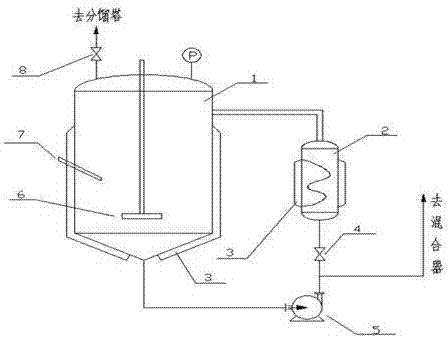
本發明屬于有機合成應用
技術領域:
,涉及采用一種來自化纖廢液回收的半纖維素連續法制造糠醛技術,具體為一種連續流微通道反應器半纖維素兩步法制備糠醛的方法。
背景技術:
:糠醛是一種目前尚不能通過化學方法合成的重要的基礎有機化工原料,是從糖類化合物中所獲得的唯一一種不飽和大比容有機化學品,其化學性質十分活潑,糠醛及其衍生物都是應用廣泛的有機化工中間體。此外,糠醛還可通過與甲醛的羥甲基化作用生成5-羥甲基糠醛,也可作為原料制備汽油、柴油和航空煤油,由糠醛通過加氫作用生成的甲基四氫呋喃可直接作為汽油的基料。隨著世界范圍內能源危機和環境問題的日益嚴峻,各化工領域對糠醛的需求量將會持續增長。但是,現有的糠醛生產工藝能耗巨大,環境污染極其嚴重,生產成本偏高且收率低下,以上諸多不利因素使歐盟和美國在過去數十年中已嚴令禁止在本國范圍內生產糠醛。中國是糠醛生產和出口大國,占世界糠醛總產量70%左右。鑒于糠醛在有機化工及能源領域中的重要作用,現有的糠醛生產工藝亟待改進。生物質水解制糠醛的反應機理是酸在水中電離出的h+與水結合為h3o+,它使半纖維素中的糖苷鍵的氧原子迅速質子化,糖苷鍵因減弱而斷裂,末端形成的碳正離子與水相互作用最終形成單糖,同時釋放出h+,繼續與水結合。水在高溫高壓條件下也可以電離出h+與oh-,具備酸堿自催化功能,因此生物質半纖維素在高溫高壓水中的反應機理也符合生物質水解的機理。半纖維素水解產生的木糖上的羥基與氫離子結合脫去一分子水,同時環斷裂形成碳碳雙鍵與碳氧雙鍵,再次脫去兩分子水成環得糠醛。由半纖維素生成糠醛的機理及水解動力學半纖維素在酸和水的作用下發生水解生成戊糖,而后木糖經過異構化作用和連續三步脫水反應生成糠醛。以酸為催化劑由木質纖維素的半纖維素部分生成的糠醛及木糖進一步發生副反應。首先,在酸的作用下,糖苷鍵被打破,半纖維素水解為戊糖,此步反應條件溫和,反應速度較快。隨后,生成的木糖在酸的作用下脫去3分子水生成糠醛。由于糠醛性質不穩定,會進一步與木糖及反應中間產物發生反應生成胡敏素,糠醛自身也會發生樹脂化反應。當反應時間較長或溫度較高時,胡敏素的產生尤為明顯。在水相中,木糖脫水反應的活化能(ea=124kj/mol),高于糠醛與木糖交互反應的活化能(ea=72kj/mol)及糠醛自身樹脂化反應的活化能(ea=68kj/mol),而在所有副反應中,糠醛與木糖的反應是生成胡敏素的主要途徑。以酸為催化劑,由木糖生成糠醛的反應過程是其中木糖的異構化是整個反應的限速步驟。通過以上機理分析可知,有兩種途徑可提高糠醛的產率和選擇性,一是優化反應條件減少副反應的發生,二是尋找恰當的催化劑加快木糖的異構化反應。現有的糠醛生產工藝存在諸多弊端:首先是收率問題,目前世界范圍內約70%的糠醛生產企業采用批處理反應器,糠醛收率只有理論值的50%左右,但是消耗蒸汽量卻是糠醛產量的30~50倍,且反應時間較長。現有的催化體系副反應較多,水相、強酸、高溫、與氧氣接觸、較長的反應時間等都會導致糠醛的縮合和樹脂化,同時,糠醛與木糖及反應中間產物之間也會發生交互聚合反應,糠醛還會進一步降解生成丙酮醛、甲醛、甘油醛、乙醇醛等,這些副反應會降低戊糖生成糠醛的選擇性。