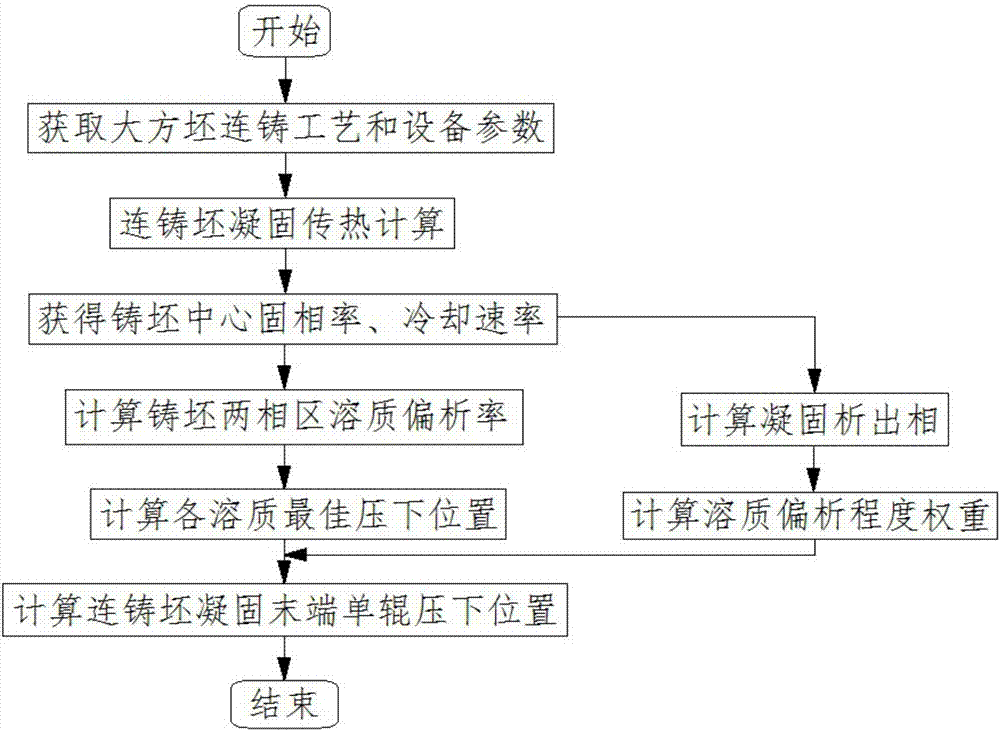
本發明涉及鋼連鑄生產
技術領域:
,尤其涉及一種大方坯連鑄凝固末端單輥壓下位置確定方法。
背景技術:
:鑄坯橫斷面尺寸大于200mm×200mm的方坯稱為大方坯。連鑄坯在凝固過程中,隨著枝晶生長,溶質元素向液相中排出,富集在凝固末端兩相區內。由于凝固末端凝固收縮、鑄坯鼓肚、熱應力和鼓肚造成凝固末端鋼液的流動,促使溶質元素隨鋼液在較大范圍內流動,最終造成中心部位溶質元素含量明顯高于其他部位,形成中心偏析。中心疏松通常伴隨著中心偏析產生,造成鑄坯中心質量缺陷。鑄坯中心偏析和中心疏松會引發鋼材一系列質量問題:對于高碳線材鋼,拉拔性能降低,拉斷率增加;對于天然氣輸送管線鋼,抗氫致裂紋(hic)能力下降,從而造成輸送管破裂;對于海洋鉆探與平臺用結構鋼,焊接性能降低等。因此連鑄坯中心偏析和中心疏松嚴重制約了高品質鋼的生產,備受冶金工作者的關注。連鑄坯凝固末端輕壓下技術作為改善鑄坯中心疏松和中心偏析的有效手段,在過去幾十年里取得了長足發展,并廣泛運用于連鑄生產過程。但由于連鑄坯凝固末端輕壓下量小,鑄坯變形過程延展和寬展變形損耗使得傳遞到鑄坯中心的壓下量較小,無法完全達到消除鑄坯中心偏析和疏松的目的。近些年,隨著我國鋼鐵產業升級換代步伐的推進,對高品質鋼的需求越來越迫切,要求越來越高。連鑄坯凝固末端重壓下技術,充分利用連鑄坯凝固末端高溫、大溫度梯度這一有利條件,實施大壓下量壓下,提高鑄坯中心壓下效率,在充分補償連鑄坯凝固末端收縮的同時,進一步通過鑄坯凝固坯殼變形,擠壓兩相區內濃縮鋼液向上游(沿拉坯方向反向)流動,促使濃縮鋼液重新混合稀釋,從而使鑄坯的凝固組織更加均勻致密,起到改善中心偏析和減少中心疏松的作用。這種技術能夠在改善鑄坯中心偏析的基礎上,整體提高鑄坯中心致密度,愈合大部分缺陷,為低圧縮比軋制創造良好條件。早在1980年,日本kawasaki鋼鐵公司mizushima煉鋼廠3#大方坯弧形連鑄機在凝固末端安裝一對平砧實現連續鍛壓(continuousforging)功能,壓下量可達40~140mm,壓下位置為fs=0.8時,鑄坯中心偏析和疏松得到明顯改善。日本新日鐵提出了采用控制面壓下技術(controlledplanereduction)。該技術在板坯凝固末端采用兩個移動的砧板(bar)來支撐和壓下未凝固鑄坯,能夠很好的抑制凝固末端鋼液的流動和補償凝固收縮,板坯中心偏析和中心疏松改善明顯。近年來,日本sumitomo金屬提出了改善鑄坯疏松的pccs工藝(porositycontrolofcastingslab),該工藝在fs>0.8時實施大壓下,可以有效愈合鑄坯內部縮孔、疏松等缺陷。韓國posco提出了采用增強扇形段完成凝固末端重壓下的posharp技術,該技術在壓下位置fs=0.3-0.6實施時,鑄坯中心位置可最大限度得到控制,且可以有效避免鑄坯壓下裂紋的產生。國內東北大學提出了大方坯連鑄凸型輥末端重壓下技術,以及增強寬厚板坯扇形段末端重壓下技術,能夠顯著提高鑄坯壓下效率,進一步提高鑄坯中心致密度。