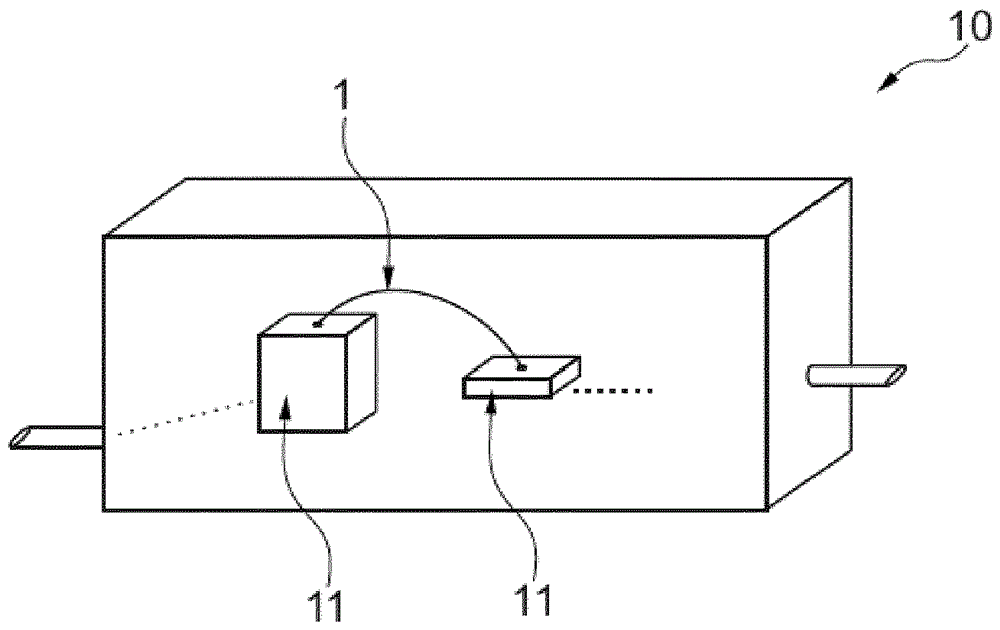
接合線用于制造在半導體器件制造過程中用于電互聯集成電路和印刷電路板的半導體器件。此外,接合線用于電力電子應用以便使晶體管、二極管等與外殼的墊或引腳(pin)電連接。雖然一開始用金來制造接合線,但現在使用不那么昂貴的材料,例如銅。盡管銅線提供非常好的導電性和導熱性,但是銅線的球形接合以及楔形接合具有其挑戰。此外,銅線易受氧化的影響。就線材幾何形狀而言,最常見的是具有圓形橫截面的接合線和具有大致矩形橫截面的接合帶。這兩種類型的線材幾何形狀都具有它們的優點,使其可用于特定的應用。因此,這兩種類型的幾何形狀都具有其市場份額。例如,接合帶對于給定的橫截面積具有更大的接觸面積。但是,帶材的彎曲受限,并且當接合時必須觀察帶材的取向以便在帶材與其所接合的元件之間達到可接受的電接觸。至于接合線,則這些彎曲起來更靈活。但是,接合涉及在接合過程中線材的焊接和更大的形變,這可能造成危害或甚至破壞接合墊以及在下方的與之接合的元件的電結構。對本發明而言,術語接合線包括所有橫截面形狀。通過本發明的方法制得的接合線的尺寸關系到粗接合線。在本發明的接合線含義中,粗線被認為是橫截面積為7500至600000μm2或12000至600000μm2的線材。在具有圓形橫截面的線材的實例中,此類線材可以具有98至510μm或125至510μm的直徑。為了實現足夠的生產量和可靠性,粗接合線的機械性能和接合行為與細接合線相比包括特定的要求。一些近來的發展涉及具有銅芯的接合線。由于高導電性,選擇銅作為芯材料。已經找尋了銅材料的不同摻雜劑以優化接合性能。例如,US7,952,028B2描述了幾種具有大量不同的摻雜劑和濃度的不同的銅基測試線。然而,就接合線本身和接合工藝而言,仍然需要進一步改進接合線技術。因此,本發明的一個目的是提供制造改進的接合線的方法。因此,本發明的另一目的是提供制造接合線的方法,所述接合線具有良好的加工性能,并且其在互連時沒有特殊要求,由此節約了成本。本發明的目的還在于提供制造接合線的方法,所述接合線具有優異的導電性和導熱性。本發明的再一目的是提供制造接合線的方法,所述接合線表現出改善的可靠性。本發明的再一目的是提供制造接合線的方法,所述接合線表現出優異的可接合性。本發明的另一目的是提供制造接合線的方法,所述接合線對于楔形接合顯示出改善的可接合性。本發明的另一目的是提供制造接合線的方法,所述接合線在接合之前顯示出提高的線芯柔軟度。本發明的另一目的是提供制造接合線的方法,所述接合線具有改進的抗腐蝕性和/或抗氧化性。令人驚訝地,已經發現通過本發明的方法制得的線材解決了上述目的中的至少一個。此外,發現包括通過本發明的方法制得的線材的系統和模塊在線材與其它電元件(例如印刷電路板、墊/引腳等)之間的界面處更可靠。本發明涉及制造接合線的方法,所述接合線包括具有表面的芯,其中所述芯包含≥98.0%的銅,并具有7500至600000μm2范圍內的橫截面積和40至95N/mm2范圍內的彈性極限RP0.2(屈服強度),該方法包括以下步驟:(a)提供銅芯前體;(b)拉制該前體直到達到線芯的最終直徑;(c)在650至1000℃范圍內的最低退火溫度下在其整個橫截面上使拉制的線材退火4秒至2小時、優選4秒至1小時的最小退火時間。