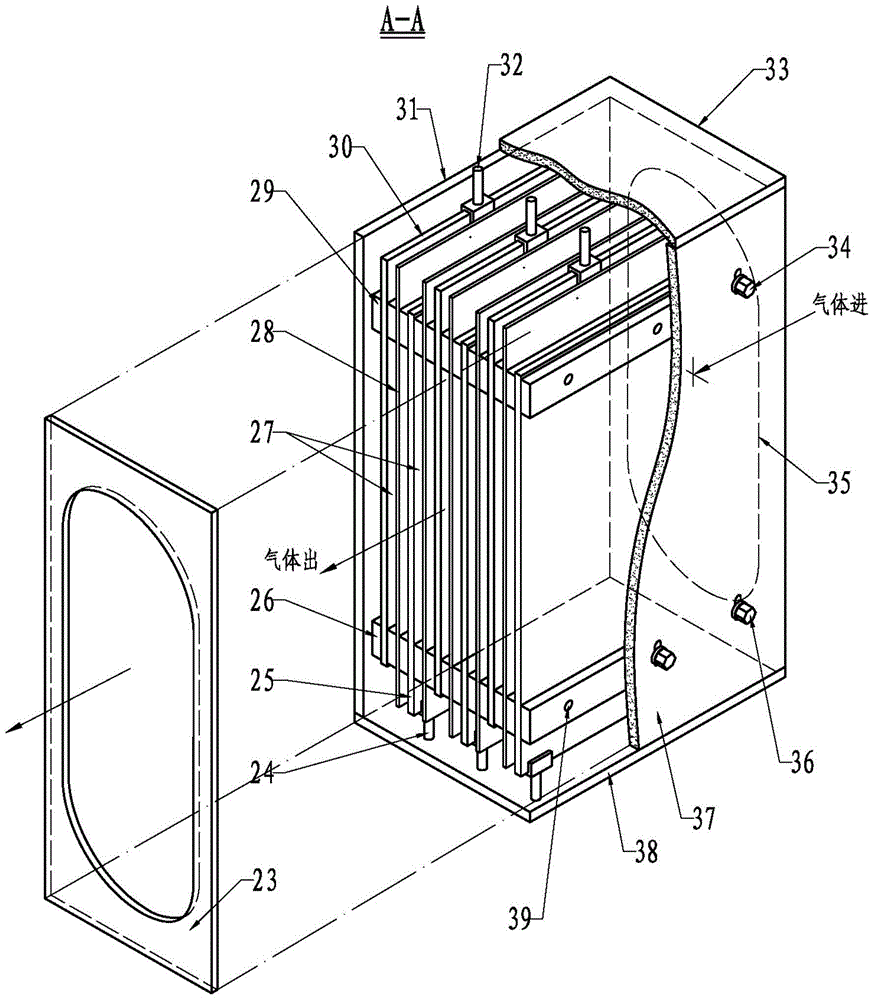
本專利涉及商用臭氧制備設備領域,更具體的說是一種自冷型臭氧發生器。
背景技術:臭氧是氧的同素異形體,是自然界最強的氧化劑之一。其氧化電位2.07V,與單質氟的氧化電位2.87V相比,氧化性能僅次于氟而位居第二位。臭氧作為一種高效、廣譜、快速的殺蟲劑,其殺菌能力是氯氣的300~600倍,具有消毒、殺菌、清洗、除臭、脫色的作用。此外還可以氧化去除水中或空氣中的微污染物質,很少產生副產物,無二次污染,綜合效果非常好。目前,已應用于室內空氣凈化、工業排放氣體凈化、半導體制造、化工、食品儲藏保鮮、飲用水殺菌、水廠或游泳池水處理及工業污水處理、水產養殖、醫療衛生等領域。但是,臭氧技術及設備未能廣泛應用和迅速發展的主要障礙,源于目前生產的工業臭氧發生器價格昂貴、體積龐大、耗能高、濃度及產量低、維保成本高等。臭氧技術的研究、設備的研制及工藝的探討在我國起步較晚。經過30多年的產業化發展,我國的臭氧生成技術有了很大的提高。無論是它的介電體材料、放電單元的結構、供氣設備、冷卻系統,還是供電電源、控制、檢測等技術都今非昔比,不僅提高了臭氧的產率,而且降低了能耗和改善了運行條件。目前,臭氧發生器大多采用介質阻擋放電法(無聲放電)。這樣的介質阻擋放電臭氧生成單元通常設計成長圓管狀,它能夠按需要進行串聯或并聯組合,從而滿足工業化大規模制備臭氧的需要。其內外兩平行且同軸的電極管之間隔以一層介電體管,并保持一定的放電間隙,內外電極常用水或油加以冷卻。另一種臭氧發生器屬于所謂板型發生器,其結構特點是具有一系列彼此間隔的平行空心電極板,空心電極板之間安置有介電體板并留有放電間隙,空心電極板內用水加以冷卻。在上述兩種傳統結構中,以一定速度流經于該放電間隙的氧分子O2在高頻高壓電形成的強電場作用下,受高能電子激發而獲得能量,并相互碰撞形成臭氧分子O3。這些典型的介質阻擋微放電臭氧發生器,在受高能電子激發放電產生臭氧的過程中,電能會在電暈氣隙內大量耗散。理論計算表明,臭氧生成所需能耗僅為0.82Kw?h/Kg?O3。事實上,現在普遍使用的介質阻擋放電臭氧發生器,當用氧氣源制造質量分數為21%的臭氧時,實際能耗為7Kw?h/Kg?O3左右。也就是說,電暈功率中僅僅只有11.7%的能量用于產生臭氧,其余88.3%的能量則以熱量形式損耗掉;當使用空氣源制造質量分數為21%的臭氧時,實際能耗為15.5Kw?h/Kg?O3,即電暈功率中僅僅只有5.3%的能量用于產生臭氧,近95%的電暈功率以熱量等形式損耗掉。這些氣體電離和介電體介質的能量耗散會使放電氣隙內氣體溫度急劇升高。由于生成臭氧的反應是可逆反應,因此已經生成的臭氧會在高溫下分解還原,如果工作氣隙內溫度得不到及時有效控制,會造成臭氧產量、濃度和電能利用率大幅度下降,并可能損壞相關器件。為了保證臭氧發生管高效穩定工作,提高臭氧產率,防止介電體熱擊穿,因此大規模工業臭氧發生器中,普遍采用水冷、油冷或者內外電極分別進行水冷和油冷。以便冷卻劑帶走熱量,防止其可逆反應帶來的臭氧產率、濃度下降及單位產量能耗增加。如前所述,氣體電離和介電體介質的能量耗散會使放電氣隙內氣體溫度升高,臭氧會在高溫下分解,從而直接影響臭氧的產量、濃度和能耗。因此快速地將這些熱量排出臭氧發生單元之外,也就成為保證已經生成的臭氧分子不被分解、臭氧發生器高效穩定工作,提高臭氧產率及濃度,降低能耗,防止介電體熱擊穿的關鍵問題。現在的臭氧發生器中,就其結構特點而言,無論是管式還是板式,它們都存在如下亟待解決完善的問題:其一:如果采用自來水非循環冷卻方式,按照發生10Kg/h臭氧所需冷卻水量計算。