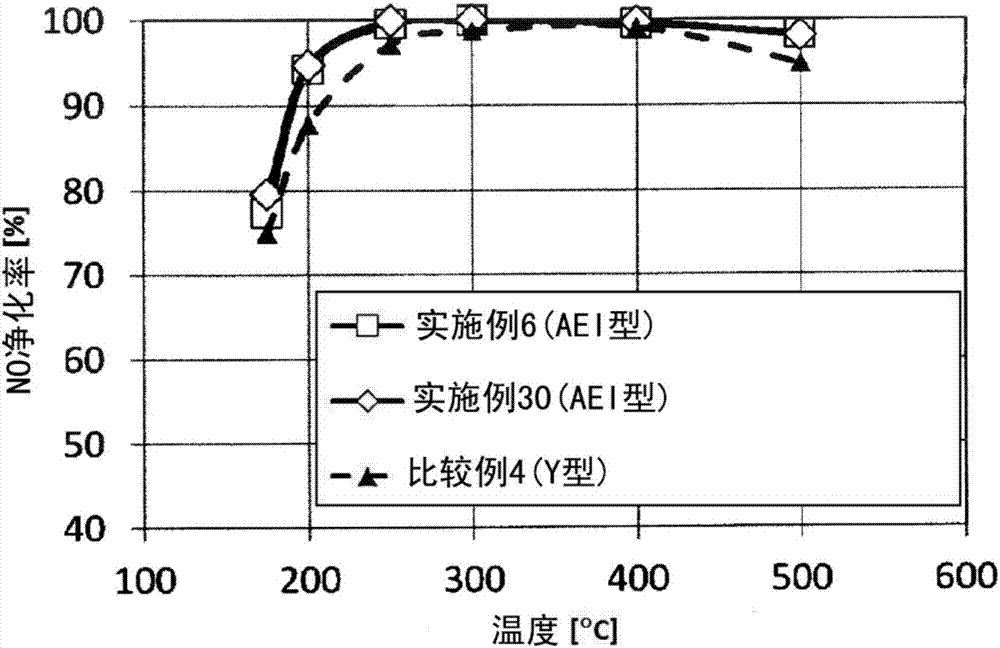
本發明涉及aei型沸石、aei型沸石的制造方法和aei型沸石的用途。具體地,本發明涉及通過不使用昂貴的y型沸石作為原料也不使用危險的氫氟酸制造便宜的、高性能的aei型沸石的方法,通過該方法制造的且具有高催化性能的aei型沸石,和aei型沸石的用途。
背景技術:
:具有基于來源自沸石的骨架結構的孔的分子篩效果以及如離子交換能力、催化能力和吸附能力等特性的沸石現在已經廣泛地用作吸附劑、離子交換劑、工業催化劑和環境催化劑。例如,已經開發了使用其上負載了如銅等金屬的沸石,具體地,cha型鋁硅酸鹽沸石和磷酸硅鋁(sapo)沸石的廢氣用催化劑。如aei型和cha型等標記是由國際沸石協會(iza)規定的定義沸石的骨架結構的代碼。已知aei型沸石具有與cha型沸石相同的沸石的孔尺寸,但具有催化活性更高的結構。aei型沸石用于選擇性催化還原(scr)催化劑中的實例詳細地記載于專利文獻1中。當用作汽車等的廢氣處理用scr催化劑時,特別是為了確實地進行如開始時的低溫操作時的廢氣的處理,已知能夠更優選地使用具有低的si/al比的催化劑。這是因為在鋁硅酸鹽系沸石的情況下,變為活性點的過渡金屬等的配位部位是鋁部位,因此,具有很多活性點的具有低si/al比的催化劑是更有利的。對于aei型沸石的通常的制造方法,記載于專利文獻2中的制造方法是基本的。在此情況下,在具體的制造方法中,例如,將作為有機結構導向劑(sda)的dmdmpoh(n,n-二甲基-3,5-二甲基哌啶鎓氫氧化物)添加至作為原料的y型沸石(骨架密度:)和膠體二氧化硅,并且將所得物在naoh的存在下攪拌并且進行水熱合成8天,由此獲得aei型沸石。在此專利文獻2中,記載的是,即使當使用硫酸鋁或氫氧化鋁等時,合成是可能的,但事實上通過在基本上全部實施例中使用y型沸石作為原料并且改變sda來進行實驗。另外,現在通常的技術常識是,當在通常的制造方法中不使用y型沸石時合成aei型沸石實際是不可能的。這通過在例如非專利文獻1等中的"雖然嘗試使用al(oh)3作為原料的合成,但沒有獲得結晶性氧化物"的記載來證實。在專利文獻1中,也使用y型沸石作為原料。專利文獻3公開了aei型沸石通過利用便宜的硝酸鋁作為原料制造aei型沸石的方法來獲得,所述方法包括將硝酸鋁和正硅酸乙酯(teos)與sda混合,然后添加氫氟酸。公開于專利文獻3中的方法是si/al比為200以上的aei型沸石的制造方法,其中氫氟酸的使用盡可能防止al進入沸石中。專利文獻4記載了aei型沸石從鋁氧化物獲得,但沒有記載aei型沸石能夠實際上在實施例等中制造。在專利文獻4中,使用稱為干燥凝膠轉換法的制造方法,其包括利用水蒸汽或包含揮發性有機胺的水蒸汽來處理通過干燥用于合成沸石的原料混合物而獲得的干燥凝膠,由此使沸石結晶。在此方法中,依然難以工業大規模制造均質沸石,并且期望能夠通過時間證明的水熱合成法進行制造。非專利文獻2公開了從含有磷的結構導向劑和含有y型沸石的原料合成aei型沸石的方法。然而,當磷化合物用作結構導向劑時,為了除去結構導向劑而焙燒合成的沸石可能產生有害的五氧化二磷,并且在通過如萃取等處理來除去磷的情況下,使工序復雜化。因此,使用含有磷的結構導向劑的方法是工業上不期望的方法。即使當使用各方法時,si/al比僅能夠降低至7左右。在專利文獻5中的比較例3中,記載了通過使用y型沸石作為原料來制造si/al比為5.5的aei型沸石;然而,僅可以獲得具有極其低的結晶性,例如在水熱耐久處理之后幾乎不具有活性的aei型沸石。因此,已經需要能夠制造具有任意的si/al比的aei型沸石的制造方法,特別是具有較低si/al比的aei型沸石,和該aei型沸石的制造方法。引用列表專利文獻專利文獻1:國際公開no.wo2013/159825專利文獻2:美國專利no.5958370專利文獻3:國際公開no.wo2005/063624專利文獻4:國際專利申請的國家公開no.2010-514662專利文獻5:國際公開no.wo2015/005369非專利文獻非專利文獻1:chemical,communications,48,8264-8266非專利文獻2:chemistryletters(2014),第43卷,第3號,第302-304頁技術實現要素:發明要解決的問題用于專利文獻3中的氫氟酸是非常危險的酸,另外,在溫度變高的水熱合成時使用氫氟酸在工業上是不切實際。如上所述,存在以下問題:鑒于y型沸石的成本,難以將y型沸石作為原料的使用應用于y型沸石例如汽車等的廢氣等中包含的nox的選擇性還原反應(scr)催化劑的大量使用。如上所述,已經需要能夠制造具有任意的si/al比和良好的結晶性的aei型沸石的制造方法,特別是具有較低si/al比的aei型沸石,和該aei型沸石的制造方法。本發明的目的是提供:通過不使用昂貴的y型沸石作為原料,也不使用危險的氫氟酸制造便宜的、高性能的aei型沸石的方法;通過該方法制造的且具有高催化性能的aei型沸石;和包括aei型沸石的催化劑。本發明的另一目的是提供:si/al比可以任意改變的aei型沸石的制造方法;另外,si/al比為6.5以下且具有良好的結晶性的aei型沸石。用于解決問題的方案作為深入研究通過不使用氫氟酸也不使用y型沸石的水熱合成法的aei型沸石的制造方法的結果,本發明人發現,使用骨架密度為以上的沸石作為原料之一能夠通過不使用y型沸石也不使用如氫氟酸等危險化學品以高產率獲得aei型沸石,通過該方法制造的aei型沸石與通過使用y型沸石作為原料獲得的傳統aei型沸石相比在催化活性方面較優異,可以制造具有任意si/al比的aei型沸石,并且也可以制造具有良好的結晶性且si/al比為6.5以下的aei型沸石,并且完成本發明。[1]一種aei型沸石的制造方法,所述aei型沸石的si/al比為50以下,所述方法包括:制備包含硅原子原料、鋁原子原料、堿金屬原子原料、有機結構導向劑和水的混合物的工序;和通過使用前述工序中獲得的混合物進行水熱合成的工序,其中所述鋁原子原料是si含量為20重量%以下且包含鋁的化合物;并且所述混合物以相對于所述混合物中的全部si原子形成sio2時的sio2為0.1重量%以上的量包括骨架密度為以上的沸石。[2]根據[1]所述的aei型沸石的制造方法,其中所述混合物中所述堿金屬原子原料中包含的堿金屬原子的50mol%以上是鈉;并且相對于所述有機結構導向劑的、所述混合物中的鈉的摩爾比為0.1以上且2.5以下。[3]根據[1]所述的aei型沸石的制造方法,其中所述混合物中所述堿金屬原子原料中包含的堿金屬原子的小于50mol%是鈉;并且相對于所述有機結構導向劑的、所述混合物中的堿金屬原子的總的摩爾比為1.0以上且10以下。[4]根據[1]至[3]任一項所述的aei型沸石的制造方法,其中所述鋁原子原料為選自由氫氧化鋁、硝酸鋁、硫酸鋁、氧化鋁、鋁酸鈉、勃姆石、假勃姆石、和烷氧基鋁組成的組的至少一種。[5]根據[1]至[4]任一項所述的aei型沸石的制造方法,其中在所述骨架密度為以上的沸石的骨架中包含由國際沸石協會(iza)定義為復合構造單元的d6r。[6]根據[1]至[5]任一項所述的aei型沸石的制造方法,其中所述骨架密度為以上的沸石為aei型和/或cha型。[7]根據[1]至[6]任一項所述的aei型沸石的制造方法,其中所述混合物中的所述有機結構導向劑是n,n-二甲基-3,5-二甲基哌啶鎓氫氧化物。[8]一種aei型沸石,其通過根據[1]至[7]任一項所述的aei型沸石的制造方法來獲得。[9]一種aei型沸石,其酸量為1.2mmol/g以上且3.0mmol/g以下且si/al比為6.5以下。[10]一種aei型沸石,其中通過29si-nmr求得的焙燒后的沸石的si/al比與si/al比的比{29si-nmr(si/al比)/xrf(si/al比)}為90%以上且200%以下;并且xrf(si/al比)為20以下。[11]根據[8]至[10]任一項所述的aei型沸石,其中所述aei型沸石以相對于鋁為0.001以上且1.0以下的摩爾比包含鉀和/或銫。[12]根據[8]至[11]任一項所述的aei型沸石,其中所述aei型沸石的平均一次粒徑為0.01μm以上且3μm以下。[13]根據[8]至[12]任一項所述的aei型沸石,其中所述混合物不包括fau型沸石。[14]一種aei型沸石,其中已經通過焙燒除去所述有機結構導向劑,所述aei型沸石的通過29si-nmr求得的si/al比為6.5以下。[15]一種催化劑,其包括根據[8]至[14]任一項所述的aei型沸石。[16]根據[15]所述的催化劑,其中除了si和al以外的金屬負載于所述aei型沸石上。