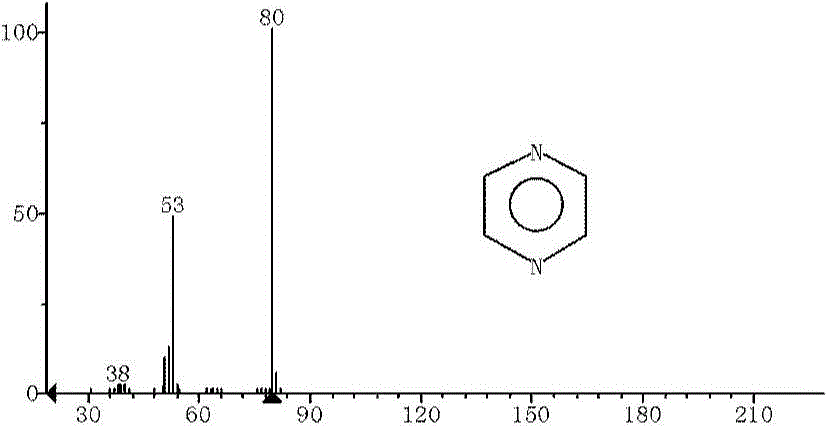
本發明一般地涉及有機材料催化熱解制備含氮芳香性化合物的方法,具體地,本發明尤其涉及由生物質催化熱解制備吡嗪類化合物、吡啶類化合物、吡咯類化合物、吲哚類化合物、苯胺類化合物或它們的組合的方法。
背景技術:生物質碳水化合物是自然界存在最多、分布最廣的一類重要的有機化合物,主要由碳、氫、氧所組成,葡萄糖、蔗糖、淀粉和纖維素等都屬于糖類化合物。隨著全球范圍內煤和石油資源的消耗和污染問題的日益嚴重,人們尋找一種可再生的、潔凈能源的需求越來越迫切。相比于化石能源,生物質能源具有分布廣、總量大、無污染、可再生的特點。此外,廢棄蛋白、城市有機垃圾等廢棄物大量流失,未得到有效利用,造成極大的資源浪費和環境污染。生物質資源是有機碳的唯一可持續來源,也是唯一可以轉化為液體燃料的可再生資源。生物質出發制備高附加值化學品也變得越來越重要。生物質熱解尤其是快速熱解可以得到高附加值的液體燃料和化學品,被認為是利用生物質的最有效的方式之一。選擇性催化熱解是在加入催化劑的條件下使生物質定向熱解從而提高一種或者幾種產物的產率。吡嗪類化合物是1、4位含兩個氮雜原子的六元雜環化合物。分子式C4H4N2。兩個氮原子占1、2兩位的稱為噠嗪,占1、3兩位的稱為嘧啶,它們都是吡嗪的同分異構體。無色晶體。熔點54℃,沸點115~116℃,液態的相對密度1.0311(61/4℃)。具有與吡啶類似的氣味。溶于水、乙醇、乙醚等。吡嗪是很弱的堿。它的芳香性與吡啶類似,很不容易發生親電取代反應,而對親核試劑比較活潑。碳原子上的氫被甲基或鹵素取代后,鹵素或甲基上的氫具有活性。吡嗪類化合物可以作為重要的醫藥中間體和香精香料中間體,也是一種具有高附加值的精細化學品。其衍生物有較多應用,如六氫吡嗪(或稱哌嗪)的檸檬酸鹽是一個常用的牲畜驅蟲劑,對蛔蟲特別有效;2-甲基吡嗪是一種重要醫藥中間體,可以制備抗結核藥物吡嗪酰胺;2-甲基吡嗪-5-羧酸可以制備具有降血糖,降血壓等藥物;2,5-二酮哌嗪是制備肽類化合物的試劑;二苯并吡嗪是一種重要染料,二苯并吡嗪是重要的染料,吩嗪(phenazine)以具有抗腫瘤,抗菌和利尿的性質而著稱。而四甲基吡嗪被報道可以捕捉超氧陰離子,并減少人體有粒細胞的氮氧化物產生。吡啶及烷基吡啶是含有一個氮原子的六元環化合物,通常將吡啶及其衍生物統稱為吡啶堿類化合物,主要包括吡啶,2-甲基吡啶,3-甲基吡啶,4-甲基吡啶等。吡啶及其衍生物是非常重要的化工中間體,廣泛應用于醫藥、農藥、飼料、合成橡膠和印染工業,還可用于表面活性劑和食品添加劑的生產。工業上吡啶主要用于生產磺胺、青霉素、維生素A、可的松、驅蟲藥和局部麻醉藥等,還可用于穩定劑、軟化劑、油漆溶劑、合成樹脂的縮合劑,以及用于合成除草劑、防腐劑和羥基吡啶等。2-甲基吡啶可用于制造合成橡膠工業的重要原料2-乙基吡啶,亦用于醫藥工業制氨丙嘧吡啶、長效磺胺、瀉藥和膠片感光膠添加劑、樹脂的原料和燃料中間體等。3-甲基吡啶可用于制維生素B、尼可拉明、強心劑、殺蟲劑、防水劑等,其最重要的用途是制造煙酸和煙酰胺,煙酸和煙酰胺可用做飼料工業的添加劑。4-甲基吡啶主要用于有機合成的原料和溶劑,還可用來制取治療結核藥物異煙肼、同時也是制取染料、農藥、催化劑、橡膠硫化促進劑和合成樹脂的原料。隨之吡啶衍生物需求的增長,從煉焦副產品回收分離吡啶及其衍生物的方法難以滿足市場需求。Chichibabin提出了以醛和氨為原料大批量生產吡啶及其衍生物的工藝路線,然而所用原料如醛、酮都是大宗化工基本原料,主要從石油化工而來。吡咯類化合物廣泛存在于植物、動物和微生物的代謝產物中,吡咯類生物單體是一種重要的五元氮雜環化合物,許多天然和合成的多取代吡咯化合物大多具有抗菌、抗炎和鎮痛作用。吡咯類化合物作為精細化工產品的重要中間體在醫藥、食品、農藥、日用化學品、涂料、紡織、印染、造紙、感光材料高分子材料等領域具有廣泛用途。如吡咯可以合成具有生物活性的卟吩膽色素原、具有抗菌活性的藤黃綠膿菌素、N-甲基-2-乙酰基吡咯、零紅菌素和燒烤香型香精2-乙酰基吡咯等。近年來,吡咯在導電聚合物領域也得到了應用,因而對其需求量日益增加。近年來,吡咯類化合物的工業生產原料主要來自于石油化工產品。吲哚是基本化工原料,廣泛用于醫藥、農藥、染料、食品以及香料等眾多領域,近年來隨著吲哚下游產品的快速發展以及新應用領域的不斷衍生,由其衍生出許多重要的高附加值的醫藥和農藥,特別是吲哚衍生物色氨酸的需求增長,使得全球吲哚需求量將大幅增長。吲哚的市場前景十分廣闊。目前工業上主要采用以苯胺和乙二醇為原料經過多相催化一步法合成吲哚。苯胺是一種重要的工業化學品,可作為橡膠硫化促進劑、染料、媒染體、藥品、炸藥原料,和二苯基甲烷聚氨酯(MDI)。烷基取代苯胺,如甲苯胺、枯胺、甲基枯胺、二甲基苯胺、二異丙基苯胺作為原料時,可以增加顯影劑、農業試劑和藥品的要用。近年來,苯胺用量持續增加,我國從2003年需求量為34萬t/a上升到206.5萬t/a。全球苯胺用量更多。預計,到2015年,全球苯胺消耗量將達到650萬t/a。當前,苯胺的主要生產方法為硝基苯催化加氫法,苯酚氨化法,硝基苯鐵粉還原法,其中90%為硝基苯催化加氫法。利用芳族硝基化合物制備方法需要消耗大量硫酸或者硝酸作為芳族化合物的硝化劑,緊接著中和反應需要大量的堿,此外在形成硝基化合物時會產生氧化氮氣體,這會引起空氣污染。本發明是一種通過對催化劑、反應條件的調控催化熱解各種生物質及其衍生物以及農林和城市廢棄物選擇性的制備吡嗪類、吡啶類,吡咯類,吲哚類以及苯胺類化合物的方法。
技術實現要素:本發明涉及有機材料在含氮氣體的存在下的催化熱解。在本發明的一個實施方案中,有機材料包括農業和城市固體廢物、食品廢物、動物廢物、碳水化合物、木質素纖維素等,或它們的組合。在本發明的一個實施方案中,有機材料包括木材、甘蔗渣、竹子、玉米秸稈、廢棄紙張、油菜籽餅、小桐子餅、餅粕、酒糟、廢棄蛋白、微藻或它們的組合。在本發明的一個實施方案中,有機材料包括葡萄糖、纖維二糖、纖維素、淀粉、木糖、木糖醇、木聚糖、殼聚糖、甲殼素、蔗糖、果糖、葡糖糖水溶液、甲基呋喃、2,5-二甲基呋喃、糠醛、5-羥甲基糠醛、5-甲基糠醛、γ-戊內酯、纖維素生物油、水溶性生物油、非水溶性生物油等,或它們的組合。一種由有機材料催化熱解制備含氮芳香性化合物的方法,所述方法包括:將有機材料和催化劑進料至反應器;在所述反應器中,在含氮氣體的存在下,在加熱條件下,使所述有機材料進料在催化劑的催化下進行反應,產生包含一種或多種含氮芳香性化合物的反應體系流。在本發明的一個實施方案中,在所述分離所述反應體系流中含氮芳香性化合物中的至少一部分中,除獲得所述包含所分離的含氮芳香性化合物的產物流之外,還獲得再循環流;將至少一部分所述再循環流進料至所述反應器。在本發明的一個實施方案中,所述含氮氣體包括NH3、有機胺如甲胺、二甲胺、乙胺和/或惰性氣體。在本發明的一個實施方案中,所述含氮氣體中包含摩爾比大于約1:19的NH3和惰性氣體。在本發明的一個實施方案中,所述含氮氣體中包含摩爾比為約1:19、1:9、1:4、1:1、4:1、19:1、1:0等的NH3和N2。在本發明的一個實施方案中,所述含氮芳香性化合物包括吡嗪類化合物、吡啶類化合物、吡咯類化合物、吲哚類化合物、苯胺類化合物等,或它們的組合。在本發明的一個實施方案中,吡嗪類化合物包括吡嗪,2-甲基吡嗪,2,5-二甲基吡嗪,2,6-二甲基吡嗪等化合物;吡啶類化合物包括吡啶,2-甲基吡啶,3-甲基吡啶,4-甲基吡啶,以及二甲基吡啶等化合物;吡咯類化合物包括吡咯,2-甲基吡咯,3-甲基吡咯,2,5-二甲基吡咯等化合物;吲哚類化合物包括吲哚,1-甲基吲哚,2-甲基吲哚,3-甲基吲哚,2,8-二甲基吲哚等化合物;苯胺類化合物包括苯胺,鄰甲基苯胺,間甲基苯胺,對甲基苯胺,二甲基苯胺等化合物。在本發明的一個實施方案中,催化劑包括沸石催化劑、非沸石催化劑、金屬催化劑和/或金屬氧化物催化劑等中的一種或多種。在本發明的一個實施方案中,催化劑包括γ-Al2O3、SiO2-Al2O3、WO3/ZrO2、SO42-/ZrO2、MCM-41、ZK-5、ZSM-23、SSZ-20、β-沸石、Y-沸石、ZSM-5和/或HZSM-5等。在本發明的一個實施方案中,催化劑具有15:1至200:1的SiO2/Al2O3,如15:1、25:1、50:1、63:1、80:1、100:1、150:1或200:1等的SiO2/Al2O3。在本發明的一個實施方案中,催化劑與所述有機材料的質量比為1:100至100:1,如1:100、1:50、1:20、1:15、1:10、1:5、1:2、1:1、2:1、5:1、10:1、15:1、20:1、50:1、100:1等。在本發明的一個實施方案中,催化劑與所述有機材料的質量比為1:1至10:1,并且所述含氮芳香性化合物是吡咯類化合物和/或吡嗪類化合物。在本發明的一個實施方案中,催化劑與所述有機材料的質量比為5:1至20:1,并且所述含氮芳香性化合物是吲哚類化合物。在本發明的一個實施方案中,催化劑由多個催化劑顆粒催化,且最大橫截面積尺寸小于約1微米的顆粒占催化劑體積總和的至少約50%。在本發明的一個實施方案中,催化劑具有約5埃至約100埃的孔。在本發明的一個實施方案中,所述催化劑包括多個孔;一種或多種催化劑的至少約95%的孔具有在第一尺寸分布和第二尺寸分布內的最小橫截面積直徑;至少5%的孔在具有在所述第一尺寸分布內的最小橫截面積直徑;至少約5%的孔具有在所述第二尺寸分布內最小橫截面積直徑;第一尺寸分布和第二尺寸分布不重疊。在一些實施方式中,可能希望使用一種或多種催化劑以建立雙峰孔徑分布。在一些情況下,可使用具有雙峰孔徑分布的單個催化劑。在其他一些情況下,可以使用兩種或者多種催化劑的混合物以建立雙峰分布。在一些實施方式中,一種或多種催化劑之一包括沸石催化劑,且一種或多種催化劑的另一種包括非沸石催化劑。在一些實施方式中,一種或多種催化劑的至少約70%、至少約80%、至少約90%、至少約95%、至少約98%或至少約99%的孔隙具有在第一尺寸分布或第二尺寸分布內的最小橫截面積直徑。在一些情況下,一種或多種催化劑的至少約2%、至少約5%或至少約10%的孔隙具有在第一尺寸分布內的最小橫截面積直徑;且一種或多種催化劑至少約2%、至少約5%或至少約10%的孔隙具有在第二尺寸分布內的最小橫截面積直徑。