其次,稀酸易腐蝕設備,且其分離和循環使用非常困難,而稀酸水解法還會導致大量酸性糠醛廢水產生,治理難度極大。再次,使用蒸汽作為熱源和萃取劑耗能巨大。因此有人希望解決上述問題,專利cn102391218a中公開了一種固定床催化木糖脫水制備糠醛的方法:反應釜中進入3mol/l的酸催化劑溶液,再加助催化劑nacl至飽和,升溫至回流,攪拌形成一個固定體積和濃度的催化劑層的旋轉液面,再將經稀酸催化水解秸稈得到的10-20%的木糖按一定速度噴加到反應釜中,進行木糖脫水反應,糠醛溶液經精餾得到純度達到99%以上的糠醛,收率達到50~70wt%。專利cn102399203a公開了一種溶解漿木片水解液硫酸連續法制造糠醛技術,具體地說是利用生產溶解漿的闊葉木桉木、楊木等的預水解液為原料,連續水解、連續生產糠醛的技術。其技術方案為:一種溶解漿木片水解液硫酸連續法制造糠醛技術,預水解液采用連續的無酸條件下制得,過濾分離水解液和少量的溶解木質素;預水解液脫水反應生產糠醛,采用以硫酸為催化劑、連續化生產工藝。所用生物質為資源豐富的闊葉木桉木、楊木等,為糠醛生產開辟了新的豐富的原料資源和方法;水解液用于生產糠醛,而水解后的木片進一步生產溶解漿,進而實現木材中半纖維素和纖維素的高效資源化利用;連續化的水解工藝和連續的糠醛生產工藝,糠醛轉化率高達到76.6%;無酸的水解工藝,水解催化劑為木片本身水解產生的乙酸、甲酸等,大大降低對設備的腐蝕。以上方法均未給出反應時間,同時收率仍較低。一步法生產糠醛因為產率低,污染嚴重,原料利用率低,所以兩步法生產糠醛越來越受到了重視。兩步法是指戊聚糖的水解和戊糖的脫水環化分別在兩個不同的水解鍋內進行,這樣可以根據每步的最佳實驗條件進行反應,使反應能夠充分進行,提高每一步反應的產率,所以兩步法糠醛生產工藝的糠醛產率較一步法高,并且原料中木質纖維素在戊聚糖水解過程中不發生反應,經分離可以用來生產其他具有附加價值的化學品,原料的利用率有所提高。而且戊聚糖水解時的條件比較溫和,容易控制,還可以降低能耗、得到很高的木糖產率。殷艷飛等人[.慈竹竹黃兩步法水解制糠醛[j].中國造紙學會第十五屆學術年會論文集,2012:495-500.]以造紙原料剩余物竹黃為原料,對兩步稀酸水解制備糠醛的工藝條件進行了研究。結果表明,戊糖得率最高的反應條件為固液比1:10,溫度115℃,反應時間2.5h,硫酸質量分數3.5%,此條件下聚戊糖轉化率可達到72.06%。在溫度154℃,反應時間8h,硫酸質量分數19.34%,戊糖初始含量4.53%的條件下,糠醛得率可達到理論得率的63.85。技術實現要素:本發明正是基于以上技術問題,提供一種利用連續流微通道反應器將半纖維素制備糠醛的方法。該方法可利用化纖行業廢堿液回收的半纖維素為原料,在連續微通道反應器中,采用兩步法反應將半纖維素直接轉化成糠醛,通過分離,回收催化劑的方式,使產率、經濟效益、降低污染、改善生態環境等方面均有較大提高。微反應工藝,即采用微通道反應器代替傳統的化學反應鍋進行化學反應的工藝,并實現工業生產的技術。