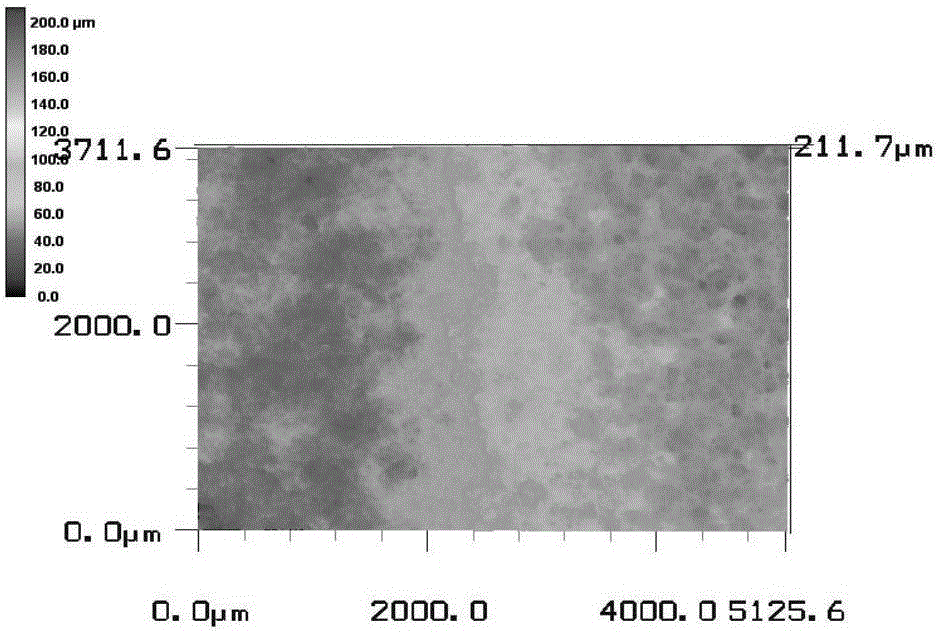
本發明屬于碳化硅陶瓷素坯表面預處理
技術領域:
,具體涉及一種選擇性去除反應燒結碳化硅表面殘留物的加工方法。
背景技術:
:碳化硅陶瓷不僅具有優良的常溫力學性能,如硬度高、抗彎強度大、耐腐蝕性好、摩擦系數低等,而且其高溫力學性能好。碳化硅陶瓷可以通過熱壓燒結、無壓燒結、熱等靜壓燒結等方法制備,其高溫強度可一直維持到1600℃,是陶瓷材料中高溫強度最好的材料。此外,碳化硅陶瓷具有優于其他非氧化物陶瓷的抗氧化性能。因此碳化硅陶瓷被廣泛應用于石油、化工、汽車、航空航天等各種領域。尤其在航空航天方面,由于碳化硅陶瓷比剛度大,所以被認為是前景最為廣闊的光學反射鏡材料。現有的生產光學級碳化硅陶瓷的主要方法是反應燒結。反應燒結是將α-SiC粉和石墨粉按比例混勻,經干壓、擠壓或注漿等方法制成多孔坯體,在高溫下與液態硅接觸,坯體中的碳與滲入的Si反應,生成β-SiC并與α-SiC相結合,游離硅填充了氣孔,從而得到高致密性的陶瓷材料。經反應燒結而成的碳化硅陶瓷素坯表面,不可避免地會存在一些表面殘留物。這些表面殘留物的主要成分是硅,以不規則的凸起物的形態粘結在碳化硅陶瓷素坯表面,對碳化硅陶瓷的進一步精密檢測和加工造成了很大的困難。由于碳化硅陶瓷的脆性較大,使用傳統機械加工的方法去除碳化硅表面殘留物時,很可能在去除掉硅的同時對碳化硅陶瓷造成損傷。且傳統的機械加工方法切削陶瓷表面殘留物時會產生大量的切削熱,也會對碳化硅陶瓷的性能產生影響。此外,傳統的機械加工方法很難適用于各種形狀的表面加工,因此尚且沒有一種合適的機械加工方法可以實現碳化硅表面殘留物的選擇性去除。目前去除這些凸起硅的方法主要是依靠人工打磨。人工打磨可以去除掉凸起物且避免損傷碳化硅,而且對于任何形狀的表面都適用。但是對于大口徑或大批量的碳化硅陶瓷,通過人工打磨的方法需要耗費大量的人力物力且存在加工效率低、工時長等問題,顯然是不符合經濟性的。此外,人工打磨的方法會產生很多固體粉塵,對環境造成污染且危害人體健康。技術實現要素:本發明的目的在于提供一種反應燒結碳化硅陶瓷表面殘留物的選擇性去除技術,可以在不損傷碳化硅陶瓷的情況下有效去除陶瓷表面的硅凸起,獲得表面粗糙度值Ra<6.3μm的表面。本發明具體實現方法是:碳化硅表面殘留物的主要成分是硅,基于碳化硅和硅在力學性質上的顯著差異,尤其是硬度相差很大,加工硅與碳化硅的難度有很大差別,加工硅所需要的磨料水射流能量遠小于加工碳化硅所需能量。通過調整磨料水射流的加工參數,選用“射流能量較小”的加工參數,使磨料水射流的射流能量可以銑削掉硅而不足以去除碳化硅,即:通過調整加工參數使磨料水射流具有選擇性去除的能力。本發明的技術方案為:反應燒結碳化硅表面殘留物的磨料水射流選擇性去除方法,如下:在一定的加工參數下,對碳化硅陶瓷素坯進行磨料水射流銑削,其中,所述的加工參數滿足的條件是:磨料水射流的射流能量僅僅銑削掉硅而不足以去除碳化硅。進一步的,所述的磨料水射流是通過磨料噴嘴后混合式超高壓磨料水射流加工系統控制噴嘴運動實現的,所述的噴嘴運動的路徑能夠覆蓋整個碳化硅陶瓷表面,保證相鄰路徑的間隔和掃描速度恒定。進一步的,在兩條射流中心軌跡保持一定間距的情況下,磨料噴嘴往返移動一個循環,將工件表面上一個射流加工區內的表面殘留物去除。噴嘴每往復移動一次,沿著與噴嘴橫移速度方向垂直的方向移動一定的距離(即橫向進給量數值),以實現整個碳化硅陶瓷素坯表面上的殘留物的去除。進一步的,所述的噴嘴的掃描路徑選擇為光柵狀掃描路徑,同心圓式的掃描路徑或螺旋線式的掃描路徑。