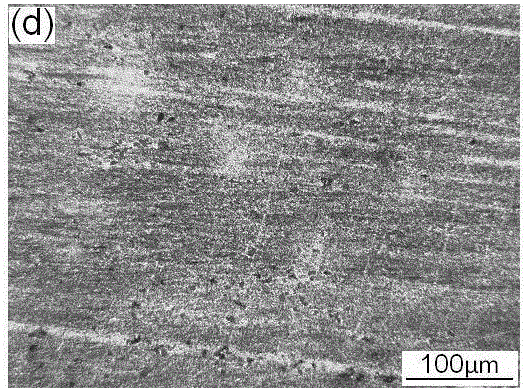
本發明屬于鋁合金材料
技術領域:
,具體為一種超高強度鋁合金板材的軋制方法。
背景技術:
:鋁合金由于其密度小、比強度和比剛度高、彈性好、抗沖擊性能良好、耐腐蝕、耐磨、易表面著色、良好的加工成型性以及高的回收再生性等特點,廣泛應用于航空、航天、汽車、機械制造、船舶、建筑、裝修等領域,其強度一般在480-500MPa之間。隨著近年來科學技術及工業經濟的飛速發展進一步提高鋁合金材料性能已成為當今國際鋁業界共同關注的問題。國家大飛機計劃的實施,對高強高韌、抗疲勞、耐熱性好的鋁合金的力學性能提出了更高的要求,因此發展大尺寸、高強高韌耐熱鋁合金薄板制備新方法,制備高強高韌的耐熱鋁合金板材,以滿足航空制造業對高性能耐熱鋁合金薄板的需求成為當前亟待解決的問題,是當前科學界和工程界研究的熱點。然而在提高鋁合金材料的強度和韌性的同時,鋁合金材料的耐久性以及損傷容限無法同步提高,甚至降低。技術實現要素:針對上述問題,本發明提供一種超高強度鋁合金板材的軋制方法,該工藝制備的鋁合金板材強度在600MPa以上,在保證提高鋁合金材料的強度和韌性的同時,提高其耐損傷性,延長其使用壽命。為實現上述發明目的,本發明的技術方案如下:所述的超高強度鋁合金板材的軋制方法,包括如下步驟:A、將精煉結束后的鋁合金錠坯在450-550℃下均勻化退火24-48h;B、控制退火后的鋁合金錠坯的溫度在360~440℃,待鋁合金錠坯內外溫度均勻后,對其進行單道次2~5%的熱軋預變形,繼續控制鋁合金錠坯的溫度為360~440℃,然后進行單道次不小于60%的大壓下量軋制變形,軋制得到厚板坯,將厚板坯進行水冷或空冷;C、將冷卻后的厚板坯在450-550℃下進行0.5-3h固溶處理,然后水淬;D、將水淬后的厚板坯在150-250℃下進行6h的預時效處理,然后空冷至室溫;E、將空冷至室溫后的厚板坯進行單道次40~60%的冷軋變形,得到板材,然后對板材進行120~200℃的終時效處理,處理時間為3~8h。優選地,所述的步驟A中鋁合金錠坯的退化溫度為460-500℃。優選地,所述的步驟C中固溶溫度為480-520℃。優選地,所述的熱軋和冷軋過程中,軋輥軋制線速度為0.4~0.6m/min。優選地,所述的鋁合金錠坯為1-8系鋁合金錠坯中的任一種。優選地,所述的鋁合金錠坯為Al-Cu-Mg合金錠坯。優選地,所述的Al-Cu-Mg合金錠坯的成分配比為:Cu4.0~4.8%,Mg1.3~1.8%,Mn0.4~0.6%,Ti0.1~0.3%,Zr0.1~0.3%,Er0.2~0.5%,其余為Al。優選地,所述的Al-Cu-Mg合金錠坯的鑄造方法為:將所述的各個成分在740-780℃下進行熔煉,熔煉過程中采用氮氣保護,并采用鈉鹽與六氯乙烷進行精煉和除氣,制得Al-Cu-Mg合金錠坯。本發明的有益效果為:本發明的超高強度鋁合金板材的軋制方法,能夠消除板材枝晶偏析問題,實現合金成分均勻化;并且能夠提高合金的顯微硬度,確保其各部分力學性能均勻一致,保證零件的使用性能;同時提高板材的強度及其耐損傷性,延長其使用壽命。附圖說明圖1為本發明對照組1鋁合金板材的顯微組織圖圖2-4為本發明實施例1-3軋制方法制備的鋁合金板材的顯微組織圖圖5為本發明實施例5的軋制方法制備的鋁合金板材的應力-應變曲線圖。具體實施方式下面通過具體實施例對本發明進行詳細說明。