為了實現以上目的,本發明的技術方案為:一種連續流微通道反應器半纖維素兩步法制備糠醛的方法,該方法分兩步進行:第一反應區:(1)為使反應達到最佳得率,將含半纖維素的原料配置成半纖維素含量為8-20wt%的水溶液,催化劑配成30-80wt%的水溶液,超出這個范圍,將有固體析出,堵塞反應器,影響反應的進行;(2)將配置好的半纖維素水溶液和催化劑(硫酸或鹽酸)水溶液,經由各自計量泵控制半纖維素水溶液和催化劑硫酸或鹽酸水溶液,進入混合模塊-1,混合后再進入微通道反應器預熱模塊-1進行預熱,設定溫度為90-120℃,壓力0.1~0.5mpa,由外部換熱器進行控制,換熱介質為導熱油,再同步進入增強傳質型模塊-1內進行混合反應,反應溫度同樣由外部換熱器進行控制在90-120℃;(3)在該反應模塊-1中發生反應后,繼續通過一系列增強傳質型微通道模塊-1,設定溫度為90-120℃,壓力0.1~0.5mpa,反應時間60-120s,反應過程完成后,生成的木糖溶液,從反應器-1的出口流出,進入混合模塊-2;第二反應區(4)在此混合模塊-2中,加入催化劑硫酸或鹽酸及阻聚劑,混合后進入預熱模塊-2,升溫至180-220℃,進入反應模塊-2,設定溫度為180-220℃,壓力1.6~2.2mpa,由外部換熱器進行控制,換熱介質為導熱油,再同步進入增強傳質型模塊內進行混合反應,混合溫度同樣由外部換熱器進行控制在180-220℃;(5)在該反應模塊-1中進行反應后,繼續通過一系列增強傳質型微通道模塊-2,反應時間1-5min,反應過程完成后,產物從反應器的出口流出;(6)自微通道反應器-2出口得到的反應液進入分離器,分離器用夾套加熱維持溫度180-220℃,生成的糠醛與水蒸汽通過節流閥進入分餾塔,得到的粗糠醛再通過精餾得到成品糠醛;由微通道反應器出來的反應液以切線方式進入分離器,在此進行氣液分離,糠醛與水蒸氣混合氣體,由上部導氣管通過節流閥排出進入分餾塔,液體落入分離器內,該液體為微量未反應的的木糖和酸性催化劑,落入分離器下部液體中繼續反應,用泵從分離器底部抽出,在維持分離器液面的同時,多余液體打回微通道反應器混合模塊-2內,根據測定結果補加催化劑,維持催化劑的濃度3-5mol/l;所述的半纖維素原料來自化纖廢液回收的半纖維素含量為10-25wt%的水溶液或半纖維含量為50-80wt%的固體物。第一步反應,所述的半纖維素水溶液流量60-120ml/min;催化劑為硫酸或鹽酸,當采用的催化劑為硫酸時,控制其流速為6-12ml/min,當采用的催化劑為鹽酸時,控制其流速為6-15ml/min;停留時間均為60-120秒。第二步反應所述的木糖溶液流量60-120ml/min;催化劑為硫酸或鹽酸,當采用的催化劑為硫酸時,控制其流量為6-12ml/min,當采用的催化劑為鹽酸時,控制其流量為6-15ml/min;停留時間均為1-5min。所用的微通道反應器為美國康寧公司的增強傳質型微通道反應器,該反應系統由多塊模塊組裝而成;該模塊的材質為碳化硅硅和特種玻璃等;模塊內微通道結構為增強混合型通道結構,增強混合型通道結構為心型結構。所述的阻聚劑為羥基苯甲醚、對叔丁基鄰苯二酚、對苯二酚、n-苯基取代脲、硫脲、萘胺和三苯基磷中的任意一種或多種的混合物,添加量為0.1wt%~1wt%。