當工作氣源為氧氣源時,每天需要480立方米的冷卻水量。當工作氣源為空氣源時,每天需要960立方米的冷卻水量。可見資源的浪費嚴重,運行成本高,而且空排水存在對環境的二次污染。若采用自來水循環冷卻方式,則需要增加一系列熱交換等設備,勢必造成設備占空比增大,設備投資加大。重要的是,自來水溫度取決于環境溫度,波動很大,這對于臭氧發生器所要求的最佳冷卻水進水溫度來說,無疑是非常不利的。其二:如果采用地下水冷卻,需要打一口深井,其申報難度可想而知。就其設備來看,要增加水過濾器、深井潛水泵、儲水罐等一系列設備,導致設備占空比增大,投資加大。再加上地下水一般都具有硬度高,礦物質含量高,雜質多,易結垢等特點。這會造成臭氧發生器放電管的熱量無法快速排出,臭氧產量、濃度會大幅下降,能耗增加。嚴重時會損壞放電管,造成系統無法正常運行。頻繁的修理還會影響整個臭氧消毒系統運營效率、維保費用增加、運行成本加大等等。其三:如果采用油來冷卻電極,它是用油泵加壓使油經過有高壓電的電極并將此電極的熱量帶走,然后經過換熱設備冷卻油溫后再回到油箱形成循環。因為油的粘度大,必需要有足夠的功率把油壓加大到很高的壓力才能循環運轉,且需使用復雜昂貴的設備進行熱交換,從而導致投資增大。否則油溫得不到控制,這對于臭氧發生器所需的最佳冷卻油進油溫度要求來說,同樣是非常不利的。臭氧的產量、濃度和單位產量的能耗也都會受到很大影響。其四:理論計算表明,其他相應條件不變的情況下,提高電源的工作頻率能大幅度提高每個臭氧發生單元的臭氧產量和濃度。例如,一個臭氧發生器用50Hz交流電產生臭氧1g,若采用10000Hz交流電則能產生臭氧43g。但是每個臭氧發生單元放電空間里釋放的熱量也將會增加43倍。此時特別需要迅速地將此熱量排出。現有電源工作頻率一般設計為3000Hz左右,臭氧能耗、產量、濃度都難以達到較高的水平。其五:實驗結果表明,工作氣體的進氣溫度、露點對臭氧的產量、濃度有很大影響。尤其是工作氣體為空氣源時,溫度隨著環境、季節的不同而變化,若進入臭氧發生管的氣源溫度上升,會使放電氣隙內的工作氣體溫度升高。如果得不到有效控制,會導致臭氧濃度、產量明顯下降,單位產量能耗增加。此外,為了控制好氣源的溫度、露點,還需要對氣源進行預處理,這樣又增加了設備的投資。其六:理論計算表明,提高工作電源的電壓,由目前普遍采用的中低壓提升為中高壓,能使產生臭氧的電離放電折合電場強度達到350Td的左右,相應的等離子體中電子平均能量可達到9ev。這時的電子所具有的能量最適于O2的離解反應,臭氧濃度將提高到350mg/L或更高。可見電離電場強度電子平均具有能量是臭氧發生技術的關鍵參量。但是,通過提高電源工作電壓建立強場強放電氣隙場,會使臭氧發生單元內的溫度上升,這就更要求能快速將這部分熱量帶離放電區域。事實上,因為不能及時有效地排出這些熱量,即使采用綜合性能更好的材料作為介電體,也很難增大工作電源電壓。臭氧的濃度、產量仍然得不到大的提高。其七:現有的工業臭氧發生器普遍體積龐大,金屬材料消耗量大,材料及制造成本過高。對于臭氧用戶而言,設備投資相對昂貴,如果用作流動性設備,又過度笨重。
