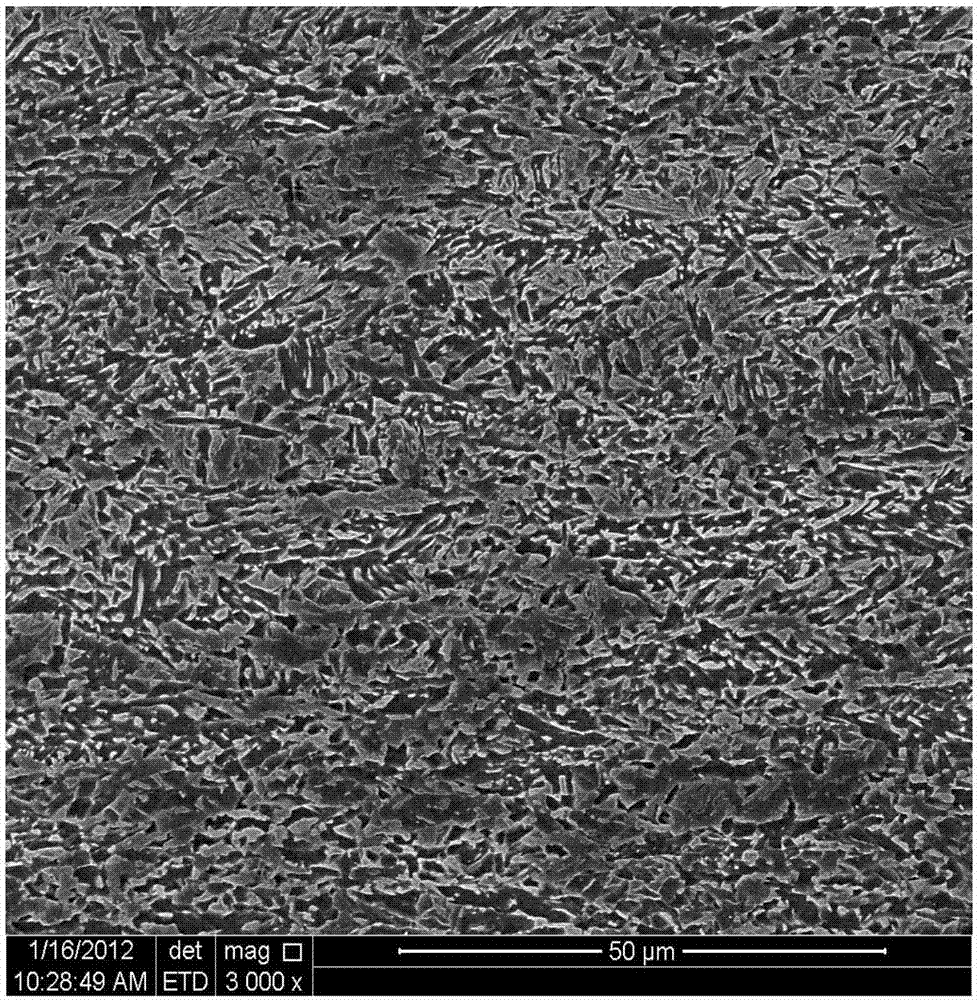
本發明屬于鋼板熱軋領域,涉及到一種具有耐沖刷磨損性能的管線鋼熱軋鋼帶及其生產方法,這種產品廣泛用于制造輸送漿體類的管線鋼管道。
背景技術:
:目前煤炭類資源還是主要采用公路、鐵路等傳統的運輸方式,每天數以萬計的重型卡車及火車來往運煤,遠遠超過承載能力,難以真正解決目前煤炭運輸的困局。因此采用大型管道輸送煤漿,再利用煤漿重新還原到煤粉,可以解決運力過載的局面。但是目前市場上管線鋼主要是用于石油、天然氣這種液體氣體的輸送。對此種管線鋼主要是要求其具有高強度及低溫韌性。輸送煤漿以及類似的固液二相介質的管線鋼還要考慮到煤漿中粉塵顆粒對管道的沖刷磨損影響。因此開發一種耐沖刷磨損性能的管線鋼是很有必要的。技術實現要素:本發明的目的是提供一種具有耐沖刷磨損性能的管線鋼熱軋鋼帶,用于制造輸送煤漿及相類似的固液二相介質的管道,此種熱軋板帶具有較好的強度、塑韌性及耐沖刷磨損性能。本發明還提供了一種具有耐沖刷磨損性能的管線鋼熱軋鋼帶的生產方法,采用低碳合金成分和恰當的煉鋼及合適的tmcp工藝,生產出在不影響力學性能的情況下,具有較好的耐沖刷磨損性能的熱軋板帶。鋼板生產是通過煉鋼、連鑄、加熱、控軋控冷、卷取和相關工藝而生產。本發明提供的一種具有耐沖刷磨損性能的管線鋼熱軋鋼帶,含有以下重量百分比的元素:c0.040~0.060%、si0.20~0.30%、mn1.70~1.80%、p≤0.012%、s≤0.0020%、als0.020~0.035%、cr0.20~0.24%、mo0.12~0.14%、nb0.06~0.08%、v0.02~0.04%、ti0.012~0.020%、n≤50ppm%,余量為fe。本發明提供的鋼材,不僅要滿足固液二相介質運輸強度要求,更要提高其耐沖刷磨損性能。在鋼種中添加cr、mo元素可以增加材料的硬度和耐磨性,但是會導致材料塑韌性的降低,考慮到塑韌性的提升以及在后續制造中的焊接性,這就需要在添加cr、mo元素提高材料硬度和耐磨性的同時添加、ni、v、ti元素等相關元素以改善其塑韌性和焊接性,并在后續的軋制過程中需要使用恰當的生產工藝來控制鋼材的最佳性能。本發明提供的一種具有耐沖刷磨損性能的管線鋼熱軋鋼帶的生產方法,包括以下流程:鐵水預處理→bof→吹氬→lf精煉→連鑄→加熱→軋制→卷取→重卷。進一步的,鐵水必須進行脫硫處理降低s含量≤0.0020%;進一步的,鑄坯落地冷卻時間≥36小時;進一步的,鑄坯冷裝入爐,在爐時間≥3.5小時;鋼坯出爐溫度按1250±30℃控制;進一步的,板卷中間坯目標厚度:60±5mm;進一步的,粗軋機壓下模式為3+5模式,精軋機七機架全部投入使用。進一步的,精軋機組壓下率采用均衡分配模式,增加f4~f7機架的壓下量,精軋壓縮比按≥3.0;進一步的,軋后冷卻采用前段層流冷卻模式。