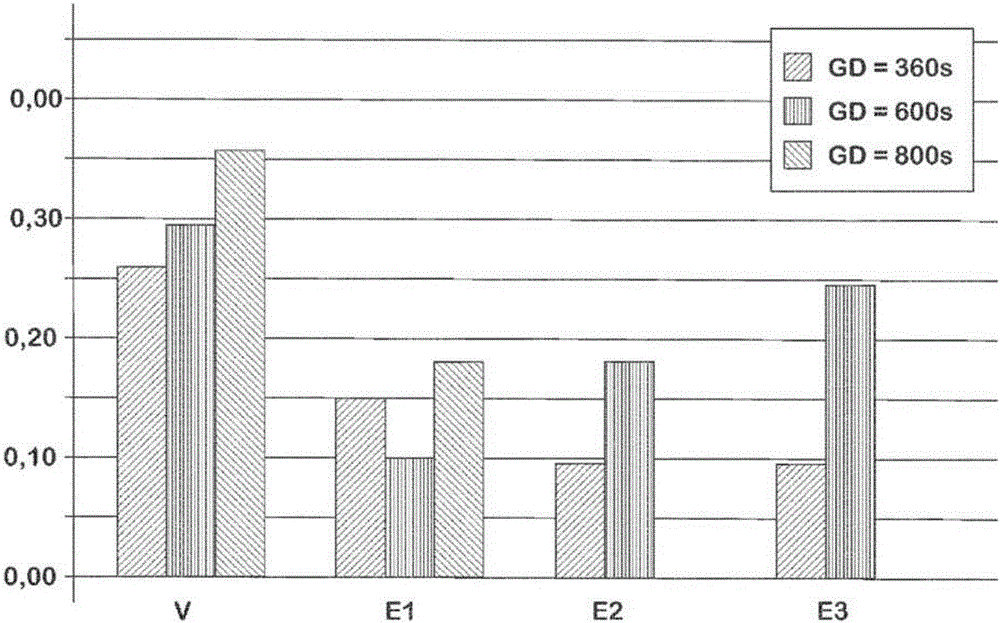
本發明涉及一種用于熱成型的扁鋼產品,該扁鋼產品由鋼基底和涂覆在鋼基底上的、基于Al的保護涂層而組成,鋼基底由具有0.1-3重量%的Mn和0.0005-0.01重量%的B的鋼制成,保護涂層可選地含有總共最大20重量%的其他合金元素。本發明同樣還涉及一種用于制造按照本發明的扁鋼產品的方法。另外,本發明還涉及一種通過熱壓淬火制成的鋼部件。本發明還涉及一種用于制造這類鋼部件的方法。
背景技術:
:“扁鋼產品”的概念在此為所有的軋制產品,其長度較其厚度而言大很多。為此,鋼帶和鋼板以及由其獲得的切割件和扁坯都屬于扁鋼產品。當在此作出合金的含量的規定時,只要沒有其他說明,則合金的含量總是以“重量%”理解。按照本發明的扁鋼產品的鋼基底由所謂的“MnB鋼”組成。這類鋼在EN10083-3中標準化。這些鋼具有良好的可硬化性并且在熱壓期間允許可靠的過程實施,通過該過程實施以經濟的方式實現了,無需額外冷卻,在熱成型過程中仍在工具中產生馬氏體硬化。這種鋼的典型實例是以名稱22MnB5已知的鋼,其可以在2004年的德國鋼編碼(Stahlschlüssel)中以材料編號1.5528找到。市場可購買到的完全鎮靜的22MnB5鋼除了含有鐵和不可避免的雜質之外通常還含有(以重量%計的):0.10-0.250%的C、1.0-1.4%的Mn、0.35-0.4%的Si、最多0.03%的P、最多0.01%的S、最多0.040%的Al、最多0.15%的Ti、最多0.1%的Nb、總計至多0.5%的Cr+Mo以及最多0.005%的B。對于熱軋的并且設置有Al涂層的MnB鋼板,其通過熱壓淬火用于制造鋼部件,在EP0971044Bl中說明了一種合金規格,根據該合金標準,MnB鋼除了含有鐵和不可避免的雜質之外還含有(以重量%計的):大于0.20%但小于0.5%的碳含量、大于0.5%但小于3%的錳含量、大于0.1%但小于0.5%的硅含量、大于0.01%但小于1%的鉻含量、小于0.2%的鈦含量、小于0.1%的鋁含量、小于0.1%的磷含量、小于0.05%的硫含量、大于0.0005%但小于0.08%的硼含量。Al涂層為所謂的AlSi涂層,其由9-10重量%的Si、2-3.5重量%的鐵和余量的鋁組成。將這種組成和涂覆的扁鋼產品加熱到大于700℃的加熱溫度,然后放入到壓制模具中,在此熱成型成鋼部件并在此快速地冷卻,以使得該扁鋼產品的鋼基底中產生硬化組織結構。在發貨狀態下,所有的錳硼鋼種是少氫的。其可擴散氫的含量分別在目前的0.1ppm的檢測限以下。MnB鋼由此基本上僅表現出較低的氫致裂紋的傾向。但是在實際中發現,在基于鋁的保護涂層涂覆的錳硼鋼在潮濕的爐氣氛中的熱成型過程中會導致鋼基底中的氫聚集。對此的原因已確定為金屬-水蒸氣反應。當在含有水蒸氣的氣氛條件下在加熱爐中將用于熱成型的、設置有Al涂層的扁鋼產品加熱到較高的溫度時,會導致該反應。在此,位于爐氣氛中的水蒸氣在材料表面上反應形成氫氣和金屬氧化物。所形成的氫氣擴散到鋼材中并在此可以通過其優選在高固有拉應力的區域中的濃集而導致延遲的失效。