在一個實施方案中,退火可以作為固定式或靜態退火過程來實施,最小退火時間則可以為4秒至2小時、優選4秒至1小時,而在退火動態進行(即采用移動的線材)的情況下,最小退火時間可以為4至30秒。如果不提供其它特殊限定,組分的所有含量或份額目前均以重量份額的形式給出。特別地,以百分比給出的份額理解為重量%。以ppm(每百萬份的份數)給出的份額理解為重量ppm。通過本發明的方法制得的此類線材在其機械與接合性能方面得到優化。在本發明的一個更優選的實施方案中,線芯或線材的彈性極限RP0.2為≤90N/mm2,最優選≤85N/mm2。彈性極限RP0.2的下限優選≥40N/mm2且最優選≥50N/mm2。這特別導致通過本發明的方法制得的接合線的屈服強度的優選和有利的范圍。通過本發明的方法制得的接合線優選具有在范圍40-95N/mm2、50-95N/mm2、40-90N/mm2或50-90N/mm2中的一個或多個內的彈性極限RP0.2。在非常優選的實施方案中,所述芯或線材的彈性極限RP0.2在65-90N/mm2或65-85N/mm2范圍內。所述線材或所述芯的彈性極限與屈服強度相同。對于彈性極限或屈服強度的定義,參照公知的理解。材料的“屈服強度”在工程和材料科學中定義為材料開始塑性形變時的應力。在塑性形變開始之前,材料將彈性形變,并在移除施加的應力時將返回其初始形狀。目前,通過使用塑性形變的0.2%-偏移屈服點(RP0.2)來定義彈性極限或屈服強度。彈性極限理解為以完成并包裝的產品形式提供的接合線的性質。此外,要理解的是,未對該線材施加過長的儲存時間、環境影響等。接合線的彈性極限以其進料至接合工具前的狀態給出。要指出的是,任何機械應力、彎曲、加熱、長儲存時間等可能影響線材的微觀結構及其彈性極限。例如,在剛剛離開退火爐的線材與包裝狀態下的成品形式的相同線材的彈性極限之間通常存在顯著的差異。要理解的是,可以特別地通過相應地選擇退火程序的參數來調節線材的彈性極限。根據本發明,這不一定意味著如現有技術中常見的那樣使線材退火至最大伸長率值。相反,選擇退火程序和線材的其它參數(銅純度、添加劑等)以實現根據本發明的彈性極限值。線材的芯定義為在表面下方的本體材料(bulkmaterial)的均勻區域。由于任何本體材料從根本上具有在一定程度上性質不同的表面區域,線材的芯的性質被理解為該本體材料區域的性質。本體材料區域的表面在形貌、組成(例如氧含量)或其它特征方面可能不同。在優選的實施方案中,該表面可以是線材的外表面。在進一步的實施方案中,線芯的表面可以作為線芯與疊置在線芯上的涂層之間的界面區域來提供。該線材是特別用于微電子學中的接合的接合線。該線材優選是一件式物體。如果一種組分的份額超出參比材料的所有其它組分,則該組分是“主要組分”。優選地,主要組分占材料總重量的≥50%。所述芯的銅含量為≥98.0%。甚至更優選地,銅含量為≥99%。進一步優選地,線芯由純度≥99.9%的銅(3N-銅)組成。最優選地,線芯由純度≥99.99%的銅(4N-銅)組成。純銅線材通常表現出良好的傳導性和良好的接合性能。在替代實施方案中,可以在線芯中提供少量附加元素。此類元素的實例包括Pd、Ag或B。在本發明通常優選的方面中,退火后線材的伸長率值在最大伸長率值的40至92%范圍內。更優選地,該伸長率值在最大伸長率值的45至85%、最優選50至80%范圍內。