在一些情況下,第一尺寸分布和第二尺寸分布選自以上提供的范圍。在本發明的一個實施方案中,所述催化劑含有以下摻雜金屬中的一種或多種:Cu、Mn、Co、Fe、Ni、Zn、Ga、Pt、In、Ru、Rh、Ir、Pt、Pd、Au、Re、T1和鑭系金屬等。在本發明的一個實施方案中,通過干/濕法浸漬或離子交換等方式將所述摻雜金屬摻雜至所述催化劑中。在本發明的一個實施方案中,催化劑為HZMS-5并且含氮芳香性化合物是吡咯類化合物。在本發明的一個實施方案中,催化劑為SO42-/ZrO2并且含氮芳香性化合物是吡嗪類化合物。在本發明的一個實施方案中,反應器中的反應溫度為300℃至800℃,如300℃、400℃、500℃、600℃、700℃、800℃等。在本發明的一個實施方案中,反應器中的反應溫度為300℃至500℃,并且含氮芳香性化合物是吡咯類化合物。在本發明的一個實施方案中,反應器中的反應溫度為500℃至800℃,優選600℃,并且含氮芳香性化合物是吲哚類化合物和/或苯胺類化合物。在本發明的一個實施方案中,所述反應器是固定床反應器和/或流化床反應器等。在本發明的一個實施方案中,所述反應器是循環流化床反應器和/或湍動流化床反應器等。在本發明的一個實施方案中,以0.05至2的WHSV(質量歸一化),如0.05、0.1、0.2、0.5、0.8、1、1.5、2的WHSV將所述有機材料進料至所述反應器中。在本發明的一個實施方案中,以0.8至2的WHSV(質量歸一化)將所述有機材料進料至所述反應器中,并且含氮芳香性化合物是吡咯類化合物。在本發明的一個實施方案中,以0.1至0.8的WHSV(質量歸一化)將所述有機材料進料至所述反應器中,并且含氮芳香性化合物是吲哚類化合物和/或苯胺類化合物。本發明首次開發了通過對催化劑種類、用量、反應溫度等因素的調控采用催化熱解方法有選擇性地轉化生物質、生物油以及生物質基化學品到吡嗪類、吡咯類、吡啶類、吲哚類以及苯胺類化學品等石油化工中的大宗和精細化學品的新線路。與現有技術的方法相比較,本發明主要是克服了以前生產這些化學品的工藝中的以下缺點:如:(1)本發明原料全部是可再生資源涵蓋所有生物質材料,之前產物原料來源于石油化工產品;(2)本發明的生產工藝是綠色的生產工藝;不會有之前生產過程中需要大量酸堿,有環境污染等缺點;(3)以生物油或者生物質基化學品為原料時,這條線路可與石油化工中反應線路相近或者完全可以替代;(4)本線路由原料到生產工藝全過程是一個可再生、綠色、環保線路。附圖說明圖1是催化劑熱解制備吡嗪類和吡咯類化合物氣質圖及質譜圖。圖2是催化熱解制備吲哚類化合物氣質圖及質譜圖。圖3是催化熱解制備苯胺類吲哚類化合物氣質圖及質譜圖。圖4是催化熱解制備吡啶類和吡咯類化合物氣質圖及質譜圖。圖5是實施例1所示的反應模型流程圖。圖6是催化熱解水溶性生物油(實施例14)反應流程示意圖。圖7是本發明的一個實施方案的工藝流程圖,其中1系列為設備;1-1:干燥器;1-2:研磨系統;1-3:反應器;1-4:產物反應器;1-5:固體分離器;1-6:冷凝系統;1-7:蒸汽回收系統;1-8:催化劑再生器;1-9:壓縮系統;1-10:流體源。2系列為流體線路圖;2-1:進料組合物,包括生物質、催化劑和載氣;可以為固體、液體和/或氣體;2-2:水分;2-3:反應產物流;2-4:分離催化劑后產物流;2-5:分離的催化劑流;2-6:氧化劑,可包括氧氣,空氣,水蒸氣;2-7:再生后催化劑流;2-8:催化劑再循環流;2-9:產物反應后產物流;2-10:分離器吹掃流;2-11:催化劑再生器吹掃流;2-12:再生器排出流;2-13:產物液體組分流;2-14:產物氣體組分流;2-15:蒸汽流;2-16:CO、CO2或其他不可回收氣體蒸汽流;2-17:其他產物,如額外氣體。具體實施方式本說明書公開了用于制備諸如吡嗪類、吡啶類、吡咯類、吲哚類和苯胺類等含氮芳香類的化學品的組合物和方法,更具體地,通過催化熱解制備化學品的組合物和方法。一些實施方式涉及通過催化熱解工藝(例如,催化快速熱解)制備流體(例如,液體、超臨界流體和/或氣體)產物,例如含氮芳香類化學品(例如,吡嗪、吡咯、吲哚、苯胺等)的方法。在一些實施方式中,產物或其一部分在標準環境溫度和壓力(SATP,即25℃和100kPa絕對壓力)下為液體。一些這樣的方法可包括使用包含有機材料(例如,液體、氣體和/或固體有機材料)和非均相熱解催化劑組分的混合物的組合物。在一些實施方式中,可將含有機材料進料至反應器,進行催化熱解,并且可將一部分產物流再循環至包含有機材料的進料流。在本發明的一些實施方案中可以產生的產物如表1所示。表1.本發明的產物中文名稱與沸點化合物名稱沸點(℃)化合物名稱沸點(℃)化合物名稱沸點(℃)化合物名稱沸點(℃)吡咯131吲哚253-2542-甲基吡咯147吲嗪-3-甲基吡咯144N-甲基吲哚2712,5-二甲基吡咯-甲基吲哚-吡啶115.32-甲基吲哚2732-甲基吡啶128-1293-甲基吲哚265-2663-甲基吡啶1442,8-二甲基吲哚-4-甲基吡啶1453,8-二甲基吲哚-吡嗪115-116苯胺1842-甲基吡嗪1352-甲基苯胺199-2002,5-二甲基吡嗪1553-甲基苯胺203-2042,6-二甲基吡嗪1544-甲基苯胺200在一些實施方式中,所述混合物可在高溫(例如,300℃至800℃)下熱解。熱解過程至少需要足以產生部分可分離和可識別的含氮芳香產物流體的時間。本文所述的方法還可包括使用專用催化劑。例如,在一些情況下,使用沸石催化劑;本文所用的催化劑可任選具有任意的二氧化硅與氧化鋁摩爾比。在一些情況下,催化劑可以有相對小的顆粒形成或包括相對小的顆粒,所述顆粒可以結塊。在一些情況下,進料至熱解反應器的組合物具有任意的催化劑與有機材料質量比。一些實施方式可涉及生物質的單級熱解法。此類方法可包括提供或使用單級熱解裝置。單級熱解裝置是在單個容器中進行熱解和隨后的催化反應的裝置。在一些實施方式中,單級熱解裝置包括流化床反應器。如下文更詳細地描述的那樣,多級裝置也可用于制備流體含氮芳香性化學品。本文所用的術語“熱解”是其在本領域中的常規含義,用于表示在不氧化的情況下僅通過熱使化合物(例如有機材料)轉化成一種或多種其他物質(例如揮發性有機化合物、氣體和焦炭),這可在使用或不使用催化劑的情況下進行。“催化熱解”是指在催化劑存在下進行的熱解,可包括下文中更詳細地描述的步驟。例如,在Huber,G.W.等,“SynthesisofTransportationFuelsfromBiomass:Chemistry,Catalysts,andEngineering”Chem.Rev.106,(2006),第4044-4098頁中概括了催化熱解工藝的實例,其通過引用整體并入本文。本文所用的術語“生物質”是其在本領域中的常規含義,用于表示能量或化學品的任何可再生的有機來源。其主要組分可為(1)樹(木材)和所有其他植物;(2)農產品與廢棄物;(3)藻類和其他海洋植物;(4)代謝廢物(肥料、下水道污物);和(5)纖維質城市廢物。例如在Huber,G.W.等,“SynthesisofTransportationFuelsfromBiomass:Chemistry,Catalysts,andEngineering”Chem.Rev.106,(2006),第4044-4098頁中描述了生物質材料的實例。發明人發現,對于某些反應,反應條件的某些變化和此類變化的組合可產生有利的產物和/或產率、更低的焦炭形成產率和/或更受控的產物形成。例如,應用高溫(例如,在反應器和/或固體分離器中)可由在較低溫度下不會發生的反應產生有利的產物和/或產率。本發明人還發現,提供具有高的催化劑與有機材料質量比的進料可產生吲哚類和苯胺類化合物產物的理想產率。例如,不希望受理論限制,本發明人相信,高加熱速率和高催化劑與進料質量比可有利于將由有機進料熱解形成的揮發性有機化合物在其熱分解前引入到催化劑中,由此導致含氮芳香性化合物的高產率。較低的質量歸一化空速也顯示產生含氮芳香化合物的理想產率。本發明人還發現,有機材料在系統的高溫組件(例如,反應器和/或固體分離器)中的較長停留時間可允許充足時間來進行另外的化學反應以形成期望的產物。在本發明中,本發明人還發現,使用具有特定性質的催化劑有助于形成較大量的含氮芳香性化合物產物。例如,在一些情況下,使用包含較小尺寸的顆粒的催化劑可導致產生較高量的含氮芳香性化合物和/或較低量的焦炭。再例如,在一些實施方式中,發現ZSM-5優先產生含氮芳香性化合物。另外,發現包括Bronstead酸位點和/或良序孔隙結構的某些催化劑在一些情況下選擇性地產生含氮芳香性化合物。在一些情況下,催化劑孔徑可用于影響所產生的產物化合物的量和類型。本文所述的實施方式還包括用于進行催化熱解的化學工藝設計。在一些情況下,所述工藝可包括使用一個或多個流化床反應器(例如,循環流化床反應器、湍動流化床反應器、鼓泡流化床反應器等)。本文所述的工藝設計可任選包括進料到一個或多個反應器中的材料的專門操作。例如,在一些實施方式中,可在將材料供應到反應器之前將該進料材料干燥、冷卻和/或研磨。本發明的其他方面涉及應用本文所述的工藝設計制成的產物組合物。不受整個熱/催化轉化工藝的特定工作模式或步驟順序的限制,本發明人認為催化熱解包括有機材料(例如,諸如固體生物質)部分熱解以產生一種或多種熱解產物(例如,揮發性有機物、氣體、固體焦炭等)和至少使得一部分所述產物流體中一種或多種的熱解產物在催化劑條件下進行催化劑催化反應。除一氧化碳、二氧化碳、水和焦炭外,該催化反應還可涉及進入催化劑(例如沸石催化劑)的揮發性有機物,在此將它們轉化為化學品(例如含氮芳香性化合物和烯烴)。在催化劑內或在與催化劑接觸時,生物質衍生物質可發生一系列脫水、氨化、脫羰、脫羧、異構化和脫氫反應,以生成含氮芳香性化合物、烯烴、CO、CO2和水。選擇性制備含氮芳香性化合物的挑戰在于能夠使碳收率最大化。利用本文所述的方法和工藝可解決燃料生產的問題。