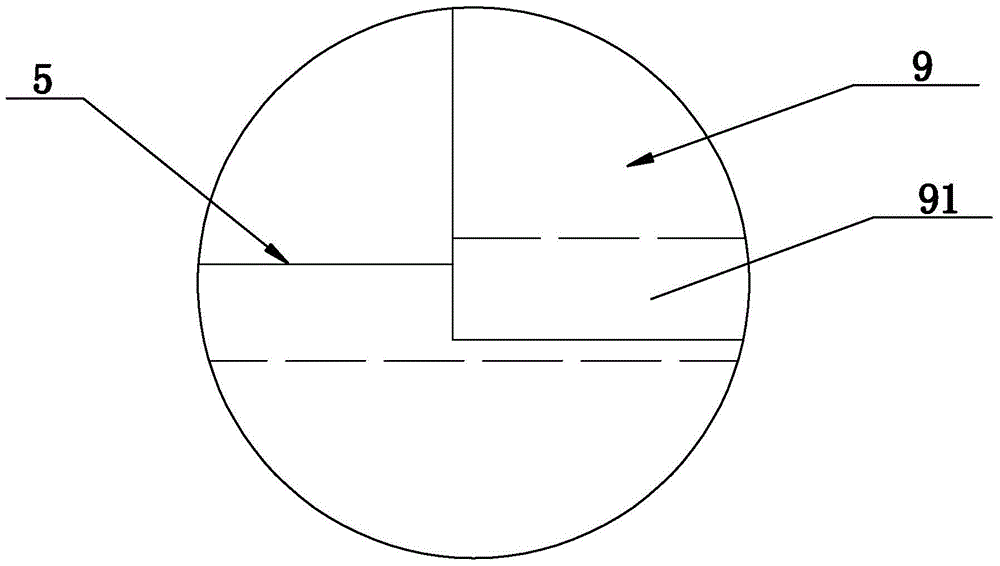
本發明涉及工件表面處理裝置技術領域,具體涉及一種鋼管內拋光定位裝置。
背景技術:隨著客戶對鋼管表面質量要求越來越高,作為中間生產商對鋼管生產也需要不斷提高其表面質量。特別是近年來氣壓和液壓設備的推廣和普及,行業內原先靠冷軋工藝生產的鋼管已經無法滿足顧客的需求。在市場行情的需求下,目前鋼管內壁拋光工序,大都是在電機的輸出軸上裝上拋光輪,操作者用手抓住鋼管,將鋼管內孔表面用力壓向拋光輪進行拋光,該種手工勞動的勞動強度較大,工作效率低,產品質量也不高,安全性和可靠性低。于是在2012.07.05,湖州華鼎不銹鋼管業有限公司發明了專利名稱為“小口徑鋼管內拋光裝置”,中國授權公告號CN202622538U,該專利技術方案雖然能降低勞動強度,但是其結構設置不合理,通過送進平臺中部支撐桿上的固定孔對鋼管進行定位,鋼管容易晃動,且鋼管送進機構裝夾鋼管呈“懸臂梁”式裝夾,鋼管在加工時容易晃動,不易保證加工質量,加工效率低。
技術實現要素:針對現有技術存在的不足,本發明的目的在于提供一種結構設計合理、鋼管固定可靠,容易保證加工質量的鋼管內拋光定位裝置。為實現上述目的,本發明提供了如下技術方案:一種鋼管內拋光定位裝置,包括鋼管固定架和固定安裝在鋼管固定架左右兩端的兩個照明燈,所述鋼管固定架下端固定設置有滾輪,且鋼管固定架上端固定安裝有工作臺,且工作臺上橫向設置有弧形的鋼管定位槽,該鋼管定位槽內放置有鋼管,所述工作臺左右 兩端一體設置有支撐架,兩支撐架上端一體設置有氣缸架,所述氣缸架上至少固定設置有兩個鋼管定位氣缸,所述鋼管定位氣缸的活塞桿朝向鋼管定位槽設置,每根鋼管定位氣缸的活塞桿頭部套接有一塊壓塊,且壓塊下端面設置有與鋼管定位槽匹配的弧形凹槽,通過鋼管定位氣缸控制活塞桿下降使壓塊上的弧形凹槽壓緊鋼管;所述工作臺上一體設置有左凸塊和右凸塊,所述左凸塊左端設置有左鋼管推動氣缸,該左鋼管推動氣缸的活塞桿頭部與左凸塊固定連接,所述右凸塊右端設置有右鋼管推動氣缸,該右鋼管推動氣缸的活塞桿頭部與右凸塊固定連接。通過采用上述技術方案,通過鋼管定位氣缸控制活塞桿下降使壓塊上的弧形凹槽壓緊鋼管,使得鋼管固定可靠,加工時不會晃動,容易保證加工質量;左鋼管推動氣缸推動工作臺向右運動,右鋼管推動氣缸推動工作臺向左運動,使得磨頭能對鋼管內壁進行拋光,實現自動化的拋光,拋光效果好,工作效率高,還降低了勞動強度,通過氣缸勻速進給,排除了人工送進不均勻、不安全等因素。本發明進一步設置為:所述左鋼管推動氣缸的活塞桿頭部套接固定有第一連接板,所述第一連接板與左凸塊之間設置有第一鎖緊螺釘,第一連接板通過第一鎖緊螺釘與左凸塊連接固定,所述左鋼管推動氣缸通過活塞桿推動工作臺向右移動。通過本設置,左鋼管推動氣缸的活塞桿與左凸塊連接可靠。本發明還進一步設置為:所述右鋼管推動氣缸的活塞桿頭部套接固定有第二連接板,所述第二連接板與右凸塊之間設置有第二鎖緊螺釘,第二連接板通過第二鎖緊螺釘與右凸塊連接固定,所述右鋼管推動氣缸通過活塞桿推動工作臺向左移動。通過本設置,右鋼管推動氣缸的活塞桿與右凸塊連接可靠。本發明還進一步設置為:所述工作臺下端均勻設置有四個鋼管固定架,每 個鋼管固定架包括與工作臺下端面垂直焊接固定的滑接管,所述滑接管內插接有滑接桿,所述滑接桿與滑接管螺紋配合。通過本設置,鋼管固定架結構設置合理,通過旋轉滑接桿可調節高度,使用方便。本發明還進一步設置為:所述鋼管定位槽左端設置有左擋板,鋼管定位槽右端設置有右擋板,所述左擋板和右擋板通過螺釘與工作臺連接固定。通過本設置,左擋板和右擋板使得鋼管定位更加準確,限制移動范圍,工作更加可靠。