在又一優選的情況下,線材在比通過退火實現最大伸長率值時的溫度高≥10℃的溫度下退火。更優選地,該溫度為比最大伸長率的溫度高≥50℃,且最優選地,該溫度比最大伸長率的溫度高≥80℃。通常,該溫度比最大伸長率的溫度高≤150℃。因此,線材可以在比最大伸長率的溫度高10至150℃、或50至150℃、或80至150℃的溫度下退火。最大伸長率值定義如下:在銅基接合線的一般情況下,可以通過最終退火步驟來調節線材的伸長率。“最終”在這方面是指此后不再設立對線材的形貌具有重大影響的生產步驟。當選擇退火參數時,通常選擇一組參數。在使線材退火的簡單情況下,在給定長度的爐中調節恒定溫度,其中線材以恒定速度通過該爐。這使線材的每一點暴露于該溫度下持續給定的時間,這一溫度和這一退火時間是該退火程序的兩個相關參數。在其它情況下,可以采用爐的特定溫度分布曲線,由此將其它參數添加到該系統中。在任何情況下,可以選擇其中一個參數作為變量。隨后,取決于該變量的所得到的線材伸長率值產生通常具有局部最大值的圖。這在本發明的含義中定義為該線材的最大伸長率值。在變量為退火溫度的情況下,這樣的圖通常被稱為“退火曲線”。在現有技術中,相對于變量參數,通常使任何線材退火至這樣的最大伸長率值,因為局部最大值的存在提供了特別穩定的制造條件。對于本發明,令人驚訝地發現,退火至低于最大伸長率值的不同值可以獲得有益的線材性質,因為可能以積極的方式影響線材形貌。如果選擇退火溫度作為變量參數,并將退火時間設定為恒定值,在將退火溫度選擇為高于最大伸長率的退火溫度的值的情況下,這是特別有益的。特別地,該制造原理可用于調節線材的平均晶粒尺寸,例如向更大的晶粒尺寸調節。通過這種調節,可以以積極的方式影響其它性質,如線材柔軟度、楔形接合行為等。為了提供良好的生產量和有效的退火,可以在退火步驟(c)的過程中將所述芯在其整個橫截面上加熱至≥650℃的最低退火溫度。甚至更優選地,該溫度為≥680℃。在退火步驟(c)的過程中將所述芯在其整個橫截面上加熱至≤1000℃的退火溫度。因此,在退火步驟(c)的過程中將所述芯在其整個橫截面上加熱至650-1000℃或680-1000℃范圍內的溫度。在一個特別優選的實施方案中,通過分股退火來實施退火,分股退火能夠以高再現性快速生產線材。分股退火意味著在線材移動穿過退火爐的同時動態實施退火,并在離開爐后纏繞到線軸(reel)上。在一個優選實施方案中,線材以包裝形式提供,并且該方法在步驟(c)之后進一步包括步驟(d)輸送和包裝所述線材,其中該線材以曲率半徑Rc彎曲,其中Rc等于0.25?(1/E-1)?Dr,或簡化為0.25?Dr/E,其中Dr定義為在曲率半徑方向上測得的線材的直徑,其中E是由彎曲造成的線材的外部細絲(outerfilament)的相對伸長率;并且其中E≤0.006。在一個更優選的實施方案中,E≤0.005或≤0.004,最優選E≤0.003。通常,E≥0.0002。這樣的程序確保不會因最終的輸送、纏繞和包裝過程的影響使線材的優化微觀結構和由此其機械性能劣化。通過這些措施,避免了通過退火步驟(c)調節線材的微觀結構之后該線材經受不利的機械應力。特別地,退火后該線材的強彎曲或其它強形變將會不利地影響其晶體的尺寸與分布。這些包括其中僅線材外部受到影響,但是該線材整體的機械性能仍在本發明的范圍內的影響。