技術實現要素:針對以上所述臭氧發生器存在的問題,本發明致力于提供臭氧生成效率高,體積小的自冷型臭氧發生器。基于上述目的,本發明通過以下方案來解決所述技術問題。本專利公開一種自冷型臭氧發生器,其特征在于包括:用于制備臭氧的臭氧發生裝置;用于冷卻氣體的冷卻裝置;用于驅動氣體在臭氧發生裝置和冷卻裝置之間循環流動的循環裝置;所述臭氧發生裝置、冷卻裝置和循環裝置形成一封閉的內循環系統,該內循環系統具有導入工作氣源的工作氣源進氣管和導出臭氧的臭氧氣體導出管。不同于現有技術采用外界冷源對臭氧發生裝置進行冷卻的方式,本專利利用放電生成臭氧的工作氣體來對臭氧發生裝置進行自冷卻。通過冷卻裝置降低工作氣體的溫度,工作氣體流經臭氧發生裝置的同時,能夠將其熱量帶離臭氧發生區域,使其溫度下降,保證臭氧發生裝置的正常高效工作。采用該方法,無需在臭氧發生裝置內增加額外的冷卻裝置,可以大大縮小設備的體積,提高其穩定性。而且較低的溫度也有利于臭氧的生成,避免在高溫下臭氧還原為氧氣,保證所生成的臭氧濃度和穩定,可以在短時間內合成濃度高于現有設備的臭氧產品,特別適用于商用制備高濃度臭氧。另外,本專利是一個將工作氣源封閉在一個循環系統內進行多次反應的原理結構,工作氣源循環的時間越長,次數越多,則所生成的臭氧濃度越高,這就有利于商用設備對產品臭氧濃度的調節。具體的結構是,所述臭氧發生裝置為一個具有氣體出口和氣體進口的密閉箱體構成的臭氧發生源,所述臭氧發生源內部包括多個并排的介電體、地電極板和高壓電極板,所述介電體、地電極板和高壓電極板之間形成氣體放電通道。該結構有別于現有采用空心電極板的板形臭氧發生器,并在空心電極板內用水加以冷卻的結構。本專利由于直接采用工作氣體對地電極板和高壓電極板進行冷卻,則所述電極板無需采用空心結構。實心結構的電極板厚度可以大大下降,從而使得整個臭氧發生裝置體積縮小。介電體、地電極板和高壓電極板相間分布,其間自然形成氣體放電通道,可以提高工作氣體流動帶走熱量的效率。本專利的介電體采用非剛性材料,只要具有高的介電強度,優良的物理化學性能及機械性能,能夠平直張緊,均可以作為用于本發明所述臭氧發生器的介電體。介電體優選柔性聚合材料,所述地電極板和高壓電極板優選不銹鋼薄板,所述臭氧發生源上設有用于張緊介電體、地電極板和高壓電極板的張緊機構。該機構可將介電體、電極板張緊拉直,并保證各個介電體、電極板平直,且相互平行,間隙均勻。從而保證工作氣體能夠在間隙內高速流動。當氣流高速通過平直張緊的介電體一側時,介電體會有微小震動,這種震動不僅不會對生成臭氧產生負作用,介電體表面還會因微震形成一定程度的湍流,這種湍流恰恰有助于破壞介電體表面影響熱傳遞效率的氣流層,增強介電體的熱傳遞效率。所述介電體為Mylar柔性聚酯材料、Kapton聚酰亞胺或Lexan聚碳酸酯材料中的一種。這些材料都具有優良的機械性能、電氣性能、熱穩定性、抗臭氧氧化腐蝕性。介電強度是玻璃的十多倍甚至更高。因為不需要像傳統的臭氧發生器那樣,承受冷卻水的靜壓力,所述介電體的厚度一般選在0.05~0.20mm之間,這遠遠低于以往常用玻璃介電體的厚度。所述電極板材料的選擇原則是在臭氧中不易被氧化、腐蝕,例如不銹鋼或經過陽極化處理的鋁材之類的薄板。厚度在0.3~0.7mm之間,優選一般在0.50mm左右,這又大大小于傳統的板式臭氧發生器空心電極或管狀臭氧發生器鋼管電極的厚度。放電間隙對放電形態和放電空間的溫度均有很大影響。減小放電間隙,可以提高放電空間的冷卻效果,抑制臭氧的分解反應,提高臭氧生成效率,降低單位產量的能耗,所以,擬采用小間隙結構。所述介電體、地電極板與高壓電極板之間形成的放電間隙選在0.5~0.75mm之間。由于采用聚合物介電體替代玻璃介電體,其介電強度是玻璃的十多倍甚至更高,所述地電極板和高壓電極板之間的工作電壓在5KV~12KV內可調,頻率為5KHz~12KHz可調。在放電間隙一定的條件下,可以使放電間隙的電離折合電場強度達到很大。