如果局部達到非常高的氫濃度,這削弱了鋼基材組織結構的晶界上的結合,以使得在使用中由于出現的應力而導致沿著晶界的開裂。為了避免由于在爐中的表面反應而導致的氫滲入,通常使用露點調節劑。在此的目的是,限制在爐氣氛中的水蒸氣供應。這類措施的一個例子為在EP1767286A1中描述的方法。在該方法中,設置有Al或Zn涂層的扁鋼產品為了其熱成型而在干燥的氣氛中(其氫氣含量不高于6體積%、優選不超過1體積%并且其露點保持在最高10℃)加熱到一個溫度,該溫度至少等于Ac3溫度并且最高等于1100℃。這樣加熱的扁鋼產品的鋼基底優選由MnB鋼組成,其具有0.05-0.5重量%的C、0.5-3重量%的Mn和最多0.05重量%的B,而在其為了改善腐蝕保護作用的Al和Zn涂層中可以分別含有0.1-1重量%的Cr、0.5-10重量%的Mg、0.1-1重量%的Ti或1-5重量%的Sn。在此,Al涂層優選是具有3-15重量%Si的AlSi涂層。鐵通常可以以0.05-0.5重量%的含量作為雜質存在于Al涂層中。然而,EP1767286A1中提出的實施例都不涉及除了不可避免的Fe雜質還包含額外的合金成分的AlSi涂層。特別是在其中規定高空氣濕度的區域中,為了提供足夠量的干燥空氣或干燥氮氣所必要的花費會引起顯著的運行開支。技術實現要素:在該現有技術的背景下,本發明的目的在于,提供一種開頭所述的扁鋼產品,其中使熱成型需要的加熱過程中的氫吸收最小化。此外還應說明一種用于制造這類扁鋼產品的方法、由該扁鋼產品熱成型的鋼部件和一種用于制造這類鋼部件的方法。本發明關于扁鋼產品的目的由此得以實現,即,根據權利要求1來形成一類扁鋼產品。用于制造按照本發明的扁鋼產品的方法在權利要求9中說明。解決了上述目的的鋼部件的特征在于,其由按照本發明的扁鋼產品而制成。用于制造這類鋼部件的方法最終可由權利要求11中得出。本發明的有利的設計方案在從屬權利要求中說明并隨后類似于一般發明構思一樣詳細地說明。按照本發明的扁鋼產品包括鋼基底和涂覆在鋼基底上的、基于Al的保護涂層,該鋼基底由具有0.1-3重量%的Mn和0.0005-0.01重量%的B的鋼組成,保護涂層可選地含有總共最大20重量%的其他合金元素。按照本發明,基于Al的保護涂層含有總共0.1-0.5重量%的至少一種的堿土金屬或過渡金屬作為額外的合金成分,其中,在扁鋼產品的熱成型過程中在保護涂層的外側的表面上形成一種堿土金屬或過渡金屬的氧化物。基于Al的保護涂層優選含有總共0.1-0.5重量%的Mg作為額外的合金成分,其中,在扁鋼產品的熱成型之后在至少700℃的加熱溫度條件下在保護涂層的外側的表面上形成氧化鎂(MgO)。按照本發明地以較少的量加入Al涂層的額外的合金成分的特征在于比保護涂層的主要成分Al更高的親氧性。在已經存在這樣少量的堿土金屬或過渡金屬的條件下,在保護涂層上產生薄的氧化層,該氧化層覆蓋了位于其和鋼基底之間的鋁。該薄層阻礙在對于扁鋼產品的熱成型而言必要的加熱過程中鋁與濕氣的反應,該濕氣存在于為了加熱扁鋼產品所使用的爐的氣氛中。這樣有效地防止了涂層的鋁的氧化和與此伴隨的氫的釋放,釋放的氫能擴散到涂層和扁鋼產品的鋼基底中。這令人意外地特別是適用于,當Al基涂層由于加熱而局部變成熔液并撕開其表面時,從而熔液狀的涂層材料與爐氣氛接觸。