線材的細絲定義為平行于線材的幾何中心線延伸并與之保持恒定距離的具有無限小直徑的理論細絲。因此上述含義中的外部細絲是在具有最大曲率半徑的位置處沿著線芯表面延伸的細絲。線材彎曲的限制尤其涉及其中在線軸上提供線材的包裝形式。取決于線材直徑,需要根據上面給出的參數提供包裝線軸的最小直徑。此外,應當注意,當處理線材時不應超過所述最小彎曲半徑。此類處理包括制造線材以及在接合工具中進料和輸送線材的程序。在進一步優選的實施方案中,通過本發明的方法制得的線材已經在退火步驟(c)之后直接纏繞到包裝線軸上。這意味著線材在纏繞到最終的包裝線軸上之前并未纏繞到中間線軸上。已表明,纏繞線材的任何程序會對其微觀結構和機械性能產生影響,因為任何這樣的程序均會將線材置于機械應力下。即使使用具有大直徑的中間線軸,在一定程度上也會是這樣的情況。由于包裝線軸的直徑限定了上面解釋的含義中線材的最小曲率半徑,本發明還涉及提供如根據本發明所制造并包裝在線軸(spool)上的線材,其中該包裝線軸滿足上面給出的曲率半徑的參數。對于通過本發明的方法制得的具有圓形橫截面的線材,已經觀察到微觀結構的不尋常的性質。這些結構有可能與良好的接合性能相關。因此,對于優選的線材,該線材的第二區域(R2)的平均晶粒尺寸與該線材的第一區域(R1)的平均晶粒尺寸之比為0.05至0.8、優選0.05至0.7和更優選0.1至0.6。線材的第一區域(R1)由距線材的幾何中心線具有≤線材最小直徑的10%的距離的所有點來限定,并且其中線材的第二區域(R2)由距芯的表面具有≤線材最小直徑的10%的距離的所有點來限定。線材的最小直徑定義為垂直且穿過其幾何中心線跨該線材的最短可能直徑。采用電子背散射衍射測定法(EBSD)實施平均晶粒尺寸的測量。將線材片段包埋在樹脂中并研磨在其中心線方向上穿過線材的縱向截面。通過離子銑削(ion-milling)拋光并進一步預備該線材的截面區域。對線材的微觀組織進行數次測量。通過這些測量來測定線材的晶粒尺寸和分布。已令人驚訝地發現,在靠近線材表面的邊界區域中的平均晶粒尺寸明顯小于在線材中心線附近的中心區域中的平均晶粒尺寸。平均晶粒尺寸看起來從線材的中心開始在徑向向外的方向上快速減小。此前已知的晶粒尺寸分布顯示平均晶粒尺寸的均勻分布或平均晶粒尺寸隨著距線材中心的距離的增加而增大。在該方法的可能的進一步發展中,在拉制前體的步驟(b)之前或之后,提供用涂層材料涂覆銅芯的步驟(e)。涂覆方法的實例是電鍍、物理氣相沉積和化學氣相沉積。在本發明的此類進一步發展中,使涂層疊置在芯的表面上。要理解的是,這樣的涂層是通過本發明的方法制得的線材的可能但非必要的特征。為了盡量減小此類涂層的材料對接合過程的影響,涂層的厚度≤0.5μm,更優選≤0.2μm。通常,涂層的厚度≥20nm。在提供涂層的情況下,該層包含貴金屬、Ti、Ni或Cr中的一種作為主要組分。特別優選的用于涂覆目的的貴金屬的實例是Pd、Au、Pt和Ag。術語“疊置”在本發明的含義中用于描述第一項(例如銅芯)相對于第二項(例如涂層)的相對位置。可能地,其它項(如中間層)可布置在第一項與第二項之間。優選地,第二項至少部分疊置在第一項上,例如相對于第一項的總表面的至少30%、50%、70%或90%。第二項最優選完全疊置在第一項上。