進一步的,所述磨料水射流銑削的具體加工參數如下:磨料流量:每小時消耗的磨料的質量,為25kg/h;磨料種類為石榴石,磨料粒度為80目;噴射角度:水刀與工件表面所成的角度,為90度;水射流壓力:100~300MPa;靶距:水射流噴嘴距離工件表面的距離,為30~90mm;噴嘴橫移速度:噴嘴在加工方向上移動的速度,為500~1000mm/min;橫向進給量:水射流一次銑削加工過程中,噴嘴沿著與橫移速度方向垂直的方向移動的距離,為1~3mm。最終獲得表面粗糙度Ra<6.3μm的碳化硅陶瓷表面。本發明的工作原理和方法:選擇“射流能量較小”的加工參數,即射流壓力較小、靶距較大、噴嘴橫移速度較大的加工參數,使磨料水射流的能量較小且發散,并且對同一個位置沖擊的時間較短。由于硅的硬度遠小于碳化硅陶瓷的硬度,硅的切削加工性優于碳化硅,因此在射流能量較小的加工參數下,硅被去除掉而碳化硅不會被破壞。對碳化硅陶瓷素坯進行磨料水射流平面銑削,即在兩條射流中心軌跡保持一定間距的情況下,磨料噴嘴往返移動一個循環,將工件表面上一個射流加工區內的表面殘留物去除。噴嘴每往復移動一次,沿著與噴嘴橫移速度方向垂直的方向移動一定的距離(即橫向進給量數值),以實現整個碳化硅陶瓷素坯表面上的殘留物的去除。本發明的有益效果為:采用磨料水射流選擇性去除的方法,可以自動高效地去除碳化硅素坯表面粘結的殘留物。與人工打磨相比,可以節省人力物力,提高生產效率。相較于傳統的機械加工方式,磨料水射流屬于冷加工范疇,在去除碳化硅表面凸起物的同時不會對碳化硅產生熱影響。且磨料水射流加工清潔,不會產生有害人體健康的粉塵等,對環境無污染。通過該種方法,可以得到表面粗糙度值Ra<6.3μm的碳化硅陶瓷表面。附圖說明圖1、圖2、圖3為水射流噴嘴掃描路徑圖,依次為光柵狀掃描路徑圖、同心圓狀掃描路徑圖、螺旋線狀掃描路徑圖;圖4為未加工之前碳化硅素坯的表面形貌圖;圖5、圖6為具體實施例1中,經磨料水射流“射流能量較大”的加工參數銑削之后的碳化硅陶瓷表面形貌圖及其在顯微鏡下觀測到的表面微觀形貌的3D圖。圖7、圖8為具體實施例2中,經磨料水射流“射流能量較小”的加工參數銑削之后的碳化硅陶瓷表面形貌圖以及在顯微鏡下觀測到的表面微觀形貌的3D圖;圖9、圖10為具體實施例3中,經磨料水射流“射流能量較小”的加工參數銑削之后的碳化硅陶瓷表面形貌圖以及在顯微鏡下觀測到的表面微觀形貌的3D圖。具體實施方式結合附圖發明作進一步說明。本具體實現的原理是:碳化硅表面殘留物的主要成分是硅,基于碳化硅和硅在力學性質上的顯著差異,尤其是硬度相差很大,加工硅與碳化硅的難度有很大差別,加工硅所需要的磨料水射流能量遠小于加工碳化硅所需能量。通過調整磨料水射流的加工參數,選用“射流能量較小”的加工參數,使磨料水射流的射流能量可以銑削掉硅而不足以去除碳化硅,即:通過調整加工參數使磨料水射流具有選擇性去除的能力;根據上述原理本發明公開了一種反應燒結碳化硅表面殘留物的磨料水射流選擇性去除方法,具體如下:在一定的加工參數下,對碳化硅陶瓷素坯進行磨料水射流銑削,其中,所述的加工參數滿足的條件是:磨料水射流的射流能量僅僅銑削掉硅而不足以去除碳化硅。進一步的,所述的磨料水射流是通過磨料噴嘴實現的,所述的噴嘴運動的路徑能夠覆蓋整個碳化硅陶瓷表面,保證相鄰路徑的間隔和掃描速度恒定。進一步的,在兩條射流中心軌跡保持一定間距的情況下,磨料噴嘴往返移動一個循環,將工件表面上一個射流加工區內的表面殘留物去除。