所述的分離器為用于連續反應器的物料分離器,該分離器包括分離器罐體和循環反應器,在所述的分離器罐體和循環反應器外部均設有蒸汽夾套,物料泵的進料口與分離器罐體的底部連通,物料泵的出料口通過三通,一端通向混合器,另外一出口通過分流閥與循環反應器連接,循環反應器通過管道與分離器罐體連通,攪拌器設置在分離器罐體內,溫度計設置在分離器罐體上。所述的分離器罐體為圓柱形錐體結構,具有球形封頭,在分離器罐體的頂部設置有壓力傳感器,壓力傳感器與壓力顯示器相連接;在所述的分離器罐體上設置氣體物料排出節流閥,物料排出節流閥設置在氣體排出口處。所述反應物料通過循環反應器以切線方向進入分離器上部;所述的循環反應器內裝有sv型原件;所述的攪拌器為渦輪式攪拌器,距離所述分離器罐體圓筒直筒底部5cm-10cm。與現有技術相比,本發明的有益效果為:(一)、連續流微通道反應器半纖維素兩步法制備糠醛,瞬間反應物料量小,可精確控制反應條件自動控制程度高,較好的實現了反應過程。在收率、選擇性或安全性等方面得到提高。本發明采用連續流微通道反應器,反應時間從傳統的數小時縮短到1至5分鐘,顯著提高了反應效率。(二)、由于原料在微通道中混合極佳,溫度精確控制,反應過程中,催化劑的用量可以大大減少,還可回用,降低了成本,且產物的選擇性明顯提高。(三)、本發明中使用連續流微通道反應器材質為特種玻璃及碳化硅,計量泵的材質為聚四氟乙烯或玻璃,耐腐蝕性優良,解決了在常規反應器中腐蝕設備嚴重的問題。(四)、在微通道反應器中,從進料、預熱、混合以及反應過程全程為連續流反應,避免了常規間歇反應中需要額外配置裝置和轉移中出現的泄露,環保安全,生產效率高。(五)、糠醛生產中主反應是木糖脫水環化生成糠醛,同時有副反應發生,主要的副反應有在高溫和酸性條件下糠醛聚合生成低聚產物以及高溫下糠醛分解等反應。因此如果能把生成的糠醛立即從反應系統(酸性、高溫)中移出,減少其在反應器中的停留時間,應是提高糠醛得率的有效的途徑之一,本申請中所述的裝置即可完成該操作。(六)、我們利用用化纖行業廢堿液回收的半纖維素為原料,采用連續流微通道反應器將半纖維素直接轉化成糠醛,通過分離,回收催化劑的方式,在產率、經濟效益、降低污染改善生態環境等方面均有較大的提高。(七)、反應中沒有廢酸液排出,全部回用,減少了對環境的污染。附圖說明:圖1為實施例1中采用的連續流微通道反應器的工藝流程示意圖。圖2為本發明中所述用于連續反應器的物料分離器的結構示意圖。其中,1——分離器筒體;2——循環反應器;3——蒸汽夾套;4——分流閥;5——物料泵;6——攪拌器;7——溫度計;8——節流閥。具體實施方式為了使本發明的內容更加便于理解,下面將結合附圖和具體實施方式對本發明中所述的工藝做進一步的闡述。但不應將此理解為本發明上述主題的范圍僅限于下述實施例。本申請文件中的%,如無特殊說明,均表示wt%。下述實施例中所用的分離器為用于連續反應器的物料分離器,該分離器包括分離器罐體和循環反應器,在所述的分離器罐體和循環反應器外部均設有蒸汽夾套,物料泵的進料口與分離器罐體的底部連通,物料泵的出料口通過三通,一端通向混合器,另外一出口通過分流閥與循環反應器連接,循環反應器通過管道與分離器罐體連通,攪拌器設置在分離器罐體內,溫度計設置在分離器罐體上。