特別是在較長的退火持續時間的情況下,相對于常規設置有Al涂層的扁鋼產品,在按照本發明的扁鋼產品中表現出在由扁鋼產品熱成型的部件中更低的氫濃度。為了制造按照本發明的扁鋼產品,本發明提出了兩種不同的途徑。按照本發明為了制造按照本發明的扁鋼產品而優選的方法途徑設置為,由此制造按照本發明的扁鋼產品,即,準備以由鋼制成的扁鋼產品的形式的鋼基底并為該鋼基底涂覆一個基于Al的保護涂層,其中,鋼具有0.1-3重量%的Mn和最高0.01重量%的B,特別是0.0005-0.01重量%的B,保護涂層含有0.1-0.5重量%的至少一種選自堿土金屬或過渡金屬組成的組的合金成分以及可選地含有總共最大20重量%的其他合金元素。還為該涂層過程提供熱浸鍍層,其中此處使用熱浸鍍層的熔池,按照本發明預設的額外的合金成分已經加合金到該熔池。替代性地,按照本發明的扁鋼產品也可以以這樣的方法途徑制造,其中,準備以由鋼制成的扁鋼產品的形式的鋼基底,其中,鋼具有0.1-3重量%的Mn和最高0.01重量%、特別是0.0005-0.01重量%的B并且剩余為以已知的方式用于調整其特性的其他合金成分,隨后為該鋼基底涂覆一個基于Al的保護涂層,其中,該保護涂層可選地含有其含量總共最大25重量%的其他合金元素,并且隨后在獲得的保護涂層上涂覆一個層,該層由至少一種選自堿土金屬或過渡金屬組成的組的合金成分而構成,其中,這樣設定所涂覆的層的厚度,以使得額外的合金成分相對于保護涂層和涂覆的層的總重量的含量為0.1-0.5重量%。對此適合的層厚度通常在5-35μm、特別是10-25μm的范圍內。在此,該方法變型的特征在于,其實現了施加具有所述額外的合金成分的這種層厚度,這些額外的合金成分可以以已知的方式有針對性地混合到涂層中,從而調整涂層的特殊性質。在制造按照本發明的扁鋼產品的過程中特別是可以設置為,選自堿土金屬或過渡金屬組成的組的、額外的合金成分通過Mg形成。基于Al的保護涂層特別是可以經濟地通過熱浸鍍層(專業術語中也稱為“火鍍”)而涂覆在鋼基底上。每一種已知的方法都適用于涂覆由按照本發明設置的額外的合金成分組成的層,通過這些方法實現了足夠薄的層沉積在基于Al的涂層上。在此,這些方法包括已知的PVD(物理氣相沉積)或CVD(化學氣相沉積)方法。同樣能夠考慮的是,通過根據滾壓包層的類型輥涂Al箔將附加層施加到鋼基底上。出于本發明的目的而在按照本發明的扁鋼產品的保護涂層中額外設置的堿土金屬首選是鎂,其中替代性或補充性地也可以是鈣、鍶、鈉或鋇。在過渡金屬中可以使用例如Zr和Ti。這些過渡金屬與存在于或滲透到Al基保護涂層中的氫形成金屬類的氫化物,該氫化物的分解持續的時間顯然比將扁鋼產品加熱至加熱溫度的時間更長(為了熱成型而需將扁鋼產品加熱到該加熱溫度),從而該扁鋼產品在相應的熱成型開始時具有所要求的熱成型溫度。因此,為了達到在700-900℃范圍內的熱成型溫度,與之相應地,加熱溫度實際上為至少700℃。為了阻礙扁鋼產品的氫吸收而按照本發明設置的額外的合金元素的總量應在0.1-0.5重量%的范圍內。試驗已經顯示,即使少量的至少一種根據本發明設置的額外的合金成分也足以用于本發明的目的。