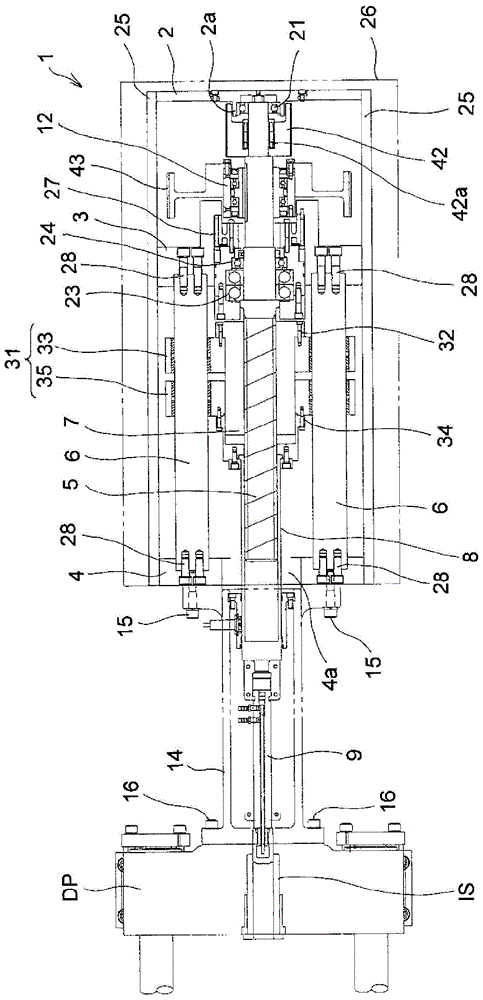
本發明涉及一種電動壓鑄機,尤其涉及向模具腔體內噴射、填充熔融金屬材料的電動噴射裝置的結構。
背景技術:壓鑄機是一種成形機,通過在每一次噴射時對噴射裝置所具備的噴射柱塞進行前進驅動,從而將一定量的Al合金、Mg合金等的熔融金屬材料噴射、填充到模具腔體內來形成所需形狀的產品。壓鑄機也與向模具腔體內噴射、填充塑料材料并對所需形狀的產品進行成形的噴射成形機同樣,經過低速噴射工序、高速噴射工序以及增壓工序(噴射成形機中稱為保壓工序。)來向模具腔體內噴射、填充成形材料,但壓鑄機與噴射成形機相比,具有高速噴射工序中的噴射速度要高1位數左右的特征。因此,以往,具備利用油壓來驅動噴射柱塞的油壓噴射裝置的油壓式壓鑄機成為主流。然而,具備油壓噴射裝置的壓鑄機雖然能對噴射柱塞進行高速驅動,但反過來也存在著種種問題,例如工程設備規模變大,能源效率較差,成形工廠內容易被油弄臟導致作業環境較差。因此,近年來,提出了具備沒有上述缺點的電動噴射裝置的壓鑄機(例如參照專利文獻1。)。專利文獻1所記載的電動噴射裝置如圖10所示,包括兩個噴射用電動伺服電機101a、101b,利用由螺母體102a、102b以及與其螺合的螺紋軸103a、103b構成的滾珠絲杠機構104a、104b將上述兩個噴射用電動伺服電機101a、101b的旋轉力轉換為螺母體102a、102b的推進力,螺母體102a、102b經由一體安裝的移動構件105使噴射柱塞106前后移動。此外,移動構件105與噴射柱塞106之間設有沖擊壓力防止裝置(液壓缸)107,該裝置內置有用于抑制沖擊壓力的沖擊緩沖彈簧107a,以防止在高速噴射工序完成時對模具腔體內的熔融金屬材料作用過大的沖擊壓力。該電動噴射裝置利用兩個噴射用電動伺服電機101a、101b的合力來驅動噴射柱塞106,因此能獲得較高的噴射速度。此外,由于移動構件105與噴射柱塞106之間具備內置有沖擊緩沖彈簧107a的沖擊壓力防止裝置107,因此能形成沒有毛邊等外觀不良的良品,并能防止因沖擊壓力引起的模具等的損壞。現有技術文獻專利文獻專利文獻1:日本專利特開2010-260070號公報
技術實現要素:發明所要解決的技術問題然而,由于專利文獻1所記載的電動噴射裝置在移動構件105與噴射柱塞106之間串聯配置沖擊壓力防止裝置107,因此電動噴射裝置、進而壓鑄機的全長會變大。本發明為了解決上述現有技術的問題而完成,其目的在于提供一種小型、且能抑制噴射填充在模具腔體內的熔融金屬上產生的沖擊壓力的電動壓鑄機。解決技術問題所采用的技術方案本發明為了解決上述問題,其特征在于,包括:可旋轉地被保持的螺紋軸;與所述螺紋軸螺合、并根據所述螺紋軸的旋轉驅動而被前后驅動的螺母體;與所述螺母體的前后移動聯動地被前后驅動的噴射柱塞;在前后移動方向上對所述螺母體以及所述噴射柱塞進行引導的引導條;以及對所述螺紋軸進行旋轉驅動的噴射用電動伺服電機,在所述螺母體與所述引導條之間配置有沖擊緩沖裝置,該沖擊緩沖裝置承受作用于所述噴射柱塞的沖擊壓力而彈性變形。