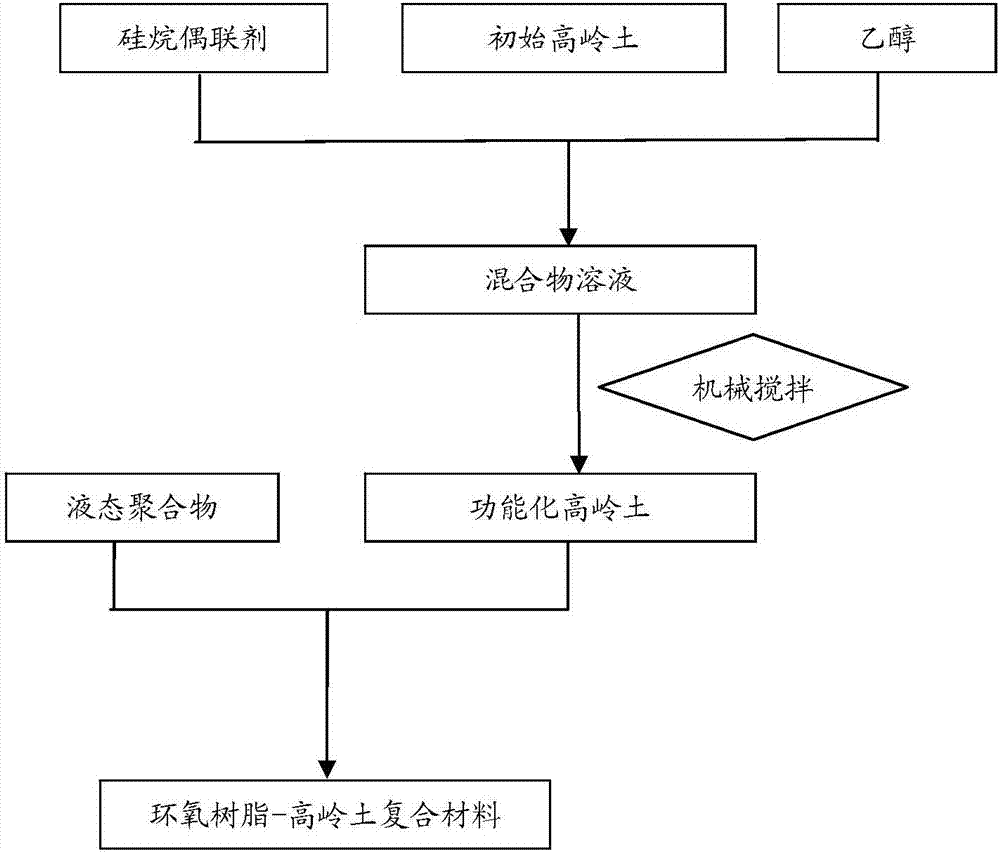
本發明涉及聚合物復合材料的
技術領域:
,更具體地說,涉及一種環氧樹脂-高嶺土的復合材料及其制備方法。
背景技術:
:環氧樹脂因其粘接強度高、粘接面廣、機械強度高、固化收縮率小、穩定性好、優良的電絕緣性能、良好的加工性等性能在電子封裝中得到了廣泛的應用。環氧樹脂主要用于電子封裝中有機基板材料、塑封料、底部填充材料等。隨著電子科技的迅速發展,電子器件的功率和集成度日益提高,自1959年以來,器件的特征尺寸不斷減小,已從微米量級向亞微米量級發展,同時集成度每年以40~50%高速度遞增。單一使用環氧樹脂的機械性能、熱性能等物理性能已經無法滿足電子封裝的要求。加入無機填料制備高性能的環氧樹脂復合材料是滿足電子封裝要求最為主要的方式。目前電子封裝中最為常用的無機填料為二氧化硅,然而二氧化硅表面存在大量的羥基基團,非常容易導致環氧樹脂的老化。在環氧樹脂的應用研究中,利用具有層狀結構的納米硅酸鹽與環氧樹脂插層復合制備環氧樹脂復合材料是提高環氧樹脂的性能的一種行之有效地方法。目前環氧樹脂/粘土納米復合材料的研究主要集中于環氧樹脂/蒙脫土復合材料的研究。高嶺土也是一種具有層狀結構的粘土礦物,在主要化學組成和結構上與蒙脫土相類似,由于高嶺土表面羥基活性較蒙脫土低,由其制備的環氧樹脂納米復合材料除了具備環氧樹脂/蒙脫土復合材料所具有的優異綜合性能外,還可能減少由硅酸鹽表面羥基引起的聚合物的老化。然而由于高嶺土難以表面功能化,很難制備出高性能的環氧樹脂/高嶺土復合材料。技術實現要素:本發明的目的在于提供一種環氧樹脂-高嶺土的復合材料及其制備方法,解決了現有技術中不易利用高嶺土制備出環氧樹脂-高嶺土的復合材料的問題。本發明解決技術問題所采用的技術方案是:一種環氧樹脂-高嶺土的復合材料,按質量分數計,所述復合材料包括環氧樹脂50%~95%和通過硅烷偶聯劑改性實現表面功能化的功能化高嶺土5%~50%。在本發明的復合材料中,改性初始高嶺土得到功能化高嶺土所用的硅烷偶聯劑為γ-氨丙基三乙氧基硅烷、γ-縮水甘油醚氧丙基三甲氧基硅烷、γ-甲基丙烯酰氧基丙基三甲氧基硅烷中的任一種。在本發明的復合材料中,初始高嶺土和硅烷偶聯劑質量比為5:1~10:1。在本發明的復合材料中,初始高嶺土的粒徑為50nm~2.0μm。在本發明的復合材料中,所述環氧樹脂為雙酚a環氧樹脂、雙酚f環氧樹脂、脂環族環氧樹脂中的至少一種。本發明還提供了上述的復合材料的制備方法,包括如下步驟:s1、將初始高嶺土與硅烷偶聯劑混合進行改性得到實現表面功能化的功能化高嶺土;s2、將環氧樹脂與改性得到的功能化高嶺土采用行星式球磨工藝混合均勻;s3、將得到的混合物采用涂布工藝制備得到環氧樹脂-高嶺土膜;s4、將環氧樹脂-高嶺土膜熱固化處理后得到環氧樹脂-高嶺土的復合材料。在本發明的制備方法中,在步驟s1中,初始高嶺土與硅烷偶聯劑在無水乙醇溶劑中進行改性反應,反應時間為2~12小時,反應溫度為50~80℃。在本發明的制備方法中,在步驟s2中,行星式球磨工藝條件如下:球磨速度為200~1500rpm,球磨時間為2~10分鐘。