術語“中間層”在本發明的上下文中是在銅芯與涂層之間的線材區域。在該區域中,如在芯中的材料以及如在涂層中的材料組合存在。在本發明的可能的實施方案中,作為中間層提供涂層,其中至少一個外層疊置在中間層上。在這樣的情況下,外層優選包含至少一種貴金屬作為主要組分。此類貴金屬可以特別是Au或Pd。在最優選的組合中,中間層包含Pd且外層包含Au作為各自的主要組分。在提供外層的情況下,中間層具有5nm至100nm范圍內的優選厚度。在一個優選的實施方案中,線材具有圓形橫截面形狀,其中穿過橫截面積的最短路徑與最長路徑之間的比率為0.8至1.0。這樣的線材被稱為具有圓形橫截面的線材。在另一優選的實施方案中,線材的形狀如條帶,其中穿過橫截面積的最短路徑與最長路徑之間的比率為0.02至0.5。根據需要,本發明的方法可以進一步包括以下步驟:(f)在步驟(c)之前將線材軋制成條帶形狀。這確保將圓形線材成形為條帶不會影響最終線材的微觀結構。附圖描述在附圖中例示了本發明的主題。但是,附圖并非意在以任何方式限制本發明或權利要求的范圍。在圖1中,描繪了線材1。圖2示出了線材1的橫截面視圖。在該橫截面視圖中,銅芯2在橫截面視圖的中間。銅芯2被涂層3包圍。在銅線2的界限上,定位銅芯的表面15。在穿過線材1的中心23的線條L上,銅芯2的直徑顯示為線條L與表面15的交點之間的端至端距離。線材1的直徑是穿過中心23的線條L與線材1的外部界限的交點之間的端至端距離。此外,描繪出了涂層3的厚度。在圖2中夸大了涂層3的厚度。如果提供涂層3的話,其典型厚度與芯直徑相比非常小,例如≤芯直徑的1%。要理解的是,線材1的涂層3是任選的。對于最優選的實施方案而言,在線芯上不提供涂層。圖3示出了制造根據本發明的線材的方法。圖4描繪了電器件10形式的模塊,其包括兩個元件11和線材1。線材1電連接兩個元件11。虛線表示另外的連接或電路,其將元件11與包圍元件11的包裝器件(packagingdevice)的外部接線連接。元件11可包括接合墊、引線指(leadfingers)、集成電路、LED等。圖5示出了由4N-銅芯組成的不具有涂層的粗線材的退火曲線。標記了根據現有技術的一個退火窗口和根據本發明的實例的一個退火窗口。圖6示出了在穿過根據本發明制得的線材的縱向截面上的EBSD測量。該線材具有直徑為300μm的圓形橫截面。測試方法所有測試和測量在T=20℃和50%的相對濕度下進行。當測量晶粒的平均晶粒尺寸時,在本文中采用電子背散射衍射測定法(EBSD)。盡管EBSD是可以測定不同晶粒的取向的方法,但是對于本發明的目的而言,該方法僅用于測量晶粒直徑。通過標準程序來進行楔形接合工藝的測量。接合線的工藝參數窗口的定義在本領域中是已知的,并廣泛用于比較不同的線材。通過下文中描述的本發明的方法制得的線材的所有實施方案已經顯示出優異的接合性能。實施例通過實施例進一步例示本發明。這些實施例用于示例性闡述本發明,而非意在以任何方式限制本發明或權利要求的范圍。實施例1使一定量的純度≥99.99%的銅材料(“4N-銅”)在坩堝中熔融。未向熔體中加入其它物質。然后由該熔體鑄造線芯前體。使用電感耦合等離子體(ICP)儀器(PerkinElmerICP-OES7100DV)來控制Cu線材的化學組成。將Cu線材溶解在濃硝酸中,并將該溶液用于ICP分析。由設備制造商根據對于體相Cu適用的公知技術建立用于測試高純Cu線材的方法學。