所述的分離器罐體為圓柱形錐體結構,具有球形封頭,在分離器罐體的頂部設置有壓力傳感器,壓力傳感器與壓力顯示器相連接;在所述的分離器罐體上設置氣體物料排出節流閥,物料排出節流閥設置在氣體排出口處。所述反應物料通過循環反應器以切線方向進入分離器上部;所述的循環反應器內裝有sv型原件;所述的攪拌器為渦輪式攪拌器,距離所述分離器罐體圓筒直筒底部5cm-10cm。連續流微通道反應器半纖維素兩步法制備糠醛的方法:設備分為兩個反應區第一反應區:(1)為使反應達到最佳得率,將半纖維素的原料配置成半纖維素含量為8-20wt%的水溶液,催化劑配成30-80wt%的水溶液,超出這個范圍,將有固體析出,堵塞反應器,影響反應的進行;(2)8-20%的半纖維素水溶液和催化劑硫酸或鹽酸水溶液,經由各自計量泵控制半纖維素水溶液和催化劑硫酸或鹽酸水溶液,進入混合模塊-1,混合后再進入微通道反應器預熱模塊-1進行預熱,設定溫度為90-120℃,壓力0.1~0.5mpa,由外部換熱器進行控制,換熱介質為導熱油,再同步進入增強傳質型模塊-1內進行混合反應,反應溫度同樣由外部換熱器進行控制在90-120℃;(3)在該反應模塊-1中發生反應后,繼續通過一系列增強傳質型微通道模塊-1,設定溫度為90-120℃,壓力0.1~0.5mpa,反應時間60-120s,反應過程完成后,生成的木糖溶液,從反應器-1的出口流出,進入混合模塊-2;第二反應區(4)在此混合模塊-2中,加入催化劑硫酸或鹽酸及阻聚劑,混合后進入預熱模塊-2,升溫至180-220℃,進入反應模塊-2,設定溫度為180-220℃,壓力1.6~2.2mpa,由外部換熱器進行控制,換熱介質為導熱油,再同步進入增強傳質型模塊內進行混合反應,混合溫度同樣由外部換熱器進行控制在180-220℃;(5)在該反應模塊-1中進行反應后,繼續通過一系列增強傳質型微通道模塊-2,反應時間1-5min,反應過程完成后,產物從反應器的出口流出;(6)自微通道反應器-2出口得到的反應液進入分離器,分離器用夾套加熱維持溫度180-220℃,生成的糠醛與水蒸汽通過節流閥進入分餾塔,得到的粗糠醛再通過精餾得到成品糠醛;由微通道反應器出來的反應液以切線方式進入分離器,在此進行氣液分離,糠醛與水蒸氣混合氣體,由上部導氣管通過節流閥排出進入分餾塔,液體落入分離器內,該液體為微量未反應的的木糖和酸性催化劑,落入分離器下部液體中繼續反應,用泵從分離器底部抽出,在維持分離器液面的同時,多余液體打回微通道反應器混合模塊-2內,根據測定結果補加催化劑,維持催化劑的濃度3-5mol/l;所述的半纖維素原料來自化纖廢液回收的半纖維素含量為10-25wt%的水溶液或含量50-80%的固體物;第一步反應,所述的半纖維素水溶液流量60-120ml/min;催化劑硫酸流速6-12ml/min或鹽酸6-15ml/min;停留時間60-120秒;第二步反應所述的木糖溶液流量60-120ml/min;催化劑硫酸流量6-12ml/min或鹽酸6-15ml/min;停留時間30-300s;所用的微通道反應器為美國康寧公司的增強傳質型微通道反應器,該反應系統由多塊模塊組裝而成;該模塊的材質為碳化硅硅和特種玻璃等;模塊內微通道結構為增強混合型通道結構,增強混合型通道結構為心型結構。