實施例1本發明的超高強度鋁合金板材的軋制方法,包括如下步驟:A、將精煉結束后的Al-Cu-Mg合金錠坯在450℃下均勻化退火24h;B、控制退火后的Al-Cu-Mg合金錠坯的溫度在360℃,待Al-Cu-Mg合金錠坯內外溫度均勻后,對其進行單道次2%的熱軋預變形,軋輥軋制線速度為0.4m/min,繼續控制Al-Cu-Mg合金錠坯的溫度為360℃,然后進行單道次60%的大壓下量軋制變形,軋輥軋制線速度為0.4m/min,軋制得到厚板坯,將厚板坯進行水冷或空冷;C、將冷卻后的厚板坯在450℃下進行0.5h固溶處理,然后水淬;D、將水淬后的厚板坯在150℃下進行6h的預時效處理,然后空冷至室溫;E、將空冷至室溫后的厚板坯進行單道次40%的冷軋變形,軋輥軋制線速度為0.4m/min,得到板材,然后對板材進行120℃的終時效處理,處理時間為3h。所述的Al-Cu-Mg合金錠坯的成分配比為:Cu4.0%,Mg1.3%,Mn0.4%,Ti0.1%,Zr0.1%,Er0.2%,其余為Al。所述的Al-Cu-Mg合金錠坯的鑄造方法為:將所述的各個成分在740℃下進行熔煉,熔煉過程中采用氮氣保護,并采用鈉鹽與六氯乙烷進行精煉和除氣,制得Al-Cu-Mg合金錠坯。實施例2本發明的超高強度鋁合金板材的軋制方法,包括如下步驟:A、將精煉結束后的Al-Cu-Mg合金錠坯在460℃下均勻化退火28h;B、控制退火后的Al-Cu-Mg合金錠坯的溫度在380℃,待Al-Cu-Mg合金錠坯內外溫度均勻后,對其進行單道次3%的熱軋預變形,軋輥軋制線速度為0.5m/min,繼續控制Al-Cu-Mg合金錠坯的溫度為380℃,然后進行單道次62%的大壓下量軋制變形,軋輥軋制線速度為0.5m/min,軋制得到厚板坯,將厚板坯進行水冷或空冷;C、將冷卻后的厚板坯在480℃下進行1h固溶處理,然后水淬;D、將水淬后的厚板坯在180℃下進行6h的預時效處理,然后空冷至室溫;E、將空冷至室溫后的厚板坯進行單道次45%的冷軋變形,軋輥軋制線速度為0.5m/min,得到板材,然后對板材進行140℃的終時效處理,處理時間為5h。所述的Al-Cu-Mg合金錠坯的成分配比為:Cu4.2%,Mg1.5%,Mn0.5%,Ti0.2%,Zr0.2%,Er0.3%,其余為Al。所述的Al-Cu-Mg合金錠坯的鑄造方法為:將所述的各個成分在75℃下進行熔煉,熔煉過程中采用氮氣保護,并采用鈉鹽與六氯乙烷進行精煉和除氣,制得Al-Cu-Mg合金錠坯。實施例3本發明的超高強度鋁合金板材的軋制方法,包括如下步驟:A、將精煉結束后的Al-Cu-Mg合金錠坯在500℃下均勻化退火32h;B、控制退火后的Al-Cu-Mg合金錠坯的溫度在400℃,待Al-Cu-Mg合金錠坯內外溫度均勻后,對其進行單道次4%的熱軋預變形,軋輥軋制線速度為0.6m/min,繼續控制Al-Cu-Mg合金錠坯的溫度為400℃,然后進行單道次65%的大壓下量軋制變形,軋輥軋制線速度為0.6m/min,軋制得到厚板坯,將厚板坯進行水冷或空冷;C、將冷卻后的厚板坯在500℃下進行1.5h固溶處理,然后水淬;D、將水淬后的厚板坯在200℃下進行6h的預時效處理,軋輥軋制線速度為0.6m/min,然后空冷至室溫;E、將空冷至室溫后的厚板坯進行單道次50%的冷軋變形,得到板材,然后對板材進行160℃的終時效處理,處理時間為6h。所述的Al-Cu-Mg合金錠坯的成分配比為:Cu4.5%,Mg1.6%,Mn0.6%,Ti0.3%,Zr0.3%,Er0.4%,其余為Al。