[17]根據[16]所述的催化劑,其中cu負載于所述aei型沸石上。[18]根據[17]所述的催化劑,其中所述催化劑的cu含量為0.1重量%以上且10重量%以下。[19]根據[15]至[18]任一項所述的催化劑,其中所述aei型沸石包含鉀和/或銫;并且所述催化劑中鉀和/或銫相對于鋁的摩爾比為0.001以上且1.0以下。[20]根據[15]至[19]任一項所述的催化劑,其中所述催化劑是廢氣處理用催化劑。[21]根據[20]所述的催化劑,其中所述催化劑是用于含有氮氧化物的廢氣的選擇性還原催化劑。[22]一種催化劑的制造方法,所述方法包括:在通過根據[1]至[7]任一項所述的aei型沸石的制造方法獲得的aei型沸石上負載cu。[23]一種蜂窩狀催化劑,其中將根據[20]或[21]所述的催化劑涂布至蜂窩狀物。[24]一種催化劑成形品,其通過將根據[20]或[21]所述的催化劑成形來形成。[25]一種氮氧化物的凈化方法,所述方法包括:在根據[20]、[21]或[23]所述的催化劑的存在下使氮氧化物與還原劑接觸。[26]根據[25]所述的氮氧化物的凈化方法,其中所述還原劑是含氮化合物。[27]根據[26]所述的氮氧化物的凈化方法,其中所述含氮化合物是氨。[28]一種廢氣凈化系統,其包括包含根據[20]、[21]或[23]所述的催化劑的選擇性還原型氮氧化物凈化催化劑。[29]根據[28]所述的廢氣凈化系統,其中所述廢氣凈化系統包括所述選擇性還原型氮氧化物凈化催化劑的下游的氨氧化催化劑。[30]一種廢氣凈化方法,其包括在選擇性還原型氮氧化物凈化催化劑中吸附氨并且通過使用吸附的氨作為還原劑來選擇性地還原氮氧化物的工序,其中根據[20]、[21]或[23]所述的催化劑用作所述選擇性還原型氮氧化物凈化催化劑。[31]根據[30]所述的廢氣凈化方法,其中所述方法包括在通過使用所述氨作為還原劑來選擇性地還原氮氧化物的工序的下游將剩余的氨氧化的工序。發明的效果依照本發明,可以在不使用昂貴的y型沸石的情況下降低原料的成本并且在不使用危險的氫氟酸的良好的工作環境下獲得aei型沸石。此外,本發明中獲得的aei型沸石在催化特性方面優異,并且可以優選地用作廢氣處理用催化劑,特別是用作含有氮氧化物的廢氣的選擇性還原催化劑。另外,本發明的制造方法能夠獲得si/al比為6.5以下且具有優異的結晶性的aei型沸石,并且可以通過使用aei型沸石作為scr催化劑來獲得具有優異的廢氣凈化性能的催化劑。另外,本發明比使用y型沸石作為原料的情況的產率方面優異并且能夠使獲得的aei型沸石的si/al比在與傳統方法中相比更寬的范圍內。附圖說明[圖1]圖1是示出實施例1中合成的沸石1的xrd圖案的圖。[圖2]圖2是示出實施例6中的催化劑1a、實施例30中的催化劑2a、和比較例4中的催化劑3a的催化活性的評價結果的圖。[圖3]圖3是示出實施例6中的催化劑1b、實施例30中的催化劑2b、和比較例4中的催化劑3b的催化活性的評價結果的圖。[圖4]圖4示出實施例31中合成的沸石的29si-nmr光譜。具體實施方式以下將詳細地說明本發明的實施方案。然而,以下說明是本發明的方面的一個實例(代表實例),并且本發明完全不限于其內容。本發明的方面也可以適當組合。這里,使用“至”的范圍意味著包括“至”之前的數值和“至”之后的數值的范圍。[aei型沸石的制造方法]本發明的aei型沸石的制造方法是si/al比為50以下的aei型沸石的制造方法,所述方法包括:制備包含硅原子原料、鋁原子原料、堿金屬原子原料、有機結構導向劑和水的混合物的工序;和進行前述工序中獲得的混合物的水熱合成的工序,其中所述鋁原子原料是si含量為20重量%以下且包含鋁的化合物;并且所述混合物以相對于所述混合物中的全部si原子形成sio2時的sio2為0.1重量%以上的量包括骨架密度為以上的沸石。本發明的實施方案中制造的aei型沸石(下文中可以稱為"本發明的aei型沸石")對應于在用于定義由國際沸石協會(iza)規定的沸石的骨架結構的代碼中用于定義aei結構的代碼。結構由x射線衍射數據來表征。然而,在測量實際制造的沸石的情況下,測量受沸石的生長方向、構成元素的比、吸附的物質、缺陷的存在、和干燥狀態等影響,各峰的強度比和峰位置輕微地偏離,因此,沒有獲得與iza的定義中記載的aei結構的各參數精確相同的數值,并且10%左右的幅度在容許的范圍內。例如,在使用cukα線作為照射源的情況下,x射線衍射中的主要峰的實例包括:在2θ=9.5°±0.2°處110面的峰、在2θ=16.1°±0.2°處202和-202面的峰(它們彼此非常接近并且通常彼此重疊)、在16.9°±0.2°處022面的峰、和在20.6°±0.2°處310面的峰。作為由國際沸石協會(iza)定義的沸石的沸石優選為鋁硅酸鹽沸石。鋁硅酸鹽沸石包含至少氧(o)、鋁(al)和硅(si)作為其骨架結構中包括的原子,并且這些原子的一些可以由其它原子(me)取代。鋁硅酸鹽沸石的骨架結構中包括的me、al和si的構成比(摩爾比)沒有特別限制。然而,在相對于me、al和si的合計,me的摩爾比為x,al的摩爾比為y并且si的摩爾比為z時,x通常為0以上且0.3以下。在x為上限值以下的情況下,合成時抑制雜質的混入,并且優選該情況。進一步,y通常為0.001以上,優選0.005以上,更優選0.01以上,并且還更優選0.05,并且通常為0.5以下,優選0.4以下,更優選0.3以下,并且還更優選0.25以下。進一步,z通常為0.5以上,優選0.6以上,更優選0.7以上,并且還更優選0.75以上,并且通常為0.999以下,優選0.995以下,更優選0.99以下,并且還更優選0.98。當y和z在上述范圍內時,使合成容易,在使用沸石作為催化劑的情況下存在充分的酸點,并且易于獲得充分的活性。其它原子me可以以一種或以其兩種以上包括。優選的me是屬于周期表的第三或第四周期的元素。<骨架密度為以上的沸石>本發明的aei型沸石的制造方法的特征在于:不使用氫氟酸;使用si含量為20重量%以下且包含鋁的化合物作為鋁原子原料;并且添加骨架密度為以上的沸石(下文中,該沸石可以稱為"本發明中添加的沸石")。骨架密度為記載于ch.baerlocher等,atlasofzeoliteframeworktypes(sixthrevisededition,2007,elsevier)中的值,并且為表示骨架密度的值。換言之,骨架密度意指沸石的每單位體積中存在的t原子(沸石的骨架結構中包含的且除氧原子之外的原子)的數目,并且骨架密度的值取決于沸石的結構。對于通過使用骨架密度為以上的沸石來制造aei型沸石的工序中的作用和效果,推測該沸石在水熱合成之前的原料混合物中不完全分解為各元素的離子,而是以數個分子結合的胚芽(embryo)形式在混合物中處于溶解的狀態,并且輔助aei型沸石的水熱合成的進行。從抑制在原料混合物中完全分解為各單一元素的離子的角度,骨架密度為以上,優選以上,更優選以上,還更優選以上,并且特別優選以上。然而,因為過度高的骨架密度導致本發明中添加的沸石以不溶解的狀態存在于混合物中,所以本發明中添加的沸石的骨架密度為以下,更優選以下,還更優選以下,并且特別優選以下。從上述本發明中添加的沸石的作用機理的觀點,骨架密度為以上的沸石中,優選在骨架中包含由國際沸石協會(iza)規定為復合構造單元的d6r(雙6元環)的沸石。具體地,此類沸石是aei、aft、afx、cha、eab、eri、gme、kfi、lev、ltl、ltn、moz、mso、mww、off、sas、sat、sav、szr和wen,更優選aei、aft、afx、cha、eri、kfi、lev、ltl、mww和sav,還更優選aei、aft和cha,并且特別優選cha型和aei型沸石。本發明中添加的沸石可以一種單獨使用,或以其兩種以上的混合物使用。在本發明中,本發明中添加的沸石的量相對于除了本發明中添加的沸石以外的原料混合物中包含的全部硅(si)原子形成sio2時的sio2為0.1重量%以上,并且優選0.5重量%以上,更優選2重量%以上,還更優選3重量%以上,并且特別優選4重量%以上,以更順利地促進反應。本發明中添加的沸石的量的上限沒有特別限制,但通常為20重量%以下,優選10重量%以下,更優選8重量%以下,并且還更優選5重量%以下,以充分地獲得成本降低的效果。本發明中添加的沸石可以為水熱合成之后不焙燒的未焙燒產物或水熱合成之后焙燒的焙燒產物;然而,因為對于展現作為沸石的晶體的核的功能難以使沸石溶解在堿中是良好的,所以未焙燒產物的使用相對于焙燒產物的使用是優選的。