所述的阻聚劑為羥基苯甲醚或對叔丁基鄰苯二酚、對苯二酚、n-苯基取代脲、硫脲、萘胺、三苯基磷中的任意一種或多種的混合物,添加量為0.1wt%~1wt%。實施例1:所用連續流微通道反應器為美國康寧公司的增強傳質型微通道反應器,(該反應器的模式為“心型”結構功能模塊)水利直徑8mm,參照圖1、確定微通道反應器連接模式,混合反應模塊數根據流速與反應停留時間確定,加熱介質為導熱油。半纖維素原料來自化纖廢液回收的半纖維素含量為20%的混濁液,設備分為兩個反應區第一反應區:(1)為使反應達到最佳得率,將半纖維素的原料配置成半纖維素含量為20wt%的水溶液,催化劑硫酸配成40wt%的水溶液,超出這個范圍,將有固體析出,堵塞反應器,影響反應的進行;(2)20%的半纖維素水溶液和催化劑硫酸水溶液,經由各自計量泵控制半纖維素水溶液和催化劑硫酸或鹽酸水溶液,按1︰0.15進入混合模塊-1,混合后再進入微通道反應器預熱模塊-1進行預熱,設定溫度為110℃,壓力0.1~0.5mpa,由外部換熱器進行控制,換熱介質為導熱油,再同步進入增強傳質型模塊-1內進行混合反應,反應溫度同樣由外部換熱器進行控制在110℃;(3)在該反應模塊-1中,繼續通過一系列增強傳質型微通道模塊-1,設定溫度為110℃,壓力0.1~0.5mpa,反應時間60s,反應過程完成后,生成的木糖溶液,從反應器-1的出口流出,進入混合模塊-2;第一步反應,所述的半纖維素水溶液流量100ml/min;催化劑硫酸流速8ml/min;停留時間60秒;第二反應區(4)在此混合模塊-2中,加入催化劑硫酸及阻聚劑((羥基苯甲醚與硫脲1比1重量比混合物),混合后進入預熱模塊-2,升溫至200℃,進入反應模塊-2,設定溫度為200℃,壓力1.8mpa,由外部換熱器進行控制,換熱介質為導熱油,再同步進入增強傳質型模塊內進行混合反應,混合溫度同樣由外部換熱器進行控制在200℃;(5)在該反應模塊-2中,繼續通過一系列增強傳質型微通道模塊-2,反應時間90s,反應過程完成后,產物從反應器的出口流出;(6)自微通道反應器-2出口得到的反應液進入分離器,分離器用夾套加熱維持溫度200℃,生成的糠醛與水蒸汽通過節流閥進入分餾塔,得到的粗糠醛再通過精餾得到成品糠醛;第二步反應所述的催化劑硫酸流量6ml/min;阻聚劑(羥基苯甲醚與硫脲1比1重量比混合物)流量0.1ml/min停留時間90s。由微通道反應器出來的反應液以切線方式進入分離器,在此進行氣液分離,糠醛與水蒸氣混合氣體,由上部導氣管通過節流閥排出進入分餾塔,液體落入分離器內,該液體為微量未反應的的木糖和酸性催化劑,落入分離器下部液體中繼續反應,用泵從分離器底部抽出,在維持分離器液面的同時,多余液體打回微通道反應器混合模塊-2內,根據測定結果補加催化劑,維持催化劑的濃度3.5mol/l;糠醛轉化率94%。