所述的Al-Cu-Mg合金錠坯的鑄造方法為:將所述的各個成分在760℃下進行熔煉,熔煉過程中采用氮氣保護,并采用鈉鹽與六氯乙烷進行精煉和除氣,制得Al-Cu-Mg合金錠坯。實施例4本發明的超高強度鋁合金板材的軋制方法,包括如下步驟:A、將精煉結束后的Al-Cu-Mg合金錠坯在530℃下均勻化退火40h;B、控制退火后的Al-Cu-Mg合金錠坯的溫度在420℃,待Al-Cu-Mg合金錠坯內外溫度均勻后,對其進行單道次5%的熱軋預變形,軋輥軋制線速度為0.5m/min,繼續控制Al-Cu-Mg合金錠坯的溫度為420℃,然后進行單道次66%的大壓下量軋制變形,軋輥軋制線速度為0.5m/min,軋制得到厚板坯,將厚板坯進行水冷或空冷;C、將冷卻后的厚板坯在520℃下進行2h固溶處理,然后水淬;D、將水淬后的厚板坯在220℃下進行6h的預時效處理,然后空冷至室溫;E、將空冷至室溫后的厚板坯進行單道次55%的冷軋變形,軋輥軋制線速度為0.5m/min,得到板材,然后對板材進行180℃的終時效處理,處理時間為7h。所述的Al-Cu-Mg合金錠坯的成分配比為:Cu4.6%,Mg1.7%,Mn0.5%,Ti0.1%,Zr0.1~0.3%,Er0.5%,其余為Al。所述的Al-Cu-Mg合金錠坯的鑄造方法為:將所述的各個成分在770℃下進行熔煉,熔煉過程中采用氮氣保護,并采用鈉鹽與六氯乙烷進行精煉和除氣,制得Al-Cu-Mg合金錠坯。實施例5本發明的超高強度鋁合金板材的軋制方法,包括如下步驟:A、將精煉結束后的Al-Cu-Mg合金錠坯在550℃下均勻化退火48h;B、控制退火后的Al-Cu-Mg合金錠坯的溫度在440℃,待Al-Cu-Mg合金錠坯內外溫度均勻后,對其進行單道次5%的熱軋預變形,軋輥軋制線速度為0.6m/min,繼續控制Al-Cu-Mg合金錠坯的溫度為440℃,然后進行單道次68%的大壓下量軋制變形,軋輥軋制線速度為0.6m/min,軋制得到厚板坯,將厚板坯進行水冷或空冷;C、將冷卻后的厚板坯在550℃下進行3h固溶處理,然后水淬;D、將水淬后的厚板坯在250℃下進行6h的預時效處理,然后空冷至室溫;E、將空冷至室溫后的厚板坯進行單道次60%的冷軋變形,軋輥軋制線速度為0.6m/min,得到板材,然后對板材進行200℃的終時效處理,處理時間為8h。所述的Al-Cu-Mg合金錠坯的成分配比為:Cu4.8%,Mg1.8%,Mn0.6%,Ti0.3%,Zr0.3%,Er0.0.5%,其余為Al。所述的Al-Cu-Mg合金錠坯的鑄造方法為:將所述的各個成分在740-780℃下進行熔煉,熔煉過程中采用氮氣保護,并采用鈉鹽與六氯乙烷進行精煉和除氣,制得Al-Cu-Mg合金錠坯。實施例6本發明的超高強度鋁合金板材的軋制方法,包括如下步驟:A、將精煉結束后的2A12鋁合金錠坯在550℃下均勻化退火48h;B、控制退火后的2A12鋁合金錠坯的溫度在440℃,待2A12鋁合金錠坯內外溫度均勻后,對其進行單道次5%的熱軋預變形,軋輥軋制線速度為0.6m/min,繼續控制2A12鋁合金錠坯的溫度為440℃,然后進行單道次68%的大壓下量軋制變形,軋輥軋制線速度為0.6m/min,軋制得到厚板坯,將厚板坯進行水冷或空冷;C、將冷卻后的厚板坯在550℃下進行3h固溶處理,然后水淬;D、將水淬后的厚板坯在250℃下進行6h的預時效處理,然后空冷至室溫;E、將空冷至室溫后的厚板坯進行單道次60%的冷軋變形,軋輥軋制線速度為0.6m/min,得到板材,然后對板材進行200℃的終時效處理,處理時間為8h。