在本發明的制備方法中,在步驟s3中,所采用的涂布工藝為凹版涂布技術。在本發明的制備方法中,在步驟s4中,熱固化處理為階梯式熱固化處理,第一階梯熱固化處理的溫度為100~140℃,時間為0.5~2h;第二階梯熱固化處理的溫度為140~180℃,時間為0.5~2h;第三階梯熱固化處理的溫度為180~200℃,時間為0.5~2h。實施本發明的環氧樹脂-高嶺土的復合材料及其制備方法,具有以下有益效果:本發明由環氧樹脂和改性的高嶺土制備得到的復合材料具有優異的機械性能和熱性能,有效地提高了力學強度、玻璃化轉變溫度以及熱穩定性能,且制備方法簡單溫和,可用于工業化生產。附圖說明圖1為本發明的環氧樹脂-高嶺土的復合材料的制備工藝流程圖。具體實施方式下面結合附圖和實施例,對本發明的環氧樹脂-高嶺土的復合材料及其制備方法作進一步說明:現有技術中,高嶺土是一種具有層狀結構的粘土礦物,在主要化學組成和結構上與蒙脫土相類似,由于高嶺土表面羥基活性較蒙脫土低,由其制備的環氧樹脂納米復合材料除了具備環氧樹脂/蒙脫土復合材料所具有的優異綜合性能外,還可能減少由硅酸鹽表面羥基引起的聚合物的老化。然而由于高嶺土難以表面功能化,很難制備出高性能的環氧樹脂/高嶺土復合材料。本發明針對上述問題提供了一種性能強大的環氧樹脂-高嶺土的復合材料及其制備方法。其中,按質量分數計,環氧樹脂-高嶺土的復合材料包括環氧樹脂50%~95%和通過硅烷偶聯劑改性實現表面功能化的功能化高嶺土5%~50%。優選地,按質量分數計,環氧樹脂-高嶺土的復合材料包括環氧樹脂65%~88%和通過硅烷偶聯劑改性實現表面功能化的功能化高嶺土12%~35%。更優選地,按質量分數計,環氧樹脂-高嶺土的復合材料包括環氧樹脂75%~80%和通過硅烷偶聯劑改性實現表面功能化的功能化高嶺土20%~25%。上述環氧樹脂為雙酚a環氧樹脂、雙酚f環氧樹脂、脂環族環氧樹脂中的至少一種。改性初始高嶺土得到功能化高嶺土所用的硅烷偶聯劑為γ-氨丙基三乙氧基硅烷、γ-縮水甘油醚氧丙基三甲氧基硅烷、γ-甲基丙烯酰氧基丙基三甲氧基硅烷中的任一種。改性過程中,所用的初始高嶺土和硅烷偶聯劑質量比為5:1~10:1。優選地,所用的初始高嶺土和硅烷偶聯劑質量比為7:1~10:1。更優選地,所用的初始高嶺土和硅烷偶聯劑質量比為8:1~9:1。在改性過程中,所使用的初始高嶺土的粒徑為50nm~2.0μm。優選地,所使用的初始高嶺土的粒徑為50nm~1.0μm。更優選地,所使用的初始高嶺土的粒徑為120nm~350nm。如圖1所示,上述環氧樹脂-高嶺土的復合材料的制備方法包括如下步驟:s1、將初始高嶺土與硅烷偶聯劑混合進行改性得到實現表面功能化的功能化高嶺土;其中,初始高嶺土與硅烷偶聯劑在無水乙醇溶劑中進行改性反應,反應時間為2~12小時,反應溫度為50~80℃;優選地,反應時間為4~6小時,反應溫度為60~70℃;其中無水乙醇的用量相當于10ml/g的初始高嶺土;s2、將環氧樹脂與改性得到的功能化高嶺土采用行星式球磨工藝混合均勻;行星式球磨工藝條件如下:球磨速度為200~1500rpm,球磨時間為2~10分鐘。