北京科學技術大學提出了利用thercast軟件對板坯凝固過程進行了模擬和試驗,研究表明:在壓下位置fs=0.8實施重壓下時,鑄坯內部偏析改善無效果,但有利于改善疏松,且產生內裂紋幾率較小。鞍鋼小方坯連鑄機在進行拉矯機能力提升改造之后,實現了小方坯末端大壓下功能,該技術應用表明:在壓下位置fs=0.56實施連鑄坯凝固末端單輥壓下,鑄坯中心偏析和疏松改善明顯。以上連鑄坯凝固末端重壓下技術進展和應用表明,無論采用何種重壓下技術,在合適的連鑄坯凝固末端實施重壓下均能夠取得良好的效果。從技術特點來看,無論是大方坯還是板坯連鑄凝固末端重壓下均采用單體設備在較短范圍內完成重壓下的一次性實施,且重壓下效果明顯;從壓下設備特點來看,早期的重壓下設備都采用獨立于拉矯系統以外的額外壓下裝置來實施(比如:日本kawasaki鋼鐵公司連續鍛壓技術和新日鐵控制面壓下技術都需要增加壓下能力更強的鍛壓裝置),隨著連鑄拉矯機能力的提升,現代連鑄凝固末端大壓下技術都采用拉矯設備直接實施壓下,具有設備控制精度高和控制靈活的特點,且重壓下工藝實施方便和效果明顯。由此可見,隨著連鑄坯拉矯設備能力的提升,鑄坯凝固末端實施重壓下技術的前提條件已得到了充分保障,其關鍵是在合適的連鑄坯凝固末端位置實施壓下,特別是大方坯連鑄機拉矯設備布置較為稀疏(各拉矯機相距1.5m左右),其末端壓下位置的選擇至關重要。然而到目前之外,幾乎所有輕壓下位置都是根據現場工藝實驗確定,且從現有報道來看,連鑄坯凝固末端壓下位置大相徑庭,這大大阻礙了連鑄坯凝固末端壓下技術的推廣和應用。技術實現要素:(一)要解決的技術問題本發明的目的在于提供一種大方坯連鑄凝固末端單輥壓下位置確定方法,該方法能夠針對于不同鑄坯有針對性地計算確定壓下位置。(二)技術方案為了達到上述目的,本發明采用的主要技術方案包括:本發明提供一種大方坯連鑄凝固末端單輥壓下位置確定方法,具體為,通過鑄坯中各溶質元素的最佳壓下位置與各溶質元素的偏析程度權重耦合確定大方坯連鑄凝固末端單輥壓下位置。根據本發明,具體包括如下步驟:s1、獲取鑄坯中各溶質元素i的最佳壓下位置的數值;s2、獲取鑄坯中各溶質元素i的偏析程度權重φi的數值;s3、根據各溶質元素i的最佳壓下位置的數值和各溶質元素i的偏析程度權重φi的數值,按照如下公式計算大方坯連鑄凝固末端單輥壓下位置根據本發明,步驟s1包括如下子步驟:s1.1、獲取鑄坯中的固相密度ρs、液相密度ρl、溶質元素i在固相中的濃度cs,i、溶質元素i在液相中的濃度cl,i、壓下效率η、鑄坯寬度w、壓下量δh、鑄坯凝固末端單輥壓下位置處液芯面積s的數值;s1.2、針對于每個溶質元素i,將步驟s1.1中確定的固相密度ρs、液相密度ρl、溶質元素i在固相中的濃度cs,i、溶質元素i在液相中的濃度cli的數值分別帶入公式獲得分別對應于各溶質元素i的連鑄坯凝固末端單輥壓下后鑄坯中心兩相區平均溶質偏析率ki、單輥壓下位置處兩相區固相率fs與單輥壓下兩相區溶質排除率ε之間的ki-fs-ε函數關系;s1.3、將步驟s1