噴嘴每往復移動一次,沿著與噴嘴橫移速度方向垂直的方向移動一定的距離(即橫向進給量數值),以實現整個碳化硅陶瓷素坯表面上的殘留物的去除。進一步的,所述的噴嘴的掃描路徑選擇為光柵狀掃描路徑,同心圓式的掃描路徑或螺旋線式的掃描路徑,具體的如圖1、2、3所示,依次為光柵狀掃描路徑圖、同心圓狀掃描路徑圖、螺旋線狀掃描路徑圖。進一步的,所述磨料水射流銑削的具體加工參數如下:磨料流量:每小時消耗的磨料的質量,為25kg/h;磨料種類:為石榴石,磨料粒度為80目;噴射角度:水刀與工件表面所成的角度,為90度;水射流壓力:100~300MPa;靶距:水射流噴嘴距離工件表面的距離,為30~90mm;噴嘴橫移速度:噴嘴在加工方向上移動的速度,為500~1000mm/min;橫向進給量:水射流一次銑削加工過程中,噴嘴沿著與橫移速度方向垂直的方向移動的距離,為1~3mm。最終獲得表面粗糙度Ra<6.3μm的碳化硅陶瓷表面。下面例舉三個具體的實施例,對本發明的效果進行說明:在試驗前,未經處理的碳化硅陶瓷素坯表面如圖4所示,可以看到在未經處理的碳化硅陶瓷素坯表面遍布著形狀不規則的凸起物;實施例1:射流壓力、靶距、噴嘴橫移速度如表1所示,其余參數采用磨料流量:每小時消耗的磨料的質量,為25kg/h;磨料種類:為石榴石,磨料粒度為80目;噴射角度:水刀與工件表面所成的角度,為90度;橫向進給量選擇1mm。銑削后碳化硅陶瓷表面效果如圖5、6所示,可以看出當射流能量較大時,可以很好地去除碳化硅表面的硅,需進一步驗證碳化硅是否被除去;經測量加工后的表面粗糙度為4.359μm。表1磨料水射流銑削碳化硅陶瓷加工參數單位銑削參數射流壓力MPa300靶距mm30噴嘴橫移速度mm/min500實施例2:射流壓力、靶距、噴嘴橫移速度如表2所示,其余參數采用磨料流量:每小時消耗的磨料的質量,為25kg/h;磨料種類:為石榴石,磨料粒度為80目;噴射角度:水刀與工件表面所成的角度,為90度;橫向進給量選擇2mm。銑削后碳化硅陶瓷表面效果如圖7、8所示,可以看出當射流能量較小時,可以很好地去除碳化硅表面的硅。通過與圖5、6觀測到的微觀圖進行對比,發現兩次加工過程射流能量不同,以未加工表面為基準測得的加工深度不同,可以說明當射流能量較大時,磨料水射流不僅去除了凸起硅還會除掉一部分碳化硅,即未實現選擇性去除;經測量加工后的表面粗糙度為4.442μm。表2磨料水射流銑削碳化硅陶瓷加工參數單位銑削參數射流壓力MPa100靶距mm60噴嘴橫移速度mm/min1000實施例3:射流壓力、靶距、噴嘴橫移速度如表3所示,其余參數采用磨料流量:每小時消耗的磨料的質量,為25kg/h;磨料種類:為石榴石,磨料粒度為80目;噴射角度:水刀與工件表面所成的角度,為90度;橫向進給量選擇3mm。銑削后碳化硅陶瓷表面效果如圖9、10所示,通過與圖7、8觀測到的微觀圖進行對比,發現兩次加工過程射流能量不同,但以未加工表面為基準測得的加工深度大致相同,為211μm左右。可以說明當射流能量較小時,磨料水射流只去除了碳化硅表面的硅,而對碳化硅沒有影響,即:可證明磨料水射流對碳化硅陶瓷表面的殘留物具有選擇去除能力。經測量加工后的表面粗糙度為5.471μm。表3磨料水射流銑削碳化硅陶瓷加工參數單位銑削參數射流壓力MPa100靶距mm90噴嘴橫移速度mm/min1000上述雖然結合附圖對本發明的具體實施方式進行了描述,但并非對本發明保護范圍的限制,所屬領域技術人員應該明白,在本發明的技術方案的基礎上,本領域技術人員不需要付出創造性勞動即可做出的各種修改或變形仍在本發明的保護范圍以內。當前第1頁1 2 3