放電電場中的電子平均能量可以維持在很高的電子伏特水平,這種電子所具有的電子平均能量最適合于氧分子O2的離解反應,并且極大地抑制了低能電子的產生。這種條件下臭氧的生成可以在短時間內制備完成,臭氧濃度和產量可大幅度提高。所述地電極板和高壓電極板分別上下交錯連接有地電極接線端子和高壓電極接線端子,且使多個地電極接線端子設置在一端,而多個高壓電極接線端子設置在另一端。將接地端和高壓端子分設于不同的端面,有利于簡化接線結構,縮小設備體積。另外在商業化臭氧生成設備中,所述地電極板和高壓電極板經過一段時間的使用之后,會產生一定的氧化損耗,這就需要對地電極板或高壓電極板進行更換。上述這種接線結構十分方便設備的維護和維修。在使用過程中,當電源系統工作時,連接于高壓電極接線端子的高頻高壓交變電通過介電體的耦合極化作用,在臭氧發生源的放電間隙中建立起氣體放電電場,同時發生數目眾多的微放電。所述冷卻裝置可以采用通用的制冷設備,一般包括安裝有蒸發器的熱交換器、壓縮蒸發氣體的壓縮機、以及冷凝器和膨脹閥構成的制冷循環系統,所述熱交換器與臭氧發生裝置、循環裝置形成內循環系統。由于工作氣源的溫度初始值對臭氧的生成十分重要,并同時考慮到要在高速的流動下能夠帶走熱量,降低臭氧發生源的溫度,控制臭氧生成區域的環境,本專利所述熱交換器冷卻氣體的溫度控制在8~12℃之間。最佳的方案是將進入臭氧發生源之前的工作氣流溫度控制在10℃甚至更低,便可以控制臭氧發生源放電區域的工作氣體溫度在比較理想的范圍,這種溫度環境更適合氧分子O2的離解反應。為了提高熱交換效率,所述蒸發器包括多個蒸發單元,所述冷卻裝置還包括將制冷劑均勻分配至每個蒸發單元的制冷劑分配室。制冷劑分配室中安裝有制冷劑分液器及分液管,保證將液態制冷劑均勻分配給制冷劑蒸發管束。由于液態制冷劑流經膨脹閥降壓后,呈氣液兩相狀態,如處理不當,將會導致各通路的制冷液分配不均。為了解決此問題,除在膨脹閥后設置分液器增強氣液混合以外,還設置等長度的分液管,增加各通路阻力,保證各通路分液均勻。進一步的設計還包括所述熱交換器內分布有多片折流板,所述蒸發器為由多根管構成的制冷劑蒸發管束,制冷劑蒸發管束沿熱交換器相距分布,通過所述管板及折流板支撐。熱交換器內橫跨蒸發管束安裝的若干塊折流板,能增加液體橫掠管束的流速和擾動,其擾動作用還有助于在蒸發管束外表面形成湍流,破壞管束表面影響熱交換效率的氣流薄層。從上述分析可見,本專利為一種自冷型板式臭氧發生器,其包括自冷型板式臭氧發生源、循環風機、熱交換器以及制冷劑循環冷卻系統。這種設計方案,除開能夠在高頻高壓工作電源所建立的強電場作用下,通過平板介質阻擋放電形式生成臭氧以外,還在循環風機的強迫輸運下,高速臭氧氣流自身能快速、及時、有效、循環的將放電所產生的熱量帶離臭氧發生強放電區域。本專利中熱交換作用與發生臭氧的作用是分開的,而傳統臭氧發生器的發生臭氧作用與和熱交換作用相互關連,而且是在發生臭氧區域內綜合進行。因此熱交換器可以采用換熱效率更高的通用類型和種類,這樣可以達到傳統臭氧發生器無法達到的熱傳遞效率,從而實現臭氧濃度和產量的大幅提高。本專利所述自冷型板式臭氧發生器,能夠通過工作氣體的導入率(工作氣源的導入量與工作氣體循環量的比值),控制臭氧氣體的循環時間和次數,從而控制輸出臭氧的濃度和產量。通過控制蒸發管束內制冷劑的蒸發溫度及壓力,控制臭氧發生源導入氣體的工作溫度,進而使臭氧發生源放電工作區域的溫度控制在最佳溫度點上。從而使臭氧的產量、濃度、能耗達到最佳值。