例如,通過控制多個工藝參數可由有機材料進料可控地制備含氮芳香性化合物,所述工藝參數尤其包括例如:催化劑選擇(包括類型和物理性質例如孔徑、粒徑、結塊的存在和程度、顆粒/結塊形狀等)、有機材料選擇、再循環流組成、反應溫度、催化劑與有機材料質量比(例如,在進料流中、在反應器中等)、催化劑二氧化硅與氧化鋁摩爾比、質量歸一化空速、在各種加工組件中的停留時間。可選擇工藝參數以使焦炭形成速率較低。在一些實施方式中包括有機材料的反應的化學工藝。在一些實施方式中,該方法可包括在足以產生一種或多種熱解產物的反應條件下在反應器(例如,流化床反應器)中熱解至少一部分有機材料。此外,該方法可包括在足以產生一種或多種流體產物的反應條件下用催化劑使至少一部分所述一種或多種熱解產物催化反應。在一些實施方式中,可由所述熱解產物通過脫水、氨化、脫羰、脫羧、異構化和脫氫反應制備一種或多種流體產物;該熱解和催化反應方法可在單個反應器中進行。在一些情況下,該化學方法可用于生產特定流體產物(例如含氮芳香性化合物和/或烯烴);并且,可將由該化學方法產生的一部分烯烴再循環至進料流,通過該進料流,有機材料被進料至反應器(例如,熱解反應器)。圖7包括根據一組實施方式用于進行催化熱解的示例性化學方法設計的示意圖。在一些實施方式中,這種方法可用于進行催化熱解。如圖7的示例性實施方式所示,進料流2-1包括待進料至反應器1-3的有機材料的進料組合物。有機材料通常可包含碳、氫、氧(其中碳是按質量計最多的組分)以及次要比例的其他元素,如氮和硫。該進料組合物中的有機材料可包括固體、液體和/或氣體。下文提供有機材料的具體實例。在一些實施方式中,進料組合物(例如,在圖7的進料流2-1中)包括有機材料和催化劑的混合物。混合物可包括例如固體、液體和/或氣體。在一些實施方式中,混合物包括固體催化劑和固體有機材料的組合物。在其他實施方式中,可與進料組合物分開提供催化劑。如下文更詳細地描述的,可使用多種催化劑,例如可使用具有不同的二氧化硅與氧化鋁摩爾比和/或不同的孔徑的沸石催化劑。在一些實施方式中,例如當使用固體有機材料時,可任選在將其進料到反應器之前例如通過任選的干燥器1-1從進料組合物中除去水分2-2。出于幾個原因,從進料流中除去水分是有利的,例如,進料流中的水分可能需要額外的能量輸入才能將該進料加熱至足夠高的溫度以實現熱解;進料的水分含量的變化會在控制反應器溫度方面造成困難;另外,從進料中除去水分可減少或省去在后繼的加工步驟中處理水的需要。在一些實施方式中,可以干燥進料組合物直至該進料組合物包含少于約10重量%,少于約5重量%,少于約2重量%或少于約1重量%的水。能夠從進料組合物中除去水的合適設備是本領域技術人員已知的。例如,在一組實施方式中,干燥器包括被加熱至特定溫度(例如,至少約80℃,至少約100℃,至少約150℃或更高)的爐,進料組合物連續、半連續或周期性地通過該爐。在一些情況下,干燥器可包括真空室,進料組合物分批進入其中處理。干燥器的其他實施方式可將高溫與真空操作結合。干燥器可一體連接到反應器上或可作為與反應器分開的單元來設置。在一些情況下,在進料進入反應器之前,可在任選的研磨系統1-2中降低進料組合物的粒度。在一些實施方式中,離開研磨系統的經磨碎的進料組合物的平均直徑可為進入該研磨系統的進料組合物的平均直徑的不大于約50%、不大于約25%、不大于約10%、不大于約5%、不大于約2%。大顆粒進料材料比小顆粒進料材料更容易運輸。在一些情況下,將小顆粒進料到反應器中是有利的。研磨系統的使用可允許在來源與生產工藝之間進行大顆粒進料,同時能夠將小顆粒進料到反應器中。能夠研磨進料組合物的合適的設備是本領域技術人員已知的。例如,研磨系統可包括工業磨機(例如,錘磨機、球磨機等)、具有刀片的單元(例如切片機、切碎機等)或任何其他合適類型的研磨系統。在一些實施方式中,研磨系統可包括冷卻系統(例如主動冷卻系統,如泵送流體熱交換器,被動冷卻系統,如包括翅片的系統,等等),其可用于在將進料組合物引入反應器之前使該進料組合物保持在較低的溫度(例如環境溫度)。研磨系統可一體連接到反應器上或可作為與反應器分開的單元設置。雖然在圖7中研磨步驟顯示為在干燥步驟后,但在一些實施方式中可顛倒這些操作的順序。在其他實施方式中,干燥和研磨步驟可使用集成單元來實現。在一些情況下,可使用分開的單元來實現有機材料的研磨和冷卻。有機材料的冷卻可能是合乎需要的,例如,以減少或防止進料材料在進入反應器之前的不想要的分解。在一組實施方式中,可將有機材料進料到研磨系統以制備磨碎的有機材料。該磨碎的有機材料可隨后從該研磨系統進料至冷卻系統并冷卻。可在將有機材料引入反應器之前將該有機材料冷卻至低于約300℃、低于約200℃、低于約100℃、低于約75℃、低于約50℃、低于約35℃或低于約20℃的溫度。在包括使用冷卻系統的實施方式中,該冷卻系統包括能夠降低生物質溫度的主動冷卻單元(例如熱變換器)。在一些實施方式中,干燥器、研磨系統和冷卻系統中的兩個或多個可以組合在單個單元中。在一些實施方式中,冷卻系統可與一個或多個反應器直接合為一體。如圖7中所示,可將進料組合物轉移至反應器1-3中。在一些情況下,該反應器可用于實施有機材料的催化熱解。在圖7的示例性實施方式中,反應器包括本領域技術人員已知的任何合適的反應器。例如,在一些情況下,反應器可包括連續攪拌釜反應器(CSTR)、間歇式反應器、半間歇式反應器或固定床催化反應器。在一些情況下,反應器包括流化床反應器和固定床反應器,例如循環流化床反應器。在一些情況下,流化床反應器可改進在熱解和/或后繼反應過程中催化劑和/或有機材料的混合,這可增強對形成的反應產物的控制。流化床反應器的使用也可改進反應器內的熱傳遞。另外,在一些情況下,流化床反應器中改進的混合可導致附著于催化劑上的焦炭量降低,從而降低催化劑的失活。本文所使用的術語“流化床反應器”是其在本領域中的常規含義,用于指包括可容納粒狀固體材料(例如二氧化硅顆粒、催化劑顆粒等)的容器的反應器,其中流體(例如氣體或液體)以高至足以懸浮該固體材料并使其表現得像流體的速度通過該粒狀固體材料。術語“循環流化床反應器”也是其在本領域中的常規含義,用于指如下的流化床反應器:其中粒狀固體材料離開該反應器,通過與該反應器流體連同的管線循環并再循環回該反應器中。鼓泡流化床反應器和湍動流化床反應器也是本領域技術人員已知的。在鼓泡流化床反應器中,對于用于使粒狀固體材料流化的流體流在足夠低的流速下操作,使得在操作過程中在該流化床的容積內觀察到氣泡和空隙。在湍動流化床反應器中,流化流的流速高于鼓泡流化床反應器中所采用的流速,因此,在操作過程中,于該流化床的容積內沒有觀察到氣泡和空隙。本文所使用術語“固定床反應器”是尤其在本領域中常規定義,又稱填充床反應器,裝填有固體催化劑或固體反應物用以實現多相反應過程的一種反應器。固體物通常呈顆粒狀,粒徑2~15mm左右,堆積成一定高度(或厚度)的床層。床層靜止不動,流體通過床層進行反應。它與流化床反應器及移動床反應器的區別在于固體顆粒處于靜止狀態。涓流床反應器也可歸屬于固定床反應器,氣、液相并流向下通過床層,呈氣液固相接觸。固定床反應器有三種基本形式:①軸向絕熱式固定床反應器流體沿軸向自上而下流經床層,床層同外界無熱交換。②徑向絕熱式固定床反應器。流體沿徑向流過床層,可采用離心流動或向心流動,床層同外界無熱交換。③列管式固定床反應器由多根反應管并聯構成。管內或管間置催化劑,載熱體流經管間或管內進行加熱或冷卻,管徑通常在25~50mm之間,管數可多達上萬根。反應器可具有任何適用于實施本文所述的方法的尺寸。例如,反應器可具有0.1-1L、1-50L、50-100L、100-250L、250-500L、500-1000L、1000-5000L、5000-10,000L或10,000-50,000L的容積。在一些情況下,反應器具有大于約1L的容積,或在其他情況下,具有大于約10L、50L、100L、250L、500L,1,000L或10,000L的容積。大于約50,000L的反應器容積也是可能的。反應器可以是圓筒形、球形或任何其他合適的形狀。本發明人發現,當在本文所述的方法和系統中執行反應條件和系統組件的特定組合時,可實現所需產物生產的更高產率、更低焦炭形成產率、和/或更受控地獲得目標產物(例如含氮芳香性化合物)。例如,可如下文所述控制反應條件,例如反應器和/或固體分離器的溫度、反應器壓力、進料流的加熱速率、催化劑與有機材料質量比、質量歸一化空速、有機材料在反應器中的停留時間、反應產物在固體分離器中的停留時間、和/或催化劑類型(以及沸石催化劑的二氧化硅與氧化鋁摩爾比)中的至少一種,以實現有益結果。可在任何合適的溫度下操作反應器。在一些情況下,在較高的溫度下操作反應器可能是合乎需要的。例如,可在至少約300℃、至少約400℃、至少約500℃、至少約600℃、至少約700℃、至少約800℃、。在一些實施方式中,可在約500℃至約800℃、約525℃至約800℃、約550℃至約700℃或約575℃至約650℃的溫度下操作反應器。在低溫條件下反應有利于產生吡咯類吡嗪類化合物;在高溫條件下,反應劇烈,有利于產生吡啶類、吲哚類以及苯胺類化合物。在其他實施方式中,可在約500℃至約600℃操作反應器。也可在任何合適的壓力下操作反應器。在一些實施方式中,可在約0.1-4Mpa的壓力下操作反應器。在一些實施方式中,可在至少約1atm、至少約5atm、至少約1Mpa或至少約4Mpa的壓力下操作反應器。在一些實施方式中,可選擇有機材料的質量歸一化空速以選擇性地制備所需的一批流體產物。本文所用的術語“質量歸一化空速”定義為進入反應器的有機材料的質量流速(例如以克/小時為單位測得)除以該反應器中催化劑的質量(例如以克為單位測得),且單位為時間的倒數。可根據所用反應器的類型應用不同方法計算有機材料在反應器中的質量歸一化空速。例如,對于采用間歇式或半間歇式反應器的系統,有機材料沒有質量歸一化空速。對于在反應過程中將催化劑進料到反應器和/或從反應器中取出催化劑的系統(例如,循環流化床反應器),可通過在操作(例如穩態操作)期間計算反應器容積內催化劑的平均量來測定質量歸一化空速。在本文所述的實施方式中可應用任何合適的質量歸一化空速。在一些情況下,可應用小于約10小時-1、小于約5小時-1、小于約1小時-1、小于約0.5小時-1、小于約0.1小時-1、小于約0.05小時-1或小于約0.01小時-1的質量歸一化空速。