然而,根據原料混合物中的組成或溫度條件,未焙燒的沸石可能不溶解并且可能不能展現作為晶體的核的功能。在此情況下,為了提高溶解性,優選使用通過焙燒除去sda的沸石。雖然在沸石的制造方法中通常見到通過添加晶種來改善產率的一些技術,但幾乎未知的是,像本發明一樣,通過將特定沸石添加至由其不能夠在原有基礎上制成期望種類的沸石的原料混合物,使得能夠制造期望種類的沸石。<鋁原子原料>在本發明中,因為鋁原子原料中的si的低含量通常使得在堿中的溶解性提高,使原料混合物均勻化,并且使結晶容易,所以使用si含量為20重量%以下、優選15重量%以下、更優選12重量%以下、并且還更優選10重量%以下且包含鋁的化合物。只要滿足該條件,鋁原子原料沒有特別限制,但優選為基本上不包括si的化合物,并且此類化合物是無定形氫氧化鋁、具有三水鋁礦結構的氫氧化鋁、具有三羥鋁石結構的氫氧化鋁、硝酸鋁、硫酸鋁、氧化鋁、鋁酸鈉、勃姆石、假勃姆石和烷氧基鋁。鋁原子原料特別優選無定形氫氧化鋁、具有三水鋁礦結構的氫氧化鋁和具有三羥鋁石結構的氫氧化鋁。其中,尤其優選無定形氫氧化鋁。這些可以一種單獨使用,或以其兩種以上的混合物使用。具有穩定的品質的這些原料是容易可得的,并且非常有助于作為本發明的有利效果之一的成本降低。從反應之前的混合物或通過使混合物熟化獲得的水性凝膠的制備的容易以及生產效率的角度,鋁原子原料的使用量以鋁原子原料中的鋁(al)與除了本發明中添加的沸石以外的原料混合物中包含的硅(si)的摩爾比計通常為0.02以上,優選0.04以上,更優選0.06以上,并且還更優選0.08以上。其上限沒有特別限制,但從將鋁原子原料均勻地溶解在水性凝膠中的角度,通常為2以下,優選1以下,更優選0.7以下,還更優選0.6以下,特別優選0.4以下,并且最優選0.2以下。<硅原子原料>用于本發明的硅原子原料沒有特別限制。作為此類硅原子原料,可以使用已知的各種物質,例如,可以使用骨架密度小于的沸石,優選除了沸石以外的包含硅的化合物,并且可以使用膠體二氧化硅、無定形二氧化硅、硅酸鈉、三甲基乙氧基硅烷、正硅酸乙酯、和鋁硅酸鹽凝膠等。這些可以一種單獨使用,或以其兩種以上的混合物使用。其中,優選處于能夠與其它組分充分均勻地混合的形式且特別在水中容易地溶解的原料,并且優選膠體二氧化硅、三甲基乙氧基硅烷、正硅酸乙酯和鋁硅酸鹽凝膠。硅原子原料以使各其它原料相對于硅原子原料的使用量在優選的前述和后述的范圍內使用。<堿金屬原子原料>用于本發明的堿金屬原子原料中包含的堿金屬沒有特別限制。用于沸石合成的已知的堿金屬可以用作此類堿金屬,并且優選包括選自由鋰、鈉、鉀、銣和銫組成的組的至少一種堿金屬離子。其中,出于以下原因,特別優選包括鈉。換言之,特別當沸石用作吸附劑或催化劑時,合成過程中進入沸石的晶體結構中的堿金屬原子可以通過離子交換從晶體內除去。在此情況下,為了使除去堿金屬原子的工序簡便,優選用于合成的堿金屬原子是鈉。因此,優選使堿金屬原子原料中包含的堿金屬原子的50mol%以上為鈉,更優選堿金屬原子原料中包含的堿金屬原子的80mol%以上為鈉,并且最優選基本上全部為鈉。相反地,當后述的有機結構導向劑的量降低至低水平時,優選使堿金屬原子原料中包含的堿金屬原子中的鈉為不超過50mol%,并且在此情況下,相對于有機結構導向劑的、原料混合物中的堿金屬原子的總的摩爾比優選為1.0以上且10以下。在此情況下,原料混合物中包含的主要堿金屬原子的優選實例包括僅鉀、僅銫、或鉀和銫的混合物。包括堿金屬原子使得結晶的進行容易并且抑制副產物(雜質晶體)的產生。可以使用的此類堿金屬原子原料的實例包括:上述堿金屬原子的如氫氧化物、氧化物、硫酸鹽、硝酸鹽、磷酸鹽、氯化物和溴化物等無機酸鹽,如乙酸鹽、草酸鹽和檸檬酸鹽等有機酸鹽。可以包括一種或兩種以上的堿金屬原子原料。堿金屬原子原料的適當量的使用,因為使得后述的有機結構導向劑以優選狀態配位至鋁,因此能夠使晶體結構的生成容易。特別地,當原料混合物中的堿金屬原子原料中包含的堿金屬原子的50mol%以上為鈉時,相對于有機結構導向劑的、原料混合物中的鈉的摩爾比優選為0.1以上且2.5以下,并且摩爾比的下限更優選0.15以上,還更優選0.2以上,特別優選0.3以上,并且尤其優選0.35以上,并且更優選2.4以下,還更優選2以下,特別優選1.6以下,并且尤其優選1.2以下。當堿金屬原子原料中包含的堿金屬原子的小于50mol%為鈉時,從堿金屬原子原料的適當量的使用因為使得后述的有機結構導向劑以優選狀態配位至鋁而也能夠使晶體結構的生成容易的觀點,優選以相對于有機結構導向劑的、原料混合物中的堿金屬原子的摩爾比為1.0以上且10以下的方式進行使用,并且該摩爾比更優選為1.3以上,還更優選1.5以上,特別優選1.8以上,并且尤其優選2.0以上,并且更優選8以下,還更優選6以下,特別優選5以下,并且尤其優選4以下。如上所述,在堿金屬原子原料中包含的堿金屬原子的小于50mol%為鈉的情況下,堿金屬原子原料的優選實例包括僅鉀原子原料、僅銫原子原料、及鉀原子原料和銫原子原料的混合物。在使用鉀原子原料和/或銫原子原料的情況下,沸石的產率趨于比僅使用鈉原子原料的情況更高。特別地,特別優選將鉀原子原料與銫原子原料混合。當使用鉀原子原料和/或銫原子原料時,鉀原子原料和/或銫原子原料殘留在aei型沸石中,并且獲得以相對于鋁的摩爾比為0.001以上且1.0以下包括鉀和/或銫的沸石。當包括鉀和銫時,摩爾比設定為鉀和銫的總量的摩爾比。在鉀和銫的總量在沸石中為重量%時,鉀和銫的總量通常為0.01重量%以上且10重量%以下,并且更優選0.05重量%以上且5重量%以下。關于此類沸石,在制造方法中,可以使用少量的有機結構導向劑,并且水熱合成時間可以是短的。<有機結構導向劑>如四乙基銨氫氧化物(teaoh)和四丙基銨氫氧化物(tpaoh)等已知的各種物質可以用作有機結構導向劑(也稱為"模板";下文中,有機結構導向劑可以稱為"sda")。另外,例如,以下物質可以用作記載于專利文獻2中的包含氮的有機結構導向劑。n,n-二乙基-2,6-二甲基哌啶鎓陽離子、n,n-二甲基-9-氮陽離子雙環[3.3.1]壬烷、n,n-二甲基-2,6-二甲基哌啶鎓陽離子、n-乙基-n-甲基-2,6-二甲基哌啶鎓陽離子、n,n-二乙基-2-乙基哌啶鎓陽離子、n,n-二甲基-2-(2-羥基乙基)哌啶鎓陽離子、n,n-二甲基-2-乙基哌啶鎓陽離子、n,n-二甲基-3,5-二甲基哌啶鎓陽離子、n-乙基-n-甲基-2-乙基哌啶鎓陽離子、2,6-二甲基-1-偶氮鎓[5.4]癸烷陽離子、和n-乙基-n-丙基-2,6-二甲基哌啶鎓陽離子等。其中,優選n,n-二甲基-3,5-二甲基哌啶鎓陽離子作為特別優選的包含氮的有機結構導向劑,并且具體地,優選使用n,n-二甲基-3,5-二甲基哌啶鎓氫氧化物。記載于非專利文獻2中的如四丁基鏻和二苯基二甲基鏻等物質可以用作包含磷的有機結構導向劑。然而,因為在如上所述將合成的沸石焙燒以除去sda時磷化合物可能生成作為有害物質的五氧化二磷,因此優選包含氮的有機結構導向劑。有機結構導向劑可以一種單獨使用,或以其兩種以上的混合物使用。從晶體生成容易的觀點,有機結構導向劑的使用量以相對于除了本發明中添加的沸石以外的原料混合物中包含的硅(si)的摩爾比計通常為0.01以上,優選0.03以上,優選0.08以上,更優選0.1以上,并且還更優選0.15以上。為了充分地獲得成本降低的效果,該摩爾比通常為1以下,優選0.8以下,更優選0.6以下,并且還更優選0.5以下。<水>從晶體生成容易的觀點,水的使用量以相對于除了本發明中添加的沸石以外的原料混合物中包含的硅(si)的摩爾比計通常為5以上,優選7以上,更優選9以上,并且還更優選10以上。該范圍進一步使晶體生成容易,并且是優選的。為了充分地獲得廢液處理所需要的成本降低的效果,相對于除了本發明中添加的沸石以外的原料混合物中包含的硅(si)的摩爾比通常為50以下,優選40以下,更優選30以下,并且還更優選25以下。<原料的混合(反應之前的混合物的制備)>在本發明的制造方法中,將通過將上述的鋁原子原料、硅原子原料、堿金屬原子原料、有機結構導向劑和水混合獲得的混合物與本發明中添加的沸石充分地混合,由此獲得反應之前的混合物,并且進行反應之前的混合物的水熱合成。包含本發明中添加的沸石的原料的混合順序沒有特別限制。然而,從優選地在制備堿溶液、然后添加硅原子原料和鋁原子原料的情況下原料更均勻地溶解的觀點,優選將水、有機結構導向劑和堿金屬原子原料混合以制備堿溶液,接著將鋁原子原料、硅原子原料和本發明中添加的沸石以所述順序添加至堿溶液并且將它們混合。