優選地,球磨速度為600~1200rpm,球磨時間為3~5分鐘;s3、將得到的混合物采用涂布工藝制備得到環氧樹脂-高嶺土膜;其中所采用的涂布工藝為凹版涂布技術,需要說明的是,凹版涂布技術為現有技術,這里不再詳細贅述;s4、將環氧樹脂-高嶺土膜熱固化處理后得到環氧樹脂-高嶺土的復合材料;熱固化處理為階梯式熱固化處理,第一階梯熱固化處理的溫度為100~140℃,時間為0.5~2h;第二階梯熱固化處理的溫度為140~180℃,時間為0.5~2h;第三階梯熱固化處理的溫度為180~200℃,時間為0.5~2h;優選地,熱固化處理為階梯式熱固化處理,第一階梯熱固化處理的溫度為115~125℃,時間為1~1.5h;第二階梯熱固化處理的溫度為155~165℃,時間為1~1.5h;第三階梯熱固化處理的溫度為185~195℃,時間為1~1.5h。下面通過具體實施例進行詳細說明。實施例1:將5g粒徑為50nm的初始高嶺土和0.5gγ-氨丙基三乙氧基硅烷置于含50ml無水乙醇的三口燒瓶中,升溫至50℃,磁力攪拌12小時得到功能化高嶺土。將5g功能化高嶺土和95g雙酚a環氧樹脂采用行星式球磨技術在轉速為200rpm球磨10分鐘條件下混合,將得到的混合物采用凹版涂布技術得到環氧樹脂-高嶺土膜,最后采用階梯式進行固化得到環氧樹脂-高嶺土的復合材料,其固化程序為100℃固化2h,140℃固化2h,180℃固化2h。實施例2:將5g粒徑為50nm的初始高嶺土和0.5gγ-縮水甘油醚氧丙基三甲氧基硅烷置于含50ml無水乙醇的三口燒瓶中,升溫至80℃,磁力攪拌2小時得到功能化高嶺土。將5g功能化高嶺土和5g雙酚f環氧樹脂采用行星式球磨技術在轉速為1500rpm球磨2分鐘條件下混合,將得到的混合物采用凹版涂布技術得到環氧樹脂-高嶺土膜,最后采用階梯式進行固化得到環氧樹脂-高嶺土的復合材料,其固化程序為140℃固化0.5h,180℃固化0.5h,200℃固化0.5h。實施例3:將5g粒徑為50nm的初始高嶺土和0.5gγ-甲基丙烯酰氧基丙基三甲氧基硅烷置于含50ml無水乙醇的三口燒瓶中,升溫至60℃,磁力攪拌6小時得到功能化高嶺土。將5g功能化高嶺土和15g脂環族環氧樹脂采用行星式球磨技術在轉速為600rpm球磨5分鐘條件下混合,將得到的混合物采用凹版涂布技術得到環氧樹脂-高嶺土膜,最后采用階梯式進行固化得到環氧樹脂-高嶺土的復合材料,其固化程序為120℃固化1h,160℃固化1h,190℃固化1h。實施例4:與實施例1不同之處在于:初始高嶺土的粒徑為2.0μm。實施例5:與實施例1不同之處在于:初始高嶺土的粒徑為1.0μm。實施例6與實施例1不同之處在于:將5g粒徑為50nm的初始高嶺土和1gγ-氨丙基三乙氧基硅烷置于含50ml無水乙醇的三口燒瓶中。實施例7:與實施例1不同之處在于:將5g粒徑為50nm的初始高嶺土和0.714gγ-氨丙基三乙氧基硅烷置于含50ml無水乙醇的三口燒瓶中。實施例8:與實施例1不同之處在于:雙酚a環氧樹脂質量為5g。實施例9:將5g粒徑為120nm的初始高嶺土和0.625gγ-氨丙基三乙氧基硅烷置于含50ml無水乙醇的三口燒瓶中,升溫至70℃,磁力攪拌4小時得到功能化高嶺土。