進一步的,均熱溫度1250±30℃,精軋終軋溫度890±30℃,卷取溫度650±30℃;進一步的,如生產厚度≥16mm的產品,卷取目標溫度下調20℃;進一步的,熱軋鋼卷厚度根據成品要求的不同可以調整。進一步的,所述重卷,厚度≤4.0mm以下投入平整。進一步的,轉爐盡量少使用鐵塊,提高優質廢鋼比例,避免鐵塊引起的硫高現象,進一步減輕專爐、精煉的脫硫任務。在lf冶煉工藝上進行優化,調整精煉造渣料配比,本著降低sio2活度的原則,取消鋁釩土合成渣造渣料,提高螢石品位,減少精煉前期鋁的加入量,避免出現精煉前期o急劇下降的現象。本發明工藝流程主要考慮一下三點:1)對鋼水純凈度的要求;2)重卷有助于表面質量檢查,并改善薄規格板形;3)滿足出口合同對產品質量及性能的要求。與現有技術相比,本發明通過加入mo、nb、v、ti等合金溶質元素,在實際生產中鐵基中通過均熱溫度1250±30℃的高溫達到固溶強化,此類溶質元素產生了彈性交互作用、化學交互作用和電子交互作用。溶質原子使固溶體基體點陣發生畸變,使固溶體中滑移阻力增加而強化。部分溶質原子可以降低合金系的層錯能,提高位錯分解的傾向,導致交滑移難于進行,從而達到合金被強化、穩定化學元素的作用。在軋制的過程中采用粗軋機壓下模式為3+5模式,精軋機七機架全部投入使用,增加f4~f7機架的壓下量的軋制模式,在微觀上可以使晶粒大小分布更均勻,宏觀上一定程度消除鋼材內部的缺陷如氣孔,縮松等,達到提高表面質量的作用。采用精軋終軋溫度890±30℃,卷取溫度650±30℃不同階段的目標溫度可以得到由針狀鐵素體、粒狀貝氏體及少量回火馬氏體構成的金相組織。馬氏體組織的存在一定程度上增加了材料的硬度,從而提高了耐磨性。金相組織中的貝氏體組織具有較高的強韌性配合,貝氏體實為鐵素體與碳化物的非層狀混合組織。因此組織中碳化物的出現進一步的提高了材料的耐沖刷磨損性能。采用本發明方法生產的鋼板力學性能中屈服強度達到580mpa以上、抗拉強度690mpa以上,-20℃夏比沖擊韌性沖擊功240j以上。通過實驗室環境72小時加速沖刷磨損試驗模擬鋼材在實際環境中使用8年的情況,本發明提供的鋼種的失重率僅為0.1%,完全可以滿足目前漿體輸送的使用要求。附圖說明圖1掃描電鏡金相組織;圖2掃描電鏡金相組織;圖3耐沖刷磨損機理;a)為本發明鋼材,b)為傳統鋼材;圖4耐沖刷磨損實驗室試驗結果對比,下面為本發明鋼材,上面為傳統鋼材。具體實施方式實施例1冶煉鋼水的化學成分見表1,余量為fe;表1鋼水化學成分wt%csimnpsals0.040~0.0600.20~0.301.70~1.80≤0.012≤0.00200.020~0.035crmonbvtin0.20~0.240.12~0.140.06~0.080.02~0.040.012~0.020≤50ppm成分設計上采用在基本五大常規元素的基礎上,添加了cr0.20~0.24%、mo0.12~0.14%元素提高材料硬度和耐磨性,并同時添加了nb0.06~0.08%、v0.02~0.04%、ti0.012~0.020%以改善其塑韌性和焊接性。