在本發明中,除了上述的鋁原子原料、硅原子原料、堿金屬原子原料、有機結構導向劑、水和本發明中添加的沸石以外,變為有助于沸石合成的組分的輔助劑,例如,如促進反應的酸組分或如多胺等金屬穩定劑等其它添加劑可以按需要在任意工序中添加和混合,由此制備反應之前的混合物,或者如后所述,起到催化劑功能的如銅等金屬可以在水熱合成時添加。另外,在本發明中,從成本的觀點,優選不使用fau型沸石作為原料的制造。換言之,優選的是,在本發明的制造方法中,包含硅原子原料、鋁原子原料、堿金屬原子原料、有機結構導向劑和水的混合物不包括fau型沸石。<熟化>如上所述制備的反應之前的混合物可以在制備之后即刻進行水熱合成,但為了獲得具有高的結晶性的沸石,優選使得在預定溫度條件下進行預定時間的熟化。特別地,大規模化容易導致攪拌性的惡化和不充分的原料的混合狀態。因此,優選通過在攪拌原料一定時間的同時使原料熟化而改善原料以處于更均勻的狀態。熟化溫度通常為100℃以下,優選95℃以下,并且更優選90℃以下。其下限沒有特別設定,但通常為0℃以上且優選為10℃以上。熟化溫度可以在熟化期間是恒定的,或可以分階段地或連續地變化。熟化時間沒有特別限制,但通常為2小時以上,優選3小時以上,并且更優選5小時以上,并且通常為30天以下,優選10天以下,并且還更優選4天以下。<水熱合成>水熱合成通過以下來進行:將如上所述制備的反應之前的混合物或通過使該混合物熟化獲得的水性凝膠(下文中,"反應之前的混合物"或"通過使混合物熟化獲得的水性凝膠"可以稱為水熱合成之前的凝膠)放入耐壓容器中,并且在自己產生的壓力下或在不抑制結晶的水平的氣體加壓下,在攪拌下、在旋轉或搖動容器的同時,或者以靜置狀態,保持預定溫度。水熱合成中的反應溫度通常為120℃以上,通常為230℃以下,優選220℃以下,更優選200℃以下,并且還更優選190℃以下。反應時間沒有特別限制,但通常為2小時以上,優選3小時以上,更優選5小時以上,并且特別優選1天以上,并且通常為30天以下,優選10天以下,更優選7天以下,并且還更優選5天以下。反應溫度可以在反應期間是恒定的,或可以分階段地或連續地變化。在上述條件下的反應,因為使得目的aei型沸石的產率改善和不同種類的沸石生成的抑制,所以是優選的。<aei型沸石的回收>在上述水熱合成之后將作為產物的aei型沸石從水熱合成反應液分離。獲得的沸石(下文中稱為"包含sda等的沸石")在孔內包含有機結構導向劑和堿金屬原子二者或者任一者。將包含sda等的沸石從水熱合成反應液分離的方法沒有特別限制。通常,該方法的實例包括通過過濾、傾析或直接干燥等的方法。從水熱合成反應液分離和回收的包含sda等的沸石,為了除去制造時使用的有機結構導向劑等,可以按需要使用水來洗滌,干燥,然后進行焙燒等,由此獲得不包含有機結構導向劑等的沸石。當本發明的aei型沸石作為催化劑(涵蓋催化劑載體)或吸附劑等的用途而使用時,在按需要除去它們之后使用該沸石。<包含有機結構導向劑的濾液的循環>回收aei型沸石之后獲得的水熱合成反應液包含未反應的結構導向劑。通過液相色譜分析,確認的是,在本發明的aei型沸石的制造方法中,以堿金屬原子原料中包含的堿金屬原子的50mol%以上是鈉的方式包括約15重量%未反應的結構導向劑,和以堿金屬原子原料中包含的堿金屬原子的小于50mol%是鈉的方式包括約8重量%未反應的結構導向劑。通過使用包含此類未反應的結構導向劑的水熱合成反應液,可以添加不足的硅原子原料、鋁原子原料、有機結構導向劑和水來制備混合物,以使混合物具有與本發明的水熱合成之前的凝膠相同的加入(preparation)組成,并且可以進行混合物的水熱合成,由此制造aei型沸石。作為除去有機結構導向劑和堿金屬二者或任一者的處理,可以采用使用酸性溶液或包含用于分解有機結構導向劑的組分的化學品液體的液相處理、使用樹脂等的離子交換處理、或熱分解處理;或者這些處理可以組合使用。通常,包含的有機結構導向劑等可以通過例如在空氣、含有氧的非活性氣體或非活性氣體氣氛中在300℃至1000℃的溫度下焙燒或者使用如乙醇水溶液等有機溶劑的萃取等的方法來除去。從制造性的角度,優選通過焙燒來除去有機結構導向劑等。在此情況下,焙燒溫度優選為400℃以上,更優選450℃以上,并且還更優選500℃以上,并且優選為900℃以下,更優選850℃以下,并且還更優選800℃以下。氮等可以用作非活性氣體。在本發明的制造方法中,傳統上不能制造的具有寬范圍的si/al比的aei型沸石可以通過改變加入組成比來制造。因而,獲得的aei型沸石的si/al比沒有特別限制;然而,因為優選對于催化劑的更多的活性點,所以si/al比優選為50以下,更優選25以下,還更優選15以下,特別優選10以下,并且尤其優選7以下。特別地,si/al比為6.5以下且具有優異的結晶性的aei型沸石過去沒有獲得,為新的物質。相反地,當在骨架內包含大量的al的沸石暴露于包含水蒸汽的氣體時,骨架內的al更可能脫離,由此引起其結構破壞。因此,si/al比優選為2以上,更優選3以上,還更優選4以上,并且尤其優選4.5以上。考慮到全部因素,為了將骨架內al的脫離的影響降低至低水平并且維持高的催化活性,si/al比優選為5.5以上且7以下,更優選大于5.5且小于7,并且還更優選6以上且6.5以下。進一步,本發明中獲得的aei型沸石特別優選具有1.2mmol/g以上且3.0mmol/g以下的酸量和6以上且6.5以下的si/al比。在本發明中,如也記載于實施例中的,由si/al比和酸量規定的沸石的si/al比通過xrf來測量。除非另有規定,在本說明書中,si/al比是通過xrf求得的值。然而,可以使用icp的結果,這是因為如從由icp發射光譜分析(下文中可以稱為"icp")的分析結果確定xrf校正曲線的事實清楚的,從xrf獲得的si/al比和通過icp中的分析獲得的si/al比理論上彼此相等。在"xrf(si/al比)"的情況下,可以同樣地使用icp。在xrf中還測量以結晶性不良的狀態進入沸石骨架的al等。不包括此類結晶性不良的沸石的結晶性良好的沸石可以通過組合si/al比和酸量來規定。當測量在si和al以結晶性良好的方式進入沸石骨架中的情況下的si/al比時,優選通過29si-(dd/)mas-nmr(下文中可以稱為"29si-nmr")等來測量si/al比。在使用該29si-nmr測量的情況下,本發明的具有低si/al比的aei型沸石也可以簡單地表示為"si/al比為6.5以下的aei型沸石"。通過焙燒除去sda之后的aei型沸石的由29si-nmr求得的si/al比優選為6.5以下,并且在此情況下的si/al比的下限與上述范圍相同。作為塊體(bulk)的si/al比與焙燒之后由29si-nmr求得的si/al比之間的小的差也表示本發明的aei型沸石具有優異的結晶性。換言之,xrf中求得的焙燒之后的aei型沸石的si/al比是作為在水熱合成時或通過焙燒骨架已經破壞的部分中包含硅和鋁的塊體的si/al比,而焙燒之后29si-nmr中求得的si/al比是在焙燒之后還保持在沸石骨架中的硅與鋁之間的比。通常,脫鋁(dealuminization)更容易地發生。因此,29si-nmr(si/al比)/xrf(si/al比)以%計趨于為100%以上。特別地,在具有例如20以下的低si/al比的aei型沸石中,脫鋁容易地發生并且此值大于200%,這是因為沸石包括大量的鋁并且結晶性不良。相反地,本發明的aei型沸石,因為雖然具有低si/al比但結晶性良好,因此耐受甚至由于焙燒導致的脫鋁。這導致使用時的高耐久性的特性和優選使用該沸石作為催化劑的特性。具體地,aei型沸石的由29si-nmr求得的焙燒之后的沸石的si/al比與作為塊體的si/al比之間的比表示為以%計的{29si-nmr(si/al比)/xrf(si/al比)},并且其下限優選為90%以上,更優選95%以上,并且還更優選100%以上,并且其上限優選為200%以下,更優選190%以下,還更優選180%以下,并且特別優選160%以下。另外,此類沸石的si/al比的上限優選為20以下,更優選10以下,并且特別優選6.5以下,并且其下限優選為2以上且優選為4以上。scr催化劑需要包含氮氧化物的廢氣的凈化性能和650℃以上的水熱耐久性。具有低si/al比的沸石具有包含氮氧化物的廢氣的凈化性能高的優點,這是因為如果它們的結晶性之間沒有差異,則具有低si/al比的沸石的活性點與具有高si/al比的催化劑相比較多。例如,在卡車中,因為在700℃以下的相對低的溫度下在包含水蒸汽的氣體氣氛下作為scr催化劑使用,所以由于水蒸汽導致的骨架內al的脫鋁難以進行。因此,優先分配至包含氮氧化物的廢氣的凈化性能,并且期望使用在沸石骨架中具有大量的活性點且si/al比為6.5以下的沸石。