將5g功能化高嶺土和36.67g雙酚a環氧樹脂采用行星式球磨技術在轉速為1200rpm球磨3分鐘條件下混合,將得到的混合物采用凹版涂布技術得到環氧樹脂-高嶺土膜,最后采用階梯式進行固化得到環氧樹脂-高嶺土的復合材料,其固化程序為115℃固化1.5h,155℃固化1.5h,185℃固化1.5h。實施例10:將5g粒徑為350nm的初始高嶺土和0.556gγ-氨丙基三乙氧基硅烷置于含50ml無水乙醇的三口燒瓶中,升溫至65℃,磁力攪拌6小時得到功能化高嶺土。將5g功能化高嶺土和9.286g雙酚a環氧樹脂采用行星式球磨技術在轉速為800rpm球磨4分鐘條件下混合,將得到的混合物采用凹版涂布技術得到環氧樹脂-高嶺土膜,最后采用階梯式進行固化得到環氧樹脂-高嶺土的復合材料,其固化程序為125℃固化1h,165℃固化1h,195℃固化1h。實施例11:將5g粒徑為50nm的初始高嶺土和0.5gγ-甲基丙烯酰氧基丙基三甲氧基硅烷置于含50ml無水乙醇的三口燒瓶中,升溫至60℃,磁力攪拌6小時得到功能化高嶺土。將5g功能化高嶺土和20g雙酚a環氧樹脂采用行星式球磨技術在轉速為600rpm球磨5分鐘條件下混合,將得到的混合物采用凹版涂布技術得到環氧樹脂-高嶺土膜,最后采用階梯式進行固化得到環氧樹脂-高嶺土的復合材料,其固化程序為120℃固化1h,160℃固化1h,190℃固化1h。對比例1:對比例1中的復合材料除了采用蒙脫土替代高嶺土外,其他條件均與實施例1相同。對比例2:對比例2中的復合材料除了采用二氧化硅替代二氧化硅外,其他條件均與實施例1相同。對實施例1-11以及對比例1-2制備得到的復合材料的導熱系數進行測試,結果如表1所示。表1項目拉升強度(mpa)熱穩定性(℃)玻璃化轉變溫度(℃)實施例168358125實施例280357124實施例367359127實施例471360124實施例569358123實施例675358127實施例770362125實施例877367126實施例975361125實施例1076364127實施例1179363131對比例134336112對比例235340113從表1可以看出,通過本發明的方法制備得到的環氧樹脂-高嶺土的復合材料比現有技術中的復合材料的拉升強度、熱穩定性和玻璃化轉變溫度均有明顯的改善。以上詳細描述了本發明的優選實施方式,但是,本發明并不限于上述實施方式中的具體細節,在本發明的技術構思范圍內,可以對本發明的技術方案進行多種簡單變型,這些簡單變型均屬于本發明的保護范圍。另外需要說明的是,在上述具體實施方式中所描述的各個具體技術特征,在不矛盾的情況下,可以通過任何合適的方式進行組合,為了避免不必要的重復,本發明對各種可能的組合方式不再另行說明。此外,本發明的各種不同的實施方式之間也可以進行任意組合,只要其不違背本發明的思想,其同樣應當視為本發明所公開的內容。應當理解的是,對本領域普通技術人員來說,可以根據上述說明加以改進或變換,所有這些改進或變換都應屬于本發明所附權利要求的保護范圍之內。當前第1頁12