由于采用了柔性薄形介電體和超薄電極,并且省去了傳統臭氧發生器水冷結構所占據的空間和材料,使得本發明所述臭氧發生器體積只有原來的五分之一甚至更小。大大節約了設備制造成本,使得價格低廉、性能優良的工業臭氧發生器走向市場成為可能。由于本發明所選用的介電體具有很高的介電強度,工作電源電壓可以提高到萬伏以上。工作電源頻率可以提高到一萬赫芝左右,這種高頻高壓電源在放電間隙一定的情況下,會建立起一個超強的放電電場,使放電間隙的電離折合電場達到很高的強度,放電電場中的電子平均能量達到氧分子離解能級,這種能級電子所具有的電子平均能量最適合于氧分子O2的離解反應,且極大地減少了低能電子的生成比例。臭氧濃度和產量將大幅提高。本發明所述自冷型板式臭氧發生器還采用了制冷劑循環冷卻系統,用于同來自臭氧發生源的高速氣流進行熱交換。使用專用制冷劑的蒸發、壓縮、冷凝、節流、再蒸發的循環冷卻方式,快速、及時、有效的對高速氣流進行冷卻,使其運行在最佳工作溫度點上。從而實現臭氧大濃度、高產量、低能耗的最終目的。綜上所述,本專利具有以下優點及技術效果:工作氣源在循環風機的驅動下,形成高速氣流,并且循環的經過臭氧發生裝置。在高頻高壓工作電源所建立的強電場作用下,使得進入該發生源的氧分子受高能電子激發電離放電而生成臭氧。工作氣源高速氣流在高頻高壓電場中通過介質阻擋放電生成臭氧的同時,該氣流自身將氣體電離和介電體介質能量耗散中釋放的大量熱能帶離臭氧發生裝置,并在熱交換器中與制冷劑循環冷卻裝置進行熱交換。傳統的臭氧發生器中,電極、介電體的冷卻與介質阻擋放電單元在結構上需要做成一體,冷卻水要直接到達并通過電極或介電體一側,方能達到冷卻電極、介電體的目的。這就要求電極與介電體必須具有足夠的剛性和強度承受冷卻水壓力,而且同樣需要熱交換設備。此外水冷腔體占據了大量空間,消耗大量金屬材料,若干支臭氧發生管并聯連接,相鄰管間還必須留有足夠的空間以供安裝及冷卻,這些都將造成臭氧發生單元及設備體積龐大,金屬材料消耗量增大,設備制造成本居高不下。傳統臭氧發生器中,由高低壓電極板、介電體及放電間隙構成的單元,厚度至少在10mm以上,其體積約占整體體積的20%~30%,而本專利中的高低壓電極板、介電體及放電間隙構成的放電單元厚度只有2~2.2mm,且各單元之間不用設計冷卻空間,其體積約占整體體積的4%~6%。例如本發明的臭氧發生器電極厚度只需要0.50mm左右,介電體厚度只需0.05~0.20mm,(傳統型臭氧發生器介電體厚度至少需要1.80~2.2mm,電極厚度至少需要2.5~3.5)。電極和介電體的體積減小,相應增加了工作氣流空間,從而使臭氧發生裝置單位體積的臭氧產量大幅度提高。傳統型臭氧發生器采用內外水冷卻時,還需考慮到冷卻水腔,這樣體積更大,同樣濃度和產量下,體積是本發明臭氧發生器的數倍。由此而知,本專利臭氧發生裝置省去了傳統水冷卻所需的空間和金屬材料,體積小,材料消耗小,成本低廉。本專利中熱交換作用與產生臭氧的作用是分開的,而傳統臭氧發生器的產生臭氧作用與和熱交換作用相互關連,而且是在發生臭氧區域內綜合進行的。由此,本專利的熱交換不需要設計成滿足介質阻擋放電的結構形式,而可以采用換熱效率更高的通用類型和種類的設備,可以達到傳統臭氧發生器未能實現的熱傳遞效率,從而實現臭氧濃度和產量的大幅提高。由于采用聚合物介電體替代玻璃介電體,介電強度是玻璃的十多倍甚至更高,工作電源的電壓能提高到萬伏以上,頻率能提高到10KHz左右。在放電間隙一定的條件下,可以使放電間隙的電離折合電場達到很高強度,放電電場中的電子平均能量能達到離解能級,這種電子所具有的電子平均能量最適合于氧分子O2的離解反應。