一種具有耐沖刷磨損性能的管線鋼熱軋鋼帶的生產方法,包括以下流程:鐵水預處理→bof→吹氬→lf精煉→連鑄→加熱→軋制→卷取→重卷。具體的,鐵水必須進行脫硫處理降低s含量≤0.0020%。轉爐盡量少使用鐵塊,提高優質廢鋼比例,避免鐵塊引起的硫高現象,進一步減輕專爐、精煉的脫硫任務。在lf冶煉工藝上進行優化,調整精煉造渣料配比,本著降低sio2活度的原則,取消鋁釩土合成渣造渣料,提高螢石品位,減少精煉前期鋁的加入量,避免出現精煉前期o急劇下降的現象。生產工藝控制細節如下:1)鑄坯落地冷卻時間≥36小時。2)鑄坯冷裝入爐,在爐時間≥3.5小時;鋼坯出爐溫度按1250℃控制;3)板卷中間坯目標厚度:60mm;4)粗軋機壓下模式為3+5模式,精軋機七機架全部投入使用(正常情況下)。5)精軋機組壓下率采用均衡分配模式,適當增加f4~f7機架的壓下量,精軋壓縮比按≥3.0;6)軋后冷卻采用前段層流冷卻模式。7)均熱溫度1250℃,精軋終軋溫度890℃,卷取溫度650℃,如生產厚度≥16mm的產品,卷取溫度適當下調20℃,熱軋鋼卷厚度根據成品要求的不同可以調整。選取試驗試樣5組、每一組分別進行拉伸、沖擊、沖刷磨損試驗,結果見表2。表2試驗結果數據掃描電鏡金相組織如圖1、圖2;驗室72小時沖刷磨損試驗對比如圖4。本發明的具有耐沖刷磨損性能的管線鋼熱軋板帶不僅具有良好的化學成分穩定性、表面質量及較好的力學性能,相比較傳統的管線鋼熱軋板帶還具有較好的耐沖刷磨損性能。本發明通過此種控軋控冷軋制工藝生產的熱軋鋼帶其金相組織由針狀鐵素體、粒狀貝氏體及少量回火馬氏體構成。如圖1、圖2;馬氏體組織的存在一定程度上增加了材料的硬度,從而提高了耐磨性。金相組織中的貝氏體組織具有較高的強韌性配合,貝氏體實為鐵素體與碳化物的非層狀混合組織。因此組織中碳化物的出現進一步的提高了材料的耐沖刷磨損性能。材料在漿體輸送的環境比較復雜,其的損失率不僅僅完全由硬度所決定。根據多項研究表明,沖刷磨損與材料組織中碳化物的類型、數量、碳化物的類型、數量、大小、分布有很大關系,其機理見圖3所示。按照如上方法生產的鋼板力學性能中屈服強度達到560mpa以上、抗拉強度630mpa以上,-20℃夏比沖擊韌性沖擊功240j以上,其力學性能已達到了x80管線鋼級別。通過實驗室環境72小時加速沖刷磨損試驗模擬鋼材在實際環境中使用8年的情況,結果如圖4,本發明生產的鋼種的失重率僅為0.1%,完全可以滿足目前漿體輸送的使用要求。當前第1頁12