在一些實施方式中,可應用約0.01小時-1至約10小時-1、約0.01小時-1至約5小時-1、約0.01小時-1至約0.1小時-1、約0.1小時-1至約1小時-1或約1小時-1至約10小時-1的質量歸一化空速。在一些實施方式中,使用流化床反應器采用小于約1小時-1、小于約0.5小時-1、小于約0.1小時-1、小于約0.05小時-1、小于約0.01小時-1、約0.01小時-1至約0.1小時-1或約0.1小時-1至約1小時-1的質量歸一化空速也是有利的。一些實施方式包括改變有機材料的質量歸一化空速,以選擇性地制備不同的流體產物。例如,在一些實施方式中,改變有機材料的質量歸一化空速可控制反應產物中含氮芳香性化合物和烯烴化合物的相對量。例如,較低的質量歸一化空速可用于制備的含氮芳香性化合物量相對大于烯烴量。較高的質量歸一化空速可用于制備的烯烴量相對大于含氮芳香性化合物量。在一些實施方式中,固體有機材料在流化床反應器中以約0.1小時-1至約10小時-1的質量歸一化空速提供以選擇性地制備烯烴化合物,或以約0.01小時-1至約0.1小時-1的質量歸一化空速提供以選擇性地制備含氮芳香性化合物。在一些情況下,控制有機材料(例如,固體有機材料)在反應器中和/或在指定的一組反應條件(即該有機材料在給定的反應器系統中發生熱解的條件)下的停留時間是有益的。在連續流系統中,有機材料在反應器中的停留時間定義為有機材料和由其形成的任何反應產物(不包括積聚在反應器中的產物,例如沉積在催化劑上的焦炭)在該反應器中度過的時間量。可根據所用反應器的類型應用不同方法計算有機材料在反應器中的停留時間。例如,在反應器包括填充床反應器的實施方式中,僅連續向該填充床反應器中供應有機材料(即不使用載體或流化流),可通過反應器容積除以離開該反應器的產物氣體的體積流量測定有機材料在此處所用反應器中的停留時間。在操作過程中對質量流封閉的反應器(例如,間歇式反應器)中發生反應的情況下,有機材料在這類反應器中的停留時間被定義為在容納該有機材料的反應器中的溫度達到足以開始熱解反應的水平(例如,對許多典型的有機進料原材料而言,通常約300℃至約800℃)時與在使反應器驟冷(例如冷卻至低于足以支持另外的熱解的溫度,例如對許多典型的有機進料原材料而言,通常約300℃至約800℃)時之間經過的時間量。在一些情況下,例如對某些流化床反應器而言,進料流可包含流化流體。在使用循環流化床的情況下,催化劑和流化流體都可進料/再循環至反應器中。在某些情況下,輔助材料可包含夾帶在有機材料中的污染物。在這樣的情況下,如上述填充床的情況那樣,可通過反應器容積除以離開該反應器的有機材料和反應產物氣體的體積流量來測定該有機材料在反應器中的停留時間;然而,由于可能不方便直接測定離開該反應器的有機材料和反應產物氣體的流量,因此可通過從離開該反應器的氣流的總體積流量中減去進入該反應器的輔助材料(例如流化流體、催化劑、污染物等)的進料體積流量來估算離開該反應器的有機材料和反應產物氣體的體積流量。在一些實施方式中,材料(例如,有機材料或任何其他合適的進料材料)在反應器中的停留時間為至少約2秒,至少約5秒,至少約10秒,至少約30秒,至少約60秒,至少約120秒,至少約240秒,或至少約480秒。在一些情況下,材料(例如有機材料或任何其他合適的進料材料)在反應器中的停留時間為小于約5分鐘,約1分鐘至約4分鐘,或約2秒至約480秒。在許多情況下,之前的“快速熱解”研究采用具有很短的進料材料(例如,有機材料)停留時間(例如,小于2秒)的系統。但是,本發明人發現,在一些情況下,應用較長的停留時間能夠留出充足時間用于附加的化學反應而形成希望的產物。例如,可通過提高反應器的容積和/或降低有機材料的體積流量來實現長的停留時間。但是,應該理解,在本文所述的一些實施方式中,進料材料(例如,有機材料)的停留時間可較短,例如,小于約2秒或小于約1秒。在使用流化床反應器的某些情況下,可通過使流體流過反應器來流化該反應器中的進料材料(例如,固體有機材料)。在圖7的示例性實施方式中,使用流體流2-8來流化反應器1-3中的進料材料。可由流體源1-10和/或由反應器的產物流經壓縮機1-9(下面將更詳細地描述)向流體流供應流體。本文所用的術語“流體”是指通常為液態、超臨界態或氣態的物質。但是,流體也可含有固體,例如,懸浮或膠體顆粒。在一些實施方式中,控制流化流體在反應器中的停留時間可能是有利的。流化流體的停留時間被定義為反應器的容積除以流化流體的體積流量。在一些情況下,流化流體的停留時間可為至少約5秒,至少約10秒,至少約30秒,至少約60秒,至少約120秒,至少約240秒,或至少約480秒。在一些情況下,流化流體的停留時間可為約2秒至約480秒,約5秒至約480秒,約10秒至約480秒,約30秒至約480秒,約60秒至約480秒,約120秒至約480秒,或約240秒至約480秒。本發明中可用的合適的流化流體尤其包括,例如惰性氣體(如氦氣、氬氣、氖氣、氮氣等)和氨氣。如圖7的示例性實施方式所示,在有機材料反應過程中形成的產物(例如,流體產物)經產物流2-3離開反應器。在一些情況下,除反應產物外,產物流可包含未反應的有機材料、流化流體和/或催化劑。在一組實施方式中,可從反應器的流出物流中回收所需的反應產物(例如,液體含氮芳香性化合物、烯烴、氣體產物等)。在一些實施方式中,可將任選的產物反應器1-4并入工藝中。例如,可使用產物反應器,以將產物流2-3中的一種或多種流體產物(例如,烯烴、含氮芳香化合物等)轉化為一種或多種其他產物。在一些情況下,產物反應器可含有能夠用于進行一個或多個催化反應的催化劑(例如,沸石催化劑)。本領域普通技術人員能夠選擇實施這些反應的合適反應器類型和/或條件。如圖7的示例性實施方式所示,可將產物流2-3送入任選的固體分離器1-5。在一些情況下,該固體分離器可用于從產物流中存在的催化劑(例如,至少部分失活的催化劑)分離反應產物。另外,在一些情況下,該固體分離器可用于從催化劑中除去焦炭和/或灰分。在一些實施方式中,該固體分離器可包含任選的吹掃流2-10,其可用于從該固體分離器中吹掃焦炭、灰分和/或催化劑。本領域普通技術人員可容易地設計實現固體分離和/或除焦步驟所需的設備。例如,在一組實施方式中,固體分離器可包括含有篩網材料的容器,該篩網材料界定該容器的保留部分和滲透部分。該篩網可用于將催化劑留在保留部分內,同時使反應產物穿過到達滲透部分。催化劑可通過篩網保留側上的開口離開固體分離器,而反應產物可離開篩網滲透側上的開口。可在任何合適的溫度下操作固體分離器。在一些實施方式中,可在高溫下操作固體分離器。本發明人發現,對于某些反應,在固體分離器中應用高溫可實現來自反應器的化合物的另外的重整和/或反應。這可增加期望產物的形成。不希望受任何理論限制,固體分離器中的高溫可提供足以驅動吸熱重整反應的能量。可在例如約25℃至約200℃、約200℃至約500℃、約500℃至約600℃、或約600℃至約800℃的溫度下操作固體分離器。在一些情況下,可在至少約500℃、至少約600℃、至少700℃、至少800℃或更高溫度下操作固體分離器。在一些情況下,控制催化劑在固體分離器中的停留時間可為有利的。催化劑在固體分離器中的停留時間被定義為固體分離器的容積除以催化劑通過該固體分離器的體積流量。在一些情況下,期望催化劑在固體分離器中的較長停留時間,以利于從催化劑中除去充足量的灰分、焦炭和/或其他不想要的產物。另外,本發明人發現,通過應用催化劑在固體分離器中的較長停留時間,可使熱解產物進一步反應以產生期望產物。在一些實施方式中,一起選擇固體分離器中的停留時間和溫度以制備所需的產物流。在一些實施方式中,催化劑在固體分離器中的停留時間為至少約1秒、至少約5秒、至少約10秒、至少約30秒、至少約60秒、至少約120秒、至少約240秒、至少約300秒、至少約600秒、或至少約1200秒。控制催化劑在固體分離器中的停留時間的方法是本領域技術人員已知的。例如,在一些情況下,固體分離器的內壁可包括用于約束通過該固體分離器的催化劑流和/或提高流體流在該固體分離器中的路徑長度的擋板。另外,可通過控制催化劑通過固體分離器的流量(例如通過控制流化流體通過反應器的流量)來控制催化劑在固體分離器中的停留時間。固體分離器可具有任何合適的尺寸。例如,固體分離器可具有0.1-1L、1-50L、50-100L、100-250L、250-500L、500-1000L、1000-5000L、5000-10,000L或10,000-50,000L的容積。在一些情況下,固體分離器具有大于約1L的容積,或者在其他情況下,固體分離器具有大于約10L、50L、100L、250L、500L、1,000L或10,000L的容積。大于50,000L的固體分離器容積也是可能的。固體分離器可是圓筒形、球形或任何其他形狀,并可為循環或非循環的。在一些實施方式中,固體分離器可包括與該工藝中所用的一個或多個反應器相似的容器或其他單元操作。固體分離器中的催化劑流可包含任何合適的幾何形狀。例如,流徑可為基本上直的。在一些情況下,固體分離器可包含具有蜿蜒、曲折、螺旋或任何其他合適形狀的流道。固體分離器的流徑的長度(或在一些實施方式中,催化劑通過固體分離器的路徑長度)與固體分離器通道的平均直徑之比可包括任何合適的比率。在一些情況下,該比率可為至少2:1、至少5:1、至少10:1、至少50:1、至少100:1或更大。上述參數可以以任何合適的組合使用,以產生期望的反應產物(例如,含氮芳香性化合物)和/或有利的產率或特定組分。例如,長的停留時間可與循環或湍動流化床反應器聯用以加工固體有機材料。在一些實施方式中,在反應器中熱解固體有機材料之后,可在固體分離器中應用較高的溫度(例如,至少500℃)和長的停留時間(例如,至少約1秒、至少約5秒、至少約10秒、至少約30秒、至少約60秒、至少約120秒、至少約240秒、至少約300秒、至少約600秒、或至少約1200秒等)。在其他實施方式中,較低的質量歸一化空速(例如,小于約0.1小時-1、小于約0.05小時-1、小于約0.01小時-1等)可用于在流化床反應器中制備大于烯烴量的含氮芳香性化合物量,例如至少約6%含氮芳香性化合物或更多。在另一組實施方式中,固體有機材料和包括大的二氧化硅與氧化鋁摩爾比(例如,至少約15)的沸石催化劑可在反應器中以高速率加熱。