線芯前體隨后在數個拉制步驟中進行拉制以形成具有規定直徑的線芯2。該線材具有幾乎圓形的橫截面,其中最長和最短直徑的比率(ration)為0.8至1.0。為了證實對于不同直徑的本發明的有益效果,制造一系列選擇的具有不同直徑的線材。下表1顯示了在制造過程的不同步驟處對于不同線材直徑測得的數據的列表:編號直徑[μm]TS1[N/mm2]EL1[%]YS1[N/mm2]TS2[N/mm2]EL2[%]YS2[N/mm2]1500215.629.0670.8218.833.8891.22400224.226.4175.0226.628.990.73300225.321.265.2225.523.0585.64125207.520.5868.0205.819.0490.2(表1:通過本發明的方法制得的不同線材的數據)對數據的解釋:TS1:緊接在退火爐后的線材的抗張強度;EL1:緊接在退火爐后的線材的伸長率;YS1:緊接在退火爐后的線材的屈服強度;TS2:在纏繞到包裝線軸上之后的線材的抗張強度;EL2:在纏繞到包裝線軸上之后的線材的伸長率;YS2:在纏繞到包裝線軸上之后的線材的屈服強度。要注意的是,在本發明的含義中線材的屈服強度是上面數據中的“YS2”,因為這指的是成品。用輸送和纏繞過程中對線材的附加機械影響來解釋YS1與YS2的結果之間的顯著差異。在退火程序之后該線材處理的優化可以減小本文中所見的屈服強度的增加。在本發明的制造線材的程序中,線材在離開退火爐之后首先纏繞到中間線軸上。隨后,該線材再次纏繞到包裝線軸上。這進一步增加了值YS1與YS2之間的差異。在制造程序的優選變體中,線材直接纏繞到包裝線軸上。為了盡量減小由纏繞造成的機械應力,所用線軸以及所有導向輥均具有最小直徑以保持線材產生的彎曲半徑高于最小值。優選的最小彎曲半徑或曲率半徑隨線材直徑而增加。曲率半徑Rc等于0.25?(1/E-1)?Dr,其中:-Dr定義為在曲率半徑方向上測得的線材的直徑;-E是由彎曲造成的線材的外部細絲的相對伸長率;并且-E≤0.006。在本實施例中,E經選擇小至0.002。這意味著例如對于300μm的線材(樣品編號1),線軸的直徑經選擇為10cm(=5cm曲率半徑)。這涉及參數E=0.0015:5cm=0.25*0.03cm/0.0015在制造布置中,具有最小彎曲半徑的項(線軸、導向輥等)主要限定了退火后線材的機械應力。因此,優選的是所有線軸和輥具有相同的半徑,并盡可能減少它們的數量。還應注意的是,線材的抗張強度TS1、TS2在很大程度上不受本文中描述的措施的影響。無論是根據本發明的特定退火還是由退火后的包裝程序造成的機械應力均沒有以顯著的方式改變該線材的性質。下表2顯示了用于表1的線材的分股退火的退火參數的更多細節:編號直徑[μm]爐溫[℃]線材速度[m/min]爐長度[m]150080030.82240080050.823300800100.824125700100.82(表2:表1的線材的退火參數)。由表2變得清楚的是,采用分股退火,通過改變線材輸送速度改變了退火時間。除了退火時間之外,退火溫度也發生改變。下表3顯示了不涉及本發明的對比例。在這些實施例中,以不同的退火參數使相同的線材基材退火。在各種情況下,改變退火參數直到達到最大伸長率值EL1max(其緊接在退火爐后測得)。