另一個重要優點是,臭氧濃度和產量大小可根據需要調節。通過調節工作氣源進氣管中工作氣體的導入率和工作氣體循環,便可以對臭氧氣體導出管的輸出臭氧量及濃度進行控制。將進入臭氧發生裝置之前的工作氣流溫度控制在10℃左右甚至更低,便可以控制臭氧發生源放電區域的工作氣體溫度在比較理想的范圍。這種溫度更適合氧分子O2的離解反應。此外,適當增加部分儀表、傳感器,即可以對臭氧的輸出濃度、產量、工作氣體的導入流量、壓力、溫度等進行自動調節,實現全自動或遠程控制。整個板式臭氧發生單元可以采用模塊化設計、制造,能按照產量大小及濃度需要進行任意組合搭配。以適合不同用戶,不同規模的市場需求。附圖說明圖1為本專利實施例系統示意圖。圖2為圖1中臭氧發生裝置結構示意圖。具體實施方式以下結合附圖對本專利的結構和工作原理做進一步的闡述。本實施例涉及一種自冷型臭氧發生器,敘述了在氣態氧、富氧空氣或空氣的氣流中用板式介質阻擋放電(無聲放電)形式產生臭氧的方法和設備,特別適用于生產商用濃度和產量的臭氧。針對以上所述臭氧發生器存在的問題,本實施例致力于提供一套能夠快速自循環冷卻、換熱設備分離、臭氧濃度可調、能耗低、設備體積小、價格低廉、高效環保的自冷型板式臭氧發生器,如圖1和圖2所示。本實施例的基本思路為:以一定流速流經臭氧發生裝置100的空氣、富氧空氣或氣態氧在高頻高壓電形成的強電場作用下,受高能電子激發獲得能量,并相互碰撞生成臭氧。如此同時,由這些富含氧分子O2和臭氧分子O3的氣流會將介電體28、地電極板25和高壓電極板30以及放電氣隙27中的熱量帶離放電區域,然后與臭氧發生裝置100以外的熱交換器14等組成的制冷劑循環冷卻裝置200進行熱交換,實現既生成臭氧又冷卻自身的目的。本實施例所采用的方法為,通過高速氣流自身將大量熱量帶離臭氧發生裝置100放電區域外。然后在熱交換器14的熱交換室12中,用管束15中的制冷劑取代傳統方法中的冷卻水或油對氣流進行傳導、蒸發、冷卻,如二氟一氯甲烷(R22)、氨(NH3)、以及其他制冷劑等等。如圖1所示,系統組成包括:用于制備臭氧的臭氧發生裝置100;用于冷卻氣體的冷卻裝置200;用于驅動氣體在臭氧發生裝置100和冷卻裝置200之間循環流動的循環裝置300;所述臭氧發生裝置100、冷卻裝置200和循環裝置300形成一封閉的內循環系統,該內循環系統具有導入工作氣源的工作氣源進氣管17和導出臭氧的臭氧氣體導出管9。所述臭氧發生裝置100為一個具有氣體出口3和氣體進口5的密閉箱體構成的臭氧發生源4。如圖2所示,所述臭氧發生源4內部包括多個并排的介電體28、地電極板25和高壓電極板30,所述介電體28、地電極板25和高壓電極板30之間形成氣體放電通道(放電間隙)。上述設備依次以管路、管件進行耦合連接。臭氧發生源4在高頻高壓電所建立的強電場作用下,通過介質阻擋放電生成臭氧分子。循環風機1強迫工作氣流高速循環流經放電間隙27、熱交換器14。發生源氣體進口5及發生源氣體出口3分別將高速氣體從臭氧發生源4導入和導出。左管板18和右管板7用來固定制冷劑蒸發管束15。為了強化管內沸騰,增強傳熱效果,蒸發管采用內螺紋高傳熱性能的金屬管,實現管內湍流的形成。管束外表面安裝有連續整體鋁片,以增大熱傳導面積。熱交換器14一端安裝有制冷劑分配室8,另一端安裝蒸發氣體儲氣室21。制冷劑分液器及分液管(圖中未示出)安裝在制冷劑分配室8中,該結構是保證將液態制冷劑均勻分配給制冷劑蒸發管束15各通路的主要部件。由于液態制冷劑流經膨脹閥降壓后,呈氣液兩相狀態,如處理不當,將會導致各通路的制冷液分配不均。