.1中確定的壓下效率η、鑄坯寬度w、壓下量δh、鑄坯凝固末端單輥壓下位置處液芯面積s的數值帶入公式獲得單輥壓下兩相區溶質排除率ε與單輥壓下位置處兩相區固相率fs的ε-fs函數關系;s1.4、將ε-fs函數關系分別帶入與各溶質元素i相對應的ki-fs-ε函數關系,獲得分別對應于各溶質元素i的連鑄坯凝固末端單輥壓下后鑄坯中心兩相區平均溶質偏析率ki與單輥壓下位置處兩相區固相率fs之間的ki-fs函數關系;s1.5、針對各溶質元素i對應的ki-fs函數關系,獲得連鑄坯凝固末端單輥壓下后鑄坯中心兩相區平均溶質偏析率ki取最小值時的單輥壓下位置處兩相區固相率fs,該單輥壓下位置處兩相區固相率fs為最佳壓下位置根據本發明,在步驟s2中:當碳元素的重量百分比小于0.53wt%時,各溶質元素i的偏析程度權重φi為其中,kδ/l為δ鐵素體/液相界面處溶質分配系數;當碳元素的重量百分比大于等于0.53wt%時,各溶質元素i的偏析程度權重φi為其中,kγ/l為γ奧氏體/液相界面處溶質分配系數。根據本發明,對應于溶質元素碳:kδ/l取0.19,kγ/l取0.34;對應于溶質元素硅:kδ/l取0.77,kγ/l取0.52;對應于溶質元素錳:kδ/l取0.76,kγ/l取0.78;對應于溶質元素磷:kδ/l取0.23,kγ/l取0.13;對應于溶質元素硫:kδ/l取0.05,kγ/l取0.035。(三)有益效果本發明的有益效果是:本發明提出大方坯連鑄凝固末端單輥壓下位置由所澆鑄鋼中各溶質元素最佳壓下位置和各溶質元素偏析程度權重耦合確定。這樣將鋼中各溶質元素的最佳壓下位置耦合考慮鋼中溶質元素的偏析程度來確定連鑄坯凝固末端單輥壓下位置,可以針對具有不同組分及其含量的鋼做有針對性的計算,無需根據現場工藝實驗確定,且計算結果更加準確。附圖說明圖1是實施例一和實施例二中的大方坯連鑄凝固末端單輥壓下位置確定方法的流程示意圖;圖2為計算大方坯連鑄坯凝固末端單輥壓下最佳位置具體實施流程圖;圖3是大方坯連鑄示意圖;圖4為大方坯連鑄凝固末端單輥壓下示意圖;圖5為大方坯連鑄凝固末端單輥壓下后鑄坯中心兩相區平均溶質偏析率ki的變化規律示意圖。具體實施方式為了更好的解釋本發明,以便于理解,下面結合附圖,通過具體實施方式,對本發明作詳細描述。實施例一在本實施例中,以斷面320mm×410mm的高強度耐候鋼yq450nqr1為例,澆注過熱度為25℃,拉速為0.75m/min。高強度耐候鋼yq450nqr1主要成分如表1所示。表1成分csimnps含量(wt.%)0.120.401.350.0140.014結合圖1,本實施例中提供的大方坯連鑄凝固末端單輥壓下位置確定方法包括如下步驟:s1、獲取鑄坯中各溶質元素i的最佳壓下位置的數值。其中,各溶質元素i指的是主要成分,對于微量成分,可不予考慮。具體包括如下子步驟:s1.1、本領域技術人員根據公知技術可直接或間接獲取到鑄坯中的固相密度ρs、液相密度ρl、溶質元素i在固相中的濃度cs,i、溶質元素i在液相中的濃度cl,i、壓下效率η、鑄坯寬度w、壓下量δh、鑄坯凝固末端單輥壓下位置處液芯面積s的數值。