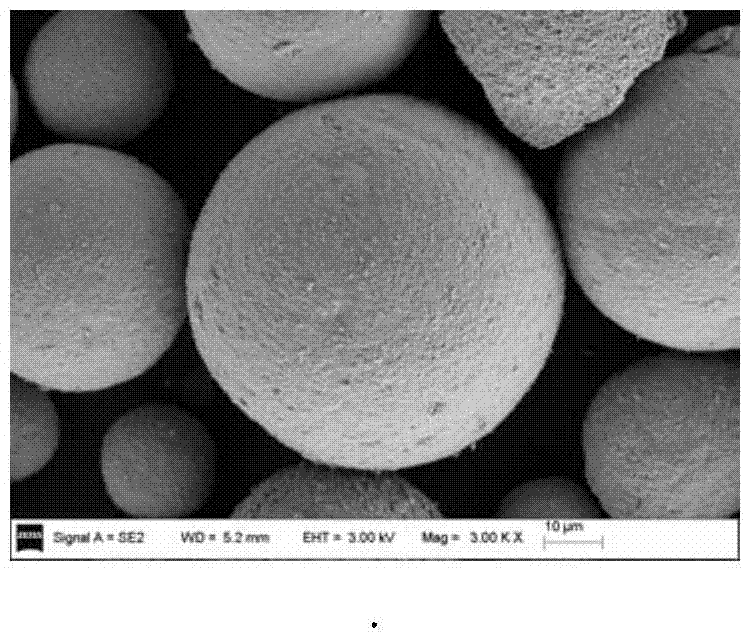
本發明涉及一種氧化鋁成膠過程提高膠體固含量的方法。
背景技術:γ-Al2O3材料由于其發達的介孔和大孔;良好的強度和抗磨損指數;較高的比表面積和孔體積、且其比表面和孔體積在較大范圍內可調整;優良的負載其它元素的性質等特點,因而被廣泛應用于吸附分離和催化領域。在流化催化裂化催化劑制備過程,氧化鋁又是不可或缺的重要載體之一。同時,利用氧化鋁直接制備成微球狀γ-Al2O3在流化床催化裝置中也有著非常廣泛的應用,多種助劑都是利用γ-Al2O3微球負載一定量的其它活性組分而成,如CN1411908公布的一種脫除煙氣中NOx,增加輕油收率且高效助燃CO的助劑,就是利用γ-Al2O3微球負載銅鋁-鈰鋁復合氧化物制備得到的。目前,人們普遍利用噴霧干燥的方法來制備氧化鋁微球,如日本大川原化工機株式會社在其專利CN1036911中公布了他們的噴霧干燥、造粒設備,又如美國圣戈本陶瓷及塑料股份有限公司在其專利CN942242中公布了他們噴霧干燥制備氧化鋁載體的方法。而常用的辦法是利用酸,擬薄水鋁石,水,甚至鋁溶膠等幾種原料,一般過程是將擬薄水鋁石膠溶并打漿均質后再利用離心式或壓力式噴霧干燥裝置將膠體以霧狀形式噴射出來,遇熱空氣后膠體中的水迅速氣化并得到干燥的微球粉末,最后經過焙燒得到需要的γ-Al2O3微球。如日本專利昭63-17220公布的方法,先用一定量的酸膠溶,并加入部分堿中和后在噴霧干燥成型,又如中國專利CN93108631.0,CN1361787A,CN1097351A等都是使用了薄水鋁石添加無機酸或鋁溶膠來噴霧干燥制備微球的方案。氧化鋁在成膠過程中卻因為酸化擬薄水鋁石粘稠度極大而很難得到高固含量的膠體,而且為了保證膠體的流動性以及不堵塞噴霧干燥裝置的進料管、噴嘴等部件,一般噴霧時膠體固含量都控制在15~25%,如上述中國專利CN93108631.0,CN1361787A,CN1097351A公開的制備方案中,其酸化擬薄膠體的固含量都不超過25%,因此其中75~85%的水分都必須在噴霧干燥裝置中被氣化帶走。因此,這就增大了生產過程中的能耗以及降低了處理量,也降低了生產效率。因此,本發明擬根據這一存在的問題,在保證流動性和適應于噴霧裝置工藝條件的前提下,大幅度調整噴霧膠體的固含量,從而提高噴霧干燥裝置的處理量和效率并降低能耗。