所述的2A12鋁合金錠坯的成分配比為:硅Si≤0.50,Cu3.8~4.9,Mg1.2~1.8,Zn≤0.30,Mn0.30~0.9,Ti≤0.15,Ni≤0.10,Fe0.000~0.500,Fe+Ni0.000~0.500,其他單個≤0.05、合計≤0.10,Al余量。所述的2A12鋁合金錠坯的鑄造方法為:將所述的各個成分在740-780℃下進行熔煉,熔煉過程中采用氮氣保護,并采用鈉鹽與六氯乙烷進行精煉和除氣,制得2A12鋁合金錠坯。實施例7本發明的超高強度鋁合金板材的軋制方法,包括如下步驟:A、將精煉結束后的5083鋁合金錠坯在530℃下均勻化退火40h;B、控制退火后的5083鋁合金錠坯的溫度在420℃,待5083鋁合金錠坯內外溫度均勻后,對其進行單道次5%的熱軋預變形,軋輥軋制線速度為0.5m/min,繼續控制5083鋁合金錠坯的溫度為420℃,然后進行單道次66%的大壓下量軋制變形,軋輥軋制線速度為0.5m/min,軋制得到厚板坯,將厚板坯進行水冷或空冷;C、將冷卻后的厚板坯在520℃下進行2h固溶處理,然后水淬;D、將水淬后的厚板坯在220℃下進行6h的預時效處理,然后空冷至室溫;E、將空冷至室溫后的厚板坯進行單道次55%的冷軋變形,軋輥軋制線速度為0.5m/min,得到板材,然后對板材進行180℃的終時效處理,處理時間為7h。所述的5083鋁合金錠坯的成分配比為:Cu4.6%,Mg1.7%,Mn0.5%,Ti0.1%,Zr0.1~0.3%,Er0.5%,其余為Al。所述的5083鋁合金錠坯的鑄造方法為:將所述的各個成分在770℃下進行熔煉,熔煉過程中采用氮氣保護,并采用鈉鹽與六氯乙烷進行精煉和除氣,制得5083鋁合金錠坯。實施例8本發明的超高強度鋁合金板材的軋制方法,包括如下步驟:A、將精煉結束后的6082鋁合金錠坯在500℃下均勻化退火32h;B、控制退火后的6082鋁合金錠坯的溫度在400℃,待6082鋁合金錠坯內外溫度均勻后,對其進行單道次4%的熱軋預變形,軋輥軋制線速度為0.6m/min,繼續控制6082鋁合金錠坯的溫度為400℃,然后進行單道次65%的大壓下量軋制變形,軋輥軋制線速度為0.6m/min,軋制得到厚板坯,將厚板坯進行水冷或空冷;C、將冷卻后的厚板坯在500℃下進行1.5h固溶處理,然后水淬;D、將水淬后的厚板坯在200℃下進行6h的預時效處理,軋輥軋制線速度為0.6m/min,然后空冷至室溫;E、將空冷至室溫后的厚板坯進行單道次50%的冷軋變形,得到板材,然后對板材進行160℃的終時效處理,處理時間為6h。所述的6082鋁合金錠坯的成分配比為:Si0.7~1.3,Fe0.50,Cu0.10,Mn0.40~1.0,Mg:0.6~1.2,Cr0.25,Zn0.20,Ti0.10,Al余量。所述的6082鋁合金錠坯的鑄造方法為:將所述的各個成分在760℃下進行熔煉,熔煉過程中采用氮氣保護,并采用鈉鹽與六氯乙烷進行精煉和除氣,制得6082鋁合金錠坯。實施例9本發明的超高強度鋁合金板材的軋制方法,包括如下步驟:A、將精煉結束后的7A09鋁合金錠坯在460℃下均勻化退火28h;B、控制退火后的7A09鋁合金錠坯的溫度在380℃,待7A09鋁合金錠坯內外溫度均勻后,對其進行單道次3%的熱軋預變形,軋輥軋制線速度為0.5m/min,繼續控制7A09鋁合金錠坯的溫度為380℃,然后進行單道次62%的大壓下量軋制變形,軋輥軋制線速度為0.5m/min,軋制得到厚板坯,將厚板坯進行水冷或空冷;C、將冷卻后的厚板坯在480℃下進行1h固溶處理,然后水淬;D、將水淬后的厚板坯在180℃下進行6h的預時效處理,然后空冷至室溫;E、將空冷至室溫后的厚板坯進行單道次45%的冷軋變形,軋輥軋制線速度為0.5m/min,得到板材,然后對板材進行140℃的終時效處理,處理時間為5h。