在此,盡可能少含量的按照本發明的額外的合金成分被證明是有利的,因為額外的合金成分的氧化快速結束,保護涂層的表面相應快速地鈍化并且由于額外的合金成分沒有過量的氫形成。因此,根據本發明用于阻礙扁鋼產品的吸收氫的額外的合金成分的含量優選限制為小于0.5重量%、特別小于0.45重量%或至多0.4重量%。這特別是在這樣的背景下適用,即,在此試驗已經表明,即使在高達0.35重量%的含量下仍實現了對于按照本發明的目的而言足夠的良好效果。當Al涂層作為熱浸涂層而涂覆并且將按照本發明設置的量的額外的合金成分被合金化到熔池中時,除了理想地防止氫吸收之外,該添加還具有這樣的優點,即,使由熔池中這些額外的合金成分的存在而引起的在熔池上產生大量熔渣的風險最小化。增加的熔渣形成可能損害涂層質量。作為阻礙氫吸收特別適宜的額外的合金成分被證實為鎂,其可以很好地合金化到此處談及類型的Al保護涂層中。所加入的Mg的量理想地這樣調整,即,使得保護涂層中存在至少0.1重量%且不超過0.5重量%的Mg,其中,由于上面已經闡述的原因,小于0.5重量%、特別是小于0.45重量%或最多0.4重量%或最多0.35重量%的Mg含量在實踐中被證明特別有利于本發明的目的。在本發明的Al涂層中為了按照本發明的目的鈣可以作為額外的合金成分以0.01-0.5重量%的含量存在,其中,由于已經闡明的原因,最高0.02重量%的低Ca含量可能是有利的。出于相同的原因,鍶也可以以0.005-0.25重量%的含量作為額外的合金元素存在于按照本發明的保護涂層中。在此同樣有利的是,將Sr的含量限制為最大0.15重量%、特別最大0.10重量%。作為用于按照本發明的目的的額外的合金成分,鋇可以以0.005-0.25重量%的含量加入按照本發明的保護涂層中,其中,出于已說明的原因,已經證明0.005-0.05重量%的Ba含量是特別有利的。如果為了按照本發明的目的將鋯和鈦作為額外的合金元素添加到保護涂層中,這可以分別以0.15-0.7重量%的含量進行,其中,由于已經闡明的原因,最高0.5重量%、特別最高0.4重量%或最高0.35重量%的含量是特別有利的。按照本發明的扁鋼產品的保護涂層通常是AlSi涂層,其除了Al之外包含3-15重量%的Si。這種AlSi涂層的典型Si含量在9-12重量%的范圍內,其中,實踐中已知的標準化額定AlSi涂層含有10重量%。除了或代替Si含量,在基于Al的保護涂層中還含有其他合金成分。特別是最大5重量%的Fe,其作為涂層中的雜質或者用于實現涂層在扁鋼產品的鋼基底上的理想的連接而加入。涂層中雜質的含量可以為最大0.5重量%。如上所述地,按照本發明設置的額外的合金成分最晚在扁鋼產品的加熱過程中通過加載在爐氣氛中的水在保護涂層的表面上形成薄氧化層,其阻礙了氫向鋼基底中的滲入并阻礙了進一步釋放氫氣的保護涂層的鋁氧化。在由按照本發明的扁鋼產品熱成型的鋼部件中,該層的厚度僅為最大200nm厚,其中,在實際中,最大100nm的層厚度被證實是足夠的。按照本發明的鋼部件可以由此制成,即,按照本發明的扁鋼產品以上述方式制成,隨后將扁鋼產品加熱至熱成型溫度,其中,該加熱在環境氣氛的條件下或在減少H2O的氣氛條件下進行,并最后將加熱的扁鋼產品熱成型為鋼部件。