根據該結構,由于螺母體與引導條之間配置有沖擊緩沖裝置,因此能并排配置上述各構件,與在移動構件(螺母體)與噴射柱塞之間串聯配置沖擊壓力防止裝置的情況相比,能縮小電動噴射裝置的全長,進而能縮小壓鑄機的全長。此外,本發明的特征在于,在上述結構的電動壓鑄機中,所述噴射柱塞經由連結體以及所述沖擊緩沖裝置與所述螺母體連結,所述沖擊緩沖裝置由以下部分構成:中央部固定于所述螺母體且端部自由滑動地安裝于所述引導條的第一構件;中央部固定于所述連結體且端部自由滑動地安裝于所述引導條的第二構件;以及配置在所述第一構件與第二構件之間的彈性構件。根據該結構,由于能經由沖擊緩沖裝置以及連結體使螺母體與噴射柱塞連結,因此能利用沖擊緩沖裝置吸收作用于噴射柱塞的沖擊壓力,能制造沒有毛邊等外觀不良的成形品。此外,本發明的特征在于,在上述結構的電動壓鑄機中,所述彈性構件以被施加與將所述噴射用電動伺服電機的驅動控制從噴射控制切換為增壓控制時模具腔體內的熔融金屬壓力同等、或稍大的壓縮力的狀態配置在所述第一構件與所述第二構件之間,第一構件及所述第二構件以即使對模具腔體內的熔融金屬施加有沖擊壓力時也不會密接的規定間隔隔開并相對配置。根據該結構,由于彈性構件以被施加與將噴射用電動伺服電機的驅動控制從噴射控制切換為增壓控制時模具腔體內的熔融金屬壓力同等、或稍大的壓縮力的狀態配置在第一構件與第二構件之間,因此在噴射工序中,彈性構件不會收縮,能向熔融金屬提供所需要的噴射壓力。此外,根據本發明,由于第一構件與所述第二構件以即使對模具腔體內的熔融金屬施加有沖擊壓力時也不會密接的規定間隔隔開并相對配置,因此能可靠地吸收過大的沖擊壓力,能制造沒有毛邊等外觀不良的成形品。發明效果根據本發明,由于螺母體與引導條之間配置有承受作用于噴射柱塞的沖擊壓力而彈性變形的沖擊緩沖裝置,因此能并排配置上述各構件,與在螺母體和噴射柱塞之間串聯配置沖擊壓力防止裝置的情況相比,能縮小電動噴射裝置的全長,進而能縮小壓鑄機的全長。附圖說明圖1是從正面側觀察實施方式的噴射裝置的主要部分剖視圖。圖2是從平面側觀察實施方式的噴射裝置的主要部分剖視圖。圖3是圖2的主要部分放大圖。圖4是實施方式的沖擊緩沖裝置的主視圖。圖5是實施方式的沖擊緩沖裝置的內視圖。圖6是實施方式的單向離合器的立體圖。圖7是示意性表示實施方式的單向離合器的結構的主要部分剖視圖。圖8是表示實施方式的壓鑄機的動作的時序圖。圖9是表示其它實施方式的噴射裝置的立體圖。圖10是現有技術的噴射裝置的結構圖。具體實施方式下面,利用附圖對本發明的電動壓鑄機所具備的電動噴射裝置的一個實施方式進行說明。如圖1和圖2所示,實施方式的電動噴射裝置1包括:以規定間隔相對配置的第一至第三保持板2、3、4;可旋轉地保持在第一及第二保持板2、3上的螺紋軸5;兩端固定在第二及第三保持板3、4上的引導條6;與螺紋軸5螺合、通過對螺紋軸5進行旋轉驅動從而被沿著引導條6前后驅動的螺母體7;一端固定于螺母體7的前端部的筒狀的連結體8;一端固定于連結體8的前端部的噴射柱塞9;對螺紋軸5進行旋轉驅動的噴射用電動伺服電機10以及增壓用電動伺服電機11;設置在螺紋軸5與增壓用電動伺服電機11之間的單向離合器(One-wayclutch)12;以及對噴射用電動伺服電機10以及增壓用電動伺服電機11的驅動進行控制的控制器13。