為了解決此問題,除在膨脹閥11后設置分液器增強氣液混合以外,還設置等長度的分液管用以增加各通路阻力,保證各通路分液均勻。制冷劑進液管10與膨脹閥11連接,導入節流后的低壓制冷劑。制冷劑蒸發氣體出氣管20與制冷系統壓縮機19相連,將通過制冷劑蒸發管束15蒸發后的蒸汽導出至壓縮機19進行壓縮。熱交換器14內橫跨蒸發管束安裝有若干塊折流板13,以增加氣體橫掠管束的流速和擾動,其擾動作用還有助于在制冷劑蒸發管束15外表面形成湍流,破壞制冷劑蒸發管束15表面影響熱交換效率的氣流薄層。經過處理的空氣、富氧空氣或氣態氧經由工作氣源進氣管17導入,通過一定比例的導入量,控制臭氧氣體導出管9輸出臭氧的濃度和產量。臭氧發生源4是本發明的核心設備,它的作用是在高頻高壓工作電源所建立的強電場作用下,使得進入臭氧發生源的空氣、富氧空氣或氣態氧中的氧分子受高能電子激發電離放電而生成臭氧。如圖2所示,臭氧發生源4包括一個由發生源左側板31、發生源右側板37、發生源蓋板33、發生源底板38、氣體導出面板23以及氣體導入面板35組成的密閉箱體。高速流動的工作氣源由氣體導入面板35及氣體導出面板23導入或導出,其余板封合成為一個臭氧發生源4的腔體,以防止周圍空氣進入發生臭氧的空間,并防止臭氧從腔體內部外漏。介電體28、地電極板25以及高壓電極板30分別夾緊在若干個上墊片29和下墊片26之間,這些構件依靠粘合劑緊密粘合,然后通過連接桿39與上端緊定調節螺釘34、下端緊定調節螺釘36固緊于臭氧發生源左右側板上。每塊電極板均有一端伸出墊片之外,伸出端交替的上下重復延伸,并連接有地電極接線端子24、高壓電極接線端子32。所選介電體28為非剛性體,地電極板25和高壓電極板30屬于可彎曲的薄鋼板,連接桿39與上端緊定調節螺釘34、下端緊定調節螺釘36構成張緊機構。通過適當結構形式調節上端緊定調節螺釘34、下端緊定調節螺釘36,可將介電體28、地電極板25以及高壓電極板30張緊拉直,并保證各個介電體28、地電極板25以及高壓電極板30平直且相互平行,間隙均勻。其中所形成的放電間隙27提供強電離電場放電空間。優選的介電體28是一種柔性薄形聚合材料,諸如Mylar聚酯、Kapton聚酰亞胺或Lexan聚碳酸酯等。這些材料都具有優異的機械性能、電氣性能、熱穩定性、抗臭氧氧化能力,介電強度是玻璃的十多倍甚至更高。因為不需要像傳統的臭氧發生器那樣,承受冷卻水的靜壓力,所以介電體28的厚度一般選在0.05~0.20mm,這大大低于以往常用玻璃介電體的厚度。當氣流高速通過平直張緊的介電體28一側時,介電體會產生微小震動,這種震動不僅不會對生成臭氧產生負作用,介電體表面還會因微震形成一定程度的湍流,這種湍流恰恰有助于破壞介電體表面影響熱傳遞效率的氣流層,增強介電體的熱傳遞效率。電極板材料的選擇原則是在臭氧中不易被氧化、腐蝕。例如不銹鋼或經過陽極化處理的鋁材之類的薄板。厚度的選擇一般在0.50mm左右,這又大大低于傳統的板式電極或管式鋼管電極的厚度。放電間隙對放電形態和放電空間的溫度均有很大影響。減小放電間隙,可以提高放電空間的冷卻效果,抑制臭氧的分解反應,提高臭氧生成效率,降低單位產量的能耗,所以,本發明擬采用小間隙結構,即放電間隙設計為0.5~0.75mm。當電源系統工作時,連接于高壓電極接線端子32的高頻高壓交變電通過介電體28的耦合極化作用,在臭氧發生源4的放電間隙27中建立起氣體放電電場,同時發生數目眾多的微放電。一定壓力、流量、露點的空氣、富氧空氣或氣態氧由熱交換器的c口進入。