本發明方法與傳統釜式反應的轉化率及反應時間的對比,見下表:不同反應方法對轉化率及反應時間的影響反應時min糠醛轉化率%間歇釜水解24075本發明水解2.594實施例2:本發明采用的微通道反應器為美國康寧公司的增強傳質型微通道反應器,該反應系統由多塊模塊組裝而成;該模塊的材質為碳化硅和特種玻璃等;模塊內微通道結構分直流型通道結構和增強混合型通道結構兩種,直流型通道為管狀結構,增強混合型通道結構為心型結構,通道水力直徑為8mm;所用連續流微通道反應器(直通道功能模塊+“心型”結構功能模塊)流程,參照圖1、確定微通道反應器連接模式,混合反應模塊數根據流速與反應停留時間確定,加熱介質為導熱油。半纖維素原料來自化纖廢液回收的半纖維素含量為70%的固體物,設備分為兩個反應區第一反應區:(1)為使反應達到最佳得率,將半纖維素的原料配置成半纖維素含量為20wt%的水溶液,催化劑鹽酸配成30wt%的水溶液,超出這個范圍,將有固體析出,堵塞反應器,影響反應的進行;(2)20%的半纖維素水溶液和催化劑鹽酸水溶液,經由各自計量泵控制半纖維素水溶液和催化劑硫酸或鹽酸水溶液,按1︰0.15進入混合模塊-1,混合后再進入微通道反應器預熱模塊-1進行預熱,設定溫度為110℃,壓力0.1~0.5mpa,由外部換熱器進行控制,換熱介質為導熱油,再同步進入增強傳質型模塊-1內進行混合反應,反應溫度同樣由外部換熱器進行控制在110℃;(3)在該反應模塊-1中,繼續通過一系列增強傳質型微通道模塊-1,設定溫度為110℃,壓力0.1~0.5mpa,反應時間40s,反應過程完成后,生成的木糖溶液,從反應器-1的出口流出,進入混合模塊-2;第一步反應,所述的半纖維素水溶液流量110ml/min;催化劑鹽酸流速10ml/min;停留時間40秒;第二反應區(4)在此混合模塊-2中,加入催化劑硫酸及阻聚劑(羥基苯甲醚與硫脲1比1重量比混合物),混合后進入預熱模塊-2,升溫至200℃,進入反應模塊-2,設定溫度為200℃,壓力1.8mpa,由外部換熱器進行控制,換熱介質為導熱油,再同步進入增強傳質型模塊內進行混合反應,混合溫度同樣由外部換熱器進行控制在200℃;(5)在該反應模塊-2中,繼續通過一系列增強傳質型微通道模塊-2,反應時間90s,反應過程完成后,產物從反應器的出口流出;(6)自微通道反應器-2出口得到的反應液進入分離器,分離器用夾套加熱維持溫度200℃,生成的糠醛與水蒸汽通過節流閥進入分餾塔,得到的粗糠醛再通過精餾得到成品糠醛;第二步反應所述的催化劑鹽酸流量10ml/min;阻聚劑(羥基苯甲醚與硫脲1比1重量比混合物)流量0.1ml/min停留時間80s;;由微通道反應器出來的反應液以切線方式進入分離器,在此進行氣液分離,糠醛與水蒸氣混合氣體,由上部導氣管通過節流閥排出進入分餾塔,液體落入分離器內,該液體為微量未反應的的木糖和催化劑鹽酸,落入分離器下部液體中繼續反應,用泵從分離器底部抽出,在維持分離器液面的同時,多余液體打回微通道反應器混合模塊-2內,根據測定結果補加催化劑,維持催化劑的濃度3.5mol/l;糠醛轉化率96%。本發明方法與傳統釜式反應的轉化率及反應時間的對比,見下表:不同反應方法對轉化率及反應時間的影響雖然本發明已經通過具體實施方式對其進行了詳細闡述,但是,本專業普通技術人員應該明白,在此基礎上所做出的未超出權利要求保護范圍的任何形式和細節的變化,均屬于本發明所要保護的范圍。當前第1頁12