所述的7A09鋁合金錠坯的成分配比為:Si0.50,Fe0.50,Cu1.2-2.0,Mn0.15,Mg2.0-3.0,Cr0.16-0.30,Zn5.1-6.1,Ti0.10,其他單個0.05、合計0.10,Al余量。所述的7A09鋁合金錠坯的鑄造方法為:將所述的各個成分在75℃下進行熔煉,熔煉過程中采用氮氣保護,并采用鈉鹽與六氯乙烷進行精煉和除氣,制得7A09鋁合金錠坯。實施例10對比實驗對照組1-5:將本發明的Al-Cu-Mg合金錠坯、2A12鋁合金錠坯、5083鋁合金錠坯、6082鋁合金錠坯、7A09鋁合金錠坯,分別在常規工藝條件下進行軋制。常規工藝步驟包括鑄造、冷軋、固溶處理、時效預處理。鑄造步驟中,以100~500℃/s的冷卻速度從液相線溫度冷卻到固相線溫度;冷軋步驟中,控制冷軋壓下率為70~90%;固溶處理步驟中,將鋁合金板以80~120℃/s的加熱速度加熱到500~560℃,保溫5s~15s,然后以30~150℃/s的冷卻速度冷卻到20~60℃;時效預處理步驟中,將鋁合金板以10~100℃/s的加熱速度加熱到85~120℃,保溫5s~15s,然后以30~150℃/s的冷卻速度冷卻到20~60℃。實驗組:按照本發明實施例1~9軋制方法制備的鋁合金板材。測試對照組1-5及實驗組1-9的力學性能,包括抗拉強度、伸長率,對比結果如表1所示:表1各工藝方法制備的板材的力學性能樣品合金抗拉強度(25℃、MPa)伸長率(%)對照組1Al-Cu-Mg50010實施例1Al-Cu-Mg60012實施例2Al-Cu-Mg61514實施例3Al-Cu-Mg63015實施例4Al-Cu-Mg64418實施例5Al-Cu-Mg65216對照組22A1241012實施例62A1249615對照組3508332730實施例7508341836對照組4608224510實施例8608231615對照組57A095305實施例97A096368由表1可知,本發明實施例1-5的軋制方法制備的板材,抗拉強度比對照組1高20-30%,拉伸率比對照組1高20-80%;實施例6的制備的板材,抗拉強度比對照組2高21%,伸長率比對照組2高23%;實施例7的制備的板材,抗拉強度比對照組3高28%,伸長率比對照組2高20%;實施例8的制備的板材,抗拉強度比對照組4高29%,伸長率比對照組2高50%;實施例9的制備的板材,抗拉強度比對照組5高20%,伸長率比對照組2高20%;可見,由本發明的軋制方法制備的板材,其力學性能明顯優于常規方法制備的板材。實施例7從附圖1可以看出:普通鋁合金板材的鑄態組織圖中存在大量粗大的析出相,這表明合金的組織性能均勻性不夠理想。從附圖2-4可以看出:本發明軋制方法制備的鋁合金板材,網格狀析出相已經消失或部分消失,部分消失的情況下也只有較少量的顆粒狀析出物,已經取得了較大的改善,體現了更好的均勻化效果。由圖5可以看出,本發明實施例5的Al-Cu-Mg合金板材在應力低于652MPa時,應力隨著應變的增大而增大,在652MPa時,達到極限載荷,此時的應變為16%;652MPa之后,板材開始發生不均勻塑性變形并形成縮頸,應力下降,最后應力達到630Mpa時板材斷裂。當前第1頁1 2 3