另外,圖中的標號14表示對噴射裝置1以及合模裝置的固定模板DP進行連接的C框,該C框14如圖2所示,利用螺栓15、16固定于第三保持板4的外表面以及固定模板DP。噴射柱塞9的前端部配置在形成于固定模板DP上的噴射套筒IS內。如圖3中放大所示,第一保持板2的中央部內表面上突出設置有輪形的軸承保持部2a,螺紋軸5的一端部經由插入到該軸承保持部2a的內表面以及螺紋軸5的外表面中的軸承21來可旋轉地保持在第一保持板2上。此外,第二保持板3的中央部設有圓形的開口部3a,輪形的階梯軸套3b從該開口部3a的周圍立起,開口部3a內可滑動地嵌入有軸承托架22。螺紋軸5的中間部經由插入到該軸承托架22的內表面與螺紋軸5的外表面中的角接觸軸承23以及軸承24來可旋轉地保持于第二保持板3。另外,第三保持板4的中央部設有螺紋軸5以及連結體8的貫通孔4a。上述各保持板2、3、4如圖1及圖2所示,通過固定構件25而成為一體,并固定在未圖示的電動壓鑄機的框架上。為了確保作業人員等的安全,優選這些保持板2、3、4以及固定構件25的周圍被保護蓋板26覆蓋。如圖1至圖3所示,在形成在第二保持板3上的階梯軸套3b的內周,與螺紋軸5同心地配置有形成為內徑比螺紋軸5的外徑大的環狀的測壓元件單元27。本例的測壓元件單元27如圖3中放大所示,具有內環部27a、外環部27b、以及形成在這兩個部分之間的彈性變形部27c,內環部27a螺釘緊固于軸承托架22,且外環部27b螺釘緊固于階梯軸套3b。彈性變形部27c上貼有未圖示的應變計,以檢測彈性變形部27c的應變量、即作用于噴射柱塞9的噴射壓力、沖擊壓力以及增壓壓力。由此,本實施方式的電動噴射裝置1中,形成為環狀的測壓元件單元27與螺紋軸5同心配置,且設置在軸承托架22與階梯軸套3b之間,因此能縮小測壓元件單元27的設置空間,從而能實現電動噴射裝置1的小型化,進而實現搭載該電動噴射裝置1的的電動壓鑄機的小型化。引導條6如圖2所示,其兩端部通過螺栓28緊固于第二及第三保持板3、4。此外,如圖1至圖3所示,螺母體7的外周具備一端自由滑動地連結于引導條6的沖擊壓力抑制用的沖擊緩沖裝置31。本例的沖擊緩沖裝置31如圖4及圖5所示,由以下部分構成:利用螺栓32緊固于螺母體7的第一構件33;利用螺栓34緊固于連結體8的第二構件35;設置在第一構件33與第二構件35之間的螺旋彈簧等彈性構件36;以及隔開所需間隔對第一構件33以及第二構件35進行連結的連結螺栓37。如圖5所示,第一構件33及第二構件35的內表面形狀形成為橫向較長的大致六邊形,其中央部設有用于供螺母體7貫通的螺母體貫通孔38,該螺母體貫通孔38周圍的規定位置設有用于供連結螺栓37貫通的連結螺栓貫通孔39。此外,螺母體貫通孔38周圍的、不與連結螺栓貫通孔39干擾的部分上大致均勻地形成有多個(圖5的示例中為10個)彈性構件收納孔40。另外,經由螺母體貫通孔38在長徑方向的端部設有用于貫通引導條6的引導條貫通孔41,該引導條貫通孔41內具備滑動軸承(金屬)42。第一構件33在螺母體7貫通螺母體貫通孔38內、且引導條6貫通引導條貫通孔41內的狀態下,利用螺栓32緊固于螺母體7。