s1.2、針對于每個溶質元素i(即c、si、mn、p、s),將步驟s1.1中確定的固相密度ρs、液相密度ρl、溶質元素i在固相中的濃度cs,i、溶質元素i在液相中的濃度cl,i的數值分別帶入公式獲得分別對應于各溶質元素i的連鑄坯凝固末端單輥壓下后鑄坯中心兩相區平均溶質偏析率ki、單輥壓下位置處兩相區固相率fs與單輥壓下兩相區溶質排除率ε之間的ki-fs-ε函數關系,即針對每一個溶質元素i(即c、si、mn、p、s),都有一個ki-fs-ε函數關系。s1.3、將步驟s1.1中確定的壓下效率η、鑄坯寬度w、壓下量δh、鑄坯凝固末端單輥壓下位置處液芯面積s的數值帶入公式獲得單輥壓下兩相區溶質排除率ε與單輥壓下位置處兩相區固相率fs的ε-fs函數關系,該ε-fs函數關系適用于所有溶質元素i。s1.4、將ε-fs函數關系分別帶入與各溶質元素i相對應的ki-fs-ε函數關系,獲得分別對應于各溶質元素i的連鑄坯凝固末端單輥壓下后鑄坯中心兩相區平均溶質偏析率ki與單輥壓下位置處兩相區固相率fs之間的ki-fs函數關系,即針對每一個溶質元素i(即c、si、mn、p、s),都有一個ki-fs函數關系。s1.5、針對各溶質元素i對應的ki-fs函數關系,獲得連鑄坯凝固末端單輥壓下后鑄坯中心兩相區平均溶質偏析率ki取最小值時的單輥壓下位置處兩相區固相率fs,該單輥壓下位置處兩相區固相率fs為最佳壓下位置其中,可以ki為縱坐標,以fs為橫坐標繪制ki-fs函數關系對應的曲線圖,在圖中選取ki值最低點時fs的值作為當然,也可以采用計算軟件直接求得。根據上述步驟,計算獲得鋼中各溶質元素的最佳壓下位置見表2。表2s2、獲取鑄坯中各溶質元素i的偏析程度權重φi的數值。具體為:在本實施例中,從表1中可看出,碳元素的重量百分比為0.12wt%,小于0.53wt%。此時,高強度耐候鋼yq450nqr1連鑄凝固過程中首先從鋼液中形成δ鐵素體,然后發生包晶反應(l+δ鐵素體→γ奧氏體),溶質偏析程度由δ鐵素體/液相界面處溶質分配系數kδ/l所決定,各溶質元素i的偏析程度權重φi為其中,kδ/l為δ鐵素體/液相界面處溶質分配系數,對應于溶質元素碳:kδ/l取0.19;對應于溶質元素硅:kδ/l取0.77;對應于溶質元素錳:kδ/l取0.76;對應于溶質元素磷:kδ/l取0.23;對應于溶質元素硫:kδ/l取0.05。由此,計算出各溶質元素i的偏析程度權重φi見表3。表3成分csimnpsφi5.261.301.324.3520s3、根據步驟s1和步驟s2計算出的各溶質元素i的最佳壓下位置的數值和各溶質元素i的偏析程度權重φi的數值,按照如下公式計算大方坯連鑄凝固末端單輥壓下位置最終為0.85,按照此數值實施后鑄坯橫向低倍無中心縮孔、中心裂紋缺陷,鑄坯中心碳偏析指數<1.05,中心疏松缺陷評級≤1.0級。實施例二結合圖1,在本實施例中,以斷面380mm×280mm的重軌鋼u75連鑄坯為例,澆注過熱度為25℃,拉速為0.68m/min。重軌鋼u75主要成分如表4所示。