相反地,具有高si/al比的沸石,因為沸石骨架中的al的量少,所以具有即使在包含水蒸汽的高溫氣體氣氛下也耐受沸石結構的破壞的優點。柴油車或汽油車,由于在800℃以上在包含水蒸汽的氣體氣氛下作為scr催化劑使用,所以需要高對水蒸汽的耐性。因此,期望使用si/al比大于6.5且更優選10以上的沸石。本發明中可獲得的aei型沸石的平均一次粒徑沒有特別限制,但為了提高用作催化劑時的氣體擴散性,優選為0.01至10μm,更優選0.02至8μm,并且還更優選0.05至5μm。特別地,本發明的aei型沸石的平均一次粒徑優選為0.01μm以上且3μm以下,并且從易于獲取的角度,優選在0.1至3μm的范圍內。aei型沸石的平均一次粒徑具體地通過記載于后述的實施例部分中的方法來測量。本發明中獲得的aei型沸石的比表面積沒有特別限制,但從更多的活性點存在于孔的內表面上的角度,優選為300至1000m2/g,更優選350至800m2/g,并且還更優選450至750m2/g。本發明的aei型沸石的比表面積通過bet法來測量。本發明中可獲得的aei型沸石的結晶性優異。這通過可以以160℃以上的氨的吸附量計測量的酸量而揭示。本發明的aei型沸石的酸量優選為0.5至3.0mmol/g,更優選0.7至3.0mmol/g,還更優選0.9至3.0mmol/g,特別優選1.2至3.0mmol/g,并且最優選1.2至2.5mmol/g。本發明的aei型沸石的酸量具體地通過記載于后述的實施例部分中的方法來測量。另外,特別優選的是,本發明中獲得的aei型沸石具有1.2mmol/g以上且3.0mmol/g以下的酸量和4.5以上且6.5以下的作為塊體的si/al比。本發明中制造的aei型沸石的離子交換能力可以通過將來源于堿金屬原子原料中或鋁原子原料、硅原子原料、有機結構導向劑和本發明中添加的沸石中包含的堿金屬原子的堿金屬部分轉換為h型或nh4型來使用,并且作為轉換的方法,可以采用已知技術。例如,可以采用通常在室溫至100℃下使用如nh4no3或nano3等銨鹽或者如鹽酸等酸的處理之后使用水清洗的方法。(堿土類金屬的添加)在本發明中,合成可以通過在合成時添加堿土類金屬來進行。通常已知的是,通過將堿土類金屬添加至沸石來改善耐水熱特性。在本發明的制造方法中,aei型沸石還可以通過將包含堿土類金屬的化合物添加至水熱合成之前的原料混合物來制造。作為堿土類金屬,可以使用鎂、鈣、鍶和鋇等,優選鎂或鈣,并且最優選鈣。堿土類金屬可以通常以化合物的形式來供給,所述化合物沒有特別限制并且其實例包括氧化物、氫氧化物和硫化物。優選添加氫氧化物形式的堿土類金屬。[aei型沸石的用途]本發明的aei型沸石的用途沒有特別限制。該用途的優選實例包括催化劑、吸附劑和分離材料。如上述專利文獻1中所述,aei型沸石特別優選用于例如凈化來自汽車等的廢氣的催化劑。特別地,6.5以下的si/al比獲得高催化活性。<通過后負載的金屬元素的耐水熱性的改善>改善本發明中獲得的aei型沸石的耐水熱性的方法的實例可列舉出在水熱合成之后的aei型沸石上或者在水熱合成之后的aei型沸石上負載用作后述的催化劑的金屬(例如,cu)的催化劑上進一步負載金屬(=m)的方法。作為為了改善耐水熱性而負載的金屬,可以使用任意的鎂(mg)、鈣(ca)、鍶(sr)、鑭(la)、鐠(pr)、硼(b)、鋯(zr)、鈰(ce)和鐵(fe)的任一種,或這些金屬可以以其兩種以上的混合物使用。包含金屬的aei型沸石還可以通過將金屬的鹽添加至aei型沸石的水熱合成之前的凝膠來制造。在此情況下,通常使用過渡金屬的如硫酸鹽、磷酸鹽、硝酸鹽、氯化物和溴化物等無機酸鹽和如乙酸鹽、草酸鹽和檸檬酸鹽等有機酸鹽,以及如五羰基化物(pentacarbonyl)和二茂鐵等有機金屬化合物等。所述鹽中,從在水中的溶解性的觀點,優選無機酸鹽和有機酸鹽。認為負載金屬的效果為通過金屬配位至沸石骨架中的鋁(al)獲得的由水蒸汽保護的效果。各金屬的含量以各金屬相對于鋁的摩爾比計為0.0001以上,優選0.0005以上,并且更優選0.001以上,并且還更優選0.005以上。其上限沒有特別限制,但因為在用作催化劑的情況下也需要進行變為活性點的過渡金屬的離子交換,所以通常為1以下,優選0.95以下,還更優選0.8以下,并且更優選0.5以下。<包含金屬的aei型沸石的合成方法>當將金屬負載于aei型沸石上時,如離子交換法或含浸法等方法的使用,因為引起排放大量廢液而趨于導致廢液處理的問題,并且因為需要浸漬了沸石的漿料的過濾和清洗等而導致工序數目的增加。相反地,本發明人發現了包含金屬的aei型沸石通過將作為金屬原料的金屬氧化物或金屬鹽導入合成沸石的工序中的凝膠中而在一個工序中合成的一鍋合成法。用于一鍋合成法中的金屬原料沒有特別限制。通常使用的金屬原料的實例包括金屬的如硫酸鹽、磷酸鹽、硝酸鹽、氯化物和溴化物等無機酸鹽,和金屬的如乙酸鹽、草酸鹽和檸檬酸鹽等有機酸鹽,以及如五羰基化物和二茂鐵等有機金屬化合物。其中,從在水中的溶解性的觀點,優選無機酸鹽和有機酸鹽。在一些情況下,優選膠體狀的氧化物或細粉末狀的氧化物。金屬沒有特別限制。從在吸附劑用途和催化劑用途中的特性的角度,金屬的典型實例包括第3至12族的金屬,例如鐵(fe)、鈷(co)、鎂(mg)、鋅(zn)、銅(cu)、鈀(pd)、銥(ir)、鉑(pt)、銀(ag)、金(au)、鈰(ce)、鑭(la)、鐠(pr)、鈦(ti)和鋯(zr),其中優選如鐵、鈷和銅等周期表的第8、9和11族的金屬,并且更優選第8和11族的金屬。沸石中包含的金屬可以為它們中的一種,或其兩種以上的金屬可以組合包含在沸石中。所述金屬中,特別優選鐵和/或銅,并且尤其優選銅。作為金屬原子原料,兩種以上的不同種類的金屬或化合物可以組合使用。為了使金屬在凝膠中穩定,還優選通過使用多胺來形成配鹽。作為用于形成配鹽的多胺,優選由通式h2n-(cnh2nnh)x-h(其中n為2至6的整數,并且x為2至10的整數)表示的多胺。在上述式中,n優選為2至5的整數,更優選2至4的整數,還更優選2或3,并且特別優選2,并且x優選為2至6的整數,更優選2至5的整數,還更優選3或4,并且特別優選4。作為此類多胺,尤其地,二亞乙基三胺、三亞乙基四胺、四亞乙基五胺是便宜且優選的,并且尤其地,三亞乙基四胺和四亞乙基五胺是特別優選的。多胺可以一種單獨使用,或以其兩種以上的混合物使用。可以包括支鏈狀多胺。當使用一鍋合成法時,除了使用金屬或者金屬和多胺以外,包含金屬的aei型沸石可以根據本發明的aei型沸石的制造方法來獲得。<廢氣處理用催化劑>當本發明的aei型沸石用作廢氣處理用催化劑,例如汽車廢氣凈化催化劑時,本發明的aei型沸石可以在原有基礎上使用,或者可以使用按需要使得包含金屬的aei型沸石。使沸石包含金屬的方法的具體實例包括如含浸、和液相或固相離子交換等方法。使得包含金屬的沸石也可以通過如上所述在水熱合成之前添加金屬(可以是單質或化合物)而直接合成。使得包含金屬的沸石中的金屬的存在狀態的實例包括在骨架結構中包含的情況或在骨架結構中不包含的情況。包含本發明的aei型沸石的催化劑可以與粘結劑混合、造粒和使用,或可以成形為如蜂窩狀等預定形狀并且使用。具體地,例如,催化劑與如二氧化硅、氧化鋁或粘土礦物等無機粘結劑或如氧化鋁纖維或玻璃纖維等無機纖維混合,然后造粒或通過擠出法或壓縮法等成形為如蜂窩狀等預定形狀,接著焙燒,由此獲得粒狀催化劑、蜂窩狀催化劑或催化劑成形品。催化劑也可以涂布至如片材或蜂窩狀物等基材,并且使用。具體地,例如,包含本發明的aei型沸石的催化劑與如二氧化硅、氧化鋁或粘土礦物等無機粘結劑混合以制造漿料,將該漿料涂布至使用如堇青石等無機物質制造的基材的表面上,并且焙燒,由此制造催化劑。優選地,在此情況下,可以通過將漿料涂布至具有蜂窩狀的基材上來獲得涂布有催化劑的具有蜂窩狀的蜂窩狀催化劑。在此情況下,使用無機粘結劑,這是因為通過將廢氣處理用催化劑作為實例而給出說明。然而,將領會的是,有機粘結劑可以根據用途或使用條件來使用。包含本發明的aei型沸石的催化劑,作為與包含氮氧化物的廢氣接觸以凈化氮氧化物的例如汽車廢氣凈化催化劑等的nox選擇性還原催化劑是有效的。在本發明的aei型沸石中包含除了si和al以外的金屬的廢氣處理用催化劑作為nox選擇性還原催化劑也是特別有效的。此類廢氣處理用催化劑的沸石中包含的金屬元素的優選實例包含過渡金屬,并且尤其選自鐵(fe)、鈷(co)、鈀(pd)、銥(ir)、鉑(pt)、銅(cu)、銀(ag)、金(au)、鈰(ce)、鑭(la)、鐠(pr)、鈦(ti)、和鋯(zr)等的組。金屬元素還更優選選自鐵或銅,并且最優選cu(銅)。這些金屬的兩種以上可以組合包含。