本發明的優點是:與現有技術相比,本發明結構設置合理,通過鋼管定位氣缸控制活塞桿下降使壓塊上的弧形凹槽壓緊鋼管,使得鋼管固定可靠,加工時不會晃動,容易保證加工質量;左鋼管推動氣缸推動工作臺向右運動,右鋼管推動氣缸推動工作臺向左運動,使得磨頭能對鋼管內壁進行拋光,實現自動化的拋光,拋光效果好,工作效率高,還降低了勞動強度,通過氣缸勻速進給,排除了人工送進不均勻、不安全等因素。下面結合說明書附圖和具體實施例對本發明作進一步說明。附圖說明圖1為本發明實施例的結構示意圖;圖2為圖1中I部的放大示意圖;圖3為圖1中II部的放大示意圖。具體實施方式參見圖1、圖2和圖3,本發明公開的一種鋼管內拋光定位裝置,包括鋼管固定架1和固定安裝在鋼管固定架1左右兩端的兩個照明燈2,所述鋼管固定架1下端固定設置有滾輪3,且鋼管固定架1上端固定安裝有工作臺4,且工作臺4上橫向設置有弧形的鋼管定位槽41,該鋼管定位槽41內放置有鋼管5,所述工作臺4左右兩端一體設置有支撐架6,兩支撐架6上端一體設置有氣缸架7, 所述氣缸架7上至少固定設置有兩個鋼管定位氣缸8,所述鋼管定位氣缸8的活塞桿81朝向鋼管定位槽41設置,每根鋼管定位氣缸8的活塞桿81頭部套接有一塊壓塊9,且壓塊9下端面設置有與鋼管定位槽41匹配的弧形凹槽91,通過鋼管定位氣缸8控制活塞桿81下降使壓塊9上的弧形凹槽91壓緊鋼管5;所述工作臺4上一體設置有左凸塊10和右凸塊11,所述左凸塊10左端設置有左鋼管推動氣缸12,該左鋼管推動氣缸12的活塞桿頭部與左凸塊10固定連接,所述右凸塊11右端設置有右鋼管推動氣缸13,該右鋼管推動氣缸13的活塞桿頭部與右凸塊11固定連接。所述左鋼管推動氣缸12的活塞桿頭部套接固定有第一連接板16,所述第一連接板16與左凸塊10之間設置有第一鎖緊螺釘17,第一連接板16通過第一鎖緊螺釘17與左凸塊10連接固定,所述左鋼管推動氣缸12通過活塞桿推動工作臺4向右移動;所述右鋼管推動氣缸13的活塞桿頭部套接固定有第二連接板18,所述第二連接板18與右凸塊11之間設置有第二鎖緊螺釘19,第二連接板18通過第二鎖緊螺釘19與右凸塊11連接固定,所述右鋼管推動氣缸13通過活塞桿推動工作臺4向左移動。作為優選的,本實施例氣缸架7上共設置兩個鋼管定位氣缸8,分別設置在氣缸架7左端和右端,兩個鋼管定位氣缸8通過鋼管定位氣缸8控制活塞桿81下降使壓塊9上的弧形凹槽91分別壓緊鋼管5左端和右端;兩個鋼管定位氣缸8尾部均通過螺釘與氣缸架7連接固定;所述的兩個照明燈2均為LED燈。為使本發明結構更加合理,作為優選的,本實施例所述工作臺4下端均勻設置有四個鋼管固定架1,每個鋼管固定架1包括與工作臺4下端面垂直焊接固定的滑接管111,所述滑接管111內插接有滑接桿112,所述滑接桿112與滑接管111螺紋配合。所述鋼管定位槽41左端設置有左擋板14,鋼管定位槽41右端設置有右擋板15,所述左擋板14和右擋板15通過螺釘與工作臺4連接固定。本發明結構設置合理,通過鋼管定位氣缸控制活塞桿下降使壓塊上的弧形凹槽壓緊鋼管,使得鋼管固定可靠,加工時不會晃動,容易保證加工質量;左鋼管推動氣缸推動工作臺向右運動,右鋼管推動氣缸推動工作臺向左運動,使得磨頭能對鋼管內壁進行拋光,實現自動化的拋光,拋光效果好,工作效率高,還降低了勞動強度,通過氣缸勻速進給,排除了人工送進不均勻、不安全等因素。上述實施例對本發明的具體描述,只用于對本發明進行進一步說明,不能理解為對本發明保護范圍的限定,本領域的技術工程師根據上述發明的內容對本發明作出一些非本質的改進和調整均落入本發明的保護范圍之內。