表4成分csimnps含量(wt.%)0.760.640.890.0140.014本實施例中提供的大方坯連鑄凝固末端單輥壓下位置確定方法包括如下步驟:s1、獲取鑄坯中各溶質元素i的最佳壓下位置的數值。其中,各溶質元素i指的是主要成分,對于微量成分,可不予考慮。具體包括如下子步驟:s1.1、本領域技術人員根據公知技術可直接或間接獲取到鑄坯中的固相密度ρs、液相密度ρl、溶質元素i在固相中的濃度cs,i、溶質元素i在液相中的濃度cl,i、壓下效率η、鑄坯寬度w、壓下量δh、鑄坯凝固末端單輥壓下位置處液芯面積s的數值。s1.2、針對于每個溶質元素i(即c、si、mn、p、s),將步驟s1.1中確定的固相密度ρs、液相密度ρl、溶質元素i在固相中的濃度cs,i、溶質元素i在液相中的濃度cl,i的數值分別帶入公式獲得對應于各溶質元素i的連鑄坯凝固末端單輥壓下后鑄坯中心兩相區平均溶質偏析率ki、單輥壓下位置處兩相區固相率fs與單輥壓下兩相區溶質排除率ε之間的ki-fs-ε函數關系,即針對每一個溶質元素i(即c、si、mn、p、s),都有一個ki-fs-ε函數關系。s1.3、將步驟s1.1中確定的壓下效率η、鑄坯寬度w、壓下量δh、鑄坯凝固末端單輥壓下位置處液芯面積s的數值帶入公式獲得單輥壓下兩相區溶質排除率ε與單輥壓下位置處兩相區固相率fs的ε-fs函數關系,該ε-fs函數關系適用于所有溶質元素i。s1.4、將ε-fs函數關系分別帶入與各溶質元素i相對應的ki-fs-ε函數關系,獲得對應于各溶質元素i的連鑄坯凝固末端單輥壓下后鑄坯中心兩相區平均溶質偏析率ki與單輥壓下位置處兩相區固相率fs之間的ki-fs函數關系,即針對每一個溶質元素i(即c、si、mn、p、s),都有一個ki-fs函數關系。s1.5、針對各溶質元素i對應的ki-fs函數關系,獲得連鑄坯凝固末端單輥壓下后鑄坯中心兩相區平均溶質偏析率ki取最小值時的單輥壓下位置處兩相區固相率fs,該單輥壓下位置處兩相區固相率fs為最佳壓下位置其中,可以ki為縱坐標,以fs為橫坐標繪制ki-fs函數關系對應的曲線圖,在圖中選取ki值最低點時fs的值作為當然,也可以采用計算軟件直接求得。根據上述步驟,計算獲得鋼中各溶質元素的最佳壓下位置見表5。表5s2、獲取鑄坯中各溶質元素i的偏析程度權重φi的數值。具體為:在本實施例中,從表4中看出,碳元素的重量百分比為0.76wt%,大于0.53wt%。此時,重軌鋼u75v連鑄凝固過程中直接從鋼液中形成γ奧氏體,溶質偏析程度由γ奧氏體/液相界面處溶質分配系數kγ/l所決定,各溶質元素i的偏析程度權重φi為其中,kγ/l為γ奧氏體/液相界面處溶質分配系數,對應于溶質元素碳:kγ/l取0.34;對應于溶質元素硅:kγ/l取0.52;對應于溶質元素錳:kγ/l取0.78;對應于溶質元素磷:kγ/l取0.13;對應于溶質元素硫:kγ/l取0.035。由此,計算出各溶質元素i的偏析程度權重φi見表6。