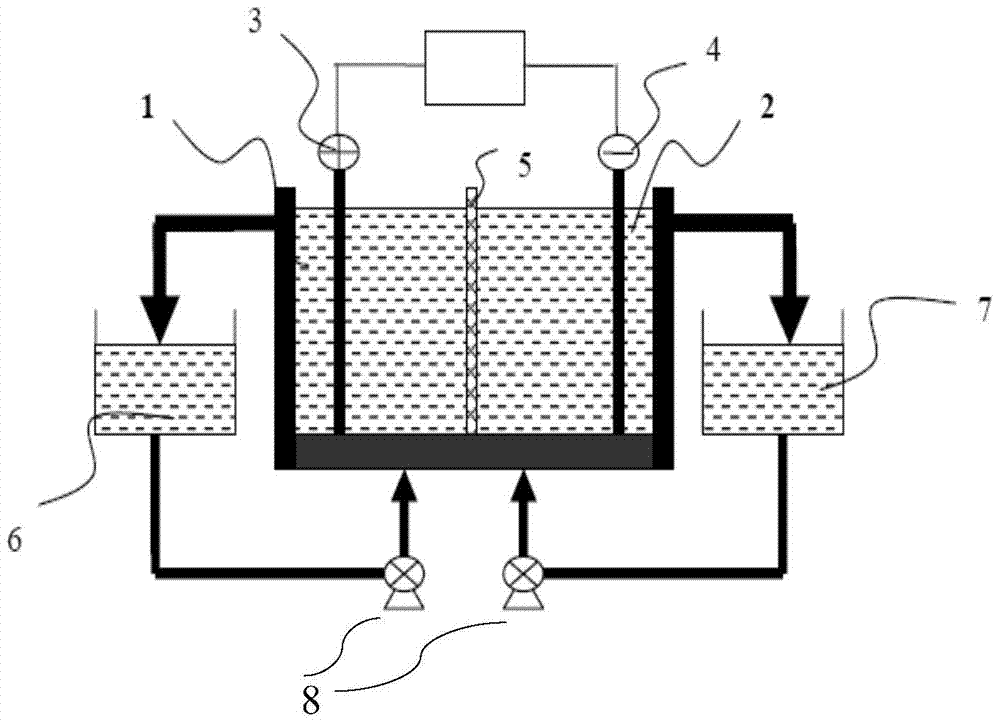
本發明涉及含鎳三氯化鐵蝕刻廢液的處理方法,具體涉及一種電解再生含鎳三氯化鐵蝕刻廢液并聯產鐵黃的方法。
背景技術:三氯化鐵溶液由于具有一定的氧化性和酸性,對鐵、鎳具有很好的腐蝕作用,因而被大量的應用于金屬蝕刻,如精細電路圖形的蝕刻、微電子封裝中在三氯化鐵蝕刻鎳不銹鋼蔭罩過程。蝕刻過程中,FeCl3被鎳不銹鋼還原成FeC12,同時少量金屬鎳會被氧化以Ni2+形式進入蝕刻液。蝕刻過程中,隨著蝕刻液中FeC13濃度的降低和Ni2+濃度的升高,蝕刻的效率會有所下降。此外,蝕刻液中Ni2+濃度的升高還容易導致產品蝕刻表面過于粗糙的傾向。根據蝕刻工藝質量要求,三氯化鐵蝕刻液的組分含量應達到以下要求:三氯化鐵含量≥35%、氯化亞鐵含量≤0.4%。因此大量用過的FeCl3蝕刻液由于不能滿足蝕刻工藝要求而從蝕刻系統中以廢液形式排出。廢液成份為三氯化鐵28~34%,氯化亞鐵2.5~8%,還有氯化鎳2.5~6%,此廢液作為危險廢棄物若不經處理而排放,不僅會造成環境的污染,而且造成資源的極大浪費,故含鎳三氯化鐵蝕刻廢液的如何高效再生利用是目前國內外普遍關注的問題。目前大多數生產廠家對含鎳三氯化鐵蝕刻廢液采用純鐵還原法進行處理,如公告號為JP5140667A的日本專利文獻中提出的鐵粉置換反應除鎳的方法,該方法用鐵粉與三氯化鐵廢液混合,將三氯化鐵還原成二氯化鐵,過量的鐵粉又置換溶液中的二價鎳離子使金屬鎳沉淀下來;除鎳后的二氯化鐵用氯氣氯化成三氯化鐵,重新用作蝕刻液。該方法中加入的鐵粉量必須是過量的,因此,回收鎳的品位相當低,沒有進一步的使用價值,而且大量投入純鐵增加了生產成本。公告號為CN1540036A的中國專利文獻公開了一種先濃縮結晶,再對母液電解分離回收鎳的方法。在該方法中,先將含鎳的三氯化鐵廢液濃縮結晶,結晶出含鎳較低的三氯化鐵晶體,然后對結晶后的三氯化鐵母液進行電解,在陰極有鐵鎳合金析出,在陽極有氯氣析出。該方法鎳的回收率較高,但由于電解過程中有氯氣析出,對設備腐蝕比較大,操作成本較高。公告號為JP10046370的日本專利文獻公開了濃縮結晶分離鎳的方法。在該方法中,含有鎳的三氯化鐵蝕刻廢液先濃縮結晶,分離出含鎳量較低的三氯化鐵晶體,其母液經反復結晶,鎳離子被富集,達到分離鎳的目的。但是該方法步驟多,浪費大,效率很低。公開號為CN1386906的中國專利文獻公開了含鎳三氯化鐵蝕刻廢液的除鎳方法,該方法包括:(1)在蝕刻廢液中加入鐵粉或鱗狀鐵皮,進行還原反應,(2)加熱反應混合物至55℃-95℃,薦往其中加入鐵粉和硫磺粉,進行二價鎳的沉淀反應,(3)往55℃-95℃的反應混合物中,或者繼續加入鐵粉和硫磺粉,或者加入鐵粉和砷化合物,或者加入鐵粉和銻化合物,進一步進行二價鎳的沉淀反應,然后過濾。