在一些情況下,可將催化劑和固體有機材料以至少約0.5:1的質量比送入反應器中并加熱至例如500℃至800℃的溫度。在一些情況下,可將催化劑和固體有機材料以至少約0.5:1的質量比送入反應器中,以使該混合物具有較長的停留時間(例如,至少約5秒)。在又一組實施方式中,可應用較長的流化流體停留時間(例如,至少約5秒)和較高的反應器溫度(例如,約500℃至約800℃)。如之前所述,并非在所有實施方式中都需要固體分離器。例如,對于應用催化固定床反應器的情況,可將催化劑留在反應器內,并且反應產物在離開反應器時可基本不含催化劑,因此不需要單獨的分離步驟。在圖7中所示的實施方式組中,分離的催化劑可經流2-4離開固體分離器。在一些情況下,離開分離器的催化劑可為至少部分失活的。在一些實施方式中,分離的催化劑可被送入催化劑再生器1-8,在此可將任何至少部分失活的催化劑再活化。在一些實施方式中,催化劑再生器可包括任選的吹掃流2-11,其可用于從該再生器中吹掃焦炭、灰分和/或催化劑。活化催化劑的方法是本領域技術人員公知的。在一組實施方式中,例如如圖7中所示,將氧化劑經流2-6送入催化劑再生器。該氧化劑可源自任何來源,尤其包括例如氧罐、大氣、水蒸氣。在再生器中,通過使催化劑與氧化劑反應,再活化該催化劑。在一些情況下,失活的催化劑可包括殘留碳和/或焦炭,它們可通過在再生器中與氧化劑反應而除去。圖7中的再生器包括排出流2-12,其可包括再生反應產物、殘留氧化劑等。催化劑再生器可具有上文關于反應器或固體分離器提到的任何合適的尺寸。另外,在一些情況下,可在高溫(例如,至少約300℃、400℃、500℃、600℃、700℃、800℃或更高)下操作再生器。也可利用本領域技術人員已知的方法(包括上述那些方法)控制催化劑在再生器中的停留時間。在一些情況下,將催化劑通過再生器的質量流速與在反應器和/或固體分離器中的流速相聯系,以保持系統中的質量平衡。如圖7的示例性實施方式中所示,再生的催化劑可經流2-7離開再生器。再生的催化劑可經再循環流2-8再循環回反應器。在一些情況下,催化劑可在操作過程中從系統流失。在一些這樣的和其他情況下,可經補充流2-12向系統中添加另外的催化劑。如圖7中示例性顯示的,再生和補充的催化劑可與流化流體一起經再循環流2-8送入反應器,但在其他實施方式中,催化劑和流化流體可經分開的流送入反應器。再回到圖7中的固體分離器1-5,反應產物(例如,流體含氮芳香性產物)經流2-3離開該固體分離器。在一些情況下,可將流2-7中的反應產物送入任選的冷凝器1-6。該冷凝器可包括熱交換器,其使至少一部分反應產物從氣態冷凝成液態。冷凝器可用于將反應產物分離成氣體、液體和固體組分。冷凝器的操作是本領域技術人員公知的。在一些實施方式中,冷凝器也可利用壓力變化來冷凝產物流的一部分。在圖7中,流2-13可包括反應產物的液體組分(例如,水、含氮芳香性化合物、烯烴化合物等),且流2-14可包括反應產物的氣體組分(例如,CO、CO2、H2,NH3等)。在一些實施方式中,可將氣體組分送入蒸氣回收系統1-7。該蒸氣回收系統可用于例如回收流2-14內的任何期望的蒸氣并經流2-15輸送它們。另外,流2-16可用于輸送來自蒸氣回收系統的CO、CO2和/或其他不可回收的氣體。應指出,在一些實施方式中,可在其他位置設置任選的蒸氣回收系統。例如,在一些實施方式中,蒸氣回收系統可位于吹掃流2-13的下游。本領域技術人員可選擇蒸氣回收系統的適當位置。可將其他產物(例如額外的氣體)經流2-17輸送到任選的壓縮機1-9,在此可將它們壓縮并用作反應器中的流化氣體和/或它們可在此輔助將有機材料輸送至反應器。在一些情況下,可進一步加工液體組分,例如將水相與有機相分離,以分離各化合物等。應理解,盡管圖7中所述的該組實施方式包括反應器、固體分離器、再生器、冷凝器等,但并非所有實施方式都包括使用這些元件。例如,在一些實施方式中,進料流可被送入催化固體床反應器并反應,并可直接從反應器收集反應產物并冷卻而不使用專用冷凝器。在一些情況下,盡管干燥器、研磨系統、固體分離器、再生器、冷凝器和/或壓縮機可用作工藝的一部分,但這些元件中的一個或多個可包括不與反應器流體連接和/或一體連接的獨立單元。在另一些實施方式中,干燥器、研磨系統、固體分離器、再生器、冷凝器和/或壓縮機中的一個或多個可不存在。在一些實施方式中,可在制備工藝中的任何位置(例如,在通過反應器后、在分離后、在冷凝后等)回收所需的反應產物(例如,含氮芳香性化合物、烯烴、氣體產物等)。在一些實施方式中,本發明的方法可包括使用多于一個反應器。例如,多個反應器可彼此流體連通,在一些實施方式中,該方法可包括在第一反應器中提供有機材料并在第一反應器中在足以產生一種或多種熱解產物的反應條件下熱解至少一部分該有機材料。在一些實施方式中,可向該第一反應器提供催化劑,并且在第一反應器中使用該催化劑在足以產生一種或多種流體產物的反應條件下使至少一部分所述一種或多種熱解產物進行催化反應。該方法還可包括在第二反應器中使用催化劑在足以產生一種或多種流體產物的反應條件下使至少一部分所述一種或多種熱解產物進行催化反應。在一些情況下,在第二反應器中使至少一部分所述一種或多種熱解產物進行催化反應后,該方法可包括在第二反應器中使來自第一反應器的至少一部分一種或多種流體產物進一步反應以制備一種或多種其他產物的步驟。多反應器構造中的一個或多個反應器可包括流化床反應器(例如,循環流化床反應器、湍動流化床反應器等)和固定床反應器(如軸向絕熱式固定床反應器、徑向絕熱式固定床反應器、列管式固定床反應器等),或在其他情況下任何其他類型的反應器(例如,上文提到的任何反應器)。例如,在一組實施方式中,第一反應器包括循環流化床反應器或湍動流化床反應器,且第二反應器包括與第一反應器流體連通的循環流化床反應器或湍動流化床反應器。另外,多反應器構造可包括本文提到的任何附加加工步驟和/或設備(例如,固體分離器、再生器、冷凝器等)。可利用本文提到的任何加工參數(例如,溫度、停留時間等)操作反應器和/或附加加工設備。本發明中可用的有機材料可包括例如木糖醇、木糖、木聚糖、葡萄糖、纖維二糖、纖維素、淀粉、半纖維素、殼聚糖、甲殼素、蔗糖、果糖、木材、甘蔗渣、毛竹、玉米秸桿、廢棄紙張、油菜籽餅、小桐子餅、餅粕、酒糟、廢棄蛋白、微藻之類的組分,及其熱解產物和此類組分和/或它們的熱解產物的組合。有機材料的其他實例尤其包括,例如塑料廢料、再生塑料、農業和城市固體廢物、食品廢物、動物廢物、碳水化合物、木質纖維材料(例如,木屑或刨花、木質纖維生物質等)或它們的組合。有機材料還包括液體材料,如葡糖糖水溶液、甲基呋喃、2,5-二甲基呋喃、糠醛、5-羥甲基糠醛、5-甲基糠醛、γ-戊內酯、纖維素生物油、水溶性生物油、非水溶性生物油等,或它們的組合。生物油(一般生物油)主要來自于熱解生物質原料產生的含氧碳氫化合物的濃縮液。將生物質在無氧或者缺氧條件下在適合溫度(450-650℃)進行熱解產生熱解氣,然后通過冷凝得到生物油。生物油是一種復雜的混合物,其中含有水,呋喃類化合物,乙酸、甲酸等有機酸,愈創木酚、丁香酚、苯酚、領苯二酚、香草醛等芳香類化合物。生物質主要包括上述原料。水溶性生物油主要來自于生物油水分離產物,將生物油與水按一定比率配制成混合物,然后將混合物在離心機中以一定轉速離心一段時間至分層,將上層倒出就是水溶性生物油,剩余部分是水不溶性生物油。如本文所示,有機材料和催化劑材料的選擇可用于改變所得流體產物的組成。如上所述,進料組合物中有機材料可包括固體、液體和/或氣體。在有機材料包括固體的情況下,固體可具有任何合適的尺寸。在一些情況下,使用具有較小粒度的有機材料固體可能是有利的。由于它們與較大固體相比具有較高的表面積/體積比,小顆粒固體在一些情況下可比較大固體反應快。另外,小粒度可實現在各顆粒內和/或反應器容積內更高效的熱傳遞。這可防止或降低不想要的反應產物的形成。另外,小粒度可提高固體-氣體和固體-固體接觸,從而改進熱和質量的傳遞。在一些實施方式中,固體有機材料的平均尺寸小于約5毫米,小于約2毫米,小于約1毫米,小于約500微米,小于約60目(250微米),小于約100目(149微米),小于約140目(105微米),小于約170目(88微米),小于約200目(74微米),小于約270目(53微米),或小于約400目(37微米)或更小。在一些情況下,希望使用平均粒度高于最小量的進料材料以降低使有機材料進料通過反應器所需的壓力。例如,在一些情況下,希望使用平均粒度為至少約400目(37微米),至少約270目(53微米),至少約200目(74微米),至少約170目(88微米),至少約140目(105微米),至少約100目(149微米),至少約60目(250微米),至少約500微米,至少約1毫米,至少約2毫米,至少約5毫米或更高的固體有機材料。可從本領域中已知的任何催化劑中選擇可用于本發明中的催化劑組分,或如了解本發明的本領域技術人員理解的那樣選擇可用于本發明的催化劑組分。在功能上,催化劑可能只受限于任何此類材料的能力,促進和/或影響脫水、脫氫、氨化、異構化、氫轉移、芳構化、脫羰作用、脫羧、醇醛縮合和/或其他任何與有機材料熱解過程相關的反應。如本領域技術人員理解的那樣,認為催化劑組分可為酸性、中性或堿性。在一些情況下,本文所述的催化劑顆粒可包括多晶固體(例如,多晶顆粒)。在一些實施方式中,催化劑顆粒還可包括單晶。在某些情況下,所述顆粒可為不同的可單獨的和分離的物理物體。在其他情況下,所述顆粒可為至少在其制備和/或使用中的多個單獨的顆粒的某些點相互緊密接觸形成的團塊。用于本文所述的實施方式中(例如,在進料流中,在反應器中等)的催化劑可具有任何合適的尺寸。在一些情況下,使用較小顆粒的催化劑是有利的,如先前所提到的,在一些實施方式中,所述催化劑顆粒可為包括多個成團的較大的催化劑顆粒物體形式。在一些實施方式中,例如,使用小催化劑顆粒可增加有機材料與催化劑表面位點接觸的程度,原因是外部催化表面積增加以及通過催化劑的擴散距離減小。在一些情況下,可至少部分基于例如所需的流體流的類型和催化劑的壽命來選擇催化劑尺寸和/或催化劑粒度。