表6成分csimnpsφi2.941.921.827.6928.57s3、根據步驟s1和步驟s2計算出的各溶質元素i的最佳壓下位置的數值和各溶質元素i的偏析程度權重φi的數值,按照如下公式計算大方坯連鑄凝固末端單輥壓下位置最終為0.88,按照此數值實施后鑄坯橫向低倍無中心縮孔、中心裂紋缺陷,鑄坯中心碳偏析指數<1.08,中心疏松缺陷評級≤1.0級。綜合上述實施例一和實施例二,本發明提出大方坯連鑄凝固末端單輥壓下位置由所澆鑄鋼中各溶質元素最佳壓下位置fs和各溶質元素i偏析程度權重φi耦合確定。這樣將鋼中各溶質元素的最佳壓下位置耦合考慮鋼中溶質元素的偏析程度來確定連鑄坯凝固末端單輥壓下位置,可以針對具有不同組分及其含量的鋼做有針對性的計算,無需根據現場工藝實驗確定,且計算結果更加準確。進一步,為了更加清晰地說明上述實施例一和實施例二中所應用的公式的含義,如下結合圖2介紹上述公式的建立過程以及設計思路。步驟1,根據具體工藝條件,確定鑄機特征參數(結晶器長度、鑄坯尺寸、二冷各區位置和長度、壓下輥位置、壓下輥徑等)、連鑄工藝參數(澆鑄溫度、拉速、結晶器冷卻水流量、進出口溫差、二冷水各區流量等)、鋼的熱物性參數(密度、導熱系數、比熱、焓變、等)。步驟2,連鑄坯凝固傳熱計算。連鑄溫度場計算圖3為連鑄示意圖,為節約計算時間,選擇鑄坯橫截面的1/4作為研究對象,鋼連鑄過程的二維凝固傳熱控制方程如下:其中:t為溫度,℃;ρ為密度,kg/m3;cp為熱容,j/(kg·℃);keff為導熱系數,w/(m·℃);l為凝固潛熱,j/kg;fs為固相分率;t為時間,s;x和y分別為鑄坯橫截面寬面和窄面方向長度,m。為了計算整個鑄流鑄坯溫度分布,將整個鑄流劃分為連續單元切片,切片產生于連鑄結晶器彎月面處,整個切片初始溫度與澆鑄溫度相等。隨后單元切片以拉速相同的運動速度從結晶器向下運動,直到消失于連鑄坯火焰切割處。單元切片溫度采用有效體積法并結合不同位置處邊界條件所確定:(a)結晶器在結晶器冷卻區,結晶器傳熱采用davies等提出的經驗公式其中:q為熱流密度,w/m2;z為離彎月面的距離,m;vc為拉速,m/s。(b)二冷區連鑄二冷區傳熱邊界條件較為復雜,二冷區鑄坯表面熱量傳遞包括:鑄坯表面輻射散熱、鑄坯表面與冷卻水霧間的強制對流換熱、冷卻水加熱蒸發傳熱、鑄坯與支撐輥接觸導熱等。為簡化處理,將二冷區冷卻水加熱蒸發傳熱、鑄坯與支撐輥接觸導熱等傳熱方式帶走的熱量,采用增大對流系數的方式來考慮。因此連鑄二冷區的傳熱可簡化表示為對流傳熱和輻射傳熱之和。q=h(tsurf-tamb)+σεb[(tsurf+273.15)4-(tamb+273.15)4](3)其中:h為綜合對流換熱系數,w/(m2·℃);tsurf為鑄坯表面溫度,℃;tamb為環境溫度,℃;σ為stefan-boltzman常數5.67×10-8w/(m2·k4);εb為鑄坯表面黑度系數,取0.8。(c)空冷區在空冷區內,鑄坯表面主要以輻射的方式向外散熱,輻射換熱的熱流公式如下:q=σε[(tsurf+273.15)4-(tamb+273.15)4](4)步驟3、獲得鑄坯中心冷卻速率、中心固相率結合單元切片所處位置和經歷的時間關系,采用顯示差分法求得單元切片各節點溫度,從而求得鑄坯中心冷卻速率,即其中,cr為中心冷卻速率,℃/s;tc為節點溫度,℃。