該方法需要在含鎳三氯化鐵刻蝕廢液中添加大量高純度的鐵和含硫或含砷、含銻的化工原料,大量純鐵的投入增加了生產成本,處理過程中三氯化鐵轉化成二氯化鐵補氯后三氯化鐵總量增加近三分之一給精確控制刻蝕液中三氯化鐵的含量增加了麻煩;另一方面含硫、含砷、含銻化工原料的使用既容易造成環境污染有不可避免的給三氯化鐵刻蝕液引入雜質增加了三氯化鐵刻蝕液再生利用后品質控制的難度。
技術實現要素:本發明提供了一種電解再生含鎳三氯化鐵蝕刻廢液并聯產鐵黃的方法,該方法操作簡單,成本低,回收利用率高。一種電解再生含鎳三氯化鐵蝕刻廢液并聯產鐵黃的方法,包括以下步驟:(1)采用陰離子膜電解法對含鎳三氯化鐵蝕刻廢液進行電解,分別獲得陽極液和陰極液,所述陽極液為再生三氯化鐵蝕刻液;(2)向所述陰極液中加入堿液和分散劑,并通入空氣進行反應,反應完成后離心,分別獲得納米鐵黃粉體和鐵黃過濾液;(3)向所述鐵黃過濾液中加入Fe2+和Ni2+的沉淀劑進行反應,反應完成后過濾,分別獲得鐵鎳共沉淀物和濾液,濾液經活性炭吸附后排放。陰離子交換膜能讓蝕刻廢液中的氯離子選擇性透過,且隨著電解時間的進行,Fe3+在陽極富集,Fe2+在陰極富集,從而使陽極液中的Fe3+濃度可以達到3.5108mol/L,Fe2+濃度小于0.0023mol/L,符合蝕刻工藝中對三氯化鐵蝕刻液的質量要求,可以直接回收利用;同時采用堿法利用富含Fe2+的陰極液制備納米鐵黃粉體,進一步回收利用鐵資源;蝕刻廢液中的Ni2+主要富集在鐵黃過濾液,經沉淀劑沉淀后的濾液經簡單吸附后即可按電鍍行業標準達標排放。整個過程操作簡單,成本低廉,對蝕刻廢液的回收利用率高,且無三廢排放。具體地,所述方法包括以下步驟:(1)采用陰離子膜電解法對含鎳三氯化鐵蝕刻廢液進行電解,分別獲得陽極液和陰極液,所述陽極液為再生三氯化鐵蝕刻液;陰離子膜電解法采用的電解槽,包括槽體,陰離子交換膜將槽體內空間分隔為陽極室和陰極室,陽極室與陽極貯液槽相通,陰極室與陰極貯液槽相通。電解過程中,陽極一側的含鎳三氯化鐵蝕刻廢液在陽極室與陽極貯液槽之間循環流動,陰極一側的含鎳三氯化鐵蝕刻廢液在陰極室與陰極貯液槽之間循環流動,且陰極室內的Cl—選擇性地透過陰離子交換膜進入陽極室內。電解過程中主要發生的反應如下:陽極反應:2Cl—→Cl2↑+2e—(Ⅰ);Fe2+→Fe3++e—(Ⅱ);陰極反應:Fe3++e—→Fe2+(Ⅲ)。作為優選,所述陰離子交換膜為均相陰膜,均相陰膜具有更好的電化學活性。作為優選,所述電解采用的電壓為6.0~7.0V。采用此電壓時,能夠使得陰陽兩極發生所需要的電極反應,同時減少其他的副反應。作為進一步優選,所述電解采用的電壓為6.0V。