技術實現要素:本發明提供一種氧化鋁膠體的制備方法、所制得的氧化鋁膠體、微球狀氧化鋁載體的制備方法、所制得的微球狀氧化鋁載體、催化裂化催化劑的制備方法及催化裂化負載型助劑的制備方法,以解決現有技術氧化鋁成膠固含量低的缺陷。為實現上述目的,本發明提出一種氧化鋁膠體的制備方法,包括:步驟1:將擬薄水鋁石分成兩部分,將第一部分擬薄水鋁石、無機酸、去離子水按照一定的重量百分比混合打漿并成膠,膠體固含量為17~21%;以及步驟2:將第二部分擬薄水鋁石經過高溫焙燒預處理后,加入到第一部分膠體中,使得總膠體的固含量提高至30~40%,得到氧化鋁膠體,對所述第二部分擬薄水鋁石的預處理為將第二部分擬薄水鋁石在溫度500~700度下焙燒2~8小時,所述第一部分擬薄水鋁石與所述第二部分擬薄水鋁石的重量百分比為50~100%:0~50%。其中,步驟1中,第一部分擬薄水鋁石、去離子水、無機酸的重量百分比為0~31%:0~59%:0~10%。其中,所用無機酸為鹽酸、硫酸或硝酸。其中,步驟1中,所述無機酸與所述擬薄水鋁石中Al元素的摩爾比為0.03~0.15。其中,步驟2中,所述第二部分擬薄水鋁石經預處理后得到γ-Al2O3中間體,將所述γ-Al2O3中間體加入到第一部分膠體中,使得總膠體的固含量提高至30~40%。而且,為實現上述目的,本發明提出了上述氧化鋁膠體的制備方法所制得的氧化鋁膠體。而且,為實現上述目的,本發明提出了一種微球狀氧化鋁載體的制備方法,包括:步驟a1:采用上述氧化鋁膠體的制備方法制備氧化鋁膠體;步驟a2:將步驟a1中的氧化鋁膠體進行造粒干燥成型,得到微球狀催化劑顆粒;以及步驟a3:將步驟a2中的微球狀催化劑顆粒于500-700℃焙燒2-8小時得到微球狀氧化鋁載體。而且,為實現上述目的,本發明提出了上述微球狀氧化鋁載體的制備方法所制得的微球狀氧化鋁載體。而且,為實現上述目的,本發明提出了一種催化裂化催化劑的制備方法,包括:步驟b1:采用上述氧化鋁膠體的制備方法制備氧化鋁膠體;以及步驟b2:利用步驟b1所制備的氧化鋁膠體作為載體制備催化裂化催化劑。而且,為實現上述目的,本發明提出了一種催化裂化負載型助劑的制備方法,包括:步驟c1:采用上述氧化鋁膠體的制備方法制備氧化鋁膠體;以及步驟c2:采用上述微球狀氧化鋁載體的制備方法制備氧化鋁微球;以及步驟c3:利用步驟c2所制備的氧化鋁微球作為載體負載一活性組分制備流化催化裂化負載型助劑。本發明提供的一種氧化鋁成膠過程中提高固含量的方法,將擬薄水鋁石分兩部分,其中一部分經過預處理后使總膠體固含量得到了顯著提高,可以將氧化鋁打漿過程中的固含量從常規的15%~25%提高至40%,從而降低干燥成型過程中需要蒸發的水量,大幅度提高制備過程中的生產效率,并降低生產過程中的能耗,并能使膠體具有良好的均勻性和流動性。附圖說明圖1為...