因此,該第一構件33也具有作為引導構件的功能,即在對螺紋軸5進行旋轉驅動時,使螺母體7沿著引導條6移動。另一方面,第二構件35在螺母體7貫通螺母體貫通孔38內、且引導條6貫通引導條貫通孔41內的狀態下,利用螺栓34緊固于連結體8。因此,該第二構件35還具有作為傳動機構及引導構件的功能,即經由連結體8將螺母體7的前后運動傳遞給噴射柱塞9,并使噴射柱塞9沿著引導條6移動。彈性構件36在被施加與從噴射工序切換為增壓工序時的熔融金屬壓力同等或稍大(例如1.05倍~1.1倍)的壓縮力的狀態下,收納在第一構件33與第二構件35之間。由此,在噴射工序中,能在彈性構件36不收縮的狀態下向金屬熔融物施加所需的噴射壓力。此外,第一構件33與第二構件35以即使受到沖擊壓力也不會密接的規定間隔隔開并進行組合。由此,能夠吸收沖擊壓力。另外,通過調整連結螺栓37,能適當調整作用于彈性構件36的壓縮力。螺紋軸5的前端部經由所需的連結件42a固定有第一滑輪42,并經由單向離合器12安裝有第二滑輪43。第一滑輪42將噴射用電動伺服電機10的旋轉力傳遞給螺紋軸5,與固定于噴射用電動伺服電機10的輸出軸的驅動側滑輪10a之間懸掛有同步帶44。與此相對,第二滑輪43將增壓用電動伺服電機11的旋轉力傳遞給螺紋軸5,與固定于增壓用電動伺服電機11的輸出軸的驅動側滑輪11a之間懸掛有同步帶45。單向離合器12如圖6及圖7所示主要由以下構件構成:內環51;外環52;可搖動地配置在上述內環51與外環52之間的多個凸輪53;對凸輪53進行保持的止動器54;以及在一個方向上對凸輪53施力的彈簧構件55。凸輪53在特定的一個方向上使內環51及外環52旋轉的情況下,當內環51的轉速高于外環52的轉速時,使上述內環51與外環52的卡合解除,使得內環51相對于外環52空轉。此外,該凸輪53在內環51的轉速低于外環52的轉速時,使內環51及外環52卡合,從而使內環51與外環52在上述特定的一個方向上一體旋轉。內環51固定與螺紋軸5的外周,外環52固定于第二滑輪43的內周。控制器13獲取來自噴射用電動伺服電機10及增壓用電動伺服電機11所具備的編碼器10b、11b的信號以及來自測壓元件單元27的信號等,負責噴射用電動伺服電機10以及增壓用電動伺服電機11的啟動時刻、停止時刻、加速條件、減速條件、轉速以及轉矩等噴射用電動伺服電機10以及增壓用電動伺服電機11的整個驅動控制。另外,作為該控制器13,也能使用負責壓鑄機整體的驅動控制的機器控制器。以下,參照圖8對上述結構的實施方式的電動噴射裝置1的動作進行說明。以下動作基于從控制器13輸出的指令信號來進行。如圖8(b)所示,若在壓鑄機執行連續自動運行的狀態下到達低速噴射的開始時刻,則在規定的旋轉方向上啟動噴射用電動伺服電機10,并將其轉速控制成預先決定的低速噴射用轉速。接著,在到達高速噴射的開始時刻后,噴射用電動伺服電機10增速,其轉速被控制成預先決定的高速噴射用轉速。噴射用電動伺服電機10的旋轉經由驅動側滑輪10a、同步帶44以及第一滑輪42被傳遞給螺紋軸5,從而以低速噴射時的轉速以及高速噴射時的轉速對螺紋軸5進行旋轉驅動。