除了si和al以外的金屬的含量在包含除了si和al以外的金屬的aei型沸石的總量中通常為0.1重量%以上,優選0.3重量%以上,更優選0.5重量%以上,并且特別優選1.0重量%以上,并且通常為20重量%以下,優選10重量%以下,并且更優選8重量%以下。特別地,當沸石中包含的金屬是銅(cu)時,催化劑中銅的含量優選為0.1重量%以上且10重量%以下,并且其更優選范圍如上所述。使本發明的aei型沸石包含上述金屬的方法沒有特別限制,并且其實例包括通過例如通常使用的離子交換法、含浸負載法、沉淀負載法、固相離子交換法、cvd法和噴霧干燥法,并且優選地通過固相離子交換法、含浸負載法和噴霧干燥法,在aei型沸石上負載金屬的方法。金屬原料沒有特別限制。通常使用的金屬原料的實例包括上述金屬的如硫酸鹽、硝酸鹽、磷酸鹽、氯化物和溴化物等無機酸鹽,和如乙酸鹽、草酸鹽和檸檬酸鹽等有機酸鹽,以及如五羰基化物和二茂鐵等有機金屬化合物。其中,從在水中的溶解性的觀點,優選無機酸鹽和有機酸鹽,更具體地,例如,優選硝酸鹽、硫酸鹽、乙酸鹽和鹽酸鹽等。在一些情況下,也可以使用膠體狀的氧化物或細粉末狀的氧化物。作為金屬原料,兩種以上的不同種類的金屬或化合物可以組合使用。在將上述金屬負載于aei型沸石上之后,優選的是在優選300℃至900℃,更優選350℃至850℃,并且還更優選400℃至800℃下進行焙燒1秒至24小時,優選10秒至8小時,并且還更優選30分鐘至4小時左右。不必須需要焙燒,但焙燒能夠提高負載于沸石的骨架結構上的金屬的分散性并且對于改善催化活性是有效的。根據本發明的實施方案的催化劑可以包括主要來源于原料的堿金屬原子,例如,鈉、鉀和銫等。其中,可以容易地除去的鈉沒有特別限制,但催化劑中的比較難以除去的鉀或銫等相對于鋁的摩爾比優選為0.001以上且1.0以下。換言之,從防止沸石骨架等通過從催化劑強制除去而損壞的角度,優選催化劑中的鉀和/或銫相對于鋁的摩爾比在上述范圍內。本發明中獲得的催化劑的比表面積沒有特別限制,但從更多活性點存在于孔的內表面上的觀點,優選為300至1000m2/g,更優選350至800m2/g,并且還更優選450至750m2/g。催化劑的比表面積通過記載于后述的實施例部分中的bet法來測量。<廢氣凈化系統>廢氣可以包含除了氮氧化物以外的組分,并且可以包含例如,烴、一氧化碳、二氧化碳、氫、氮、氧、硫氧化物和水。當使用催化劑時,可以使用已知的還原劑,例如,如氨、脲、肼、碳酸銨、氨基甲酸銨、碳酸氫銨和甲酸銨等含氮化合物(不包括氮氧化物)以及烴。具體地,從柴油汽車,汽油汽車,用于固定發電機、船舶、農業機械、建設機械、二輪車輛和航天器用的各種柴油發動機,鍋爐,和燃氣渦輪等排出的各種廢氣中包含的氮氧化物可以通過本發明的廢氣處理用催化劑而凈化。除了氮氧化物凈化用催化劑的用途以外,本發明的aei型沸石可以用于例如,在使用本發明的氮氧化物凈化用催化劑來凈化氮氧化物的后段工序中使在氮氧化物的凈化中消耗的剩余的還原劑(例如,氨)氧化的氧化催化劑的用途。以此方式,包含本發明的aei型沸石的催化劑作為氧化催化劑可以使剩余的還原劑氧化以減少廢氣中的還原劑。在此情況下,用于吸附還原劑的如鉑金屬等金屬負載于如沸石等載體上的催化劑可以用作氧化催化劑,并且可以使用本發明的aei型沸石用作載體或用作氮氧化物的選擇性還原催化劑的催化劑和在負載有例如鐵和/或銅的本發明的aei型沸石上進一步負載如鉑金屬等金屬的催化劑。包含本發明的aei型沸石的催化劑可以用于各種廢氣凈化系統中。該系統的實例可包括:包括包含本發明的催化劑的選擇性還原型氮氧化物凈化催化劑的廢氣凈化系統,并且氨氧化催化劑可以進一步配置在廢氣凈化系統中選擇性還原型氮氧化物凈化催化劑的下游。包含本發明的aei型沸石的催化劑可以用于各種廢氣凈化方法中。該廢氣凈化方法的實例包括:包括使得氨吸附于選擇性還原型氮氧化物凈化催化劑中并且使用吸附的氨作為還原劑來選擇性地還原氮氧化物的工序的廢氣凈化方法,其中包含aei沸石的催化劑優選地用作選擇性還原型氮氧化物凈化催化劑。在使用氨作為還原劑來選擇性地還原氮氧化物的工序的下游可以進一步包括使剩余的氨氧化的工序。可以使用的氨的實例包括:從外部導入廢氣凈化系統中的氨、和從外部導入廢氣凈化系統中的脲生成的氨。也可以使用廢氣凈化系統中從廢氣生成的氨。在使用本發明的催化劑的情況下,催化劑與廢氣之間的接觸條件沒有特別限制,但催化劑在廢氣的空間速度通常為100/h以上,優選1000/h以上,并且還更優選5000/h以上,并且通常為500000/h以下,優選400000/h以下,并且還更優選200000/h以下,并且溫度通常為100℃以上,更優選125℃以上,并且還更優選150℃以上,并且通常為1000℃以下,優選800℃以下,還更優選600℃以下,并且特別優選500℃以下的情況下使用。實施例以下將參考實施例具體地描述本發明。然而,本發明絕不限于下述實施例,除非偏離本發明的主旨。[分析/評價]通過以下方法進行下述實施例和比較例中獲得的沸石的分析和性能評價。[粉末xrd的測量]<樣品的制備>通過使用具有相同形狀的樣品保持器,使得用瑪瑙研缽以人力粉碎的約100mg沸石樣品具有恒定的樣品量。<設備規格和測量條件>粉末xrd測量設備規格和測量條件如下。[表1]<粉末xrd測量設備規格><測量條件>[通過29si-nmr的si/al比的測量]29si-nmr測量設備規格和測量條件如下。沸石骨架中的si/al比可以通過該方法來求得。[表2][平均一次粒徑的測量]本發明中的平均一次粒徑相當于一次顆粒的粒徑。通過測量在使用掃描電子顯微鏡觀察顆粒時任意選擇的30個以上的一次顆粒的粒徑并且通過將一次顆粒的粒徑平均,求得平均一次粒徑。將該粒徑作為具有等于顆粒的投影面積的面積的圓的直徑(圓當量直徑)。[cu含量和沸石組成的分析]作為標準樣品的沸石中的硅原子和鋁原子的含量和包含的銅原子的元素分析如下。沸石樣品通過加熱溶解在鹽酸水溶液中,接著通過icp分析求得硅原子、氯原子和銅原子的含量(重量%)。另外,制作標準樣品中的分析元素的熒光x射線強度和分析元素的原子濃度的校正曲線。基于該校正曲線,通過熒光x射線分析法(xrf)來求得包括沸石的催化劑樣品中的硅原子、鋁原子和銅原子的含量(重量%)。使用由horiba,ltd.制造的ultima2c(設備名)來進行icp分析。使用由shimadzucorporation制造的edx-700(設備名)來進行xrf。[bet比表面積的測量]使用由ohkurarikenin.制造的全自動粉末比表面積測量設備(設備名:ams1000)通過流通式單點法進行測量。[酸量:氨的吸附量的測量]通過使用由beljapan,inc.制造的全自動升溫脫附光譜設備(設備名:belcat-b,microtracbelcorp.制造),在以下條件下測量在沸石的評價中通常稱為酸量的氨的吸附量。使用的氣體:載氣:高純度he吸附氣體:5%nh3/he預處理:將沸石在50sccm的he流通下保持在450℃下1小時。nh3的吸附:使5%nh3/he在160℃下以50sccm流動15分鐘以使nh3吸附(至沸石)。脫附/測量:將溫度在50sccm的he流通下以10℃/min從160℃升高至800℃以使nh3脫附,并且將脫附的nh3的量作為氨的吸附量,即酸量。[icp的測量]將包含沸石的催化劑樣品使用氫氟酸水溶液處理,之后進一步通過加熱溶解在鹽酸水溶液中,接著通過誘導耦合等離子體(icp)發射光譜分析來求得鉀的含量。[催化活性的評價]將制備的催化劑樣品加壓成形,然后粉碎,通過篩子,并且整粒為0.6至1mm。將一毫升整粒的催化劑樣品填充至常壓固定床流通式反應管中。在使具有記載于以下表2中的組成的氣體以200000/h的空間速度sv流通經過催化劑層的同時,加熱催化劑層。當出口no濃度在175℃、200℃、250℃、300℃、400℃或500℃的各溫度下變為恒定時,基于以下值來評價催化劑樣品的氮氧化物除去活性:no凈化率(%)={(出口no濃度)-(出口no濃度)}/(入口no濃度)×100.[表3]氣體組分濃度no35oppmnh3385ppmo215體積%h2o5體積%n2除了以上組分以外的余量[催化劑的水蒸汽處理方法]為了評價水熱處理之后的催化活性,將800℃的10體積%的水蒸汽以3000/h的空間速度sv通過3g催化劑樣品5小時,并且進行水蒸汽處理。[沸石的合成][實施例1]向1.8g水、11.7g作為有機結構導向劑(sda)的n,n-二甲基-3,5-二甲基哌啶鎓氫氧化物(sachem,inc.制造)和0.3gnaoh(wakopurechemicalindustries,ltd.