對于這些線材,給出了緊接在退火爐后測得的值TS1和YS1(參見上面對表1的解釋)。編號直徑[μm]爐溫[℃]線材速度[m/min]爐長度[m]TS1[N/mm2]EL1max[%]YS1[N/mm2]YS2[N/mm2]150080050.82219.737.6181.0101.52400800100.82228.636.1190.9110.53300600100.82226.632.9395.1112.34125600100.82207.928.693.7108.2(表3:對比例,其中以最大伸長率值為目標進行退火)。成品的屈服強度值YS2顯著高于通過本發明的方法制得的線材。對于對比線材而言,成品的屈服強度值均不低于100N/mm2。關于通過本發明的方法制得的線材的退火程序,參照圖5。該圖顯示了300μm線材的退火曲線。在該曲線中,在不同的溫度下進行退火,而退火時間保持恒定。測量緊接在退火爐后的伸長率值EL1并相對于退火溫度來顯示。在本發明的分股退火的方法中,由線材速度和爐長度的值計算退火時間。要理解的是,通過本發明的方法制得的線材不限于分股退火。如在通常情況下那樣,退火曲線表現出局部最大值,其位于大約600℃處。要理解的是,最大伸長率值的退火溫度還取決于退火時間。在圖5中顯示出兩個退火窗口A和B。第一窗口A在局部最大值周圍對稱布置,并且指的是根據現有技術的接合線的退火。傳統上使用在局部最大值處或其附近的這種類型的退火,因為其提供良好的工藝穩定性和再現性。以來自第二退火窗口B的參數使通過本發明的方法制得的線材退火。該窗口布置在退火曲線的高端尾部附近。當伸長率降低至≤最大伸長率值EL1max的92%時,限定窗口B的溫度下邊界。窗口B的溫度上邊界僅由要獲得的屈服強度的下限來限定。要指出的是,取決于退火程序后線材經受的機械應力(其有助于提高屈服強度),該溫度上邊界可能不同。在其它試驗中,測量和評估了通過本發明的方法制得的線材的晶體微觀結構。圖6顯示了上述樣品編號3線材(300μm直徑)的晶粒結構。將線材樣品沿其中心線切片。顯示出兩個不同的區域R1和R2,其中第一區域R1布置在中心線周圍。第二區域R2布置在線材表面下方。各區域的徑向寬度為線材直徑的10%。由所顯示的晶粒結構顯而易見的是,中心區域R1中的平均晶粒明顯大于近表面區域R2中的平均晶粒。測量結果的評估在中心區域R1中給出了25μm的平均晶粒尺寸。在表面區域R2中的平均晶粒尺寸為11μm。不同區域中的這些平均晶粒尺寸之比為11μm/25μm=0.44。接合測試已經表明,通過本發明的方法制得的線材顯示了優異的接合性能。此外,該線材在接合工具中的處理和接合工藝穩定性因該線材的高柔軟度而得以提高。實施例2作為本發明的第二實施例,制造條帶形式的接合線。根據上述第一實施例進行所有制造步驟,除了在退火步驟之前使線芯扁平化的附加步驟。通過軋制該線材來實現線材的扁平化。所得帶材的最短直徑與其最長直徑之比為0.1。其最短直徑為100μm,其最長直徑為1000μm,橫截面積大致為100,000μm2。要注意的是,包裝產品的退火程序和調節的YS2值對于帶材與對于上述圓形線材而言相同。考慮到要遵循的最小曲率半徑,帶材繞其較短的直徑有規律地纏繞,因此該直徑是選擇線軸和導向輥的直徑的相關參數。當前第1頁1 2 3