同樣可求得鑄坯中心固相率fs,即式中:tl為液相線溫度,℃;ts為固相線溫度,℃。步驟4、計算連鑄坯兩相區溶質偏析如圖4所示,在連鑄坯凝固末端采用單輥壓下方式能夠有效補充鋼液凝固收縮,同時還能夠通過變形坯殼擠壓兩相區內富含溶質元素的濃縮鋼液向上游(拉坯反方向)排出,從而達到消除中心偏析,提高鑄坯中心致密度的目的。單輥壓下前,單輥壓下位置處兩相區體積為vm,平均溶質密度為ρm,平均溶質元素i的含量為cin,i,固相體積為vs,固相密度為ρs,溶質元素i在固相中的濃度為cs,i,液相體積為vl,液相密度為ρl,溶質元素i在液相中的濃度為cl,i,根據溶質質量守恒原理可得如下關系式:ρmvmcin,i=ρsvscs,i+ρlvlcl,i(6)兩相區平均溶質密度ρm與兩相區內固相密度ρs和液相密度ρl滿足如下關系式:ρm=fsρs+flρl(7)其中:fs和fl分別為固相體積分率和液相體積分率,可分別由下式(8)和式(9)求得:將式(7)~(9)代入式(6),經整理可得壓下前兩相區平均溶質濃度cin,i的表達式如下:當實施單輥輕壓下時,鑄坯坯殼變形使得兩相區體積減小vd,從而使得兩相區內的濃縮鋼液向上游擠壓排出。假設剩余的兩相區平均溶質濃度為cout,i,再次根據溶質質量守恒原理可得如下關系式:ρm(vs+vl-vd)cout,i=ρsvscs,i+ρl(vl-vd)cl,i(11)并且單輥壓下兩相區溶質排除率ε可表示為壓下鑄坯變形使得兩相區減小體積vd與兩相區原有液相體積vl之比:其中,vd=ηwδh;vl=(1-fs)s。將式(7)~(9)和式(12)代入式(11),經整理可得單輥壓下后兩相區平均溶質密度cout,i表達式如下:因此單輥壓下后,鑄坯中心兩相區平均溶質偏析率ki為壓下后兩相區平均溶質濃度cout,i與壓下前兩相區平均溶質濃度cin,i之比:由于固相體積分率fs和液相體積分率fl滿足如下關系式:fl=1-fs(15)所以將式(15)代入式(14)可得到連鑄坯凝固末端單輥壓下后,鑄坯中心兩相區平均溶質偏析率ki的表達式如下:圖5為大方坯連鑄凝固末端單輥壓下后鑄坯中心兩相區平均溶質偏析率ki的變化規律。本發明定義不同溶質元素宏觀偏析率極小值(ki,min)所對應單輥壓下位置處鑄坯中心固相率為即該元素的最佳壓下位置。當單輥壓下位置處時,隨著fs的增加,連鑄坯固液兩相區內枝晶生長的同時,溶質元素不斷向液相中排出,造成枝晶間溶質元素富集,溶質微觀偏析指數增加。雖然壓下效率隨著固相率的增加存在減少趨勢,但壓下能有效地使枝晶間偏析溶質元素擠壓排出,兩相區宏觀溶質偏析率隨著壓下位置固相率的增加而降低,從而有效地防止鑄坯中心偏析形成。當單輥壓下位置時,隨著固相率的增加,殘留鋼液的流動性變差且壓下效率降低,不利于壓下對凝固末端富含偏析鋼液的擠壓排出,并且枝晶間部分偏析溶質元素開始凝固,溶質元素宏觀偏析開始形成,壓下已經不能有效地抑制溶質元素偏析的形成。