在此電壓下,電流效率η最高,達到95.82%。作為優選,電解過程中陽極電極的電流密度為90~150A/m2。此時陽極室內Fe2+氧化為Fe3+的效率最高。作為優選,所述陽極電極為金屬鈦電極。金屬鈦電極不會參與陽極反應,且電解效率較高。電解完成后,陽極液即為再生三氯化鐵蝕刻液,再生三氯化鐵蝕刻液的Fe3+濃度可以達到3.5108mol/L,Fe2+濃度小于0.0023mol/L。(2)向所述陰極液中加入堿液和分散劑,并通入空氣進行反應,反應完成后離心,分別獲得納米鐵黃粉體和鐵黃過濾液;分散劑的加入是為了使陰極液中的Fe2+離子分散開來,以便Fe2+能分別地與加入的OH—進行反應,使生成的鐵黃粉體不形成團聚。作為優選,所述分散劑為十六烷基三甲基溴化銨,十六烷基三甲基溴化銨的加入量為陰極液的1~2%,更優選的加入量為陰極液的1%。本步驟中發生的反應主要是:Fe2++2OH-→Fe(OH)2(Ⅳ);4Fe(OH)2+O2→4FeOOH+2H2O(Ⅴ)。堿法制備鐵黃的過程中,反應所需的溫度、pH值以及空氣流速是鐵黃形態結構的主要控制因素。本發明中,步驟(2)所述反應在室溫、pH2~4條件下進行,反應時間不少于40h。溫度太低會使反應速率變慢,而溫度過高會使生成的納米鐵黃粉體晶格轉化為Fe3O4,當溫度大于80℃時,反應產物為純相Fe3O4黑色固體。當pH為2~4時,Fe(OH)2逐漸轉化為FeOOH沉淀下來,當pH大于6.5時,Ni2+開始以共沉淀或進入晶格的形式沉淀下來,導致納米鐵黃粉體純度不高。作為進一步優選,步驟(2)所述反應在25℃、pH4.0條件下進行。作為優選,空氣的通入量為6~7L/(L·min);更優選為6.45L/(L·min)(此時的氧化速率最快)。通入空氣的作用是使生成的Fe(OH)2不斷氧化為FeOOH并釋放出H+,因此需要在反應過程中不斷加堿使反應液pH保持在2~4之間,更優選為保持反應液pH至4。反應完成后,進行離心分離,分別獲得鐵黃粗品和濾液;鐵黃粗品經水洗3次后、再進行醇洗3次獲得納米鐵黃粉體。得到的納米鐵黃粉體可以進一步用十二烷基苯磺酸鈉包覆,進行表面改性,以降低納米鐵黃粉體的吸油量。(3)向所述鐵黃過濾液中加入Fe2+和Ni2+的沉淀劑進行反應,反應完成后過濾,分別獲得鐵鎳共沉淀物和濾液,濾液經活性炭吸附后排放。作為優選,所述沉淀劑為硫化鈉。硫化鈉可以與Fe2+和Ni2+反應,使Fe2+和Ni2+以硫化物的形式沉淀。作為優選,加入過量的硫化鹽以使Fe2+、Ni2+完全沉淀。實驗發現,當硫化鈉含量為10%,過量系數為3.57時,鐵黃過濾液中Fe2+、Ni2+基本沉淀完全。作為優選,先調節所述鐵黃過濾液的pH至6~6.5,再加入沉淀劑反應。