在一些實施方式中,在某些情況下包括單個的催化劑顆粒或在其他情況下包括多個顆粒的團塊的催化劑物體的平均直徑(通過常規的篩析所檢測)可為小于約5毫米,小于約2毫米,小于約1毫米,小于約500微米,小于約60目(250微米),小于約100目(149微米),小于約140目(105微米),小于約170目(88微米),小于約200目(74微米),小于約270(53微米),或小于約400目(37微米)或更小。在一些實施方式中,催化劑物體可為具有以下最大橫截面尺寸的顆粒或由其形成:小于約5微米、小于約1微米、小于約500nm、小于約100nm、約100nm至約5微米、約500nm至約5微米、約100nm至約1微米、或約500nm至約1微米。如先前所述,在某些情況下,具有前文所述范圍的尺寸的催化劑顆粒可成團而形成可分離的具有上一段所述范圍的尺寸的催化劑物體。本文所用的顆粒的“最大橫截面尺寸”是指顆粒的兩個邊界之間的最大尺寸。本領域普通技術人員能夠通過例如分析催化劑制劑的掃描電子顯微圖像(SEM)來測量顆粒的最大橫截面尺寸。在成團顆粒的實施方式中,當測定最大橫截面尺寸時應分開考慮顆粒。在這樣的情況下,通過建立各成團顆粒之間的虛構邊界并測量由這樣的邊界而產生的假定的個體化顆粒的最大橫截面尺寸來進行測量。在一些實施方式中,催化劑內較大量的顆粒的最大橫截面尺寸位于給定的范圍內。例如,在一些實施方式中,催化劑內至少約50%、至少約75%、至少約90%、至少約95%、或至少約99%的顆粒的最大橫截面尺寸為小于約5微米、小于約1微米、小于約500nm、小于約100nm、約100nm至約5微米、約500nm至約5微米、約100nm至約1微米、或約500nm至約1微米。在一些情況下,在特定范圍內具有最大橫截面尺寸的顆粒可占催化劑中較大比例的體積比。例如,在一些實施方式中,具有如下最大橫截面尺寸的顆粒:小于約5微米、小于約1微米、小于約500nm、小于約100nm、約100nm至約5微米、約500nm至約5微米、約100nm至約1微米、或約500nm至約1微米占所使用的所有催化劑的體積總和的至少約50%、至少約75%、至少約90%、至少約95%或至少約99%。在一些實施方式中,催化劑內的顆粒基本上具有相同尺寸。例如,催化劑可包括具有如下尺寸分布的顆粒:該尺寸分布使得顆粒的最大橫截面尺寸的標準差不大于顆粒的平均最大橫截面尺寸的約50%、不大于約25%、不大于約10%、不大于約5%、不大于約2%或不大于約1%。標準差(小寫的σ)是其在本領域中的常規含義,可如下計算:其中,Di是顆粒i的最大橫截面尺寸,Davg是所有顆粒的平均最大橫截面尺寸,n是催化劑內的顆粒數量。上述標準差與顆粒的平均最大橫截面尺寸之間的百分比比較可通過標準差除以平均值并乘以100%獲得。使用包括位于上述所選尺寸分布的顆粒的催化劑可導致由有機材料反應所產生的含氮芳香性化合物的產率和/或選擇性增加。例如,在一些情況下,相對于使用含有處于所需范圍之外的尺寸分布的顆粒的催化劑所產生的含氮芳香性化合物的量(例如,使用大比例的大于1微米、大于5微米等的顆粒),使用含有具有所需尺寸范圍(例如,上述任何尺寸分布)的顆粒的催化劑可導致反應產物中含氮芳香性化合物的量增加至少約5%,至少約10%,或至少約20%。可選地,單獨或與上述考慮相結合,根據孔徑可以選擇催化劑(例如,通常與沸石相關的介孔型和孔徑),例如小于約100埃、小于約50埃、小于約20埃、小于約10埃、小于約5埃或更小的平均孔徑。在一些實施方式中,可使用平均孔徑為約5埃至約100埃的催化劑。在一些實施方式中,可使用平均孔徑為約5.5埃至約6.5埃,或約5.9埃至約6.3埃的催化劑。在一些情況下,可使用平均孔徑為約7埃至約8埃或約7.2埃至約7.8埃的催化劑。本文所用的術語“孔徑”用于表示孔的最小橫截面直徑。孔的最小橫截面直徑可對應于與孔長度垂直地測得的最小橫截面尺寸(例如,橫截面直徑)。在一些實施方式中,“平均孔徑”或“孔徑分布”為X的催化劑是指催化劑內孔的最小橫截面直徑的平均值為約X的催化劑。應理解,本文所用的孔的“孔徑”或“最小橫截面直徑”是指本領域技術人員公知的Norman半徑調節孔徑。本領域普通技術人員會理解如何測定催化劑中的孔徑(例如,最小孔徑、最小孔徑的平均值)。例如,XRD可用于測定孔徑(例如,沸石孔徑)的其他技術包括,例如氦測比重術或低壓氬吸附技術。除非另有指明,否則本文中提到的孔徑為通過x-射線衍射測定的那些,其如上所述校正以反映它們的Norman半徑調節孔徑。在一些實施方式中,應用篩選法選擇具有適于轉化特定熱解產物分子的孔徑的催化劑。篩選法可包括確定進行催化反應的熱解產物分子的尺寸(例如,熱解產物分子的分子動力學直徑)。本領域普通技術人員可計算例如給定分子的動力學直徑。催化劑的類型則可如下進行選擇,使得催化劑的孔隙(例如Norman調節最小半徑)大到足以使熱解產物分子擴散至催化劑中和/或與催化劑反應。在一些實施方式中,可選擇催化劑使得它們的孔徑小至足以防止其他不希望反應的熱解產物進入和/或反應。非限制性地,一些這樣的和其他催化劑可選自天然存在的沸石、合成沸石及它們的組合。在一些實施方式中,如本領域技術人員理解的那樣,催化劑可為絲光沸石結構轉化(MordeniteFrameworkInverted,MFI)型沸石催化劑,例如ZSM-5沸石催化劑。任選地,此類催化劑可包括酸性位點。其他類型的沸石催化劑尤其包括鎂堿沸石、沸石Y、沸石β、絲光沸石、MCM-22、ZSM-23、ZSM-57、SUZ-4、EU-1、ZSM-11、(S)AlPO-31、SSZ-23。在其他實施方式中,可使用非沸石催化劑,例如,WOx/ZrO2、硫酸鋁等。在一些實施方式中,催化劑可包括金屬和/或金屬氧化物。合適的金屬和/或氧化物尤其包括,例如鎳、鉑、釩、鈀、錳、鈷、鋅、銅、鉻、鎵和/或它們的任何氧化物。在一些實施方式中,可將金屬和/或金屬氧化物浸入催化劑(例如,在催化劑的晶格結構的空隙中)。可將金屬和/或金屬氧化物摻入催化劑的晶格結構中。例如,在催化劑的制備過程中,可包括金屬和/或金屬氧化物,且金屬和/或金屬氧化物可占據所產生的催化劑(例如,沸石催化劑)的晶格部位。作為另一個實例,金屬和/或金屬氧化物可與沸石反應或否則與其相互作用,使得金屬和/或金屬氧化物取代沸石的晶格結構內的原子。在某些實施方式中,可使用包括鎵的絲光沸石結構轉化(MFI)沸石催化劑。例如,可使用鎵鋁硅酸鹽MFI(GaAlMFI)沸石催化劑。本領域普通技術人員熟悉可被認為是鋁硅酸鹽MFI沸石的GaAlMFI沸石,其中,一些Al原子被Ga原子取代。在一些情況下,沸石催化劑可為氫形式(例如,H-GaAlMFI)。在一些實施方式中,鎵鋁硅酸鹽MFI催化劑可為其中一些鋁原子被鎵原子取代的ZSM-5沸石催化劑。在一些情況下,鎵鋁硅酸鹽沸石催化劑中的Si摩爾數與鎵鋁硅酸鹽沸石催化劑中的Ga和Al的總摩爾數之比(即以Si:(Ga+Al)表示的摩爾比)可為至少約15:1、至少約20:1、至少約25:1、至少約35:1、至少約50:1、至少約75:1或更高。在一些實施方式中,使用沸石中Si的摩爾數與Ga和Al的總摩爾數之比如下的催化劑是有利的:約15:1至約100:1、約15:1至約75:1、約25:1至約80:1或約50:1至約75:1。在一些情況下,鎵鋁硅酸鹽沸石催化劑中的Si與鎵鋁硅酸鹽沸石催化劑中的Ga的摩爾比可為至少約15:1、至少約60:1、至少約120:1、至少約200:1、約30:1至約300:1、約15:1至約200:1、約15:1至約120:1、或約15:1至約75:1。鎵鋁硅酸鹽沸石催化劑中的Si與鎵鋁硅酸鹽沸石催化劑中的Al的摩爾比可為至少約10:1、至少約20:1、至少約30:1、至少約40:1、至少約50:1、至少約75:1、約10:1至約100:1、約10:1至約75:1、約10:1至約50:1、約10:1至約40:1、或約10:1至約30:1。另外,在一些情況下,可選擇催化劑的性質(例如,孔隙結構、酸性位點的類型和/或數量)以選擇性地制備所需產物。在一些實施方式中,可能希望使用一種或多種催化劑以建立雙峰孔徑分布。在一些情況下,可使用具有具有雙峰孔徑分布的單個催化劑(例如,主要含有5.9-6.3埃孔隙和7-8埃孔隙的單個催化劑)。在其他情況下,可使用兩種或多種催化劑的混合物以建立雙峰分布(例如,兩種催化劑的混合物,各催化劑類型包括不同范圍的平均孔徑)。在一些實施方式中,一種或多種催化劑的一種可包括沸石催化劑,且一種或多種催化劑的另一種包括非沸石催化劑(例如,介孔型催化劑、金屬氧化物催化劑等)。例如,在一些實施方式中,一種或多種催化劑(例如,沸石催化劑、介孔型催化劑等)的至少約70%、至少約80%、至少約90%、至少約95%、至少約98%或至少約99%的孔隙具有在第一尺寸分布或第二尺寸分布內的最小橫截面直徑。在一些情況下,一種或多種催化劑的至少約2%、至少約5%或至少約10%的孔隙具有在第一尺寸分布內的最小橫截面直徑;且一種或多種催化劑的至少約2%、至少約5%或至少約10%的孔隙具有在第二尺寸分布內的最小橫截面直徑。在一些情況下,第一尺寸分布和第二尺寸分布選自上文提供的范圍。在一些實施方式中,第一尺寸分布和第二尺寸分布彼此不同并且不重疊。非重疊范圍的一個實例是5.9-6.3埃和6.9-8.0埃,重疊范圍的一個實例是5.9-6.3埃和6.1-6.5埃。可選擇第一尺寸分布和第二尺寸分布以使范圍不彼此緊鄰,例如5.9-6.3埃和6.9-8.0埃的孔徑。范圍彼此緊鄰的一個實例是5.9-6.3埃和6.3-6.7埃的孔徑。作為一個具體實例,在一些實施方式中,使用一種或多種催化劑提供雙峰孔徑分布以同時制備含氮芳香性化合物和烯烴化合物。也就是說,一種孔徑分布可有利地制備較高量的含氮芳香性化合物,另一孔徑分布可有利地制備較高量的烯烴化合物。在一些實施方式中,所述一種或多種催化劑的至少約70%、至少約80%、至少約90%、至少約95%、至少約98%或至少約99%的孔隙具有約5.9埃至約6.3埃或約7埃至約8埃的最小橫截面直徑。另外,所述一種或多種催化劑的至少約2%、至少約5%或至少約10%的孔隙具有約5.9至約6.3埃的最小橫截面直徑;且所述一種或多種催化劑的至少約2%、至少約5%或至少約10%的孔隙具有約7埃至約8埃的最小橫截面直徑。