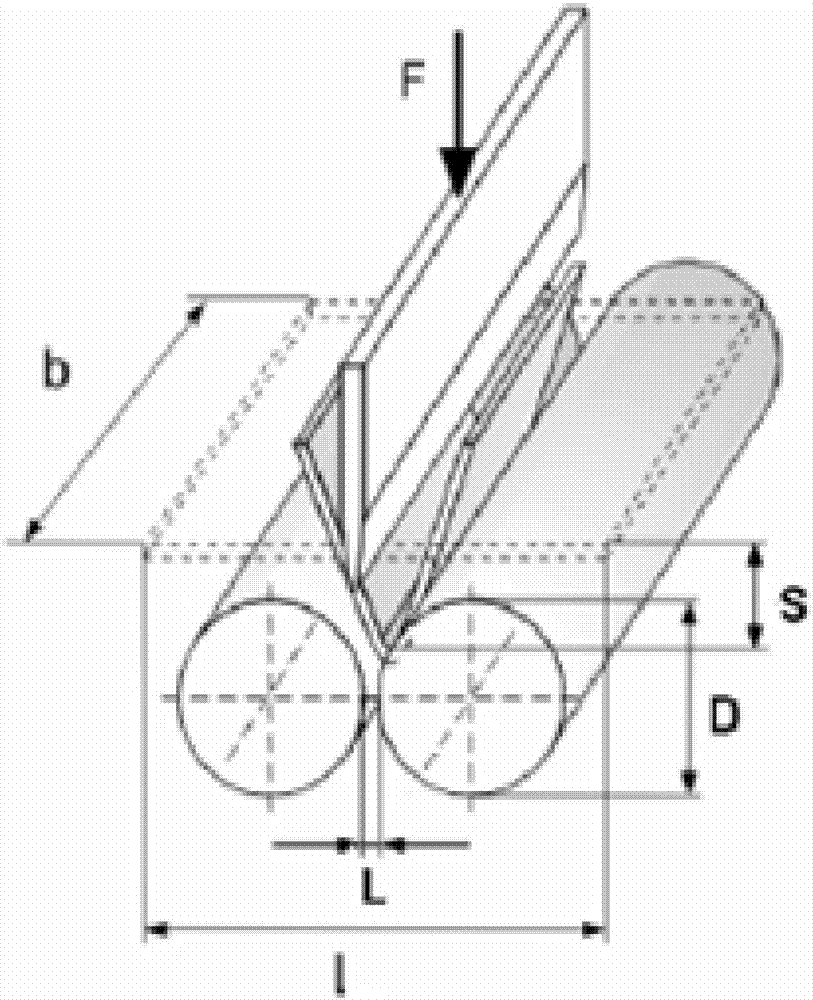
本發明屬于軋鋼
技術領域:
,涉及一種高韌性熱成形鋼及其制造方法。
背景技術:
:隨著汽車工業的發展,節能減排已成為當今世界共同關注的焦點。汽車輕量化是實現這一目標的主要措施。而汽車輕量化必須兼顧安全性,高強度汽車用鋼的應用則是節能減排、同時又保持汽車安全性的重要途徑。但是,高強度鋼板強度很高,在冷沖過程中易出現回彈嚴重、沖壓開裂、復雜零件沖壓成形困難等問題。目前,熱沖壓成形工藝可以克服上述的問題,并成為人們關注的焦點。熱沖壓成形過程為將鋼板加熱至奧氏體溫度區間保溫,然后利用鋼板在高溫下塑性良好、變形抗力小等特點,在裝有冷卻系統的模具中快速成形并淬火冷卻,以獲得超高強度零件,同時保證了零件的形狀及尺寸精度。在復雜的載荷條件下不僅要求熱成形零件具有高強度,同時也需要良好的塑韌性。然而,由于熱成形淬火后得到的全部為馬氏體組織,強度非常高,但是韌性不足,其強度可達1500mpa以上,而延伸率只有5%左右,三點彎曲角度一般在65度以下。中國專利200810112020.2一種熱成形馬氏體鋼,該鋼的主要化學成分(wt%)為:c:0.10~0.33%,si:0.50~2.30%,mn:0.50~2.00%,p:≤0.020%,s:≤0.015%,al:0.015~0.060%,o:≤0.002%,n:0.002~0.008%,其余為fe及不可避免的不純物。其抗拉強度為1300mpa~1700mpa,延伸率高于15%,主要通過添加0.50~2.30%的si,在熱成形工序中馬氏體轉變前采用緩冷工藝獲得一定量殘余奧氏體的方法,提高延伸率。然而此方法熱成形時工藝控制難度大,緩冷工藝使生產效率降低,同時,殘余奧氏體的存在也限制了應用。中國專利201110269388.1一種汽車用高韌性熱成形鋼板的熱處理方法,其成分質量百分比為:c:0.20~0.40%,si:0.10~0.50%,mn:1.0~2.0%,p:≤0.02%,s:≤0.01%,nb:0.02~0.06%,ti:0.01%~0.05%,cr:0.1~0.5%,b:0.001~0.005%,al:0.01~0.1%,n:≤0.01%,其余為fe及不可避免雜質。熱成形鋼板在沖壓成形后放入退火爐內;在100~500℃范圍內,進行1~10min的回火處理,將回火后的鋼板取出后再空氣中自然冷卻至室溫。該發明在傳統熱成形鋼的基礎上,通過回火的方法消除鋼板快速冷卻產生的內應力和軟化馬氏體組織,進而改善高強韌性鋼的韌性,但其強度也有較為明顯的降低,且生產效率及成本較高。