制造)的混合物中,添加、攪拌和溶解0.4g無定形al(oh)3(al2o3,53.5重量%,aldrichcorporation制造)以制成透明溶液。向該溶液中,添加5.5gsnowtex40(二氧化硅濃度為40重量%,nissanchemicalindustries,ltd.制造),在室溫下攪拌5分鐘,并且添加作為″本發明中添加的沸石″的0.1g作為未焙燒產物的aei型沸石(骨架密度為si/al=7,sar二氧化硅/氧化鋁的比為14)并且在室溫下攪拌2小時以獲得反應之前的混合物。將反應之前的混合物放入耐壓容器中,并且在170℃的烘箱中旋轉容器(15rpm)的同時進行水熱合成4天。在該水熱合成反應之后,將反應液冷卻,并且將生成的晶體通過液體的過濾而回收。在100℃下干燥回收的晶體12小時之后獲得的沸石粉末的xrd的測量確認,可以合成展現以晶格間距表示的、在表4中列出的位置處具有峰和相對強度的xrd圖案的aei型沸石1。圖1中示出沸石1的xrd圖案。在圖1中,縱軸表示強度(cps),而橫軸表示衍射角2θ(°)。基于xrf分析的沸石1的si/al比為6.1。[表4][實施例2]除了反應之前的混合物的原料的使用量在表10中列出以外,以與實施例1相同的方式來獲得沸石粉末。獲得的沸石粉末的xrd的測量確認,可以合成展現以晶格間距表示的、在表5中列出的位置處具有峰和相對強度的xrd圖案的aei型沸石2。基于xrf分析的沸石2的si/al比為5.8。[表5][實施例3]除了反應之前的混合物的原料的使用量在表10中列出以外,以與實施例1相同的方式來獲得沸石粉末。獲得的沸石粉末的xrd的測量確認,可以合成展現以晶格間距表示的、在表6中列出的位置處具有峰和相對強度的xrd圖案的aei型沸石3。基于xrf分析的沸石3的si/al比為5.2。[表6][實施例4]除了水熱合成的反應溫度(烘箱溫度)設定為135℃以外,以與實施例1相同的方式來獲得沸石粉末。獲得的沸石粉末的xrd的測量確認,可以合成展現以晶格間距表示的、在表7中列出的位置處具有峰和相對強度的xrd圖案的aei型沸石4。基于xrf分析的沸石4的si/al比為4.9。[表7][實施例5]將反應之前的混合物以與實施例1相同的方式來獲得,然后放入耐壓容器中,在90℃下進行熟化2天,然后在170℃的烘箱中旋轉容器(15rpm)的同時進行水熱合成4天。在該水熱合成反應之后,將反應液冷卻,并且將生成的晶體通過液體的過濾而回收。在100℃下干燥回收的晶體12小時之后獲得的沸石粉末的xrd的測量確認,可以合成展現以晶格間距表示的、在表8中列出的位置處具有峰和相對強度的xrd圖案的aei型沸石5。基于xrf分析的沸石1的si/al比為5.3。[表8][比較例1]除了不使用作為本發明中添加的沸石的aei型沸石(即,省略添加snowtex40,然后攪拌所得物5分鐘,并且添加aei型沸石的工序),反應之前的混合物的原料的使用量在表12中列出,將水熱合成的反應溫度(烘箱溫度)設定為135℃,并且將反應時間設定為7天以外,以與實施例1相同的方式來進行水熱合成。將產物回收并且干燥以獲得固體1。獲得的固體1的xrd的測量確認,沒有看到峰并且該固體是無定形的。[比較例2]除了不使用aei型沸石(即,省略添加snowtex40,然后攪拌所得物5分鐘,并且添加aei型沸石的工序)并且反應之前的混合物的原料的使用量在表12中列出以外,以與實施例1相同的方式來進行水熱合成。將產物回收并且干燥以獲得固體2。獲得的固體2的xrd的測量確認,沒有看到峰并且該固體是無定形的。[比較例3]向1.9g水、5.5gn,n-二甲基-3,5-二甲基哌啶鎓氫氧化物(sachem,inc.制造)和20.5g1m(mol/l)naoh水溶液(wakopurechemicalindustries,ltd.制造)的混合物中,添加,攪拌和溶解2.4gy型沸石(usy30cbv720,zeolystinternational制造)(骨架密度為)以制成透明溶液。向該溶液中,添加1.9gsnowtex40(二氧化硅濃度為40重量%,nissanchemicalindustries,ltd.制造)并且在室溫下攪拌2小時以獲得反應之前的混合物。將反應之前的混合物放入耐壓容器中,并且在135℃的烘箱中旋轉容器(15rpm)的同時進行水熱合成7天。在該水熱合成反應之后,將反應液冷卻,并且將生成的晶體通過液體的過濾而回收。在100℃下干燥回收的晶體12小時之后獲得的沸石粉末的xrd的測量確認,可以合成展現以晶格間距表示的、在表9中列出的位置處具有峰和相對強度的xrd圖案的aei型沸石6。基于xrf分析的沸石6的si/al比為7.3。[表9][實施例7至29,和31至38,和比較例5]實施例1中使用的原料和其投入量如表10至13中列出來改變,并且在表10至13中列出的水熱合成條件下以同樣的過程來合成沸石。然而,不可能合成比較例5中的沸石。用于合成的原料如下詳細地記載:koh:wakopurechemicalindustries,ltd.制造csoh:mitsuwachemicalsco.,ltd.制造cataloidsi-30:jgccatalystsandchemicalsltd.制造(二氧化硅濃度:30重量%)氣相法二氧化硅(aerosil200):nipponaerosilco.,ltd.制造將用于實施例1的aei型沸石用作作為焙燒產物的aei型沸石。骨架密度為的cha型沸石用作作為未焙燒產物的cha型沸石,并且通過在600℃下焙燒作為未焙燒產物的cha型沸石獲得的cha型沸石用作作為焙燒產物的cha型沸石。通過與后述的實施例30相同的方法來焙燒實施例35至38中獲得的固體,并且通過icp分析的其中ca量的結果為:實施例35:0.889重量%;實施例36:0.843重量%;實施例37:0.575重量%;和實施例38:0.482重量%。這表示鈣進入沸石中。[比較例6]根據專利文獻5的比較例3的記載來制造記載于專利文獻5的比較例3中的sio2/al2o3=11(即,si/al比為5.5)的aei型沸石。換言之,將純水、氫氧化鈉、fau型沸石(y型,陽離子型:銨型,sio2/al2o3比=11:日揮觸媒化成株式會社制造)和3號硅酸鈉(kishidachemicalco.,ltd.制造)添加至20%n,n-二甲基-3,5-二甲基哌嗪鎓氫氧化物(dmpoh)的水溶液,并且將所得物混合以獲得具有以下摩爾組成的原料混合物:sio2/al2o3比=31;na/sio2比=0.53;dmpoh/sio2比=0.16;oh/sio2比=0.69;和h2o/sio2比=46。將獲得的原料混合物填充至密閉容器中,并且在旋轉容器的同時,使原料混合物在135℃和15天的條件下結晶。將結晶后的原料混合物進行固液分離,使用純水來清洗,然后在70℃下干燥,并且將所得物在空氣氣氛和600℃下焙燒6小時。當獲得的aei型沸石的sio2/al2o3比通過xrf來測量時,該比為12(si/al=6),并且獲得的aei型沸石與專利文獻5的比較例3的aei型沸石基本上相同。當測量該沸石的酸量時,酸量為1.12mmol/g。低sio2/al2o3比和低酸量的結果意味著沸石的結晶性非常不良。這符合專利文獻5的第[0108]段中的"要理解的是,aei沸石的氮氧化物還原率在其進行1小時的水熱耐久處理時顯著降低"的記載。上述的實施例1至5、7至29和31至38以及比較例1至3、5和6中的反應之前的混合物中原料的使用量、水熱合成條件、產率、si/al比、酸量和平均一次粒徑總結于表10至13中。在表10至13中,各原料的量(g)下面的括號內的各數值表示以下:al(oh)3:除了本發明中添加的沸石以外的原料混合物中包含的al相對于si的摩爾比;堿金屬原子原料:在原料混合物中的堿金屬原子(na、k或cs)相對于sda的摩爾比;*在添加堿土類金屬的情況下,在原料混合物中的堿土類金屬原子(ca)相對于sda的摩爾比;sda:除了本發明中添加的沸石以外的原料混合物中包含的sda相對于si的摩爾比;水:除了本發明中添加的沸石以外的原料混合物中包含的水相對于si的摩爾比;添加的沸石(實施例):相對于除了本發明中添加的沸石以外的原料混合物中包含的全部si換算的sio2的量,本發明中添加的沸石的比例(重量%);和添加的沸石(比較例):相對于除了添加的沸石以外的原料混合物中包含的全部si換算的sio2的量,添加的沸石的比例(重量%)。產率(重量%)從以下等式來計算:(產率)=(包含sda的aei型沸石的重量(g))/{(制造時添加的鋁原子原料和硅原子原料分別換算的al2o3和sio2的重量(g))+(本發明中添加的沸石的重量(g))}×100。