在一些實施方式中,所述一種或多種催化劑的至少約70%、至少約80%、至少約90%、至少約95%、至少約98%或至少約99%的孔隙具有約5.9埃至約6.3埃,或約7埃至約200埃的最小橫截面直徑。另外,所述一種或多種催化劑的至少約2%、至少約5%或至少約10%的孔隙具有約5.9埃至約6.3埃的最小橫截面直徑;且所述一種或多種催化劑的至少約2%、至少約5%或至少約10%的孔隙具有約7埃至約200埃的最小橫截面直徑。在一些實施方式中,所述一種或多種催化劑的至少約70%、至少約80%、至少約90%、至少約95%、至少約98%或至少約99%的孔隙具有在第一分布和第二分布內的最小橫截面直徑,其中第一分布為約5.9埃至約6.3埃,第二分布與第一分布不同且不重疊。在一些實施方式中,第二孔徑分布可為約7埃至約200埃,約7埃至約100埃,約7埃至約50埃,或約100埃至約200埃。在一些實施方式中,第二催化劑可為介孔型的(例如,具有約2納米至約50納米的孔徑分布)。在一些實施方式中,雙峰孔徑分布可有益于使兩種或多種有機材料組分進料反應。例如,一些實施方式包括在反應器中提供包括第一組分和第二組分的固體有機材料,其中第一組分和第二組分不同。可用作第一組分或第二組分的化合物的實例包括本文所述的任何有機材料(例如,甘蔗渣、葡萄糖、木材、毛竹、玉米秸桿、纖維素、半纖維素、木質素或任何其他有機材料)。例如,所述第一組分可包括纖維素、半纖維素和木質素之一,且所述第二組分包括纖維素、半纖維素和木質素之一。該方法還包括在反應器中提供第一催化劑和第二催化劑。在一些實施方式中,所述第一催化劑可具有第一孔徑分布,且所述第二催化劑可具有第二孔徑分布,其中第一孔徑分布和第二孔徑分布不同且不重疊。第一孔徑分布可為例如約5.9埃至約6.3埃。第二孔徑分布可為例如約7埃至約200埃,約7埃至約100埃,約7埃至約50埃,或約100埃至約200埃。在一些情況下,所述第二催化劑可為介孔型的或無孔的。第一催化劑可選擇性地使第一組分或其衍生物進行催化反應以制備流體產物。另外,第二催化劑可選擇性地使第二組分或其衍生物進行催化反應以制備流體含氮芳香性產物。該方法還可包括在足以產生一種或多種熱解產物的反應條件下在反應器中熱解至少一部含有機材料,和用第一催化劑和第二催化劑使至少一部分熱解產物進行催化反應以制備一種或多種含氮芳香產物。在一些情況下,也可產生至少部分失活的催化劑。在一些實施方式中,與本文所述的實施方式聯用的方法包括提高組合物的催化劑與有機材料質量比,以提高可識別的含氮芳香性化合物的生成。如本文所示(代表但有別于某些現有催化熱解法),本文所述的制品和方法可用于制備分離的、可識別的含氮芳香性化合物,選自但不限于吡嗪、甲基吡嗪、吡啶、甲基吡啶、苯胺、甲基苯胺、吲哚、甲基吲哚及它們的組合。在一些實施方式中,可通過添加一種或多種另外的化合物來影響催化劑的反應化學。例如,將金屬添加至催化劑中可導致特定化合物的選擇性形成的轉變(例如,將金屬添加到氧化鋁-硅酸鹽催化劑中可導致生成更多CO)。另外,當流化流體包含氫時,可降低催化劑上形成的焦炭量。在一些實施方式中,催化劑可包括二氧化硅和氧化鋁(例如,沸石催化劑)。催化劑中的二氧化硅和氧化鋁可以以任何合適的摩爾比存在。在一些實施方式中,應用相對于氧化鋁的摩爾數具有更大摩爾數的二氧化硅(即高的二氧化硅與氧化鋁摩爾比)的催化劑是有利的。本發明人意外地發現,例如與本文所述的實施方式結合,高的二氧化硅與氧化鋁摩爾比可導致形成較大量的含氮芳香性化合物產物。例如,在一些情況下,進料組合物可包括至少約15:1、至少約30:1、至少約40:1、至少約50:1、至少約75:1、至少約100:1、至少約150:1或更高的二氧化硅與氧化鋁摩爾比。在一些實施方式中,使用二氧化硅與氧化鋁摩爾比為約15:1至約200:1、約30:1至約150:1、約50:1至約160:1、或約100:1至約150:1的催化劑是有利的。在一些實施方式中,催化劑和有機材料可以以任何合適的比率存在。例如,在進料組合物(例如,通過包括催化劑和有機材料的一個或多個進料流或通過分開的催化劑和有機材料進料流)包括催化劑和有機材料(例如,循環流化床反應器)的情況下,催化劑和有機材料可以以任何合適的質量比存在。作為另一實例,在一開始在反應器中裝載催化劑和有機材料的混合物(例如,間歇式反應器)的情況下,催化劑和有機材料可以以任何合適的質量比存在。在涉及循環流化床反應器的一些實施方式中,進料流中(即向反應器提供的包括固體催化劑和固體有機材料的組合物中)催化劑與有機材料的質最比可為至少約0.5:1、至少約1∶1、至少約2:1、至少約5:1、至少約10:1、至少約15:1、至少約20:1或更高。在涉及循環流化床反應器的一些實施方式中,進料流中催化劑與有機材料的質量比可為小于約0.5:1、小于約1:1、小于約2:1、小于約5:1、小于約10:1、小于約15:1或小于約20:1;或約0.5:1至約20:1、約1:1至約20:1、或約5:1至約20:1。應用較高的催化劑與有機材料質量比可有利于由進料材料熱解形成的揮發性有機化合物在熱分解成焦炭之前引入催化劑。當催化劑與有機材料的質量比小于約5:1時,主要產物為吡咯類化合物和吡嗪類化合物;當催化劑用量提高,吡咯類以及吡嗪類化合物選擇性下降,吲哚類化合物,苯胺類化合物以及吡啶類化合物提高。當催化劑與有機材料比例約10:1時,產物主要為吲哚類化合物和苯胺類化合物,提高二氧化硅與氧化鋁摩爾比,吡啶類化合物選擇性提高。不受任何理論限制,這種效應可至少部分是由于反應器中存在化學計量過量的催化劑位點而導致的。在一些實施方式中,如反應器為固定床反應器時,空速(液體進料與催化劑的質量歸一化比例)可以以任何合適的比率存在。例如進料為液體原料時,相對于單位催化劑體積的液體進料量(WHSV),以0.05至10的WHSV,如小于約0.05、小于約0.1、小于約0.2、小于約0.5、小于約0.8、小于約1、小于約1.5、小于約2、小于約5、小于約10進料至反應器。當WHSV大于約為2時,主要產物為吡咯類化合物,吡啶類化合物;隨著WHSV下降,吡咯類化合物選擇性降低,吲哚類化合物和苯胺類化合物選擇性提高。在一些實施方式中,本文所述的制品和方法構造成在例如在單級熱解設備中或另外可選的多級熱解設備中選擇性地制備含氮芳香性化合物。流體產物可包括例如含氮芳香性化合物的量占固體有機材料的總反應產物的至少約10wt%,至少約15wt%,至少約20wt%,至少約25wt%,至少約30wt%,至少約35wt%,至少約39wt%,約10wt%至約40wt%,約10wt%至約35wt%,約15wt%至約40wt%,約15wt%至約35wt%,約20wt%至約40wt%,約20wt%至約35wt%,約25wt%至約40wt%,約25wt%至約35wt%,約30wt%至約40wt%,或約30wt%至約35wt%。上述化合物產率以碳產率計即通過將產物中的碳摩爾數除以進料中的碳摩爾數來計算碳產率。以給定產物中的碳摩爾數除以所有產物(不包括CO、CO2和焦炭(例如,留在催化劑上的固體焦炭))中的碳摩爾數來計算選擇性。應指出,本領域普通技術人員能夠在重量百分比和碳產率之間進行轉換。例如,可通過化學分析測定碳質材料進料中的碳量。此外,可利用它們的分子式計算各反應產物的碳百分比。本文所用的術語“含氮芳香性化合物”用于表示包括一個或多個具有芳香性環基,例如單芳環體系(例如吡嗪、吡啶、吡咯等)和稠多環芳環體系(例如吲哚等)的烴化合物。含氮芳香性化合物的實例包括但不限于,吡嗪、2-甲基吡嗪、2,5-二甲基吡嗪、2,6-二甲基吡嗪、吡啶、2-甲基吡啶、3-甲基吡啶、4-甲基吡啶、、二甲基吡啶、吡咯、2-甲基吡咯、3-甲基吡咯、2,5-二甲基吡咯、吲哚、1-甲基吲哚、2-甲基吲哚、3-甲基吲哚、2,8-二甲基吲哚、苯胺、鄰甲基苯胺、間甲基苯胺、對甲基苯胺、二甲基苯胺等或它們組合中一種或幾種。在一些實施方式中,可制備單環和/或更多環的含氮芳香性化合物。含氮芳香性化合物可具有例如C5-C14、C6-C8、C6-C12、C8-C12、C10-C14的碳數,N1-N2、N3-N4、N5-N6的氮數。吡嗪類化合物可以作為重要的醫藥中間體和香精香料中間體,也是一種具有高附加值的精細化學品。吡啶及其衍生物是非常重要的化工中間體,廣泛應用于醫藥、農藥、飼料、合成橡膠和印染工業,還可用于表面活性劑和食品添加劑的生產。吡咯類化合物作為精細化工產品的重要中間體在醫藥、食品、農藥、日用化學品、涂料、紡織、印染、造紙、感光材料高分子材料等領域具有廣泛用途。吲哚是基本化工原料,廣泛用于醫藥、農藥、染料、食品以及香料等眾多領域。苯胺是一種重要的工業化學品,可作為橡膠硫化促進劑、染料、媒染體、藥品、炸藥原料,和二苯基甲烷聚氨酯(MDI)。在本發明的一些實施方案中,可以將以上含氮芳香性化合通過本領域公知的方法分離,例如可以采用蒸餾(包括常壓蒸餾、減壓蒸餾、分子蒸餾)、精餾、柱層析色譜法、酸抽提法、離子變換色譜法、萃取法等方法。在本發明中,根據不同的催化方法可以有選擇性地制備不同化合物。首先可以根據化合物的本身物性參數(見表一)進行蒸餾,可以得到不同溫度的餾分。如吡嗪類餾分,吡咯類餾分,吡啶類餾分、苯胺類餾分和吲哚類餾分。然后再進行精餾分離產物得到更高純度的產品。有些化合物之前沸點相差很低,如2-甲基吲哚與3-甲基吲哚,可以根據其極性大小,采用柱層析色譜法等進行分離。有些化合物之間沸點相近,但是分子量相差很大,可以采用分離蒸餾方法。另外,在一些實施方式中,可選擇促進含氮芳香性化合物的選擇性制備的催化劑。例如,在一些情況下,ZSM-5可優先制備較高量的含氮芳香性化合物。在一些情況下,包括Bronstead酸位點的催化劑可促進含氮芳香性化合物的選擇性制備。另外,具有良序孔隙結構的催化劑可促進含氮芳香性化合物的選擇性制備。例如,在一些實施方式中,平均孔徑為約5.9埃至約6.3埃的催化劑可特別用于制備含氮芳香性化合物。另外,平均孔徑為約7埃至約8埃的催化劑可用于制備烯烴。在一些實施方式中,使用一個或多個上述工藝參數的組合以促進含氮芳香性化合物的選擇性制備。制成的含氮芳香性化合物與烯烴的比例可為例如約0.1:1至約10:1、約0.2:1至約5:1、約0.5:1至約2:1、約0.1:1至約0.5:1、約0.5:1至約1:1、約1:1至約5:1、或約5:1至約10:1。