若螺紋軸5被旋轉驅動,則與螺紋軸5螺合的螺母體7被前進驅動,如圖8(b)所示,以規定的低速噴射時的前進速度以及高速噴射時的前進速度對經由沖擊緩沖裝置31以及連結體8與螺母體7連結的噴射柱塞9進行前進驅動。由此,提供給噴射套筒IS內的一定量的熔融金屬在以規定的噴射速度低速噴射到未圖示的模具腔體內以后,以規定的噴射速度高速噴射。在利用噴射柱塞9的前進將噴射套筒IS內的熔融金屬噴射到模具腔體內時,對模具腔體內的熔融金屬施加有沖擊性的沖擊壓力。若沖擊壓力過大,則產品容易產生毛邊等成形不良。本實施方式的電動噴射裝置1利用沖擊緩沖裝置31所具備的彈性構件36來吸收沖擊壓力。即,由于高速噴射工序中產生的沖擊壓力會經由噴射柱塞9及連結體8傳遞給沖擊緩沖裝置31的第二構件35,因此如圖8(a)所示,第一構件33與第二構件35之間的彈性構件36被壓縮,利用其彈性變形將沖擊壓力吸收。由此,不會對模具腔體內的熔融金屬作用過大的沖擊壓力,能制造出良品。此外,本實施方式的沖擊緩沖裝置31由于配置于螺母體7的外周,因此與沖擊緩沖裝置31和螺母體7串聯配置的情況相比,能縮短電動噴射裝置1的全長,進而縮短電動壓鑄機的全長。在到達噴射工序的末期時,控制器13如圖8(b)所示,對噴射用電動伺服電極10進行減速控制,最終停止噴射用電動伺服電機10的旋轉。此外,控制器13在開始噴射用電動伺服電機10的減速控制以前,開始增壓用電動伺服電機11的啟動,并將其轉速保持在預先決定的規定轉速。噴射用電動伺服電機10的轉速在減速控制下而逐漸減少,增壓用電動伺服電機11的轉速在啟動控制下而逐漸增大,因此在噴射用電動伺服電機10的減速控制中,噴射用電動伺服電機10的轉速與增壓用電動伺服電機11的轉速反轉。因此,對于即使在增壓用電動伺服電機11啟動后、由噴射用電動伺服電機10進行旋轉驅動的螺紋軸5的轉速也大于由增壓用電動伺服電機11進行旋轉驅動的螺紋軸5的轉速的情況下,單向離合器12進行空轉,增壓用電動伺服電機11的旋轉里不會傳遞給螺紋軸5。由此,通過對噴射用電動伺服電極10進行驅動控制,從而執行噴射工序中的低速噴射工序以及高速噴射工序。若在該狀態下,由噴射用電動伺服電機10進行旋轉驅動的螺紋軸5的轉速進一步降低,由噴射用伺服電機10進行旋轉驅動的螺紋軸5的轉速低于由增壓用電動伺服電機11進行旋轉驅動的螺紋軸5的轉速,則在該階段,單向離合器12自動切換為連接狀態,增壓用電動伺服電機11的旋轉里被傳遞給螺紋軸5。該旋轉力被螺母體7轉換為推進力,經由沖擊緩沖裝置31及連結體8傳遞給噴射柱塞9。利用該增壓用電動伺服電機11的動力補給,從而如圖8(c)所示,向模具腔體內的熔融金屬提供所需的增壓壓力,執行噴射工序后的增壓工序。由此,能防止鑄物孔等成形不良。另外,在上述增壓用電動伺服電機11的驅動控制中,在開始噴射用電動伺服電機10的減速控制之前開始增壓用電動伺服電機11的啟動,但本發明的主旨并不限定于此,也可以在開始噴射用電動伺服電機10的減速控制的同時、或在此之后開始啟動增壓用電動伺服電機11。由此,本實施方式的噴射裝置1能從增壓用電動伺服電機11獲得執行增壓工序所需的動力補給,因此無需在螺紋軸5上設置大型的飛輪裝置,能實現壓鑄機的小型化和輕量化。