因此溶質元素i的最佳壓下位置為但不同溶質元素最佳壓下位置不盡相同。步驟6、計算凝固析出相由于鋼中溶質元素偏析與鋼液凝固過程中析出固相溶解度有關,鋼中各溶質元素偏析程度權重φi為鋼水凝固過程中溶質元素i在固相中的溶解能力所決定,溶質元素i在固相中溶解度越低,溶質偏析越嚴重;溶質元素i在固相中溶解度越高,溶質偏析越輕。即:鋼水凝固時固液界面處溶質分配系數越小,溶質從固相向液相排出越多,溶質偏析越嚴重。為此,所述鋼中各溶質元素偏析程度權重φi可由鋼水凝固過程中固液界面處溶質分配系數ki的倒數所決定。當碳元素的重量百分比小于0.53wt%時,鋼水首先凝固形成δ鐵素體,溶質偏析程度由δ鐵素體/液相界面處溶質分配系數kδ/l所決定,即:當碳元素的重量百分比大于等于0.53wt%時,鋼水凝固形成γ奧氏體,溶質偏析程度由γ奧氏體/液相界面處溶質分配系數kγ/l所決定,即:鋼中主要溶質元素溶質分配系數見表7。表7元素csimnpskδ/l0.190.770.760.230.05kγ/l0.340.520.780.130.035步驟7、計算溶質偏析程度權重φi確定碳元素的重量百分比是小于0.53wt%還是大于等于0.53wt%后,按照上述兩個公式計算溶質偏析程度權重φi。8、計算連鑄坯凝固末端單輥壓下位置為此,大方坯連鑄凝固末端單輥壓下位置由所澆鑄鋼中各溶質元素最佳壓下位置fs,i和各溶質元素偏析程度權重φi所決定,即:綜上,根據連鑄坯凝固傳熱計算,獲得大方坯中心冷卻速率和固相率,作為連鑄坯兩相區中心偏析計算的輸入條件。結合連鑄坯兩相區中心偏析計算,定量確定不同位置處實施單輥壓下,鑄坯中心溶質偏析改善程度,獲得不同溶質元素最佳壓下位置在此基礎上,根據鋼液凝固過程中,首先析出相(δ或γ相),確定溶質偏析程度。從而獲得大方坯連鑄凝固末端單輥壓下最佳位置。該位置實施壓下不僅能夠有效補償連鑄坯凝固收縮,還能夠通過鑄坯變形擠壓兩相區富集溶質元素的濃縮鋼液排出,從而有效改善鑄坯中心偏析,提高鑄坯中心致密度。總體而言,本發明基于連鑄坯凝固末端壓下擠壓鑄坯液芯變形造成兩相區內富含溶質元素的濃縮鋼液向上游(拉坯反方向)排出這一原理,建立了連鑄坯凝固末端單輥壓下后平均溶質偏析率模型,定量確定了鋼中各溶質元素的最佳壓下位置,并耦合考慮鋼中溶質元素的偏析程度,以更加準確地確定連鑄坯凝固末端單輥壓下位置。并且,本發明考慮了鋼中各溶質元素偏析程度和鋼水凝固過程中相變對鋼中溶質元素偏析程度的影響,從而為消除鋼中易偏析元素(比如:碳、硫等)選擇最佳壓下位置提供了可靠方法。并且,本發明考慮了鋼中成分和澆鑄條件對鋼凝固過程溶質偏析的影響,能夠根據連鑄條件(鋼中成分等)實時調整連鑄坯凝固末端壓下位置,應用效果穩定,降低了工業試驗成本,縮短了新產品連鑄工藝開發周期,提高了經濟效益。以上內容僅為本發明的較佳實施例,對于本領域的普通技術人員,依據本發明的思想,在具體實施方式及應用范圍上均會有改變之處,本說明書內容不應理解為對本發明的限制。當前第1頁12