中國專利201110259342.1一種雙相熱成形鋼的制備方法,該鋼的主要化學成分質量百分比為::c:0.10~0.50%,si:0.30~2.50%,mn:1.0~3.0%,p:≤0.02%,s:≤0.01%,al:1.0~3.0%,n:≤0.01%,余量為fe及不可避免雜質;制造方法為:首先根據化學成分進行冶煉鑄造,原料坯入加熱爐加熱,加熱溫度為1200~1250℃,保溫0.5~1.5小時,終軋溫度為800~900℃,卷取溫度為600~700℃;熱成形工藝為:加熱溫度為750~850℃,保溫3~8min,以大于40℃/s的速度冷卻至室溫,主要通過設置熱成形工藝的加熱溫度為780~850℃,進而使得熱成形鋼處于奧氏體和鐵素體對應的兩個相區,快冷即可獲得鐵素體和馬氏體構成的雙相組織。通過此方法雖然使得成形后的鋼板塑性增加,但強度大幅降低。中國專利201410209907.9汽車用高抗彎性能熱成形鋼及其制造方法,該鋼的主要化學成分質量百分比為:c:0.18~0.30%,si:≤0.30%,mn:1.00~1.60%,p:≤0.015%,s:≤0.0020%,nb:0.02%~0.10%,mo:0.15%~0.40%,v:≤0.10%,w:≤0.40%,ti:0.02%~0.06%,cr:0.10~0.30%,b:0.0005~0.0040%,al:0.020~0.060%,n:≤0.004%,o:≤0.003%,余量為fe及不可避免雜質;制造方法為:首先根據化學成分進行冶煉鑄造,原料坯入加熱爐加熱至1100~1250℃,保溫2.8~4小時,精軋溫度控制在820~890℃,卷取溫度為540~650℃,然后再進行冷軋退火處理。熱成形工藝為:加熱至奧氏體化溫度,保溫,以大于40℃/s的速度模淬至小于等于200℃。該方法通過加入大量的合金元素,細化晶粒,從而提高熱成形鋼的塑韌性。但是,大量的合金元素加入大大增加了材料的制造成本;同時,這種熱成形鋼是在傳統熱成形鋼的基礎進行的改進,主要還是通過添加b元素來提高淬透性,b元素的添加給鋼區生產帶來了一定的難度。技術實現要素:因此,基于上述背景,本文開發了一種汽車用高韌性熱成形鋼及其制造方法。(1)與中國專利200810112020.2(主要通過添加0.50~2.30%的si,在熱成形工序中馬氏體轉變前采用緩冷工藝獲得一定量殘余奧氏體的方法,提高延伸率。然而此方法熱成形時工藝控制難度大,緩冷工藝使生產效率降低)相比,本專利僅通過合金元素的控制,獲得高韌性的熱成形鋼,提高了生產效率;(2)與中國專利201110269388.1以及中國專利201110259342.1(利用軟相組織來提高鋼的韌性,但鋼的強度降低)相比,本專利在保證熱成形鋼強度的同時,提高了韌性;(3)與中國專利201410209907.9相比,本專利成分設計不含ti、mo、b等元素,合金成本更低、煉鋼工藝更易控制;同時也提高了熱成形鋼的延伸率與抗彎性能(彎曲角度大于80°)。(4)根據某高端主機廠要求,熱成形鋼在成形后的三點彎曲角度必須≥60°,本發明獲得的熱成形鋼三點彎曲角度達到了80°以上。為實現本發明鋼的制造,成分選擇、工藝過程和工藝內容如下:1)主要化學成分重量百分比為:c:0.1~0.25;si:0.1~0.5;mn:1.0~2.0;p:≤0.020;s:≤0.010;al:0.01~0.06;cr:0.1~0.5;nb:0.01~0.06。