此外,使用了如下那樣的單向離合器12作為離合器機構,該單向離合器12在由噴射用電動伺服電機10進行旋轉驅動的螺紋軸5的轉速低于由增壓用電動伺服電機11進行旋轉驅動的螺紋軸5的轉速的階段自動切換為連接狀態,因此,無需控制器13進行離合器裝置的切換控制,能減輕控制器13的負擔。低速噴射工序、高速噴射道工序以及增壓工序的各個工序中,作用于噴射柱塞9的低速噴射壓力、高速噴射壓力、沖擊壓力以及增壓壓力經由噴射柱塞9、連結體8、沖擊緩沖裝置31、螺母體7、螺紋軸5、角接觸軸承23、以及軸承托架22傳遞給測壓元件單元27的內環部27a。由此,在測壓元件單元27的彈性變形部27c上產生與低速噴射壓力、高速噴射壓力、沖擊壓力以及增壓壓力相對應的應變,并從應變計輸出與該應變量相對應的電信號,因此通過將該電信號讀取到控制器13中,從而能監視低速噴射壓力、高速噴射壓力、沖擊壓力以及增壓壓力。本實施方式的噴射裝置中,由于將測壓元件單元27配置于螺紋軸5的外周,因此與測壓元件單元27和螺母體5串聯配置的情況相比,能縮短電動噴射裝置1的全長,進而縮短電動壓鑄機的全長。若在完成增壓工序后結束冷卻工序,并對未圖示的模具開閉電動伺服電機進行驅動來執行開模工序,則增壓工序時被壓縮的彈性構件36的恢復力會從開模工序開始時通過噴射柱塞9向料柄(biscuit)施加推出方向的壓力,能使料柄推出動作追隨開模動作。之后,對噴射用電動伺服電機10進行反轉驅動來使螺母體7恢復到原位置。連結體8及噴射柱塞9也隨之恢復到原位置。另外,本發明的主旨在于,在螺母體7與引導條6之間配置承受作用于噴射柱塞9的沖擊壓力而彈性變形的沖擊緩沖裝置31,而關于其它結構,則不限于上述實施方式,能適當進行設計變更。例如也能如圖9所示,具備多臺(圖9的示例中為兩臺)噴射用電動伺服電機10,并將各噴射用電動伺服電機10的旋轉力經由多根(圖9的示例中為兩根)同步帶44傳遞給螺紋軸5。此外,同樣也能如圖9所示,將增壓用電動伺服電機11的旋轉力經由多級(圖9的示例中為兩級)減速機構傳遞給螺紋軸5。圖9所示的兩級減速機構由以下部分構成:固定于增壓用電動伺服電機11的輸出軸的驅動側滑輪11a;固定于中間軸61的第一中間滑輪62以及直徑小于該第一中間滑輪62的第二中間滑輪63;經由單向離合器12安裝在螺紋軸5上的第二滑輪43;懸掛在驅動側滑輪11a以及第一中間滑輪62上的第一同步帶64;以及懸掛在第二中間滑輪63以及第二滑輪43上的第二同步帶65。根據上述各變形例,能使用低輸出的噴射用電動伺服電機10以及增壓用電動伺服電機11來產生高噴射壓力以及增壓壓力,因此能更廉價地獲得更高性能的電動壓鑄機。標號說明1電動噴射裝置2、3、4保持板5螺紋軸6引導條7螺母體8連結體9噴射柱塞10噴射用電動伺服電機11增壓用電動伺服電機12單向離合器13控制器21軸承22軸承托架23角接觸軸承24軸承25固定構件26保護蓋板27測壓元件單元28螺栓31沖擊緩沖裝置33第一構件35第二構件36彈性構件37連結螺栓38螺母體貫通孔39連結螺栓貫通孔40彈性構件收納孔41引導條貫通孔42第一滑輪43第二滑輪44、45同步帶51內環52外環53凸輪54止動器55彈簧構件