未調節pH之前,所述鐵黃過濾液的pH約為3.5,呈酸性,此時投加硫化鹽會產生有毒的硫化氫氣體。作為優選,所述沉淀反應也在室溫條件下進行。溫度太低反應速率變慢,溫度升高投加硫化鈉會產生有毒的硫化氫氣體,且增加Fe2+、Ni2+的去除成本。反應時間一般為30min,此時鐵黃過濾液中的Ni2+基本沉淀完全。反應完成后過濾,一方面得到黑色的硫化亞鐵和硫化鎳共沉淀物,另一方面得到pH為10~12的濾液,濾液經活性炭吸附后可按電鍍行業標準達標排放。與現有技術相比,本發明的有益效果為:本發明首先采用陰離子膜電解法對含鎳三氯化鐵蝕刻廢液進行電解,獲得的陽極液即為再生三氯化鐵蝕刻液,Fe3+濃度可以達到3.5108mol/L,Fe2+濃度小于0.0023mol/L,符合蝕刻工藝中對三氯化鐵蝕刻液的質量要求,可以直接回收利用;再通過堿法利用富含Fe2+的陰極液制備納米鐵黃粉體,進一步回收利用鐵資源;蝕刻廢液中的Ni2+主要富集在鐵黃過濾液,經沉淀劑沉淀后的濾液經簡單吸附后即可按電鍍行業標準達標排放。整個過程操作簡單,成本低廉,對蝕刻廢液的回收利用率高,且無三廢排放。附圖說明圖1為本發明電解再生含鎳三氯化鐵蝕刻廢液并聯產鐵黃的工藝流程圖;圖2為陰離子膜電解法所采用的電解槽的結構示意圖。具體實施方式下面結合附圖和具體實施方式對本發明作進一步詳細說明。實施例1本實施例一種電解再生含鎳三氯化鐵蝕刻廢液并聯產鐵黃的方法(其工藝流程如圖1所示),包括以下步驟:(1)采用陰離子膜電解法對含鎳三氯化鐵蝕刻廢液進行電解:本實施例含鎳三氯化鐵蝕刻廢液的成分為:氯化鐵32%、氯化亞鐵4.6%、氯化鎳2.9%、游離酸2.1%,比重1474g/L。陰離子膜電解法所采用的電解槽如圖2所示。由圖2可見,該電解槽包括采用聚氯乙烯塑料板制成的長方形槽體,長方形槽體內設有陰離子交換膜5(材質為全氟磺酸膜),陰離子交換膜5將長方形槽體分隔為陽極室1和陰極室2,陽極室1和陰極室2內分別插設有陽極電極3和陰極電極4,本實施例中,陽極電極3和陰極電極4均為金屬鈦電極。長方形槽體外部設有分別與陽極室1和陰極室2連通的陽極貯液槽6和陰極貯液槽7,陽極室1和陽極注液槽6之間,以及陰極室2和陰極貯液槽7之間設有耐腐蝕泵8,耐腐蝕泵8的作用主要是將陽極注液槽6和陰極貯液槽7內的蝕刻廢液分別打入陽極室1和陰極室2。電解前,分別向陽極貯液槽6和陰極貯液槽7內注入含鎳三氯化鐵蝕刻廢液,并通過耐腐蝕泵8分別輸入陽極室1和陰極室2內。電解過程中,通過耐腐蝕泵8使陽極室1中的電解液在陽極室1和陽極貯液槽6之間循環流動,使陰極室2中的電解液在陰極室2和陰極貯液槽6之間循環流動;電解槽電壓為6.0V,陽極電極3和陰極電極4的電流密度均為102A/m2,電解1.5h。