在風機馬達2帶動的循環風機1的高速輸送下,該工作氣體經由熱交換器折流板13、循環輸送管6、發生源氣體進口5、氣體導入面板35等強迫進入臭氧發生源4的放電間隙27。其中的氧分子在強放電電場作用下,受高能電子的激勵而獲得能量,并且相互碰撞發生氧氣離解反應,從而形成臭氧分子。在受高能電子激發放電產生臭氧過程中,電能在電暈氣隙內大量耗散,大量熱能也隨這些富含氧分子和臭氧分子的氣流被帶離,使得臭氧發生源4內的介電體28、地電極板25、高壓電極板30和放電空間被冷卻并維持在適當溫度。攜帶大量熱能的臭氧氣體經由循環風機1強迫流動,從循環風機輸出管22輸運到臭氧發生源4以外的制冷劑循環冷卻裝置200中進行熱交換。此過程中高速氣流在折流板13的引導下通過熱交換器14中的制冷劑蒸發管束15,以一定流速從制冷劑蒸發管束15外肋片間掠過,將大量熱量通過這些肋片、管壁傳遞給管內流動的制冷劑,此時制冷劑快速蒸發,蒸發氣體由壓縮機19吸入壓縮、冷凝器16冷凝、膨脹閥11節流減壓后進入下一個冷卻循環。被快速冷卻的富含臭氧高速氣體,在進入臭氧發生源4之前的工作氣流溫度控制在10℃左右甚至更低。在高速風機強迫輸運下,來自臭氧發生源4出口的臭氧氣體,絕大部分同不斷由c口進入熱交換器14的工作源氣體混合,再次冷卻后被輸運到臭氧發生源4,進入到下一個介質阻擋放電生成臭氧的循環,隨著這種循環的不斷進行,工作氣體的臭氧濃度達到一定的數值,一定濃度和數量的臭氧由臭氧氣體導出管9輸出至用戶端。在該實施例中,依靠循環風機1,控制一定壓力、流量的工作氣體強迫進入臭氧發生源4的放電間隙27參與離解反應。由這些富含氧分子和臭氧分子的氣流將介電體28、地電極板25、高壓電極板30、放電氣隙27中的熱量帶離放電區域,然后與臭氧發生源4以外的熱交換器14等組成的制冷劑循環冷卻系統進行熱交換,實現富含臭氧的工作氣體快速冷卻。通過控制循環風機1的轉速以及由c口導入的工作源氣體進氣壓力、流量、導入率,可以控制工作氣體通過臭氧發生源的再循環次數及流動狀態,進而控制臭氧氣體輸出的商用濃度和產量。通過控制熱交換器14中蒸發管束15的蒸發溫度、壓力,就能將介質阻擋放電生成臭氧過程中高速氣流的溫度冷卻到合適工作點,進而控制臭氧發生源4工作區域氣體的工作溫度。在其他優選的實施例中,所述介電體不僅適用柔性薄形聚合物材料,也適用其他非剛性材料,只要具有更高的介電強度,優良的物理化學性能及機械性能,能夠平直張緊,均可以作為用于本發明所述臭氧發生器的介電體。除開本實施例所描述的熱交換系統以外,還適用于其他諸如直接蒸發式空氣冷卻器、干式殼管蒸發器等各種熱交換器。本實施例中制冷劑循環冷卻系統不僅適用于現在常用的制冷劑,如二氟一氯甲烷(R22)、氨(NH3)等,也適合其他能用于本方案循環冷卻的制冷劑。本實施例中用來與臭氧氣體進行熱交換的是制冷劑循環冷卻系統,其冷卻劑主要是R22等能用于本方案循環冷卻的制冷劑。但是也可以采用其他常用熱交換設備,如水、油、氣體冷卻熱交換系統等等。本實施例中所涉及的制冷劑循環冷卻系統,除用于本方案描述的自冷型板式臭氧發生器以外,還適合在其他中小型工業臭氧發生器系統中使用。包括任何立式、臥式、管式、板式臭氧發生裝置。顯然,本專利的上述實施例僅僅是為清楚地說明本專利所作的舉例,而并非是對本專利的實施方式的限定。對于所屬領域的普通技術人員來說,在上述說明的基礎上還可以做出其它不同形式的變化或變動。這里無需也無法對所有的實施方式予以窮舉。凡在專利的精神和原則之內所作的任何修改、等同替換和改進等,均應包含在本專利權利要求的保護范圍之內。