[催化劑的制備/催化活性的評價][實施例6]為了除去沸石中的有機物質,將實施例1中合成的沸石1在空氣氣流下在600℃下焙燒6小時。然后,為了除去焙燒的沸石中的na離子,將焙燒的沸石分散在3mnh4cl水溶液中并且在60℃下進行離子交換5小時。將沸石通過過濾來回收并且使用離子交換水洗滌三次。然后,上述的離子交換和洗滌進一步重復兩次。將獲得的沸石粉末在100℃下干燥12小時以獲得nh4型沸石1a。xrf中的沸石1a的分析結果確認,除去99%以上的na。乙酸銅(ii)水溶液通過將1gcu(oac)2·h2o(kishidachemicalco.,ltd.制造)溶解在37g水中來獲得。將沸石1a分散在乙酸銅(ii)水溶液中并且在40℃下進行離子交換1.5小時。通過過濾來回收沸石(沸石1b)并且使用離子交換水洗滌三次。然后,將1gcu(oac)2·h2o(kishidachemicalco.,ltd.制造)再溶解在37g水中以制備乙酸銅(ii)水溶液,并且將沸石1b分散在乙酸銅(ii)水溶液中并且在80℃下進行離子交換2小時。通過過濾來回收沸石(沸石1c)并且使用離子交換水洗滌三次以獲得沸石粉末,將該沸石粉末在100℃下干燥12小時,之后在空氣中在450℃下焙燒1小時,由此獲得包括含cu的aei型沸石的催化劑1a。基于xrf分析的催化劑1a的cu含量為3.9重量%。催化劑1a的bet比表面積的測量結果為601m2/g。另外,催化劑1a的催化活性的評價結果在表14和圖2中示出。[實施例30]為了除去沸石中的有機物質,將實施例26中合成的沸石26在空氣氣流下在550℃下焙燒6小時。然后,為了除去沸石中的na和k離子,將焙燒的沸石分散在3mnh4cl水溶液中并且在70℃下進行離子交換5小時。將沸石通過過濾來回收并且使用離子交換水洗滌三次。將獲得的沸石粉末在100℃下干燥12小時以獲得nh4型沸石26a。乙酸銅(ii)水溶液通過將2.2gcu(oac)2·h2o(kishidachemicalco.,ltd.制造)溶解在74g水中來獲得。沸石26a分散在乙酸銅(ii)水溶液中并且在70℃下進行離子交換2小時。通過過濾來回收沸石(沸石26b)并且使用離子交換水洗滌三次。然后,將2.2gcu(oac)2·h2o(kishidachemicalco.,ltd.制造)再溶解在74g水中以制備乙酸銅(ii)水溶液,并且將沸石26b分散在乙酸銅(ii)水溶液中并且在70℃下進行離子交換2小時。通過過濾來回收沸石(沸石26c)并且使用離子交換水洗滌三次以獲得沸石粉末,將該沸石粉末在100℃下干燥12小時,之后在空氣中在500℃下焙燒3小時,由此獲得包括含cu的aei型沸石的催化劑2a。icp中的催化劑2a的分析結果確認,殘存0.77重量%的k。基于xrf分析的催化劑2a的cu含量為4.8重量%。催化劑2a的bet比表面積的測量結果為579m2/g。另外,催化劑2a的催化活性的評價結果在表14和圖2中示出。.<通過29si-nmr的組成分析>對于計算存在于通過本發明的制造方法獲得的aei型沸石的沸石骨架中的si/al比,優選上述的通過si-nmr的分析。作為處于未焙燒狀態的實施例31中獲得的固體的29si-nmr分析的結果,發現該固體在骨架中的si/al比為4.9。在此情況下的測量結果在圖4中示出。對于峰的歸屬,在峰頂為-99±1ppm處的峰是q4(2al)、在-104±1ppm處的峰是q4(1al),并且在-110±1ppm處的峰是q4(0al)時,計算sar。相反地,在xrf中計算塊體狀態的si/al比,并作為xrf中的實施例31中獲得的固體的si/al比的計算的結果,發現si/al比為4.5。因此,29si-nmr和xrf中si/al比的分析結果顯示,該固體中的al原子的大多數存在于通過本發明的制造方法獲得的aei型沸石的沸石骨架中。作為焙燒實施例26的固體以除去sda之后的29si-nmr測量的結果,其骨架中的si/al比為5.6。在xrf中塊體狀態的si/al比為4.7,并且估計由焙燒導致輕微的脫鋁;然而,結晶性難以惡化。通常,認為具有低si/al比的沸石具有不良的骨架中的al的分散性。然而,本發明中獲得的沸石,雖然具有低si/al比,但通過29si-nmr的測量獲得的q4(1al)處的峰面積比例高,并且具有al分散的特征。1al的高比例使得變為催化劑的活性點的過渡金屬的導入容易。q4(0al)表示介由氧結合至si的al的存在率是0,并且其面積比例越大表示越難以導入過渡金屬。相反地,q4(nal)(n≥2)的峰表示存在兩個以上的介由氧結合至si的al原子,并且由于彼此接近的al原子的存在,認為預先配位的過渡金屬抑制過渡金屬與附近的al配位。因此,為了導入更多的變為催化劑的活性點的過渡金屬,q4(1al)的峰面積通常為44%以上,優選44.5%以上,更優選45%以上,并且還更優選45.5%以上。其上限沒有特別限制。對于傅里葉變換之后的各光譜峰,通過由洛倫茲(lorentz)波形、高斯波形或二者的混合制作的峰形狀的最優化計算來進行波形分離分析。在最優化計算中,通過使用中心位置、高度和半值寬度作為可變參數通過非線性最小二乘法來計算最優值。為了鑒別各峰,參考g.engelhardt和d.miche:"high-resolutionsolid-statenmrofsilicatesandzeolites",(1987),(johnwiley&sons,chichester).等。[比較例4]為了除去沸石中的有機物質,將比較例3中合成的沸石6在空氣氣流下在600℃下焙燒6小時。然后,為了除去焙燒的沸石中的na離子,將焙燒的沸石分散在3mnh4cl水溶液中并且在60℃下進行離子交換3小時。將沸石通過過濾來回收并且使用離子交換水洗滌三次。然后,上述的離子交換和洗滌進一步重復兩次。將獲得的沸石粉末在100℃下干燥12小時以獲得nh4型沸石6a。xrf中沸石6a的分析結果確認,除去99%以上的na。乙酸銅(ii)水溶液通過將1gcu(oac)2·h2o(kishidachemicalco.,ltd.制造)溶解在37g水中來獲得。將沸石6a分散在乙酸銅(ii)水溶液中并且在60℃下進行離子交換1小時。通過過濾來回收沸石(沸石6b)并且使用離子交換水洗滌三次。然后,將1gcu(oac)2·h2o(kishidachemicalco.,ltd.制造)再溶解在37g水中以制備乙酸銅(ii)水溶液,并且將沸石6b分散在乙酸銅(ii)水溶液中并且在80℃下進行離子交換1小時。通過過濾來回收沸石(沸石6c)并且使用離子交換水洗滌三次以獲得沸石粉末,將該沸石粉末在100℃下干燥12小時,之后在空氣中在450℃下焙燒1小時,由此獲得包括含cu的aei型沸石的催化劑3a。基于xrf分析的催化劑3a的cu含量為3.8重量%。催化劑3a的bet比表面積的測量結果為612m2/g。另外,催化劑3a的催化活性的評價結果在表14和圖2中示出。[表14]對于廢氣處理中認為重要的低溫區域中的活性,催化劑1a、催化劑2a和催化劑3a的在200℃下的反應之后的氣體中殘留的no濃度的比較揭示了,在催化劑1a和催化劑2a的情況下殘留no的濃度是在催化劑3a的情況下的一半以下。以上結果揭示了,本發明的aei型沸石的催化活性高于使用y型沸石作為原料的aei型沸石的。將通過借由上述方法進行催化劑1a、2a和3a的水蒸汽處理獲得的催化劑分別作為催化劑1b、2b和3b。催化劑1b、2b和3b的催化活性的評價結果在表15和圖3中示出。[表15]通常,廢氣處理用催化劑的水熱處理趨于導致作為活性點負載的cu的聚集,導致nh3的氧化的促進,以及導致高溫區域中活性的降低。然而,在此情況下進行了水熱處理的各催化劑在500℃下反應之后的氣體中殘留的no的濃度的比較揭示了,在催化劑1b和催化劑2b的情況下殘留no的濃度是在催化劑3b的情況下的一半以下。以上結果揭示了,即使在水熱處理之后在高溫區域中,本發明的aei型沸石的活性也高于使用y型沸石作為原料的aei型沸石的活性。認為這是因為本發明的aei型沸石的si/al比低于使用y型沸石作為原料的aei型沸石的si/al比,約兩個al原子配位至構成晶體結構的d6r,并且二價cu最優地配位至d6r,由此提高穩定性并抑制由于水熱處理導致的cu的聚集。產業上的可利用性本發明能夠獲得便宜、高性能的aei型沸石;并且沸石可以優選地用于廢氣處理以及催化劑或分離膜等。另外,可以提供si/al比為6.5以下且結晶性良好的aei型沸石,由此使用該沸石提供特別在低溫(例如,200至250℃)下尤其具有優異的凈化性能的高性能的催化劑。當前第1頁12