余量為fe和不可避免的雜質。2)生產工藝采用煉鋼→熱軋→酸軋→連退;3)采用專用保護渣;4)加熱出爐溫度控制在1150℃~1250℃;5)終軋溫度控制在850℃~950℃;6)卷取溫度:550℃~700℃;7)酸軋壓下率:50%~70%;8)退火溫度:700℃~850℃;9)熱成形加熱溫度:900℃~950℃;10)保溫時間:3min~10min;11)保壓時間:3s~12s。本發明在成功開發出的熱成形鋼屈服強度≥1000mpa、抗拉強度≥1500mpa、延伸率≥10%,三點彎曲角度≥80°。說明鋼板在具有高強度的同時也有良好的抗彎曲性能。附圖說明圖1(a)熱成形前鋼的組織:鐵素體+珠光體;圖1(b)熱成形后的組織:馬氏體;圖2vda238-100冷彎性能檢測標準具體實施方式下面根據附圖對本發明進行詳細描述,其為本發明多種實施方式中的一種優選實施例。鑄坯化學成分(wt%)為:c:0.1~0.25;si:0.1~0.5;mn:1.0~2.0;p:≤0.020;s:≤0.010;al:0.01~0.06;cr:0.1~0.5;nb:0.01~0.06。余量為fe和不可避免的雜質。1)鐵水預處理:要求前后扒渣;2)轉爐冶煉:出鋼進行脫氧合金化;同時加強出鋼擋渣操作;3)氬站:進行強攪操作對鋼包頂渣初步還原;4)lf爐精煉:出站前保證喂鈣線ca含量控制在0.0030~0.0050%;5)rh爐精煉:真空度在300pa以下保持時間12min以上;6)連鑄:中包目標溫度控制在液相線溫度以上20~40℃,采用專用保護渣;二次冷卻采用弱冷制度;7)加熱出爐溫度控制在1150℃~1250℃;8)終軋溫度控制在850℃~950℃;9)卷取溫度:550℃~700℃;10)酸軋壓下率:50%~70%;11)退火溫度:700℃~850℃;12)熱成形加熱溫度:900℃~950℃;13)保溫時間:3min~10min;14)保壓時間:3s~12s。鋼水的化學成分見表1,其余為fe和不可避免的雜質元素。表1實施例化學成分,wt%實施實例csimnpsalcrnb10.220.261.270.01/0.0320.350.03120.220.271.280.01/0.0320.370.032鋼水連鑄后,進行熱軋軋制,然后再進行酸軋和連續退火,最后經過熱成形沖壓,典型顯微組織如圖1所示。圖1為本發明所涉及的高抗彎性能熱成形鋼的顯微組織照片為4%硝酸腐蝕后顯微組織照片,組織為鐵素體+珠光體;熱成形后的組織為98%以上的馬氏體組織。其主要工藝參數和最終力學性能見表2。表2生產工藝與產品力學性能上面結合附圖對本發明進行了示例性描述,顯然本發明具體實現并不受上述方式的限制,只要采用了本發明的方法構思和技術方案進行的各種改進,或未經改進直接應用于其它場合的,均在本發明的保護范圍之內。當前第1頁12