(2)制備再生三氯化鐵蝕刻液:電解結束后,將陽極液導入蝕刻液調整槽(圖中省略),檢測溶液中的Fe3+、Fe2+和游離酸的濃度,通過計算向每升陽極液中加入濃度為20%、體積為20ml的氫氧化鈉溶液,調整蝕刻液酸度,得到再生三氯化鐵蝕刻液。再生三氯化鐵蝕刻液滿足:游離酸≤0.5%,氯化鐵>35%,氯化亞鐵<0.2%,比重約1400g/L左右的三氯化鐵蝕刻液要求。(3)制備納米鐵黃粉體:電解結束后,將陰極液導入反應器(圖中省略)中,向每升組成為Fe3+:Fe2+=1:5(物質量)的陰極液中加入濃度為0.4g/L的十六烷基三甲基溴化銨200ml、陰極液體積170-180倍的氫氧化鈉溶液(0.4mol/L),在25℃下進行氧化反應。反應過程中,不斷調節反應液的pH為4.0,通入空氣流量為6.45L/(L·min)以加速氧化,氧化反應約40h后,通過離心分離,分別獲得鐵黃粗品和濾液;鐵黃粗品經水洗3次后、再經醇洗3次后獲得納米鐵黃粉體。納米鐵黃粉體(FeOOH)的產率達到88.9%,Fe2O3的含量為80.8%,n為2.11。在30℃、pH3.5條件下,采用十二烷基苯磺酸鈉對納米鐵黃粉體進行包覆,其中十二烷基苯磺酸鈉為納米鐵黃粉體質量的7%,包覆時間為30min。此時納米鐵黃粉體的吸油量從包覆前的65.1g/100g降至包覆后的34.7g/100g。(4)分離鎳:在室溫下,向每500mL鐵黃過濾液中加入10ml碳酸鈉(0.2mol/L),調節鐵黃過濾液pH為6~6.5;然后投加10%硫化鈉,過量系數3.57,反應30min后自然過濾,此時硫化亞鐵和硫化鎳共沉淀物為黑色,共沉淀物為1.6752g。得到的分離鎳濾液每500ml,用2g/L活性炭吸附30min后即可按GB21900-2008電鍍污染物排放標準達標排放。實施例2本實施例一種電解再生含鎳三氯化鐵蝕刻廢液并聯產鐵黃的方法(其工藝流程如圖1所示),包括以下步驟:(1)采用陰離子膜電解法對含鎳三氯化鐵蝕刻廢液進行電解:采用的含鎳三氯化鐵蝕刻廢液、電解槽與實施例1相同。但保持電解槽陽極電極3和陰極電極4的電流密度均為90A/m2,恒電流電解3.5h。(2)制備再生三氯化鐵蝕刻液:同實施例1。(3)制備納米鐵黃粉體:同實施例1,但氧化反應時間為32h,納米鐵黃粉體產率達到90%,Fe2O3%的含量為80.9%,n為2.10。采用同樣的方法對納米鐵黃粉體進行包覆,納米鐵黃粉體的吸油量從包覆前的64.8g/100g降至包覆后的33.5g/100g。(4)分離鎳:分離鎳的方法同實施例1,得到共沉淀物1.6679g,分離鎳濾液pH為12.15。得到的分離鎳濾液每500ml,用2g/L活性炭吸附30min后即可按GB21900-2008電鍍污染物排放標準達標排放。