該熱成型在此可以以已知的方式這樣實施,即,使熱成型溫度這樣高,以使得鋼基底的組織結構是奧氏體的,并且扁鋼產品在成型(兩個階段的過程)之后或在成型過程中、即在成型工具中(一個階段的過程)淬火,從而在扁鋼產品的鋼基底的組織結構中形成硬化組織結構。附圖說明隨后,借助實施例進一步說明本發明。附圖中:圖1以示意圖示出了存在于按照本發明的鋼部件上的保護涂層的層結構;圖2示出了一個圖表,該圖表反映了在熱浸鍍層之后但在熱壓淬火之前按照本發明的扁鋼產品的近表面層的GDOES測量的結果;圖3示出了一個圖表,該圖表再次反映了在熱壓淬火之后按照本發明的扁鋼產品的近表面層的GDOES測量的結果;圖4示出了一個圖表,其中相互比較了設置有常規的AlSi保護涂層和設置有按照本發明的保護涂層的扁鋼產品的經過不同的退火持續時間而出現的氫吸收。具體實施方式針對為了證實本發明的作用而實施的試驗使用了由MnB鋼組成的鋼板組成的四個樣品E1、E2、E3、V,這些樣品的組成在表1中說明。CSiMnPSAlTiCr+MoB0.220.251.160.0140.0020.0380.0230.210.0026剩余鐵和不可避免的雜質,以重量%計。表1在該時間點上不含氫的樣品E1、E2、E3和V分別通過熱浸鍍層而設置有AlSi保護涂層,其組成在表2中說明。樣品SiMgFeE1100.4最高3E2100.3最高3E3100.05最高3V10-最高3剩余鐵和不可避免的雜質,以重量%計。表2保護涂層的最小涂覆重量分別為120g/m2。這樣設置有保護涂層的扁鋼產品樣品E1、E2、E3、V分別在爐中連續經過360s、600s或者800s的退火持續時間GD(參見圖4)在標準化氣氛(其露點為14.0℃)的條件下加熱至900℃。隨后將這些樣品在4-6秒的轉移時間內轉移到熱壓成型工具中并在此熱成型成為一個部件。在熱成型的過程中,各個樣品快速地冷卻,以使得在它們的鋼基底的組織結構中產生硬化組織結構。如在圖1中示意性示出的,在按照本發明的樣品E1、E2、E3中,在退火處理的過程中產生在鄰接保護涂層S的表面O的薄MgO層“M”,其除了MgO之外還含有Al2O3,其中這些樣品位于鋼基底“S”上的、包括FeAl(Si)化合物的保護涂層“C”分別含有Mg作為額外的合金成分。層M使位于其下方的、包括FeAl(Si)化合物的AlSi層“A”相對于潮濕的爐氣氛“P”得到隔離并且這樣防止了層A的鋁的過度氧化。對于樣品E1在圖2中示出了在熱浸鍍層之后和熱壓淬火之前保護涂層的GDOES分析的結果,并且在圖3中示出了熱壓淬火之后保護涂層的GDOES分析結果。還表明,在熱壓淬火之前和之后,在AlSi涂層上存在薄Mg層。圖2和圖3的比較顯示,在壓硬化之前鎂組分基本上均勻地分布在層內(圖2),而相反地在壓硬化之后聚集在近表面的層中(圖3)。以這種方式由樣品E1,E2,E3和V制成的鋼部件中,確定氫含量Hdiff,該氫含量是指在熱處理過程中擴散到鋼基底中的氫。圖4中比較了對于不同時長退火的樣品E1,E2,E3和V的測試結果。已顯示,按照本發明的保護涂層即使當Mg僅以非常小的量存在于保護涂層中時也產生氫吸收的決定性的降低。當前第1頁1 2 3