實施例在以下實施例中,對于反應產物的表征主要采用氣相色譜法,氣相色譜-質譜法,其中,主要使用杭州科曉儀器制造的GC-1690氣相色譜儀,采用30m×0.25mm×0.25μm色譜柱,以10℃/min程序升溫至280℃。氣相-質譜聯用儀主要使用美國ThermoTraceGCUltrawithanISQimassspectrometer,采用TR-35MS色譜柱(30m×0.25mm×25um),檢測方法是在40℃保持3min,然后以5℃/min升溫至180℃,再以10℃/min升溫至280℃。下列非限制性實施例和數據旨在說明與本發明的方法和/或組合物相關的各個方面和特征,包括通過本文所述的熱解法可獲得的各種化合物的選擇性制備,但并非列舉本發明的整個范圍。與現代技術相比,本發明的方法和組合物提供令人驚訝的、意外的結構和數據。盡管通過使用幾種催化劑和原料例證本發明的效用,但本領域技術人員會理解的是,用與本發明的范圍相當的各種其他催化劑材料和/或原料可獲得相當的結果。實施例1在此實施例中使用直徑34mm,長度300mm的石英管式反應器。在反應器中,催化劑由石英棉支承。將石英反應器裝在溫控爐中。在操作過程中,使用氨氣作為載氣,通過氣體流量計控制其流速。本實驗載氣采用NH3或者NH3/N2、NH3/He混合氣。粉狀原料與載氣流一起從石英管開口處流至熱解界面。液體產物從反應器流至冷凝器,氣體產物收集在氣體采樣袋中。使用氣相色譜儀分析液體和氣體產物。(模型反應圖見圖5)作為若干實施方式的代表,用粉狀催化劑和進料(<140篩目)進行實施例1-10中所述的催化熱解試驗。除非此實施例中另行說明,否則這些反應條件由上所述。通過物理混合碳水化合物進料和催化劑制得粉狀反應物。以葡萄糖與HZSM-5(Si/Al=25),制備催化劑與進料質量比為2的葡萄糖的物理混合物。還制備催化劑與進料質量比為2的纖維二糖/HZSM-5,纖維素/HZSM-5,木糖/HZSM-5,木糖醇/HZSM-5,木聚糖/HZSM-5,殼聚糖/HZSM-5,甲殼素/HZSM-5,蔗糖/HZSM-5,果糖/HZSM-5,產物分布GC/MS圖見附圖1。實施例2將催化劑添加到熱解工藝中顯著降低焦炭形成并提高相熱穩定產物的轉化率。測試6種不同催化劑用于葡萄糖的催化熱解,包括:γ-氧化鋁(γ-Al2O3),二氧化硅氧化鋁(SiO2-Al2O3),氧化鎢氧化鋯(WO3/ZrO2),硫酸二氧化鋯(SO42-/ZrO2),MCM-41,HZSM-5(Si/Al=63)。通過物理混合碳水化合物進料和催化劑制得粉狀反應物,本實驗催化劑與葡萄糖的用量比為2,反應溫度為550℃,氣體流速為200mi/min.催化劑與葡萄糖混合后研磨成粉末。催化劑結構極大地改變產物選擇性,利用HZSM-5催化劑可提高吡咯類化合物選擇性,利用SO42-/ZrO2可以提高吡嗪類化合物選擇性。實施例3該實施例研究了反應溫度對產物產率的影響。表4和表5表明隨著溫度的升高對氮雜環產物有所提高,但是隨著溫度升高吡咯類化合物的選擇性有所下降,吲哚類化合物和苯胺類化合物的選擇性會有所提高。實施例4該實施例研究了改變催化劑的二氧化硅與氧化鋁摩爾比的影響。這些實驗的條件如下:催化劑/進料質量比為5;催化劑,HZSM-5;反應溫度550℃;載氣速率200ml/min。使用葡萄糖作為這些實驗的原料。表6顯示不同二氧化硅與氧化鋁摩爾比對葡萄糖催化熱解的產物選擇性。如表6所示低硅鋁比可以提高吡咯的選擇性,硅鋁比提高有利于提高吡啶類化合物的選擇性。實施例5該實施例研究了改變催化劑與葡萄糖的進料量比對產物收率以及產物分布的影響。這些實驗的條件如下:催化劑,HZSM-5;反應溫度500℃;載氣速率150ml/min。使用葡萄糖作為這些實驗的原料。表7顯示作為二氧化硅與氧化鋁摩爾比的函數的葡萄糖催化熱解的產物選擇性。如表7所示,催化劑與進料量比分別為1、2、5、10、15、20。由表7和8表明,隨著催化劑用量的增加,吡咯類產物和吡嗪類產物逐漸降低,吲哚類產物逐漸增加。實施例6實施例研究了改變載氣中NH3與N2比率對產物收率以及產物分布的影響。這些實驗的條件如下:催化劑,HZSM-5;反應溫度500℃;以NH3與N2混合氣為載氣,載氣速率250ml/min。使用葡萄糖作為這些實驗的原料。本實驗載氣NH3/N2為0:1,1:19,1:9,1:4,1:1,4:1,19:1以及1:0.表9顯示NH3與N2分布對的葡萄糖催化熱解的產物選擇性。由表9表明,產物中含氮化合物與載氣中NH3有著很重要關系,隨著NH3量增加,相應含氮化合物的量也增加。實施例7催化劑中的金屬浸漬對產物產率存在影響。用金屬浸漬HZSM-5(二氧化硅與氧化鋁摩爾比為25)孔隙使產物選擇性移向CO和CO2,表明金屬可影響化學反應。不希望受到任何理論限制,金屬可提高脫碳和/或脫羧反應速率。對下列金屬進行測試。除了以下所述金屬,本專利還包含其他金屬如:In,Ru,Rh,Ir,Pt,Pd,Au,Re,Tl,La系。表10概述了摻雜金屬的HZSM-5上的葡萄糖催化熱解獲得的結果。利用兩種不同方法將金屬摻雜至HZSM-5中:干/濕法浸漬和離子交換。使用離子交換法浸漬的催化劑比使用干/濕法浸漬法浸漬的催化劑產生更高的吡咯類化合物和吲哚類化合物產率。實施例8催化劑孔徑同樣影響含氮雜環化合物的收率。使用葡萄糖作為這些實驗的原料。表11表示在幾種不同的沸石結構上催化熱解葡萄糖的碳產率數據。這些實驗的條件如下:催化劑,反應溫度500℃;載氣速率200ml/min,催化劑與葡萄糖進料比為5。從表11中的結果可以看出,孔徑接近ZSM-5有利于產生含氮雜環化合物。實施例9天然形成的生物質也可用于實驗中的原料通過催化熱解制備吡咯類化合物和吲哚類化合物。表12概述天然形成的生物質催化熱解的結果。木材、甘蔗渣、玉米秸稈、廢棄紙張、油菜籽餅、微藻使用HZSM-5催化劑熱解產生含氮化合物、不含氮化合物、產生氣體以及焦炭。這些結果表明,可以用天然形成的生物質催化熱解制備吡咯類化合物和吲哚類化合物等含氮化合物。實施例10通過物理混合碳水化合物進料和催化劑制得粉狀反應物。制備催化劑與進料質量比為10的HZSM-5/葡萄糖,HZSM-5/纖維素以及HZSM-5/木糖,木糖醇/HZSM-5,木聚糖/HZSM-5,果糖/HZSM-5,蔗糖/HZSM-5,殼聚糖/HZSM-5,甲殼素/HZSM-5混合物制備吲哚類產物和苯胺類化合物。這些實驗的條件如下:催化劑為HZSM-5;催化劑與進料量比為10,進料速度為0.2g/min。產物分布GC/MS圖見附圖2.實施例11上述實施例主要采用的試驗方法為流化床方式,催化劑與原來混合研磨后,制備成140篩目的粉末進樣;本實驗還可以采用固定床方式進樣,試驗方式如下:在此實施例中,使用直徑34mm,長度300mm的石英管式反應器,在反應器中填充HZSM-5催化劑以產生固定床,催化劑兩端由石英棉支承,將石英反應器裝在溫控爐中。在操作過程中,使用氨氣作為載氣,通過氣體流量計控制其流速。粉狀原料與氨氣載氣流一起從石英管開口處流至熱解界面。液體產物從反應器流至的冷凝器,氣體產物收集在氣體采樣袋中。使用氣相色譜儀分析液體和氣體產物。本實施例主要采用固定床分別制備吡嗪類化合物、吡咯類化合物、吲哚類化合物以及苯胺類化合物。實驗方法如下,分別制備催化劑質量分別為2g,5g和10g固定床反應器,將反應至于反應器中,反應原料隨載氣一同進入催化劑床層,液體產物流至冷凝器,氣體產物收集在氣體采樣袋中。使用氣相色譜儀分析液體和氣體產物。表14明制備含氮化合物,表15明液體中各種化合物的碳選擇性。實施例13上述實施例主要描述固體進樣方式,包括催化劑和反應原料混合后流動床反應方式和固定床反應方式;此實施例描述了固定床、流動反應器系統的使用。在此實施例中,使用直徑為10mm,長度為250mm的石英管式反應器。在此反應器中裝載一定量(0.01g-2.5g)HZSM-5催化劑以產生固定床,其由石英棉支撐,將石英反應器裝在高溫爐中。本實驗載氣采用NH3或者NH3/N2、NH3/He混合氣。反應原料為液體原料,通過質量流量控制器控制其流速。通過注射泵將液體原料引入載氣中進入反應器。液體產物從反應器流至冷凝器,氣體產物收集在氣體采樣袋中。使用氣相色譜儀分析液體和氣體產物。本實施例中,以空速(WHSV)即液體進料質量(g/h)除以催化劑重量(g)計算質量歸一化為空速。通過產物中的碳摩爾數除以輸入反應器的碳摩爾數,計算碳產率。作為若干實施方式的代表,進行實施例14-16中所述的催化熱解試驗。除非實施例中另行說明,否則這些反應條件由上所述。實施例14本實施例主要研究液體反應、原料的影響。這些實驗的條件如下:催化劑為ZSM-5,催化劑用量為1g,反應溫度500℃;載氣為NH3,載氣速率40ml/min。本實驗中纖維素生物油和生物油分別來自于500℃條件下熱解纖維素、楊木、微藻等得到。本實施例以松木和纖維素為代表,其他生物質同樣適用于本實驗原料要求。水溶性生物油主要來自于生物油水分離產物,生物油與水比率為1∶4配制成混合物,然后將混合物在離心機中以1000轉/分鐘轉速離心20分鐘,將上層倒出就是水溶性生物油,剩余部分是水不溶性生物油。(反應流程模型圖見圖6)實施例15本實施例主要以呋喃為模型化合物研究WHSV對產物分布的影響。實驗的條件如下:催化劑為HZSM-5(Si/Al=25),催化劑用量為1g,反應溫度500℃;載氣為NH3,載氣速率20ml/min。由表17可知,隨著WHSV變小,吡咯和甲基吡咯的選擇性下降,吡啶類化合物,吲哚類化合物以及苯胺類化合物的選擇性提高。由于生物油中主要化合物為呋喃基化合物,因此本實施例以呋喃為模型化合物。降低WHSV,使得反應更加充分產物向有利于吲哚方向產生,提高WHSV利于產生吡咯類化合物。實施例16本實施例主要以呋喃為模型化合物研究溫度對產物分布的影響。實驗的條件如下:催化劑為HZSM-5(Si/Al=25),催化劑用量為1g;載氣為NH3,載氣速率40ml/mm,WHSV是1h-1。本實施例的產物主要包括吡啶類化合物,吡咯類化合物,苯胺類化合物以及吲哚類化合物。由表18可知,溫度升高,吡咯和甲基吡咯的選擇性下降,吡啶類化合物,吲哚類化合物以及苯胺類化合物的選擇性提高。